1. ¿Cuáles son las características de la estructura cristalina primaria de la soldadura?
Responder:
La solidificación de un baño fundido de soldadura también sigue los principios fundamentales de la solidificación general de metales líquidos, que implica la formación de núcleos cristalinos y su crecimiento.
A medida que el metal líquido en el baño de soldadura se enfría y solidifica, los granos parcialmente fundidos en el metal base en la zona de fusión generalmente sirven como sitios para la nucleación de cristales.
Posteriormente, estos núcleos cristalinos atraen y absorben átomos del líquido circundante, lo que lleva al crecimiento de cristales.
Debido a que los cristales crecen en la dirección opuesta a la conducción de calor y en dos direcciones opuestas, pero están obstruidos por cristales en crecimiento vecinos, los cristales resultantes adoptan una forma columnar y se denominan cristales columnares.
En circunstancias específicas, el metal líquido en el baño fundido también puede sufrir una nucleación espontánea durante la solidificación.
Si la disipación de calor se produce en todas las direcciones, los cristales crecerán uniformemente en todas direcciones, formando cristales equiaxiales.
Aunque normalmente se observan cristales columnares en la costura de soldadura, también pueden aparecer cristales equiaxiales en el centro de la soldadura bajo ciertas condiciones.
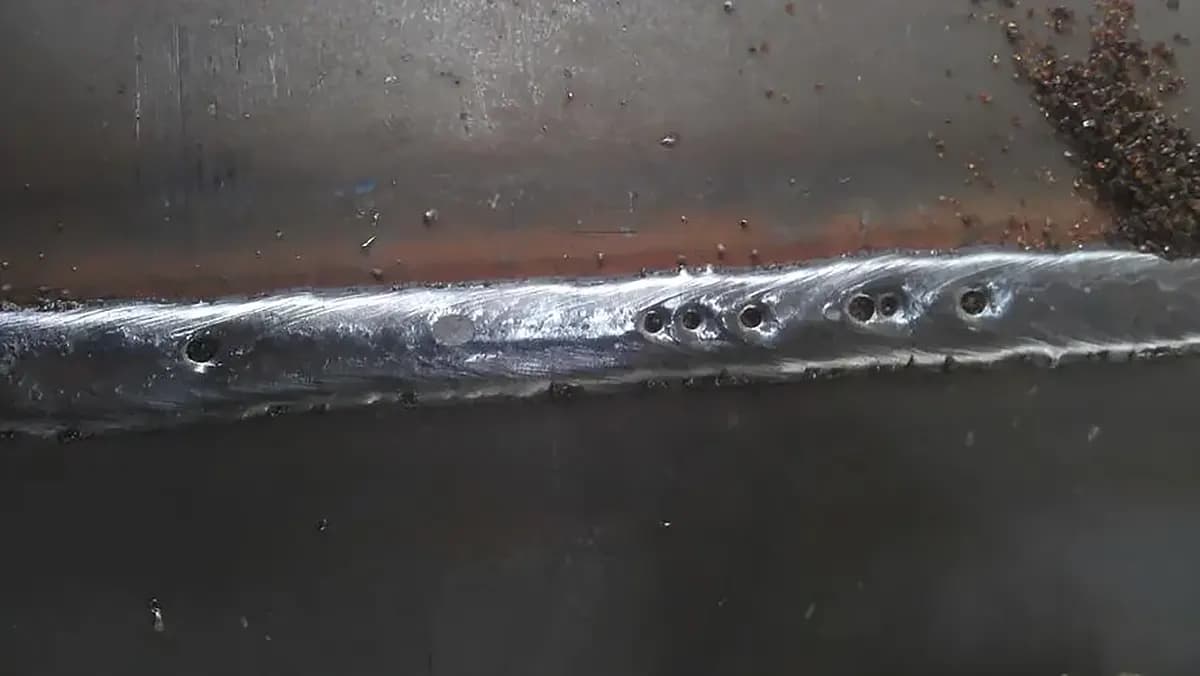
2. ¿Cuáles son las características de la estructura de cristalización secundaria de la soldadura?
Responder:
Después de la cristalización primaria, el metal de soldadura continúa enfriándose por debajo de la temperatura de transformación de fase, provocando un cambio en su estructura metalográfica.
Por ejemplo, al soldar acero con bajo contenido de carbono, los granos cristalinos primarios son austeníticos. A medida que la temperatura desciende por debajo del punto de transformación, la austenita se descompone en ferrita y perlita. En consecuencia, la estructura después de la cristalización secundaria está compuesta principalmente de ferrita con una pequeña cantidad de perlita.
Sin embargo, debido a la rápida velocidad de enfriamiento de la soldadura, el contenido de perlita obtenido es generalmente mayor que el encontrado en la estructura de equilibrio. Cuanto mayor sea la velocidad de enfriamiento, más significativo será el contenido de perlita.
El contenido reducido de ferrita da como resultado un aumento de la dureza y la resistencia, pero una disminución de la plasticidad y la tenacidad. La estructura real a temperatura ambiente se obtiene después de una cristalización secundaria.
Diferentes condiciones de soldadura y tipos de acero pueden producir diferentes microestructuras de soldadura.
3. Tomemos como ejemplo el acero con bajo contenido de carbono para explicar qué estructura se obtiene después de la cristalización secundaria del metal de soldadura.
Responder:
Tomemos como ejemplo el acero de bajo contenido plástico, que tiene una estructura cristalina primaria austenítica.
El proceso de transformación de la fase sólida en el metal de soldadura se conoce como cristalización secundaria del metal de soldadura, que da como resultado una microestructura de ferrita y perlita.
En la estructura de equilibrio del acero con bajo contenido de carbono, el contenido de carbono en el metal de soldadura es muy bajo, lo que da como resultado una estructura columnar gruesa de ferrita con una pequeña cantidad de perlita.
Sin embargo, debido a la alta velocidad de enfriamiento durante la soldadura, la ferrita no puede precipitar completamente según el diagrama de fases hierro-carbono, lo que resulta en un mayor contenido de perlita que en la estructura plana.
La velocidad de enfriamiento durante la soldadura también determina el tamaño del grano, la dureza y la resistencia del metal. Se obtienen granos más finos con velocidades de enfriamiento más altas, lo que da como resultado una mayor dureza y resistencia, pero la disminución de ferrita y el aumento del contenido de perlita pueden conducir a una plasticidad reducida.
Por lo tanto, la microestructura final de la soldadura está determinada por la composición del metal y las condiciones de enfriamiento durante la soldadura.
Debido a la naturaleza del proceso de soldadura, la estructura del metal de soldadura es fina, lo que da como resultado mejores microestructuras y propiedades que en el estado fundido.
4. ¿Cuáles son las características de soldar metales diferentes?
Responder:
1)Las características de la soldadura de metales diferentes se definen principalmente por las diferencias significativas en la composición de la aleación del metal depositado y la soldadura. El comportamiento del charco de soldadura varía según la forma de la soldadura, el espesor del metal base, el recubrimiento o fundente del electrodo y el tipo de gas protector utilizado.
Como resultado, la cantidad de fusión del metal base es diferente y también se ve afectada la dilución mutua de la concentración de componentes químicos en el área de fusión del metal depositado y el metal base. Por lo tanto, el grado de falta de uniformidad de uniones soldadas de metales diferentes con respecto a la composición química regional depende no sólo de la composición original de las soldaduras y materiales de relleno, sino también del proceso de soldadura utilizado.
2)Después del ciclo de soldadura térmica, aparecerán diferentes estructuras metalográficas en cada zona de la unión soldada debido a la falta de homogeneidad de la estructura. Esto está relacionado con la composición química, el método de soldadura, la capa de soldadura, el proceso de soldadura y el tratamiento térmico del metal base y el material de aportación.
3)La falta de uniformidad en el rendimiento, resultante de las diferentes composiciones químicas y estructuras metálicas de la junta, conduce a diferencias significativas en las propiedades mecánicas de la junta.
La resistencia, dureza, plasticidad y tenacidad de cada zona a lo largo de la unión pueden ser muy diferentes. En la zona afectada por el calor a ambos lados de la soldadura, el valor del impacto puede diferir varias veces. El límite de fluencia y la resistencia a altas temperaturas también pueden variar mucho debido a diferencias en composición y estructura.
4)La no uniformidad de la distribución del campo de tensiones y la distribución de las tensiones residuales en diferentes juntas metálicas está determinada principalmente por la diferente plasticidad de cada área de la junta.
Además, la diferencia en la conductividad térmica del material puede provocar un cambio en el campo de temperatura del ciclo térmico de soldadura. Los diferentes coeficientes de expansión lineal en cada región y otros factores son razones de la distribución desigual del campo de tensiones.
5. ¿Cuáles son los principios de selección de materiales de soldadura para soldar diferentes aceros?
Responder:
Los principios de selección para diferentes materiales de soldadura de acero incluyen principalmente los siguientes cuatro puntos:
- Cuando la resistencia y plasticidad del metal de soldadura no sean críticas, seleccione materiales de soldadura con buena plasticidad, asegurándose de que la unión soldada no desarrolle grietas u otros defectos.
- Las propiedades del metal de soldadura de diferentes materiales de soldadura de acero deben cumplir los requisitos técnicos de al menos uno de los dos metales base.
- Los materiales de soldadura deben tener un buen rendimiento del proceso y producir soldaduras visualmente atractivas. Los materiales de soldadura deben ser asequibles y fácilmente disponibles.
Lectura relacionada: Soldabilidad de materiales metálicos.
6. ¿Qué pasa con la soldabilidad del acero perlítico y del acero austenítico?
Responder:
El acero perlítico y el acero austenítico son dos tipos distintos de acero con diferentes estructuras y componentes. Al soldar estos dos tipos de acero, el metal de soldadura se crea fusionando dos tipos diferentes de metales base y materiales de relleno, lo que puede generar desafíos de soldabilidad.
1) Dilución de soldaduras.
El acero perlítico contiene elementos de baja aleación que pueden diluir la aleación general del metal de soldadura.
El efecto de dilución del acero perlítico reduce el contenido de elementos formadores de austenita en la soldadura.
Como consecuencia, la soldadura puede desarrollar una estructura martensítica, lo que puede afectar negativamente a la calidad de la unión e incluso provocar grietas.
2) Formación de capas de transición.
Durante el ciclo térmico de soldadura, el grado de mezcla entre el metal base fundido y el metal de aportación varía en el borde del baño fundido.
En esta ubicación, el metal líquido se caracteriza por una baja temperatura, baja fluidez y un corto tiempo de residencia en estado líquido.
Debido a diferencias significativas en la composición química entre el acero perlítico y el acero austenítico, el metal base fundido y el metal de aportación no pueden fundirse adecuadamente en el borde del baño fundido en el lado perlítico.
En consecuencia, las soldaduras en el lado del acero perlítico contienen una proporción significativa de metal base perlítico, y la proporción aumenta cerca de la línea de fusión.
Esto crea una capa de transición con diferentes componentes internos del metal de soldadura.
3) Se forma una capa de difusión en la zona de fusión.
En el metal de soldadura compuesto por estos dos tipos de aceros, el acero perlítico tiene un mayor contenido de carbono, pero un menor contenido de elementos de aleación que el acero austenítico.
Por otro lado, en la zona de fusión, la diferencia de concentración de los elementos formadores de carbono y carburo se forma en ambos lados del acero perlítico en el caso del acero austenítico.
Cuando la junta funciona a una temperatura superior a 350-400 ℃ durante un período prolongado, la zona de fusión exhibirá una difusión de carbono obvia, es decir, difusión desde el lado del acero perlítico hasta la soldadura austenítica a través de la zona de fusión.
Como resultado, se forma una capa descarburada ablandada sobre el metal base del acero perlítico cerca de la zona de fusión, y se forma una capa descarburada correspondiente a la descarburación en un lado de la soldadura austenítica.
4) Debido a que las propiedades físicas del acero perlítico y del acero austenítico son muy diferentes, la composición de la soldadura también es muy diferente.
Este tipo de unión no puede tratarse térmicamente para eliminar la tensión de soldadura. El tratamiento térmico sólo puede provocar una redistribución de tensiones, lo que es muy diferente a soldar el mismo metal.
5) Agrietamiento retardado.
Durante el proceso de cristalización, el baño fundido creado al soldar diferentes aceros contiene estructuras de austenita y ferrita que están estrechamente relacionadas entre sí.
Debido a que el gas puede difundirse fácilmente en este proceso, el hidrógeno difusible puede acumularse y provocar un craqueo retardado.
7. ¿Cuáles son las medidas para prevenir grietas durante la soldadura de reparación de hierro fundido?
Responder:
(1) Precalentamiento antes de soldar y enfriamiento lento después de soldar
Precalentar la pieza soldada en su totalidad o parcialmente antes de soldar y enfriarla lentamente después de soldar puede reducir la tendencia a la porosidad de la pieza soldada y minimizar la tensión de soldadura, evitando así que la pieza soldada se agriete.
(2) Se adopta la soldadura por arco frío para reducir la tensión de soldadura.
Para evitar grietas, se seleccionan como metales de aportación materiales de soldadura con buena plasticidad, como níquel, cobre, níquel-cobre y acero con alto contenido de vanadio. Esto permite que el metal de soldadura alivie la tensión mediante la deformación plástica.
La reducción de la tensión de soldadura se puede lograr mediante el uso de electrodos de diámetro delgado, corriente pequeña, soldadura intermitente y técnicas de soldadura dispersa para disminuir la diferencia de temperatura entre la soldadura y el metal base. Además, martillar la soldadura puede ayudar a eliminar la tensión y prevenir grietas.
(3) Otras medidas: ajustar la composición química del metal de soldadura para reducir su rango de temperatura frágil;
Para mejorar la reacción metalúrgica de desulfuración y desfosforización en la soldadura, se deben agregar elementos de tierras raras. Además, agregar elementos de grano refinado Zengna refinará los granos de soldadura.
En algunos casos, el método de la zona de tensión por calentamiento se utiliza para reducir la tensión en el área donde se está reparando la soldadura. Este método también es eficaz para prevenir la aparición de grietas.
Lectura relacionada: ¿Cómo soldar hierro fundido?
8. ¿Qué es la concentración de estrés? ¿Cuáles son los factores que causan la concentración del estrés?
Responder:
Debido a las características desconocidas de la forma del cordón de soldadura y del propio cordón de soldadura, se produce una discontinuidad en la forma colectiva, lo que conduce a una concentración de tensiones cuando se carga. Esta concentración de tensión provoca una distribución desigual de la tensión de trabajo de la unión soldada, lo que da como resultado un pico de tensión local σmax que es mucho mayor que la tensión promedio σm.
Hay muchas razones para la concentración de tensiones en la soldadura, siendo los defectos del proceso un factor importante. La entrada de aire, las inclusiones de escoria, las grietas y la penetración incompleta en la soldadura pueden causar concentración de tensiones, siendo las grietas de soldadura y la penetración incompleta las más graves.
Otros factores que contribuyen a la concentración de tensiones incluyen la apariencia irrazonable de la soldadura, como el refuerzo excesivo de las soldaduras a tope y los extremos altos de las soldaduras en filete, y el diseño irrazonable de las calles, como los cambios repentinos en las interfaces de las calles o el uso de juntas superiores con placas de cubierta.
Las disposiciones poco razonables de las uniones de soldadura también pueden causar concentración de tensiones. Por ejemplo, las uniones en T con solo soldaduras pueden provocar una concentración de tensiones.
9. ¿Qué es la falla plástica y cuáles son sus peligros?
Responder:
La falla plástica puede resultar en inestabilidad plástica (deformación o fluencia plástica significativa) o fractura plástica (fractura de borde o fractura dúctil).
El proceso comienza con la deformación elástica de la estructura soldada bajo carga, seguida de fluencia, deformación plástica (inestabilidad plástica), microfisuras o huecos, macrofisuras, crecimiento inestable y finalmente fractura.
En comparación con la fractura frágil, es menos probable que se produzca fractura plástica en ambientes fríos por las siguientes razones:
(1) Se produce una deformación plástica irrecuperable después de la fluencia, lo que inutiliza las estructuras soldadas con requisitos de alto tamaño.
(2) Para los recipientes a presión fabricados con materiales de alta tenacidad y baja resistencia, la falla no está controlada por la tenacidad a la fractura de los materiales, sino que es causada por la inestabilidad plástica debido a una resistencia insuficiente.
Los daños plásticos pueden invalidar la estructura soldada, provocando accidentes catastróficos que afectan la producción empresarial, provocan víctimas innecesarias y perjudican gravemente el desarrollo económico nacional.
10. ¿Qué es una fractura frágil y cuáles son sus daños?
Responder:
La fractura frágil generalmente se refiere a la fractura por disociación (incluida la fractura de cuasi disociación) y la fractura del límite de grano (intergranular) que se divide a lo largo de un determinado plano cristalino.
La fractura por escisión, por otro lado, es un tipo de fractura intragranular que ocurre cuando los materiales se separan a lo largo de un plano cristalográfico específico dentro del cristal.
Bajo ciertas condiciones, como baja temperatura, alta tasa de deformación y alta concentración de tensión, los materiales metálicos pueden sufrir fractura por escisión cuando la tensión alcanza un cierto valor.
Existen varios modelos que explican la generación de fracturas por clivaje, muchos de los cuales están relacionados con la teoría de las dislocaciones.
En general, se cree que cuando el proceso de deformación plástica de los materiales se ve gravemente afectado, los materiales no pueden adaptarse a las tensiones externas mediante la deformación y, en cambio, se separan, lo que provoca grietas por escisión.
Las inclusiones, los precipitados quebradizos y otros defectos en los metales también juegan un papel importante en la generación de grietas por escisión.
La fractura frágil ocurre típicamente cuando la tensión no es mayor que la tensión de diseño permitida de la estructura y no hay deformación plástica significativa. Puede propagarse rápidamente por toda una estructura, causando daños repentinos que son difíciles de detectar y prevenir con anticipación, lo que a menudo resulta en lesiones personales y pérdidas de propiedad.
11. ¿Cuál es el papel de las grietas de soldadura en la fractura frágil estructural?
Responder:
De todos los defectos, las grietas son las más peligrosas. Cuando se somete a cargas externas, se produce una pequeña deformación plástica cerca del frente de la grieta y se produce una cierta cantidad de desplazamiento de apertura en la punta, lo que hace que la grieta se desarrolle gradualmente.
Si la carga externa aumenta a un nivel crítico, la grieta se expandirá a gran velocidad. En este punto, si la grieta está ubicada en una zona de alta tensión de tracción, a menudo resulta en una fractura frágil de toda la estructura.
Sin embargo, si la grieta extendida ingresa a un área con baja tensión de tracción, habrá suficiente energía para mantener una mayor expansión de la grieta, o la grieta ingresa a un material con mejor tenacidad (o el mismo material con mayor temperatura y mayor tenacidad). donde recibe mayor resistencia.
Si la grieta no puede continuar expandiéndose, el daño causado por la grieta se reducirá en consecuencia.
12. ¿Cuáles son las causas de las fracturas frágiles de estructuras soldadas?
Responder:
Las causas de la fractura se pueden resumir en tres aspectos:
(1) La humanidad de los materiales es insuficiente
La capacidad de deformación microelástica del material es especialmente débil, especialmente en la punta de la entalla.
La falla frágil bajo tensión baja generalmente ocurre a temperaturas más bajas y la tenacidad de los materiales disminuye drásticamente a medida que disminuye la temperatura.
Además, con el avance de los aceros de baja aleación y alta resistencia, el índice de resistencia aumenta, mientras que la plasticidad y la tenacidad disminuyen.
En muchos casos, la fractura frágil se origina en la zona de soldadura, lo que hace que la falta de tenacidad en la soldadura y la zona afectada por el calor sean la principal causa de falla frágil bajo tensión baja.
13. ¿Cuáles son los principales factores que se deben considerar al diseñar estructuras soldadas?
Responder :
Las principales consideraciones para uniones soldadas son las siguientes:
- La unión soldada debe tener suficiente tensión y rigidez para garantizar una larga vida útil.
- Se deben considerar el entorno de trabajo y las condiciones de las uniones soldadas, como temperatura, corrosión, vibración y fatiga.
- La carga de trabajo del precalentamiento previo a la soldadura y el tratamiento térmico posterior a la soldadura debe minimizarse para miembros estructurales grandes.
- La soldadura debería requerir poco o ningún mecanizado.
- Se deben minimizar los trabajos de soldadura.
- La deformación y la tensión de las estructuras soldadas deben mantenerse al mínimo.
- La estructura soldada debe ser fácil de construir y crear buenas condiciones de trabajo para la construcción.
- Se deben adoptar nuevas tecnologías y soldadura mecanizada y automática para mejorar la productividad laboral.
- La soldadura debe inspeccionarse fácilmente para garantizar la calidad de la unión.
14. Describir las condiciones básicas del corte de gas. ¿Se puede cortar el cobre rojo con oxígeno y llama de acetileno? ¿Por qué?
Responder:
Los requisitos básicos para el corte con gas son los siguientes:
(1) El punto de ignición del metal debe ser inferior a su punto de fusión.
(2) El punto de fusión del óxido metálico debe ser inferior al del propio metal.
(3) La quema de metal en oxígeno debe producir una cantidad sustancial de calor.
(4) La conductividad térmica del metal debe ser baja.
El cobre rojo no se puede cortar con llama de oxígeno-acetileno porque la cantidad de calor generada por el óxido de cobre (CuO) es demasiado pequeña y la conductividad térmica del cobre es demasiado alta. Como resultado, el calor no se puede concentrar cerca de la incisión, lo que imposibilita el corte con gas.
15. ¿Cuál es la función principal del polvo de soldadura con gas?
Responder:
El objetivo principal del polvo de soldadura es generar escoria mediante la reacción con óxidos metálicos o impurezas no metálicas presentes en el baño fundido, facilitando así el proceso de escoria.
Simultáneamente, la escoria generada cubre la superficie del baño fundido y actúa como una barrera, aislando el baño fundido del aire circundante. Este aislamiento evita que el metal presente en el baño de soldadura se oxide continuamente a altas temperaturas.
16. ¿Cuáles son las medidas del proceso para prevenir la porosidad de la soldadura en la soldadura por arco manual?
Responder:
(1) Las varillas y fundentes de soldadura deben almacenarse en un ambiente seco y secarse antes de su uso si es necesario.
(2) El alambre de soldadura y las superficies soldadas deben mantenerse limpios, libres de agua, aceite, óxido o cualquier otro contaminante.
(3) La especificación de soldadura debe seleccionarse con precisión, teniendo en cuenta factores como la corriente de soldadura adecuada y la velocidad de soldadura.
(4) Se debe emplear el método de soldadura correcto, incluido el uso de electrodos alcalinos para soldadura por arco manual y soldadura por arco corto, reduciendo el rango de oscilación del electrodo, disminuyendo la velocidad de movimiento del electrodo y controlando el inicio y la parada del arco corto.
(5) El espacio de montaje de la soldadura de control no debe ser demasiado grande.
(6) No se deben utilizar varillas de soldadura con revestimientos agrietados, pelados, deteriorados, excéntricos y con núcleos corroídos.
17. ¿Cuáles son las principales medidas para evitar el frío al soldar hierro fundido?
Responder:
(1) Se recomienda encarecidamente el uso de electrodos grafitados. Estos electrodos se fabrican a partir de hierro fundido con una alta concentración de elementos grafitizados (como carbono, silicio, etc.) añadidos al revestimiento o al alambre de soldadura. Alternativamente, también se pueden utilizar electrodos de hierro fundido a base de níquel o cobre.
(2) Antes de soldar, se requiere precalentamiento para preparar los materiales. Durante la soldadura, es importante mantener la preservación del calor y, después de soldar, se recomienda un enfriamiento lento para reducir la velocidad de enfriamiento de la zona de soldadura. Hacerlo prolonga el tiempo que la zona de fusión está en estado incandescente, lo que hace que la grafitización sea suficiente y reduce el estrés térmico.
(3) Considere utilizar un proceso de soldadura fuerte para obtener resultados óptimos.
18. ¿Intenta describir el papel del fundente en el proceso de soldadura?
Responder:
El fundente juega un papel crucial para garantizar la calidad de la soldadura. Cumple las siguientes funciones:
- Después de fundirse, el fundente flota sobre la superficie del metal fundido para proteger el charco fundido y evitar la erosión de gases nocivos en el aire.
- El fundente de soldadura ayuda en la desoxidación y la aleación y, junto con el alambre de soldadura, garantiza que el metal de soldadura alcance la composición química y las propiedades mecánicas requeridas.
- Garantiza que la soldadura tenga una apariencia bien formada.
- Disminuye la velocidad de enfriamiento del metal fundido, reduciendo así defectos como la porosidad y la inclusión de escoria.
- Evita salpicaduras, reduce pérdidas y aumenta el coeficiente de conexión.
19. ¿A qué se debe prestar atención en el uso y mantenimiento de la máquina de soldadura por arco de CA?
Responder:
(1) La máquina de soldar debe funcionar de acuerdo con su corriente de soldadura nominal y la duración de carga y no debe sobrecargarse.
(2) Debe evitarse un cortocircuito prolongado de la máquina de soldar.
(3) La corriente de regulación debe funcionar sin carga.
(4) Inspeccione periódicamente el contacto del cable, el fusible, la conexión a tierra y el mecanismo de regulación y asegúrese de que estén en buenas condiciones.
(5) Mantenga la máquina de soldar limpia, seca y bien ventilada para evitar la entrada de polvo y lluvia.
(6) Coloque la máquina en una posición estable y apague la fuente de alimentación después de su uso.
(7) Es necesario realizar un mantenimiento e inspección regulares de la máquina de soldar.
20. ¿Cuáles son los peligros de una fractura frágil?
Responder:
La fractura frágil es un fenómeno repentino que no se puede detectar ni prevenir a tiempo. Cuando esto ocurre, las consecuencias pueden ser graves, provocando importantes pérdidas económicas y poniendo en peligro la seguridad humana.
Como resultado, la cuestión de la fractura frágil en estructuras soldadas debe recibir mayor atención.
21. ¿Características y aplicación de la pulverización por plasma?
Responder:
La pulverización por plasma se caracteriza por una alta temperatura de la llama del plasma que puede fundir casi todos los materiales refractarios, lo que la hace adecuada para una amplia gama de aplicaciones de pulverización. También presenta una alta velocidad de flujo de llama de plasma, un excelente efecto de aceleración de partículas de polvo y una resistencia superior de unión del recubrimiento.
Debido a su versatilidad, la pulverización por plasma es ideal para diversos materiales cerámicos y tiene una amplia gama de aplicaciones, lo que la convierte en el mejor método para pulverizar materiales cerámicos.
22. ¿Procedimiento de preparación de la tarjeta de procedimiento de soldadura?
Responder:
Para preparar la tarjeta de procedimiento de soldadura, se debe identificar la calificación del procedimiento de soldadura correspondiente y se debe elaborar un boceto de la junta basado en el plano de ensamblaje del producto, el plano de procesamiento de piezas y sus requisitos técnicos.
La tarjeta de procedimiento de soldadura debe incluir el número de calificación del procedimiento de soldadura, el número de la tarjeta de procedimiento de soldadura, el número de plano, el nombre de la junta, el número de junta y los elementos del certificado del soldador.
La secuencia de soldadura debe prepararse en función de la calificación del procedimiento de soldadura, las condiciones reales de producción, el personal técnico y la experiencia en producción.
También se deben incluir parámetros específicos del proceso de soldadura en función de la calificación del proceso de soldadura.
La autoridad de inspección, el método de inspección y la proporción de inspección de los productos deben determinarse de acuerdo con los requisitos de los planos y estándares del producto.
23. ¿Por qué se debe agregar una cierta cantidad de silicio y manganeso al alambre de soldadura blindado con gas CO2?
Responder :
El dióxido de carbono es un gas oxidante que puede quemar los elementos de aleación de una costura de soldadura durante el proceso de soldadura, reduciendo significativamente las propiedades mecánicas de la soldadura. Esta oxidación puede provocar la formación de poros y salpicaduras.
Para resolver estos problemas, se pueden agregar silicio y manganeso al alambre de soldadura para que desempeñe un papel desoxidante, evitando la oxidación y las salpicaduras de soldadura.
24. ¿Cuál es el límite de explosión de una mezcla combustible y qué factores lo afectan?
Responder:
El rango de concentración de gas, vapor o polvo combustible presente en una mezcla combustible que puede provocar una explosión se denomina límite de explosión.
El límite de concentración inferior se conoce como límite explosivo inferior y el límite superior se conoce como límite explosivo superior.
Varios factores como la temperatura, la presión, el contenido de oxígeno, el diámetro del recipiente y otros pueden influir en el límite de explosión. Un aumento de temperatura produce una disminución del límite de explosión, y lo mismo ocurre cuando hay un aumento de presión.
Además, un aumento de la concentración de oxígeno en la mezcla de gases provoca una disminución del límite explosivo inferior.
En el caso del polvo combustible, factores como la dispersión, la humedad y la temperatura también pueden afectar su límite explosivo.
25. ¿Qué medidas se deben tomar para evitar descargas eléctricas al soldar en el tambor de una caldera, condensador, tanque de aceite, tanque de aceite y otros contenedores metálicos?
Responder:
(1) Los soldadores deben evitar el contacto con piezas de hierro durante la soldadura eléctrica. Deben pararse sobre almohadillas aislantes de goma o usar zapatos aislantes de goma y ropa de trabajo seca.
(2) Debe haber un supervisor fuera del barco que pueda observar y escuchar el trabajo del soldador. Se debe instalar un interruptor para cortar la energía según la señal del soldador.
(3) El voltaje de las lámparas portátiles utilizadas en contenedores no debe exceder los 12 V. La carcasa del transformador de lámpara portátil debe estar conectada a tierra de manera confiable y está prohibido el uso de un autotransformador.
(4) Los transformadores para lámparas portátiles y los transformadores de soldadura no deben colocarse en calderas ni contenedores metálicos.
26. ¿Cómo distinguir la soldadura por fusión de la soldadura fuerte? ¿Cuáles son las características de cada uno?
Responder:
La soldadura por fusión implica unir átomos entre piezas soldadas, mientras que la soldadura fuerte conecta piezas soldadas utilizando metal de aportación, un medio intermedio con un punto de fusión más bajo que la soldadura.
La soldadura por fusión ofrece varias ventajas, como altas propiedades mecánicas de las uniones soldadas y una alta productividad al unir piezas gruesas y grandes. Sin embargo, también tiene algunas desventajas, como grandes tensiones y deformaciones y cambios microestructurales en la zona afectada por el calor.
La soldadura fuerte, por otro lado, tiene ventajas como una baja temperatura de calentamiento, uniones planas y lisas y una apariencia hermosa. También produce pequeñas tensiones y deformaciones. Sin embargo, sus desventajas incluyen una baja resistencia de las juntas y altos requisitos de espacio libre durante el montaje.
27. Tanto el dióxido de carbono como el argón pertenecen a gases protectores. ¿Cuáles son sus propiedades y usos?
Responder:
El dióxido de carbono es un gas oxidante. Cuando se utiliza como gas protector en soldadura, puede causar una oxidación severa de las gotas fundidas y charcos de metal, lo que resulta en la pérdida por combustión de elementos de aleación. Además, tiene una baja procesabilidad y puede provocar poros y grandes salpicaduras.
Por lo tanto, actualmente solo es adecuado para soldar aceros con bajo contenido de carbono y aceros de baja aleación, y no se recomienda para aceros de alta aleación y metales no ferrosos. Especialmente al soldar acero inoxidable, puede provocar la carburación de la soldadura y reducir la resistencia a la corrosión intergranular, lo que hace que su uso sea menos amplio.
El argón, por otro lado, es un gas inerte que no reacciona químicamente con el metal fundido, lo que produce cambios mínimos en la composición química de la costura de soldadura. Las costuras soldadas producidas con argón son de buena calidad y se pueden utilizar en diversos aceros aleados, aceros inoxidables y metales no ferrosos.
A medida que el precio del argón disminuye gradualmente, se está convirtiendo en una opción popular para soldar una gran cantidad de aceros con bajo contenido de carbono.
28. ¿Intenta describir la soldabilidad y las características de soldadura del acero 16Mn?
Responder:
El acero 16Mn contiene aproximadamente un 1% de Mn además del acero Q235A, lo que da como resultado un equivalente de carbono de 0,345%~0,491%. Como resultado, el acero tiene un buen rendimiento de soldadura. Sin embargo, la tendencia al endurecimiento del acero 16Mn es ligeramente superior a la del acero Q235A, por lo que al soldar estructuras gruesas y rígidas se deben utilizar parámetros más bajos para evitar fisuras, especialmente a bajas temperaturas. En tales casos, se puede aplicar un precalentamiento adecuado antes de soldar.
Para soldadura por arco manual se recomienda el uso de varillas de soldadura E50. En los casos en los que la ranura no se pueda abrir para la soldadura automática por arco sumergido, se puede utilizar alambre de soldadura H08MnA con fundente 431. Al biselar, se debe utilizar alambre de soldadura H10Mn2 con fundente 431. Durante la soldadura con gas protector CO2, se debe usar alambre de soldadura H08Mn2SiA o H10MnSi. ser usado.