1. Prefacio
La nitruración de gas tiene varias ventajas sobre la nitruración de iones, incluida la facilidad de operación, la alta repetibilidad del proceso, la estructura simple del equipo y la capacidad de lograr un control automático del proceso.
Uno de los beneficios más importantes de la nitruración gaseosa es la mejora de la temperatura y la uniformidad de la atmósfera durante el proceso.
En particular, la profundidad de la capa de nitruración en la raíz del diente y el círculo primitivo de los engranajes de módulo pequeño es más uniforme durante la nitruración con gas en comparación con la nitruración con iones.
En los últimos años, el proceso de nitruración con gas ha experimentado avances significativos, como el desarrollo de procesos de preoxidación y nitruración con gas y varias otras técnicas de nitruración con gas.
Estos avances han reducido en varios grados el tiempo del ciclo de producción entre la nitruración iónica y la nitruración gaseosa.
Sin embargo, es fundamental prestar atención a posibles problemas durante el proceso de control de la atmósfera durante la nitruración de engranajes.
2. Limpieza antes de la nitruración con gas
Antes de someterse a nitruración y carga de gas, el equipo debe limpiarse a fondo para garantizar que no haya agua ni impurezas presentes.
Si este paso no se completa correctamente, la superficie nitrurada resultante puede parecer desigual y pueden aparecer manchas oscuras.
Aunque no existe una diferencia significativa en la profundidad, dureza o estructura metalográfica de la capa de nitruración entre las áreas deslustradas y las áreas normales, estas manchas pueden afectar significativamente la calidad de la apariencia general del equipo.
La macromorfología de estas áreas puntiformes irregulares se analizó utilizando un estereomicroscopio de campo ultraprofundo (como se ve en la Figura 1).
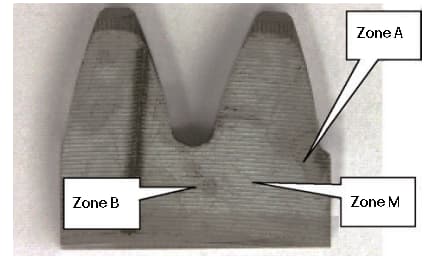
Fig.1 Macromorfología del área manchada de la cara del extremo del engranaje
La morfología microscópica del área teñida se analizó utilizando un microscopio electrónico de barrido (como se ve en la Figura 2). Las áreas que parecían blancas a simple vista se observaron bajo un microscopio electrónico de barrido.
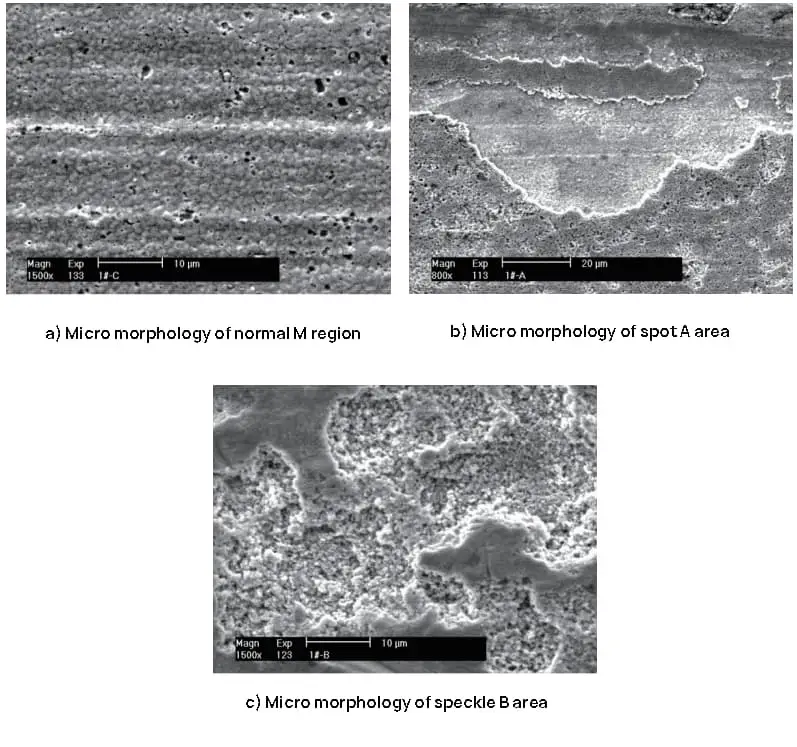
Fig.2 Micromorfología de la zona de la mancha de la cara del extremo del engranaje.
La composición química del área manchada de apariencia anormal en la cara del extremo del engranaje se comparó y analizó con el área normal en la cara del extremo del engranaje. Los resultados de esta comparación se presentan en la Tabla 1.
Tabla 1 resultados de comparación (fracción de masa) (%) de la determinación de la composición química en la microárea de la cara del extremo del engranaje
Ubicación de detección: | W. | norte | oh | N / A | Alabama | Sí | PAG | s | W. | k | Aquí | cr | Minnesota | Fe | |
Zona M | Superficie normal | 0,22 | 0,98 | – | – | – | 0,26 | – | – | – | – | – | 0,19 | 0,63 | 97,72 |
0,21 | 0,99 | – | – | – | 0,24 | – | – | – | – | – | 0,25 | 0,57 | 97,73 | ||
Zona A | Superficie de mancha blanca | 0,43 | 1.03 | 2.91 | – | – | 0,22 | – | – | – | 0,09 | 0,21 | 0,19 | 0,35 | 94,59 |
0,38 | 0,89 | 2.58 | – | 0,07 | 0,18 | 0,05 | 0,11 | 0,08 | 0,10 | 0,25 | 0,12 | 0,31 | 94,86 | ||
Pelar fondo plano | 0,28 | 0,73 | 8.59 | – | 0,09 | 0,56 | 0,04 | 0,08 | 0,10 | 0,12 | 0,06 | 0,33 | 1,40 | 89,61 | |
0,39 | 0,84 | 11:59 | 0,15 | 0,10 | 0,67 | 0,13 | 0,11 | 0,09 | 0,12 | 0,06 | 0,34 | 1.71 | 83,71 | ||
Zona B | Manchas oscuras | 1.03 | 0,58 | 29,53 | 0,50 | 0,10 | 0,51 | 0,05 | 0,90 | 0,39 | 1.21 | 0,18 | 0,26 | 0,51 | 64,25 |
0,80 | 0,55 | 28.27 | 0,38 | 0,04 | 0,53 | 0,07 | 1.04 | 0,36 | 1.33 | 0,11 | 0,20 | 0,50 | 65,84 | ||
Mancha redonda blanca | 0,62 | 0,83 | 3.29 | 0,25 | 0,16 | 0,39 | 0,10 | 0,15 | 0,20 | 0,22 | 0,60 | 0,29 | 0,58 | 92,33 | |
0,96 | 0,66 | 5.05 | 030 | 0,16 | 0,60 | 0,06 | 0,14 | 0,23 | 0:30 | 0,96 | 0,32 | 1.09 | 89,16 |
Como se ve en la Tabla 1, el contenido del elemento O en el área teñida anormalmente es mayor que en el área normal. Además de un mayor contenido de O, también contiene trazas de Na, S, Cl, K, Ca, Mg, Al y otros elementos procedentes de aguas residuales, productos de limpieza y aceite de afeitar.
Este análisis muestra que la aparición de nitruración gaseosa se debe a una mala limpieza previa al proceso de nitruración. Por lo tanto, se debe prestar especial atención a los siguientes puntos al limpiar engranajes de nitruración de gas:
- Cuando utilice un agente limpiador a base de agua, la temperatura del agua para el enjuague final no debe ser demasiado alta. Si la temperatura del agua es demasiado alta, se evaporará rápidamente y dejará residuos en la superficie de la pieza de trabajo. Lo mejor es reducir la temperatura de enjuague y utilizar una pistola de aire de alta presión para secar la pieza de trabajo.
- Es posible limpiar con sustancias como acetona o gasolina, pero estas sustancias tienen un punto de inflamación bajo. Es importante garantizar una ventilación adecuada y seguridad contra incendios en el entorno de limpieza.
- La pieza de trabajo debe estar completamente seca antes de limpiarla con un limpiador de hidrocarburos.
- Se debe considerar la calidad del agua utilizada en el proceso de limpieza y se debe utilizar agua pura en la medida de lo posible.
3. Control de distorsión por nitruración de engranajes
La distorsión que se produce durante la nitruración de engranajes está influenciada por varios factores, incluida la forma del engranaje, la tensión residual del mecanizado, el material del engranaje, las herramientas de nitruración, el proceso de nitruración y la velocidad de enfriamiento del engranaje después de la nitruración.
En la producción típica, la gente tiende a centrarse en los primeros factores, pero a menudo ignoran la velocidad de enfriamiento del engranaje después de la nitruración. Esto es especialmente relevante para el orificio interior de engranajes de paredes delgadas, que son particularmente sensibles a la velocidad de enfriamiento después de la nitruración.
Por ejemplo, considere el engranaje que se muestra en la Figura 3.
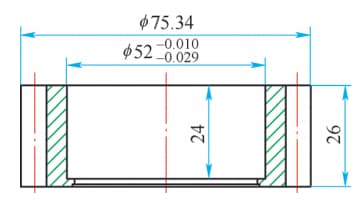
Fig.3 tamaño del engranaje
El tamaño del orificio interior antes de la nitruración era φ 52-0,02-0,035 mm. La Tabla 2 presenta la relación entre el tiempo de enfriamiento del engranaje y la expansión del orificio interno.
Tabla 2 Relación entre el tiempo de enfriamiento del engranaje y la expansión del orificio interno
Tiempo de enfriamiento después de la nitruración. /H |
Expansión del agujero interior /mm |
Tasa de aprobación (%) |
Comentarios |
≥6 | 0,012~0,021 | 75 | El tamaño del orificio interior excede la tolerancia superior |
4~5 | 0,008~0,012 | 99 | El agujero interior está básicamente dentro del rango de tamaño. |
≤4 | 0,005~0,01 | 78 | Tamaño del orificio interior fuera de tolerancia |
Los resultados de las pruebas muestran que la tendencia a la distorsión de los orificios internos de los engranajes a diferentes velocidades de enfriamiento es consistente y generalmente aumenta, pero el grado de distorsión varía. Cuando la velocidad de enfriamiento después de la nitruración es lenta, la distorsión del orificio interior es mayor, y cuando la velocidad de enfriamiento después de la nitruración es rápida, la distorsión del orificio interior es menor.
Para garantizar una distorsión estable del orificio interior del engranaje y mejorar la tasa de calificación del orificio interior del engranaje después de la nitruración, se debe controlar cuidadosamente la velocidad de enfriamiento del engranaje durante la nitruración con gas.
4. Remedio para la oxidación provocada por fuga de gas del horno de nitruración de gas
Si se produce una fuga de gas en el horno de nitruración de gas debido a problemas de sellado u otros problemas, la superficie de la pieza se oxidará. Esta oxidación no afecta la calidad interna de la pieza, pero no cumple con los estándares de calidad de apariencia. En tal situación, el proceso de reducción descrito en la Tabla 3 se puede utilizar para la reparación.
Tabla 3 Proceso de reparación de piezas oxidadas
Temperatura de reparación /℃ |
tiempo de reparación /min |
Tasa de descomposición del amoníaco (%) |
480~500 | 30~40 | 30~40 |
La apariencia del engranaje después de la nitruración de gas, la oxidación y la reducción de fugas de gas se muestra en la Figura 4.
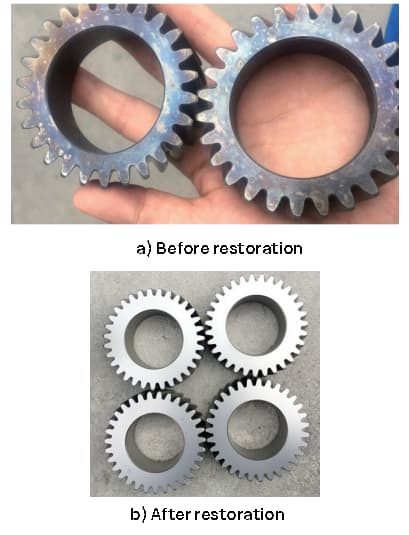
Fig. 4 Aspecto de los engranajes antes y después de la reducción de fugas de gas amoniaco
Es importante señalar que durante el proceso de reducción de la apariencia, la temperatura de nitruración no debe exceder la primera temperatura de nitruración. Normalmente, la temperatura de nitruración durante la reducción debe ser aproximadamente 20°C más baja que la última temperatura de nitruración. La duración del proceso de reducción se puede ajustar en función del grado de oxidación.
5. Conclusión
Los tres problemas y soluciones anteriores resaltan la importancia de prestar atención a cada detalle en el proceso de tratamiento térmico. Con una cuidadosa consideración de cada paso, podrá resolver eficazmente cualquier problema que pueda surgir.