En el proceso de producción, no es raro que haya una dureza insuficiente después del templado, lo cual es un defecto común en el tratamiento térmico y el templado.
Hay dos manifestaciones de este defecto: baja dureza en toda la pieza y puntos insuficientes o blandos en zonas localizadas.
Cuando se produce una dureza insuficiente, es necesario realizar una prueba de dureza o un análisis metalográfico para determinar la causa y luego investigar los posibles factores contribuyentes, como las materias primas, el proceso de calentamiento, el medio de enfriamiento, el método de enfriamiento y la temperatura de templado, para encontrar una solución. .
I. Materias primas
1. Selección inadecuada de materias primas o distribución incorrecta de materiales
Es importante elegir el material adecuado de las piezas para evitar durezas insuficientes o puntos débiles. Se debe usar acero con medio o alto contenido de carbono en lugar de acero con bajo contenido de carbono, y se debe usar acero aleado para herramientas en lugar de acero ordinario con alto contenido de carbono.
En el ejemplo 1, el uso de acero #45 en lugar de acero #25 para el engranaje da como resultado una dureza de enfriamiento de 60 HRC en comparación con una dureza de 380 hbs.
En el ejemplo 2, se recomienda utilizar 9mn2v para el molde en lugar de acero T8, ya que el proceso de enfriamiento a 9mn2v fue seguido por error por enfriamiento de aceite, lo que generó una dureza de solo 50HRC.
Ambos casos ilustran una dureza general insuficiente que puede detectarse mediante una prueba de dureza o una prueba metalográfica.
Para evitar estos problemas se recomienda:
- Seleccionar adecuadamente los materiales en el proceso de diseño.
- Fortalecer la gestión de materiales realizando análisis químicos y marcados de clasificación antes de almacenar el material.
- Solicite al operador del tratamiento térmico que realice un análisis de chispas para garantizar que el material cumpla con los requisitos del dibujo antes de comenzar el proceso.
- Considere utilizar acero aleado con buena templabilidad cuando la sección transversal de la pieza sea grande o el espesor sea grande.
2. La microestructura irregular de las materias primas da como resultado una dureza local insuficiente o puntos débiles
La presencia de segregación o agregación de carburo, como agregación de ferrita, grafito o una estructura de Widmanstatten severa en la microestructura, puede provocar deficiencias de dureza o puntos débiles.
Para resolver este problema, se recomienda homogeneizar la microestructura mediante un tratamiento repetido de forjado o precalentamiento, como normalizar u homogeneizar el recocido antes del enfriamiento.
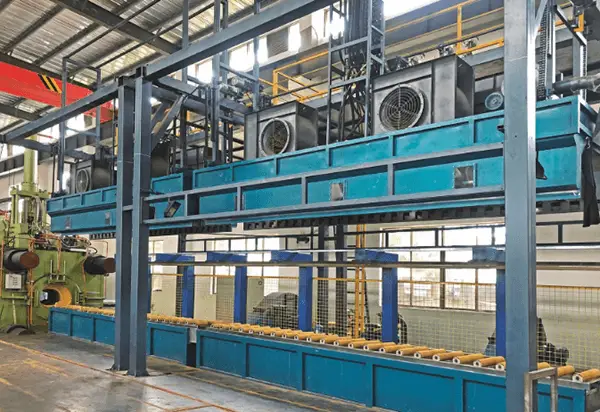
II. Proceso de calentamiento
1. La temperatura de enfriamiento es baja y el tiempo de retención es corto
La dureza del acero hipoeutectoide puede verse afectada cuando la temperatura de calentamiento cae entre AC3 y AC1, ya que la ferrita no se disuelve completamente en austenita, lo que da lugar a una mezcla de ferrita y martensita en lugar de martensita uniforme después del enfriamiento. Esto se puede ver mediante análisis metalográfico.
Asimismo, un calentamiento o un tiempo de retención insuficientes pueden impedir que la perlita se transforme en austenita en aceros con alto contenido de carbono, especialmente en aceros de alta aleación, afectando la dureza de la pieza.
En la producción, estos problemas a menudo pueden ocurrir debido a desviaciones en las lecturas de temperatura o temperaturas irregulares del horno, así como a estimaciones incorrectas del espesor del material.
Para evitar estos problemas se recomienda:
- Controle la velocidad de calentamiento para evitar temperaturas desiguales en el horno y tiempos de mantenimiento prematuros.
- Verifique periódicamente la precisión de los instrumentos indicadores de temperatura.
- Siga estrictamente el manual del material para determinar la velocidad y temperatura de calentamiento del enfriamiento.
- Calcule con precisión el espesor del material, especialmente para piezas con formas especiales.
2. La temperatura de enfriamiento y calentamiento es demasiado alta, el tiempo de retención es demasiado largo
Para aceros para herramientas como el T8, a una temperatura de enfriamiento de 780e, se forman austenita y carburo (Fe3C). La cantidad de carbono disuelto en la austenita es ligeramente superior al 0,77%. Después del enfriamiento, la austenita se transforma en martensita.
Sin embargo, si la temperatura de calentamiento es demasiado alta o el tiempo de retención es demasiado largo, una gran cantidad de carbono en el carburo se disolverá en austenita, aumentando su estabilidad y provocando que la austenita se transforme en martensita a medida que la temperatura comienza a bajar. Esto hace que una gran cantidad de austenita retenida esté presente en la pieza después del enfriamiento, lo que da como resultado una microestructura de m + AC.
La austenita retenida tiene propiedades austeníticas y baja dureza, lo que provoca una disminución de la dureza después del temple. El contenido de austenita retenida puede verse influenciado tanto por la temperatura de calentamiento como por la temperatura de revenido.
Para evitar este problema se recomienda:
- Controle estrictamente la temperatura de enfriamiento y el tiempo de retención para evitar que el exceso de carbono se disuelva en austenita.
- Reduzca la velocidad de enfriamiento del templado o utilice el enfriamiento escalonado para permitir que la austenita subenfriada se transforme en martensita.
- Transformar la austenita retenida en martensita mediante tratamiento en frío.
- Utilice templado a alta temperatura para reducir la austenita retenida y aumentar la dureza.
3. Durante el enfriamiento y calentamiento, la superficie de la pieza se descarboniza.
Después del enfriamiento, la superficie del acero n.° 45 muestra ferrita y martensita con bajo contenido de carbono mediante análisis metalográfico. Sin embargo, tras eliminar la capa de descarburación, la dureza cumple los requisitos.
Este problema suele ser causado por el calentamiento en un horno de caja sin protección adecuada o con una protección deficiente, o por el calentamiento en un baño de sal con una desoxidación deficiente, lo que resulta en la reacción de los átomos de oxígeno y carbono en la pieza de trabajo para formar CO, reduciendo el contenido de carbono en la superficie de la pieza de trabajo y provocando una dureza superficial insuficiente.
Para evitar este problema se recomienda:
- Utilice un horno de calentamiento no oxidante con una atmósfera protectora, como una atmósfera protectora de craqueo de alcohol y metanol.
- Adopte enfriamiento por calentamiento al vacío.
- Empaque y selle un horno tipo caja general con chatarra o carbón vegetal.
- Aplique una capa antioxidante a la superficie de la pieza de trabajo.
- Coloca el carbón en el horno y calienta la pieza después de cubrirla con una solución de ácido bórico y alcohol.
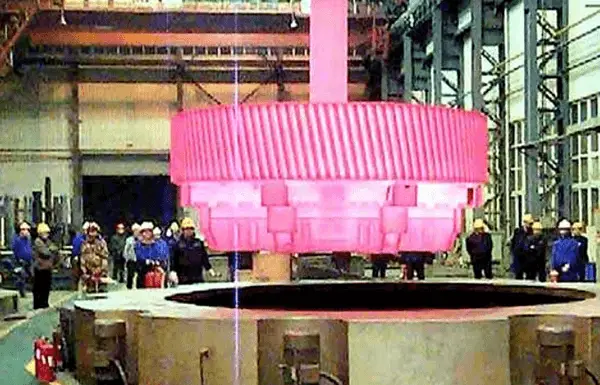
III. Problemas en el proceso de enfriamiento.
1. Selección inadecuada del medio de enfriamiento
La dureza de las piezas templadas en un baño de agua o sal y enfriadas con aceite suele ser baja debido a una capacidad de enfriamiento insuficiente y a una velocidad de enfriamiento lenta, lo que lleva a la transformación de austenita en perlita (AYP) en lugar de martensita (m), principalmente en el núcleo. de la pieza de trabajo.
Por ejemplo, la dureza de un martillo manual T10 templado en aceite es de solo 45 HRC, como se ve a través del análisis metalográfico, que muestra la presencia de troostita en lugar de martensita.
Para solucionar este problema, es importante seleccionar el medio de refrigeración adecuado en función del material, la forma y el tamaño de la pieza de trabajo.
2. Influencia de la temperatura media de enfriamiento
Cuando se enfría continuamente una gran cantidad de piezas mediante enfriamiento con agua, la falta de un sistema de enfriamiento circulante puede hacer que la temperatura del agua aumente y la capacidad de enfriamiento disminuya, lo que provoca fallas en el endurecimiento.
Cuando se utiliza refrigeración por aceite, la baja temperatura y la baja fluidez del aceite al comienzo del proceso pueden provocar una capacidad de refrigeración insuficiente y fallos en el endurecimiento.
Para evitar estos problemas se recomienda:
- Adopte un sistema de enfriamiento circulante y mantenga la temperatura del agua alrededor de 20E durante el enfriamiento con agua.
- Calentar el aceite adecuadamente, especialmente al principio, a una temperatura superior a 80°C, siguiendo el principio de “agua fría y aceite caliente” al enfriar.
3. El medio de extinción es muy antiguo.
Un exceso de impurezas en el baño alcalino (sal) o agua insuficiente pueden provocar puntos débiles durante el enfriamiento.
Para evitar este problema, es importante cambiar periódicamente el medio de enfriamiento y controlar adecuadamente el contenido de agua en el baño alcalino (sal).
4. Control inadecuado del tiempo de enfriamiento
Al fabricar piezas clave con secciones transversales grandes o complejas de acero al carbono, se utiliza enfriamiento con agua y enfriamiento con aceite para evitar deformaciones y grietas. Sin embargo, debido a la alta temperatura de la pieza y especialmente a la lenta velocidad de enfriamiento del núcleo, no es posible obtener martensita uniforme y completa.
Para resolver este problema, se recomienda:
- Controlar adecuadamente el tiempo de enfriamiento del agua. Si la pieza de trabajo se sujeta con unos alicates, transfiérala al aceite inmediatamente cuando la mano ya no sienta vibraciones.
- Retire los residuos de las cavidades más grandes para reducir el espesor de la pieza antes del enfriamiento.
- Tenga en cuenta que un tiempo de residencia demasiado prolongado en el baño de sal durante la etapa de enfriamiento puede provocar una transformación de bainita y una dureza insuficiente.
En conclusión, el fenómeno de extinción insuficiente ocurre con frecuencia, y corresponde al operador determinar las razones y encontrar soluciones en base a análisis específicos y en diferentes situaciones.