Una vez identificadas las herramientas necesarias, los operadores deben definir la secuencia de plegado correcta para obtener su producto.
Esto es fundamental, ya que un error en la secuencia de plegado puede impedir obtener el perfil deseado, ralentizar el proceso de plegado o provocar problemas dimensionales en el producto si las contramedidas están mal colocadas.
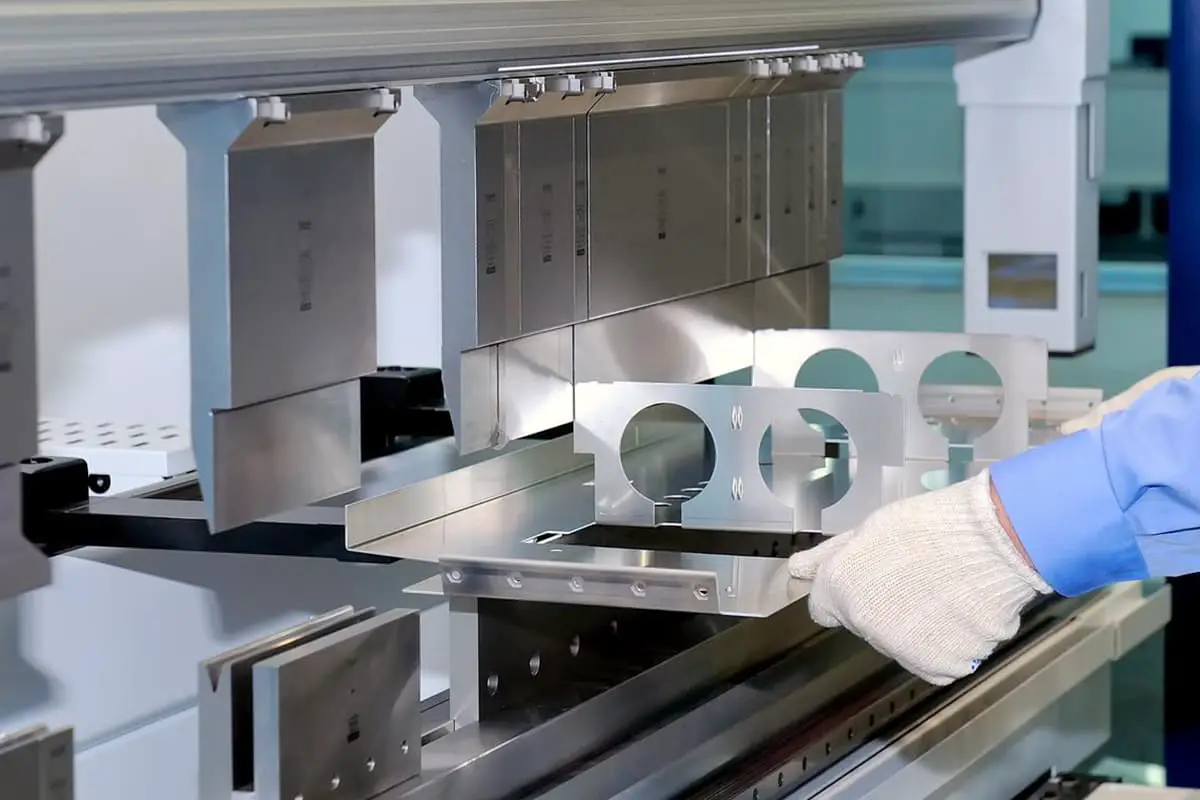
No es posible definir en un solo artículo todos los parámetros a considerar para obtener la secuencia de plegado correcta, ya que la experiencia del operador juega un papel importante a la hora de encontrar las herramientas adecuadas para el perfil en cuestión.
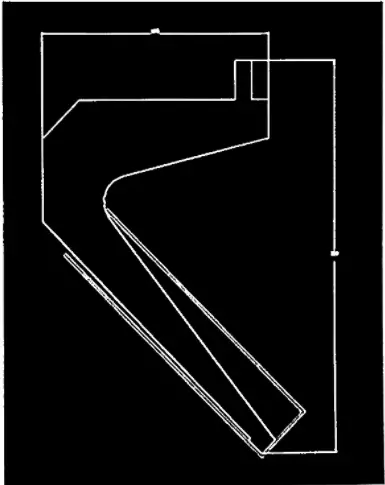
Sin embargo, podemos ofrecerle algunos consejos útiles. Profundicemos en ello.
1. Especialmente para principiantes, es recomendable trazar la secuencia de plegado, modificando el perfil de la chapa en cada paso.
2. Para evaluar la posibilidad de colisión entre el perfil y las herramientas, comience eligiendo el último codo y vaya hacia atrás.
El último pliegue suele cerrar un perfil y dificulta la ejecución de las demás fases; Por este motivo, lo mejor es comenzar siempre la secuencia con los pliegues más pequeños más cercanos a los bordes de la chapa.
3. Para una secuencia rápida y eficiente, elija la secuencia que requiera girar o girar la placa lo menos posible.
Cada una de estas acciones implica movimientos desperdiciados por parte del operador.

5. Antes de realizar el plegado, simulelo gráficamente utilizando el dibujo del catálogo (normalmente hay una escala graduada en la parte inferior detrás de la herramienta) o un recorte de la herramienta.
Si el operador tiene acceso a CAD o software de simulación, puede utilizarlo para evaluar la viabilidad del perfil, o la posibilidad de colisiones entre la chapa y las herramientas o la plegadora.
6. Identificar una secuencia de doblado que permita al operador sostener adecuadamente la lámina durante el doblado y sin poner en riesgo la seguridad.
7. Si un perfil tiene ángulos obtusos o lados no rectos, determine la secuencia de plegado para que la hoja siempre quede correctamente colocada contra los topes traseros.
Esto es muy importante para obtener un producto preciso con las dimensiones correctas.
De hecho, en ocasiones el posicionamiento hace imposible estar seguros de que la longitud de la curva al final del ciclo sea correcta y conforme a la medida introducida en el control numérico.
Por esta razón, la secuencia debe configurarse de manera que la placa siempre toque los calibres traseros en superficies planas y rectas.
Para reducir los tiempos de producción, recomendamos que los diseñadores eviten diseñar perfiles con superficies de apoyo que no sean planas o tengan ángulos obtusos.
También les recomendamos consultar:
- el tipo de topes traseros disponibles
- el número de los metros traseros
- la altura máxima alcanzable
- la distancia mínima entre dos tope trasero, ya que presionar la chapa contra un solo tope trasero no puede garantizar un doblado preciso.
Cuando se esté doblando chapa delgada, se recomienda apoyarla en los topes traseros y sostenerla durante todo el proceso de doblado para evitar que se arquee y, por ende, modifique la dimensión X; Por este motivo, los topes traseros tienen múltiples superficies de apoyo.

Si un operador no puede colocar correctamente la lámina de metal contra los topes traseros, dibuje la línea de doblez en la lámina de metal con un marcador y verifique visualmente que todas las dimensiones sean correctas.
En este caso, es importante asegurarse de que las líneas sean el punto medio de la curva.
Los operadores de plegadoras necesitan dibujos claramente comprensibles con todas las dimensiones necesarias.
Si el operador es principiante, los diseñadores deberían proporcionarle una vista tridimensional para ayudarle; Además, las dimensiones dibujadas deben ser alcanzables, por lo que es mejor no utilizar demasiadas cifras decimales ni tolerancias excesivamente ajustadas.
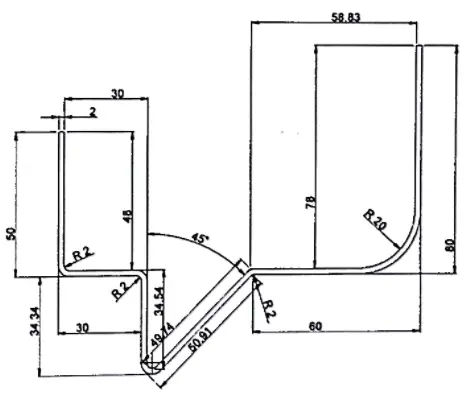
8. Otro factor fundamental a la hora de preparar la secuencia de plegado es la tolerancia de las dimensiones del perfil.
Recuerde que durante el proceso de doblado el control numérico mide las distancias entre los topes traseros y la línea de doblado, que es el punto de contacto del punzón.
Por este motivo, las dimensiones de algunos lados dependen de pliegues anteriores.
Por ejemplo, si plegáramos el dibujo hacia la derecha, tomando las medidas A y C de los bordes de la hoja, nos aseguraríamos de que estas dimensiones fueran las correctas, mientras que el tramo medio de 120 mm, es decir, la porción restante , sólo sería correcto si el procesamiento de la hoja fuera perfecto.
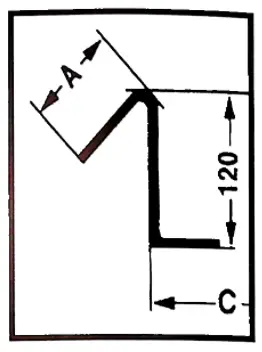
Por lo tanto, se recomienda que el ciclo de doblado se organice de tal manera que las mediciones con tolerancias estrechas siempre se realicen directamente desde el punto de contacto con los calibres traseros y nunca sean simplemente el resultado de otros dobleces.
De esta manera, los posibles defectos pueden limitarse a lados no críticos. Los diseñadores deben indicar a los operadores de plegadoras qué medidas son realmente críticas y qué tolerancias mayores están permitidas, reduciendo significativamente los problemas de montaje.
Para obtener más información sobre tolerancias dimensionales, lea DIN 6935.
9. La configuración del tope trasero evita defectos dimensionales, por lo que los operadores de la plegadora deben verificar periódicamente el ajuste del eje X.
Además de comprobar la pieza, los operadores deben utilizar un calibrador para comprobar la distancia entre el tope trasero y el borde de la matriz, cuyo ancho de vástago se conoce.