En la industria del mecanizado, “precisión de mecanizado” es un término común que se utiliza con frecuencia. Esto se menciona varias veces al día y, cuando se habla con personas de la industria, siempre se habla de la precisión del mecanizado.
Surge entonces la pregunta: ¿cómo puede la máquina CNC garantizar la precisión del mecanizado?
La precisión de las máquinas herramienta CNC depende en última instancia de la precisión de la propia máquina herramienta. Esta precisión incluye varios factores, como la precisión geométrica, la precisión de posicionamiento, la precisión de posicionamiento repetido y la precisión de corte.
Precisión geométrica:
También se conoce como precisión estática, que refleja de manera integral los errores geométricos de los componentes principales de las máquinas herramienta CNC después del ensamblaje.
Precisión de posicionamiento :
Esto demuestra la precisión del movimiento de la máquina herramienta que se mide bajo el control del dispositivo de control numérico. En función del valor medido de la precisión de posicionamiento, se puede determinar la precisión ideal para mecanizar la pieza en el proceso de mecanizado automatizado de la máquina herramienta.
La precisión del posicionamiento se refiere a la diferencia entre la posición real de la pieza o herramienta y la posición estándar (posición teórica o ideal). Cuanto menor sea la diferencia, mayor será la precisión.
Garantizar un procesamiento preciso de las piezas depende de lograr una alta precisión de posicionamiento, lo cual es un requisito previo crucial.
Precisión de posicionamiento repetido
Esto se refiere a la consistencia en la precisión de la posición que se obtiene al ejecutar repetidamente el mismo código de programa en una máquina herramienta CNC. También incluye la consistencia de los resultados obtenidos al procesar un lote de piezas en las mismas condiciones, como usando la misma máquina herramienta CNC y métodos de operación, y con el mismo programa de piezas.
Precisión de corte:
Se trata de una inspección exhaustiva de la precisión geométrica y de posicionamiento de la máquina herramienta durante las operaciones de corte.
Como se indicó anteriormente, la precisión de las máquinas herramienta CNC se divide en aspectos mecánicos y eléctricos. Los aspectos mecánicos cubren la precisión del husillo, incluido el desplazamiento y la barra colectora, la precisión del husillo, la precisión del accesorio durante el procesamiento y la rigidez de la máquina herramienta.
Los aspectos eléctricos se refieren principalmente a métodos de control como el circuito semicerrado y el circuito completamente cerrado, los métodos de retroalimentación y compensación y la precisión de la interpolación durante el procesamiento.
Así, la precisión de la máquina herramienta no depende únicamente de si está completamente cerrada o no.
I. Introducción al principio
La cadena de movimiento de las máquinas herramienta CNC incluye los siguientes componentes: dispositivo CNC → servocodificador → servoaccionamiento → motor → tornillo → piezas móviles.
Dependiendo de la posición de instalación del dispositivo sensor de posición, el control se puede clasificar en tres tipos: control de circuito completamente cerrado, control de circuito semicerrado y control de circuito abierto.
Sistema de servoalimentación con control de circuito completamente cerrado
La máquina herramienta está equipada con dispositivos sensores de posición, como reglas de cuadrícula y sincronizadores de inducción lineal, que se instalan en sus partes móviles, como bancos de trabajo. Estos dispositivos proporcionan información en tiempo real sobre la posición de las piezas móviles.
Después de que el sistema CNC procesa la información, el estado de la máquina herramienta se transmite al servomotor. El servomotor compensa automáticamente cualquier error de movimiento mediante el comando del sistema.
Sin embargo, debido a que implica un control de circuito cerrado de los grandes vínculos de inercia del tornillo de avance, el par de tuercas y la mesa de la máquina herramienta, puede resultar más difícil depurar el sistema hasta un estado estable.
Además, la instalación de dispositivos de medición como reglas de cuadrícula y sincronizadores de inducción lineal puede resultar costosa y complicada, lo que puede provocar oscilaciones.
Por lo tanto, la mayoría de las máquinas herramienta en general no utilizan un control de circuito cerrado completo.
Sistema de servoalimentación con control de circuito semicerrado
Se instala un dispositivo de detección de posición en el extremo del motor de accionamiento o en el extremo de la varilla del tornillo para detectar el ángulo de rotación del tornillo o del servomotor. Esto ayuda a medir indirectamente la posición real de las piezas móviles de la máquina herramienta, que luego se envía de vuelta al sistema de control a través de retroalimentación.
Con avances en la fabricación mecánica y mejoras en la precisión de los elementos sensores de velocidad y los pasos de los tornillos, las máquinas herramienta CNC de circuito semicerrado han logrado un nivel muy alto de precisión de alimentación.
Como resultado, la mayoría de los fabricantes de máquinas herramienta han adoptado ampliamente sistemas CNC de circuito semicerrado.
II . Aplicación práctica
Sistema de control de circuito completamente cerrado
Los dispositivos de detección de posición, como reglas de cuadrícula y sincronizadores de inducción lineal, tienen distintos niveles de precisión, que van desde ±0,01 mm a ±0,003 mm. El nivel de precisión afecta la precisión del posicionamiento e incluso con un control total de bucle cerrado, pueden ocurrir errores.
La detección de posición también se ve afectada por las propiedades térmicas, específicamente la deformación térmica. Los dispositivos de medición suelen estar hechos de materiales no metálicos y el coeficiente de expansión térmica varía entre los distintos componentes de la máquina herramienta.
Este es un aspecto crítico de la precisión de la máquina herramienta y debe abordarse reduciendo la generación de calor durante el mecanizado para superar la deformación térmica causada por la temperatura. Las máquinas herramienta de alta gama utilizan varios métodos, como enfriamiento de tornillos huecos, lubricación de rieles guía y enfriamiento a temperatura constante del fluido de corte para reducir la deformación térmica.
La instalación de un dispositivo de detección de posición también es crucial. En teoría, cuanto más cerca esté del eje de transmisión (par de tornillos), más precisa será la medición. Sin embargo, debido a limitaciones de espacio estructural, solo hay dos formas de instalar la regla de rejilla: cerca del lado del tornillo guía o en el exterior del riel guía.
Aunque se recomienda optar por el primer método de instalación, puede resultar inconveniente a efectos de inspección y mantenimiento. Por otro lado, aunque se seleccionó una regla de cuadrícula de alta precisión, no pudo lograr la precisión requerida para las máquinas herramienta CNC.
En el primer caso, la posición de instalación de la regla de rejilla está relativamente cerca del eje de transmisión, pero aún se mantiene a una cierta distancia de él. Esta distancia, junto con la oscilación del objeto durante la conducción, provoca problemas en la detección y control de la regla de la cuadrícula.
Cuando el objeto impulsado oscila hacia el lado de montaje de la regla de la cuadrícula, confunde la velocidad de movimiento como insuficiente durante la detección, lo que hace que el sistema emita una señal de aceleración. Cuando el objeto en movimiento oscila hacia el otro lado, la regla de la cuadrícula confunde la velocidad de movimiento como demasiado rápida durante la detección y el sistema emite una señal de desaceleración.
Estas operaciones repetidas no mejoran el control de los ejes de coordenadas lineales de la máquina herramienta CNC, pero intensifican la vibración del objeto impulsor. Esto conduce a un fenómeno peculiar en el que el circuito completamente cerrado no es tan bueno como el circuito semicerrado.
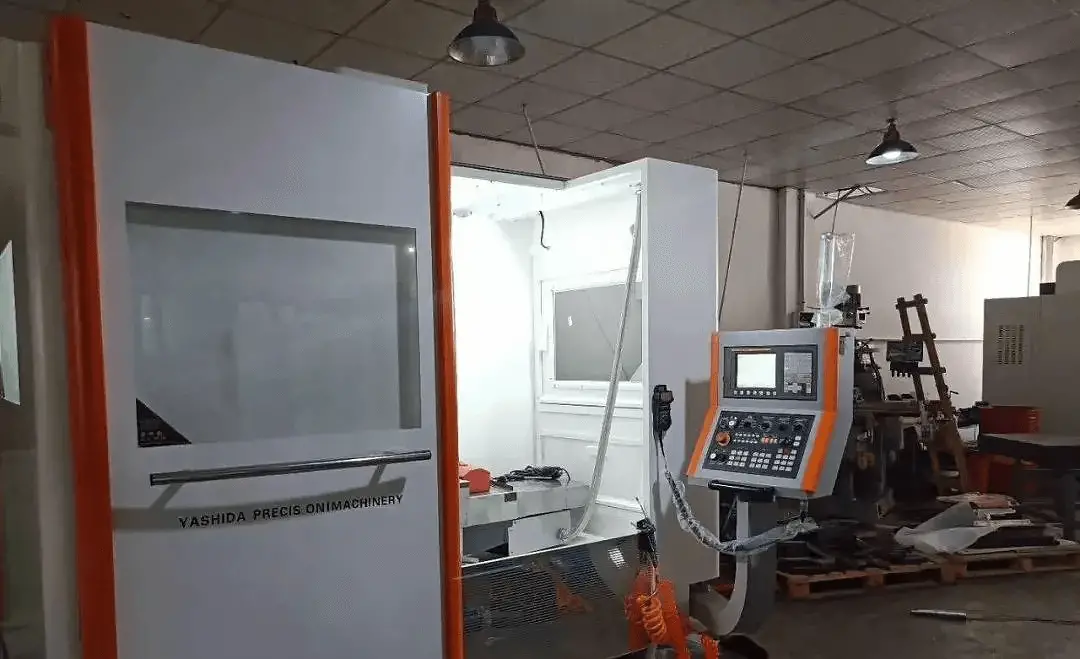
Impacto ambiental de la producción:
Generalmente, las fábricas de mecanizado tienen ambientes agresivos, donde el polvo y las vibraciones son fenómenos habituales. Sin embargo, las básculas de rejilla y los sincronizadores de inducción lineal son componentes de precisión que miden la posición relativa del movimiento mediante la reflexión de la luz.
El polvo y la vibración son los dos factores más importantes que afectan la precisión de la medición. Además, la niebla de aceite de corte y la niebla de agua son más graves durante el mecanizado de máquinas herramienta y afectan en gran medida la regla de la rejilla y el sincronizador de inducción lineal.
Por lo tanto, si se utiliza un sistema de control de circuito completamente cerrado, es esencial garantizar una instalación y un sellado adecuados y mejorar el entorno de producción. De lo contrario, la precisión de la nueva máquina herramienta, que originalmente era buena, disminuirá dentro de un año y la máquina a menudo hará sonar una alarma.
Sistema de control de circuito semicerrado
Debido a que el dispositivo de medición generalmente se instala encima del motor o del tornillo de avance, es más fácil de sellar, lo que hace innecesarios los requisitos ambientales.
El error de precisión del sistema de control de circuito semicerrado depende principalmente del espacio libre hacia adelante y hacia atrás del tornillo.
Gracias a los avances en la tecnología de procesamiento mecánico, el nivel actual de fabricación de tornillos de avance importados es relativamente alto. Los pares de tornillos de avance de alta precisión prácticamente eliminan el juego de ida y vuelta.
Además, durante el proceso de ensamblaje, el par de tornillos adopta un par de tornillos de bolas invertidas de doble hilera, que pueden eliminar por completo el juego hacia adelante y hacia atrás.
Muchas fábricas de máquinas herramienta utilizan el método de preestirado durante el ensamblaje de la máquina herramienta para eliminar el impacto de la deformación térmica en la precisión de la rosca.
Por lo tanto, el actual sistema de control de circuito semicerrado puede garantizar una alta precisión de la máquina herramienta.
Conclusión
En resumen, se puede ver que, en teoría, el control de circuito completamente cerrado puede mejorar la precisión del posicionamiento básico en comparación con el control de circuito semicerrado si no se consideran factores externos. Sin embargo, no abordar factores como el calor de la máquina, la contaminación ambiental, el aumento de temperatura, la vibración y la instalación puede llevar a un escenario en el que el control de circuito completamente cerrado funcione peor que el control de circuito semicerrado.
Si bien puede funcionar bien a corto plazo, los cambios de polvo y temperatura pueden afectar significativamente los datos de retroalimentación de medición de la regla de cuadrícula a largo plazo, reduciendo así su efectividad.
Además, si hay un problema con la regla de la cuadrícula, genera una alarma, lo que puede provocar un mal funcionamiento de la máquina herramienta.
Debido a consideraciones de costo y competitividad, se ha simplificado el control total de circuito cerrado para máquinas herramienta de costo medio y bajo. Como resultado, es posible que algunos aspectos, como el sellado y el control del aumento de temperatura, no estén bien garantizados.
En tales casos, simplemente configurar la regla de la cuadrícula no puede mejorar la precisión de la máquina herramienta y puede generar costos significativos.