1. Preámbulo
42CrMo es una aleación de acero de alta resistencia conocida por sus excelentes propiedades mecánicas, como alta resistencia y tenacidad, buena templabilidad y falta de fragilidad debido al revenido.
Después del templado y revenido, tiene un alto límite de fatiga, resistencia al impacto y buena tenacidad al impacto a bajas temperaturas, lo que lo hace ideal para fabricar componentes de acero de tamaño grande y mediano que requieren resistencia y tenacidad.
Nuestra empresa eligió acero 42CrMo para fabricar un pivote grande, y el proceso de fabricación implica los siguientes pasos: forjado en bruto, normalización, mecanizado en desbaste, enfriamiento y revenido, acabado, círculo de endurecimiento por inducción y círculo de rectificado.
La estructura de pivote se ilustra en la Figura 1.
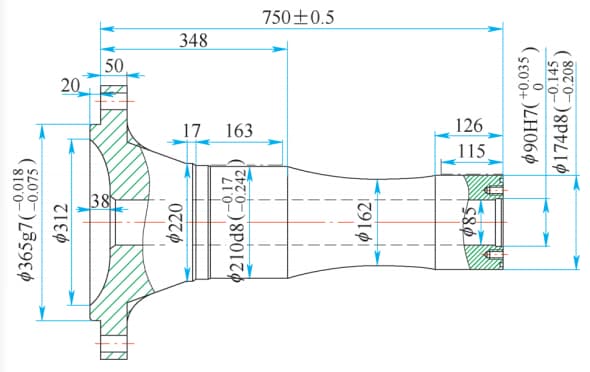
Fig. 1 Estructura pivotante
2. Descripción general de piezas defectuosas
Pueden ocurrir grietas en el eje de pivote durante los procesos de enfriamiento, revenido y enfriamiento.
La grieta suele aparecer en el área del arco de transición entre la raíz del eje de pivote y la brida.
Todo el eje de pivote se rompe a lo largo de la dirección radial y se extiende hasta la brida del extremo de biela.
El eje de pivote podría romperse por completo. Consulte la Fig. 2 para conocer la forma y ubicación de la grieta.
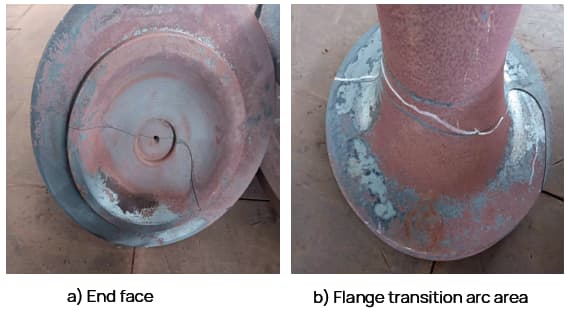
Fig.2 Morfología de la grieta después del temple, revenido y temple.
El proceso de enfriamiento y revenido de esta pieza implica mantenerla a 840 ℃ durante 3 horas, seguido de enfriamiento con aceite una vez que se retira del horno. El tiempo de enfriamiento es de 30 minutos y se utiliza aceite Houghton K como aceite de enfriamiento.
Se han producido varios lotes de este producto sin agrietarse.
Para analizar las causas de las grietas, se tomó muestra de una parte fisurada del ala del extremo grande y se analizó su composición química, estructura metalográfica y grietas. Se tomaron muestras de la grieta de la brida (ver Fig. 3) para su análisis.
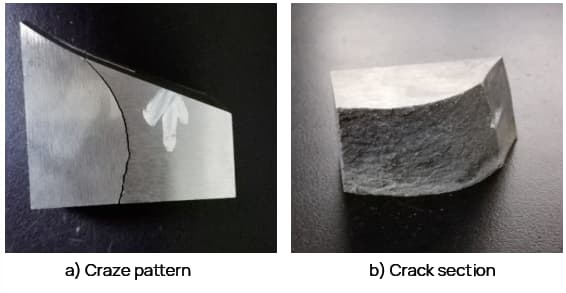
Fig. 3 Muestreo de bridas
Consulte la Tabla 1 para obtener los resultados del análisis de composición química.
Tabla 1 Composición química (fracción de masa) del pivote de acero 42CrMo (%)
Elemento | Valor estandar | Valor medido |
W. | 0,38~0,45 | 0,43 |
Sí | 0,17~0,37 | 0,28 |
Minnesota | 0,5~0,8 | 0,68 |
s | ≤0,035 | 0.007 |
PAG | ≤0,035 | 0,016 |
cr | 0,9 ~ 1,2 | 1 |
Mes | 0,15~0,25 | 0,2 |
No | ≤0,30 | 0.034 |
Culo | ≤0,30 | 0,046 |
Alabama | – | 0.026 |
La estructura metalográfica se muestra en la Fig.
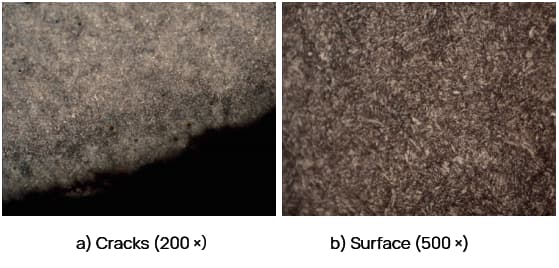
Fig. 4 Grieta metalográfica y estructura superficial
Los resultados del análisis indican que la composición química del acero 42CrMo cumple con los requisitos técnicos. La dureza superficial medida es 296 HBW, que se encuentra dentro del rango requerido de 277-331 HBW. La estructura metalográfica es de sorbita templada y la estructura central es de sorbita templada+ferrita.
La grieta en la pieza tiene forma de arco y no hay descarburación en ninguno de los lados de la grieta, lo que indica que no hubo grieta antes del templado y revenido, y no se observaron otras anomalías.
Los analistas físicos y químicos atribuyen la grieta a una tensión excesiva durante el temple, revenido y temple, según la muestra.
Sin embargo, debido al tamaño de la pieza y al desafío del muestreo, el autor sugiere que la posición de corte de la muestra puede ser el área de crecimiento de la grieta y no la ubicación de inicio de la grieta, lo que requiere un análisis más detallado.
Como la fuente de la grieta no se puede identificar a través de la superficie de la fractura, se propone cortar la pieza para localizar la fuente de la grieta. El corte con llama o plasma puede afectar el sitio de la fractura; por lo tanto, se recomienda el corte con alambre para cortar el sitio de la grieta en la zona de transición del eje de la pieza defectuosa.
Cuando el corte alcanza 1/3 del diámetro, el eje de pivote se divide en dos secciones, permitiendo un análisis más profundo de la causa de la grieta.
3. Análisis de las causas del crack.
La morfología de la fractura después del corte con alambre se muestra en la Fig.
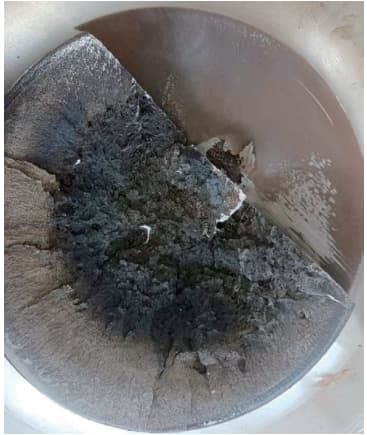
Fig. 5 Posición de la fractura después de cortar el alambre
El centro de la fractura aparece de color marrón, mientras que el exterior tiene un color metálico normal. El color marrón en el centro es anormal y probablemente causado por oxidación.
El análisis indica que probablemente existían grietas en el centro de la pieza antes del enfriamiento, revenido y los procesos posteriores de forjado, normalización y enfriamiento. Las grietas habrían sufrido oxidación durante estos procesos, provocando una decoloración marrón.
Para confirmar esta hipótesis, se tomó una muestra de la zona marrón y se analizó. La muestra se cortó desde el centro en dirección axial. Después del corte y procesamiento, se encontró que numerosas grietas estaban distribuidas radialmente, como se ilustra en la Figura 6.
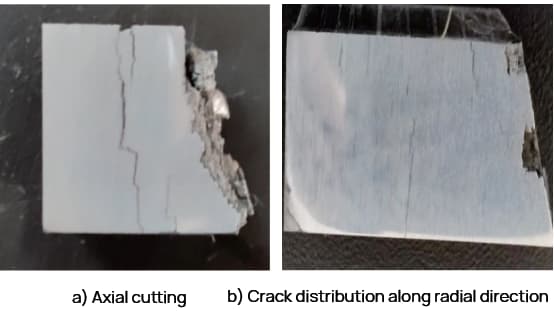
Fig. 6 Ubicación de la fractura de fisura
El análisis de la muestra muestra que la muestra tiene una estructura de bandas obvia (Grado 4), como se muestra en la Fig.
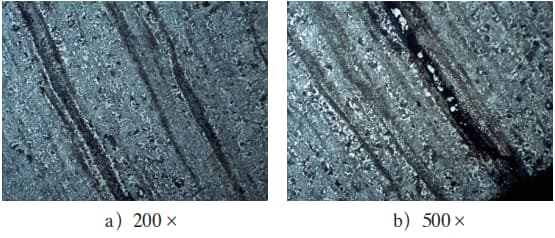
Fig. 7 Estructura metalográfica del centro de grieta.
Las grietas, que son múltiples y aproximadamente paralelas, se distribuyen a lo largo de la dirección de la estructura de bandas y perpendicularmente a la dirección de forjado.
El autor cree que había grietas presentes antes del proceso de templado y revenido del eje de pivote, y estas grietas estaban ubicadas en el centro, sin grietas visibles en la superficie.
Durante el proceso de templado y revenido, las grietas se expandieron debido a la influencia del estrés organizativo y térmico, y la estructura de bandas también jugó un papel importante.
Como resultado, es necesario realizar análisis adicionales para determinar si hubo problemas como una temperatura de forjado insuficiente y una velocidad de forjado irrazonable durante el proceso de forjado.
Para evitar que entren al mercado piezas defectuosas, se investigaron exhaustivamente los productos en proceso.
Todos los productos en proceso se han sometido a pruebas END utilizando un detector de fallas ultrasónico.
Después de la investigación, se descubrieron dos productos anormales y se verificaron sus números de serie de producción.
Resultó que los números de serie de producción de los dos productos anormales eran parte del mismo lote de piezas forjadas que contenían las piezas agrietadas.
Para validar el análisis y juicio inicial, se realizó un corte con alambre en las piezas anormales encontradas a lo largo de la dirección axial.
La superficie de corte reveló claramente la presencia de varias grietas detalladas, perpendiculares a la dirección de forjado, como se ilustra en la Fig.
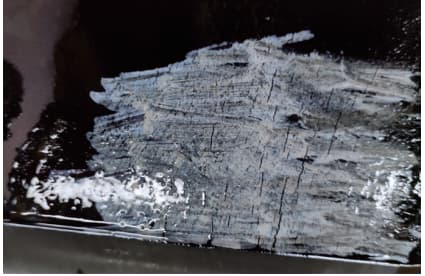
Fig. 8 Superficie de corte de piezas defectuosas
Mediante comprobaciones adicionales se concluyó que la grieta se generó durante el forjado.
4. Conclusión
1)La fractura del eje de pivote se puede atribuir directamente a la grieta de forja formada durante el proceso de forja de la pieza. Esta grieta se expandió durante el enfriamiento y revenido, y la presencia de una estructura en bandas también contribuyó a su crecimiento.
2)Al realizar un análisis de falla, es importante localizar cuidadosamente la fuente de la grieta. Diferentes ubicaciones de muestreo pueden afectar significativamente los resultados del análisis. Por tanto, es fundamental analizar e identificar la causa desde el origen para evitar desviaciones.
3) Reforzar la inspección entrante de las materias primas es crucial para evitar que piezas defectuosas entren en el proceso de producción.