¿Qué es la soldadura por pulverización?
La soldadura por pulverización implica calentar un recubrimiento en polvo de aleación autosoluble precalentado a un rango de temperatura de 1000 a 1300 ℃, fundir las partículas, hacer flotar la escoria en la superficie del recubrimiento y dispersar el boruro y el siliciuro en el recubrimiento. Este proceso permite una buena combinación entre las partículas y la superficie del sustrato.
El depósito final forma una estructura cristalina metálica densa y crea una capa de unión metalúrgica de aproximadamente 0,05-0,1 mm con la matriz. Esta capa de unión tiene una resistencia de aproximadamente 400 MPa, excelente resistencia al impacto, resistencia al desgaste y resistencia a la corrosión, al tiempo que exhibe una apariencia similar a un espejo.
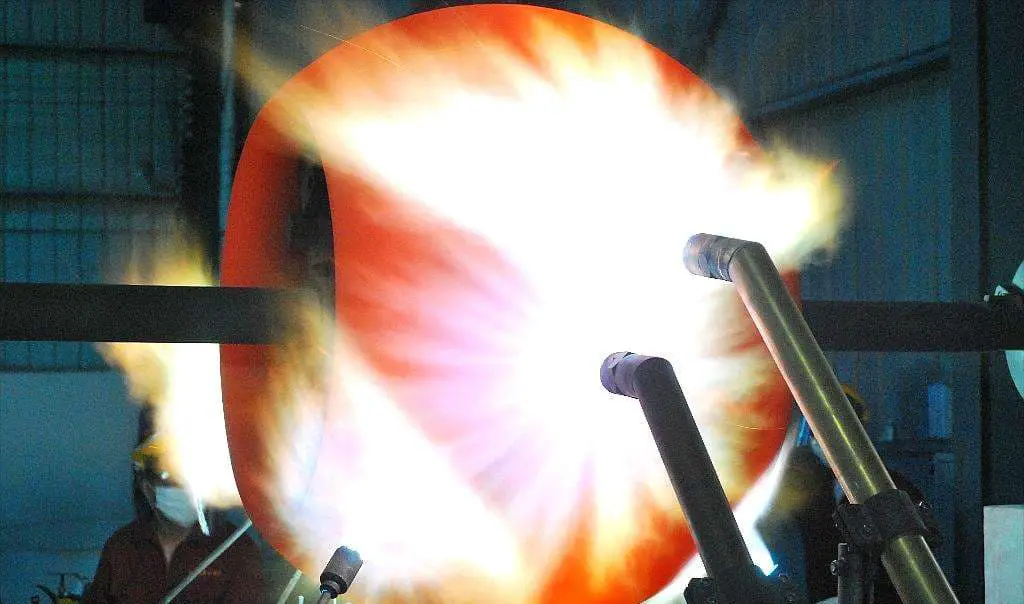
Ventajas de la soldadura por pulverización
En comparación con el recubrimiento por pulverización, el recubrimiento por soldadura por pulverización ofrece importantes ventajas. Sin embargo, debido a la alta temperatura que alcanza la matriz durante el proceso de reflujo, hasta 900°C, puede producirse una mayor deformación térmica, lo que conlleva ciertas limitaciones en el ámbito de aplicación de la soldadura por pulverización.
Las piezas y materiales adecuados para la soldadura por pulverización son generalmente:
① Piezas vulnerables que requieren una alta dureza superficial y buena resistencia al desgaste bajo cargas de impacto, como hojas de lijadora, placas de dientes de trituradoras, dientes de cucharón de excavadora, etc.
② Piezas grandes y vulnerables con geometrías simples, como ejes, émbolos, correderas, cilindros hidráulicos y placas de canal.
③ Materiales que incluyen acero con bajo contenido de carbono, acero con contenido medio de carbono (menos del 0,4% de carbono), acero estructural que contiene menos del 3% de manganeso, molibdeno y vanadio, acero inoxidable de níquel-cromo, hierro fundido y otros materiales similares.
Polvo de aleación autofundente para soldadura por pulverización
El polvo de aleación autofundible se compone de níquel, cobalto y hierro como materiales base. Se añaden cantidades apropiadas de elementos de boro y silicio para que sirvan como agentes desoxidantes, formadores de escoria, fundente de soldadura y para reducir el punto de fusión de la aleación. Este tipo de aleación es adecuado para refundir el recubrimiento con llama de acetileno-oxígeno.
Hay muchos tipos de polvos domésticos de aleaciones autofundibles disponibles. Los polvos de aleación a base de níquel tienen una fuerte resistencia a la corrosión, resistencia a la oxidación hasta 650 °C y una fuerte resistencia al desgaste.
El polvo de aleación a base de cobalto se caracteriza por una excelente dureza al rojo, lo que le permite mantener una buena resistencia al desgaste y a la corrosión hasta 700°C.
El polvo de aleación a base de hierro tiene una resistencia superior al desgaste abrasivo en comparación con los otros dos tipos.
Proceso de soldadura por pulverización
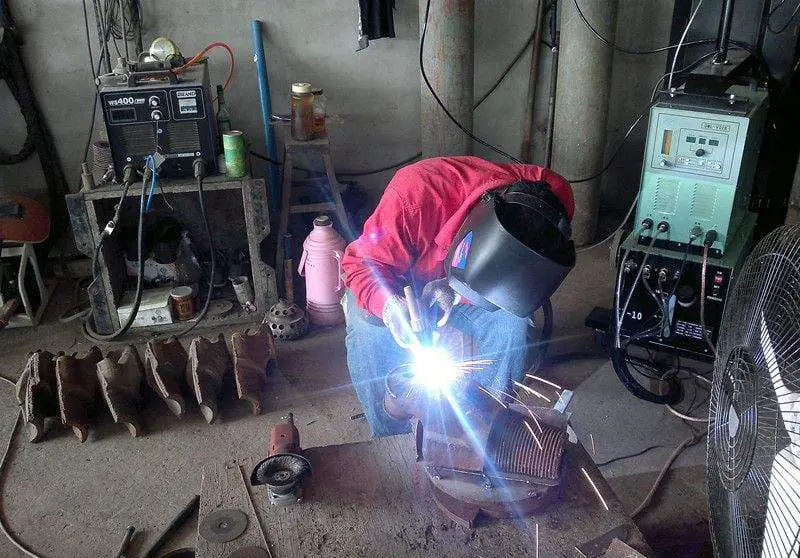
El proceso de soldadura por pulverización es esencialmente similar al de pulverización. Sin embargo, en la soldadura por pulverización, se realiza un proceso de reflujo adicional durante el procedimiento de pulverización del polvo.
La soldadura por pulverización comprende dos tipos: soldadura por pulverización en un paso y soldadura por pulverización en dos pasos.
Antes de iniciar el proceso es necesario tener en cuenta los siguientes puntos:
① La capa de cementación o nitruración presente en la superficie de la pieza debe eliminarse durante el pretratamiento.
② La temperatura de precalentamiento de la pieza de trabajo debe ser de 200-300°C para acero al carbono común y de 350-400°C para acero austenítico resistente al calor. Para el precalentamiento se debe utilizar una llama de carbón neutra o débil.
Es importante señalar que el espesor de la capa pulverizada se reduce aproximadamente un 25% después de la refundición. Por lo tanto, este factor debe tenerse en cuenta al medir el espesor de la capa caliente después de la pulverización.
Soldadura por pulverización en un solo paso.
El método de un solo paso implica alternar entre rociar y fusionar una sección a la vez usando la misma pistola rociadora.
Se encuentran disponibles pistolas de soldadura por pulverización medianas y pequeñas.
Antes de comenzar, precalentar la pieza y aplicar una capa protectora de 0,2 mm, sellando bien la superficie para evitar la oxidación.
Empiece a pulverizar y fundir desde un extremo, manteniendo una distancia de 10-30 mm.
Calentar la capa protectora parcialmente en secuencia hasta que la masa fundida comience a humedecerse sin fluir. Repita el proceso, pulverizando y derritiendo el polvo hasta que alcance el espesor predeterminado y la superficie presente un reflejo “espejo”. Luego continúe expandiéndose hacia adelante hasta cubrir toda la superficie con la capa de pulverización y soldadura.
Si el espesor es insuficiente, repetir el proceso.
El método de un solo paso es adecuado para piezas pequeñas o áreas pequeñas que requieren soldadura por pulverización.
Método de soldadura por pulverización en dos pasos.
El método de dos pasos consiste en aplicar primero la capa de spray y luego fundirla nuevamente.
Se utilizan pistolas pulverizadoras de alta potencia, como las de soldadura SpH-E y pistolas pulverizadoras, para derretir completamente el polvo de aleación en la llama y crear una capa de depósito de deformación plástica en la superficie de la pieza de trabajo.
El polvo a base de hierro debe pulverizarse utilizando una llama de carbón débil, mientras que para los polvos a base de níquel y cobalto se deben usar llamas neutras o de carbón débil.
Cada capa de pulverización de polvo debe tener menos de 0,2 mm de espesor y la pulverización repetida debe lograr el espesor de reflujo deseado, generalmente de 0,5 a 0,6 mm.
Si se requiere una capa gruesa de soldadura por pulverización y la refundición no es suficiente, se puede pulverizar y refundir varias veces.
El reflujo es el proceso clave en el método de dos pasos y debe realizarse inmediatamente después de la pulverización.
Se debe utilizar una llama suave y potente, neutra o una llama carbonizada débil.
La distancia de pulverización debe ser de unos 20-30 mm y el ángulo entre la llama y la superficie debe ser de 60°-75°.
Comenzando a unos 30 mm del recubrimiento, la velocidad de fusión debe controlarse adecuadamente y el recubrimiento debe calentarse hasta que aparezca un reflejo "espejo" del recubrimiento antes de refundir la siguiente parte.
Durante la refundición, es necesario evitar una fusión excesiva (es decir, agrietamiento de la superficie del espejo), escurrimiento del metal de recubrimiento u oxidación de la superficie debido a un tiempo de calentamiento local excesivo.
Durante la refundición multicapa, la capa anterior debe enfriarse a aproximadamente 700°C y la escoria de la superficie debe eliminarse antes de la pulverización secundaria.
La refusión no debe realizarse más de tres veces.
Enfriamiento de la pieza de trabajo.
Las piezas de acero con contenido medio y bajo de carbono, las piezas de acero de baja aleación y las piezas fundidas de hierro para soldar de capa fina con formas simples se pueden enfriar de forma natural en el aire.
Sin embargo, para las piezas fundidas de hierro con una capa de soldadura gruesa y una forma compleja, las piezas fundidas de acero aleado con alto contenido de manganeso, cobre y vanadio y piezas con alta dureza deben enterrarse en pozos de cal para un enfriamiento lento.
Diferencia de proceso entre pulverización y soldadura por pulverización
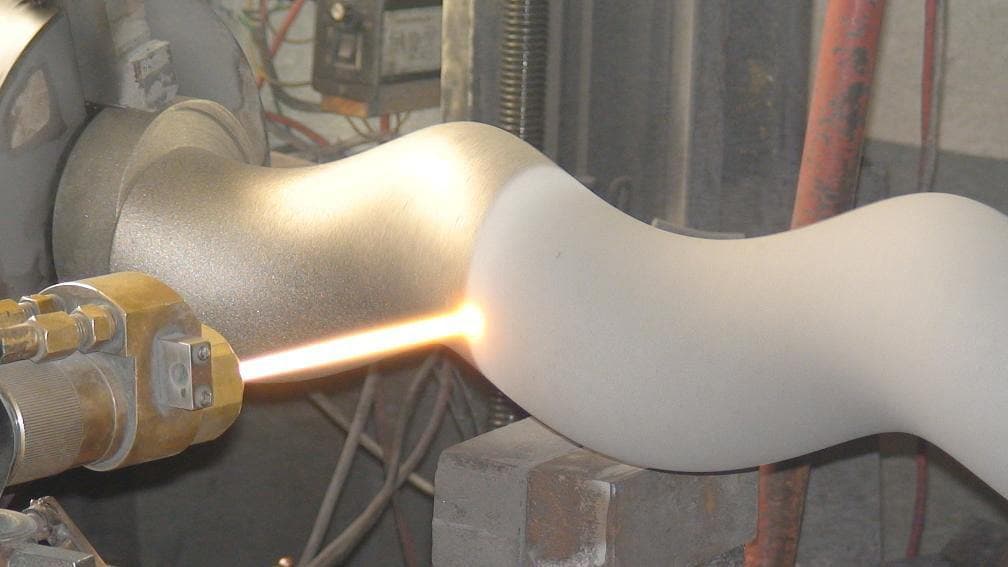
La combinación de capa de pulverización y capa de soldadura por pulverización con metal base es diferente.
Cuando se calienta aluminio recubierto de níquel con un haz de llama pulverizado, se produce una reacción química exotérmica y la eliminación del óxido con chorro de arena alcanza Sa3, RZ>50 μm. La superficie de acero al carbono forma un recubrimiento de unión mecánica con una capa inferior de unión micrometalúrgica y una capa de trabajo, que también produce un efecto de "gancho de anclaje". Por el contrario, la unión entre la capa de soldadura por pulverización y el sustrato es un revestimiento de unión puramente metalúrgico.
Los diferentes materiales de pulverización requieren el uso de polvo de aleación autofundible para la soldadura por pulverización, mientras que la pulverización requiere un polvo de baja autofusión, que no es necesariamente un polvo de aleación autofundible.
Se pueden usar varios polvos de aleaciones autofundibles tanto para soldadura por aspersión como para soldadura por aspersión, pero el polvo en aerosol no tiene autofusión. Por lo tanto, sólo se puede utilizar para pulverización y no para el proceso de soldadura por pulverización.
La pieza de trabajo se calienta de manera diferente durante la pulverización y la soldadura por pulverización, y la temperatura de precalentamiento antes de la pulverización también es diferente. Como resultado, la microestructura y las propiedades de la pieza después de la pulverización también son diferentes.
La densidad del recubrimiento también difiere, ya que la capa de soldadura por pulverización es densa, mientras que el recubrimiento por pulverización tiene algunos poros.
Además, la capacidad de carga es diferente. Generalmente, el recubrimiento por pulverización puede resistir el contacto en grandes áreas y se utiliza principalmente en superficies de trabajo lubricadas, superficies de contacto y otras condiciones de trabajo con menos estrés. Sin embargo, el recubrimiento de soldadura por pulverización puede soportar grandes fuerzas de impacto, tensiones de extrusión o tensiones de contacto.
Aplicación de soldadura por pulverización
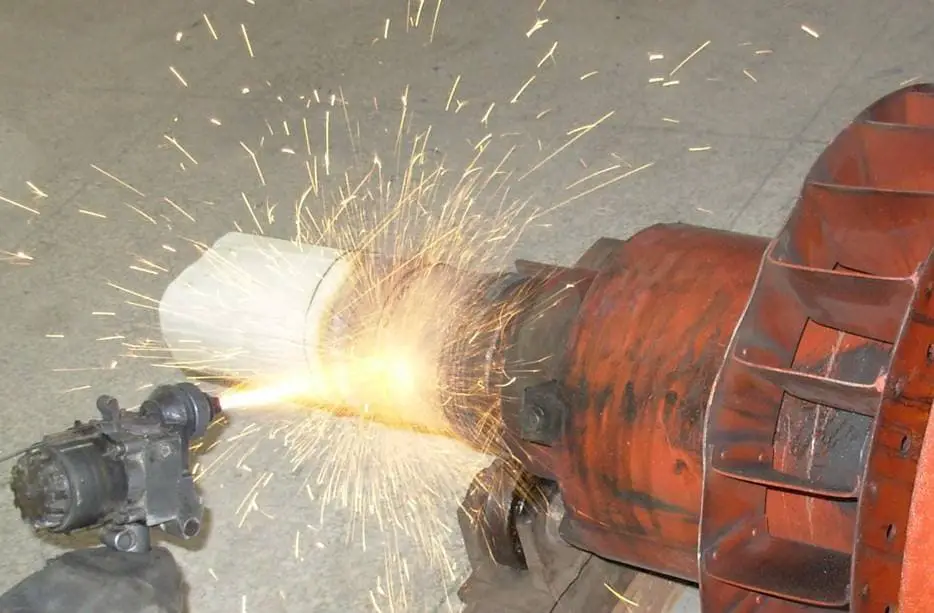
(1) La carga superficial sobre piezas fabricadas con diversos aceros al carbono y aceros de baja aleación es significativa, especialmente bajo cargas de impacto.
Para piezas con una fuerza de unión entre el revestimiento y el sustrato de 350-450 N/mm 2 , dureza de la soldadura por pulverización HRC150 ≤ 65, espesor del revestimiento que oscila entre 0,3 y varios milímetros y rugosidad de la superficie de la capa de soldadura por pulverización después del rectificado que alcanza Ra0,4-0,1 μm por encima.
(2) Cuando se utiliza en medios corrosivos, el recubrimiento debe ser compacto y libre de poros.
(3) El diseño de la superficie original de la pieza adopta enfriamiento, carburación, nitruración, cromado duro y otros procesos, que requieren que la superficie tenga una alta dureza.
(4) El entorno de trabajo de la pieza de trabajo es deficiente, como fuerte desgaste abrasivo, desgaste por erosión, cavitación, etc.
(5) El proceso de soldadura por pulverización de polvo de aleación de llama de oxiacetileno es adecuado para reforzar o reparar superficies de diversas piezas de acero al carbono y acero de baja aleación, pero se deben observar algunas características de los materiales de las piezas.
Cuando el coeficiente de expansión lineal del material base es muy diferente al de la capa de soldadura por aspersión de aleación, es decir, menor que 12 × 10 -6 /℃ o mayor que 12 × 10 -6 /℃, se debe utilizar este proceso. con precaución para evitar grietas.
Si el contenido de elementos con alta afinidad por el oxígeno en el metal base es superior al 3%, como tungsteno y molibdeno, el contenido total de aluminio, magnesio, cobalto, titanio, molibdeno y otros elementos es superior al 0,5%, o el azufre. El contenido en acero es mayor, también causará dificultades para la soldadura por pulverización.
Esto ocurre porque estos materiales generan una película de óxido densa y estable bajo la acción del oxígeno, bloqueando el efecto humectante de la aleación fundida sobre la base.
Durante la refundición, la aleación líquida rodará como cuentas, como “gotas de sudor”.
Por lo tanto, cuando se utiliza el proceso de soldadura por pulverización, se debe prestar atención a la adaptabilidad de este proceso al material base pulverizado.
(6) Materiales metálicos que pueden soldarse por pulverización sin tratamiento especial:
① Acero estructural al carbono con contenido de carbono ≤ 0,25%.
② Aleación de acero estructural con contenido total de Mh, Mo, V, Cr y Ni <3%.
③ Acero inoxidable 18-8, acero inoxidable con níquel, acero fundido gris, hierro maleable, hierro dúctil, hierro puro con bajo contenido de carbono, cobre rojo.
(7) Los materiales metálicos que requieren un enfriamiento lento después de la soldadura por pulverización a 250-375 ℃ deben precalentarse:
① Acero estructural al carbono con contenido de carbono >0,4%;
② Acero estructural de aleación de manganeso, molibdeno y vanadio con contenido total de níquel> 3%;
③ Acero de aleación estructural con contenido de cromo ≤ 2%;
(8) Materiales metálicos que requieren recocido isotérmico después de la soldadura por pulverización:
① Acero inoxidable martensítico con contenido de cromo ≥ 13%;
② Acero estructural de aleación de níquel-molibdeno con contenido de carbono ≥ 0,4%.
Después de determinar el proceso de soldadura por pulverización, la selección del proceso de soldadura por pulverización de uno o dos pasos debe basarse en las siguientes condiciones:
(1) Si la pieza de trabajo requiere reparación local y la posición de soldadura por pulverización no puede tolerar una gran entrada de calor, utilice el proceso de soldadura por pulverización de un solo paso. Por ejemplo, mediante este proceso se puede reparar cicatrices locales en varias guías de máquinas herramienta.
(2) Si la superficie de la pieza es compleja o irregular, como ruedas dentadas, superficies de dientes de engranajes, alimentadores de tornillo, etc., utilice el proceso de soldadura por pulverización de un solo paso.
(3) Para piezas grandes que son difíciles de calentar en su conjunto, como ruedas de locomotoras y tranvías, se debe utilizar el proceso de soldadura por pulverización de un solo paso.
(4) Para piezas generales del eje que pueden girar en la máquina herramienta, utilice el proceso de soldadura por pulverización de dos pasos.
(5) La dureza del recubrimiento debe ser lo más cercana posible a la dureza de la superficie del diseño original. Por ejemplo, si la dureza de la superficie del diseño original es HRC≥55, que se logró mediante procesos de enfriamiento o tratamiento químico, se debe utilizar el polvo de “recubrimiento duro”, como Ni 15 Ni 60 Fe 65 o polvo compuesto Wc.
(6) Las superficies no conjugadas muy desgastadas, como impulsores, carcasas de bombas de lodo, dientes de las palas del cargador de rocas, superficies del alimentador en espiral, etc., deben estar hechas de polvos compuestos de alta dureza como Ni 15 Ni 60 Faith 65 o Wc.
(7) Las piezas de trabajo que no se pueden procesar en tornos y rectificadoras pero que deben procesarse solo se pueden procesar manualmente con limas y otras herramientas. Por ejemplo, para reparar cicatrices locales en la superficie del riel guía de la máquina herramienta, es necesario utilizar únicamente polvos de soldadura por pulverización de baja dureza, como SH, F 103 Ni 15 , etc.
(8) Diferencias entre los procesos de soldadura por pulverización y recubrimiento por arco:
Durante el proceso de soldadura por pulverización, la unión entre la capa de soldadura por pulverización y la matriz es una unión metalúrgica por difusión de solución, mientras que la superficie utiliza una unión metalúrgica por fusión.
La matriz no se funde durante el proceso de soldadura por pulverización, pero hay un efecto de disolución entre la capa de soldadura por pulverización y la matriz, lo que da como resultado una zona de difusión mutua de la solución entre las dos.
Dado que la matriz es insoluble, la capa de soldadura por pulverización no se diluirá con el material base. Por lo tanto, la tasa de dilución es extremadamente baja, lo que garantiza un buen rendimiento de la capa de soldadura por pulverización.
Por el contrario, la matriz de soldadura superpuesta se funde y la tasa de dilución de la capa de soldadura superpuesta es alta. El rendimiento de la capa de soldadura sólo se puede garantizar si la capa de soldadura es demasiado gruesa, lo que dificulta garantizar los bordes y esquinas del contorno de la pieza. Esto puede provocar defectos comunes, como socavaciones y colapsos de las esquinas. Sin embargo, la soldadura por pulverización no presenta tales defectos.
Características de la soldadura por pulverización de piezas de hierro fundido.
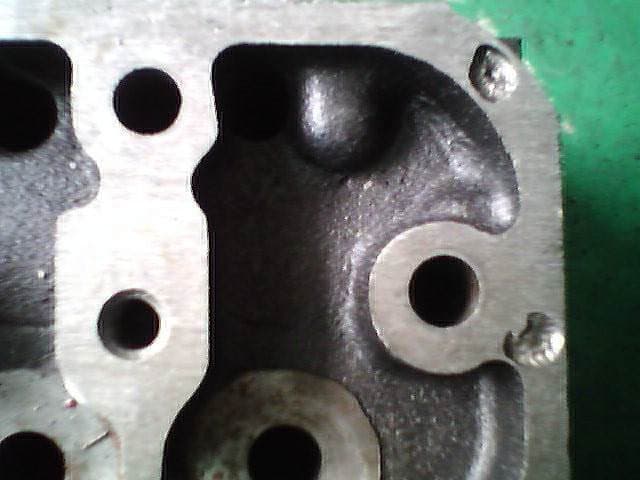
(1) El hierro fundido es una aleación de hierro y carbono con un contenido de carbono superior al 2%. Se utiliza ampliamente en diversas industrias y normalmente contiene entre un 2,5% y un 4% de carbono, entre un 1% y un 3% de silicio y pequeñas cantidades de manganeso, azufre, fósforo, etc.
El hierro fundido tiene un alto contenido de carbono, baja resistencia y es sensible a los cambios de temperatura. Durante la reparación por soldadura, experimenta calentamiento local, grandes diferencias de temperatura y velocidades de enfriamiento rápidas. Como resultado, soldar hierro fundido es un desafío.
La mala soldabilidad del hierro fundido provoca varios problemas durante la reparación por soldadura:
(2) La pieza de reparación soldada puede desarrollar fácilmente una microestructura blanca que es dura, quebradiza y difícil de mecanizar. Una estructura de este tipo también tiende a agrietarse fácilmente.
(3) Las velocidades rápidas de calentamiento y enfriamiento durante la reparación por soldadura pueden causar grietas por tensión térmica. Además, la presencia de impurezas como azufre y fósforo en el hierro fundido aumenta la probabilidad de que se produzcan grietas durante la reparación de la soldadura.
(4) La porosidad y la inclusión de escoria también son problemas comunes. Debido al alto contenido de carbono, más impurezas y velocidades de enfriamiento rápidas en el proceso de reparación de soldadura, los gases y óxidos no pueden precipitar y flotar con el tiempo, lo que lleva a la formación de porosidad o inclusión de escoria en la zona de soldadura.
Afortunadamente, la soldadura por pulverización en un solo paso con polvo de aleación de llama de oxígeno y acetileno puede resolver estos problemas satisfactoriamente.
(5) El punto de fusión del polvo de aleación utilizado en la soldadura por pulverización es menor que el de la matriz. Durante la refundición, la matriz de hierro fundido no se funde, evitando así el problema de la dilución de la capa de soldadura por pulverización y la creación de una zona semifundida. En consecuencia, una correcta soldadura por pulverización no produce una microestructura blanca en la zona de reparación de la soldadura, facilitando el procesamiento.
Además, debido a que la matriz no se funde, naturalmente evita que impurezas como el azufre y el fósforo se fundan en la capa de soldadura por aspersión, lo que ayuda a prevenir el agrietamiento.
(6) El proceso de soldadura por pulverización de un solo paso implica menos entrada de calor al sustrato y tiene un efecto térmico menor sobre el sustrato, lo que lo hace más eficaz para controlar el agrietamiento por tensión térmica. El bajo aporte de calor resulta especialmente ventajoso a la hora de reparar piezas con alta precisión dimensional.
Además, el uso de calentamiento con llama de oxígeno y acetileno, que es más lento que el enfriamiento por soldadura eléctrica, también es útil para prevenir grietas y deformaciones.
(7) El polvo de aleación utilizado en la soldadura por pulverización contiene fuertes elementos desoxidantes como el boro y el silicio. Estos elementos protegen a otros elementos del polvo de la quema oxidativa y reducen los óxidos en la superficie de la matriz, evitando así la formación de poros y la inclusión de escoria.
(8) La capa de soldadura por pulverización tiene una estructura compacta y plana, está bien formada, no tiene socavaduras y solo requiere una pequeña cantidad de procesamiento. Esto se traduce en ahorro de material y alta eficiencia. Las piezas de hierro fundido soldadas por pulverización generalmente utilizan polvo de aleación a base de níquel SH F103, Ni15, etc. Sin embargo, el polvo de aleación a base de hierro tiene un alto punto de fusión, una gran fragilidad, un impacto significativo en la matriz y un rendimiento deficiente.
(9) Durante la soldadura por pulverización, el objetivo principal de precalentar la pieza es eliminar la humedad de la superficie de la pieza y generar cierta expansión térmica. Esto reduce la diferencia de temperatura, minimizando así el estrés térmico y promoviendo una mejor fuerza de unión de la capa de soldadura por pulverización.
As temperaturas de pré-aquecimento geralmente variam de 250-300°C para aço, 450-500°C para aço inoxidável austenítico, 350-400°C para aço inoxidável níquel-cromo e 250-300°C para aço de baixa liga e hierro fundido. Para piezas pequeñas y acero que se oxida fácilmente, la temperatura de precalentamiento es más baja.
El espesor de la capa de soldadura por pulverización depende de las características de expansión térmica y contracción en frío de la pieza de trabajo después de la pulverización. La contracción después de la refundición suele rondar el 25-30%. Por lo tanto, al determinar el espesor del recubrimiento, se deben tener en cuenta la tolerancia de mecanizado y el diámetro de la pieza antes de la pulverización, junto con la contracción.
El espesor del recubrimiento por pulverización se calcula de la siguiente manera: Espesor del recubrimiento antes de la refundición = (espesor de la capa de soldadura por pulverización + tolerancia de mecanizado) ÷ (1-0,3).
Lectura relacionada: ¿Cómo soldar hierro fundido?
Circunstancias en las que no se puede utilizar el proceso de soldadura por pulverización.
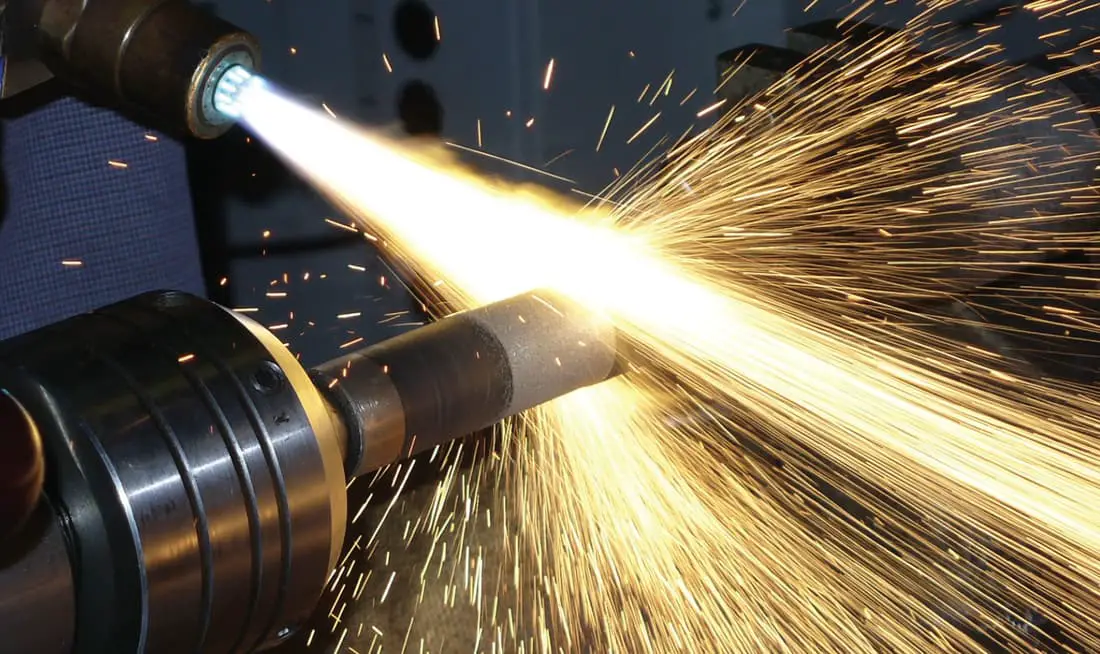
(1) Materiales con punto de fusión inferior al de las aleaciones, como el aluminio y sus aleaciones, el magnesio y sus aleaciones, el latón y el bronce.
(2) La pieza de trabajo es un eje delgado o una placa muy delgada que no debe deformarse.
(3) Los requisitos de diseño originales de la pieza son muy estrictos y la estructura metalográfica no puede cambiar.
(4) Acero de aleación de níquel-cromo-molibdeno con alta templabilidad.
(5) Acero martensítico con alto contenido en cromo y contenido de cromo superior al 18%.
(Nota: La soldadura por pulverización de alta precisión se puede realizar en ejes largos con un diámetro exterior de más de 28 mm y una longitud de menos de 8 m).
Puntos clave del proceso de soldadura por pulverización para piezas fundidas de hierro
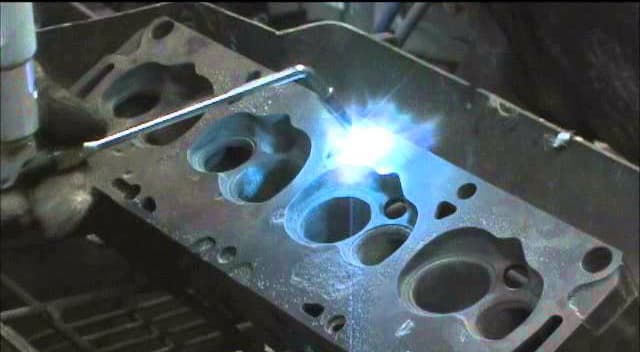
① Hay muchas piezas en vehículos y equipos mecánicos hechas de hierro fundido, y son inevitables varios problemas durante la fabricación o el uso. El proceso de soldadura por aspersión con llama de oxígeno y acetileno no solo es una forma eficaz de fortalecer el hierro fundido, sino también un medio ideal para reparar diversos defectos y daños, como agujeros de arena, agujeros de aire, desgaste y otros daños en las piezas fundidas.
② La soldadura por pulverización se utiliza principalmente para reparar defectos locales de piezas de fundición de hierro, que varían en tamaño y profundidad. Es adecuado para soldadura por pulverización en un solo paso. Se deben utilizar pistolas pulverizadoras de pequeña potencia tanto como sea posible para reducir la entrada de calor al sustrato, dependiendo de las piezas y la reparación de soldadura requerida. Generalmente, se seleccionan QH-1/h, QH-2/h, QH-4/h, etc.
③ Durante la soldadura por pulverización, se debe preferir el polvo de aleación a base de níquel (serie Ni-B-Si) debido a la mala soldabilidad de las piezas de hierro fundido. El punto de fusión del polvo de aleación a base de níquel es generalmente de 950 ~ 1050 ℃ y la matriz no se funde durante la refundición. Al mismo tiempo, la capa de soldadura por pulverización en polvo a base de níquel con bajo contenido de carbono tiene baja dureza y buena plasticidad. La relajación de la tensión de la soldadura por pulverización es útil para prevenir grietas, lo cual es extremadamente importante para los operadores no calificados.
④ Al seleccionar las especificaciones de soldadura por pulverización, se deben considerar factores como el material de hierro fundido, el tamaño de las piezas defectuosas y los requisitos de las condiciones de trabajo. Es importante garantizar la energía de llama necesaria y, al mismo tiempo, minimizar la entrada de calor al sustrato. Se deben seguir los límites apropiados de presión de oxígeno y gas acetileno, y la distancia de pulverización y fusión se debe ajustar adecuadamente durante la pulverización y refundición del polvo para controlar la entrada de calor.
⑤ Los pequeños defectos locales, como orificios de aire y arena, se pueden reparar soldando sin precalentar antes de la soldadura por pulverización. El área de calentamiento alrededor de la capa de soldadura por aspersión debe minimizarse para que el área de alta temperatura sea lo más pequeña posible.
⑥ Para la reparación de defectos locales pequeños y profundos, es adecuada la soldadura por pulverización continua. Este método tiene una alta tasa de deposición de polvo, un rápido crecimiento del espesor y una alta eficiencia, pero requiere tecnología de operación calificada para coordinar la cantidad de alimentación de polvo con la velocidad de pulverización y fusión para lograr una pulverización y penetración uniformes.
⑦ Para defectos grandes y profundos, se puede utilizar soldadura por pulverización intermitente para evitar un aumento del estrés térmico debido al calentamiento excesivo del sustrato. También se pueden utilizar soldadura eléctrica y soldadura por pulverización, y se pueden utilizar varillas de soldadura para rellenar las partes inferior y superior para la soldadura por pulverización. Si el espesor de la pared de la pieza fundida es grande, se puede utilizar alambre previamente rociado para aumentar la resistencia de la unión, evitar que la capa de soldadura por rociado se desprenda del metal base y eliminar parte del estrés térmico de la soldadura por rociado.
⑧ Las piezas fundidas grandes y complejas para la soldadura por pulverización a menudo experimentan un alto estrés térmico, por lo que se deben tomar medidas para reducir la acumulación de tensión durante la soldadura por pulverización, como el uso de métodos de reducción del estrés por calentamiento y el método de simetría de la subsección. El precalentamiento antes de soldar y el enfriamiento lento después de soldar también pueden lograr buenos resultados.
⑨ Es importante controlar la temperatura de reflujo durante la soldadura por pulverización. Si la temperatura es demasiado alta, los elementos de aleación pueden quemarse, la matriz puede sobrecalentarse e incluso derretirse, lo que provoca que el carbono del hierro fundido entre en la capa de soldadura por pulverización. Esto aumenta el contenido de carbono, la dureza y reduce la plasticidad, lo que puede provocar un mayor estrés térmico que conduce a la formación de grietas. Sin embargo, si la temperatura de reflujo es demasiado baja, puede provocar inclusión de cenizas o impenetrabilidad y afectar la fuerza de la unión. Los operadores deben prestar atención a la condición de la superficie del recubrimiento durante el reflujo y retirar la pistola de reflujo inmediatamente tan pronto como aparezca el "reflejo de espejo", lo que indica que el polvo se ha derretido y la escoria ha flotado. Las piezas refundidas no se deben recalentar.