Para resolver el problema del agrietamiento en productos de carburo cortados con alambre, se analizó la microestructura de la superficie de la aleación ajustando los parámetros de procesamiento del corte con alambre según la situación actual de los productos de la empresa. A través de comparación experimental, se identificaron los principales factores causantes de grietas y se propusieron soluciones.
1. Prefacio
WEDM (mecanizado por descarga eléctrica por alambre) se utiliza ampliamente en el procesamiento de carburo como material de moldes y piezas resistentes al desgaste, principalmente para piezas de tamaño pequeño, de forma compleja e inadecuadas para el mecanizado con muelas abrasivas. Este proceso mejora la eficiencia del procesamiento en comparación con los métodos tradicionales.
Sin embargo, cuando se utiliza WEDM para mecanizar piezas de aleación con estructuras complejas, a menudo se ignora el impacto en el área de la microestructura de la superficie de la aleación. Esto puede provocar cambios significativos en la microestructura de la superficie mecanizada, afectando el rendimiento de la pieza de carburo.
Las investigaciones han demostrado que WEDM puede causar microfisuras y otros defectos en la superficie de los productos de troquel, lo que afecta su rendimiento. Para solucionar este problema, los investigadores propusieron medidas de mejora, como el uso de fluido de corte compuesto en los dos primeros cortes y queroseno en el acabado final. Se ha demostrado que esto reduce la rugosidad de la superficie (Ra) a menos de 1 mm para el carburo YG8.
Liu Yike analizó los resultados de las pruebas del mecanizado WEDM de moldes de carburo basándose en el principio de electroerosión y descubrió que, aunque aumentar el ancho del pulso mejora la eficiencia del mecanizado, pueden producirse grietas más allá de cierto valor. Luo Binhui y otros realizaron una prueba comparativa sobre procesos de electroerosión que pueden afectar el agrietamiento en fresas de carburo y encontraron soluciones al problema del agrietamiento.
Esta publicación se basa en investigaciones previas y la experiencia de la empresa para analizar mejor el mecanismo de agrietamiento en productos de carburo causado por el corte de alambre. Al cambiar los parámetros eléctricos de la electroerosión por hilo, se analiza el impacto de los parámetros eléctricos de corte por hilo en las grietas microestructurales de la superficie de la aleación y se proponen métodos para reducir y prevenir las grietas.
2. Mecanismo de generación de grietas
El corte con alambre se diferencia del corte convencional porque no entra en contacto directo con la pieza de trabajo. En cambio, se basa en la descarga continua de chispas pulsadas que se produce entre el filo y la pieza de trabajo. Esta descarga aprovecha la alta temperatura generada durante la chispa parcial e instantánea para desgastar gradualmente los materiales metálicos.
La descarga de chispas se realiza en un medio líquido aislado, como una emulsión. La densidad de corriente en el área de descarga durante el corte del alambre puede alcanzar 10.000 A/mm2 y la temperatura puede alcanzar 10.000-12.000 ℃. El líquido dieléctrico utilizado en el proceso se enfría rápidamente.
La energía EDM crea un campo de temperatura no uniforme y variable en el tiempo en la superficie del material, lo que genera un estrés térmico significativo y fuertes propiedades de choque térmico. En WEDM, la superficie de mecanizado sufre un rápido calentamiento y enfriamiento, lo que provoca una expansión y contracción desigual del material y potencialmente conduce a un gran estrés térmico.
Esto es particularmente problemático cuando se mecanizan materiales duros y quebradizos como el carburo y el cermet, y puede provocar grietas en la superficie si los parámetros eléctricos no se eligen correctamente y la tensión térmica excede el límite de resistencia del material.
A menudo aparecen microfisuras en la superficie debido a la generación de tensión de tracción causada por la alta temperatura instantánea y el rápido enfriamiento durante la electroerosión. Estas grietas generalmente ocurren solo en la capa fundida, pero pueden expandirse hacia la capa afectada por el calor cuando la energía del pulso es alta (durante el mecanizado en desbaste).
La energía de descarga recibida por la pieza tiene un impacto significativo en la formación de microfisuras: una energía más alta da como resultado grietas más anchas y profundas, mientras que una energía de pulso más baja conduce a grietas más estrechas y menos profundas y distribuciones de agujeros más pequeños y pequeños.
La sensibilidad de los diferentes materiales de las piezas al agrietamiento varía según la conductividad térmica del material, siendo los materiales frágiles como el carburo particularmente propensos a microfisuras superficiales.
En la Figura 1 se muestra una visualización del proceso de descarga de corte de alambre.
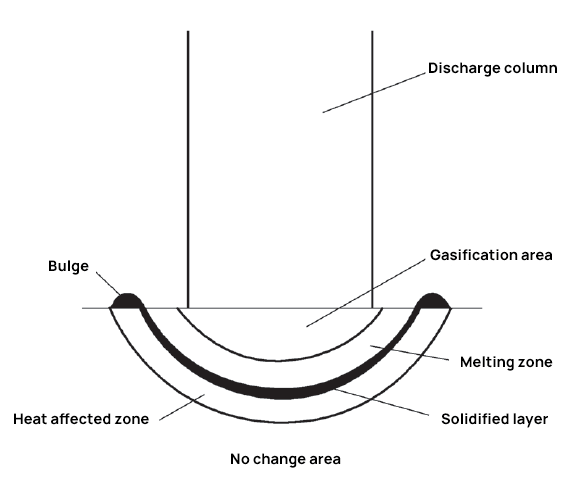
Fig. 1 descarga de corte de alambre
Según el modelo de tensión térmica, la tensión máxima es directamente proporcional a la cantidad de calor que ingresa al material. Esta relación es consistente en condiciones similares y está directamente relacionada con la energía de entrada del pulso eléctrico.
A medida que aumenta la potencia de entrada, el material absorbe más calor.
Por tanto, a mayor potencia, mayor será la tensión y más fácil será que se produzcan grietas. Ignorando la pérdida de energía, la energía que actúa sobre la pieza de trabajo en el proceso de mecanizado se puede simplificar como energía del pulso de descarga de corte de alambre, que es
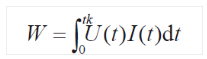
Dónde,
- W es energía de pulso (J);
- U es voltaje de descarga instantánea intermitente (V);
- I es la corriente de descarga instantánea intermitente (A);
- t es el tiempo(s);
- tk es la duración de la descarga (ancho de pulso, s).
La energía (w) de un pulso de descarga durante el corte del alambre es proporcional al voltaje de descarga (U), la corriente de descarga (I) y la duración de la descarga (ancho de pulso, tK). Se observó que cuando el ancho del pulso es constante, un aumento en el voltaje y la corriente de descarga intensificará la generación y propagación de microfisuras. Por otro lado, si el voltaje y la corriente de descarga son fijos, un aumento en el ancho del pulso tendrá el mismo efecto.
3. Plan de prueba
Los bujes de eje de carburo son muy valorados por su dureza, resistencia al desgaste y resistencia a la corrosión, lo que los hace populares en la industria de producción de petróleo. Se utilizan en diversos componentes, como motores de bombas eléctricas sumergibles, bombas centrífugas, protectores, ejes separadores y casquillos de cojinetes lisos, casquillos de eje de motor, casquillos de cojinete perforador, casquillos de cojinete de empuje y casquillos de eje. Estos manguitos realizan funciones cruciales, como proporcionar soporte giratorio, estabilidad, empuje y sellado.
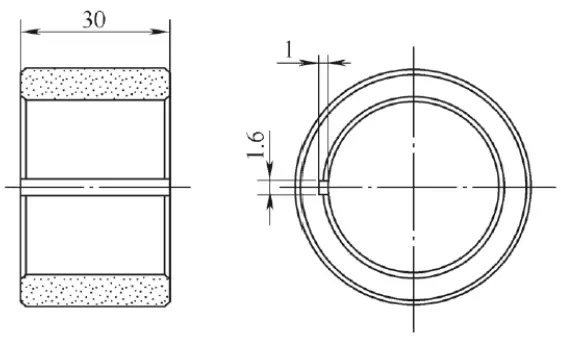
Fig. 2 Manguito de eje de carburo convencional
En la prueba, el equipo de corte de alambre mediano utilizado fue el CTP350.
El fluido de corte utilizado fue una emulsión con una concentración del 8% y el alambre de corte utilizado fue un alambre de molibdeno de 0,18 mm de diámetro.
En cada caso, sólo se fijó una pieza para su procesamiento.
Consulte la Tabla 1 para conocer los parámetros de procesamiento de corte de alambre.
Grupo de prueba No | NO. | Voltaje/V | Actual/A | Duración del pulso/μs | Intervalo de pulso/μs | Velocidad de alimentación de alambre/(m/s) |
Uno | 1 | 100 | 1.5 | 40 | 320 | 15 |
dos | 100 | 1.5 | 36 | 282 | 15 | |
3 | 100 | 1.5 | 24 | 192 | 15 | |
4 | 100 | 1.5 | 12 | 96 | 15 | |
Dos | 5 | 100 | 3.5 | 20 | 160 | 15 |
6 | 100 | 2.8 | 20 | 160 | 15 | |
7 | 100 | 2.4 | 20 | 160 | 15 | |
8 | 100 | 2.0 | 20 | 160 | 15 | |
Tres | 9 | 120 | 2.0 | 20 | 160 | 15 |
10 | 110 | 2.0 | 20 | 160 | 15 | |
11 | 90 | 2.0 | 20 | 160 | 15 | |
12 | 70 | 2.0 | 20 | 160 | 15 | |
cuatro | 13 | 100 | 2.8 | dieciséis | 128 | 15 |
14 | 80 | 1.0 | 6 | 48 | 6 | |
15 | 50 | 0.3 | 4 | 32 | 3 |
4. Resultado de la prueba
4.1 Efecto del ancho de pulso sobre las microfisuras en la superficie de la aleación
1 # ~ 4 # Las fotografías metalográficas del producto se muestran en la Fig.
Se observa que a medida que disminuye la anchura del pulso, las microfisuras en la superficie de la aleación se vuelven progresivamente más pequeñas. Con una duración de pulso de 40 milisegundos, la profundidad de las microfisuras alcanza los 15 milímetros. Sin embargo, con una duración de impulso de 12 milisegundos prácticamente no se producen microfisuras.
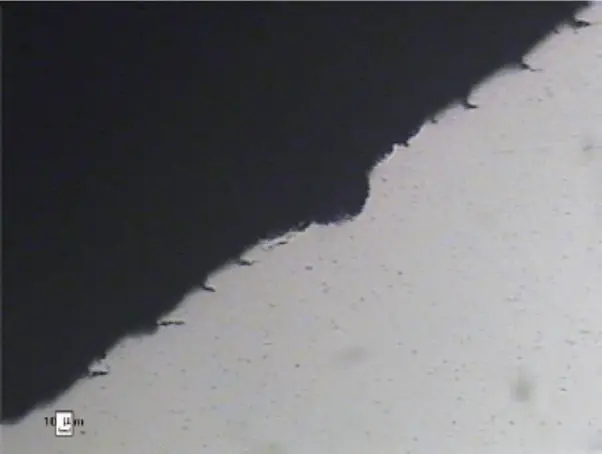
Fig. 3 Fotografías metalográficas n.º 1 de productos.
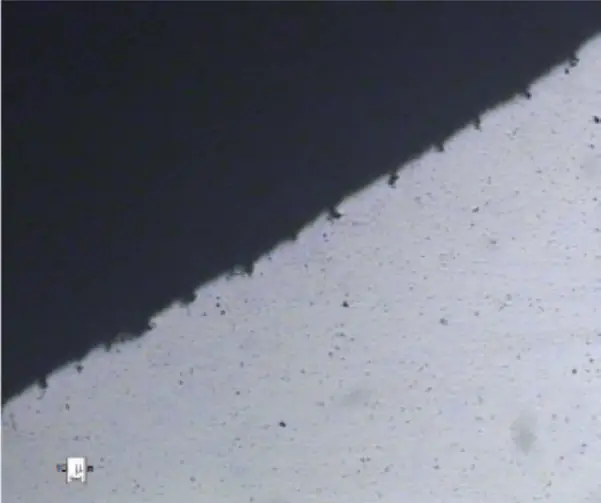
Fig. 4 #2 fotografías metalográficas de productos
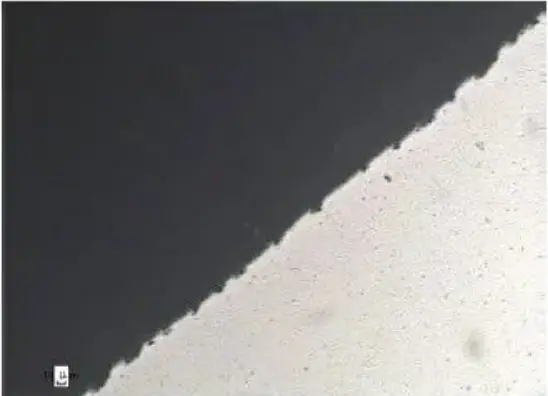
Fig. 5 #3 fotografías metalográficas de productos.
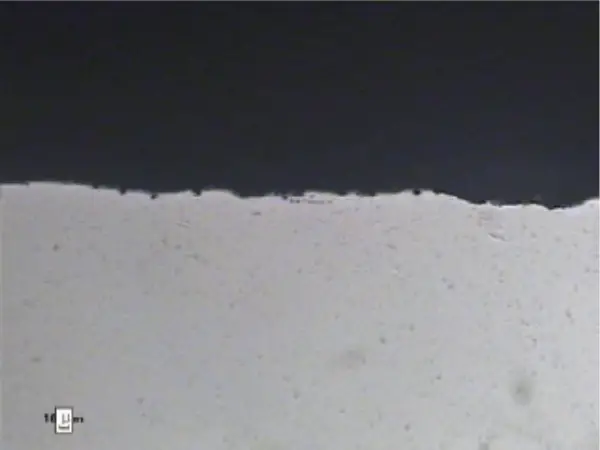
Fig. 6 #4 fotografías metalográficas de productos.
4.2 Efecto de la corriente sobre las microfisuras en la superficie de la aleación.
Las fotografías metalográficas del producto 5# ~ 8# se muestran en la Fig. 7 ~ Fig. 10.
Se observó que la profundidad de la grieta aumenta a medida que aumenta la corriente de procesamiento. A 3,5 A, la profundidad de la grieta supera los 30 mm; cuando la corriente de procesamiento es de 2,8 A, la profundidad de la grieta es igual a 30 mm; y cuando la corriente de procesamiento es de 2,4 A, la profundidad de la grieta es de 20 mm. A 2,0 A, la profundidad de la grieta es menor y mide 10 mm.
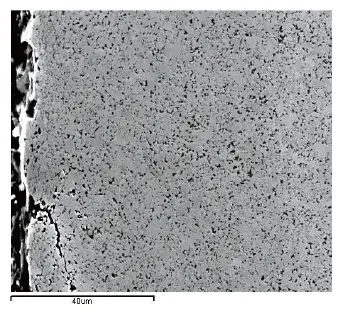
Fig. 7 #5 fotografías metalográficas del producto
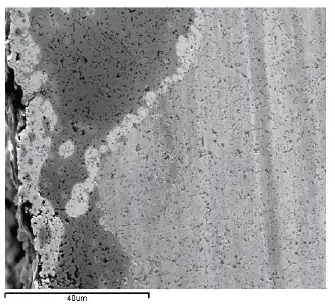
Fig. 8 #6 fotografías metalográficas de productos.
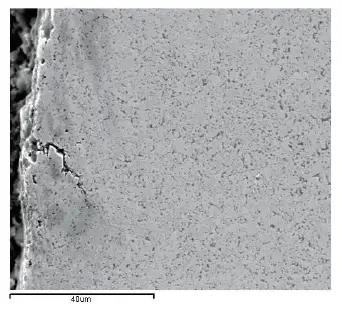
Fig. 9 #7 fotografías metalográficas de productos.
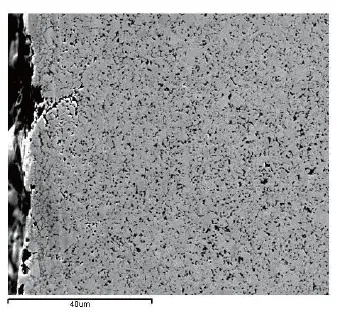
Fig. 10 #8 fotografías metalográficas de productos
4.3 Efecto de la tensión sobre las microfisuras en la superficie de la aleación.
Las fotografías metalográficas del producto de 9# ~ 12# se muestran en la Fig. 11 ~ Fig. 14.
Se observó que cuando la corriente se establece en 2 A y el ancho del pulso es de 20 ms, el voltaje de procesamiento varía de 70 a 120 V. No se encontraron microfisuras en la aleación en la sección cortada. Esto indica que, con corriente y ancho de pulso constantes, el efecto del voltaje sobre el microcraqueo de la aleación es insignificante.
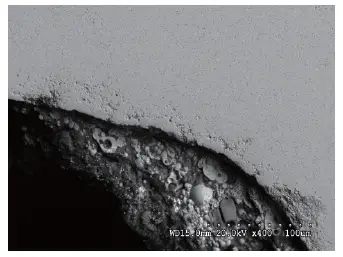
Fig. 11 #9 fotografías metalográficas de productos.
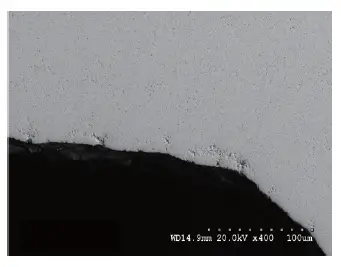
Fig. 12 #10 fotografías metalográficas de productos.
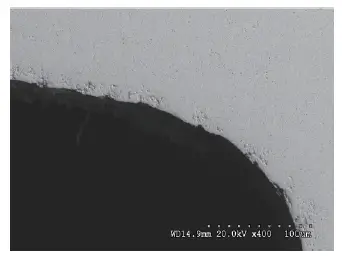
Fig. 13 #11 fotografías metalográficas de productos.

Fig. 14 #12 fotografías metalográficas de productos.
4.4 Efecto de los tiempos de corte sobre las microfisuras en la superficie de la aleación
13# ~ 15# fotografías metalográficas de productos se muestran en la Fig.
La calidad de la superficie de los productos se ha mejorado significativamente mediante múltiples procesos de corte, reduciendo la profundidad de las microfisuras.
Con hilo medio cortado y procesado dos veces, la profundidad de las microfisuras en el producto se reduce a 15 mm.
Y con un corte y procesamiento de alambre medio tres veces, la profundidad de las microfisuras se reduce aún más a 10 mm.
Dos procesos de corte cumplieron con el requisito actual de que la profundidad de las microfisuras en los productos de manguito de eje de carburo sea inferior a 20 mm.
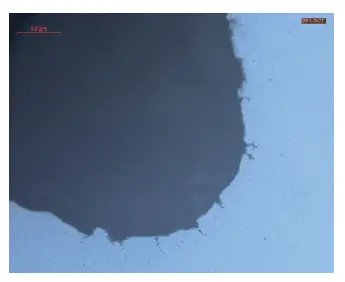
Fig. 15 #13 fotografías metalográficas de productos.
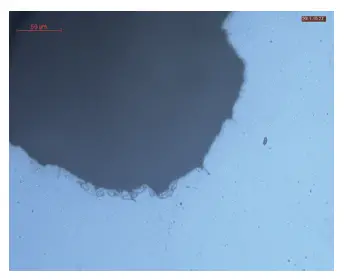
Fig. 16 #14 fotografías metalográficas de productos.
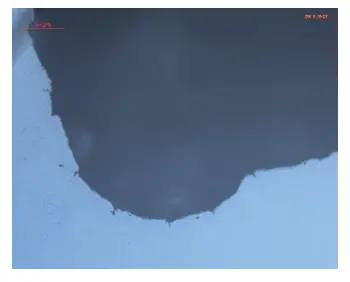
Fig. 17 #15 fotografías metalográficas de productos.
5. Conclusión
Durante el EDM (mecanizado por descarga eléctrica), la superficie de la pieza sufre un rápido cambio de temperatura debido a la abrupta alternancia de frío y calor. Esto da como resultado un fuerte proceso de choque térmico transitorio con alta velocidad y gran amplitud.
Al mecanizar materiales frágiles como el carburo, las grietas se pueden reducir o evitar reduciendo la amplitud de la tensión y su choque térmico variable en el tiempo. Esto se puede lograr mediante varios métodos que limiten el choque térmico.
El ancho de pulso y la corriente de procesamiento tienen un impacto significativo en las microfisuras superficiales de la aleación. Un ancho de pulso más amplio y una corriente más alta provocan grietas más profundas. Sin embargo, el efecto de la tensión sobre las microfisuras superficiales no es significativo.
No se observaron microfisuras cuando el ancho del pulso se ajustó a 12 ms. Para evitar grietas, se recomienda evitar procesar corrientes superiores a 2 A al seleccionar los parámetros eléctricos.
Para minimizar el estrés térmico y su impacto en la pieza de trabajo, se deben utilizar parámetros eléctricos de pulso estrecho y pico alto y se debe utilizar el efecto de superposición del campo de temperatura. Esto hará que el material de la pieza se vaporice, lo que generará un mayor calor de gasificación que elimina la mayor parte del calor y evita que la superficie de la pieza se sobrecaliente.
El corte múltiple es un método eficaz para reducir y eliminar las microfisuras superficiales.