El nivel de fabricación del molde es un indicador importante para medir el nivel de fabricación del producto de un país, y el molde en sí tiene un costo elevado, conocido como “oro negro”.
Con el desarrollo de la industria automotriz, especialmente el rápido desarrollo de vehículos de nueva energía en China, la demanda de moldes ha seguido aumentando y los requisitos de calidad y vida útil de los moldes se han vuelto cada vez más altos.
Por lo tanto, es necesario elegir razonablemente el material del molde, desarrollar el proceso de tratamiento térmico correcto, seleccionar el método de tratamiento de superficie adecuado e investigar y desarrollar nuevos materiales para el molde.
En este artículo, utilizamos la producción real del material de moldes de fundición a presión de nuestra empresa como ejemplo para analizar y discutir los métodos de proceso para extender la vida útil de los moldes.
Fabricación de moldes para fundición a presión.
Requerimientos técnicos
Los requisitos técnicos para la fabricación de moldes de fundición a presión son los siguientes:
- Materiales: H68M
- Dimensiones: 400 mm × 910 mm × (3000 ~ 5000 mm)
Proceso de producción: Lingote de electroescoria → Corte → Calentamiento → Forja → Tratamiento térmico → Mecanizado → Inspección → Envío.
⑴ Requisito de dureza de la superficie: ≤229HBW, diferencia de dureza única: ≤40HBW.
⑵ Relación de forjado: ≥5.
⑶ Requisitos de la prueba de rendimiento: Energía de impacto con muesca: no menos de 25 J, energía de impacto sin muesca: no menos de 350 J.
⑷ Prueba no destructiva UT equivalente a defecto individual: ≤1,0 mm. No se permiten defectos densos.
⑸ Tamaño del grano: más fino que el nivel 6.
⑹ Requisitos de inclusión: consulte la Tabla 1.
Tabla 1: Requisitos de inclusión para materiales de moldes
Clase A | Clase B | Clase C | Clase D | Clase D (Nivel) |
||||
Grueso | Multar | Grueso | Multar | Grueso | Multar | Grueso | Multar | |
≤0,5 | ≤0,5 | ≤1,0 | ≤1,0 | ≤0,5 | ≤0,5 | ≤1,0 | ≤1,0 | ≤1,0 |
⑺ Las materias primas se producen en horno de arco eléctrico + refinación + desgasificación al vacío + refundición de electroescoria. La composición química se muestra en la Tabla 2, con (H) ≤2.0PPm, (O) ≤25PPm y (N) = 70~170PPm.
Tabla 2: Composición química de los materiales del molde (fracción de masa,%)
Elemento | W. | Sí | Minnesota | PAG | s | cr | Mes | V |
Mínimo | 0,36 | 0,25 | 0,25 | – | – | 4.95 | 2.2 | 0,50 |
Máx. | 0,42 | 0,45 | 0,45 | 0,015 | 0.005 | 5.25 | 2.8 | 0,80 |
Proceso de producción:
⑴ Utilice un lingote de electroescoria de 12,5 t para quitar el bebedero y las rebabas de la placa del lingote y luego cárguelo en el horno de calentamiento de gas. La temperatura de calentamiento se controla a 1260°C. Después de 24 horas de aislamiento, el forjado comienza utilizando el proceso de dos rebotes y dos tirones con una relación de forjado superior a 6, como se muestra en la Figura 1.
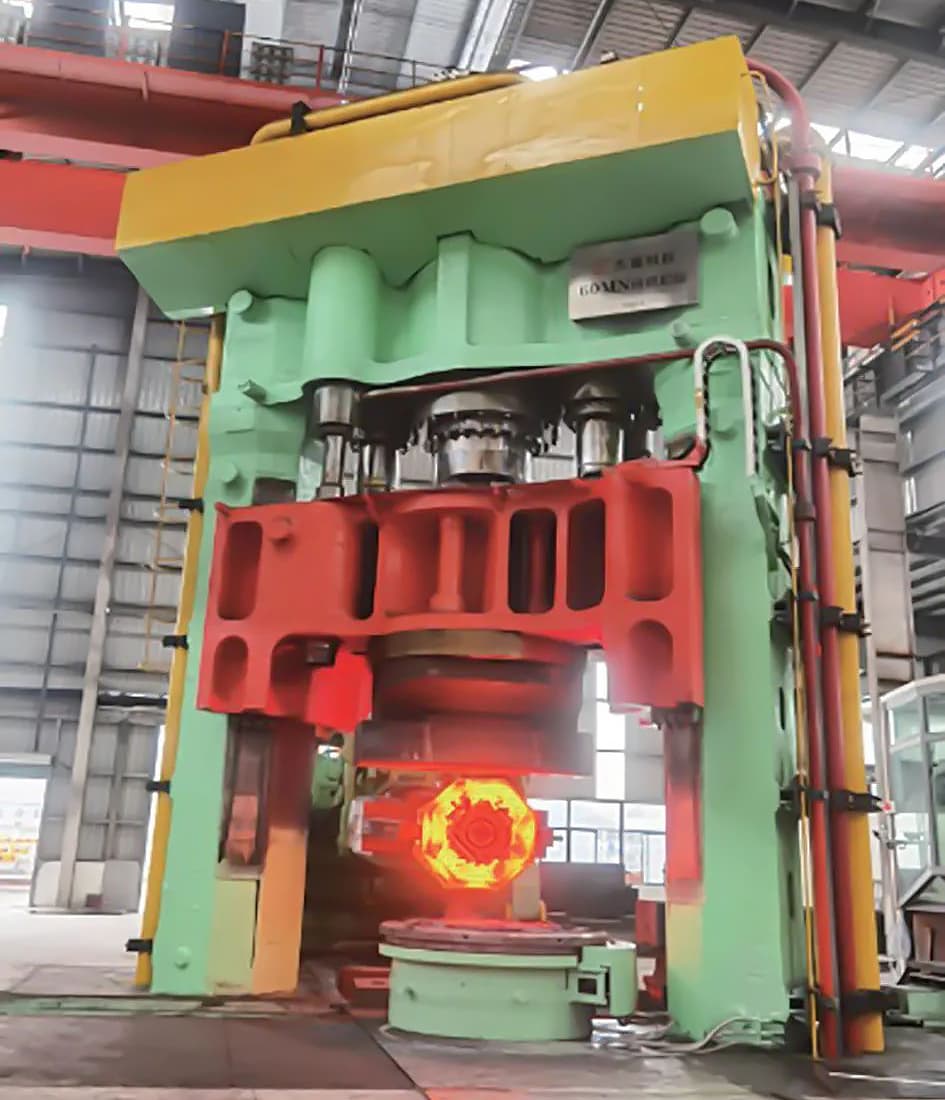
⑵ Después de la forja, adopte el control de enfriamiento por aire y colóquelo oportunamente en el horno de recocido para el tratamiento térmico posterior a la forja a aproximadamente 400 °C. La temperatura de calentamiento para el tratamiento térmico es de 850°C durante 20 horas de aislamiento y luego de 730°C durante 30 horas de aislamiento. El horno de calentamiento se enfría a menos de 30°C/h y el molde se retira del horno cuando la temperatura del horno es inferior a 450°C.
⑶ Después del tratamiento térmico, realice el procesamiento mecánico de acuerdo con los requisitos del dibujo. Una vez completado el procesamiento, ejecute la prueba UT. Se enviarán los productos calificados.
Los principales factores que afectan la vida útil de los moldes de fundición a presión son:
⑴ La pureza del interior del material.
⑵ Selección razonable del proceso de fabricación de materiales.
⑶ La racionalidad del diseño del molde de fundición y las condiciones de trabajo.
Mejora del proceso para el nuevo material de molde de fundición a presión H68M
⑴ Según el proceso de producción anterior, la vida útil del material del molde H68M no ha mejorado significativamente en comparación con otros materiales nacionales.
Nuestro personal técnico siguió y analizó el proceso de fundición, control del proceso de forja y control del tratamiento térmico en sitio para obtener información sobre pureza, estructura y tamaño de grano, como se muestra en las Figuras 2, 3 y 4. Esto proporcionó experiencia para mejorar aún más el material. control de la vida útil en el futuro.
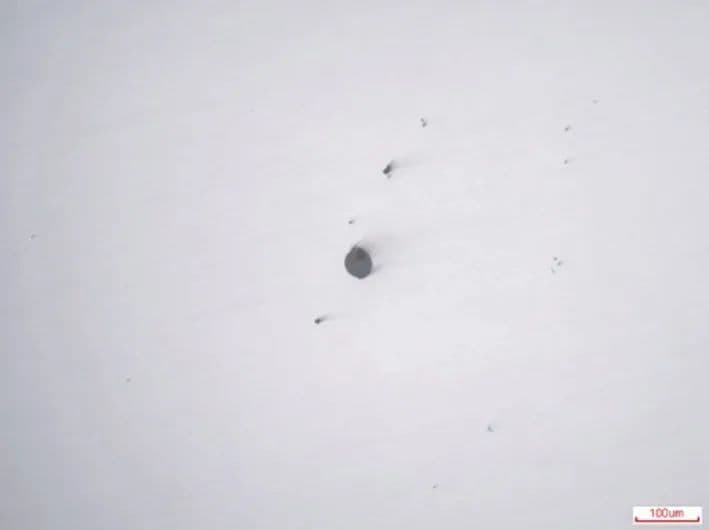
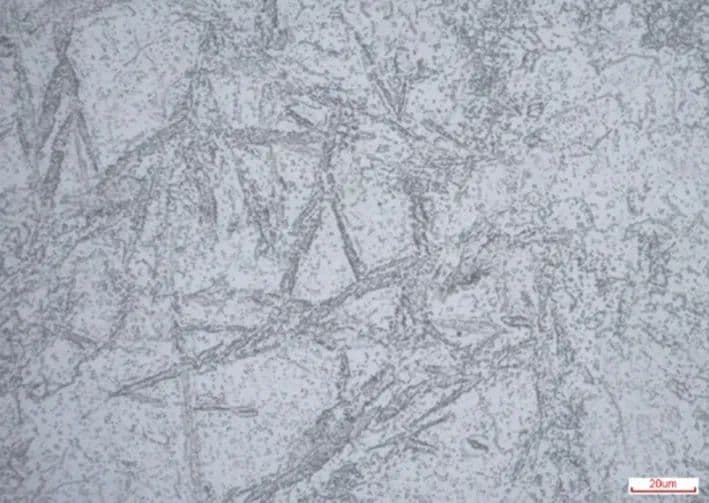

En relación con los extensos datos experimentales anteriores, nuestro equipo de investigación técnica ha analizado e implementado las siguientes mejoras en los procesos de fundición, forjado y tratamiento térmico posterior al forjado.
Medida de mejora 1
La microestructura ideal de la aleación base se logró mediante un diseño de composición razonable. La composición química mejorada se muestra en la Tabla 3.
Tabla 3 Composición química ajustada (fracción de masa, %) del H68M después de la actualización
Elemento | W. | Sí | Minnesota | PAG | s | cr | Mes | V |
Mínimo | 0,36 | 0,20 | 0:30 | – | – | 4.95 | 2.350 | 0,55 |
Máx. | 0,40 | 0,40 | 0,45 | 0,015 | 0.005 | 5.15 | 2,65 | 0,75 |
Medida de mejora 2
Se utilizaron chatarra limpia de acero y aleaciones como materia prima, y se emplearon medidas efectivas como el refinado LF, la desgasificación al vacío y la escoriación eléctrica bajo atmósfera protectora para reducir el contenido de impurezas, gases nocivos e inclusiones en el acero.
Esto dio como resultado la obtención de palanquillas puramente forjadas. En el proceso de fundición, se ha controlado el riesgo de falla del material causado por esto, y la pureza del material se puede controlar al nivel que se muestra en la Tabla 4. La imagen de inclusiones a gran aumento se muestra en la Figura 5.
Tabla 4 Datos de detección de gran aumento ajustados después de la mejora
Nota | Clase A | Clase B | Clase C | Clase D | Clase D (Nivel) | ||||
H68M | Grueso | Multar | Grueso | Multar | Grueso | Multar | Grueso | Multar | |
≤0,5 | ≤0,5 | ≤1,0 | ≤1,0 | ≤0,5 | ≤0,5 | ≤1,0 | ≤1,0 | ≤1,0 |
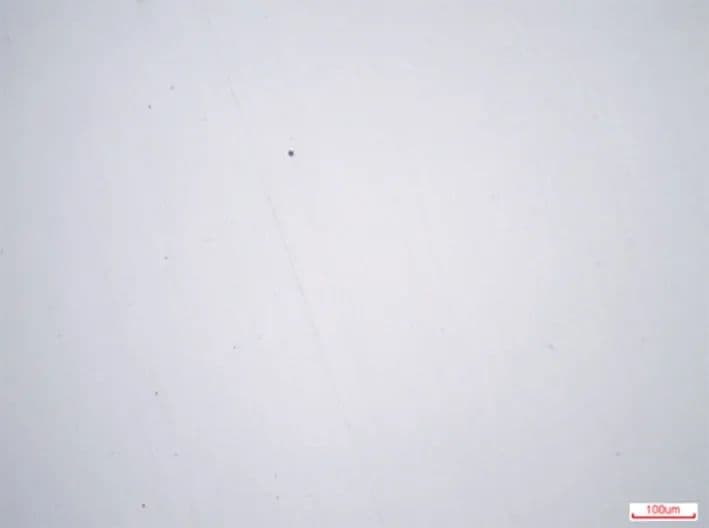
Medida de mejora 3
Durante el calentamiento, se empleó difusión a alta temperatura de 1280 ℃. El proceso de forjado utilizó un control de proceso de tres estirados y tres tamaños y un proceso de rectificado cruzado con una cantidad de deformación final controlada para que fuera superior al 30%.
Se utilizó la combinación de forjado por compresión multidireccional y proceso EFS (Ultrafine Refining) para obtener granos refinados y una microestructura recocida uniforme.
Esto permitió una buena microestructura de tratamiento térmico incluso después del mecanizado y acondicionamiento, lo que proporcionó una buena base para el uso del molde. La imagen de la microestructura ajustada se muestra en la Figura 6 y la imagen del tamaño de grano se muestra en la Figura 7.

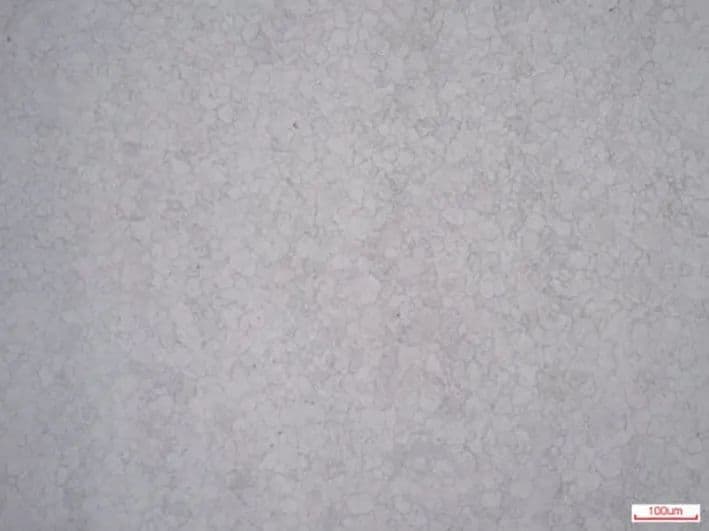
Al implementar las medidas anteriores, nuestro material H68M producido cumple con los estándares de la Asociación Norteamericana de Fundición a Presión.
Se debe probar el material del molde de fundición para determinar el valor de impacto con muesca en V para inspeccionar la tenacidad del material.
Al mismo tiempo, se debe comprobar la ductilidad del material comprobando su energía de impacto sin entallar. El H68M cumple con los requisitos de la prueba Dievar y obtiene el valor de impacto en condiciones de funcionamiento endurecidas a 44-46 HRC como se muestra en la Tabla 5.
Tabla 5 Valor de impacto del material H68M endurecido a 44-46 HRC en condiciones de funcionamiento
Nota | En forma de V (J) | Sin espacio (J) | ||
valor medio | valor mínimo | valor medio | valor mínimo | |
1.2367 | ≥19 | ≥14,9 | ≥300 | ≥269 |
H68M | ≥25 | ≥18 | ≥350 | ≥300 |
A través del diseño optimizado de la composición de la aleación del material y el estricto control de los procesos de dosificación, fundición, escoria eléctrica, forjado y tratamiento térmico postforjado durante la producción, el material H68M exhibe un excelente rendimiento en alta templabilidad, alta dureza al rojo, alta tenacidad y alta ductilidad.
Conclusión
(1) Al ajustar el diseño de la composición química del material H68M, se ha convertido en un tipo de acero para moldes para trabajo en caliente con alta templabilidad, alta dureza al rojo, alta tenacidad y alta ductilidad.
(2) El material H68M se ha sometido a escoria eléctrica, homogeneización a alta temperatura, tratamiento de refinamiento de grano y tres veces a un fuerte proceso de trefilado y dimensionamiento para superar las expectativas del cliente. La vida útil de los 10.000 moldes requeridos por los pedidos contractuales de los clientes ahora se puede aumentar a más de 20.000, lo que reduce significativamente el costo de uso de moldes y crea valor para los clientes.