El progreso del desarrollo del molde juega un papel crucial en todo el cronograma del proyecto y es una parte importante de la preparación de la producción OEM.
En los siguientes párrafos, analizaremos el proceso y el control del programa de desarrollo del molde, desde la publicación de los datos de la carrocería hasta la inspección y aceptación final del molde.
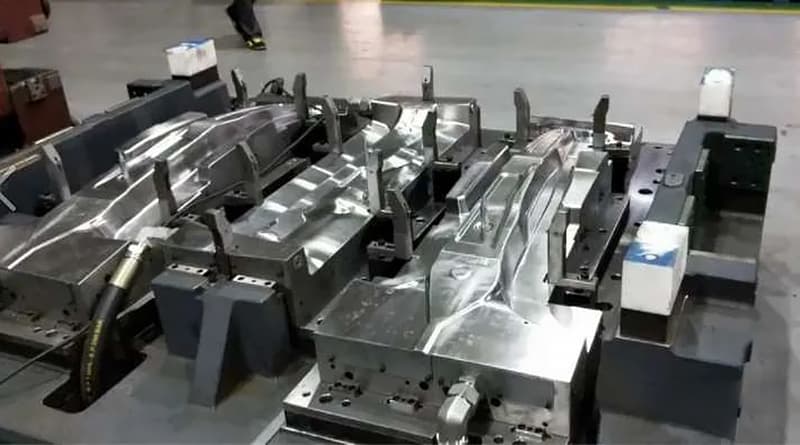
1. Divulgación de datos de procesos corporales.
El departamento de diseño de carrocerías publica modelos de simulación de productos y el personal de ingeniería del departamento de desarrollo de ingeniería lleva a cabo análisis de procesos y cotizaciones basadas en los modelos de simulación de productos (como datos comparativos para la licitación).
El modelo de simulación del proceso corporal se utiliza para la licitación de moldes y el análisis del proceso correspondiente. El proceso de licitación no se discutirá en detalle aquí. A continuación, hablaremos brevemente sobre la gestión del desarrollo de moldes una vez finalizada la fábrica de moldes.
2. Análisis de viabilidad del proceso de fabricación de piezas de carrocería (desarrollador de moldes y departamento de desarrollo de ingeniería)
Después de recibir el modelo de simulación del proceso de carrocería, el desarrollador del molde realiza un análisis de viabilidad del proceso de fabricación de cada pieza. En principio, las fábricas de moldes deben realizar análisis CAE (es decir, análisis de simulación de formabilidad de piezas) en todas las piezas recientemente desarrolladas.
El papel del análisis CAE:
- A través del análisis CAE, podemos observar el proceso de conformado de chapa de manera más intuitiva.
- Acortar el ciclo de diseño y análisis de moldes.
- Anticípese a la posibilidad de que aparezca moho.
- Adopte un diseño optimizado para minimizar el consumo de moldes y materiales de acero y reducir los costos de fabricación.
- Identifique posibles peligros de moldes y piezas antes de la fabricación.
- Garantice la racionalidad del diseño de moldes y reduzca los costos de diseño.
- Con base en el análisis de los problemas potenciales de las piezas, la fábrica de moldes puede proponer sugerencias razonables para cambios de diseño de manera oportuna y promover el trabajo de desarrollo de manera más eficiente.
El departamento de desarrollo puede utilizar plenamente la experiencia de depuración de producción en el sitio y verificar si los parámetros del proceso y el alargamiento suplementario son razonables según los resultados del análisis CAE de las piezas proporcionadas por la fábrica de moldes.
En respuesta a riesgos como arrugas o grietas en las piezas, el departamento puede proponer soluciones en el momento oportuno.
3. Diseño y firma conjunta del diagrama DL
Una vez completado el análisis CAE, en la mayoría de los casos se puede realizar el diseño del diagrama DL del molde.
El diseño del diagrama DL se refiere al análisis y diseño del proceso de estampado, también conocido como diagrama de flujo del proceso del molde, que incluye el tamaño de la hoja de la pieza, la dirección y el ángulo del estampado, la disposición de los procesos de estampado, la dirección de alimentación, la distribución y dirección de cuchillas de chatarra, ilustración de dirección de remoción de chatarra, orificio CH, identificación de partes izquierda y derecha y etiquetado de cada proceso.
Además, el diagrama DL también debe reflejar el equipo de estampado para los procesos relevantes, la altura del molde, el material del molde, la carrera de trabajo de los anillos o placas de prensado de bordes, el método de posicionamiento de la chapa y el análisis de presión del proceso completado.
Una vez finalizado el proyecto DL, se debe realizar la auditoría interna en la fábrica de moldes. Una vez que se hayan corregido los problemas de auditoría interna, el diseño se puede proporcionar al departamento de desarrollo del OEM y firmarlo conjuntamente.
La firma conjunta del diagrama DL es fundamental, ya que afecta directamente al diseño posterior del molde y tiene un impacto significativo en el ciclo y el costo de desarrollo del molde. Si el diagrama DL se cambia más adelante, provocará un desperdicio considerable en términos de ciclo de desarrollo y costo.
El departamento de desarrollo de ingeniería analiza principalmente la racionalidad del proceso de la pieza de trabajo, la precisión de los parámetros de la máquina, la racionalidad del suplemento del proceso, la tasa de utilización del material y examina la conveniencia de la alimentación junto con la situación de la prensa.
4. Diseño y firma del diagrama de estructura del molde.
El orden de co-firma de los diagramas de estructura del molde: co-firma del diagrama del molde de dibujo - co-firma del diagrama del molde de brida de formación - co-firma del diagrama del molde de punzonado y bordes.
Como el ciclo de fundición y procesamiento del molde es inflexible, es importante garantizar el progreso del proyecto dibujando el paso del diagrama de la estructura del molde lo antes posible para ganar tiempo adicional para la posterior fabricación del molde.
Generalmente, el primer muestreo del molde es un muestreo semimanual, que solo requiere conformado, mientras que el resto de los bordes y punzonados se pueden completar mediante corte de alambre.
Por lo tanto, el diseño de los diagramas del molde de estiramiento y del molde de brida debe realizarse antes de diseñar el diagrama del molde de punzonado y canteado.
La fábrica de moldes diseña el diagrama de estructura del molde basándose en las pautas del diagrama DL y, una vez finalizado, también está sujeto a revisión interna. Después de resolver cualquier problema encontrado durante la revisión, se puede presentar al departamento de desarrollo de OEM para su firma conjunta.
El departamento de desarrollo OEM debería centrarse en:
- Funcionalidad del molde
- Estabilidad y resistencia estructural.
- Seguridad en la producción de moldes
- Consistencia de los parámetros del molde con prensas de producción en masa.
- Comodidad de depuración y producción
- Consistencia del material para componentes clave del molde con requisitos de protocolo técnico
Para los problemas descubiertos durante la revisión, se debe pedir a la fábrica de moldes que los corrija tanto como sea posible. Es posible que algunos problemas no tengan un impacto significativo en la funcionalidad del producto, pero pueden afectar la conveniencia operativa o reducir la eficiencia de la producción. Para cumplir con los plazos y cronogramas, es posible que la fábrica de moldes no coopere mucho al realizar cambios.
En este punto, el personal de desarrollo del OEM (ingenieros) debe mostrar coraje y determinación porque los cambios durante la fase de diseño siempre son más rápidos que los cambios posteriores (después de la formación del molde).
Los diseñadores de fábricas de moldes deben pensar desde la perspectiva del departamento de producción y considerar el problema desde múltiples ángulos.
Los puntos débiles discutibles requieren una discusión objetiva entre muchas partes para encontrar la mejor solución. Durante el proceso de revisión del diagrama del molde, los técnicos de desarrollo de ingeniería deben tener una postura firme y una sólida experiencia técnica y de depuración en el sitio para reducir muchos problemas posteriores.
5. Lanzamiento del modelo de fundición numérico y evaluación y rectificación del modelo de espuma realista (EPS)
Después de revisar el diseño del diagrama de la estructura del molde, se pueden hacer modelos de espuma realistas. En la fase del modelo de espuma realista, el equipo de diseño necesita publicar datos de fundición para garantizar la moldeabilidad del modelo real.
El modelo de espuma realista es un material formado por espuma de poliestireno a alta temperatura. NC lo procesa según el diagrama de estructura del molde y considera las tolerancias de procesamiento del molde adecuadas (8 a 10 días) y la tasa de contracción de la espuma.
El ciclo de producción de espuma EPS suele durar aproximadamente una semana. Después de la producción, es necesario someterse a una evaluación in situ para garantizar la coherencia con el diagrama de estructura del molde.
También verifica si los problemas identificados en la revisión del diagrama de estructura del molde se han corregido o si hay nuevos problemas que no se descubrieron durante la revisión del diseño.
La evaluación de modelos realistas de espuma es un proceso indispensable en la fabricación de moldes porque es el último obstáculo para los cambios estructurales en el molde. Después de entrar en la etapa de fundición, es difícil modificar la estructura del molde.
6. Fundición a presión
Después de moler la espuma EPS, se puede enviar a la fundición para su fundición. El proceso específico no se discutirá aquí. El ciclo de fundición en molde es de 15 a 20 días. Una vez completada la fundición del molde, se transporta de regreso a la fábrica de moldes para su inspección.
El objetivo principal es comprobar si hay defectos importantes en la fundición, como grietas en su interior. Los defectos internos, como la inclusión de arena, deben mecanizarse antes de que se observen.
7. Liberación de modelos numéricos NC y mecanizado de moldes NC
Una vez completada la fundición del molde, el mecanizado NC puede comenzar siempre que se hayan publicado los datos NC.
La fábrica de moldes puede realizar programación CNC basada en los datos NC del producto y luego realizar el mecanizado NC del molde. El mecanizado de moldes NC se puede dividir en: desbaste – montaje – semiacabado – acabado.
Durante el proceso de mecanizado NC se pueden detectar defectos como inclusiones de arena o grietas en el interior de la pieza fundida. Una vez completado el mecanizado NC, el molde debe someterse a un tratamiento térmico para lograr la dureza requerida.
El ciclo de mecanizado NC del molde es generalmente de 20 a 25 días.
En situaciones donde el tiempo de desarrollo del diseño es corto, es importante organizar el tiempo de mecanizado NC de manera razonable. El personal de desarrollo de ingeniería puede llevar a cabo el control del progreso en el sitio y supervisar la fábrica de moldes para desarrollar un plan de mecanizado razonable.
Es importante evitar mantener inactivos los equipos de mecanizado CNC para asegurar el progreso.
8. Proceso de ajuste de moldes, depuración y muestreo.
El paso de montaje del molde incluye: alineación de la base del molde – cierre del molde – moldeo de prueba – muestreo, etc. Una vez mecanizado NC el molde, todavía queda algo de espacio para su montaje posterior.
La depuración del instalador de moldes verifica principalmente la tasa de coincidencia de los moldes superior e inferior y la tasa de guía para garantizar que se produzcan piezas de estampado calificadas.
A través de la depuración del instalador del molde, se puede identificar la calidad del molde y también se puede determinar el tamaño a cortar.
9. Preaceptación del molde
Una vez que la fábrica de moldes completa toda la fabricación del molde de acuerdo con el plan y realiza una prueba automática del molde que se va a calificar, puede solicitar la aceptación previa del departamento de desarrollo de OEM.
La fábrica de moldes debe proporcionar un informe de autoinspección del molde y la tasa de calificación de las piezas estampadas. El departamento de desarrollo de OEM organiza personal para llevar a cabo la aceptación previa en la fábrica de moldes después de recibir la orden de aceptación previa de la fábrica de moldes.
El molde se acepta principalmente desde tres aspectos: estática del molde, calidad dinámica de la pieza de estampado y función del molde.
Las inspecciones estáticas y dinámicas se llevan a cabo según normas, mientras que la inspección de piezas estampadas se divide en calidad de superficie, precisión dimensional y rigidez.
En principio, los problemas encontrados durante el proceso de preaceptación requieren que la fábrica de moldes los rectifique antes del embalaje y envío.
Sin embargo, si algunos problemas no afectan la calidad del producto y la dificultad de rectificación es pequeña, pueden persistir para que los instaladores de la fábrica de moldes continúen rectificando en el sitio de producción en los casos en que el tiempo sea corto.
10. Depuración y aceptación del sitio de producción de moldes.
Debido a las diferencias en las máquinas herramienta y las tasas de coincidencia de la superficie del molde, para garantizar la calidad del producto, una vez que el molde ha sido aceptado previamente, es necesario depurarlo cuando se transporta al sitio de producción.
Generalmente, la primera ronda de ajuste del molde de estiramiento demora de 1 a 2 meses y el ciclo completo de depuración del molde puede durar medio año o más. El proceso de depuración del sitio de producción de moldes gira en torno a los siguientes aspectos:
- Las piezas estampadas deben sujetarse al dispositivo de soldadura para verificar la coordinación del molde, la abrazadera, el calibre, la herramienta de inspección y el dispositivo de soldadura.
- Garantice la precisión de las piezas estampadas inspeccionándolas con el medidor de inspección. La tasa de calificación debe ser generalmente superior al 90%.
- La fábrica de moldes debe corregir los problemas o defectos encontrados durante el estampado de piezas en el medidor de inspección o la retroalimentación del proceso de soldadura y depuración.
- Verifique los elementos de inspección estática y dinámica de la función del molde.
- La confiabilidad del molde en producción continua en la prensa de producción, es decir, el requisito de tasa de desperdicio en producción continua es inferior al 2%.
El ciclo de depuración y rectificado del molde es largo. Los elementos anteriores deben corregirse y el molde debe funcionar de manera estable durante tres meses antes de que el departamento de desarrollo del OEM pueda organizar al usuario del molde, al personal de mantenimiento, al inspector de calidad, etc. informe de aprobación.
Una vez completada la aceptación final, el trabajo de desarrollo del molde se considera completo.
Sin embargo, mientras no se deseche el molde, su ciclo de vida continúa. El trabajo del departamento de desarrollo OEM se transfiere luego al departamento de procesos y sistemas de producción para su uso, gestión y mantenimiento.
Con un buen uso y mantenimiento del molde se puede prolongar su vida útil, reducir la tasa de desechos y aumentar la eficiencia de producción, lo que aporta considerables beneficios económicos a la empresa.
1 comentario
Hola muy buenos días ! Quería consultarle que soy una estudiante de una escuela técnica .. Y nos dieron un trabajo donde preciso usar su máquina! Y una de las consignas es hacer una ficha técnica.. Me podría adjuntar ests información así la realizo? Voltaje, HP, rpm, medidas, potencia, etc .. Gracias !