La soldadura por arco de argón es un método de soldadura por arco eléctrico con el gas inerte "argón" como gas protector.
Se rocía argón desde la boquilla para formar una capa protectora de gas inerte en el área de soldadura para aislar la invasión de aire y proteger el arco y el baño de soldadura.
Este método de soldadura tiene muchas ventajas:
- Buen efecto de protección, alta calidad de soldadura, sin salpicaduras y hermosa formación de soldadura;
- Pequeña deformación de soldadura, puede realizar soldadura de un lado y conformado de doble cara, garantizar la penetración de la raíz y puede soldar en múltiples posiciones;
- Puede soldar diversos metales y aleaciones;
- Combustión de arco estable, operación de arco abierto, sin escoria, automatización fácil de realizar.
Por lo tanto, se ha utilizado ampliamente en la producción práctica.
Sin embargo, debido a la escasa resistencia al viento de la soldadura por arco de argón, es particularmente sensible al óxido, el agua y el aceite, y tiene requisitos estrictos en cuanto a pureza del gas, limpieza de ranuras y proceso de soldadura, lo que facilita la formación de poros.
Combinado con la práctica de producción, esta publicación analiza el problema de la porosidad en la soldadura por arco de argón e introduce algunos métodos de tratamiento y cuidado.
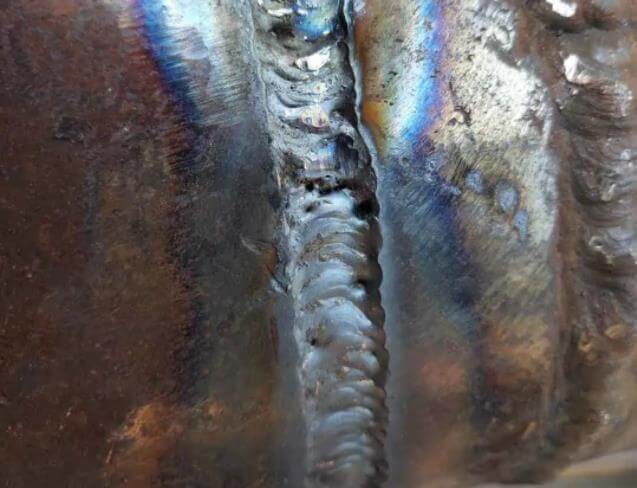
I. Características y peligros de los poros de gas.
1.1 Características de los poros de gas
Los poros de gas son cavidades que se forman en las costuras de soldadura cuando las burbujas de gas en el baño fundido no pueden escapar durante la solidificación, un defecto de soldadura común e importante en la soldadura por arco de argón TIG. Sus formas pueden ser esféricas, ovaladas, espirales o de gusano.
Los que están dentro de la costura de soldadura se denominan poros de gas internos, mientras que los expuestos en la superficie de la costura son poros de gas externos. El tamaño de los poros del gas varía; pueden existir individualmente, agruparse o distribuirse continuamente a lo largo de la costura.
1.2 Peligros de los poros de gas
Los poros de gas, al ser defectos volumétricos, afectan significativamente el rendimiento de la costura de soldadura. Reducen principalmente la capacidad de carga de la costura. Esto ocurre porque los poros del gas ocupan un cierto volumen de la costura de soldadura, reduciendo el área transversal efectiva de trabajo y, en consecuencia, el rendimiento mecánico de la costura.
Esto reduce particularmente la plasticidad de la costura, así como su resistencia a la flexión y al impacto. Si los poros de gas penetran la superficie de la costura de soldadura, especialmente si penetran la superficie en contacto con el medio, el medio existirá dentro de las cavidades.
Cuando el medio es corrosivo, se produce corrosión concentrada, lo que hace que las cavidades se vuelvan más profundas y más grandes hasta que se produce la penetración de la corrosión y las fugas. Esto compromete la integridad de la costura de soldadura y, en casos graves, puede provocar la destrucción de toda la estructura metálica.
Por lo tanto, se debe prestar gran atención a prevenir los poros de gas en la costura de soldadura y garantizar la calidad de la soldadura.
II. Formación de poros de gas
2.1 Formación de poros de gas
Durante todo el proceso de soldadura, los alrededores del baño de soldadura se llenan de gases complejos, principalmente del aire circundante y de impurezas en la pieza de trabajo, como óxido, pintura y grasa, que producen gases cuando se calientan.
Todos estos interactúan continuamente con el charco de metal fundido. Algunos gases ingresan al charco fundido a través de reacciones químicas o disolución, lo que hace que el metal líquido en el charco fundido absorba cantidades significativas de gas. Si estos gases se expulsan rápidamente, incluso si el baño de soldadura cristaliza rápidamente, no se formarán poros de gas.
Sin embargo, si se forman gases durante el proceso de cristalización del baño fundido y el proceso de cristalización es demasiado rápido para que los gases escapen, permanecerán en la costura de soldadura y formarán poros de gas.
2.2 Factores que influyen en la formación de poros de gas
La formación de poros de gas en los cordones de soldadura TIG es a menudo el resultado de la acción combinada de varios gases, siendo el H 2 y el 2 los protagonistas principales. Un análisis detallado es el siguiente:
Efectos del H2 :
El H 2 en la zona de soldadura proviene de varias fuentes. Algunas composiciones, agua cristalina e impurezas en la superficie de la pieza contienen componentes de hidrógeno. Además, el proceso de fundición del acero también contiene hidrógeno.
Bajo las altas temperaturas del arco eléctrico, estos componentes forman burbujas que se disipan rápidamente hacia el exterior. Si el H 2 no puede fluctuar durante el proceso de enfriamiento de la costura de soldadura, se formarán poros de gas.
Efectos del N 2 :
El N 2 proviene principalmente del aire. El porcentaje en peso de N 2 en los metales básicos y los alambres de soldadura no es muy alto y existe en el acero y otras aleaciones de hierro como soluciones de óxido sólido y otras formas.
La solubilidad del N2 en el acero varía drásticamente con la temperatura y el N2 precipitado forma burbujas que se expulsan del baño de soldadura. Las burbujas que no pueden ser expulsadas a tiempo permanecen en la costura de soldadura y forman poros de gas. La formación de poros de gas ocurre cuando el arco y el metal en el baño de soldadura se exponen al aire sin protección suficiente.
III. Factores que influyen en los estomas.
1. El argón es impuro
Al soldar acero al carbono, la pureza del argón no debe ser inferior al 99,7%, al soldar aluminio, no debe ser inferior al 99,9% y la pureza del argón utilizado para soldar titanio y aleaciones de titanio es de hasta el 99,99%.
Método para detectar la pureza del argón:
(l) Suelde la placa o el tubo de acero pulido sin alambre de soldar y luego vuelva a fundirlo en el cordón de soldadura varias veces. Si hay poros, indica que el argón es impuro.
(2) Durante la soldadura, hay una chispa muy pequeña alrededor del arco, lo que también indica que el argón es impuro.
(3) A veces, cuando la pureza del argón está cerca de los requisitos de pureza de los requisitos de soldadura, no se puede detectar mediante los dos métodos de detección anteriores, pero al soldar juntas soldadas con espacios, se generarán poros intermitentes en la raíz de la soldadura. o se generarán poros en la superficie durante la soldadura por superposición, o hay una capa de óxido en la superficie del cordón de soldadura.
(4) Suelde algunos puntos de la placa de níquel. Si la mancha es de color blanco plateado y la superficie parece un espejo, indica que la pureza del argón está calificada.
2. flujo de argón
El flujo de argón es muy pequeño y la capacidad de interferencia antiviento es débil;
Demasiado grande, el caudal de gas es demasiado grande y el flujo laminar cercano a la pared que se forma al pasar a través de la boquilla es demasiado fino.
Una vez expulsado el gas, rápidamente se desordenará y será fácil envolver el aire, lo que deteriorará el efecto protector del baño de soldadura.
Por tanto, el flujo de argón debe ser apropiado para estabilizar el flujo de gas.
3. Fuga de aire en el cinturón de aire.
Las fugas de aire en la interfaz de la correa neumática o en la correa neumática provocarán un flujo de gas muy pequeño durante la soldadura y el aire será aspirado hacia la correa neumática, lo que dará como resultado un efecto de protección deficiente.
4. Influencia del viento
Si el viento es ligeramente fuerte, la capa protectora de argón formará turbulencias, lo que dará como resultado un efecto de protección deficiente.
Por lo tanto, se deben tomar medidas de protección contra el viento cuando la velocidad del viento sea > 2 m/S;
Al soldar tuberías, el orificio de la tubería debe bloquearse para evitar la ventilación hacia la tubería.
5. Influencia de la boquilla de la pistola de soldar
El diámetro de la boquilla es demasiado pequeño. Cuando el rango de protección efectiva del argón alrededor del arco es menor que el área del baño de soldadura, provocará una protección insuficiente y producirá poros.
Especialmente para operaciones en campo y soldadura de tuberías grandes, se deben usar boquillas de mayor diámetro para proteger eficazmente el arco y el baño de soldadura.
6. Distancia entre la boquilla de la pistola de soldar y la pieza de trabajo
La distancia es pequeña y la sensibilidad al viento cruzado es pequeña;
La distancia es grande y la capacidad para resistir la interferencia del viento es pobre.
7. La presión en el cilindro es demasiado baja.
Cuando la presión en el cilindro de gas sea inferior a 1MPa, se debe detener.
8. El ángulo de la pistola de soldar es demasiado grande.
Si el ángulo de la pistola de soldar es demasiado grande, por un lado, entrará aire en el baño de soldadura y, por otro lado, el flujo de argón en el lado del arco largo deteriorará el efecto de protección del arco y del baño de soldadura.
9. Influencia del caudalímetro de hidrógeno.
La salida de gas inestable del medidor de flujo, ya sea grande o pequeña, afectará el efecto de protección.
10. Impacto de la operación
Cuando utilice la pistola de soldadura por arco de argón con botón de control, ventile el gas antes de soldar para evitar una presión excesiva en la zona de gas, lo que provocará un flujo de gas excesivo instantáneo y orificios de aire durante el encendido del arco.
11. Accesorios inadecuados para pistolas de soldar
La abrazadera del electrodo de tungsteno no es compatible, el camino del gas bloqueado no es suave y el gas protector fluye desde un lado de la boquilla, lo que no puede formar un anillo protector completo.
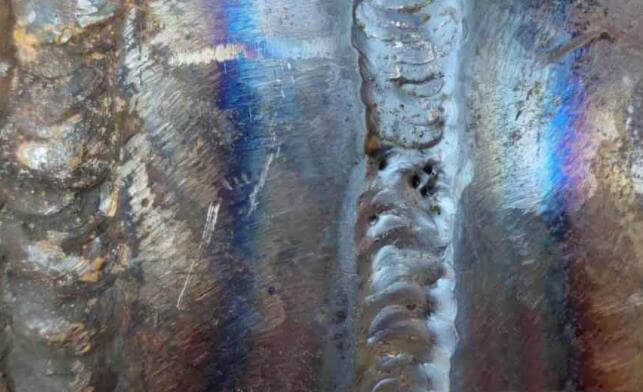
4. Influencia de los materiales de soldadura.
1. Influencia del tipo de alambre de soldadura
El alambre de soldadura por arco sumergido no debe usarse para reemplazar el alambre de soldadura TIG manual, de lo contrario se generarán poros intermitentes o continuos.
2. El alambre de soldadura no está limpio.
El óxido, las manchas de aceite y el agua en la superficie del alambre de soldadura promoverán directamente una gran cantidad de poros en la soldadura.
V. Influencia del material metálico básico
1. Influencia de la calidad de la placa o del tubo.
Si hay una capa intermedia en la placa o tubo, las impurezas en la capa intermedia promoverán la generación de defectos de poros.
2. Influencia del tipo de acero
El acero en ebullición (con un alto contenido de oxígeno y muchas impurezas) no se puede soldar mediante soldadura por arco de argón.
SIERRA. Influencia del electrodo de tungsteno.
1. Influencia de la parte extrema del tungsteno.
La parte extrema del tungsteno no es afilada, la deriva del arco es inestable, el área protectora de argón se destruye y el metal en el baño fundido se oxida para producir poros.
2. Protección deficiente debido al arco que se eleva durante el encendido del arco.
Cuando se utiliza equipo de cebado de arco de alta frecuencia, la temperatura de la parte extrema del tungsteno es baja al inicio del cebado del arco, por lo que no tiene suficiente capacidad de emisión térmica electrónica.
Los electrones se emiten fácilmente desde el sitio de la película de óxido y ascienden a lo largo del electrodo hasta encontrarse con el sitio de óxido.
En este momento, el arco se alarga y el efecto protector del argón sobre el baño de soldadura empeora.
Cuando la temperatura del electrodo de tungsteno aumenta, se emiten electrones desde el extremo frontal del electrodo de tungsteno.
La longitud del arco y la deformación de fase son cortas.
En este momento, el óxido de la superficie del electrodo de tungsteno se puede eliminar siempre que se pula y limpie.
VII. Influencia del proceso de soldadura
1. Limpieza de surcos
La superficie de la ranura y la tira de 10 mm en ambos lados de la ranura deben pulirse para evitar que el imán generado por el arco durante la soldadura succione el óxido cerca del charco fundido hacia el charco fundido.
2. Influencia de la velocidad de soldadura
La velocidad de soldadura es muy rápida.
Debido a la influencia de la resistencia del aire en el flujo de gas de protección, el flujo de gas argón se doblará y se desviará del centro del electrodo y del baño de soldadura, lo que no es bueno para el baño de soldadura ni para el blindaje del arco.
3. Influencia del método de extinción del arco.
Durante la extinción del arco, se debe adoptar el método de extinción del arco mediante la atenuación de la corriente o la adición de alambre de soldadura, llevando el arco al lado de la ranura y reduciendo el arco.
No detenga el arco repentinamente, lo que resultaría en la separación del baño fundido de alta temperatura de la protección efectiva del flujo de gas argón, para evitar poros o contracción en el pozo del arco.
4. Influencia de la corriente de soldadura.
La corriente de soldadura es demasiado pequeña, el arco es inestable y el arco se desvía irregularmente en el extremo del electrodo de tungsteno, dañando la zona protectora.
Si la corriente de soldadura es demasiado grande, el arco perturbará el flujo de aire y el efecto de protección empeorará.
5. Influencia de la longitud de extensión del electrodo de tungsteno
Si el electrodo de tungsteno se extiende durante mucho tiempo, el efecto protector del argón sobre el arco y el baño de soldadura empeorará.
VIII. Medidas para prevenir la formación de porosidad.
Aunque existen varias causas de la porosidad, elegir el proceso de soldadura adecuado y mejorar las habilidades operativas del soldador son formas clave de evitarla.
1. Tratamiento previo a la soldadura de la pieza de trabajo y del alambre de soldadura.
La soldadura TIG es especialmente sensible al aceite, el óxido y el agua, lo que puede provocar fácilmente porosidad, por lo que se requiere una alta calidad superficial del material base. Es fundamental realizar una limpieza rigurosa antes de soldar, puliendo el área entre 10 y 15 mm dentro y fuera del bisel de la pieza de trabajo para eliminar las películas de óxido de la superficie, impurezas como aceite y humedad, y exponer el brillo metálico.
Asimismo, es necesario lijar el aceite y el óxido de la superficie del alambre de soldadura hasta que el metal brille.
2. Pureza del argón
El argón es un gas inerte que no se descompone a altas temperaturas ni reacciona con el metal de soldadura para provocar oxidación. Durante la soldadura por arco de argón, la pureza del argón debe ser superior al 99,95%. Además, cuando la presión dentro del cilindro de argón cae por debajo de 2,0 MPa y el contenido de humedad aumenta, se debe suspender su uso.
El caudal de argón debe ser el adecuado, determinado por la siguiente fórmula empírica: Q=K·D, donde Q representa el caudal de argón, D es el diámetro de la boquilla y K es un coeficiente (0,8-1,2). Por lo tanto, el caudal de argón es generalmente de 6 a 9 l/min. El recorrido del gas también debe mantenerse libre de obstrucciones, sin que se produzcan obstrucciones ni fugas.
3. Diámetro de la boquilla
El diámetro de la boquilla se puede determinar mediante la siguiente fórmula empírica: D = (2,5-3,2) d, donde D representa el diámetro de la boquilla y el diámetro del electrodo de tungsteno. Según esta fórmula, el diámetro de boquilla adecuado suele ser de 6 a 12 mm.
4. Longitud de extensión del electrodo de tungsteno
Si la longitud de extensión del electrodo de tungsteno es demasiado grande, la distancia entre la boquilla y la pieza de trabajo aumenta, lo que reduce el efecto protector. Por otro lado, si la longitud de la extensión es demasiado corta, aunque el efecto de protección puede ser bueno, puede obstruir la línea de visión del soldador y provocar que el electrodo de tungsteno y el alambre de soldadura choquen, provocando un cortocircuito e impidiendo la soldadura.
5. Velocidad de soldadura
La velocidad de soldadura es uno de los principales parámetros de soldadura. Si la velocidad es demasiado rápida, el gas protector pasará por alto el electrodo de tungsteno y la piscina, lo que reducirá el efecto de protección y la porosidad. También puede afectar la formación de la costura de soldadura, por lo que se debe seleccionar una velocidad de soldadura adecuada durante la soldadura.
6. Flujo previo y posterior al gas
Enviar argón 3 a 4 segundos antes del inicio del arco puede expulsar el aire del tubo, lo que garantiza que el arco se inicie en un ambiente protegido por gas y evita que el electrodo de tungsteno y el charco se oxiden y creen poros. Retrasar el corte de gas puede proporcionar una piscina enfriada y protegida, así como también prevenir defectos como picaduras de arco, grietas y porosidad en el punto de terminación del arco. Por lo tanto, es fundamental dominar el método correcto de extinción del arco.
7. Habilidades operativas
El dominio de las habilidades operativas es un paso vital para prevenir la porosidad, y todo soldador debe poseer una base sólida de estas habilidades esenciales. El soplete, el alambre y la pieza de trabajo deben mantener una posición y un ángulo relativo correctos, con movimientos coordinados.
Durante la soldadura, el arco debe ser estable, con una altura constante, y las fluctuaciones bruscas están estrictamente prohibidas para evitar que el gas entre instantáneamente en el baño de soldadura y cause porosidad. Al mismo tiempo, es importante observar cambios en el baño fundido para aumentar la capacidad de expulsar la porosidad.
Al soldar en todas las posiciones, el soplete, el alambre y la pieza de trabajo deben mantener una cierta distancia entre sí. La dirección es generalmente de abajo hacia arriba, es decir, en el orden del plano superior (vertical). Al apagar el arco, es fundamental evitar la aparición de ranuras y agujeros de contracción, asegurando que la costura de soldadura no sea inferior al material base.
Esto se puede lograr aumentando la costura de soldadura, es decir, disminuyendo la velocidad de soldadura al apagar el arco, aumentando la inclinación hacia atrás del soplete y aumentando la alimentación del alambre cuando la temperatura del baño de soldadura es demasiado alta. Si es necesario, el arco se puede extinguir y volver a encender hasta que se llene el pozo del arco.
En conclusión, la soldadura TIG por arco de argón tiene excelentes características de soldadura. La práctica de producción a largo plazo ha demostrado que la adopción de las medidas de proceso mencionadas anteriormente puede controlar eficazmente la generación de porosidad, mejorando significativamente la tasa de detección de fallas por primera vez y la calidad de la junta soldada.
IX. Conclusión
Aunque hay muchos factores que causan poros en la soldadura TIG manual, siempre que comprendamos las características de la soldadura por arco de argón, investigaremos los factores que influyen uno por uno según la situación real y eliminaremos todos los factores que causan poros en la soldadura TIG manual. soldar durante la soldadura por arco de argón, podemos mejorar la calidad de la soldadura en la producción real.