Cronograma
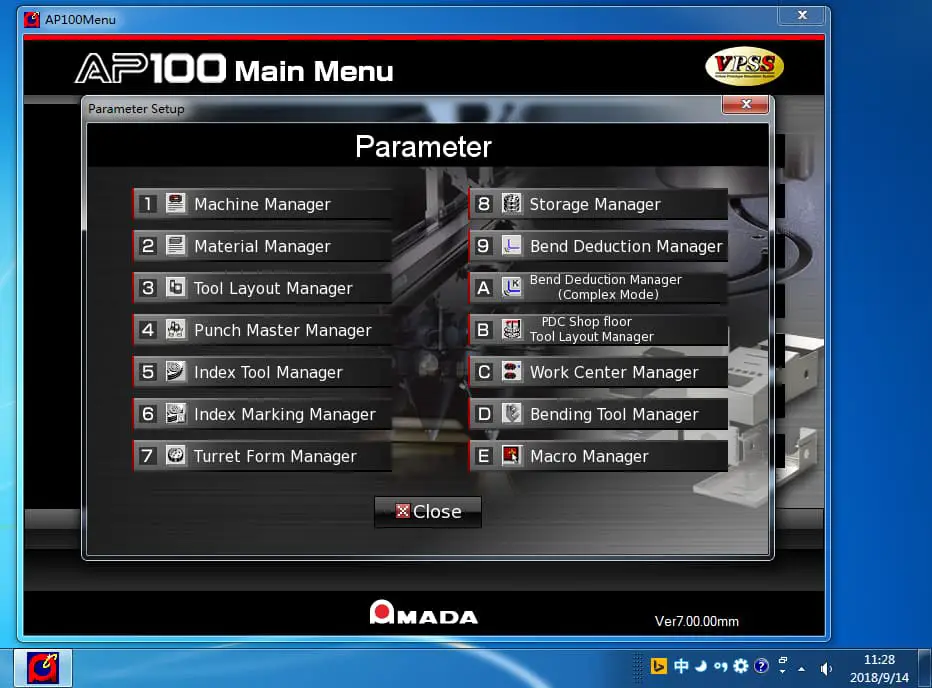
1. Familiarización con formatos matriciales comunes y especializados:
Conocer las matrices disponibles hace que la programación sea más conveniente y eficiente.
2. Aplicación racional de los vacíos de la matriz:
Anteriormente, las holguras estándar eran 0,1 veces el espesor de la placa para aluminio y cobre, 0,15 veces para hierro y 0,2 veces para acero inoxidable. Ahora, AMADA propone un nuevo estándar de espacio libre para troqueles para punzonadoras hidráulicas (las tres prensas de nuestra fábrica son hidráulicas).
La separación del troquel se puede aumentar adecuadamente en 0,05 veces el espesor de la placa según el estándar original.
Esto se debe a que las punzonadoras hidráulicas tienen una velocidad de corte instantánea más lenta y aumentar la separación del troquel no afectará la apariencia de la sección cortada, al mismo tiempo que evitará que el material rebote durante el proceso de corte.
3. Cantidad de troquelado:
Durante el proceso de diseño de corte, es esencial calcular la cantidad de corte de cada golpe del troquel. Generalmente, la longitud del material cortado por el troquel no debe ser inferior a 2/3 de la longitud del troquel; de lo contrario pueden quedar sobras.
Las formas rectangulares son propensas a tener escombros, particularmente en los cuatro ángulos rectos, mientras que las formas circulares son las que tienen menos probabilidades de tener escombros. Por lo tanto, es fundamental prestar atención a la secuencia de punzonado durante el proceso de diseño de corte.

En el ejemplo anterior, la Figura 1 muestra que perforar primero la forma circular y luego la forma cuadrada puede causar fácilmente grietas en las cuatro esquinas de la forma cuadrada. Si se cambia la secuencia de punzonado a la de la Figura 2, el desgaste del troquel será mucho menor.
Durante el proceso de diseño de corte, es fundamental utilizar el borde más largo de la matriz para cortar los bordes, como se muestra en el siguiente ejemplo:
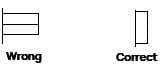
4. Cálculo de longitud en programación:
(1) En corte de línea verdadero:
Al cortar filos de forma continua, el propio programa interno de la máquina calculará este filo dividiendo la longitud total del filo cortado menos la longitud del primer corte, en lugar de la longitud total dividida por la longitud de la hoja como podríamos imaginar.
Es esencial tener en cuenta que cuando la punzonadora corta bordes continuamente, no conecta con precisión cada corte con el siguiente. En cambio, la punzonadora establece automáticamente una superposición de 0,2 mm entre los dos cortes. Debemos prestar atención a esto al calcular.
Por ejemplo, al cortar un filo de 240 mm con una hoja rectangular RE80x5, podríamos pensar que se necesitan exactamente tres cortes.
Sin embargo, si se utiliza un corte de línea real, en realidad se realizarán cuatro cortes, lo que afecta significativamente el desgaste del troquel y la vida útil.
Hay dos soluciones para esto: primero, podemos utilizar un enfoque de una sola hoja, cortando una a la vez; En segundo lugar, según la situación real, podemos dejar un nudo de 0,4 mm en el primer corte.
(2) Mordisquear:
No todos los troqueles redondos o cuadrados se pueden utilizar para mordisquear. En nuestra fábrica, utilizamos troqueles redondos φ10, φ11, φ12 y troqueles cuadrados RE6x3 para mordisquear. Es mejor no utilizar otros troqueles para mordisquear, especialmente los más pequeños. El corte sólo es adecuado para láminas delgadas, ya que provoca un rápido desgaste de los troqueles cuando se utiliza en láminas gruesas.
Cuando utilice un troquel redondo para cortar un círculo, primero perfore el centro con un troquel redondo más grande y luego proceda con el corte. No dejes ningún nudo. Al mordisquear con un dado cuadrado, es mejor dejar tres nudos más pequeños y espaciados uniformemente a lo largo de la circunferencia.
5. Salir de nudos
Durante el proceso de programación, los nodos no deben hacerse ni demasiado grandes ni demasiado pequeños; Además, no se les debe dejar demasiado ni demasiado poco. Si los nudos son demasiado grandes, el producto será difícil de quitar o se deformará después de quitarlo. Si los nudos son demasiado pequeños, el producto puede caerse.
¿Cuál es la talla más adecuada para nosotras?
No existe un estándar establecido; Depende de la situación real. El tamaño de nudo ideal es aquel en el que el producto no cae durante el proceso de punzonado y se desprende del material debido a su peso cuando el operador tira la lámina de la mesa de trabajo.
Aquí hay algunos puntos de referencia para su consideración:
Rieles | <1.0 | 1.0-1.6 | 1,6-2,5 | 2,5-3,0 | ||||
---|---|---|---|---|---|---|---|---|
nodos de esquina | Nodos intermedios | nodos de esquina | Nodos intermedios | nodos de esquina | Nodos intermedios | nodos de esquina | Nodos intermedios | |
Aluminio, Cobre | 0,35 | 0,4 | 0,4 | 0,5 | 0,5 | 0,5 | 0,5 | 0,6 |
Hierro | 0.3 | 0,4 | 0,4 | 0,4 | 0,4 | 0,5 | 0,4 | 0,5 |
Acero inoxidable | 0.3 | 0,35 | 0.3 | 0,35 | 0,4 | 0,4 | 0,4 | 0,4 |
Los valores anteriores son algunos valores de referencia para dejar nudos en espesores de placa comunes, pero los valores reales dependen de la situación específica. En cuanto a cuantos nudos son adecuados, generalmente debemos dejar un nudo entre cada 350-400mm. Por ejemplo, si tenemos un esquema rectangular desplegado de 50x1200mm, podemos dividirlo en tres secciones y dejar dos nodos en el medio. Intente dejar nudos simétricamente en el producto para mantener equilibrada la tensión.
Nota: Durante el proceso de composición, los nodos deben agregarse adecuadamente en ciertos puntos.
Composición
Coloque diferentes productos del mismo material y espesor de tablero en una sola hoja para un procesamiento único y así lograr ahorros de material, tiempo y esfuerzo.
- Familiarícese con las especificaciones del material:
- Placa de aluminio: t(espesor) * 1220*2440
- Placa de cobre: t(espesor) * 600*1500
- Placa fría (SPC): t(espesor) * 1250*2500 (t(espesor) * 1220*2440)
- Tablero decapado (SPHC/SPHD): t(espesor) * 1250*2500 (t(espesor) * 1220*2440)
- Placa electrolítica: t(espesor) * 1220*2440
- Placa de acero inoxidable: t (espesor) * 1220 * 2440
Estas son algunas especificaciones comunes de materiales laminados. Se pueden solicitar especificaciones personalizadas según los requisitos de tamaño del producto desplegado.
- Zona de seguridad: preste atención a la zona de seguridad mientras compone. Generalmente, el filo de la estación D se establece en 15 80 y el filo de la estación E se establece en 20 110. No incluya el troquel dentro de la zona de seguridad para evitar dañar el troquel y la abrazadera.
- Distancia entre diseños: Durante la composición, la distancia mínima entre productos no debe ser menor que el ancho de la matriz. Por ejemplo, si utiliza RE45*5 para cortar, la distancia mínima no debe ser inferior a 5 mm.
- Composición de bordes compartidos: El AP100 tiene un comando automático de bordes compartidos, pero también se puede realizar manualmente. Al componer con bordes compartidos, asegúrese de aumentar el tamaño de los nodos o dejar más.
- Selección de matrices en composición tipográfica: Utilice la menor cantidad de matrices posible en composición tipográfica. En la secuencia de punzonado, el último troquel de corte debe perforarse desde el lado opuesto de la abrazadera hacia la abrazadera.
- Punzonado de matriz de formación especial: para matrices de formación como bridas, semi-estirado, persianas y prensado de puentes, preste especial atención a la secuencia de punzonado. Si forma hacia abajo, deje nudos más grandes y coloque el troquel de formación al final de la secuencia, perforando desde la abrazadera hacia el otro lado a lo largo de la dirección X y hacia afuera. Si forma hacia arriba, asegúrese de que los troqueles posteriores no presionen en la posición de formación para que no sea necesario colocarlos al final de la secuencia.
Problemas comunes en la composición de programación
Hay varios problemas comunes en la programación tipográfica:
- Grabación:
a) Material en sí: en materiales blandos y livianos, como placas de aluminio, el estampado puede ocurrir fácilmente durante el proceso de punzonado. Debido al peso liviano de la placa de aluminio, los desechos de corte en sí son muy livianos a la misma velocidad de punzonado, y cuando los desechos aún no han caído por completo, el troquel superior los levanta y se produce el estampado cuando los desechos se presionan en el placa durante el siguiente corte.
b) Velocidad de punzonado: Durante el proceso de corte, si la velocidad es demasiado rápida y los desechos aún no han caído por completo, el troquel superior levanta los desechos y se produce el relieve cuando los desechos se presionan contra la placa durante el siguiente corte.
c) Cantidad de corte insuficiente: Durante el proceso de punzonado, si la cantidad de corte es inferior a 2/3, el troquel puede levantar los residuos.
- Material de arrastre:
a) Profundidad insuficiente del troquel superior: Si el material no está completamente perforado, es probable que el troquel superior arrastre el material al levantarlo.
b) Espacio excesivo del troquel: si el espacio del troquel inferior es demasiado pequeño, es fácil pellizcar el material y es probable que la placa arrastre el material durante el movimiento.
c) Borde de corte del troquel no afilado: Si el material no está completamente perforado, es probable que el troquel superior arrastre el material al levantarlo.
d) Velocidad de punzonado de la prensa: si la velocidad es demasiado rápida y el material no se corta o cae por completo, puede provocar que el material sea arrastrado.
e) Fuerza de expulsión insuficiente: La presión del resorte no es suficiente.
f) Puñetazo desalineado, distribución desigual de fuerzas.
- Muere residual:
a) Cantidad de corte insuficiente: Cuando es inferior a 2/3 de la longitud del troquel, puede producirse troquel residual.
b) Durante la erosión, si el paso es demasiado pequeño, es probable que se produzca una muerte residual grave. Ajuste el tono en consecuencia según los requisitos reales.
- Caída del producto:
a) Los nodos son demasiado pequeños, pocos o no están razonablemente ubicados.
- Desplazamiento de medio dibujo y rayones:
Cuando la placa se mueve, la mitad del diseño se raya en el disco de la cuchilla. Cuando la mitad del diseño se mueve sobre el disco de la cuchilla, se atasca en el troquel inferior. Cuando la placa se mueve, la mitad del diseño es arrastrada con fuerza, lo que provoca el desplazamiento del material y el desplazamiento de las otras mitades del diseño.
Para evitar estos problemas, considere los factores que los causan y tenga en cuenta la programación y las operaciones en el sitio para resolver los problemas de manera más rápida y precisa.