La fundición es el método más flexible para fabricar piezas complejas.
La aplicación de tecnología de fundición avanzada ha aportado nueva vitalidad a la industria manufacturera.
Con la llegada de numerosos programas de software y el rápido desarrollo de la tecnología informática, ahora es posible proporcionar información precisa y confiable para la producción de piezas fundidas que cumplan con los requisitos en términos de geometría, tamaño y desempeño en servicio.

Alrededor del 15% al 20% de las piezas de automóviles se fabrican utilizando diferentes métodos de fundición, que incluyen principalmente componentes clave del sistema de energía y piezas estructurales importantes.
En la actualidad, los países desarrollados en la industria automotriz emplean tecnología de producción avanzada para piezas fundidas de automóviles, lo que da como resultado productos de alta calidad, eficiencia de producción y contaminación ambiental mínima.
Se estandarizaron y serializaron las materias primas y auxiliares utilizadas en la fundición, y todo el proceso productivo fue mecanizado, automatizado e inteligente.
A medida que la tecnología automotriz continúa avanzando rápidamente, se están adoptando tecnología de moldeo rápido, tecnología CAE, modelado 3D, tecnología CNC y otras tecnologías para brindar soporte confiable para acortar el período de preparación de la producción de piezas fundidas y reducir el riesgo de desarrollar nuevos productos.
Tecnología de fundición de automóviles.
1. Proceso de fundición
La fundición cubre principalmente la fundición en arena y la fundición especializada.
Fundición en molde de arena ordinaria
La fundición en arena es un proceso que utiliza arena como material de molde. Consta de tres tipos de moldes: molde de arena húmeda, molde de arena seca y molde de arena endurecida químicamente. Es importante tener en cuenta que no toda la arena se puede utilizar para fundir.
La ventaja de la fundición en arena es su bajo coste, ya que la arena utilizada en el molde se puede reutilizar. Sin embargo, la producción de moldes de fundición puede llevar mucho tiempo y el molde en sí no se puede reutilizar. Una vez finalizada la fundición, se debe destruir el molde para recuperar el producto terminado.
casting especial
La fundición especial se clasifica además en dos tipos según los materiales de moldeo utilizados. El primer tipo utiliza arena y piedra minerales naturales como materiales primarios de moldeo e incluye métodos tales como fundición de precisión, fundición en molde de barro, fundición en molde de cáscara, fundición a presión negativa, fundición en molde completo y fundición en molde cerámico. El segundo tipo de fundición especial utiliza metal como material de moldeo principal y cubre técnicas como la fundición en molde metálico, la fundición a presión, la fundición continua, la fundición a baja presión y la fundición centrífuga.

Fig. 1 Clasificación del proceso de fundición.
En la industria automotriz, los procesos de fundición primarios utilizados se dividen en las dos categorías siguientes:
Fundición de gravedad 1.1G (GDC)
La fundición por gravedad, también conocida como fundición por gravedad, se refiere al proceso en el que el metal fundido se vierte en un molde y llena la cavidad bajo la influencia de la gravedad de la Tierra.
En los casos en que el producto final requiere un espacio hueco, se coloca un núcleo de arena dentro de la cavidad del molde.
Para garantizar un flujo adecuado de metal fundido, el dispositivo de vertido se puede inclinar, lo que se conoce como "GDC inclinado".
La fundición por gravedad cubre diversas técnicas, como la fundición en moldes de arena, la fundición en moldes de metal, la fundición de precisión, la fundición de espuma perdida y la fundición en moldes de barro.
De estas técnicas, la fundición en molde de arena es la más utilizada en la industria automotriz.
1.1.1 S y fundición
Actualmente, las piezas automotrices de hierro fundido más utilizadas se producen mediante moldeo en arena húmeda, principalmente mediante el uso de presión estática o moldeo por impacto de aire con flujo de aire precomprimido. Este método tiene numerosas ventajas, incluido el bajo consumo de energía, el bajo nivel de ruido, la contaminación reducida, la alta eficiencia y el funcionamiento confiable.
Los fabricantes de equipos extranjeros han mejorado continuamente sus máquinas de moldeo incorporando varios métodos de mejora, como compactación por impacto de aire, impacto de aire más compactación con mayor flujo de aire, presión estática más compactación, compactación multicontacto activa y proceso de moldeo por extrusión y compactación para obtener un producto más uniforme. Dureza del molde de arena.

Fig. 2 proceso de fundición en arena
Con los avances en componentes semiconductores de alta potencia, computadoras y tecnología microelectrónica, los servosistemas eléctricos se están utilizando para reemplazar los accionamientos hidráulicos y neumáticos en las líneas de moldeo, acelerando así el ritmo de producción y aumentando significativamente la confiabilidad operativa.
Al mismo tiempo, el sistema de control hidráulico se simplifica significativamente, lo que reduce los requisitos de mantenimiento.
Utilizando una máquina secadora de arena de doble cilindro, la pieza fundida y la compuerta se pueden prelimpiar simultáneamente.
El proceso de vertido en las líneas de moldeo a menudo puede limitar la tasa de producción general, por lo que se recomienda el uso de equipos de vertido automático.
Algunos fabricantes utilizan ollas a presión de aire y técnicas de vertido por contacto para conservar el hierro fundido, mantener la calidad y proteger la caja de arena.
En el proceso de fundición, se utiliza comúnmente la inoculación por flujo y algunos emplean una combinación de inoculación en molde y filtración.
En el proceso de fundición, diferentes fábricas utilizan diferentes métodos para producir núcleos de arena. Se puede utilizar una caja de núcleo frío, una caja de núcleo caliente o un núcleo de cáscara dependiendo de las condiciones.
Los núcleos de arena como el núcleo de arena del cárter, el cilindro, el núcleo de arena superior y el núcleo de arena de las caras delantera y trasera generalmente se fabrican con la caja de núcleo fría para garantizar la precisión dimensional y ahorrar energía.
La caja de núcleo frío se está volviendo cada vez más popular.
El núcleo frío se produce principalmente utilizando el método de endurecimiento con trietilamina curado ISO, y en los Estados Unidos se ha desarrollado un método avanzado conocido como ISO Max.
Para mejorar la calidad de la superficie interna y la limpieza de la cavidad interna de la pieza fundida, se utilizan recubrimientos a base de agua en lugar de recubrimientos a base de alcohol para evitar la contaminación.
El secado por microondas después del recubrimiento es un método altamente eficiente y que ahorra energía, y la calidad del núcleo de arena producido es mejor que la obtenida mediante el secado tradicional con gas o gas natural.
Se emplea el proceso KCY-CORE, donde se abren orificios de proceso en el núcleo de arena para el llenado y la solidificación secundaria de la arena, lo que da como resultado la integración de múltiples núcleos de arena en un núcleo de arena combinado. Luego, el núcleo de arena combinado se recubre y se seca, lo que mejora significativamente la precisión dimensional de la pieza fundida con un error dimensional general de menos de 0,3 mm.
El sistema de moldeo de arena incluye equipos de separación magnética de arena vieja, equipos de trituración de bloques de arena, equipos de cribado y equipos de enfriamiento de arena vieja para garantizar la calidad de la arena vieja reciclada.
Se introducen en el sistema arena nueva, polvo de carbón, bentonita y otros materiales añadidos de forma precisa y cuantitativa según una proporción predeterminada, y la adición de agua se ajusta en tiempo real en función de los datos de control para mantener el rendimiento de la arena del moldeo.
También existe un control de circuito cerrado en tiempo real del rendimiento de la arena de moldeo de todo el sistema o un sistema especializado en línea para controlar la calidad de la arena de moldeo.
Cabe señalar que el sistema de arena de moldeo tiene una gran rotación y una fuerte inercia, por lo que el ajuste del rendimiento de la arena de moldeo debe basarse en la tendencia, tomándose medidas predecibles para garantizar la estabilidad de la calidad de la arena de moldeo.
Las piezas fundidas comunes incluyen: bloque de motor, culata, caja de cambios, colector de admisión, etc.
1.2 D es decir, fundido
Cuando la pieza fundida requerida tiene una sección transversal compleja o paredes delgadas en áreas específicas (como se muestra en la Figura 3), la gravedad por sí sola puede no ser suficiente para garantizar que el metal fundido llene completamente la cavidad del molde.
En estos casos, se puede aplicar presión al líquido metálico para asegurar el llenado completo de la cavidad del molde.
Esto se puede lograr mediante fundición a alta presión (HPDC) o fundición a baja presión (LPDC).
Las piezas fundidas producidas mediante el proceso HPDC tienen buena consistencia dimensional y tolerancias similares, alrededor de +/- 0,2 mm, que no se pueden lograr mediante fundición por gravedad (GDC) o incluso fundición a presión (LPDC).
Con el rápido avance de la tecnología automotriz, la tecnología de fundición a presión a alta presión se ha convertido en un foco de atención en la fundición de automóviles.

Fig.3 piezas complejas de paredes delgadas
1.2.1 Fundición a alta presión
La fundición a alta presión es un proceso en el que se inyecta rápidamente metal líquido o semilíquido en un molde a alta presión, solidificándose y cristalizándose bajo presión para formar la fundición.
El proceso de fundición a alta presión se puede dividir en tres etapas: cierre del molde, inyección y expulsión.

Fig. 4 Flujo del proceso de fundición a alta presión
En el proceso de fundición a presión, los parámetros de inyección tienen un gran impacto en la porosidad de las piezas de fundición a presión y deben ajustarse en consecuencia.
Utilizando un sistema cerrado de control del tiempo de acabado de la inyección, es posible lograr una fundición a presión sin rebabas.
La calidad de las piezas fundidas se puede comprobar mediante la detección de defectos por rayos X y pruebas ultrasónicas.
La fundición al vacío y la fundición a presión con oxígeno, que se basan en la tecnología de fundición a alta presión, tienen como objetivo eliminar los defectos de la fundición, mejorar la calidad interna y ampliar la aplicación de la fundición a presión.
La fundición por compresión implica llenar y solidificar la fundición bajo presión, lo que ofrece estabilidad, reducción de salpicaduras de metal, pérdida mínima por oxidación del metal fundido, ahorro de energía, operación segura y reducción de defectos en los orificios de fundición.
Este proceso se ha utilizado ampliamente en el desarrollo y aplicación de piezas fundidas de aleación de aluminio de alto rendimiento, como subchasis de aleación de aluminio.
Fundición al vacío
Para minimizar o eliminar la porosidad en las piezas fundidas causada por la rápida mezcla de gas con metal fundido durante el proceso de fundición a presión, es común utilizar la fundición al vacío del molde antes de la fundición a presión.
Según el grado de vacío en la cámara de presión y la cavidad, la fundición a presión al vacío se puede dividir en fundición a presión al vacío normal y fundición a presión al alto vacío.

Fig. 5 Diagrama de flujo del proceso de fundición a presión al vacío
La clave para la fundición a presión de alto vacío es lograr un alto nivel de vacío en un corto período de tiempo.
La Figura 6 muestra el diagrama del principio de funcionamiento de la máquina de fundición a presión de alto vacío tipo succión.
Utiliza vacío para aspirar el líquido metálico hacia la cámara de presión y luego lo inyecta rápidamente para lograr un alto grado de vacío en el proceso de fundición a presión.
El principio de la fundición a presión al alto vacío implica bombear aire desde toda la cámara de presión y la cavidad a través de un tubo de vacío antes de la fundición a presión.
El proceso de bombeo de vacío debe completarse lo más rápido posible, creando una gran diferencia de presión entre el líquido metálico en el crisol y la cámara de presión, lo que hace que el líquido metálico fluya hacia la cámara de presión a través del tubo ascendente de líquido y luego el punzón de inyección de presión. comienza a aplicar presión para la inyección.

Fig. 6 Máquina de fundición a presión por succión y alto vacío
Fundición a presión llena de oxígeno
La fundición a presión llena de oxígeno implica llenar con oxígeno seco la cámara de presión y la cavidad del molde de fundición a presión para reemplazar el aire y otros gases presentes.
El proceso de fundición a presión lleno de oxígeno se muestra en la Figura 7.
Este método de fundición sólo es aplicable a aleaciones de aluminio.
Cuando se inyecta líquido de aleación de aluminio en la cámara de presión y en la cavidad del molde de fundición, reacciona con el oxígeno para formar Al 2 Ó 3 , lo que da como resultado partículas pequeñas de Al2O3 distribuidas uniformemente (con un diámetro inferior a 1 um), lo que reduce o elimina la porosidad y mejora. la compactación de la pieza fundida.
Estas pequeñas partículas se encuentran dispersas por toda la pieza fundida, representando alrededor del 0,1% al 0,2% de la masa total y no afectan el mecanizado.

Fig. 7 Diagrama esquemático de fundición a presión llena de oxígeno.
2. Equipo de fundición
Los equipos utilizados en la industria de fundición de automóviles deben ser rápidos, eficientes y fiables, capaces de funcionar de forma continua.
Teniendo en cuenta los estrictos estándares de calidad de las piezas fundidas para automóviles, estas máquinas de fundición también deben tener una alta precisión.
Algunos de los principales equipos de fundición incluyen: máquinas de moldeo, mezcladores de arena, máquinas para fabricar núcleos, equipos de moldeo, equipos de extracción de polvo, hornos de fundición, máquinas de fundición a presión, herramientas de mecanizado, granalladoras, máquinas de limpieza y equipos de prueba.
Destacan en particular la máquina de colada a presión y el horno de colada.
Horno de fusión 2.1S
El horno de fundición emplea un suministro de energía de frecuencia media para establecer un campo magnético de frecuencia media, induciendo así una corriente parásita dentro del material ferromagnético y generando calor, logrando así el propósito de calentar el material.
El horno eléctrico de frecuencia media utiliza una fuente de alimentación de frecuencia media de 200-2500 Hz para el calentamiento por inducción, la fusión y el mantenimiento de la temperatura.
Este horno de fundición se utiliza principalmente para fundir acero al carbono, acero aleado y acero especial, así como para fundir y aumentar la temperatura de metales no ferrosos como el cobre y el aluminio.
Lectura relacionada: Metales ferrosos y no ferrosos
El equipo es compacto, liviano y altamente eficiente, con bajo consumo de energía, rápidas velocidades de fusión y calentamiento, fácil control de temperatura y alta eficiencia de producción.
El conjunto completo del equipo del horno de fundición consta de un gabinete de potencia de frecuencia intermedia, un condensador de compensación, dos cuerpos del horno, cables enfriados por agua y un reductor.
El cuerpo del horno consta de cuatro partes: la carcasa del horno, la bobina de inducción, el revestimiento del horno y el engranaje reductor de inclinación.
La carcasa del horno está fabricada de materiales no magnéticos.
La bobina de inducción es un cilindro en espiral construido a partir de tubos rectangulares huecos, a través de los cuales circula agua de refrigeración durante el proceso de fundición. La barra de cobre que sale de la bobina está conectada al cable refrigerado por agua.
El revestimiento del horno, situado cerca de la bobina de inducción, está hecho de arena de cuarzo.
El cuerpo del horno se inclina mediante la rotación directa del engranaje reductor de inclinación.
Este engranaje presenta un cambio de velocidad de turbina de dos etapas y ofrece una rotación confiable y estable con un excelente rendimiento de autobloqueo. En caso de un corte de energía, el mecanismo de inclinación se detendrá automáticamente para evitar cualquier peligro potencial.
Los motores de engranajes reductores de inclinación de ambos hornos se pueden controlar a través del interruptor de selección del horno, con un cable de goma de cuatro núcleos y una caja de distribución, lo que permite al operador permanecer en una ubicación conveniente mientras controla la inclinación y reajusta el cuerpo del horno.
Actualmente, muchas fundiciones siguen en un estado industrial 2.0 y necesitan urgentemente actualizaciones en materia de protección medioambiental, automatización, inteligencia y seguridad.
Con la llegada de la Industria 4.0, todos los parámetros de fundición se registrarán a través de sensores capaces de operar en entornos con temperaturas extremadamente altas.
Datos como el nivel de llenado del horno de calentamiento y el nivel de contaminación en el baño de soldadura serán información crucial para construir un horno de fundición inteligente e interconectado.
En el futuro, una fábrica de hornos de fundición podrá utilizar un robot para las operaciones de limpieza.
El robot tendrá acceso a todos los parámetros del horno y podrá tomar medidas inmediatas antes de que la contaminación alcance niveles críticos.
2.2 Máquina de fundición, es decir, máquina de fundición
La máquina de fundición a presión es una máquina que utiliza fundición a presión. Consta de una cámara de compresión caliente y una cámara de compresión fría, y además se divide en dos tipos: recta y horizontal.
Bajo la presión de la máquina de fundición a presión, el metal fundido se inyecta hidráulicamente en el molde, donde se enfría y solidifica.
Después de abrir el molde, se puede recuperar una pieza sólida de metal.
La máquina de fundición a presión se compone de un mecanismo de sujeción, un mecanismo de inyección, un sistema hidráulico y un sistema de control eléctrico.
Además, la máquina también incluye diversos componentes y bases, dispositivos auxiliares y otras piezas.

Fig. 8 Estructura básica de la máquina de fundición a presión.
Durante los últimos 30 años, la máquina de fundición a presión ha experimentado importantes avances en términos de tamaño, automatización, modularidad y flexibilidad.
En los últimos tiempos, la integración y reducción de peso de la fundición a presión de automóviles ha generado nuevos y mayores requisitos para las máquinas de fundición a presión, siendo la tecnología de conformado integrada en la carrocería un tema particularmente candente.
Esto ha puesto a las máquinas de fundición a presión de alta resistencia a la vanguardia de la innovación. Por ejemplo, Tesla compró recientemente una máquina de fundición a presión de 8.000 toneladas de la empresa italiana DRA, que es un 30% más grande que la máquina de fundición a presión de 6.000 toneladas utilizada en el Modelo Y.
Predigo que este récord se batirá continuamente a medida que evolucione la industria.
Examinemos por qué las máquinas de fundición a presión de alta resistencia son el futuro de la industria y qué ventajas ofrecen.
Ventaja 1: Ventaja de costos de conformado de material de una sola estación
La Figura 9 muestra la estructura del bastidor del Tesla Model Y. El componente amarillo representa una gran parte integrada de la carrocería trasera y el paso de rueda en la parte superior de la torre del eje trasero.
Con la ayuda de una máquina de fundición a presión a gran escala, este complejo componente que normalmente requiere múltiples estaciones y procesos se puede completar en una sola operación.
Como resultado, ofrece una importante ventaja de costes.
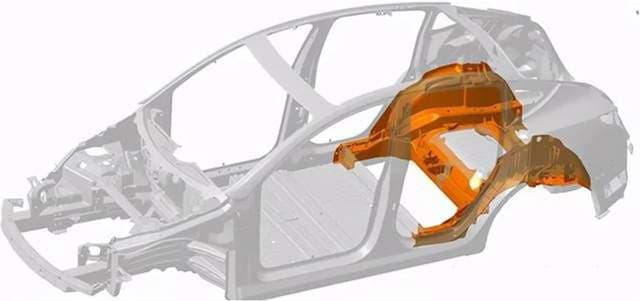
Fig. 9 diagrama estructural del marco modelo Y
Ventaja 2: Integración de Estampación y Soldadura y Optimización del Ritmo de Producción General
Tesla aspira a convertirse en el Toyota o Volkswagen de la nueva industria energética, haciendo del ritmo de producción un factor crítico.
Para aumentar la velocidad de la máquina de fundición a presión de 8.000 toneladas, la tecnología se puede utilizar para crear una cavidad entre las semipelículas fundidas en ambos lados durante el proceso de sellado a presión de las piezas fundidas y para inyectar metal fundido protector de temperatura en el cavidad.
Como la cavidad se encuentra en un estado de presión negativa, elimina eficazmente las burbujas de aire generadas por la turbulencia de la fundición, lo que contribuye a la consistencia del material y la velocidad de la fundición durante la fundición a presión.
Según datos de Tesla, cada operación de fundición implica inyectar unos 80 kg de líquido de aleación de aluminio en el molde de la cámara fría a una velocidad de 10 metros por segundo.
El tiempo del ciclo de producción es de alrededor de 85 segundos, con un ritmo de producción de 42 piezas por hora, lo que representa una optimización del tiempo del ciclo actual.
Sin embargo, estas ventajas van acompañadas de algunos desafíos, como la mecánica de ejercicios y el diseño de moldes, que deberán abordarse a medida que la industria continúa desarrollando máquinas de fundición a presión a gran escala.
3. Materiales de fundición
bloque de cilindros 3.1C
Tradicionalmente, el material utilizado en los bloques de motor de los automóviles era el hierro fundido, que todavía hoy ocupa una posición dominante en la industria.
Sin embargo, con la mejora continua del rendimiento del motor y la demanda de reducción de peso, el material del bloque del motor está experimentando una rápida innovación.
Hay tres áreas principales de desarrollo:
- Mejore la calidad del hierro fundido para aumentar la resistencia y el rendimiento del cilindro.
- Utilizar hierro fundido con grafito vermicular para producir bloques de cilindros de motor, que ofrecen mayor resistencia y mejor rendimiento ante la fatiga, admiten diseños de paredes delgadas, soportan una mayor presión de estallido, reducen la deformación de los cilindros y aumentan la potencia entre un 10% y un 20%.
- Bloques de cilindros de aleación de aluminio, que se están desarrollando rápidamente y representan la dirección principal para los bloques de cilindros de turismos.
Generalmente, se prefiere el uso de aleaciones de aluminio para reducir el peso y el consumo de energía de los vehículos.
Sin embargo, las limitaciones de la resistencia a la fatiga térmica y el rendimiento de la aleación de aluminio dificultan su aplicación en bloques de motores de alta potencia y su costo es relativamente alto.
culata 3.2C
La culata de motor es un área de aplicación importante para las aleaciones de aluminio, especialmente en el mercado de culatas de automóviles de pasajeros, que está dominado en gran medida por materiales de aleación de aluminio.
En el mercado de camiones, el uso de hierro fundido para cabezas de motores de alta potencia es poco común, y las cabezas de hierro vermicular se han convertido en la opción preferida, capaces de solucionar el problema de las grietas en las cabezas de fundición gris.
3.3 Clasificación del eje C
La aplicación de la tecnología de sobrealimentación de motores es un proceso crítico para mejorar el rendimiento del automóvil con miras a la eficiencia energética y la reducción de emisiones.
Ya sea para motores de gasolina o diésel, principalmente en el mercado de camiones, el uso de cigüeñales de hierro nodular de perlita, muy utilizados antiguamente, no cumple con los requisitos debido a la mayor presión de explosión del motor, y ha sido sustituido por materiales de acero forjado. como 40Cr.
Sin embargo, con los avances en tecnologías como el laminado en filete y el endurecimiento por inducción de los cigüeñales de hierro nodular de Pearlite, los cigüeñales de hierro nodular siguen manteniendo una participación de mercado significativa en los mercados de automóviles y camiones de pasajeros de potencia media.
Además, en el país y en el extranjero también se han estudiado los cigüeñales de motor fabricados con hierro dúctil endurecido isotérmicamente.
3.4 Otros
Otras piezas fundidas de automóviles, como piezas de soporte y componentes estructurales de motores y chasis, incluidos varios soportes, discos, carcasas y piezas de dirección, están hechas de materiales de hierro fundido para cumplir con los requisitos de rendimiento.
A medida que los requisitos de protección ambiental del automóvil continúan evolucionando, el uso de hierro fundido gris y acero fundido está disminuyendo gradualmente, mientras que el hierro dúctil de alto rendimiento, las aleaciones de magnesio, las aleaciones de aluminio y los materiales especiales de hierro fundido son cada vez más predominantes.
Tendencia de desarrollo 3.5D
Actualmente, el hierro fundido es el principal material utilizado en las piezas fundidas de automóviles. En particular, el uso de hierro dúctil ha reemplazado a muchas piezas fundidas de acero y hierro gris, y el uso de hierro maleable en piezas de automóviles ha disminuido. Su resistencia y tenacidad superiores, así como su facilidad de producción, han aumentado su aplicación.
La investigación y el desarrollo de hierro dúctil de alta resistencia y tenacidad serán fundamentales para su uso continuo en la industria. Otro material prometedor, el hierro dúctil templado isotérmicamente, tiene excelentes propiedades mecánicas y ha experimentado un rápido desarrollo y una aplicación exitosa en el extranjero, particularmente en la producción de cigüeñales, engranajes, soportes y piezas estructurales.
La fundición de grafito vermicular, inventada en 1948, tiene un rango de producción estrecho y un rendimiento limitado, por lo que su uso ha sido limitado. Sin embargo, con los avances en la tecnología de control de producción, el hierro fundido con grafito vermicular puede tener futuro en la producción de piezas fundidas complejas. Tiene mayor resistencia a la tracción, módulo de elasticidad y resistencia a la fatiga que el hierro fundido y el aluminio, lo que lo convierte en un material ideal para bloques y culatas de motores.
La tendencia hacia la reducción del peso de los vehículos ha llevado al uso de aleaciones de magnesio y aluminio en las piezas fundidas de automóviles. Por cada 10% de reducción del peso del vehículo, el consumo de combustible se reduce un 5,5% y las emisiones se reducen alrededor de un 10%. Las aleaciones de aluminio tienen una densidad más ligera (1/3 de la del hierro) y una resistencia equivalente a la de la fundición gris, lo que las hace ideales para fabricar bloques y culatas de motor.
Las aleaciones de aluminio han experimentado un rápido crecimiento en los últimos años, y las aleaciones de magnesio, con su densidad más ligera, se han aplicado a volantes de automóviles, marcos de asientos, paneles de instrumentos, cubiertas y otras piezas, a medida que la investigación y el desarrollo de aplicaciones continúan avanzando.
Dirección de Desarrollo de Fundición de Automóviles
1. Dirección de desarrollo de piezas de fundición.
Diseño integrado de piezas fundidas para automóviles.
Con las crecientes demandas de eficiencia energética y protección ambiental en la industria automotriz, así como la necesidad de reducir los costos de producción, se están aprovechando los beneficios del moldeo a presión para lograr la integración de piezas a través de un diseño y una estructura optimizados. Se trata de combinar varias piezas formadas mediante estampación, soldadura, forja y fundición, lo que da como resultado un peso reducido de las piezas y menos pasos de procesamiento, lo que da como resultado componentes más ligeros y de alto rendimiento.
La tendencia hacia la integración de la fundición en la industria del automóvil se manifiesta especialmente en la fundición de aleaciones no ferrosas.
Para utilizar plenamente el proceso de fundición para la producción de piezas estructurales complejas, ha habido un aumento en el uso de piezas fundidas de alta presión con diseño integrado, como paneles interiores de puertas, molduras de asientos, molduras de paneles de instrumentos, molduras frontales y cortafuegos. .
Estas piezas fundidas son significativamente más grandes en tamaño en comparación con las que se producen actualmente y requieren una máquina de fundición a presión de 4.000 a 5.000 toneladas o incluso más grande para su producción.

Fig. 10 Cuerpo fundido a presión integrado del Tesla Model Y
Ligereza de las piezas fundidas de automóviles
Para mejorar el rendimiento energético, reducir el consumo de combustible y reducir la contaminación de los gases de escape, manteniendo al mismo tiempo la resistencia y la seguridad del vehículo, es importante minimizar el peso total del vehículo tanto como sea posible.
Por cada 100 kg de reducción del peso en vacío del vehículo, el consumo de combustible cada 100 km se puede reducir entre 0,3 y 0,6 litros.
Una reducción del 10% en el peso del vehículo puede resultar en un aumento del 6% al 8% en la eficiencia del combustible.
Debido a las crecientes preocupaciones sobre la protección del medio ambiente y la conservación de energía, la reducción de peso se ha convertido en una tendencia en la industria automotriz mundial, y las piezas fundidas de automóviles livianos se han convertido en una dirección de desarrollo crucial.
La consecución de la reducción de peso se conseguirá principalmente a través de los siguientes tres puntos:
1) Diseño liviano
Una de las principales desventajas del diseño de igual espesor es que no puede aprovechar plenamente el rendimiento estructural y conduce a un aumento del peso de la pieza fundida.
Para optimizar el diseño de piezas y componentes, se emplean análisis CAE, optimización de topología y otros métodos para igualar los valores de tensión de cada pieza, lo que da como resultado un espesor de pared inconsistente. El espesor del material de las piezas de baja tensión se reduce para reducir el peso de la pieza.
El moldeo por fundición tiene la ventaja de producir piezas fundidas estructurales complejas y varias secciones transversales irregulares. Durante el proceso de diseño, se utiliza CAE u optimización de topología para analizar la tensión de los componentes.
A partir de la distribución de fuerzas se determina la forma de las piezas y el espesor específico del material local. El peso de las piezas se puede reducir significativamente mediante refuerzo, apertura de orificios y cambio de sección.
2) Aplicación de materiales de aleación.
El uso de materiales de aleación ligera, como el aluminio y el magnesio, es la principal medida de ahorro de peso adoptada por los fabricantes de automóviles de todo el mundo.
El aluminio tiene una densidad que es sólo un tercio de la del acero y tiene una excelente resistencia a la corrosión y ductilidad. El magnesio tiene una densidad aún menor, sólo dos tercios de la del aluminio, y tiene una fluidez excelente en condiciones de fundición a alta presión.
Tanto el aluminio como el magnesio tienen una alta resistencia específica (la relación entre resistencia y masa), lo que los hace cruciales para reducir el peso del vehículo y mejorar la eficiencia del combustible.
Sin embargo, cabe señalar que el coste de las materias primas para las aleaciones ligeras, como el aluminio y el magnesio, es significativamente mayor que el de los materiales de acero, lo que limita su aplicación más amplia en la industria del automóvil.
A pesar del elevado coste de las materias primas, el uso de piezas fundidas de magnesio y aluminio en cada vehículo sigue aumentando año tras año. Por un lado, este aumento de costes se ve compensado por los avances tecnológicos y, por otro, la competencia en el mercado está obligando a los fabricantes de automóviles a reducir sus márgenes y adoptar más aleaciones ligeras.
Sin embargo, el desarrollo de tecnología de conformado avanzada es clave para aumentar significativamente el uso de aleaciones ligeras y reducir el costo de los lingotes de magnesio y aluminio.
3) Materiales de fundición de alto rendimiento.
Mejorar el rendimiento de los materiales y permitir que las piezas soporten mayores cargas por unidad de peso es uno de los métodos eficaces para reducir el peso de las piezas fundidas.
Las piezas fundidas de soporte estructural constituyen una parte importante de las piezas fundidas para automóviles, lo que hace que el desarrollo de sus piezas fundidas sea un enfoque clave.
Mediante tratamiento térmico y otras técnicas, se puede cambiar la microestructura del material para mejorar la resistencia, rigidez o tenacidad de las piezas y reducir eficazmente su peso.
El hierro dúctil templado isotérmicamente tiene mayor resistencia que el acero fundido ordinario y menor densidad. Su densidad es de 7,1 g/cm 3 mientras que la del acero fundido es de 7,8 g/cm 3 . Este material ha sido ampliamente recomendado en los últimos años.
Al adoptar hierro dúctil templado isotérmicamente, las piezas fundidas pueden ser un 10 % más ligeras que las piezas fundidas de acero del mismo tamaño.
Tabla 1 Efecto de ligereza al reemplazar material de hierro dúctil templado isotérmicamente
Piezas de repuesto | Peso del hierro dúctil templado isotérmicamente (kg) | Peso de acero fundido/kg | Tasa de reducción de peso /% |
Cruz superior de suspensión delantera | 10:25 am | 25 | 59.00 |
Cruz inferior de suspensión delantera | 32,46 | 64 | 49,28 |
Soporte de resorte de suspensión delantera superior | 21:28 | 34,6 | 38,50 |
Soporte de resorte de suspensión trasera inferior | 20,74 | 33.16 | 37,45 |
Travesaño inferior de suspensión trasera | 9:32 am | 50.16 | 84,58 |
En términos de piezas fundidas de aleaciones de aluminio y magnesio, también se utilizan como sustitutos materiales de alta resistencia y tenacidad.
Aprovechando el ahorro de peso logrado con las aleaciones ligeras originales, el uso de materiales de alto rendimiento conduce a un mayor ahorro de peso.
Por ejemplo, General Motors en Estados Unidos utiliza una aleación AE44 de alto rendimiento para reemplazar la aleación de aluminio original y emplea fundición a alta presión para producir la estructura. Esto supone una reducción de peso adicional de 6 kg, además de la reducción de peso conseguida con la aleación de aluminio.
Desarrollo digital de piezas fundidas para automóviles.
La integración del desarrollo de la fundición de automóviles y la tecnología digital aumenta en gran medida el nivel de la tecnología de fundición y acorta el ciclo de diseño de productos y producción de prototipos.
Actualmente, la tecnología de fabricación digital se utiliza ampliamente en el desarrollo de piezas fundidas para automóviles.
Durante la etapa de diseño de estructuras y procesos de fundición, se utilizan comúnmente software de diseño 3D como Pro/E, CATIA y UG, y algunas empresas de fundición avanzadas han implementado diseños sin papel.
Se utilizan software como Magma, ProCAST y Huazhu CAE para simular el proceso de solidificación, la microestructura, la segregación de componentes y las propiedades de los materiales de las piezas fundidas de automóviles. Estas simulaciones también incluyen el campo de velocidad, el campo de concentración, el campo de temperatura, el campo de fase y el campo de tensión en el proceso de fundición, lo que permite un esquema de proceso optimizado antes de la producción en masa.
Para mantenerse al día con el rápido ritmo del desarrollo de piezas fundidas para automóviles, la tecnología de creación rápida de prototipos (RP) se utiliza ampliamente para la creación rápida de prototipos de piezas fundidas para automóviles basadas en el diseño y desarrollo CAD/CAE.
Los datos CAD/CAE originales se utilizan para crear un prototipo de fundición o un prototipo de molde mediante el apilamiento capa por capa mediante unión, fusión o sinterización. El primero se puede utilizar para muestras de fundición de prototipos mediante fundición a la cera perdida o fundición de yeso, mientras que el segundo se puede utilizar como molde para la fabricación de núcleos de arena y fundición mediante moldeo de ensamblaje de núcleos.
Además, el método de sinterización por láser de polvo (SLS) se puede utilizar para producir directamente núcleos y moldes de arena para la producción de prueba de piezas fundidas.
Para moldes externos con una estructura relativamente simple, también se puede utilizar una máquina herramienta CNC para el procesamiento de levas de plástico mecanizable para obtener la caja de núcleo y el patrón necesarios para la producción de fundición experimental, o el bloque de arena se puede procesar directamente para producir el molde de arena para el molde exterior.
En general, la tecnología digital impregna el diseño, desarrollo y producción de prueba de piezas fundidas, lo que resulta en una mejora significativa en la velocidad y eficiencia del desarrollo de piezas fundidas.
Actualmente, el principal desafío es que las tecnologías digitales para el diseño, el análisis y la fabricación rápida están separadas. Convertir datos de un paso a otro todavía requiere mucho trabajo tedioso.
En el futuro, se espera que se pueda desarrollar una plataforma de interfaz de datos unificada para las tecnologías digitales aplicadas en cada etapa del desarrollo de la fundición, se pueda establecer un estándar de conversión de datos estandarizado y se pueda lograr una conversión de datos perfecta entre diferentes software, además mejorando la velocidad de desarrollo del equipo.
2. Dirección de desarrollo de la tecnología de fundición de automóviles.
Tecnología de producción de fundición de estructura compleja de pared delgada
A medida que la industria automotriz evoluciona y aumenta la necesidad de eficiencia energética y reducción de emisiones, las piezas de automóviles se vuelven cada vez más ligeras.
Lograr ligereza a través de un diseño de paredes delgadas es una dirección de desarrollo crucial para los bloques de motor.
El diseño de pared delgada de 3 mm del bloque de cilindros impone requisitos estrictos para la fabricación y el ensamblaje del núcleo en el proceso de ensamblaje del núcleo y fundición vertical.
El centro de fabricación central puede lograr una alta inteligencia y automatización en la producción central.
Todo el proceso, desde la adición de arena cruda y resina hasta la mezcla de arena, la fabricación de núcleos, la reparación de núcleos, el ensamblaje, el recubrimiento, el secado, el moldeado, el ensamblaje de núcleos y el avellanado, puede ser altamente automatizado, lo que garantiza una calidad de fabricación estable de los núcleos y el ensamblaje. , precisión dimensional y calidad de secado del recubrimiento, evitando así riesgos de calidad y dimensionales causados por factores humanos y satisfaciendo las necesidades de la producción de núcleos de cilindros a gran escala.
Esto resuelve eficazmente el problema de la inestabilidad y la alta tasa de desperdicio durante la producción en masa.
Además, la mejora en la precisión dimensional del núcleo de arena reduce en gran medida la carga de trabajo y el costo de limpieza, garantizando efectivamente el requisito de espesor de pared de 3 mm.
Tecnología de fabricación de grandes piezas estructurales de aleación de aluminio y magnesio.
La fundición estructural a gran escala de aleaciones de aluminio y magnesio se ha convertido en una tendencia crucial en respuesta a la creciente demanda de eficiencia energética, protección ambiental y reducción de costos en componentes. Su tecnología de fabricación también se ha convertido en un punto focal del desarrollo actual.
En la actualidad, los principales métodos de producción de piezas estructurales de aleación de aluminio y magnesio a gran escala incluyen la fundición a alta presión, la fundición por compresión y la fundición a baja presión.
La fundición a alta presión es el proceso de producción dominante debido a su alta eficiencia y excelente calidad del producto.
Los esfuerzos para mejorar la tecnología de fabricación de piezas estructurales de aleación de aluminio y magnesio a gran escala se centran principalmente en reducir el aire atrapado durante la fundición a alta presión, minimizar la formación de bolsas de aire y abordar los problemas del tratamiento térmico.
Una solución al problema del aire atrapado es la fundición a presión de alto vacío, que puede prevenir eficazmente la formación de bolsas de aire.
Esta tecnología de fundición a presión al vacío se ha aplicado con éxito a la producción en masa de piezas fundidas estructurales de automóviles, proporcionando técnicas y procesos de conformado avanzados para la producción de piezas fundidas de aleaciones de alta calidad.
Tecnología de fundición de precisión para piezas fundidas.
Con el avance de la tecnología de fundición de automóviles, el moldeo por fundición de precisión se ha convertido en un método de fundición popular. Las piezas fundidas producidas con este método se pueden utilizar sin mucho corte o incluso sin corte alguno.
En los últimos años, el desarrollo de la tecnología de moldeo de precisión por fundición ha sido rápido debido a las mejoras en la precisión dimensional de las piezas fundidas. Han surgido varios métodos de formación de piezas fundidas, incluida la fundición en arena de precisión, la fundición a espuma perdida, la fundición a presión controlable y la fundición a presión.
Para eliminar defectos de fundición, mejorar la calidad interna y ampliar la aplicación de la fundición a presión, se han desarrollado varios métodos de proceso basados en la tecnología de fundición a alta presión, como la fundición al vacío, la fundición a presión llena de oxígeno, la matriz reológica o la tixotrópica de metal semisólido. fundición.
La fundición por compresión, en la que la pieza fundida se llena y solidifica bajo presión, se utiliza ampliamente en la producción de piezas fundidas de aleación de aluminio de alto rendimiento, como subchasis de aleación de aluminio. La fundición por compresión tiene las ventajas de estabilidad, ausencia de salpicaduras de metal, reducción de la pérdida por oxidación del metal fundido, eficiencia energética, operación segura y reducción de defectos en los orificios de fundición.
La creciente demanda de producción de automóviles requiere que las piezas fundidas sean de alta calidad, excelente rendimiento, forma casi final, múltiples variedades, bajo consumo y bajo costo. Las piezas de fundición representan entre el 15% y el 20% de un vehículo completo, lo que significa que la industria de la fundición debe adoptar continuamente nuevas tecnologías y materiales para mejorar el nivel general de fundición.
La tecnología de fundición de precisión cumple con los requisitos de las piezas fundidas de automóviles y su aplicación cubrirá diversos procesos de producción de piezas fundidas de automóviles.