Las estructuras de soporte son un componente esencial para la fabricación exitosa de piezas impresas en 3D.
Aunque una de las principales ventajas de la impresión 3D es su capacidad para crear formas geométricas complejas y libres, gran parte de la libertad de diseño que ofrece la impresión 3D es difícil de lograr sin el uso de estructuras de soporte.
Son cruciales para evitar la deformación y el colapso de piezas, entre otros usos; por lo tanto, comprender y diseñar estructuras de soporte es una habilidad necesaria para cualquier ingeniero de fabricación aditiva.
Este artículo analiza los requisitos, los pros y los contras, la eliminación y cómo minimizar el uso de estructuras de soporte en diversas tecnologías de impresión.
La importancia de las estructuras de soporte en la impresión 3D
Utilizadas junto con prácticamente todas las tecnologías de impresión 3D, las estructuras de soporte desempeñan un papel crucial para garantizar la capacidad de impresión de las piezas durante el proceso de impresión 3D.
Los soportes ayudan a evitar la deformación de las piezas, fijarlas a la base de impresión y asegurar su conexión con el cuerpo principal de las piezas impresas. Al igual que los andamios, estos soportes se utilizan durante el proceso de impresión y se retiran posteriormente.
La impresión de piezas con características de diseño complejas, como protuberancias, agujeros y puentes, presenta desafíos importantes.
Tomemos como ejemplo la impresión 3D en metal; Cuando la impresión incluye protuberancias o estructuras de puentes, puede ocurrir deformación e incluso colapso durante el proceso si no se utilizan estructuras de soporte.
Estas estructuras de soporte ayudan a prevenir el colapso de las piezas formadas durante la impresión, lo que aumenta considerablemente la tasa de éxito de la impresión. Sin embargo, no todas las estructuras colgantes requieren soporte adicional.
Si el ángulo vertical del voladizo es inferior a 45 grados, no se necesita soporte.
Cuando el ángulo vertical de dicha estructura es inferior a 45 grados, la impresora 3D tiene un desplazamiento horizontal mínimo en capas sucesivas, lo que permite que cada capa proporcione soporte para el siguiente nivel.
Por lo tanto, 45 grados es un ángulo crítico, por debajo del cual no se necesita soporte. Por supuesto, esto también depende del rendimiento de la impresora y de las propiedades de los materiales utilizados. Si el rendimiento de la impresora es deficiente, es posible que se requiera soporte incluso para ángulos inferiores a 45 grados.
Además, tecnologías como la impresión 3D de metal implican a menudo procesos a alta temperatura, durante los cuales el soporte también puede servir como disipador de calor.
Esto se debe a que las estructuras de soporte agregadas durante el proceso de fabricación aditiva de metal ayudan a alejar el calor de la pieza, evitando la formación de tensiones residuales debido a las altas temperaturas durante la impresión y previniendo defectos como deformaciones, deformaciones y grietas.
Por supuesto, no es sólo la impresión 3D en metal la que considera añadir soportes; Casi todas las tecnologías de impresión 3D necesitan incluir, hasta cierto punto, estructuras de soporte.
La siguiente tabla ilustra las diferencias en el uso de soporte entre varios métodos de impresión 3D:
Principios técnicos | Materiales | ¿Se necesita apoyo? |
Fusión selectiva por láser (SLM) Sinterización directa de metales por láser (DMLS) Deposición de energía directa (DED) Fusión por haz de electrones (EBM) | Materiales metálicos | Sí |
Estereolitografía (SLA) | Fotopolímero | Sí |
Sinterización selectiva por láser (SLS) | Materiales en polvo | No |
voladura de materiales | Materiales en polvo | Sí |
Modelado por deposición fundida (FDM) | Plástico termoplástico | Sí |
spray adhesivo | Materiales en polvo | No |
Fusión de lecho de polvo (SLM, DMLS, EBM)
Las estructuras de soporte son indispensables en la impresión 3D de metal. Aunque los componentes formados por la tecnología de fusión en lecho de polvo están rodeados de polvo suelto, lo que proporciona cierto soporte, estas tecnologías siempre requieren soporte para asegurar su fijación a la base y mitigar los efectos de las tensiones residuales.
Sin estructuras de soporte, los componentes que sobresalen o están inclinados, así como la tensión interna del metal, pueden dañar el objeto impreso y provocar fallos en la impresión. Generalmente, las estructuras de soporte en la tecnología de impresión basada en lecho de polvo se dividen principalmente en dos tipos:
Soporte lineal: Este tipo de soporte está formado por columnas verticales conectadas a toda la estructura saliente. Sin embargo, este tipo de soporte es más difícil de eliminar.
Soporte en forma de árbol: este tipo de soporte tiene forma de ramas de árboles. Se utiliza para soportar las partes sobresalientes del componente. Sólo está conectado a las posiciones sobresalientes.
Su ventaja es que es más fácil de desmontar y no daña el componente en sí.
Sin embargo, cabe señalar que las estructuras de soporte en forma de árbol sólo son adecuadas para voladizos no planos. Para repisas planas, no pueden proporcionar suficiente soporte.
Se puede agregar soporte al área de contacto entre la parte inferior de la pieza impresa y la cama de impresión, donde la tensión residual se concentra más.
Esto ayuda a alejar el calor de la pieza, minimizando así la deformación térmica que puede provocar grietas, deformaciones, hundimientos, delaminación y contracción.
Deposición directa de energía (DED)
La deposición directa de energía es un proceso que fabrica piezas fundiendo directamente el material y construyéndolo capa por capa.
A diferencia de las piezas formadas por fusión de un lecho de polvo que se apoyan en el lecho de polvo circundante, las piezas impresas con DED existen de forma independiente en un espacio tridimensional.
En consecuencia, también requieren estructuras de soporte para garantizar la estabilidad de las piezas, la capacidad de impresión de características complejas y la disipación de calor.
1. Proyecto de apoyo
Al diseñar soportes para piezas producidas mediante tecnología de fusión en lecho de polvo, es fundamental garantizar que se puedan separar fácilmente del cuerpo principal; de lo contrario, no se podrán retirar durante el posprocesamiento.
Los soportes para piezas metálicas suelen imprimirse como una estructura de rejilla.
De esta forma, actúan como disipadores de calor, transfiriendo calor de la pieza, permitiendo que se enfríe de forma más controlada y evitando deformaciones, además de ahorrar costes de material y tiempo de construcción.
Agregar más soportes generalmente da como resultado piezas más precisas, pero también aumenta los costos y el tiempo de posprocesamiento. Curiosamente, la empresa holandesa MX3D ha creado una herramienta de impresión 3D de metal que combina un brazo robótico multieje con una máquina de soldar, permitiendo imprimir piezas metálicas sin necesidad de soportes.
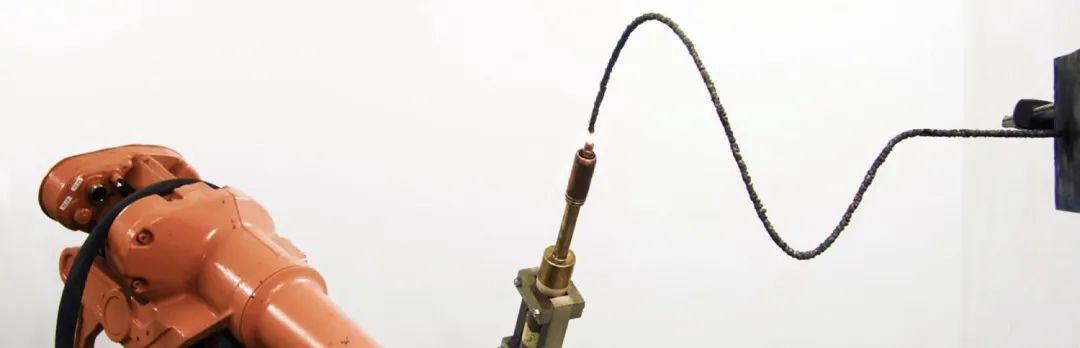
2. Eliminación del apoyo
Quitar soportes de piezas metálicas suele ser más complicado que los procesos basados en polímeros y normalmente requiere herramientas de corte.
Además, si la apariencia de la pieza terminada es importante, es necesario un posprocesamiento (como el pulido) de la pieza metálica para obtener un acabado superficial liso.
Durante el desmontaje del modelo, la mayoría de los soportes son fáciles de quitar si el método es correcto. Primero, puede abrir suavemente los soportes con los dedos para poder manipularlos manualmente.
Para posiciones especiales, podemos optar por utilizar herramientas para desmontar los soportes, incluidos alicates de punta fina, raspadores y cuchillos de trinchar.
Estereolitografía (SLA)
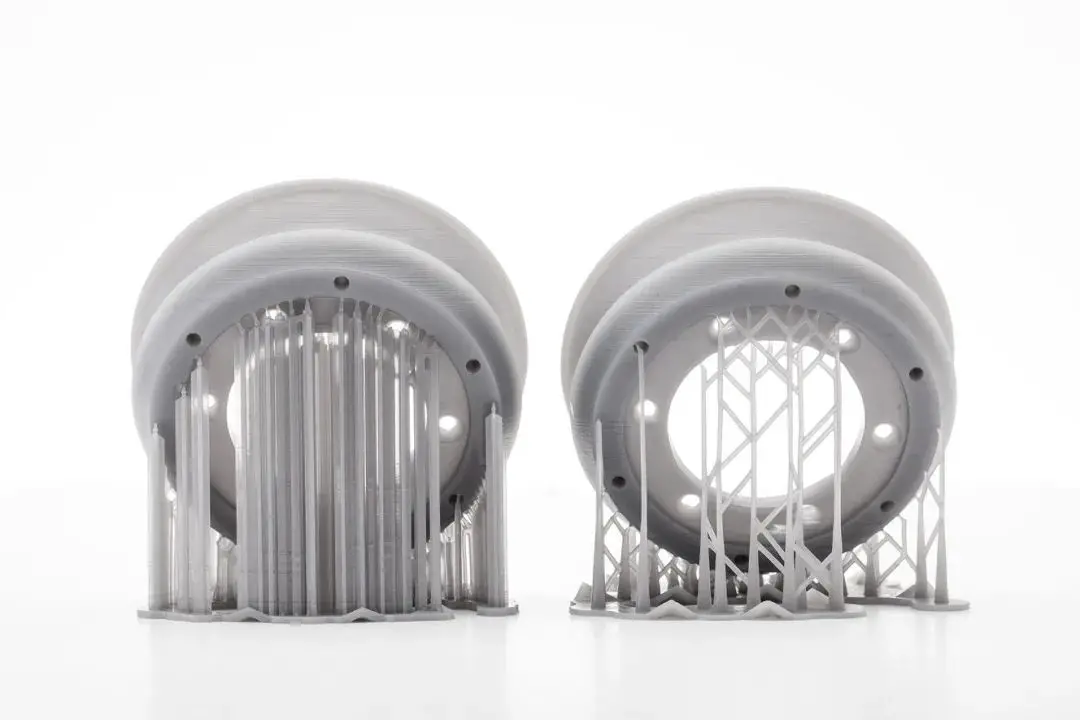
La estereolitografía funciona utilizando una fuente de luz para solidificar la resina líquida. Esta tecnología requiere estructuras de soporte para sujetar firmemente las piezas a la base de impresión y evitar deformaciones.
Los soportes utilizados en SLA son muy finos y tocan ligeramente las piezas para ahorrar materiales. Esto significa que se pueden quitar fácilmente de forma manual, manual o con unos alicates. Sin embargo, como quitar los soportes dejará marcas en la pieza final, es necesario lijarla para asegurar un acabado superficial liso.
1. Proyecto de apoyo
SLA se utiliza a menudo para aplicaciones que requieren estética o acabados superficiales lisos, como prototipos visuales, moldes y audífonos.
Si este es el caso, es fundamental diseñar las piezas para garantizar que la zona frontal de la impresión no entre en contacto con las estructuras de soporte. Aquí es donde entra en juego el diseño de orientación de piezas.
La orientación de las piezas es una consideración crucial en la fase de diseño porque reposicionar las piezas puede ayudar a reducir la cantidad de soporte necesario. Por ejemplo, las piezas tubulares, si se colocan en horizontal, ocuparán más espacio y por tanto requerirán más soporte.
Por otro lado, colocar la misma pieza verticalmente garantiza que se conecte a la placa de construcción con un soporte mínimo.
Modelado por deposición fundida (FDM)
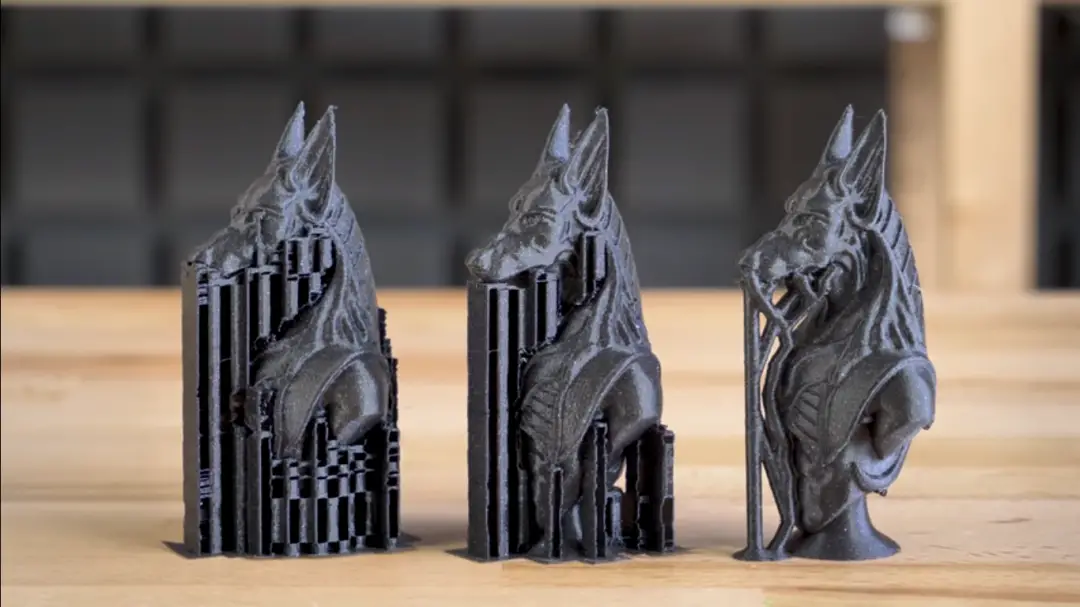
La tecnología de modelado por deposición fundida (FDM) crea piezas extruyendo filamentos calentados capa por capa, cada uno de los cuales se une al anterior después de enfriarse y solidificarse.
1. Proyecto de apoyo
En el proceso FDM, cada capa sobresale ligeramente para poder extenderse más allá del ancho de la capa anterior. Esto significa que se pueden crear características en ángulos de hasta 45 grados sin soporte.
Sin embargo, cuando el voladizo de una pieza FDM supera los 45 grados o la pieza incluye características como puentes y superficies sobresalientes de más de 5 milímetros, se requiere soporte. El soporte en FDM puede tomar la forma de una estructura de celosía o una estructura en forma de árbol.
2. Eliminación del apoyo
Una técnica para eliminar soportes de impresiones FDM es mediante una solución de disolución química.
Normalmente, las impresoras 3D industriales FDM (con dos cabezales de impresión) utilizan materiales de soporte solubles como el alcohol polivinílico (PVA) y el poliestireno de alto impacto (HIPS). Estos materiales se pueden depositar en el modelo mediante una extrusora independiente.
Aunque el PVA se disuelve en agua, puede verse afectado por los cambios de temperatura, provocando obstrucciones en el cabezal de impresión. HIPS, por otro lado, se disuelve en limoneno en lugar de agua y no se ve afectado fácilmente por los cambios de temperatura.
El uso de soportes solubles elimina la necesidad de operaciones manuales y la necesidad de lijado y pulido adicional para eliminar los rastros dejados por los soportes. Por otro lado, este proceso puede llevar mucho tiempo (varias horas) y ser costoso.
voladura de materiales
Cuando se utiliza una impresora 3D Material Jetting, siempre se requiere soporte para estructuras sobresalientes, independientemente del ángulo.
Sin embargo, estos soportes suelen estar fabricados de diferentes materiales que son solubles en agua o que se pueden retirar fácilmente posteriormente con agua a presión o mediante inmersión en un baño de ultrasonidos.
Sinterización selectiva por láser y chorro de aglutinante
La sinterización selectiva por láser y el Binder Jetting son tecnologías basadas en polvo que generalmente no requieren estructuras de soporte.
Esto se debe a que en estas dos tecnologías las piezas impresas están encapsuladas en un polvo suelto que sirve como estructura de soporte.
Desventajas de los corchetes
Si bien son necesarias, las estructuras de soporte aumentan el tiempo general de impresión y los costos de materiales del proceso de producción.
Gastos de materiales:
La generación de medios requiere material adicional durante el proceso de impresión, lo que aumenta el tiempo y los costos de material. Igualmente importante es el hecho de que los soportes no son reutilizables y normalmente se desechan, lo que genera desperdicio de material.
Libertad geométrica limitada:
Al retirar los soportes manualmente, se debe considerar el uso de manos o herramientas al diseñar los soportes. Sin embargo, esto puede limitar su capacidad para diseñar ciertas formas geométricas que requieren soporte pero que son inaccesibles manualmente o con herramientas.
Tiempo añadido:
Diseñar una pieza para acomodar estructuras de soporte y luego crear los propios soportes lleva más tiempo. A pesar de la disponibilidad de software que genera soportes automáticamente, la creación de estructuras de soporte para aplicaciones industriales aún requiere modificaciones manuales y un cierto nivel de conocimiento de diseño.
Postprocesamiento adicional:
Una vez completada la pieza, es necesario retirar los soportes, a veces manualmente, aumentando así el tiempo necesario para el posprocesamiento.
Riesgo de Daño: Durante la fase de postprocesamiento se deben retirar los soportes y pulir la superficie de la pieza.
Cualquier manipulación incorrecta durante el desmontaje de los soportes puede provocar defectos en la superficie de la pieza, afectando su precisión dimensional y su apariencia estética.
Además, cuando los soportes se colocan incorrectamente, como en estructuras delgadas, pueden ocurrir fracturas estructurales. Pueden romperse junto con las estructuras de soporte, provocando un fallo total de la impresión.
Por lo tanto, el uso de estructuras de soporte tiene ciertas desventajas y sólo deben agregarse cuando sea necesario.
Además, también podemos evitar el uso de soportes biselados. El biselado transforma las ubicaciones de los voladizos en voladizos seguros con ángulos inferiores a 45 grados, eliminando la necesidad de soportes y garantizando un uso eficiente del material.
Cuatro métodos para minimizar los apoyos
Reducir el número de apoyos necesarios suele ser una buena estrategia. Ayuda a ahorrar costos de materiales y tiempo de producción. A continuación se ofrecen cuatro consejos esenciales sobre cómo maximizar la reducción y, al mismo tiempo, ahorrar tiempo y materiales de impresión:
1. Elija la orientación ideal de la pieza
Experimentar con la orientación de las piezas es una de las mejores formas de reducir la cantidad de soportes necesarios. La orientación correcta afecta significativamente el tiempo de impresión, el costo y la rugosidad de la superficie de la pieza.
Dependiendo de la dirección de la pieza (vertical, horizontal o angular) se podrán necesitar menos o más soportes.
Considere una pieza impresa con la forma de la letra "T". Colocados en su dirección habitual, ambos brazos de la carta colapsarían sin estructuras de soporte. Sin embargo, si la orientación de la pieza está invertida – dispuesta en posición de “T” invertida – no es necesario ningún soporte.
Este ejemplo ilustra que una pieza se puede construir de varias maneras. Cada cara de la pieza puede tener una superficie diferente conectada a la cama de impresión, lo que implica diferentes necesidades de soporte. Estas necesidades dependen en gran medida de la orientación de la pieza.
Otro ejemplo: al diseñar piezas con características tubulares huecas, una orientación horizontal ocupa más espacio, mientras que una orientación vertical o en ángulo ahorra espacio y reduce la cantidad de soportes necesarios.
2. Optimización de las estructuras de soporte
Cuando los soportes son inevitables, hay que optimizarlos para utilizar el menor material posible y acelerar el proceso de impresión. Por ejemplo, el diseño de optimización de la topología y el soporte de la estructura de celosía se pueden utilizar para reducir el volumen de los soportes, ahorrando así material.
Para muchos procesos de impresión 3D, las técnicas convencionales de generación de soporte se limitan a producir estructuras estrictamente verticales. No ahorran espacio, especialmente cuando hay muchas áreas encima de la cama de impresión que necesitan soporte.
Por el contrario, crear estructuras de soporte en forma de árboles puede ser una opción viable. Estos soportes se asemejan a un árbol ramificado y pueden reducir el uso de material en aproximadamente un 75 % en comparación con las estructuras verticales rectas.
Autodesk Meshmixer es una de las herramientas de software disponibles para crear este tipo de estructuras para procesos FDM, SLA y DMLS.
3. Uso de redondeos y chaflanes
Los filetes y chaflanes pueden servir como soluciones alternativas para crear estructuras de soporte en superficies que sobresalen más de 45 grados.
Un chaflán es una esquina o borde en ángulo o achaflanado, mientras que un filete es una esquina o borde redondeado. Básicamente, estas características cambian ángulos mayores de 45 grados a ángulos de 45 grados o menos y se pueden agregar al interior o exterior de una pieza.
4. Segmentación de piezas impresas
Para modelos 3D muy complejos, a menudo tiene sentido imprimir las piezas individualmente y luego ensamblarlas. Esto no solo reduce la cantidad de soportes, sino que también acelera el proceso de impresión, ahorrando material.
Sin embargo, tenga en cuenta que si se ensamblan piezas impresas en 3D, deben imprimirse en la misma orientación para garantizar un encaje adecuado.
Soportes para impresión 3D: necesarios pero frustrantes
Durante mucho tiempo, las estructuras de soporte se consideraron una “desventaja” inevitable en la impresión 3D. Sin embargo, los avances recientes en hardware y software están desafiando lentamente esta noción.
Tomemos, por ejemplo, Desktop Metal, un fabricante de impresoras 3D de metal, que recientemente desarrolló una solución conocida como "soportes separables" para sus sistemas de estudio y producción, obteniendo una patente para el proceso.
Estos soportes para piezas metálicas impresas en 3D se pueden retirar manualmente. Los soportes separables de Desktop Metal funcionan utilizando una capa de polvo cerámico como interfaz entre la superficie de la pieza y la estructura de soporte.
Tras el proceso de sinterización, la capa cerámica se disuelve, permitiendo retirar sin esfuerzo los soportes de la pieza.
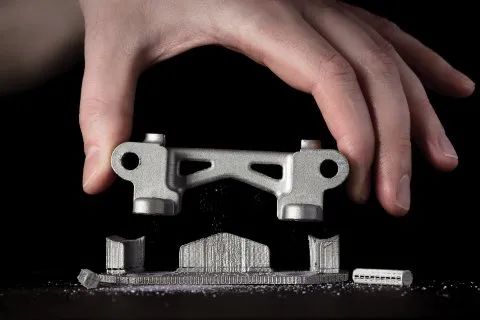

PostProcess Technologies es otra empresa que tiene como objetivo simplificar y acelerar el paso de eliminación de soporte para piezas impresas en 3D. La empresa ofrece una gama de soluciones de eliminación de soporte automatizadas y manos libres para piezas fabricadas aditivamente mediante tecnologías FDM, SLA, PolyJet y CLIP.
Sin embargo, una empresa ha ido aún más lejos en el ámbito del soporte. Velo3D, la empresa detrás del sistema de fusión de lecho de polvo Sapphire, ofrece una tecnología llamada Intelligent Fusion para su sistema, que permite la impresión de piezas metálicas complejas, centrándose en lograr una impresión casi sin soporte.
En comparación con otros sistemas de lecho de polvo metálico, el uso del software de simulación patentado de Velo3D y el monitoreo de circuito cerrado pueden reducir los soportes necesarios para la producción de piezas hasta cinco veces.
En 2021, SLM Solutions lanzó la “Tecnología FreeFloat Supportless”, que reduce o elimina significativamente la necesidad de estructuras de soporte en la impresión de piezas mediante la integración unificada de múltiples tecnologías.
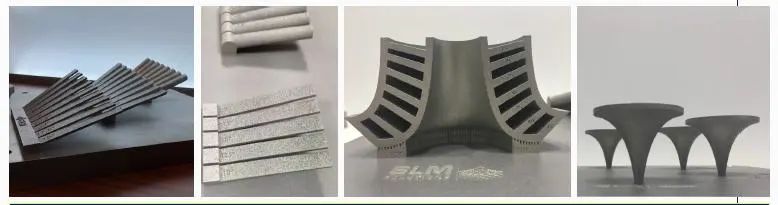
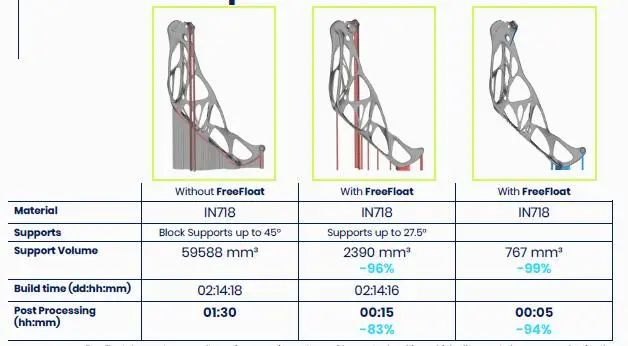
En 2022, los expertos de EOS desarrollaron una variedad de técnicas de optimización de procesos para la producción de piezas impresas en 3D sin soporte, como anillos de estator, carcasas, bombas de turbina, tanques de aceite, intercambiadores de calor, válvulas e impulsores, siendo el ejemplo particularmente típico el impulsor cerrado.
Al optimizar el software de diseño y los conjuntos de parámetros, EOS ha permitido a los usuarios imprimir voladizos y puentes en ángulos mucho más bajos, a veces hasta cero grados, lo que requiere muchos menos soportes o ninguno.
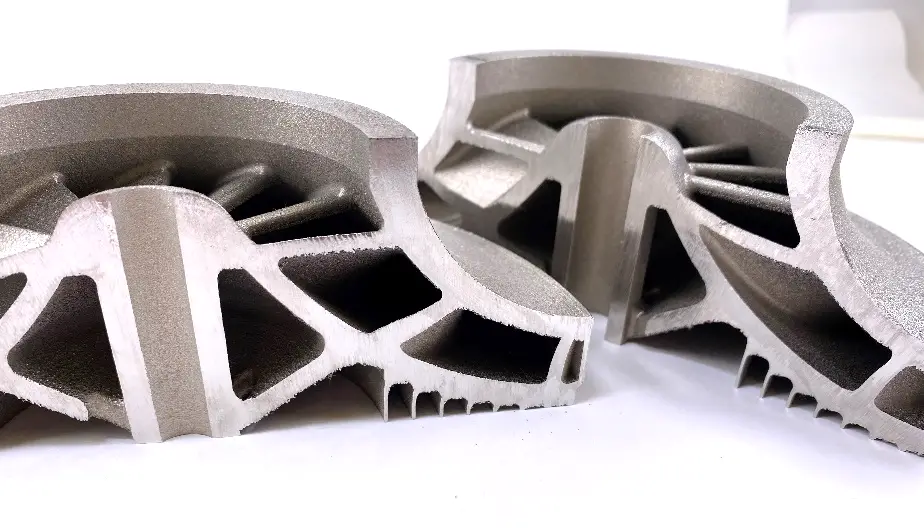
Sin duda, los fabricantes nacionales han logrado avances notables en la impresión sin soporte. No hace mucho, se informó que la empresa líder en impresión 3D, Polite, había descubierto una solución para la impresión sin soporte: las estructuras que sobresalen menos de 30° no necesitan soporte.
Polite afrontó el desafío de la tecnología de impresión 3D de metal SLM independiente.
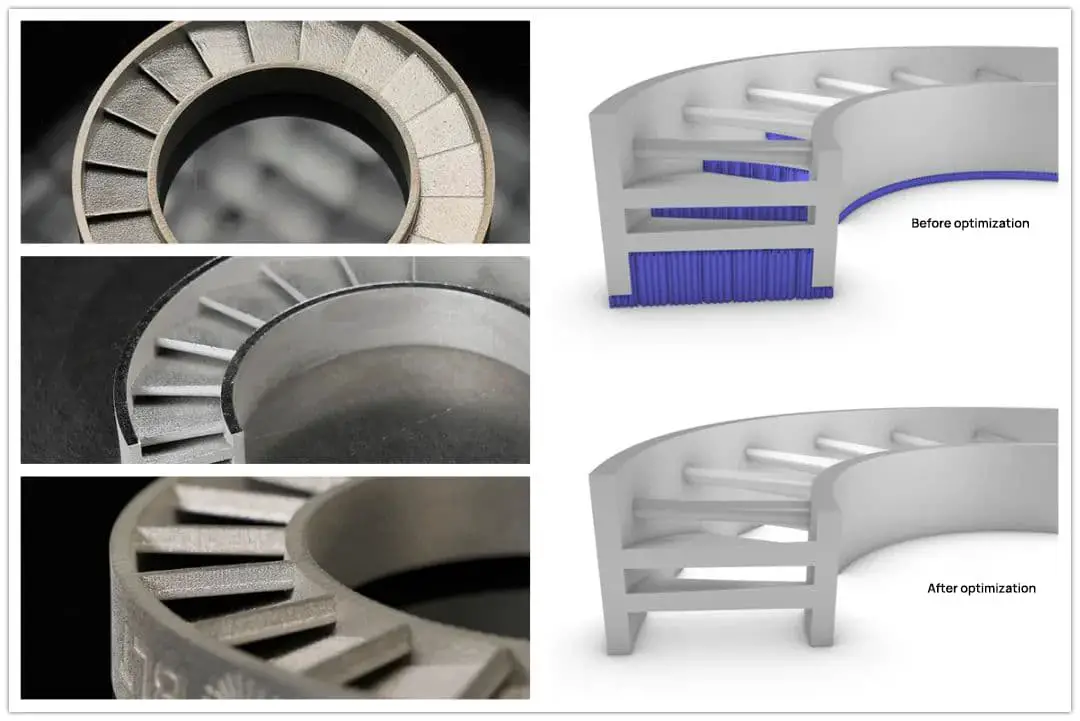
En general, optimizar el diseño y la eliminación del soporte es un desafío clave para hacer que el flujo de trabajo de la impresión 3D sea más rápido y sencillo.
Como puede verse en los ejemplos anteriores, la industria de fabricación aditiva desarrolla continuamente soluciones para superar este desafío.
Sin embargo, además de tecnología, los profesionales necesitan un mayor nivel de habilidades y conocimientos para presentar mejores soluciones.
Esperamos que este artículo haya ampliado tus conocimientos sobre cómo utilizar las estructuras de soporte de manera más efectiva en la impresión 3D, ayudando así a transformarlas de enemigos a aliados.