La fundición a presión es un proceso de fundición de metal, que se caracteriza por la aplicación de alta presión al metal fundido a través de la cavidad interna del molde.
El molde generalmente está hecho de una aleación de mayor resistencia, que es algo similar al moldeo por inyección.
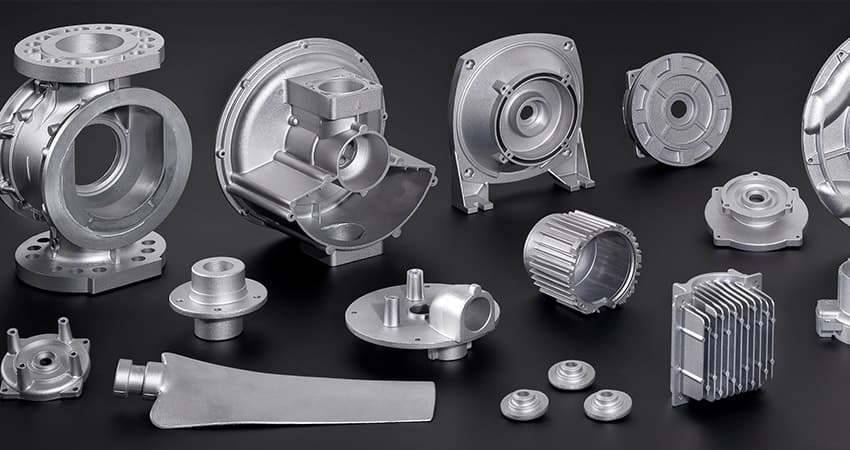
Aportó una innovación sin precedentes al mundo de la impresión.
Después de la industrialización a gran escala de la industria gráfica, el tipo tradicional prensado a mano fue reemplazado por el moldeado a presión.
Alrededor de 1900, la introducción de la tipografía en el mercado mejoró aún más la tecnología de automatización de la industria gráfica, de modo que a veces se pueden ver en los periódicos más de diez máquinas de fundición a presión.
Con el crecimiento continuo de los productos de consumo, los inventos de Otto obtuvieron cada vez más aplicaciones.
La gente puede utilizar la fundición a presión para fabricar piezas y productos en grandes cantidades.
En 1966, General Dynamics inventó el proceso de fundición a presión de precisión, que a veces se denomina fundición a presión doble.
Proceso de fundición a presión
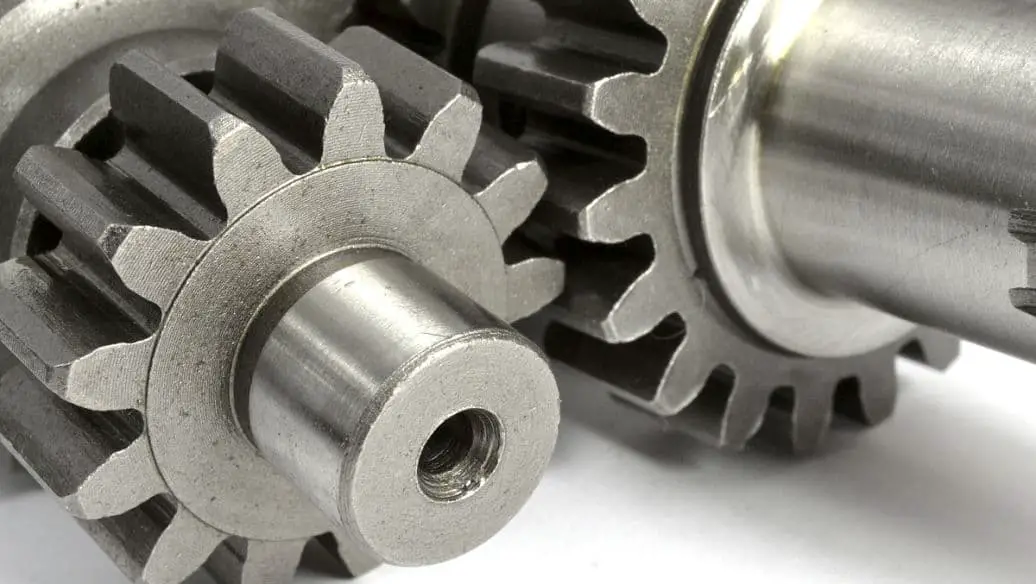
La fundición a presión en cámara fría se puede utilizar para metales que no se pueden utilizar en el proceso de fundición a presión en cámara caliente, incluidas las aleaciones de aluminio, magnesio, cobre y zinc con alto contenido de aluminio.
En este proceso, primero se debe fundir el metal en un crisol independiente.
Luego se transfiere una cierta cantidad de metal fundido a una cámara de inyección o boquilla de inyección sin calentar.
Estos metales se inyectan en el molde mediante presión hidráulica o mecánica.
Debido a que es necesario transferir el metal fundido a la cámara fría, la mayor desventaja de este proceso es que el tiempo del ciclo es muy largo.
Existen máquinas de colada a presión de cámara fría verticales y horizontales.
Las máquinas de fundición a presión verticales son generalmente máquinas pequeñas, mientras que las máquinas de fundición a presión horizontales tienen varios modelos.
Molde de fundición
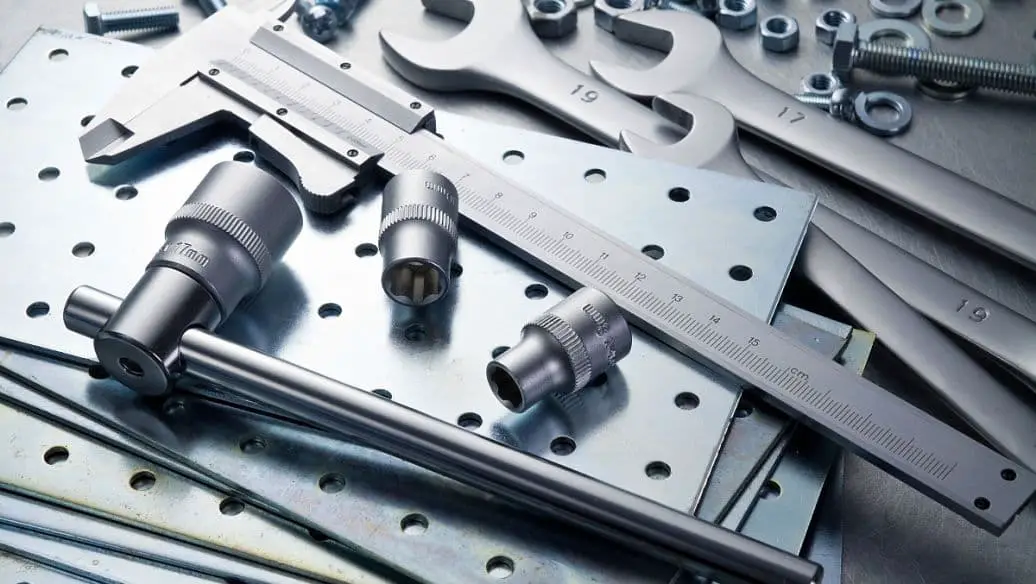
Ventajas del casting
Las ventajas de la fundición a presión incluyen una excelente precisión dimensional.
Generalmente esto depende del material de fundición. El valor típico es que el error es de 0,1 mm para los primeros 2,5 cm de tamaño y el error aumenta en 0,002 mm por cada aumento de 1 cm.
En comparación con otros procesos de fundición, su superficie de fundición es lisa y el radio del filete es de aproximadamente 1 a 2,5 micrones.
Se puede fabricar una pieza fundida con un espesor de pared de aproximadamente 0,75 mm en relación con el método de fundición en caja de arena o en molde permanente.
Puede fusionar directamente estructuras internas como manguitos de alambre, elementos calefactores y superficies de soporte de alta resistencia.
Otras ventajas incluyen que puede reducir o evitar el mecanizado secundario, una velocidad de producción rápida, una resistencia a la tracción de fundición de hasta 415 MPa y puede fundir metales de alta fluidez.
Desventajas del casting
La mayor desventaja de la fundición a presión es el alto coste.
Los equipos de fundición, los moldes y los componentes relacionados con los moldes son costosos en comparación con otros métodos de fundición.
Por lo tanto, es más económico producir una gran cantidad de productos al realizar piezas fundidas a presión.
Otras desventajas incluyen: este proceso solo es aplicable a metales con alta fluidez y la masa fundida debe estar entre 30 gy 10 kg.
En la fundición a presión normal, siempre hay poros en el último lote de piezas fundidas.
Por lo tanto, no se puede realizar ningún tratamiento térmico ni soldadura porque el gas en el espacio se expandirá bajo la acción del calor, lo que provocará microdefectos internos y descamación de la superficie.
Característica de fundición
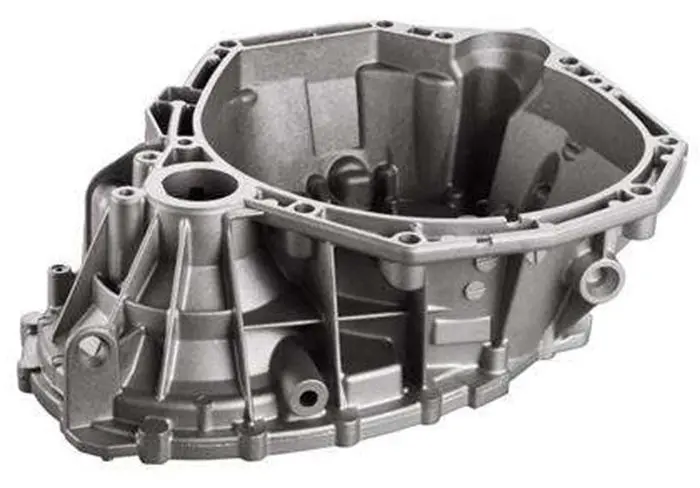
La fundición a presión, brevemente llamada fundición a presión, es un método de fundición en el que el líquido de aleación fundido se vierte en la cámara de presión para llenar la cavidad del molde de acero a alta velocidad, y el líquido de aleación se solidifica bajo presión para formar una pieza fundida.
Las principales características de la fundición a presión, a diferencia de otros métodos de fundición, son la alta presión y la alta velocidad.
① El metal fundido llena la cavidad del molde bajo presión y cristaliza y solidifica bajo mayor presión. La presión común es de 15-100mpa.
② El líquido metálico llena la cavidad del molde a alta velocidad, generalmente de 10 a 50 m/s y, a veces, más de 80 m/S (la velocidad lineal de la cavidad del molde introducida a través de la entrada, la velocidad de entrada).
Por lo tanto, el tiempo de llenado del líquido metálico es extremadamente corto, aproximadamente 0,01-0,2 segundos (dependiendo del tamaño de la pieza fundida).
La fundición a presión es un método de fundición de precisión. La tolerancia dimensional de las piezas fundidas a presión es muy pequeña y la precisión de la superficie es muy alta.
En la mayoría de los casos, las piezas fundidas se pueden ensamblar y aplicar sin girar, y las piezas roscadas se pueden fundir directamente.
Desde piezas comunes de cámaras, piezas de máquinas de escribir, piezas de calculadoras electrónicas, decoraciones y otras piezas pequeñas, así como piezas complejas de vehículos como automóviles, locomotoras y aviones, la mayoría de ellas se fabrican mediante fundición a presión.
Forma de fracaso del lanzamiento
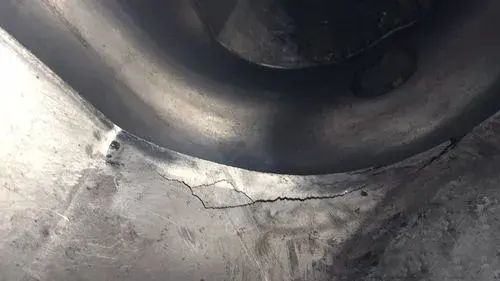
imagen D
Durante la producción de fundición a presión, el molde se somete repetidamente a enfriamiento y calentamiento, y la superficie de formación y su interior se deforman, lo que conduce a tensiones térmicas cíclicas repetidas, lo que resulta en daños secundarios a la estructura y pérdida de tenacidad, lo que conduce a la apariencia. de microfisuras y continúa expandiéndose.
Una vez que las grietas se expanden, el metal fundido se comprimirá y la tensión mecánica repetida acelerará el crecimiento de las grietas.
Por lo tanto, por un lado, la matriz debe estar completamente precalentada al inicio de la fundición.
Además, en el proceso de producción de fundición a presión, el molde debe mantenerse en un cierto rango de temperatura de trabajo para evitar fallas prematuras por agrietamiento.
Al mismo tiempo, es necesario garantizar que no se produzcan causas internas antes de que el molde entre en producción y durante la fabricación.
Porque en la producción real, la mayoría de las fallas del molde son fallas por grietas por fatiga térmica.
fragmentación F
Bajo la acción de la fuerza de inyección, el molde iniciará grietas en la parte más débil, especialmente cuando las marcas de escritura o mecanizado eléctrico en la superficie de moldeo del molde no están pulidas, o cuando las esquinas de la moldura son claras, aparecerán grietas finas. primero .
Cuando hay fases quebradizas o granos gruesos en los límites de los granos, es fácil fracturarse.
Sin embargo, cuando ocurre una fractura frágil, la grieta crece rápidamente, lo cual es un factor muy peligroso para la falla por fractura de la matriz.
Por lo tanto, por un lado, se deben pulir todos los rayones y marcas de mecanizado eléctrico en la superficie del molde, incluso si están en el sistema de fundición.
Además, es necesario que los materiales de matriz utilizados tengan alta resistencia, buena plasticidad, buena tenacidad al impacto y resistencia a la fractura.
Corrosión C
Como se mencionó anteriormente, las aleaciones de fundición comúnmente utilizadas incluyen aleaciones de zinc, aleaciones de aluminio, aleaciones de magnesio y aleaciones de cobre, así como aleaciones de aluminio puro.
Zn, Al y Mg son elementos metálicos relativamente activos que tienen buena afinidad con los materiales del molde, especialmente el Al es fácil de morder en el molde.
Cuando la dureza del molde es alta, la resistencia a la corrosión es mejor, pero si hay puntos débiles en la superficie del molde, la resistencia a la corrosión es desfavorable.
Hay muchos factores que conducen a fallas en el molde, incluidos factores externos (como la temperatura de fundición, si el molde está precalentado, la cantidad de recubrimiento de agente acuoso que se rocía, si el tonelaje de la máquina de fundición a presión coincide, si la fundición a presión es demasiado alta). alto, la velocidad de la compuerta interna es demasiado rápida, la apertura del agua de refrigeración no está sincronizada con la producción de fundición a presión, el tipo y composición del material de fundición de Fe, el tamaño y forma de la fundición, el espesor de la pared, el tipo de revestimiento, etc).
También existen causas internas (por ejemplo, la calidad metalúrgica del propio material del molde, el proceso de forjado de la pieza en bruto, la racionalidad del diseño de la estructura del molde, la racionalidad del diseño del sistema de paso, la tensión interna generada durante el mecanizado del molde). máquina (mecanizado eléctrico), el proceso de tratamiento térmico del molde, incluidos varios requisitos correspondientes de precisión y limpieza).
Si hay una falla temprana del molde, es necesario averiguar cuáles son las causas internas o externas para futuras mejoras.
Sin embargo, en la producción real, la corrosión es solo local en el molde, por ejemplo, las piezas lavadas directamente por la compuerta (núcleo y cavidad) son propensas a la corrosión y las piezas con dureza blanda son propensas a adherirse a la aleación de aluminio.
Problemas de casting
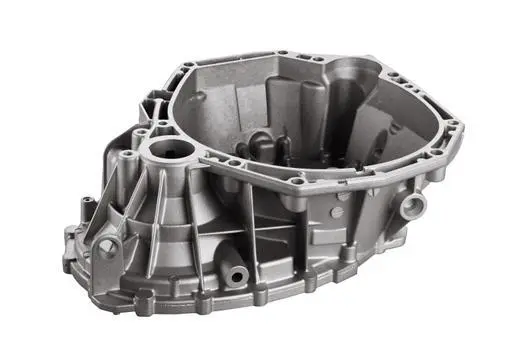
Verter desbordamiento
Requisitos para molde en máquina de colada horizontal con cámara fría:
① El diámetro interior de la cámara de presión debe seleccionarse de acuerdo con la presión específica requerida y la plenitud de la cámara de presión.
Al mismo tiempo, la desviación del diámetro interior del manguito de compuerta debe ampliarse adecuadamente en unos pocos hilos en comparación con la desviación del diámetro interior de la cámara de presión, para evitar el problema de atasco del punzón o desgaste grave causado por diferentes ejes del manguito de compuerta y el diámetro interior de la cámara de presión, y el espesor de la pared del manguito de compuerta no debe ser demasiado delgado.
La longitud del casquillo del bebedero generalmente debe ser más corta que la manija de entrega del punzón de inyección para que la pintura pueda retirarse de la cámara de presión.
② Los orificios internos de la cámara de presión y el casquillo del bebedero deben pulirse finamente después del tratamiento térmico y luego pulirse a lo largo de la dirección del eje.
La rugosidad de la superficie debe ser ≤ Ra0,2 μ m.
③ El desviador está conectado a la cavidad que forma la carcasa.
Su profundidad cóncava es igual a la profundidad del canal, su diámetro corresponde al diámetro interno del casquillo del bebedero y tiene una inclinación de 5° en la dirección de desmolde.
Cuando se utiliza el canal del tipo de introducción de revestimiento, se reduce el volumen de la longitud efectiva de la cámara de presión y se puede mejorar la plenitud de la cámara de presión.
Requisitos del molde
① La entrada del canal del molde horizontal frío generalmente debe ubicarse en la posición por encima de 2/3 del diámetro interior de la parte superior de la cámara de presión, para evitar que el líquido metálico en la cámara de presión ingrese al canal prematuramente y comience a solidificarse de antemano bajo la acción de la gravedad.
② El área de la sección transversal del canal debe reducirse gradualmente desde el canal de entrada hasta la entrada.
Para expandir la sección transversal, se producirá una presión negativa cuando el metal fundido fluya, lo que es fácil de aspirar el gas en la superficie de separación y aumentar la turbulencia en el flujo de metal fundido.
Generalmente, la sección en la salida es entre un 10 y un 30% más pequeña que la de la entrada.
③ El pasillo debe tener cierta longitud y profundidad.
El propósito de mantener una cierta longitud es estabilizar y guiar el flujo.
Si la profundidad no es suficiente, la temperatura del metal fundido bajará rápidamente;
Si la profundidad es demasiado profunda, la condensación será muy lenta, lo que no sólo afectará a la productividad sino que también aumentará la cantidad de materiales reciclados.
④ El área de la sección transversal del canal debe ser mayor que la de la entrada para garantizar la velocidad de vertido del metal en el molde.
El área de la sección transversal del canal principal debe ser mayor que la de cada canal secundario.
⑤ Los dos lados de la parte inferior del corredor deben redondearse para evitar grietas prematuras, y los dos lados se pueden hacer con una pendiente de aproximadamente 5°.
Rugosidad de la superficie del corredor ≤ Ra0,4 μm.
Ingate
① La superficie de separación no debe cerrarse inmediatamente después de que el metal fundido ingresa al molde, y la ranura de desbordamiento y la ranura de escape no deben impactar directamente el núcleo.
La dirección del flujo del metal fundido después de ingresar al molde debe llenarse desde la pared gruesa hasta la pared delgada a lo largo de las nervaduras y aletas fundidas tanto como sea posible.
② Al seleccionar la posición de entrada, el flujo de metal fundido debe ser lo más corto posible.
Cuando se utiliza una entrada de cables múltiples, es necesario evitar que múltiples cables de metal fundido converjan y choquen entre sí después de la inyección, lo que provocará la inclusión de corrientes parásitas, la inclusión de oxidación y otros defectos.
③ La puerta interna de las piezas de paredes delgadas debe ser adecuadamente más pequeña que la de las piezas gruesas para garantizar la velocidad de llenado requerida.
La configuración de la puerta interior debe ser fácil de cortar y el cuerpo de fundición no debe dañarse (comer carne).
Tanque de desbordamiento
① La ranura de rebose debe ser fácil de quitar de la pieza fundida y no debe dañar el cuerpo de la pieza tanto como sea posible.
② Al colocar una ranura de escape en la ranura de desbordamiento, preste atención a la posición del puerto de desbordamiento para evitar bloquear la ranura de escape demasiado pronto y hacer que la ranura de escape sea ineficaz.
③ No está permitido configurar múltiples puertos de desbordamiento o un puerto de desbordamiento que sea demasiado ancho y grueso en el mismo tanque de desbordamiento, para evitar que líquido frío, escoria, gas, pintura, etc. entren al tanque de desbordamiento. el metal fundido regresa a la cavidad del molde del tanque de desbordamiento y provoca defectos de fundición.
Diseño de moldes de fundición
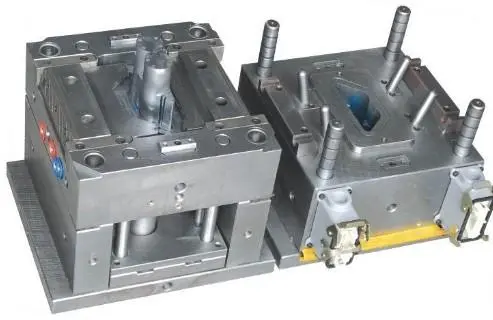
Con la premisa de cumplir con la función del producto, diseñar razonablemente piezas de fundición, simplificar la estructura de la matriz de fundición, reducir los costos de fundición, reducir los defectos de fundición y mejorar la calidad de las piezas de fundición.
Debido a que el proceso de moldeo por inyección se deriva del proceso de fundición a presión, la guía de diseño de fundición a presión es muy similar a la guía de diseño de piezas de plástico en algunos aspectos.
Para obtener un diseño detallado de piezas fundidas, consulte el libro "Guía de diseño de productos para fabricación y ensamblaje" publicado por China Machine Press.
islote
(incluidas las esquinas), el plano de fundición a menudo indica requisitos como un filete R2 sin marcar.
No debemos ignorar el papel de estos filetes sin marcar en la apertura del molde, y no debemos dejar claras las esquinas o los filetes que sean demasiado pequeños.
El filete de fundición puede hacer que el líquido metálico se llene suavemente, hacer que el gas en la cavidad se descargue en secuencia, reducir la concentración de tensión y extender la vida útil del molde. (No es fácil que la pieza fundida presente grietas o defectos diversos por un relleno inadecuado).
Por ejemplo, hay muchas esquinas limpias en el molde del cárter estándar.
Relativamente hablando, el molde del cárter hermano está mejor abierto hoy en día y también hay muchos cárteres pesados.
Pendiente de liberación
Está prohibido tener hendiduras laterales artificiales en la dirección de desmoldeo (generalmente las piezas fundidas quedan atrapadas en el molde durante la prueba del molde, y las hendiduras locales son causadas por perforación, cincelado duro, etc. cuando el molde se manipula con métodos incorrectos).
Aspereza
Las piezas de moldeo y el sistema de vertido deben pulirse cuidadosamente según sea necesario y deben pulirse en la dirección de desmoldeo.
Ahora todo el proceso de introducir el metal fundido en el sistema de fundición desde la cámara de presión y llenar la cavidad tarda sólo entre 0,01 y 0,2 segundos.
Para reducir la resistencia al flujo de metal líquido y minimizar la pérdida de presión, se requiere un alto acabado superficial.
Al mismo tiempo, las condiciones de calentamiento y erosión del sistema de fundición son relativamente malas y cuanto peor sea el acabado, más fácil será dañar el molde.
5. Dureza de la parte moldeada del molde: aleación de aluminio: aproximadamente HRC46°, cobre: aproximadamente HRC38°.
Durante el procesamiento, el molde debe intentar dejar espacio para reparación, alcanzar el límite de tamaño superior y evitar soldaduras.
Movilidad
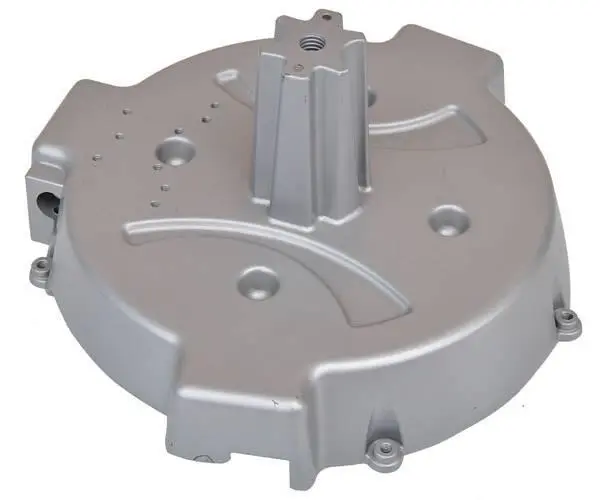
La fluidez se refiere a la capacidad del líquido de aleación para llenar el molde.
La fluidez determina si la aleación puede fundir piezas fundidas complejas.
La aleación eutéctica tiene la mejor fluidez entre las aleaciones de aluminio.
Hay muchos factores que afectan la fluidez, principalmente la composición, temperatura y partículas sólidas de óxidos metálicos, compuestos metálicos y otros contaminantes en el líquido de la aleación, pero los factores externos fundamentales son la temperatura y la presión de vertido (comúnmente conocido como fuga de cabeza).
En la producción real, cuando se determina la aleación, además de fortalecer el proceso de fusión (refinado y eliminación de escoria), también es necesario mejorar el proceso de fundición (permeabilidad del molde de arena, temperatura de escape y del molde metálico) y aumentar la temperatura de fundición. sin afectar la calidad de la fundición para asegurar la fluidez de la aleación.
Precauciones para las condiciones de moldeo por fundición:
La máquina de fundición a presión, la aleación de fundición a presión y la matriz de fundición a presión son los tres elementos principales de la producción de fundición a presión, ninguno de los cuales es indispensable.
El proceso de fundición a presión consiste en utilizar estos tres elementos de manera orgánica e integral, de manera que se produzcan piezas fundidas calificadas, con buena apariencia, calidad interna y dimensiones de acuerdo con los requisitos de los planos o acuerdos de manera estable, rítmica y eficiente. e incluso piezas fundidas de alta calidad.
Temperatura de fusión del material, temperatura del molde y temperatura de fusión durante la inyección;
Finalmente, se debe reparar el estado de los productos fundidos para obtener productos perfectos.
Principio de selección de la temperatura de trabajo del troquel de fundición:
1) La temperatura del molde es demasiado baja, la estructura interna de la pieza fundida está suelta y es difícil expulsar el aire, lo que dificulta el conformado;
2) La temperatura del molde es muy alta y la estructura interna de la pieza fundida es densa, pero la pieza fundida es fácil de "soldar" a la cavidad del molde y es difícil quitar la pieza fundida después de adherirla al molde.
Al mismo tiempo, una temperatura demasiado alta expandirá el molde y afectará la precisión dimensional de la pieza fundida.
3) La temperatura del molde debe seleccionarse dentro de un rango apropiado. Generalmente, después de que la prueba sea apropiada, el control constante de la temperatura es bueno.
Las precauciones para las condiciones de moldeo por fundición se pueden resumir en los dos aspectos siguientes:
*Temperatura de fusión del material, temperatura del molde y temperatura de fusión durante la inyección;
Técnica de fundición
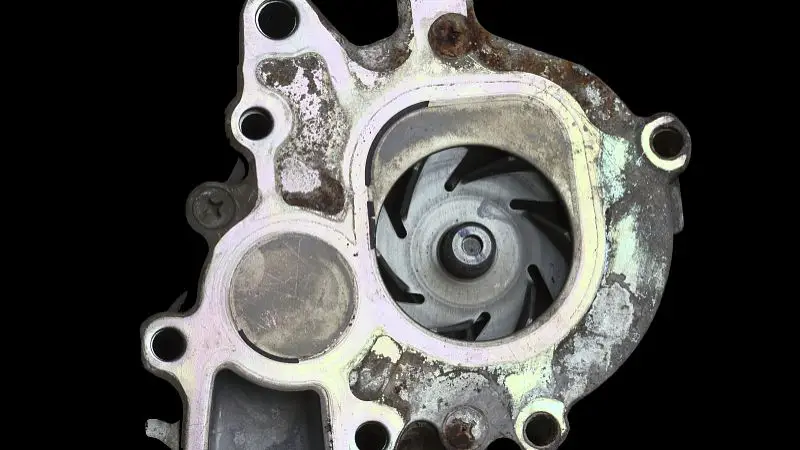
La fundición a presión es uno de los métodos de conformado de metales más avanzados.
Es una forma efectiva de obtener menos y ninguna viruta. Es ampliamente utilizado y se desarrolla rápidamente.
El tamaño y el peso de la pieza fundida dependen de la potencia de la máquina de fundición a presión.
Debido al aumento de potencia de la máquina de fundición a presión, la forma y el tamaño de la pieza fundida pueden variar desde unos pocos milímetros hasta 1-2 m;
El peso puede variar desde unos pocos gramos hasta decenas de kilogramos.
Se pueden fundir en el extranjero piezas de fundición de aluminio con un diámetro de 2 my un peso de 50 kg.
La fundición a presión ya no se limita a la industria del automóvil y la industria de instrumentos, sino que se ha expandido gradualmente a otros sectores industriales como la maquinaria agrícola, la industria de máquinas herramienta, la industria electrónica, la industria de defensa nacional, la tecnología informática, los equipos médicos, los relojes, las cámaras y el hardware de la agenda. y otras decenas de industrias, específicamente: repuestos para automóviles, accesorios para muebles, accesorios para baños (sanitarios), repuestos para iluminación, juguetes, máquinas de afeitar, pasadores de corbata, repuestos eléctricos y electrónicos, hebillas de cinturones, cajas de relojes, adornos metálicos, cerraduras, cremalleras, etc. .
En el aspecto de la tecnología de fundición a presión, han surgido nuevas tecnologías como la fundición a presión al vacío, la fundición a presión oxigenada, la fundición a presión densa y de alta velocidad y la aplicación de núcleos solubles.
Desempeñará un muy buen papel en la promoción de la industria de fundición a presión de China.
Desarrollo
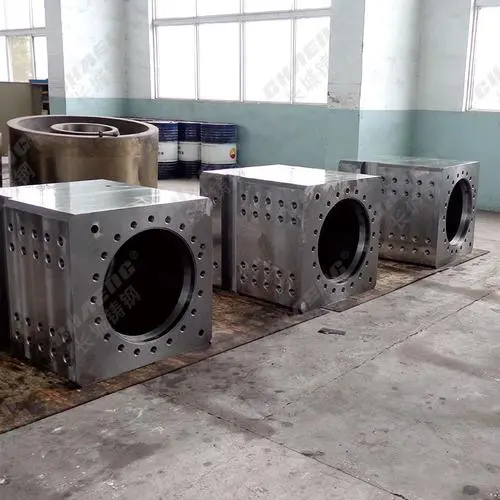
La producción de piezas fundidas a presión requiere máquinas y equipos de fundición a presión. Las máquinas de fundición a presión son la base de la producción de fundición a presión.
El nivel técnico del equipo de fundición a presión determina la calidad y el nivel de las piezas fundidas.
Por lo tanto, para promover el desarrollo de la industria de fundición a presión, debemos dar prioridad al desarrollo de equipos de fundición a presión.
China es un gran país en el sector de la fundición a presión, pero aún es necesario mejorar su nivel de tecnología de producción y equipamiento industrial.
El Duodécimo Plan Quinquenal de China indica claramente que la tarea principal del desarrollo de la industria de la fundición es dar prioridad al desarrollo de equipos técnicos importantes, incluidas "unidades de fundición de máquinas de fundición a presión de gran tonelaje", con el objetivo de proporcionar apoyo de equipos para la actualización tecnológica de empresas de fundición a presión.
El desarrollo de tecnología y equipos de fundición a presión ayudará a mejorar el nivel de maquinaria y equipos de fundición a presión, a fin de mejorar la calidad y el nivel técnico de las piezas fundidas y promover el desarrollo de la industria de la fundición a presión.