Función del orificio de fabricación de chapa metálica
El orificio de fabricación de chapa está diseñado para evitar que se estire durante el doblado de la chapa.
Cuando la línea de plegado se cruza en un solo punto o está cerca del borde de la placa y tiene menos del doble del espesor de la placa, es necesario aumentar el tamaño del orificio de fabricación para evitar que se doble y se estire.
Los agujeros de fabricación se utilizan normalmente en piezas de chapa que requieren doblarse y doblarse los bordes. En los casos en los que no es necesario enrollar ni doblar los bordes, se puede eliminar la necesidad de un orificio inicial de fabricación.
Desventajas de no tener agujeros de fabricación:
Sin agujeros de fabricación, los bordes y esquinas del material reducirán su espesor y requerirán masilla para soldar. Esto también puede provocar la deformación de la soldadura.
Ventajas de tener agujeros de fabricación:
En los casos de envoltura de bordes, los orificios de fabricación pueden garantizar un pliegue suave en el borde enrollado sin doblarse ni estirarse.
Habilidades de perforación de agujeros en el proceso de doblado de chapa metálica
Determinación del tamaño del orificio de fabricación:
El tamaño del orificio de fabricación de chapa se determina en función de su posición. Si el agujero está ubicado en la intersección de dos líneas, debe tener el doble del espesor de la placa. El espesor mínimo no debe ser inferior a 1,5 veces el espesor de la chapa. Al doblar chapas gruesas, el orificio de fabricación debe ampliarse adecuadamente para tener en cuenta el ángulo de curvatura.
Desventajas de este agujero de fabricación:
Después del doblado, especialmente en el caso de láminas gruesas, hay una pérdida significativa de material en el ángulo de doblado, lo que hace que sea feo y difícil de soldar. En esta situación, es necesario mejorar el método de fabricación de agujeros.
Método de optimización de orificios de fabricación
El tamaño del orificio en la fabricación de chapa metálica se puede determinar en función del borde de flexión y teniendo en cuenta el espesor de la placa y el ángulo de flexión para evitar posibles problemas.
Para obtener una representación visual, consulte la figura siguiente.
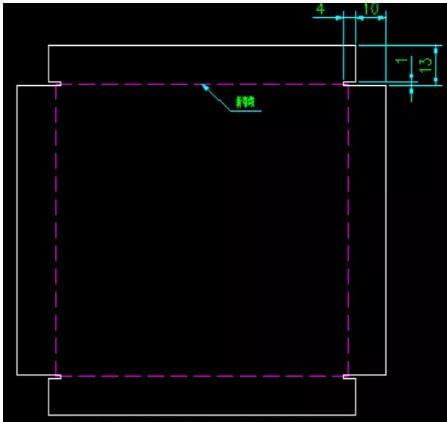
La figura superior muestra una caja de chapa cuadrada con un espesor de 3 mm y una altura de plegado de 15 mm en los cuatro lados.
Esquema de mejora de orificios de fabricación
Mejora en el Método de Blanking:
Existen dos métodos de corte de chapa: corte por punzonado y corte por láser. El punzonado produce principalmente orificios redondos, con una capacidad limitada para producir orificios cuadrados o largos debido a restricciones del molde. En el caso de la lámina de 3 mm que se muestra en la figura anterior, se utiliza corte por láser para el estampado.
Mejora de la forma del orificio de fabricación:
Para evitar problemas estéticos después del doblado, se puede utilizar una forma de tira larga para los agujeros de fabricación.
Determinación del tamaño del orificio de fabricación de tiras largas:
Normalmente se utiliza un ancho de 1 mm, ya que no afecta negativamente a la apariencia ni a la liberación de deformaciones por flexión de la chapa.
Método para calcular la dimensión de profundidad:
La dimensión de profundidad se calcula de la siguiente manera: 10 mm es igual a la altura de plegado menos 3 mm más un factor de 5 y 4 mm es igual al espesor de la chapa más 1 mm.
Efecto de mejora del agujero de fabricación.
Cuando se utiliza este método, la pieza de chapa después de doblarla tendrá un espacio estrecho de solo 1 mm. Vea la representación tridimensional para obtener una representación visual.
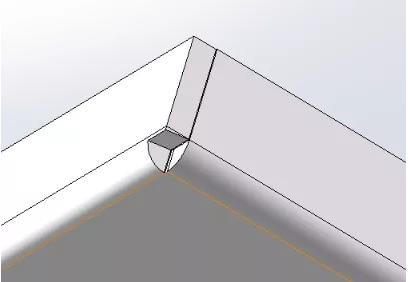
Después de doblar el orificio de fabricación realizado mediante este método, el ángulo de flexión se controla bien y, como resultado, se puede realizar la soldadura sin necesidad de material de relleno adicional.
¿Por qué se deben evitar doblarse y estirarse?
Impacto de flexión y tracción:
(1) El tamaño del pliegue se ve afectado:
Durante el proceso de trefilado, se requiere una cantidad significativa de fuerza para separar el espesor de la chapa. Esto puede hacer que la pieza se mueva y provocar un desplazamiento dimensional debido a la dirección impredecible de la fuerza aplicada.
(2) El dado doblado es vulnerable a sufrir daños:
Como se indicó anteriormente, hay altos niveles de fuerza presentes en los bordes afilados, que pueden exceder la capacidad de soporte de la matriz, provocando su colapso y daño.
Doblado Posicionamiento Fabricación Orificio Aplicación Patrón
Tamaño y forma del orificio de fabricación:
- El tamaño de la abertura para el orificio de fabricación es de 1 mm x 0,2 mm con un radio de raíz de 0,1 mm. Este diseño es adecuado para espesores de chapa menores o iguales a 3 mm.
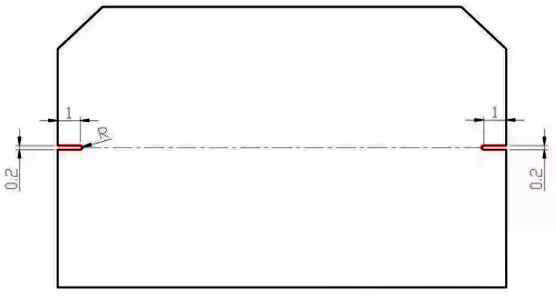
- El tamaño de la abertura para el orificio de fabricación es de 1 mm x 0,4 mm con un radio de raíz de 0,2 mm. Este diseño es adecuado para espesores de chapa que oscilan entre 3 mm y 6 mm.
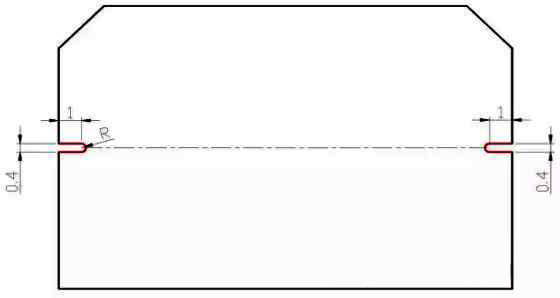
Ámbito de uso:
- Tipo de ángulo:
El ángulo de curvatura no es perfecto de 90 grados y se perforan orificios de posicionamiento en todas las posiciones de curvatura, incluidos los puntos de curvatura superpuestos.
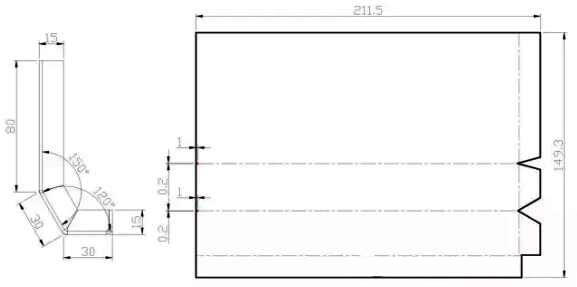
- Tipo de montaje:
Para piezas de apariencia o piezas de unión a tope con estrictos requisitos de precisión, los orificios de posicionamiento deben perforarse en la posición de flexión.
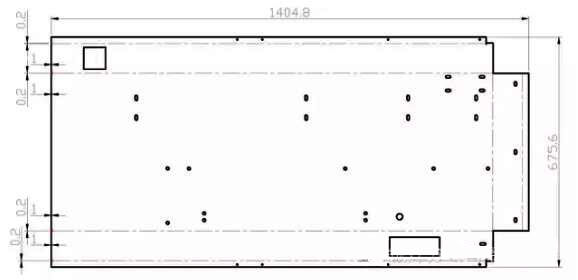
- Tipo de tamaño grande:
Cuando el tamaño del pliegue supera los 200 mm, todos los orificios de posicionamiento deben perforarse en la posición del pliegue.
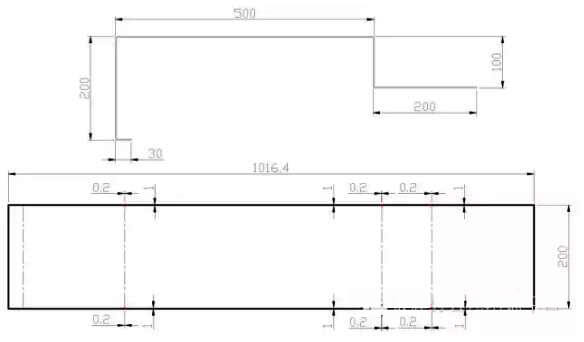
- Plegado continuo de varios tipos complejos:
Para el doblado continuo de piezas complejas, se deben agregar orificios de posicionamiento comenzando desde el tercer borde de doblado.
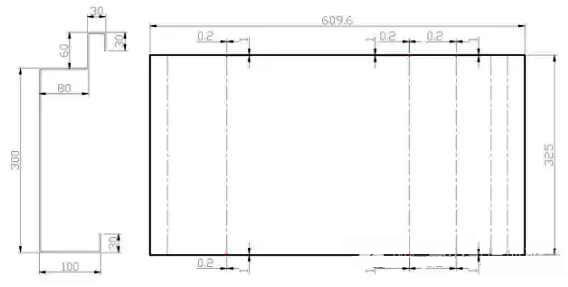
- Tipo de orden de plegado:
Para piezas que no se pueden procesar siguiendo la secuencia de doblado estándar, se deben perforar orificios de posicionamiento en la posición de doblado.
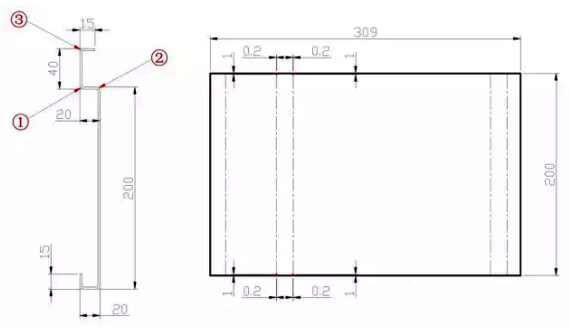
- Tipo de pliegue repetido:
Debido a las limitaciones del equipo de doblado, se deben perforar orificios de posicionamiento en todas las posiciones de doblado para piezas que requieren dobleces repetidos.
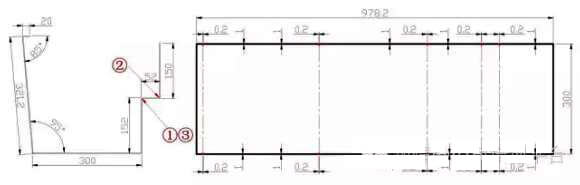
- No confíes en la regla de parada:
Se deben perforar orificios de posicionamiento en todas las posiciones de pliegue para las piezas que no se pueden colocar contra el tipo de regla de tope.
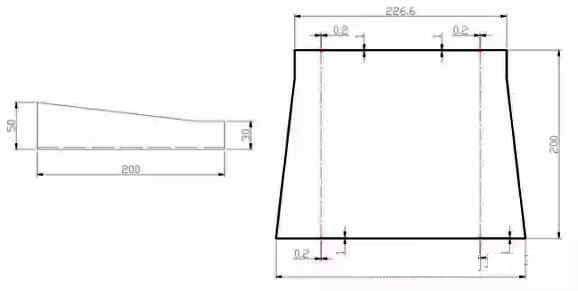
- Tipo de carril guía:
Los orificios de posicionamiento se deben perforar en la posición de flexión para piezas tipo riel guía.
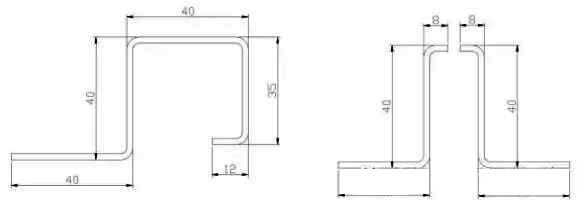
- Orificio de posicionamiento circular:
Se perforan orificios de posicionamiento en los puntos iniciales de los arcos en ambos extremos de la curva.
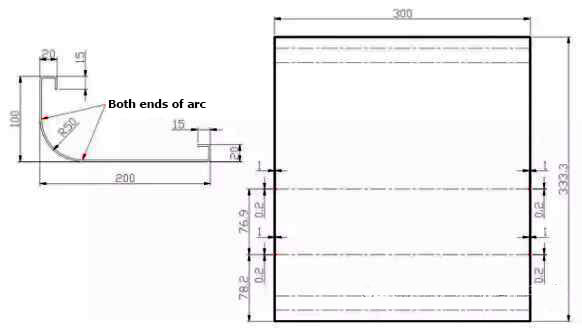
- Tipo de placa de tracción:
Los orificios de posicionamiento deben perforarse en el lugar donde se doblan los componentes de la placa impulsora.
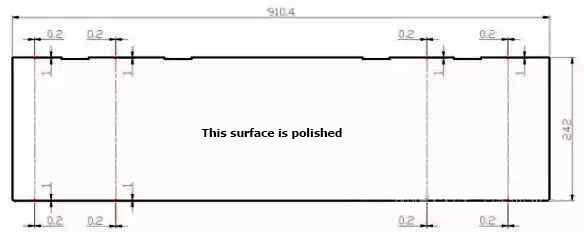
- Tipo de superposición:
Los orificios de posicionamiento deben perforarse en la ubicación superpuesta de los componentes superpuestos. El orificio de posicionamiento debe perforarse hasta la dimensión especificada para un doblado continuo, según el borde superpuesto.
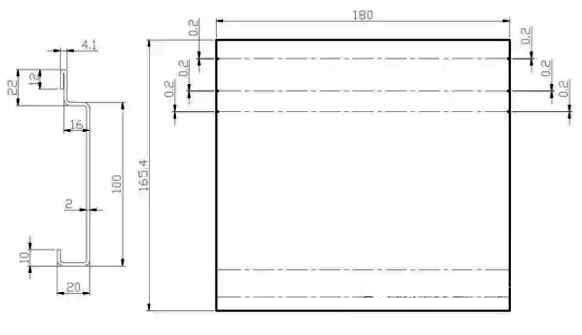