Los rodamientos son un componente crítico para la confiabilidad, eficiencia y vida útil de su equipo. La mayoría de los equipos de proceso giratorios actuales dependen de rodamientos de rodillos o rodamientos de película fluida para contrarrestar la gravedad y otras fuerzas sobre el equipo y permitir que el eje gire libremente. Elegir el rodamiento adecuado para su equipo y aplicación es esencial para el correcto funcionamiento de ese equipo.
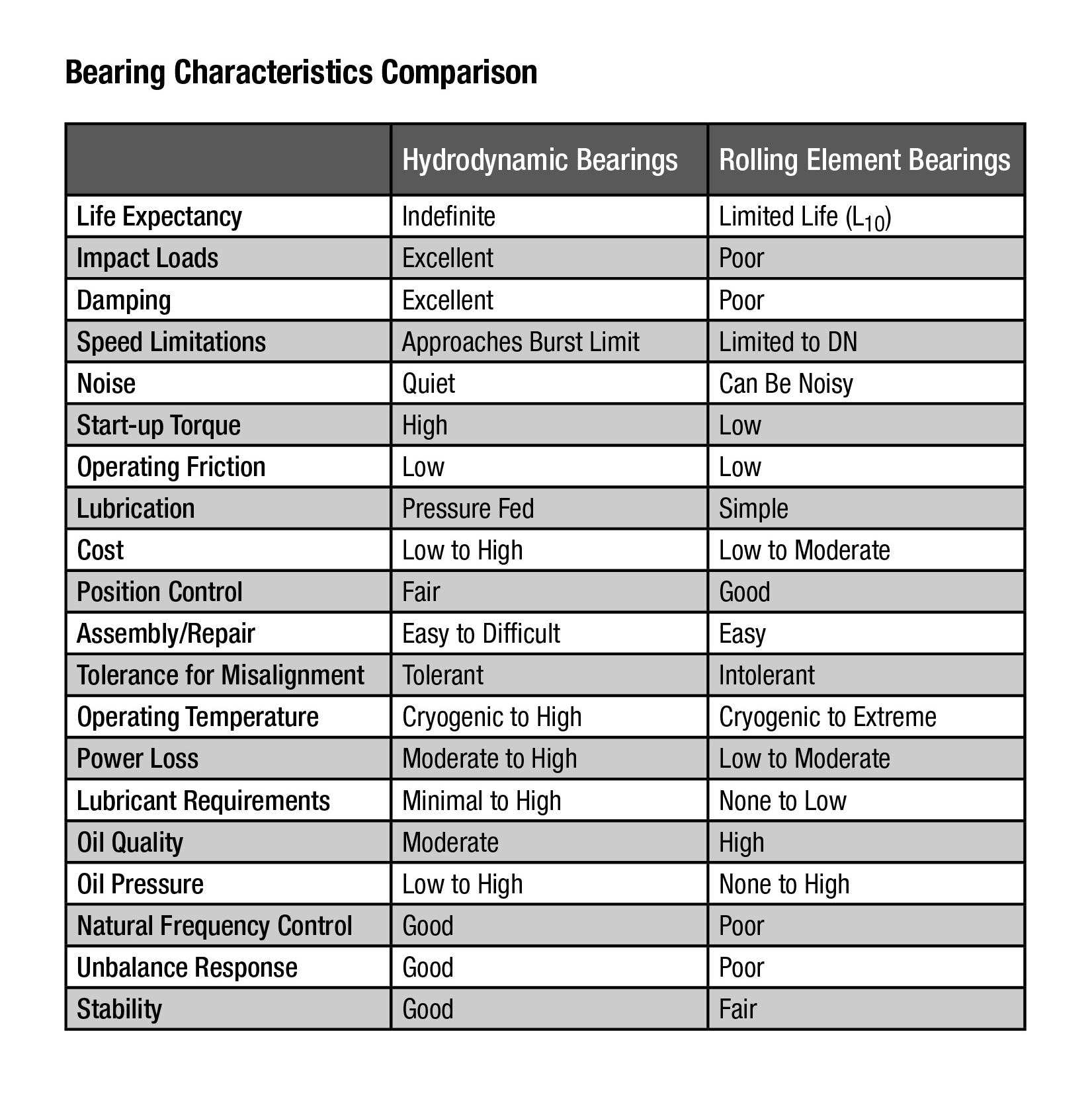
Tabla 1. Los operadores pueden comparar las cualidades de los rodamientos hidrodinámicos y los elementos rodantes.
Una diferencia clave entre los rodamientos y los rodamientos de película fluida cuando se trata del mantenimiento de equipos de proceso es la vida útil esperada de los rodamientos. Los rodamientos suelen tener una vida útil predecible según las condiciones de funcionamiento. Si se diseñan y mantienen adecuadamente, los rodamientos de película fluida pueden funcionar durante décadas. En la Tabla 1 se proporcionan comparaciones adicionales de las características de los elementos rodantes y de los rodamientos de película fluida, como las necesidades de lubricación y la capacidad para manejar cargas de impacto.
La correcta selección de materiales y diseño mecánico es la base de la larga vida útil de un rodamiento de película fluida. Los factores típicos que afectan la selección de materiales incluyen carga, velocidad, temperatura de funcionamiento, requisitos de aislamiento y tipo y limpieza de lubricante. Dependiendo de sus necesidades, las opciones de materiales incluyen babbitt (también conocido como metal blanco), bronce, aluminio, peltre, polímero, cerámica y cermet.
y diamante.
Para el diseño mecánico, el diseñador de rodamientos de película fluida no solo debe considerar dimensionar adecuadamente el rodamiento para manejar cargas y minimizar la pérdida de potencia, sino también incorporar características para optimizar la formación de la película y ajustar las características dinámicas del rodamiento. El ajuste fino de las características de los rodamientos mejora su rendimiento
equipos de proceso.
Principio de funcionamiento básico
La superficie estacionaria de un rodamiento de película fluida está separada de la superficie giratoria por una fina película de lubricante, como aceite, aire, agua o fluido de proceso. En los rodamientos de película de fluido hidrodinámico, la presión de la película que separa las superficies y neutraliza las cargas se crea mediante el movimiento relativo (rotación) de las superficies a medida que el lubricante se atrae hacia una geometría convergente entre las superficies. Debido a esta fuerza de separación, el contacto superficial no ocurre durante el funcionamiento normal, lo que reduce el desgaste y la pérdida de energía en comparación con el contacto superficie a superficie.
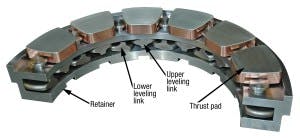
Un cojinete de empuje con cojinete basculante autonivelante puede adaptarse a desalineaciones.
Los rodamientos de empuje resisten cargas axiales, que son cargas a lo largo del eje de rotación, mientras que los rodamientos de empuje soportan cargas radiales, que son perpendiculares al eje de rotación. Los materiales y el diseño de los cojinetes de película fluida de muñón y empuje se seleccionan para optimizar la geometría del cojinete para una mayor eficiencia del equipo de proceso y menos demandas de equipo auxiliar.
Materiales
La selección de materiales de construcción para un rodamiento de película fluida se basa en dos factores principales: requisitos de aplicación y entorno operativo.
El bronce se puede utilizar cuando las temperaturas de funcionamiento están por encima del límite. Los cojinetes de bronce lubricados con aceite son comunes en aplicaciones de equipos de proceso donde la superficie del cojinete puede alcanzar los 150 °C (302 °F) y, en algunos casos, incluso más. Esto puede causar daños al eje o a los cojinetes en presencia de contaminantes o desalineación. Además, se debe tener cuidado al seleccionar el material de la superficie giratoria cuando se utilizan cojinetes de bronce para limitar la posibilidad de dañar los componentes giratorios.
Para equipos de proceso rotativos y alternativos que requieren temperaturas más altas o mejor formabilidad y ajustabilidad que el bronce, se puede utilizar aluminio con aleación de estaño como material de soporte. La lata de aluminio puede funcionar a temperaturas más altas de hasta 160 °C (320 °F) y no se fatiga fácilmente. Las latas de aluminio se aplican sobre acero para mayor resistencia o sobre cromo-cobre para mejorar la transferencia de calor. Ambos se pueden utilizar contra una variedad de componentes giratorios, incluidos los aceros dulces.
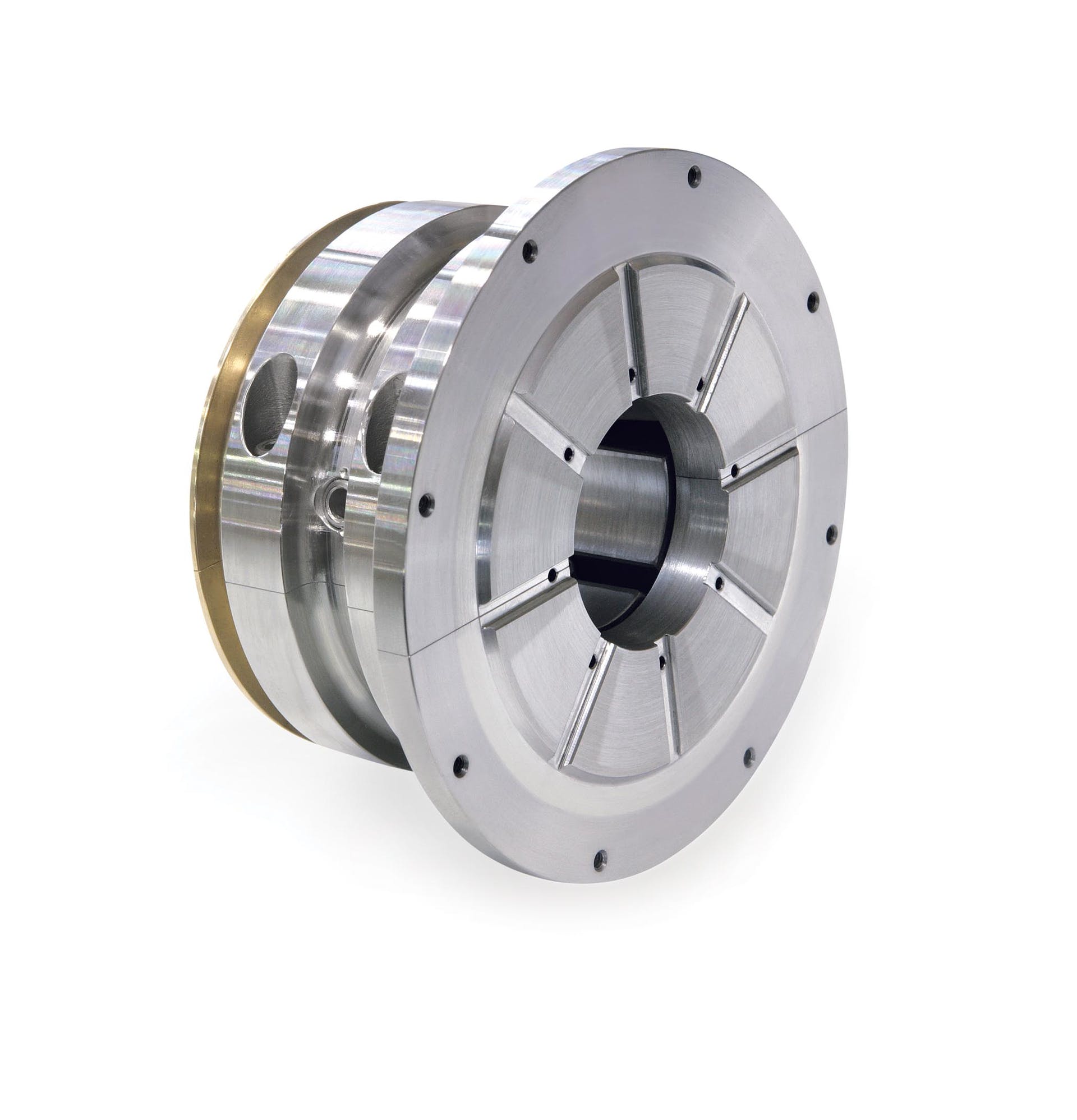
Una combinación de cojinetes axiales de perfil fijo cónico y cojinetes basculantes
Los polímeros diseñados como componentes sólidos o como recubrimientos sobre soportes de acero también son ampliamente aceptados en equipos de proceso. Los rodamientos de polímero presentan capacidad de incrustación y conformabilidad y pueden funcionar a temperaturas y cargas más altas. Debido a que operan con películas relativamente delgadas, los cojinetes de empuje de polímero se usan a menudo en aplicaciones lubricadas con aceite con cargas unitarias de hasta 8 megapascales (1160 psi), que es aproximadamente el doble de la carga generalmente aceptada por los cojinetes Babbitt, y temperaturas de hasta 200°. C. (392°F).
Los rodamientos de polímero también son menos susceptibles al ataque químico, aíslan contra las corrientes eléctricas y funcionan exitosamente en una variedad de lubricantes, incluidos agua y fluidos de proceso. Con la composición correcta del material, los rodamientos de polímero pueden resistir la rotura de la película debido a sobrecarga o pérdida temporal de lubricación.
Cuando las altas temperaturas, los materiales corrosivos o los lubricantes contaminados impiden el uso de aluminio, estaño, bronce y polímero, los rodamientos de película fluida se pueden fabricar con superficies extremadamente duras. La cerámica y el diamante se han utilizado con éxito cuando las temperaturas de funcionamiento superan los 200 °C (392 °F), cuando las películas son muy delgadas y/o cuando hay abrasivos presentes. Aluminio, estaño y polímero, que pueden funcionar contra aceros suaves y otros materiales tradicionales de eje, cerámica y requieren una elección deliberada de material para superficies giratorias y estacionarias para lograr la vida útil y el rendimiento deseados del rodamiento, especialmente cuando hay abrasivos presentes o las películas son extremadamente delgadas. .
El mejor material para los rodamientos puede variar incluso dentro del mismo conjunto y el material por sí solo no garantiza el rendimiento. Los materiales cuidadosamente seleccionados deben combinarse con un diseño mecánico óptimo.
Diseño de rodamientos
La formación de película es fundamental para la vida útil y el rendimiento de un rodamiento de película fluida. Un lubricante viscoso, un movimiento relativo entre superficies y una geometría de rodamiento convergente son esenciales para el desarrollo de la película. Juntos, crean presión para contrarrestar la gravedad y otras fuerzas que actúan sobre el árbol.
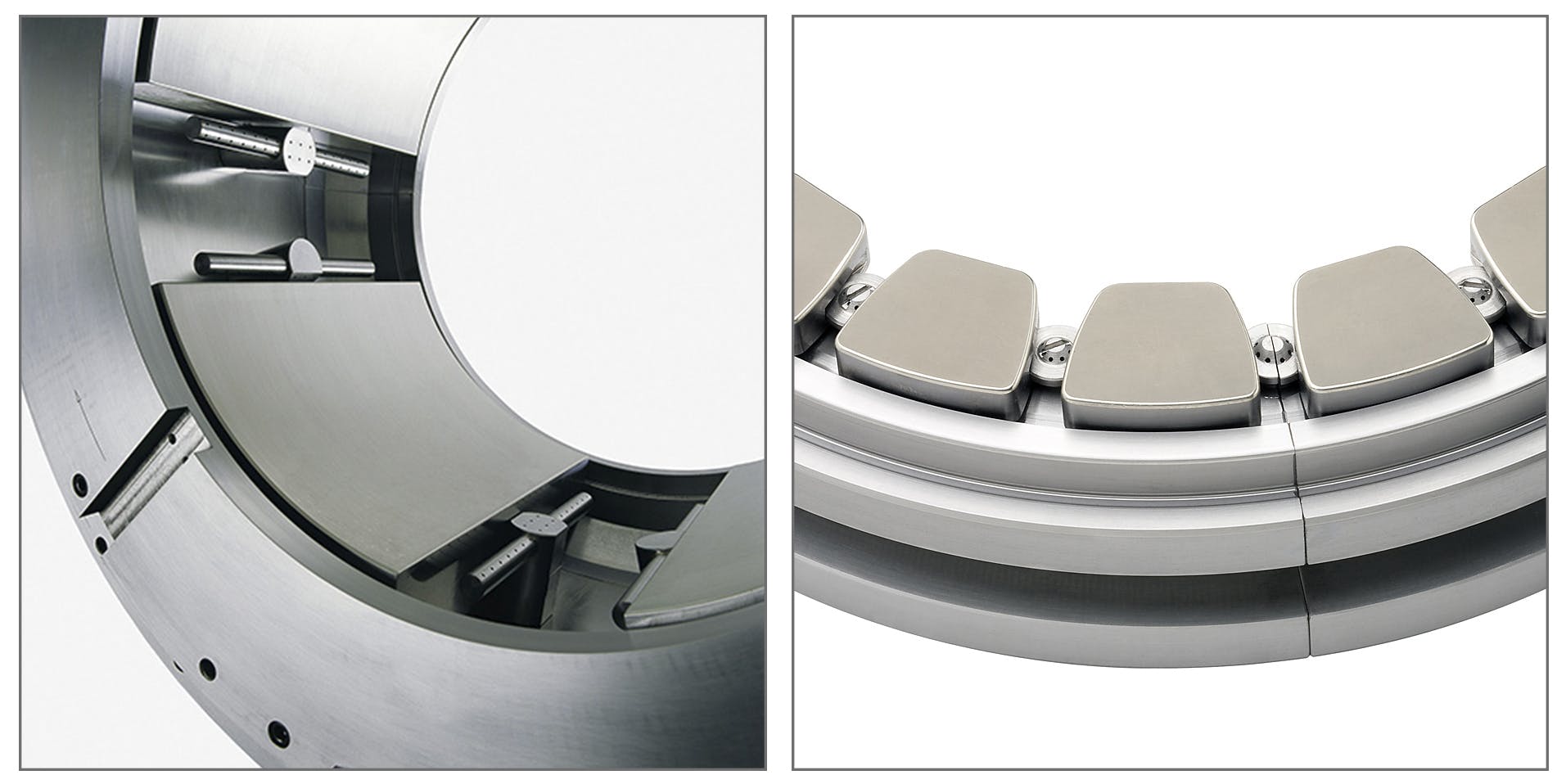
Cojinetes lisos (izquierda) y de empuje (derecha) que muestran dos estilos de lubricación directa.
Aunque las cargas axiales se pueden soportar con caras de rodamiento planas, la geometría generalmente se mecaniza en la superficie de un rodamiento de empuje de perfil fijo para crear una cuña convergente y aumentar la capacidad de carga del rodamiento. Una geometría fija está diseñada para una condición específica, por lo que a menudo se utilizan rodamientos de empuje con insertos inclinables para adaptarse a las condiciones cambiantes. Los cojinetes de empuje de zapata de inclinación autonivelantes compensan la desalineación entre el cojinete y el collar, igualando la carga entre las zapatas.
Debido a los diferentes diámetros del rodamiento y del eje, un cojinete liso naturalmente tiene una cuña convergente cuando el eje no está centrado en el rodamiento. Para mejorar el rendimiento estático y dinámico, se puede mecanizar un perfil definido en el rodamiento para revelar la película adecuada. Los rodamientos de inclinación pivotante se utilizan a menudo si la estabilidad es una preocupación, si es necesario adaptarse a condiciones variables o si otros parámetros de rendimiento del rodamiento requieren optimización.
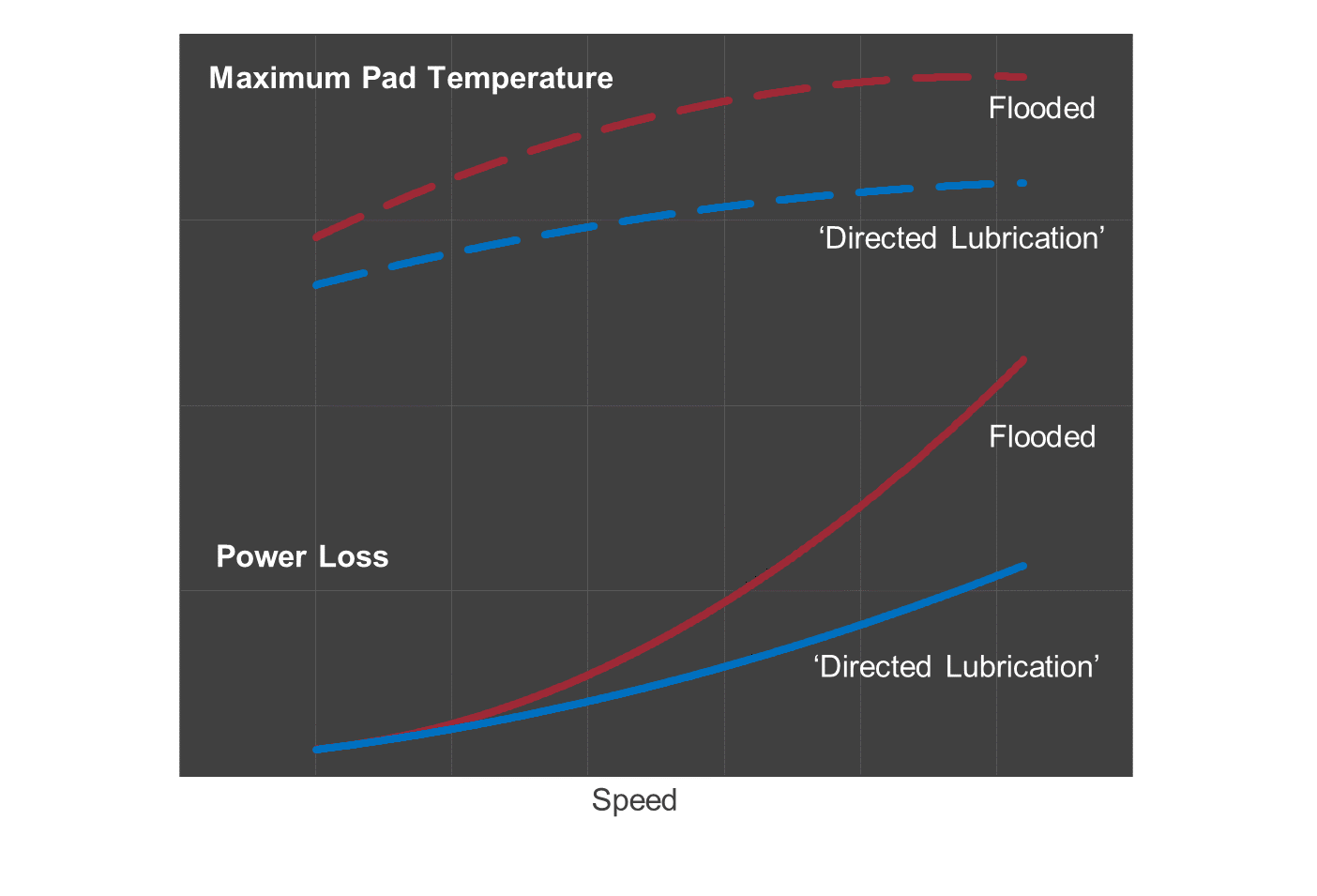
Cambiar de un rodamiento con carga ligera y lubricación por inundación (punto A) a un rodamiento optimizado más pequeño con lubricación directa (punto B) puede reducir significativamente la pérdida de potencia.
Los cojinetes de empuje y de muñón están dimensionados para manejar los requisitos de carga de la aplicación y encajan en el gabinete especificado. Se pueden optimizar otras características para lograr un rendimiento estático específico en cojinetes de empuje y un rendimiento dinámico y estático en cojinetes de muñón. El arco de la almohadilla, o la parte de la almohadilla que desarrolla presión, se puede ajustar para influir en la pérdida de energía y la temperatura. El desplazamiento, o la distancia del borde delantero del muñón con respecto al arco de la almohadilla, tiene un efecto significativo en la formación de la película y puede influir en las temperaturas de los cojinetes, la pérdida de potencia y, en el caso de los cojinetes de muñón, el rendimiento.
En particular, en los rodamientos de rodillos basculantes, las temperaturas, la pérdida de potencia y el rendimiento dinámico pueden verse afectados significativamente por el juego del rodamiento (la diferencia entre el diámetro interior del rodamiento y el diámetro del eje), la longitud del rodamiento y la precarga. La precarga representa la desviación del orificio del inserto mecanizado en relación con el orificio del rodamiento montado. Es positivo cuando el orificio de la zapata es más grande que el orificio del cojinete, cero cuando el orificio de la zapata y el cojinete son iguales y negativo cuando el orificio de la zapata es más pequeño que el orificio del cojinete. Si la precarga es positiva, se forma una cuña convergente. Una precarga negativa limita el flujo hacia la pastilla y
no es recomendado.
Tanto en los cojinetes principales como en los cojinetes de empuje basculantes, el muñón se selecciona en función de necesidades específicas, como la vida útil requerida (esfuerzo), la rigidez y la facilidad para inclinar el muñón en una o más direcciones. Los tipos de pasadores comunes son contacto puntual, contacto lineal, rótula y pasador flexible. Cada uno de ellos tiene distintas ventajas.
Otra elección de diseño que afecta significativamente el rendimiento del rodamiento es el método de introducción y extracción de lubricante en el rodamiento. Al suministrar lubricante al borde delantero de la zapata del balancín y permitir que el lubricante fluya libremente desde el rodamiento y su alojamiento, los rodamientos lubricados directamente funcionan con menores pérdidas de potencia y a temperaturas de funcionamiento más bajas que los rodamientos inundados, donde el lubricante generalmente se suministra lejos de la película y el flujo fuera del rodamiento son limitados. La lubricación por inundación crea un corte de lubricante en el exterior de la película que no contribuye a la capacidad de carga del rodamiento.
Poniendolo todo junto
La combinación de materiales seleccionados y características de diseño optimizará aún más el rendimiento en comparación con los materiales o las características de diseño por sí solos. Por ejemplo, combinar la lubricación directa con rodamientos de materiales avanzados, que pueden soportar películas más delgadas, temperaturas más altas y, por lo tanto, cargas más altas, puede reducir significativamente la pérdida de potencia en comparación con un diseño inundado con materiales de rodamientos tradicionales. El uso de materiales avanzados permite un rodamiento más pequeño y el uso de fluidos de menor viscosidad, incluso fluidos de proceso, reduciendo así la pérdida de potencia. Si no es necesario reducir la pérdida de energía, se puede lograr un mayor margen de seguridad.
Con los materiales y el diseño adecuados, los rodamientos de película fluida pueden ofrecer un rendimiento dinámico de primer nivel, baja fricción, poco o ningún desgaste y una larga vida útil, lo que los convierte en la opción correcta para satisfacer las necesidades de los equipos de proceso modernos.