El acero para matrices para trabajo en caliente H13 tiene una excelente resistencia térmica, resistencia a la fatiga en frío y en caliente y resistencia a la erosión del metal líquido. Como resultado, encuentra amplias aplicaciones en matrices de extrusión en caliente, matrices de fundición a presión de aleaciones de aluminio y otros tipos de matrices.
En el proceso de uso, el rendimiento de impacto de la matriz determina su vida útil, ya que la matriz debe soportar una fuerza de impacto sustancial.
La tecnología de fundición a presión se utiliza predominantemente en la producción de piezas de automóviles, como soportes, embragues y cárteres, debido al crecimiento de la industria del automóvil.
Las dos características importantes de la fundición a presión son la alta presión y el llenado de alta velocidad de la cavidad del molde. En comparación con el molde de extrusión, el molde de fundición a presión tiene que soportar más energía de impacto durante el proceso de producción, especialmente cuando se fabrican piezas grandes. Esto requiere el uso de acero para moldes de alta calidad.
La matriz de extrusión hecha de barras de acero H13 producidas mediante procesos convencionales y módulos relativamente pequeños puede lograr el efecto deseado en términos de longevidad.
El flujo del proceso de producción de un lote de módulos de acero H13 en una fábrica es el siguiente: pretratamiento de hierro fundido → fundición en un horno eléctrico de 20t → refinación en un horno LF (horno de refinación de cuchara) → tratamiento al vacío en un horno VD (horno de refinación al vacío) → fundición en lingotes de 16t → refundición de lingotes de 16t en horno de electroescoria con protección de gas de 16t → recocido de lingotes → calentamiento (1180 ℃, 20 h) → 45MN/producto terminado de palanquilla de forja rápida (especificación de sección: 400 mm × 500 mm) → recocido → pruebas no destructivas → inspección por muestreo.
Durante las pruebas de energía de impacto de una placa de acero, se descubrió que el rendimiento ante el impacto no cumplía con el estándar esperado.
Para identificar la causa del rendimiento de bajo impacto, investigadores como Li Yongdeng y Yang E de Daye Special Steel Co., Ltd., el Laboratorio Provincial Clave de Acero Especial de Alta Calidad de Hubei y el Instituto Huangshi de Supervisión e Inspección de Calidad de Productos de Hubei analizaron los materiales. . Identificaron el motivo del impacto energético insatisfactorio y proporcionaron una base para mejoras posteriores en la producción.
1. Inspección física y química
1.1 Análisis de composición química.
Se detectó la composición química del módulo de acero H13 con energía de impacto no calificada y los resultados cumplen con los requisitos de GB/T 1299-2014 para herramientas y troqueles de acero.
1.2 Prueba de rendimiento de impacto
La prueba de resistencia al impacto debe realizarse utilizando probetas de impacto sin muescas transversales.
Las muestras deben tomarse de la parte central del módulo y luego someterse a un tratamiento de enfriamiento y revenido después de realizar el blanco, seguido de mecanizado hasta el tamaño de muestra final.
Se probaron tres muestras y el tamaño de la muestra de impacto fue de 55 mm x 10 mm x 7 mm.
Una muestra con un buen rendimiento de impacto debería tener una energía de impacto de más de 300 J, mientras que una muestra con un rendimiento de impacto deficiente debería tener una energía de impacto de menos de 100 J.
1.3 Análisis SEM de fractura de muestra de impacto.
Después de una limpieza ultrasónica, se analizó la superficie de fractura de la muestra de impacto mediante un microscopio electrónico de barrido.
Para las muestras que no alcanzaron la energía de impacto esperada, la superficie de fractura parece relativamente plana en general. Tras un examen más detenido, se observaron diversos grados de características de fractura intergranular en el área de origen de la fractura.
Las muestras con mayor energía de impacto mostraron áreas más pequeñas de fractura intergranular, mientras que aquellas con menor energía de impacto mostraron áreas más grandes de fractura intergranular.
Las muestras que alcanzaron la energía de impacto esperada exhibieron una morfología de fractura Bremsstrahlung, sin observarse grietas intergranulares. Además, no se encontraron defectos como grandes inclusiones en la superficie de la fractura.
Las morfologías de fractura de muestras con energía de impacto baja y alta se muestran en la Figura 1 y la Figura 2, respectivamente.
En general, la fractura intergranular es una forma de límite de grano.
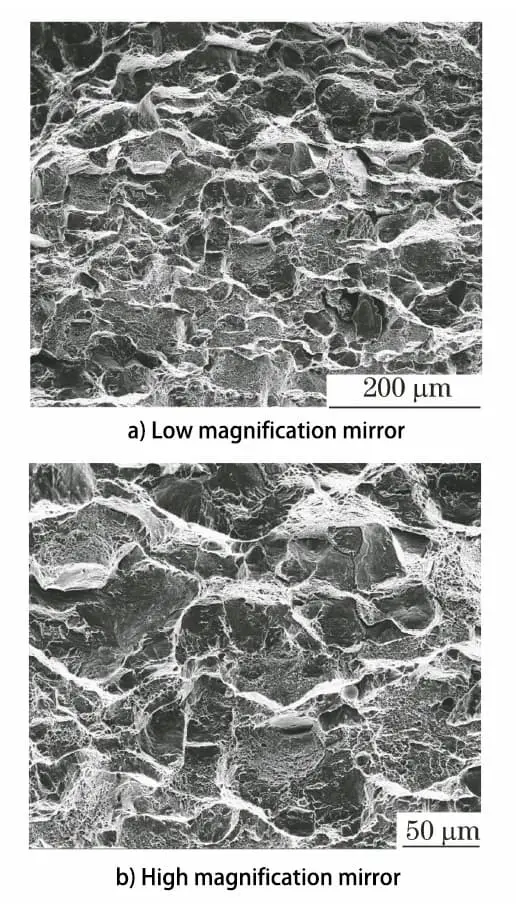
Fig. 1 Micromorfología de fractura de una muestra de energía de bajo impacto

Fig. 2 Micromorfología de fractura de una muestra de energía de alto impacto
1.4 Inspección metalográfica
Después de lijar y pulir la superficie de fractura de la muestra de impacto, se atacó con ácido nítrico y alcohol y se observó bajo un microscopio metalográfico.
Se observó que era evidente el límite de grano local de la muestra con baja energía de impacto. El carburo estaba agrupado y en bandas en el límite del grano y no se encontraron carburos primarios significativos.
Se tomaron muestras recocidas del mismo lote con baja energía de impacto. Después de lijar, pulir y grabar con alcohol y ácido nítrico, la microestructura mostró perlita esférica. Los carburos esféricos se distribuyeron localmente en cadenas y no se encontró ninguna agregación aparente de carburos. Esto indica que la segregación en el proceso de fundición se encuentra en un nivel normal.
La Figura 3 muestra la microestructura de las muestras con baja energía de impacto.

Fig. 3 Microestructura de fractura de una muestra de energía de bajo impacto
Para la muestra con la mayor energía de impacto, la estructura templada y revenida muestra una martensita revenida homogénea y no se encontraron carburos en los límites de grano obvios.
Por otro lado, la estructura recocida correspondiente muestra una perlita esferoidal uniforme y no se observó ningún fenómeno de red de agregación de carburos (ver Fig. 4).

Fig. 4 Microestructura de fractura de una muestra de energía de alto impacto
2. Análisis integral
La composición química del acero H13, fundido mediante refundición de electroescoria, cumple con los requisitos de la norma GB/T 1299-2014.
Las observaciones de la microestructura indican que no hay acumulación aparente de carburo o segregación de bandas, y no hay inclusiones no metálicas significativas en la superficie de la fractura. Esto indica que el proceso de fundición está bajo control normal.
Con base en el análisis de la micromorfología y estructura metalográfica de la fractura por impacto, la muestra con baja energía de impacto presenta características intergranulares, y presenta redes evidentes de carburos en su estructura.
La muestra con alta energía de impacto tiene una morfología de hoyuelos y su estructura es uniforme.
La fractura intergranular ocurre cuando el límite de grano del acero soporta la carga de impacto porque es relativamente débil.
La razón principal de la baja tenacidad al impacto del acero H13 es la precipitación de carburos secundarios a lo largo del límite de grano. Las investigaciones indican que los carburos que se encuentran en el acero H13 son principalmente V8C7, Cr23C6 y Cr3C2 (Cr2VC2).
El calentamiento insuficiente durante la forja y el enfriamiento inadecuado después del proceso contribuyen a la acumulación de estos carburos a lo largo del límite de grano. Esta acumulación debilita el límite de grano y, como resultado, reduce la tenacidad al impacto del acero.
Para mejorar las propiedades de impacto del acero H13, es fundamental evitar la precipitación de carburos secundarios a lo largo del límite de grano. Esto se puede lograr controlando estrictamente la temperatura de calentamiento antes de la forja y la velocidad de enfriamiento después del proceso. De este modo se puede reducir eficazmente la precipitación de carburos reticulares.
El refinado y dispersión de carburos en acero se puede lograr mediante la homogeneización a alta temperatura, aumentando la deformación durante la forja y disminuyendo la temperatura final de forja. Este proceso es beneficioso para inhibir la precipitación de carburos secundarios a lo largo de los límites de los granos.
Al someter el acero H13 a un tratamiento de homogeneización a alta temperatura, se puede mejorar eficazmente la segregación de componentes que se produce durante la fundición y la solidificación, y se debilita la tendencia de los carburos y las impurezas a segregarse en los límites de los granos.
El enfriamiento rápido después de la forja puede evitar la precipitación de carburos gruesos o reticulados en el acero, así como también evitar que los carburos secundarios precipiten a lo largo de la frontera del grano para formar cadenas de carburo.
El enfriamiento rápido seguido de un recocido después de la forja puede producir una estructura de perlita esferoidal uniforme en el acero.
El aumento de la deformación durante el proceso de forjado puede mejorar la estructura interna del acero. Las grandes estructuras de fundición y los carburos eutécticos inestables pueden romperse aplicando grandes tensiones.
Si es posible, se puede emplear el proceso de forjado por recalcado y estiramiento para mejorar aún más la estructura de acero H13 y sus propiedades.
3. Conclusión y sugerencias
(1) La razón principal por la que el rendimiento de impacto transversal del acero H13 fundido por refundición de electroescoria no puede alcanzar el objetivo esperado se debe a la falta de un control adecuado sobre el proceso de forjado.
Después del tratamiento térmico, los carburos secundarios precipitan a lo largo de los límites de los granos, debilitándolos. Para mejorar eficazmente la tenacidad al impacto transversal del acero H13, es esencial evitar la precipitación secundaria de carburo en una red a lo largo del límite de grano.
(2) La resistencia al impacto del acero H13 se puede mejorar significativamente implementando un tratamiento de homogeneización a alta temperatura, aumentando la deformación de forjado, mejorando la velocidad de enfriamiento después de la forja, minimizando la segregación y previniendo la precipitación de carburo a lo largo de los límites de los granos.