La industria de fabricación de maquinaria cubre una amplia gama de sectores, incluidos el transporte, máquinas herramienta, maquinaria agrícola, maquinaria textil, maquinaria eléctrica e instrumentos de precisión. En general, el proceso productivo implica talleres de fundición, forja, tratamiento térmico, mecanizado y montaje.
El flujo básico de producción consiste en fundición, forja, tratamiento térmico, mecanizado y montaje. En el proceso de fabricación de máquinas, las piezas metálicas generalmente se crean mediante fundición, forja, soldadura, estampado y otros métodos, seguido del corte para producir piezas calificadas y finalmente ensambladas en una máquina.
El mecanizado es el uso de diversas máquinas herramienta para realizar operaciones como torneado, cepillado, taladrado, rectificado, fresado y otros procesamientos en frío de piezas metálicas.
La evaluación y detección de riesgos laborales son cruciales en la industria de la maquinaria, particularmente en el sector de fabricación de maquinaria. Existen muchos peligros potenciales en esta industria y los siguientes puntos resaltan algunos de los factores que requieren atención.
O factores de riesgo laboral
1 . Forjar
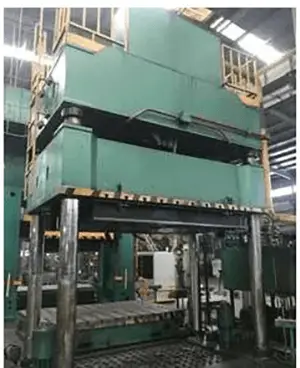
La forja es un proceso en el que se aplica una fuerza externa a una pieza en bruto, lo que provoca deformación plástica y da como resultado la forja.
Riesgos físicos:
El ruido es el riesgo laboral más perjudicial en el proceso de forja. Los martillos de forja (martillos neumáticos y martillos de presión) pueden generar ruidos y vibraciones fuertes e intensas, generalmente en forma de ruido impulsivo, con una intensidad superior a 100 dB (A). Una detección de ruido realizada en el taller de forja de una fábrica de maquinaria arrojó resultados que oscilaron entre 83 y 100,2 dB(A), con una media de 92,08 dB(A). Las punzonadoras y cortadoras también pueden producir ruido de alta intensidad, pero la intensidad suele ser menor que la de los martillos de forja.
La temperatura en el horno de calentamiento puede alcanzar los 1200°C, mientras que la temperatura de forjado oscila entre 500 y 800°C. Durante la producción se pueden producir altas temperaturas y un fuerte calor radiante en el lugar de trabajo.
Peligros de polvo y veneno:
Se puede generar polvo de metal y polvo de carbón durante la carga, descarga y forjado en el horno de forjado y el martillo de forjado, particularmente en los hornos de la industria del combustible. Los hornos de combustión pueden emitir gases nocivos como monóxido de carbono, dióxido de azufre y óxidos de nitrógeno.
dos . Fundición
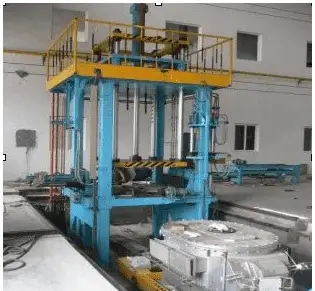
El modelado se puede dividir en moldeado manual y mecánico. El moldeado manual implica completar el exprimido de arena, retirar el molde, cortar y cerrar la caja manualmente. Este proceso requiere mucha mano de obra y expone a los trabajadores directamente al polvo, venenos químicos y factores físicos, lo que genera importantes riesgos laborales. Por otro lado, el moldeo mecánico presenta alta productividad, calidad estable, baja intensidad de mano de obra para los trabajadores y menos posibilidades de que los trabajadores entren en contacto con polvo, venenos químicos y factores físicos, lo que genera riesgos laborales relativamente pequeños.
Peligro de polvo:
Durante el moldeo, la caída de arena y la limpieza se produce una cantidad importante de polvo de arena. La naturaleza y los daños del polvo están determinados principalmente por el tipo de arena de moldeo utilizada. Por ejemplo, cuando se utiliza arena de cuarzo, es más dañina debido a su alto contenido en sílice libre. Una detección de concentración de polvo realizada en el taller de moldeo de una fábrica de maquinaria arrojó resultados que oscilaron entre 27,5 y 62,3 mg/m 3 con un promedio de 39,5 mg/m 3 .
Venenos y peligros físicos:
El secado, fusión y vertido del carbón del molde de arena y del núcleo de arena produce altas temperaturas y radiación de calor. Si se utiliza carbón o gas como combustible, se produce monóxido de carbono, dióxido de azufre y óxidos de nitrógeno. Si se utilizan hornos de inducción de alta frecuencia o hornos microondas para calentar, se producirán campos electromagnéticos de alta frecuencia y radiación de microondas.
3 . Tratamiento térmico
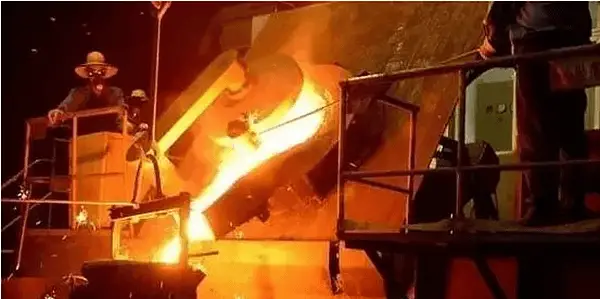
El principal objetivo del proceso de tratamiento térmico es cambiar las propiedades físicas del metal, como dureza, tenacidad, elasticidad, conductividad, entre otras, preservando la forma de las piezas. Esto tiene como objetivo cumplir con los requisitos del proceso y mejorar la calidad del producto.
El proceso de tratamiento térmico cubre la normalización, el temple, el recocido, el revenido y la cementación.
El tratamiento térmico se puede clasificar en tres categorías: tratamiento térmico general, tratamiento térmico superficial (que incluye enfriamiento superficial y tratamiento térmico químico) y tratamiento térmico especial.
Gas toxico
Los procesos de tratamiento térmico de piezas mecánicas, incluyendo normalización, recocido, carburación, enfriamiento y otros, requieren una amplia gama de materiales auxiliares, como ácidos, álcalis, sales metálicas, nitratos y cianuros.
Estos ingredientes son sustancias altamente corrosivas y tóxicas que pueden representar una amenaza importante para el medio ambiente y la salud humana.
Por ejemplo, cuando se utiliza cloruro de bario como medio de calentamiento y la temperatura alcanza los 1300°C, una gran cantidad de cloruro de bario se evapora, creando polvo de cloruro de bario que contamina el aire del taller.
El proceso de cloración también libera una cantidad sustancial de amoníaco al aire del taller.
El ferrocianuro de potasio y otros cianuros se utilizan en los procesos de cementación y carburación, mientras que los óxidos de nitrógeno se producen mediante la interacción del nitrato fundido y la mancha de aceite con la pieza en un horno de baño de sal.
Además, en el proceso de tratamiento térmico se utilizan a menudo agentes orgánicos como metanol, etanol, propano, acetona y gasolina.
Riesgos físicos
La normalización y el recocido de piezas mecánicas son procesos de tratamiento térmico que se llevan a cabo a altas temperaturas. Los hornos de calefacción, los baños de sal y las piezas calentadas en el taller son fuentes de calor.
Estas fuentes de calor pueden crear un ambiente de alta temperatura con una fuerte radiación térmica.
Además, diversos motores, ventiladores, bombas industriales y otros equipos mecánicos pueden generar ruido y vibraciones. Sin embargo, el nivel de ruido en la mayoría de los talleres de tratamiento térmico es bajo y los casos en los que el ruido supera los estándares son raros.
4 . Mecanizado
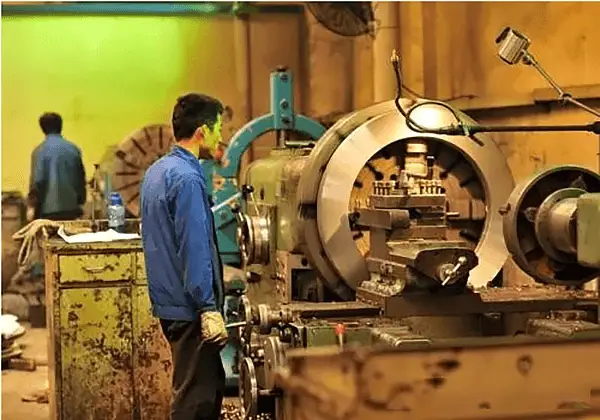
En el proceso de fabricación mecánica, las piezas metálicas se fabrican mediante fundición, forja, soldadura, estampado y otras técnicas. Luego, se utilizan diversas máquinas herramienta, como tornos, cepilladoras, taladradoras, amoladoras, fresadoras y otras, para realizar el procesamiento en frío de las piezas metálicas, incluidos torneado, cepillado, taladrado, rectificado y fresado. Finalmente, las piezas calificadas se cortan y ensamblan en máquinas.
Mecanizado general
Los riesgos laborales en el proceso productivo son mínimos, principalmente por el uso de emulsiones de corte y el impacto del corte en los trabajadores.
Las emulsiones de corte comúnmente utilizadas consisten en aceite mineral, ácido nafténico o ácido oleico y álcali (sosa cáustica). La transferencia a alta velocidad de máquinas herramienta puede provocar salpicaduras de emulsión, que pueden contaminar fácilmente la piel y provocar enfermedades cutáneas como foliculitis o acné.
Durante el proceso de mecanizado, también se genera una cantidad importante de polvo metálico y mineral en el rectificado grueso y fino. Las piedras de afilar sintéticas están compuestas principalmente de esmeril (cristal de alúmina), con un bajo contenido en dióxido de silicio, mientras que las piedras de afilar naturales contienen una gran cantidad de dióxido de silicio libre, lo que puede provocar neumoconiosis y silicosis de aluminio.
La mayoría de las máquinas herramienta producen ruido mecánico que oscila entre 65 dB (A) y 80 dB (A), y los casos de ruido excesivo son raros.
Mecanizado especial
Los factores de riesgo laboral en el mecanizado especializado están relacionados principalmente con las herramientas de mecanizado utilizadas.
Por ejemplo, la electroerosión produce polvo metálico, el procesamiento con láser genera altas temperaturas y radiación ultravioleta, los rayos X con haz de electrones generan polvo metálico, el procesamiento con haz de iones produce polvo metálico, radiación ultravioleta y radiación electromagnética de alta frecuencia, y si se utiliza un electrodo de tungsteno, ionizante. También puede haber radiación.
Por otro lado, el mecanizado electroquímico, el mecanizado por chorro de líquido y el mecanizado ultrasónico tienen riesgos relativamente menores.
Además, el funcionamiento del equipo también puede generar ruido y vibraciones.
5 . Ensamble mecanico
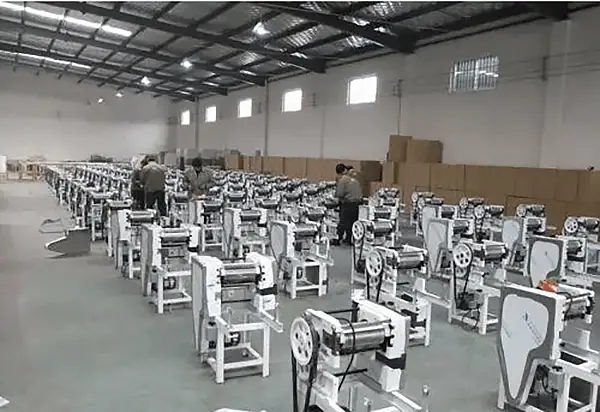
Los factores de riesgo laboral en procesos de montaje mecánico sencillo son pocos y similares a los del mecanizado en general.
Sin embargo, en procesos de montaje complejos, los riesgos laborales están relacionados principalmente con las técnicas de montaje específicas utilizadas.
Por ejemplo, el uso de diversas técnicas de soldadura puede dar lugar a riesgos laborales relacionados con la soldadura, mientras que el uso de adhesivos puede dar lugar a riesgos laborales relacionados con los adhesivos. Si se requiere un proceso de recubrimiento, también puede haber riesgos laborales asociados con el proceso de recubrimiento.
Medidas de protección
Los riesgos laborales en la industria de fabricación de máquinas incluyen principalmente los peligros del polvo de silicio en la producción de fundición, los disolventes orgánicos como el benceno y sus derivados en la producción de recubrimientos y el polvo de soldadura (humo) en las operaciones de soldadura. Para hacer frente a estos peligros, se deben tomar las siguientes medidas:
- Disposición razonable del taller: en el diseño del taller, se deben hacer esfuerzos para minimizar la contaminación cruzada de riesgos laborales. Por ejemplo, el horno de fundición debe estar ubicado al aire libre o alejado de zonas concurridas, y los procesos de remachado, soldadura y pintura deben estar separados.
- Control de polvo: Siempre que sea posible, se debe utilizar arena de moldeo con bajo contenido de sílice libre y se debe reducir el moldeo manual y la limpieza con arena. La limpieza con arena es el proceso con mayor concentración de polvo en la producción de fundición y debe recibir especial atención. Esto se puede lograr instalando sistemas de ventilación y eliminación de polvo de alta potencia y realizando operaciones de pulverización húmeda para reducir la concentración de polvo en el aire del lugar de trabajo. Los trabajadores también deben usar máscaras contra el polvo que cumplan con las normas nacionales pertinentes.
- Antivirus y respuesta a emergencias: Se deben instalar medidas de sellado o dispositivos de ventilación local para equipos que puedan producir toxinas químicas en procesos de tratamiento térmico y fundición de metales. En los lugares de trabajo que producen gases altamente tóxicos como monóxido de carbono, cianuro de hidrógeno, formaldehído y benceno (por ejemplo, ciertos procesos de templado, pintura y pegado), se deben implementar planes de respuesta de emergencia para intoxicaciones ocupacionales agudas, se deben colocar carteles de advertencia y se deben colocar máscaras antigás o respiradores. debe ser provisto.
- Control de ruido: El ruido es un riesgo laboral importante en la industria de fabricación de máquinas y puede controlarse reduciendo el ruido de alta intensidad de equipos como martillos neumáticos, compresores de aire, rectificadoras, pulidoras, estampadoras y equipos de corte. Se deben centralizar las fuentes de ruido de alta intensidad y utilizar protección de aislamiento acústico. Las fuentes de ruido aerodinámico deben amortiguarse al entrar o salir. En las salas de control y salas de postoperatorios se deberán aplicar tratamientos de aislamiento y absorción acústica. Los trabajadores que accedan a los lugares de trabajo con una intensidad sonora superior a 85 dB(A) deberán utilizar tapones para los oídos o protectores auditivos antirruido.
- Control de vibraciones: La vibración es un riesgo laboral común en la industria de fabricación de máquinas. Se deben tomar medidas para reducir la vibración o implementar operaciones de rotación para equipos como remachadoras, prensas de forja, compactadores de arena para moldeo, sistemas de caída de arena y máquinas limpiadoras de arena.
- Protección de radiofrecuencia: Se deben utilizar materiales de protección adecuados para proteger los equipos que producen radiación de alta frecuencia, microondas y otras radiaciones de radiofrecuencia. También se debe proporcionar aislamiento de distancia y protección contra la intemperie.
- Prevención del golpe de calor: Se deben tomar medidas efectivas de enfriamiento y prevención del calor del verano para los trabajadores en entornos de alta temperatura, como fundición, forja y tratamiento térmico. Esto se puede lograr mediante una combinación de tecnología de ingeniería, atención médica y medidas de organización y gestión del trabajo, como la disposición racional de las fuentes de calor, el suministro de bebidas frescas y saladas, el funcionamiento rotativo y el aire acondicionado en las salas de control y quirófano.