En los últimos años, con la sustancial reducción de los precios de los láseres y cabezales de soldadura láser, se ha incrementado la aplicación de la soldadura láser, utilizándose también en la soldadura de armarios de control.
En comparación con el proceso tradicional de soldadura por arco, la soldadura por arco de aparamenta es menos eficiente y requiere un procesamiento posterior a la soldadura sustancial.
La llegada y promoción de la tecnología de soldadura láser ha roto este punto muerto, no sólo mejorando la eficiencia de la soldadura sino también eliminando la necesidad de esmerilado posterior a la soldadura.
Los cordones de soldadura de alta calidad han permitido avances significativos en el proceso de soldadura de armarios de control. Este artículo presenta las tres tecnologías de integración principales de la unidad de soldadura láser del gabinete del panel de distribución, la plantilla y el proceso de soldadura láser.
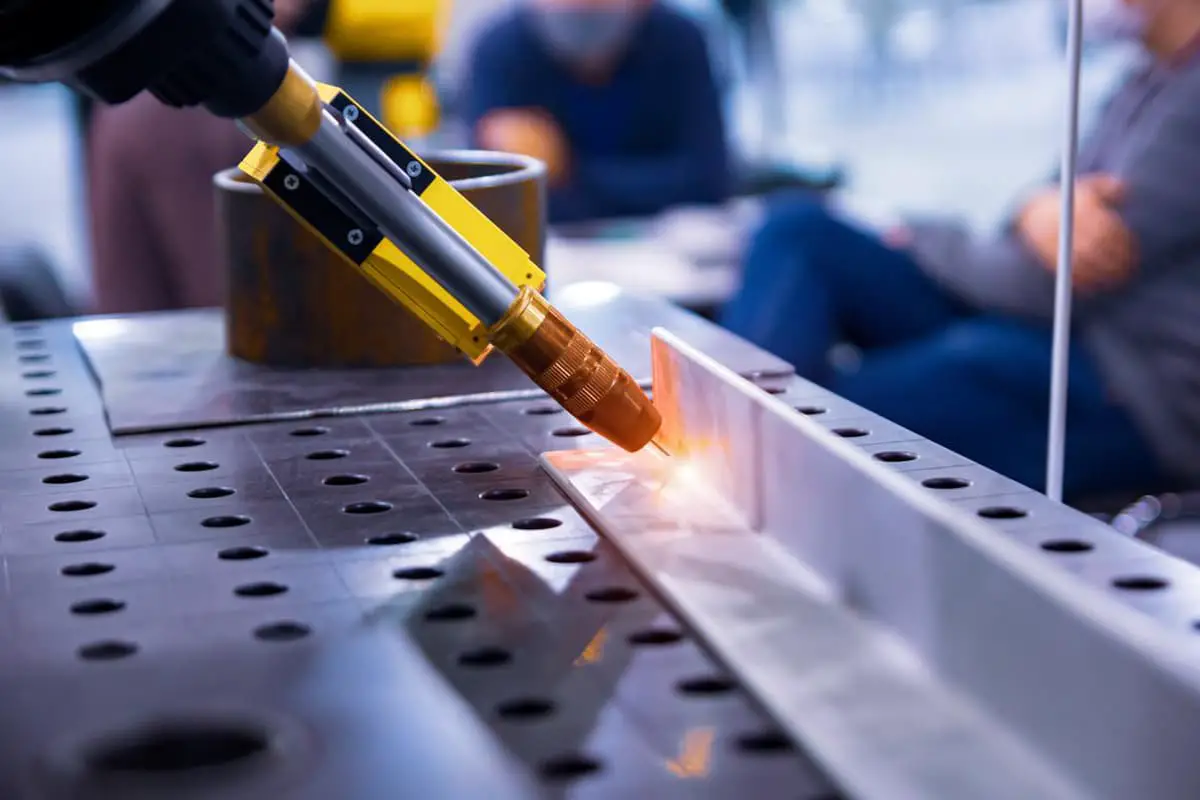
Tecnología de integración de unidades
Las unidades de soldadura de aparamenta suelen emplear soldadura robótica y diseños de máquinas de soldadura dedicadas para la integración de la unidad.
Los diseños de las máquinas de soldar dedicadas generalmente corresponden a uno o varios tipos de piezas, con poca flexibilidad y altos costos. Por el contrario, la soldadura robótica es más flexible, puede adaptarse a una variedad de tamaños y especificaciones de piezas y es relativamente rentable.
El diseño más utilizado es la unidad de soldadura láser robótica de doble estación. Esta unidad suele constar de un robot de seis ejes, un posicionador giratorio de doble estación, un láser y una cabina protectora.
Se utiliza carga manual y se realiza soldadura interna y carga y descarga externa, mejorando así la utilización del equipo y la eficiencia de la producción. Esta es actualmente la disposición de unidad más común para la soldadura de aparamenta.
Como se muestra en la Figura 1, el posicionador giratorio generalmente está equipado con plantillas de sujeción ajustables para cumplir con los requisitos de soldadura de diferentes especificaciones, lo que ofrece una gran versatilidad. Dependiendo de los diferentes requisitos del proceso de soldadura del cliente, también se pueden configurar las formas de las unidades en las Figuras 2 y 4.
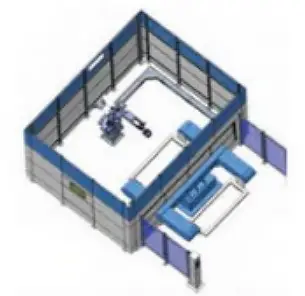
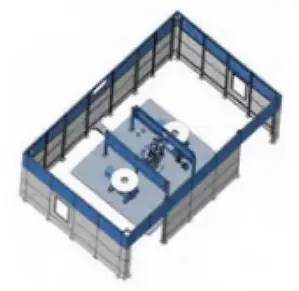
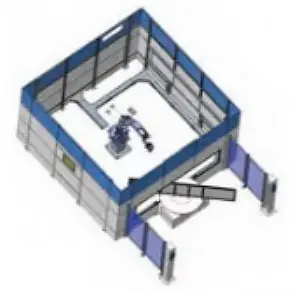
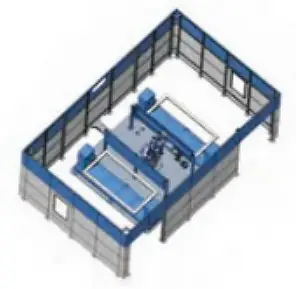
Tecnología de plantilla automática
En la actualidad, la soldadura de armarios de distribución generalmente adopta soldadura por arco; Las piezas individuales se sueldan por puntos antes de someterlas a soldadura continua.
La soldadura por puntos generalmente se realiza manualmente o con plantillas de soldadura por puntos, mientras que la soldadura continua generalmente emplea robots o máquinas de módulos lineales dedicados que utilizan plantillas de soldadura continua.
La soldadura por puntos manual exige una gran cualificación a los trabajadores, ya que debe garantizar tanto el espacio entre las costuras de soldadura como la consistencia de la soldadura por puntos.
La calidad de la soldadura por puntos previa a la soldadura influye en la precisión dimensional y en la calidad del cordón de soldadura de la posterior soldadura general del armario.
Las plantillas de soldadura por puntos se utilizan generalmente para garantizar la holgura y la calidad de las costuras de soldadura, pero su uso afecta significativamente la eficiencia de la soldadura y no es adecuado para soldaduras a gran escala.
La Figura 5 muestra una plantilla de soldadura por puntos para gabinetes de distribución, donde el riel deslizante se ajusta manualmente para adaptarse a diversas especificaciones para la soldadura por puntos de gabinetes.
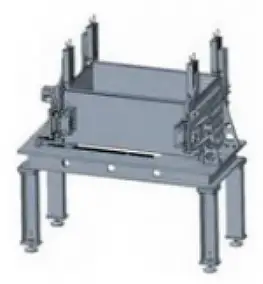
La Figura 6 muestra una plantilla de soldadura continua para gabinete de distribución, que posiciona la pieza soldada por puntos, la fija mediante un cilindro y un módulo lineal, y realiza la soldadura continua de varias especificaciones de gabinetes a través de un módulo lineal y un módulo giratorio.
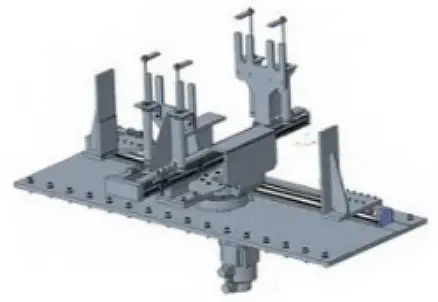
Las plantillas automáticas pueden lograr la sujeción, el posicionamiento y la soldadura automáticos de piezas individuales, pero requieren dimensiones espaciales, diseños estructurales, transmisión y control más grandes.
Un gabinete de distribución típico generalmente se compone de tres subcomponentes, incluida la placa plegable del gabinete y dos placas de sellado laterales. El espesor de la lámina es generalmente de solo 1,5 mm (que varía según el fabricante) de lámina de acero al carbono, como se muestra en la Figura 7.
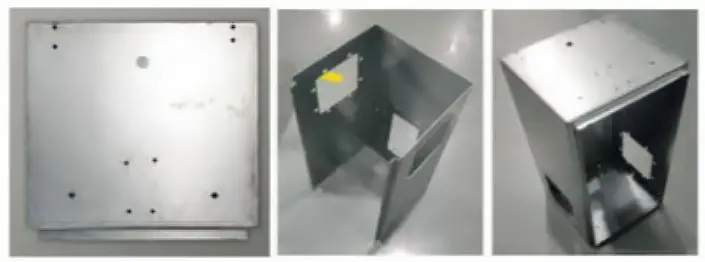
Los gabinetes de aparamenta vienen en una variedad de especificaciones y tamaños, y todos son placas delgadas. Para realizar la soldadura láser, primero se debe resolver el soporte interno de la placa doblada del gabinete, asegurando que el soporte interno impida las piezas después de soldar. El soporte interno y el prensado externo deben poder ajustarse automáticamente en función de diferentes especificaciones y tamaños.
Para piezas de gran tamaño, se deben considerar las cuestiones del soporte auxiliar intermedio y la rigidez de sujeción, así como resolver la consistencia de los espacios largos en las costuras de soldadura y la precisión de posicionamiento repetitivo de la ubicación de soldadura de la pieza.
No debe haber costuras excesivamente grandes que puedan causar problemas con la resistencia y calidad de la soldadura láser.
Finalmente, a través de un diseño de estructura espacial restringida, se debe dejar espacio para soldar, permitiendo que el robot suelde en la postura más ideal.
La Figura 8 muestra una plantilla de soldadura láser para gabinete de distribución automática, que puede realizar funciones como soporte interno, evitar piezas y prensado externo para diferentes tamaños y especificaciones de gabinete.
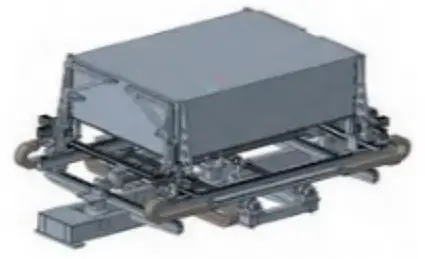
Proceso de soldadura láser
Además de garantizar los espacios libres de montaje y la precisión del posicionamiento de la costura de soldadura a través de los accesorios, la estructura de la pieza debe ajustarse adecuadamente para cumplir con los requisitos del proceso de soldadura láser del gabinete.
Al agregar ranuras de posicionamiento a la placa de flexión y a la placa final en la etapa preliminar, la calidad de la soldadura del gabinete en la etapa posterior ha mejorado significativamente.
Sin embargo, el tamaño de la ranura afectará la calidad de las costuras de soldadura posteriores. A través de pruebas, hemos logrado un tamaño de ranura satisfactorio. Al realizar pruebas por lotes con este tamaño de ranura, la resistencia y la estética de las costuras de soldadura cumplieron con los requisitos del cliente, como se muestra en la Figura 10.
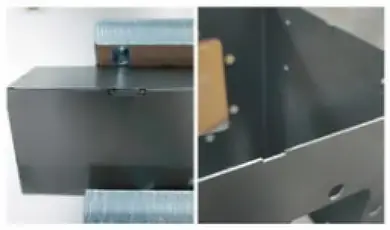
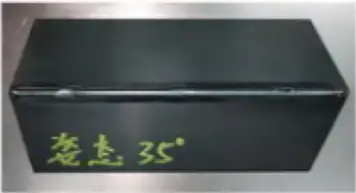
Al emplear soldadura de filete láser, se elimina la necesidad de esmerilado posterior a la soldadura, lo que mejora la eficiencia de la soldadura y la estética del gabinete. Sin embargo, la soldadura de filete impone requisitos estrictos en cuanto a la distancia de enfoque y el ángulo de incidencia de la soldadura.
Una gran cantidad de pruebas de soldadura han demostrado que el filete autofundible requiere un punto grande para cubrir las placas superior e inferior, por lo que se ve un gran desenfoque. Al obtener el mismo tamaño de punto, la posición de soldadura del cabezal de soldadura de enfoque de 300 mm está más alejada de la lente protectora, lo que es más seguro.
Simultáneamente, bajo desenfoque negativo, el cabezal de soldadura de enfoque de 300 mm se puede combinar con el componente de soplado coaxial del cabezal de soldadura de 200 mm, asegurando que la costura de soldadura aún esté protegida por el gas bajo un desenfoque grande.
Numerosas pruebas han demostrado que cambiar el ángulo libre a 35° produce los mejores resultados de soldadura. La Figura 11 compara los efectos de la soldadura en diferentes ángulos de incidencia.
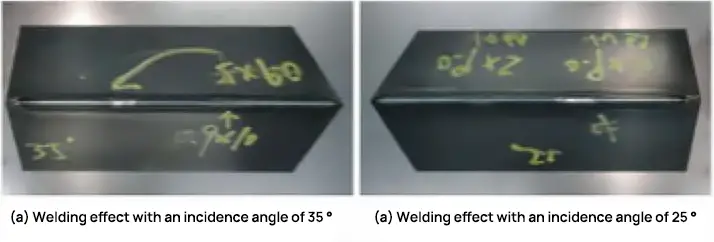
Envuélvelo
(1) La soldadura láser del cuerpo del gabinete de distribución utiliza una unidad de soldadura láser robótica de doble estación para lograr la soldadura interna y la carga y descarga externa, mejorando la utilización del equipo y la eficiencia de la producción.
(2) La soldadura láser del cuerpo del gabinete de distribución está equipada con un dispositivo automático dedicado, que permite todas las funciones, como soporte interno para diferentes tamaños de especificaciones, evitación de piezas y fijación externa.
(3) La soldadura láser del cuerpo del gabinete de distribución adopta una estructura de ranura de posicionamiento y un proceso de soldadura en ángulo, lo que elimina la necesidad de rectificado posterior a la soldadura, mejora la eficiencia de la soldadura y la estética del gabinete y resuelve el problema de la mala calidad de la soldadura de la distribución. cuerpo del gabinete.