Se descubrieron grietas en varias partes de la pared interior del orificio de la llave del reductor y en la cara del extremo del engranaje, en dirección circunferencial, después de operaciones de rectificado de engranajes en una fábrica. El engranaje en sí está hecho de material 18CrNiMo7-6.
El proceso de producción: mecanizado en desbaste → cementación y temple + revenido → acabado (apertura de llave, etc.).
Para determinar la causa de la grieta del engranaje se llevaron a cabo una serie de pruebas y análisis.
1. Proceso de prueba y resultados
1.1 Macroinspección
Se descubrieron grietas en la circunferencia exterior del engranaje, así como en la dirección circunferencial de la pared del orificio interior y la cara del extremo. En algunas grietas de los extremos se levantaron ambos lados, como se muestra en la Figura 1.
Al abrir a lo largo de la grieta se observó la morfología de la fractura. La mayoría de las fisuras presentaban un brillo metálico plateado de porcelana fina y no se identificaron fracturas previas. Se determinó que la esquina de la raíz del chavetero era el origen de las grietas.
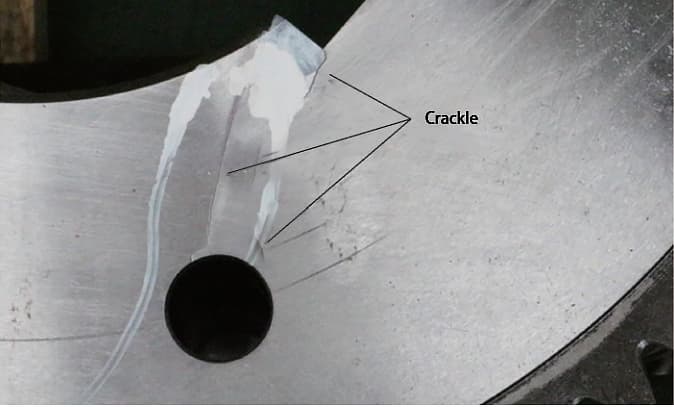
Fig. 1 Ubicación y morfología de las grietas en los engranajes
Se pueden ver patrones radiales obvios y bordes desgarrados alrededor de la fuente de la grieta, lo que indica una morfología de fractura frágil de alta tensión, como se muestra en las Figuras 2 y 3.
El chavetero parece áspero y hay un claro rastro de corte de hilo.
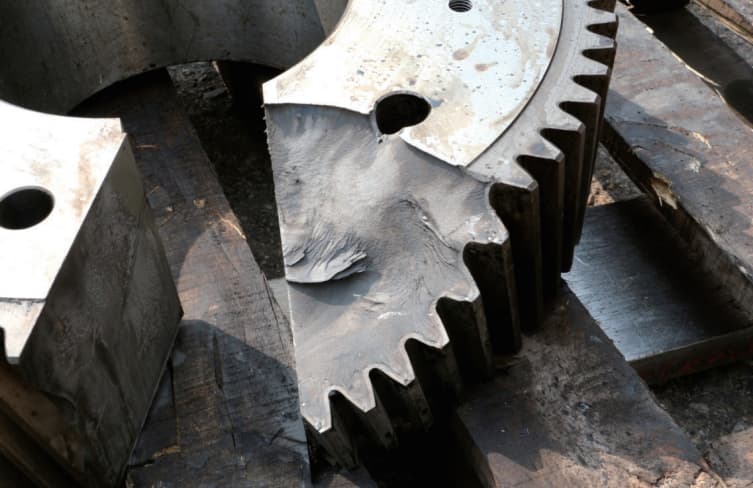
Fig. 2 Macromorfología de la fractura de engranajes.
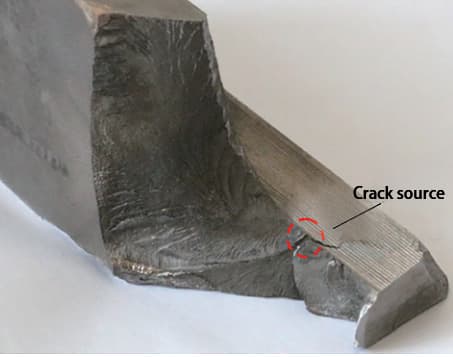
Fig. 3 Ubicación de la fuente de grietas en los engranajes
1.2 Inspección de composición química
La composición química del engranaje se analizó utilizando un espectrómetro de emisión atómica ICP (plasma acoplado inductivamente) y los resultados cumplieron con los requisitos de la norma EN 10084-2008 Condiciones técnicas de entrega para acero carburado.
Consulte la Tabla 1 para obtener los resultados de las pruebas.
Tabla 1 Composición química del engranaje (fracción de masa) (%)
Componente | W. | s | PAG | Minnesota | Sí | cr | No | Mes |
Requisitos estándar | 0,15~0,21 | ≤0,035 | 0.025 | 0,50-0,90 | 0,40 | 1,50~1,80 | 1,40~1,70 | 0,25-0,35 |
engranaje agrietado | 0,18 | 0.002 | 0,016 | 0,76 | 0,23 | 1,68 | 1,62 | 0,27 |
1.3 Inspección de dureza y metalografía.
La capa cementada del engranaje tiene aproximadamente 1,58 mm de profundidad. La dureza promedio de la superficie del diente es 725HV1 y la dureza central es 43.0HRC, todo de acuerdo con los requisitos técnicos del dibujo.
Según el método B en GB/T 10561-2005 Determinación del contenido de inclusiones no metálicas en el acero - Examen micrográfico mediante tabla de clasificación estándar, todos los tipos de inclusiones no metálicas son superiores al grado 0,5.
Según la determinación del tamaño de grano medio de los metales GB/T6394-2017, el tamaño de grano es 6,5.
La capa carburizada del engranaje comprende una pequeña cantidad de carburo de grano fino, martensita acicular gruesa y más austenita retenida.
Según el examen metalográfico GB/T 25744-2010 de cementación, temple y revenido de acero, el carburo se clasifica como Grado 1, la martensita como Grado 5 y la austenita retenida como Grado 6, que no cumplen con los requisitos de GB/T 3480.5 -2008. Cálculo de la capacidad de soporte de engranajes rectos y helicoidales - Parte 5: Resistencia y calidad de los materiales para estructura superficial de acero cementado y contenido de austenita retenida, como se muestra en la Figura 4.

Fig.4 Estructura de la capa carburizada (500 ×)
La muestra se obtuvo cortándola desde el origen de la grieta, puliéndola y luego corroyéndola con una solución corrosiva con ácido nítrico y alcohol al 4%.
Al examen microscópico se observó una capa blanca y brillante en la superficie del chavetero, de apariencia rugosa, con raíz irregular y microfisuras presentes.
La Figura 5 indica que no hay carburación ni descarburación en ninguno de los lados de la microfisura.
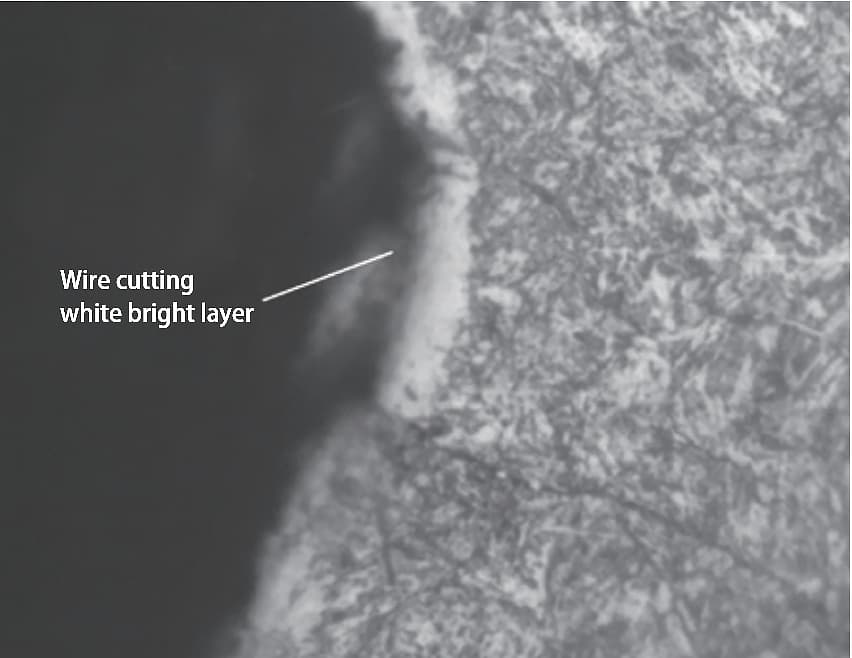
Fig. 5 Cable de corte con capa blanca brillante (500 ×)
2. Análisis y discusión
Se probó el engranaje reductor y los resultados indicaron que la composición del material, la inclusión, el tamaño de las partículas, la dureza y la profundidad de penetración cumplían con los requisitos necesarios.
Las principales razones detrás de la avería del engranaje son las siguientes:
1) La velocidad de corte rápida del alambre produce un chavetero áspero, rastros de mecanizado notables y una forma de filete de transición irregular. Estos factores agravan la concentración de tensiones en el chavetero, lo que lleva a la formación de una fuente de grieta. Posteriormente, bajo tensión de trituración, la grieta se expande gradualmente hasta convertirse en una grieta de engranaje.
Además, una alta velocidad de alimentación del hilo provoca la formación de una capa blanca en la superficie de la llave, que contiene numerosas microfisuras. Estas microfisuras, a su vez, provocan grietas en procesos posteriores.
Durante la fabricación y uso de piezas con esquinas cóncavas afiladas, bordes convexos o muescas, se produce una concentración significativa de tensiones en la transición de estas áreas. Como resultado, se pueden formar grietas.
Además, las marcas rugosas de la herramienta en la superficie mecanizada causadas por la precisión de la máquina herramienta, la forma del borde de la herramienta y la operación durante el procesamiento de la pieza también contribuyen a la concentración de tensiones y degradan el rendimiento.
Tras la inspección, se encontró que la superficie de la chaveta del engranaje era rugosa, con marcas visibles de herramientas de mecanizado. La forma del filete en la raíz de la clave era irregular, lo que provocaba una gran concentración de tensiones.
2)La superficie del chavetero tenía una capa blanca brillante resultante del corte del cable. Esta capa es una capa de enfriamiento que contiene una cantidad significativa de austenita residual, una estructura inestable que puede convertirse en martensita y crear tensiones sustanciales. Cuando se acumula tensión en el hilo de transición, se produce un aumento en la concentración de tensión, lo que lleva a la formación de microfisuras.
Además, la aguja de martensita de la capa carburada es más gruesa y el contenido de austenita residual es excesivo, reduciendo la resistencia del engranaje y aumentando su fragilidad.
Además, la austenita retenida continúa transformándose en martensita enfriada a temperatura ambiente, generando grandes tensiones residuales internas y acelerando el crecimiento de grietas.
3. Conclusiones y sugerencias
Debido a la alta velocidad de corte del alambre del engranaje, la superficie de la llave se vuelve rugosa, la forma del filete de transición se vuelve irregular y se genera una capa blanca brillante en la superficie mecanizada. Esta capa intensifica la concentración de tensiones en el chavetero, formando una fuente de grietas. Bajo la influencia de la tensión abrasiva y la tensión residual, las grietas se expanden gradualmente con el tiempo.
Se recomienda fresar el chavetero antes de cementar. Si es necesario cortar el alambre después de la cementación, se debe controlar la velocidad del alambre para garantizar la forma adecuada del filete de transición en la raíz del chavetero y mejorar la calidad del procesamiento del chavetero. Si no se puede evitar la capa blanca brillante, se debe pulir y eliminar manualmente después de cortar el alambre.