En las primeras etapas, la línea de producción manual utilizaba matrices de estampado, lo que generaba una alta tasa de retrabajo y desechos debido a las virutas de hierro que caían de los bordes de las matrices. Esto afectó seriamente nuestra calidad, costo y eficiencia.
Para resolver este problema, hemos establecido un grupo de investigación técnica centrado en el corte y la caída de virutas de hierro, y hemos realizado una investigación exhaustiva sobre el problema de la caída de virutas de hierro. Los resultados de esta investigación fueron exitosos.
El objetivo de la principal fábrica de motores de la industria del automóvil es lograr una alta calidad manteniendo un bajo coste.
La tasa de producción de la línea de producción de estampado manual en la antigua fábrica era de 3 a 5 golpes por minuto (spm). Sin embargo, después de actualizar a una línea de producción automática, la tasa de producción aumentó de 6 a 10 ppm, lo que resultó en una doble eficiencia de producción y importantes ahorros de costos en producción y operaciones.
Un desafío al que nos enfrentamos fue que los moldes utilizados en la línea manual no eran suficientes para soportar las demandas de la línea automática. Para superar esto, los moldes utilizados en la línea manual tuvieron que transformarse y actualizarse para cumplir con los requisitos de la producción automática en línea cerrada.
El problema de las virutas de hierro que se caen del troquel de estampación
El objetivo principal de convertir el molde de la línea de estampado manual en un molde automático es resolver el problema de la caída de limaduras de hierro durante el corte.
La escritura de hierro en la producción de estampado tiende a adherirse a la superficie del molde y las piezas (como se muestra en la Figura 1), provocando hendiduras en la superficie de las piezas (como se muestra en la Figura 2).
Cuando el inspector de calidad de final de línea detecta defectos de indentación, se deben reelaborar o descartar al menos 7 piezas.
Esto no sólo afecta gravemente la calidad de la apariencia de los productos de estampado, sino que también aumenta el costo de las operaciones posteriores.
Eliminar la escritura en hierro producida por troqueles de corte es un desafío importante en la producción de estampado.
Al optimizar y transformar la estructura del troquel de la línea de producción manual, podemos reducir efectivamente la cantidad de escritura de hierro producida durante la producción y no habrá aplastamiento significativo de la escritura de hierro residual en la superficie de las piezas estampadas.
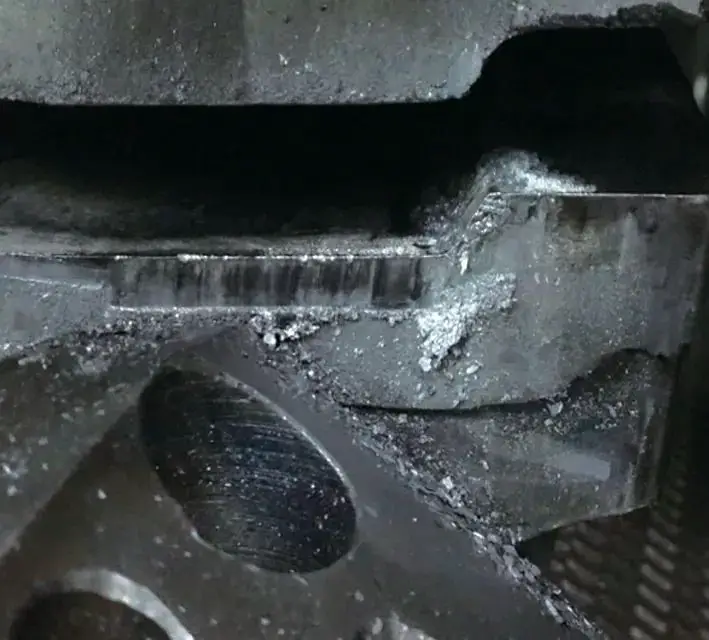
Fig. 1 acumulación de limaduras de hierro en el bloque inferior del troquel
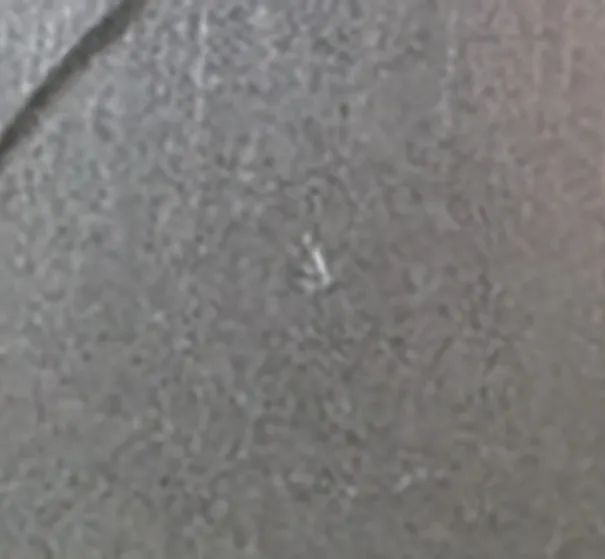
Fig. 2 aplastamiento en la superficie exterior de piezas estampadas.
Optimización y rectificado de la estructura de las palas.
La optimización y corrección del bloque de cuchillas de corte y punzonado puede cumplir con los estándares, mantener una producción estable, minimizar la generación de limaduras de hierro y resolver eficazmente el problema de la escritura con hierro.
⑴ La optimización y mejora del bloque de herramientas de enderezamiento incluye los siguientes pasos (como se muestra en las Figuras 3 y 4):
① Suavizado de la parte “ondulada” de la superficie de referencia;
② Transforme el cono positivo de la superficie de corte en un plano vertical de 90°;
③ Afilado de bordes mediante reparaciones;
④ Mantenga la superficie de referencia a una distancia de 10 mm.
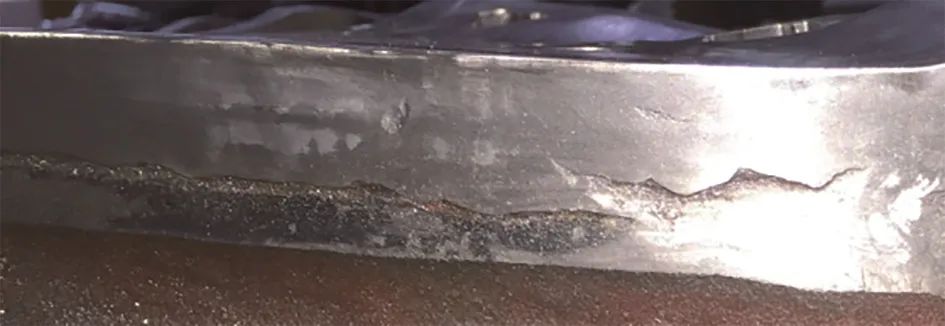
Fig. 3 antes del rectificado del bloque de herramientas de reparación directa
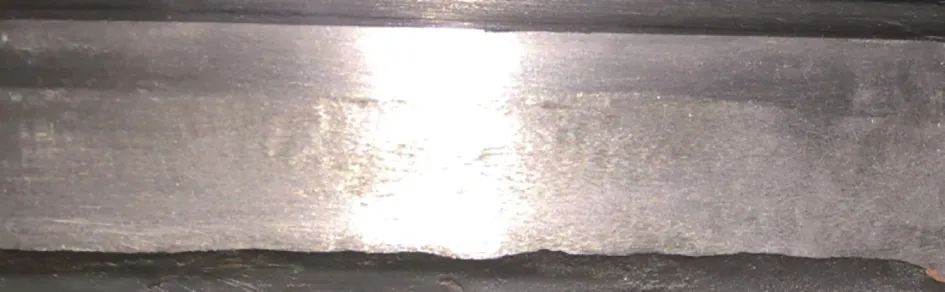
Fig. 4 después del rectificado del bloque de herramientas de reparación directa
⑵ La optimización y mejora del punzón incluye los siguientes pasos (como se muestra en las Figuras 5 y 6):
① Reducir la entrada original de 10 mm a 5 mm;
② Bajar el borde periférico de la parte superior del punzón y aplanar la protuberancia media;
③ Dar forma y pulir el borde y la circunferencia del punzón.
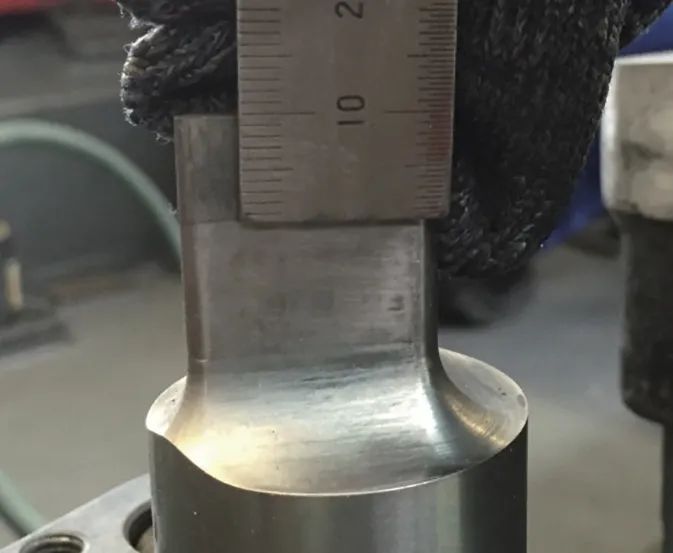
Fig. 5 Ingesta excesiva de pinchazos
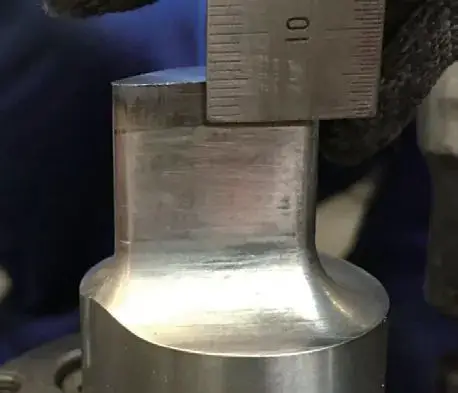
Fig.6 Ingesta razonable de pinchazos
⑶ La optimización y mejora del espacio libre de la hoja y su distancia desde la placa de presión incluye:
① Rectifique y alinee el espacio de la hoja con punta roja para asegurar un espacio uniforme y adecuado (como se muestra en las Figuras 7 y 8);
② Aumente el espacio entre el filo y la placa de presión de 0 ~ 0,1 mm a 0,5 mm ~ 0,7 mm (como se muestra en las Figuras 9 y 10).
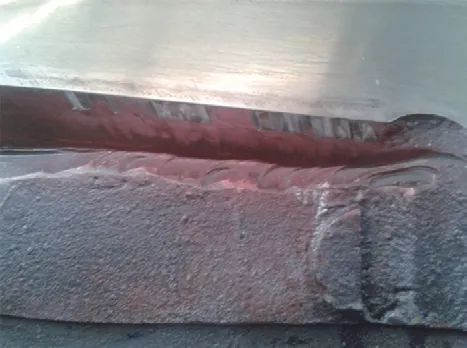
Fig. 7 la holgura de la cuchilla es demasiado pequeña
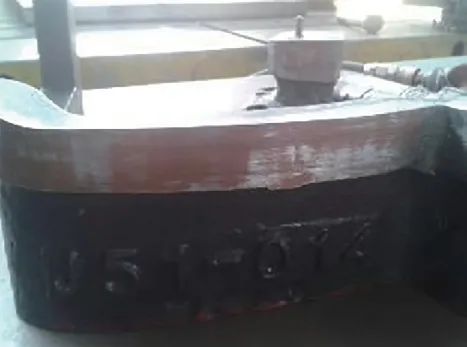
Fig. 8 espacio libre uniforme entre las hojas
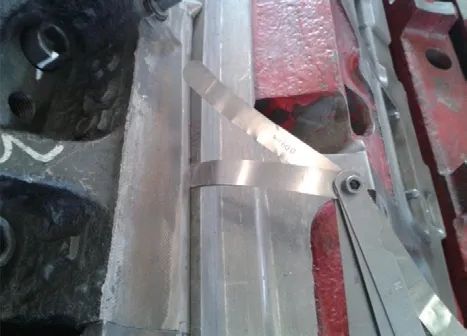
Fig. 9 el espacio entre el filo y el contorno de la placa de presión es pequeño
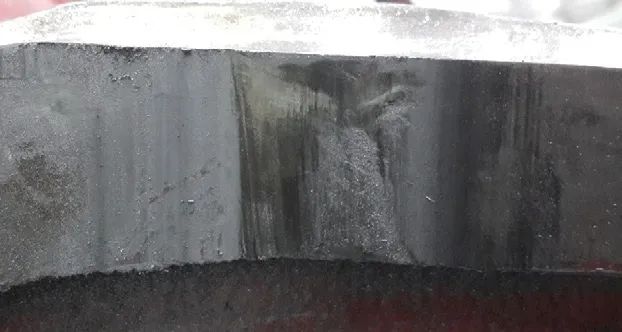
Fig. 10 el espacio entre el filo y el contorno de la placa de presión es uniforme
(4) La optimización y mejora de las cuchillas residuales incluye los siguientes pasos (como se muestra en las Figuras 11 y 12):
① Reducir el espacio entre la cuchilla residual y el bloque de cuchillas de 7 mm a 1 mm;
② Reducir el consumo de 12 mm a 4 mm;
③ Cambie de un cuchillo no vacío a un cuchillo vacío.
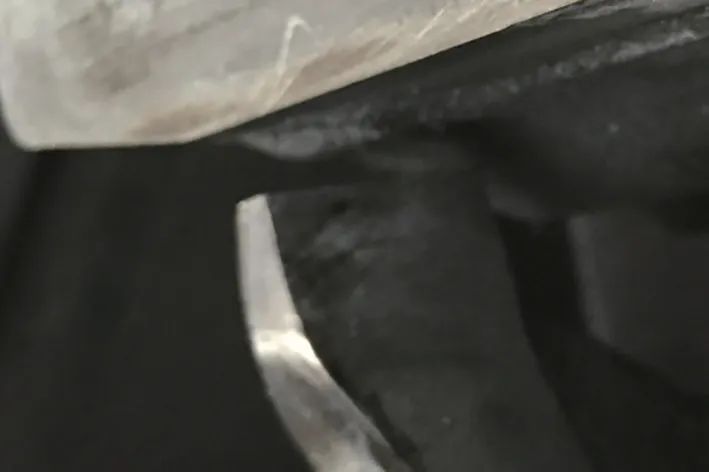
Fig. 11 Restos de cuchillo antes del pulido
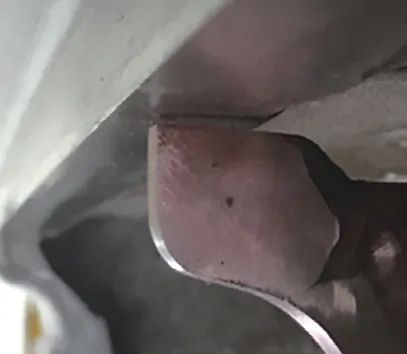
Fig. 12 después del pulido de restos de cuchilla
Rectificación de la estructura de prensado central.
La optimización y mejora de la superficie de prensado del núcleo de prensado incluye los siguientes pasos (como se muestra en las Figuras 13 y 14):
① Reduzca la superficie de control de prensado del núcleo de prensado de un máximo de 40 cm a menos de 20 cm.
Reducir el área de prensado ayuda a minimizar los retrocesos, ya que ni siquiera pequeñas cantidades de limaduras de hierro se introducirán en el molde;
② Aumentar la tasa de lapeado del núcleo de presión del 75% a más del 95%;
③ Alise y pula todas las superficies a presionar.
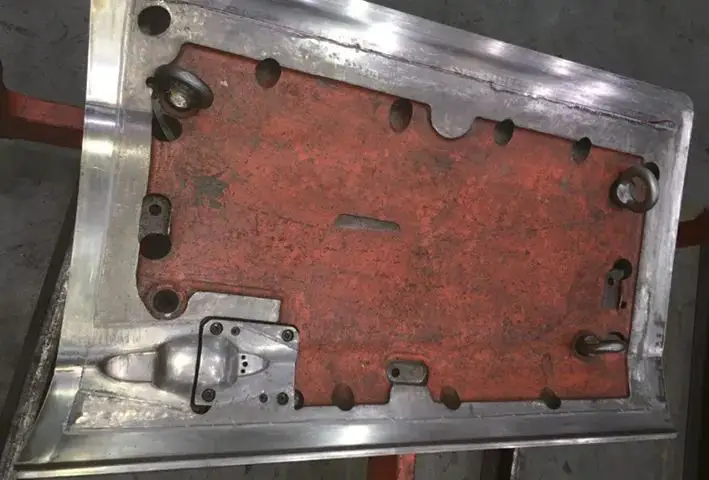
Fig. 13 antes de rectificar el perfil del núcleo de prensado
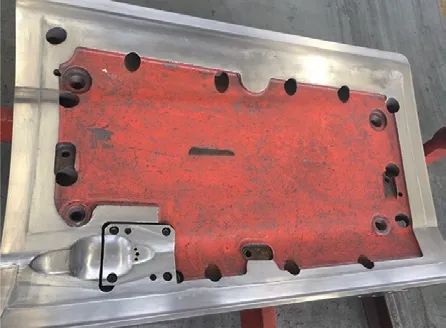
Fig. 14 después de rectificar el perfil del núcleo de prensado
Se agregó un orificio de ventilación con un diámetro de 30 mm al área cerrada local dentro del núcleo de prensado para mantener la consistencia con la presión del aire externo, evitando así el problema de absorber restos de hierro debido a la presión negativa dentro del molde durante la producción (. como se muestra en las Figuras 15 y 16).
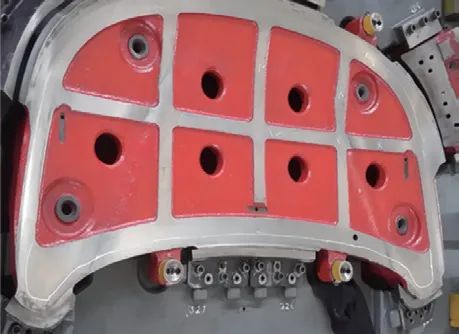
Fig. 15 antes de agregar el orificio de ventilación al núcleo de prensado
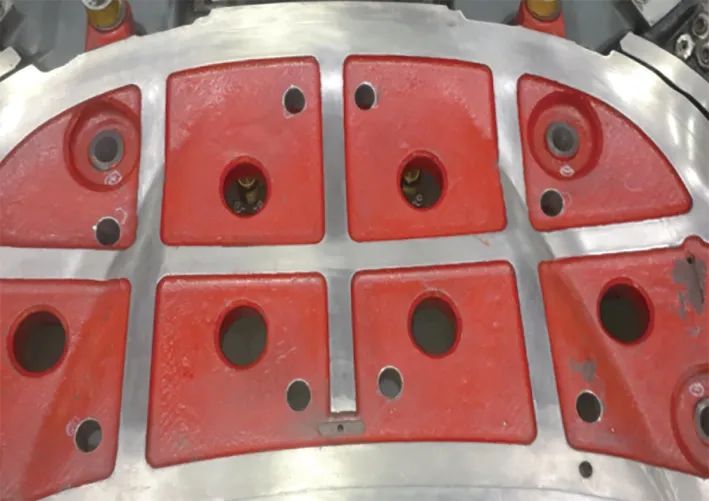
Fig. 16 después de agregar el orificio de ventilación al núcleo de prensado
Agregue un orificio de ventilación para perforar
Optimizar y mejorar la adición de orificios de ventilación en el punzón incluye:
① Aumentar el número de orificios de ventilación en la superficie del punzón de 230 a 290, lo que da como resultado un aumento del 26 %.
Los orificios de ventilación están ubicados en áreas con grandes superficies y transiciones de arco suaves.
El tamaño de los orificios de ventilación es de φ6 mm, lo que coincide con el tamaño original (como se muestra en las Figuras 17 y 18);
② Alisar y pulir la superficie convexa del modelo.
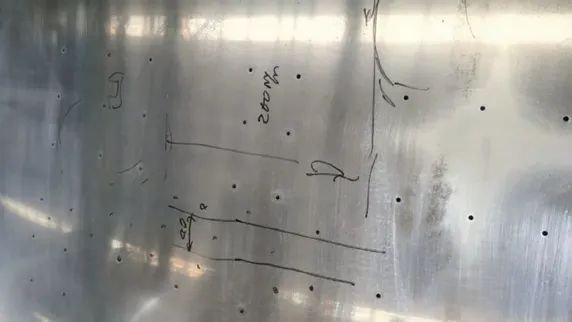
Fig. 17 taladre antes de agregar el orificio de ventilación
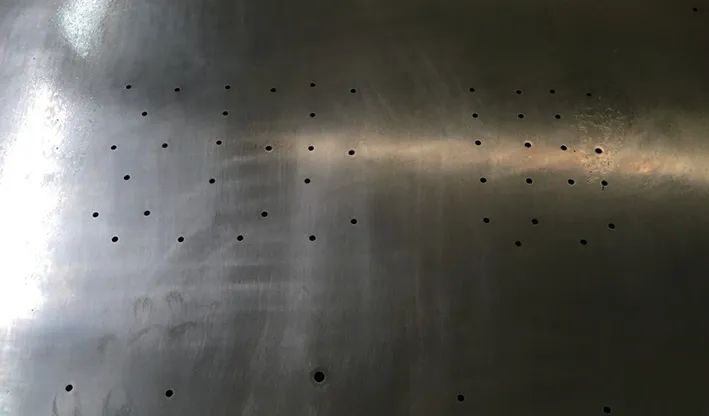
Fig. 18 después de agregar el orificio de ventilación al punzón
Conclusión
Al optimizar y mejorar el filo, el núcleo de prensado y la estructura del punzón, los parámetros del proceso cumplen con los requisitos del proceso de corte y minimizan la generación de escritura de hierro de corte, evitando así el aplastamiento de piezas y moldes por la escritura de hierro.
En los últimos 8 meses de producción, la tasa de retroceso disminuyó del 8,5% al 3,1% y se mantuvo estable durante tres meses consecutivos con una clara mejora.
Para solidificar los logros y buscar la mejora continua, tomamos dos acciones:
En primer lugar, aplicamos historias de éxito a la etapa de diseño estructural de nuevos moldes para minimizar al máximo el problema de las virutas y la caída de escrituras de hierro.
En segundo lugar, establecemos pautas para el mantenimiento de troqueles de estampado con inscripciones de hierro que caen de los bordes de los troqueles, que se controlan a través del sistema y proceso para garantizar la estabilidad de los troqueles de estampado durante la producción y operación y reducir la cantidad de productos no calificados causados. por escrituras de hierro.