Aunque el aluminio y sus aleaciones se utilizan ampliamente para soldar productos importantes, presentan dificultades en la producción de soldadura real. Algunos de los principales problemas incluyen la porosidad en la soldadura, el agrietamiento en caliente durante la soldadura y el logro de la misma resistencia en la unión.
Una de las razones de estos problemas es la fuerte actividad química del aluminio y sus aleaciones, que hace que la superficie sea muy propensa a la formación de películas de óxido, a menudo refractarias. Por ejemplo, el punto de fusión del Al2O3 es 2050 ℃ y el punto de fusión del MgO es 2500 ℃. Además, el aluminio y sus aleaciones tienen una alta conductividad térmica, lo que facilita evitar su fusión durante la soldadura.
La película de óxido, que tiene una densidad similar a la del aluminio, puede formar inclusiones en el metal de soldadura. Además, la película de óxido menos densa con MgO puede absorber más agua y, a menudo, es una causa importante de porosidad de la soldadura. Además, el aluminio y sus aleaciones tienen un gran coeficiente de expansión lineal y una alta conductividad térmica, lo que los hace propensos a deformarse durante la soldadura.
Finalmente, el artículo analiza las grietas relativamente graves que se producen durante las pruebas.
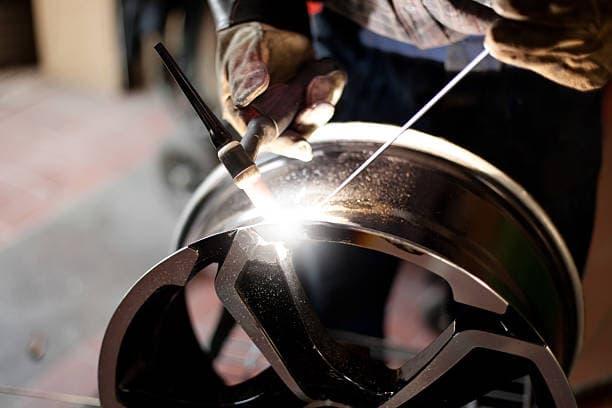
1. Grietas en uniones soldadas de aleaciones de aluminio y sus características.
Durante el proceso de soldadura de aleaciones de aluminio, pueden aparecer diversas grietas en las uniones soldadas debido a diferencias en los tipos, propiedades y estructuras de soldadura de los materiales.
La forma y distribución de estas grietas puede ser bastante compleja.
Según su localización, estas grietas se pueden dividir en dos tipos:
(1) Grietas en el metal de soldadura: grietas longitudinales, grietas transversales, grietas en cráter, grietas en forma de pelo o de arco, grietas de raíz y microfisuras (especialmente en soldadura multicapa).
(2) Grietas en la zona afectada por el calor: grietas de soldadura, grietas laminares y microfisuras térmicas cercanas a la línea de fusión.
Las grietas generadas durante la soldadura se pueden clasificar en grietas calientes y grietas frías, según el rango de temperatura en el que ocurren.
Las grietas en caliente ocurren a altas temperaturas durante la soldadura y son causadas principalmente por la segregación de elementos de aleación en el límite del grano o por la presencia de materiales de bajo punto de fusión.
La forma, el rango de temperatura y las principales causas del agrietamiento en caliente varían según los materiales metálicos soldados.
Las grietas en caliente se pueden dividir en tres tipos: grietas de cristalización, grietas de licuefacción y grietas de poligonización.
Las grietas por cristalización se producen principalmente durante el proceso de soldadura a altas temperaturas. Cerca del solidus, el metal solidificado se contrae, provocando una cantidad insuficiente de metal líquido residual que no puede llenarse con el tiempo, lo que lleva a la generación de grietas.
El agrietamiento intergranular ocurre debido a esfuerzos de contracción por solidificación o fuerzas externas, principalmente en acero al carbono, soldaduras de acero de baja aleación y algunas aleaciones de aluminio con más impurezas.
Las grietas por licuefacción ocurren debido a la tensión de contracción durante la solidificación de los límites de los granos calentados a altas temperaturas en la zona afectada por el calor.
En las pruebas, se encontró que una limpieza insuficiente de la superficie del material de aportación provocaba la presencia de inclusiones y poros en la soldadura después de la soldadura. En la prueba de números de tres grupos, debido a que el material de relleno de soldadura es una estructura fundida y la inclusión es un material de alto punto de fusión, permanece en la soldadura después de soldar.
La estructura de fundición es relativamente escasa, con muchos orificios, lo que facilita la absorción de componentes que contienen agua cristalina y aceite de calidad. Estos factores pueden causar porosidad durante la soldadura, y las inclusiones y los poros se convierten en partes clave que inducen microfisuras cuando la soldadura está bajo tensión de tracción.
Observaciones microscópicas adicionales revelaron una interacción entre estas inclusiones y microfisuras inducidas por poros. Sin embargo, es un desafío determinar si las inclusiones actúan principalmente como una fuente de concentración de tensiones para inducir el agrietamiento o como una fase frágil para inducir el agrietamiento.
Además, se cree ampliamente que la porosidad en las soldaduras de aleaciones de aluminio y magnesio no afecta significativamente la resistencia a la tracción de la soldadura. Sin embargo, este estudio encontró microfisuras y porosidad inducidas por inclusión en las muestras de tracción de soldadura simultáneamente.
Es necesario seguir estudiando si las microfisuras inducidas por poros son un fenómeno secundario asociado o uno de los principales factores que causan una disminución significativa en la resistencia a la tracción de las soldaduras.
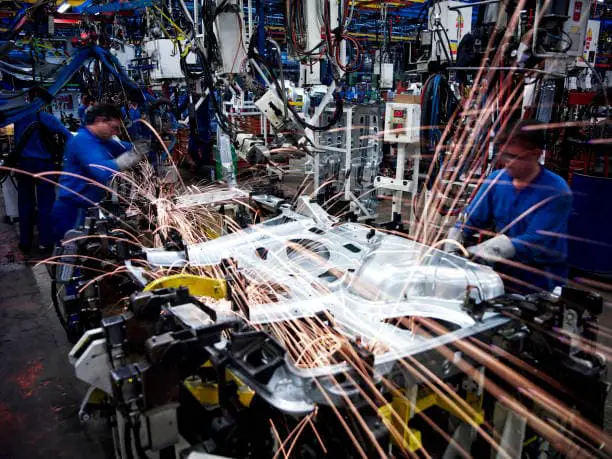
2. Proceso de generación de crack en caliente
Actualmente, la teoría de la soldadura por fisuras en caliente, propuesta por Prokhorov tanto a nivel nacional como internacional, se considera muy refinada.
En resumen, la teoría sugiere que la generación de grietas en el cristal depende principalmente de los siguientes tres factores:
- El tamaño del frágil rango de temperatura.
- La ductilidad de la aleación dentro de este rango de temperatura.
- La tasa de deformación del metal cuando se encuentra en el rango de temperatura frágil.
El tamaño del rango de temperatura frágil y el valor de ductilidad dentro de este rango se denominan comúnmente factores metalúrgicos que pueden producir grietas en caliente en la soldadura, mientras que la tasa de deformación del metal dentro del rango de temperatura frágil se conoce como factor mecánico.
El proceso de soldadura implica una serie de procedimientos tecnológicos desequilibrados. Esta característica está estrechamente ligada a factores metalúrgicos y mecánicos de fractura metálica en uniones soldadas, tales como heterogeneidad física, química y organizativa, escorias e inclusiones, elementos gaseosos y vacantes con concentraciones sobresaturadas de los productos de los procesos tecnológicos y metalúrgicos de soldadura. .
Todos estos factores están estrechamente relacionados con el inicio y desarrollo de grietas en la metalurgia.
En términos de factores mecánicos, el gradiente de temperatura específico y la velocidad de enfriamiento del ciclo térmico de soldadura pueden hacer que la unión soldada se encuentre en un estado complejo de tensión-deformación bajo ciertas condiciones restrictivas, lo que proporciona las condiciones necesarias para el inicio y desarrollo de grietas.
Durante el proceso de soldadura, el efecto combinado de factores metalúrgicos y mecánicos puede fortalecer o debilitar la unión metálica de dos maneras.
Si se establece una fuerte unión en el metal de la junta soldada durante el enfriamiento, la deformación puede permanecer obediente bajo ciertas condiciones de restricción rígida. Cuando la soldadura y el metal cerca de la costura pueden soportar tensiones de restricción externas y tensiones residuales internas, es menos probable que se produzca agrietamiento y la sensibilidad del metal al agrietamiento es baja.
Por otro lado, si no se puede resistir la tensión, es más probable que se rompa la unión resistente del metal, lo que provocará grietas. En este caso, la sensibilidad al agrietamiento del metal de la junta soldada es alta.
El metal de la junta de soldadura se enfría a temperatura ambiente a una cierta velocidad desde la temperatura de solidificación de cristalización. Su sensibilidad al agrietamiento depende de la comparación de la capacidad de deformación y la deformación aplicada, así como de la comparación de la resistencia a la deformación y la tensión aplicada.
Sin embargo, durante el proceso de enfriamiento, diferentes etapas de temperatura pueden dar como resultado diferente resistencia intergranular y crecimiento de la resistencia del grano, diferentes distribuciones de deformación entre y dentro de los granos, diferentes comportamientos de difusión inducida por deformación, diferentes condiciones de concentración de tensiones y factores que conducen a la fragilización del metal. Estos pueden causar diferentes eslabones débiles específicos en las uniones soldadas, y el grado en que se debilitan también puede variar.
La aparición de grietas en el metal de la unión soldada está estrechamente relacionada con factores metalúrgicos y mecánicos.
El gradiente de tensiones en los factores mecánicos está relacionado con el gradiente de temperatura, el cual está determinado por las características del ciclo térmico. La conductividad térmica del metal determina las características del ciclo térmico, que se consideran factores metalúrgicos. Estos incluyen las características de cambio termoplástico del metal, la expansión térmica y la transformación estructural.
El estado tensión-deformación del metal de la unión soldada está muy influenciado por factores metalúrgicos y mecánicos. Además, estos factores cambian a medida que la temperatura disminuye y la velocidad de enfriamiento cambia.
Los diferentes rangos de temperatura afectan de manera diferente la resistencia del metal de la junta soldada. Por ejemplo, es probable que el amplio rango de temperaturas de cristalización y la baja temperatura de solidus provoquen una concentración de tensiones en el metal líquido residual de bajo punto de fusión entre los granos, lo que provoca grietas en el metal sólido. De manera similar, si la contracción es grande, especialmente en condiciones de enfriamiento rápido, es probable que se produzca agrietamiento cuando la tasa de deformación por contracción es alta y el estado tensión-deformación es severo.
Durante la última fase de solidificación y cristalización del metal de soldadura durante la soldadura de aleaciones de aluminio, el eutéctico se comprime en el centro de la intersección del cristal para formar una "película líquida". En este punto, debido a la gran contracción durante el enfriamiento, la contracción libre no está disponible para generar grandes tensiones de tracción. Como resultado, la película líquida forma un eslabón débil, que puede agrietarse en la zona débil bajo el efecto de una tensión de tracción.
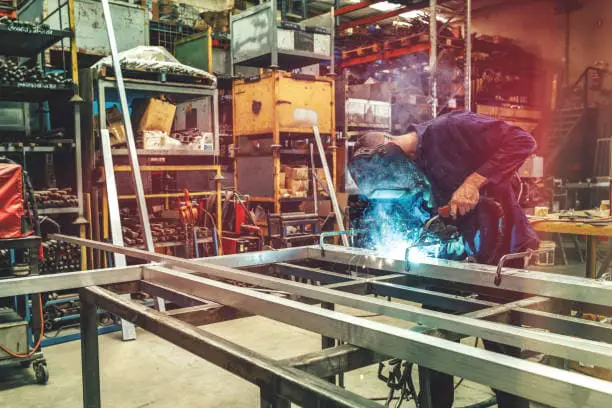
3. Mecanismo de craqueo en caliente
Para investigar la aparición de grietas en caliente al soldar aleaciones de aluminio, el proceso de cristalización del baño de soldadura se clasifica en tres etapas.
La primera etapa es la etapa líquido-sólido, durante la cual hay una pequeña cantidad de núcleos de cristal a medida que el baño fundido de soldadura comienza a enfriarse debido a la alta temperatura. A medida que baja la temperatura y aumenta el tiempo de enfriamiento, los núcleos cristalinos crecen gradualmente y emergen otros nuevos.
Sin embargo, aún predomina la fase líquida y no hay contacto entre granos adyacentes, lo que permite el libre flujo de la aleación de aluminio líquida que aún no se ha solidificado. Por lo tanto, incluso bajo tensión de tracción, cualquier espacio abierto puede llenarse fácilmente con el metal líquido que fluye, lo que hace que la probabilidad de agrietamiento en esta etapa sea muy pequeña.
La segunda etapa es la etapa sólido-líquido. Aquí, la fase sólida en el baño fundido continúa aumentando a medida que avanza la cristalización y los núcleos cristalinos previamente formados continúan creciendo.
Cuando la temperatura desciende hasta cierto punto, los cristales metálicos de aleación de aluminio solidificados entran en contacto entre sí y ruedan juntos continuamente. En esta etapa, el flujo de aleación de aluminio líquido se bloquea y la cristalización del baño fundido pasa a la fase sólido-líquido.
Debido a la pequeña cantidad de metal de aleación de aluminio líquido, la deformación del propio cristal puede desarrollarse fuertemente en esta etapa y la fase líquida residual entre los cristales no es fácil de fluir.
Los pequeños espacios generados bajo tensión de tracción no se pueden llenar, e incluso una pequeña tensión de tracción puede provocar la posibilidad de agrietamiento. Esta etapa se conoce como “zona de temperatura frágil”.
La tercera etapa es la etapa de solidificación completa. Cuando la soldadura formada después de la solidificación completa del metal fundido se somete a tensión de tracción, tiene buena resistencia y plasticidad, y la probabilidad de agrietamiento en esta etapa es relativamente baja.
Por lo tanto, cuando la temperatura es mayor o menor que la zona de temperatura frágil entre ab, el metal de soldadura tiene mayor resistencia al agrietamiento cristalino y menos tendencia al agrietamiento. En general, para metales con menos impurezas (incluidos metales base y materiales de soldadura), el rango de temperatura frágil es estrecho.
La tensión de tracción opera en este rango durante un corto período de tiempo, por lo que la tensión total de soldadura es relativamente pequeña, lo que resulta en una menor tendencia a que se desarrollen grietas durante la soldadura.
Sin embargo, si hay muchas impurezas en la soldadura, el rango de temperatura frágil es relativamente amplio y el tiempo de acción de la tensión de tracción en este rango es relativamente largo, lo que lleva a una mayor tendencia a producir grietas.
4. Medidas de prevención de fisuras por soldadura en aleaciones de aluminio.
Para reducir la probabilidad de grietas en caliente al soldar aleaciones de aluminio, se pueden realizar mejoras a través de dos aspectos: factores metalúrgicos y factores tecnológicos.
En cuanto a los factores metalúrgicos, la prevención de grietas intergranulares en caliente durante la soldadura implica ajustar el sistema de aleación de soldadura o agregar modificadores al metal de aportación.
Para controlar una cantidad adecuada de eutéctico fusible y reducir el rango de temperatura de cristalización desde la perspectiva de la resistencia al agrietamiento, es necesario ajustar el enfoque del sistema de aleación de soldadura.
Debido a que la aleación de aluminio es una aleación eutéctica típica, el rango de temperatura de solidificación "máxima" de la aleación corresponde a la tendencia máxima al agrietamiento.
La presencia de una pequeña cantidad de eutéctico fusible siempre aumenta la tendencia a la formación de grietas por solidificación. Para contrarrestar esto, el contenido de los elementos principales de la aleación normalmente se incrementa más allá del componente de aleación con la máxima tendencia a agrietarse para producir un efecto de "curación".
Además, se añaden al metal de aportación oligoelementos como Ti, Zr, V y B como modificadores en un intento de mejorar la plasticidad y la tenacidad, refinando los granos y evitando el agrietamiento en caliente durante la soldadura. Este intento se viene realizando desde hace algún tiempo y ha dado resultados positivos.
La Figura 3 muestra los resultados de la prueba de resistencia al agrietamiento del alambre de soldadura Al-4,5% Mg con un modificador bajo la condición de una soldadura de filete superpuesta rígida. La prueba incluyó la adición de 0,15% Zr y 0,1% Ti+B. Los resultados indican que la adición simultánea de Ti y B mejoró significativamente la resistencia al agrietamiento.
Ti, Zr, V, B y Ta comparten una característica común: pueden reaccionar con el aluminio para formar una serie de reacciones peritécticas, dando como resultado la formación de compuestos metálicos refractarios como Al3Ti, Al3Zr, Al7V, AlB2, Al3Ta, etc. .
Estas pequeñas partículas refractarias pueden actuar como núcleos cristalinos de solidificación no espontánea durante el proceso de solidificación del metal líquido, facilitando así el refinamiento del grano.
Los factores del proceso, como las especificaciones de soldadura, el precalentamiento, la forma de la unión y la secuencia de soldadura, son cruciales para resolver las grietas de soldadura, que se basan en la tensión de soldadura. Los parámetros del proceso de soldadura impactan el desequilibrio del proceso de solidificación y el estado de la estructura de solidificación, así como la tasa de crecimiento de la deformación durante la solidificación, influyendo así en la formación de grietas.
Los métodos de soldadura que emplean energía térmica concentrada facilitan la soldadura rápida y pueden prevenir la formación de cristales columnares gruesos con fuerte directividad, mejorando así la resistencia al agrietamiento.
Reducir la velocidad de soldadura y emplear una pequeña corriente de soldadura puede disminuir el sobrecalentamiento del baño fundido y mejorar la resistencia al agrietamiento. Sin embargo, aumentar la velocidad de soldadura aumenta la tasa de deformación de las uniones soldadas y la tendencia al agrietamiento en caliente. Por lo tanto, es evidente que al aumentar la velocidad y la corriente de soldadura aumenta la tendencia al agrietamiento.
Durante el montaje y soldadura de estructuras de aluminio, la soldadura no presenta mucha rigidez. Por ello se pueden tomar medidas como soldar secciones, precalentar o reducir la velocidad de soldadura.
El precalentamiento puede reducir la expansión relativa de la muestra y, en consecuencia, disminuir la tensión de soldadura, lo que reduce la tensión en el rango de temperatura frágil. Se debe utilizar en la medida de lo posible la soldadura a tope con ranuras y pequeños espacios, evitando uniones transversales y secuencias de posicionamiento y soldadura inapropiadas. Cuando se completa o se detiene la soldadura, se debe llenar el cráter inmediatamente y retirar la fuente de calor; de lo contrario, es fácil que se produzcan grietas en el cráter.
Durante la soldadura de uniones soldadas multicapa de aleaciones de la serie 5000, a menudo se producen microfisuras debido a la fusión intergranular local, lo que requiere un control de la entrada de calor de soldadura desde la siguiente capa del cordón de soldadura.
Según los hallazgos de este artículo, limpiar la superficie del metal base y el material de relleno es crucial para soldar aleaciones de aluminio. La inclusión de materiales se convierte en la fuente de grietas en la soldadura y la razón principal de la disminución del rendimiento de la soldadura.