Cortar placas de acero de menos de 10 mm no es un problema con una cortadora láser. Sin embargo, para placas más gruesas, a menudo se requiere un láser de alta potencia con una potencia superior a 5 kW. Esto da como resultado una disminución significativa en la calidad del corte.
El alto costo de los equipos láser de alta potencia hace que el modo de salida del corte por láser sea menos favorable. Como resultado, los métodos tradicionales de corte por láser no tienen ninguna ventaja a la hora de cortar láminas gruesas.
Los desafíos técnicos al cortar láminas gruesas con una máquina de corte por láser para metales son:
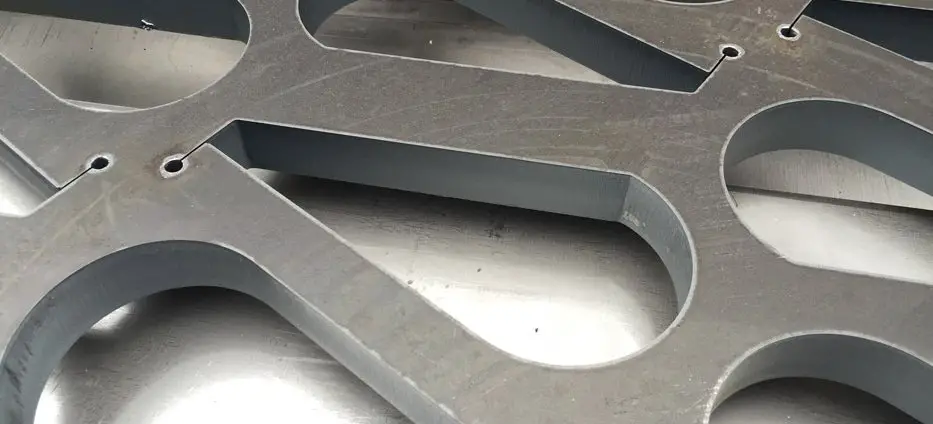
El proceso de combustión en estado casi estacionario es difícil de mantener.
La cortadora láser de metal tiene limitaciones en cuanto al grosor de las placas que se pueden cortar durante el proceso de corte real. Esto está relacionado con la inestabilidad de la combustión de la hoja de hierro.
La temperatura en la parte superior de la grieta debe alcanzar el punto de ignición para mantener el proceso de combustión continuo. La energía liberada por la reacción de combustión del óxido de hierro por sí sola no garantiza la continuación del proceso de combustión.
Por un lado, la temperatura del filo disminuye debido al enfriamiento constante del flujo de oxígeno de la boquilla de corte. Por otro lado, la capa de óxido de hierro que se forma tras la combustión cubre la superficie de la pieza, bloqueando la difusión de oxígeno. Cuando la concentración de oxígeno disminuye a un cierto nivel, el proceso de combustión se extinguirá.
En el corte por láser de haz convergente tradicional, el rayo láser se enfoca en un área pequeña de la superficie. La alta densidad de potencia del láser hace que la temperatura de la superficie de la pieza alcance el punto de ignición no sólo en el área de radiación del láser, sino también en un área más amplia debido a la conducción de calor.
El diámetro del flujo de oxígeno en la superficie de la pieza es mayor que el diámetro del rayo láser, lo que provoca una fuerte reacción de combustión no sólo en el área de radiación del láser sino también fuera de ella.
Al cortar placas gruesas, la velocidad de corte es lenta. La superficie de la pieza de trabajo se quema más rápido que la velocidad de movimiento del cabezal de corte. Después de un tiempo de combustión, el proceso de combustión finaliza debido a la disminución de la concentración de oxígeno. Cuando el cabezal de corte se mueve a esta posición, la reacción de combustión comienza de nuevo.
El proceso de quemado del filo se produce periódicamente, lo que provoca fluctuaciones de temperatura y una mala calidad del corte.
La pureza y la presión del oxígeno en la dirección del espesor de la placa son difíciles de mantener constantemente.
La disminución de la pureza del oxígeno también juega un papel crucial a la hora de determinar la calidad del corte de láminas gruesas con una cortadora láser. La pureza del flujo de oxígeno tiene un impacto significativo en el proceso de corte.
Una disminución de la pureza del flujo de oxígeno en un 0,9% conduce a una disminución del 10% en la tasa de combustión hierro-oxígeno. Una disminución de la pureza del 5% da como resultado una disminución del 37% en la tasa de combustión. Esta disminución en la tasa de combustión reduce en gran medida la entrada de energía en la costura cortada y disminuye la velocidad de corte.
Además, el contenido de hierro en la capa líquida de la superficie de corte aumenta, provocando que aumente la viscosidad de la escoria y dificultando la descarga de la escoria. Esto da como resultado una acumulación significativa de escoria en el fondo de la incisión, lo que hace que la calidad de la incisión sea inaceptable.
Para mantener la estabilidad del corte, se debe mantener constante la pureza del flujo de oxígeno de corte en la dirección del espesor de la placa y la presión.
En el corte por láser tradicional se utiliza una boquilla cónica convencional, adecuada para cortar láminas finas. Sin embargo, al cortar chapa gruesa, se forma una onda de choque en el campo de flujo de la boquilla a medida que aumenta la presión de alimentación. La onda de choque plantea varios riesgos para el proceso de corte, como reducir la pureza del flujo de oxígeno y afectar la calidad de la incisión.
Hay tres soluciones a este problema:
(1) Agregue una llama de precalentamiento alrededor del flujo de oxígeno de corte.
(2) Agregue un flujo de oxígeno auxiliar alrededor del flujo de oxígeno de corte.
(3) Diseño razonable de las paredes internas de la boquilla para mejorar el campo del flujo de aire.