El método tradicional de producción de láminas de acero al silicio, utilizadas en motores y electrodomésticos, consiste en instalar moldes en prensas mecánicas.
La matriz de estampado en frío de lámina de acero al silicio se compone principalmente de matrices macho y hembra, que se instalan en la prensa para perforar la lámina de acero al silicio en el estator y el rotor del motor o en el chip de hierro del transformador.
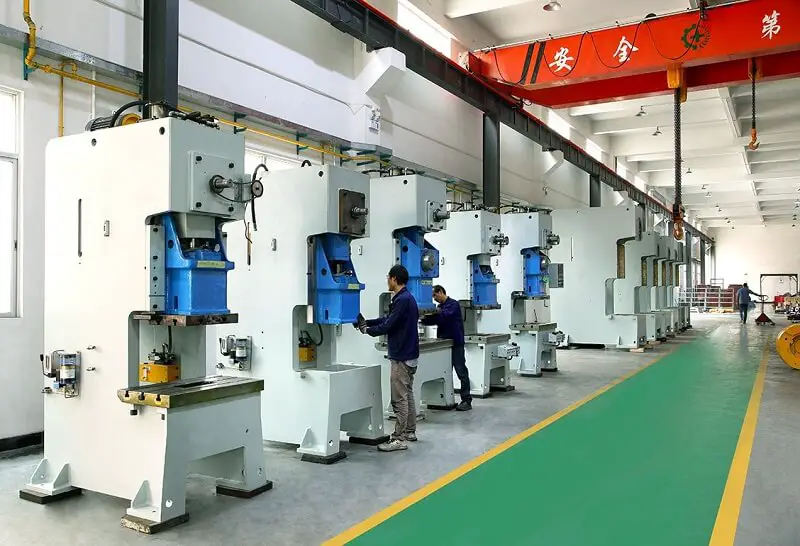
Durante el funcionamiento de una matriz de chapa de acero al silicio, el borde está sujeto a fuerzas de impacto, cizallamiento y flexión. Además, el borde también es comprimido y frotado por la chapa de acero al silicio. Un recubrimiento especial en la superficie de la lámina de acero al silicio aumenta la fricción y el desgaste de los bordes, que es la razón principal del fallo normal de la matriz.
Como resultado, el desgaste del troquel es severo y a menudo es necesario afilarlo antes de que alcance su vida útil óptima. El número de piezas perforadas en un juego de matrices suele ser menor que su valor teórico.
Por ejemplo, consideremos el proceso de moldear una lámina de acero al silicio para un motor en particular. Se requieren siete tipos de matrices para completar, con un costo total de 190.000 yuanes. La dureza de una matriz de estampado para una lámina de rotor es de 60 a 62 Hrc y se instala en una máquina herramienta de estampado de 60 t. Normalmente, la matriz puede perforar más de 200.000 piezas.
Sin embargo, el borde del orificio de la matriz colapsa después de usarse menos de 9.000 veces. Moler el troquel (generalmente después de 50.000 a 60.000 veces) y volver a aplicarlo a la máquina no resuelve el problema. En cambio, el colapso persiste y aparecen grietas en el borde exterior de la matriz.
Durante el estampado continuo, las grietas se expanden rápidamente y la matriz falla, quedando inutilizable después de menos de 20.000 usos. Cada vez que se producen dos motores, es necesario afilar tres tipos de moldes, lo que cuesta entre 400 y 800 yuanes cada vez, lo que hace que el coste de fabricación del producto sea relativamente alto.
Especialmente durante la producción de prueba de nuevos productos, los costos de fabricación de moldes son considerablemente altos y el ciclo de producción es largo, lo que duplica el costo del desarrollo de nuevos productos.
Producción y requisitos de láminas de acero al silicio
La chapa de acero al silicio es un componente crucial de motores y aparatos eléctricos. Su desempeño incide directamente en la pérdida de energía eléctrica y en la eficiencia, tamaño y peso de productos como los transformadores.
Por lo tanto, la chapa de acero al silicio generalmente debe cumplir los siguientes requisitos:
- Debe tener un revestimiento superficial liso, excelente forma, alta precisión dimensional y mínima variación de espesor dentro de la misma placa.
- Debe tener propiedades electromagnéticas favorables y una estructura de grano orientada que cumpla con los requisitos de la aplicación.
El proceso de corte de láminas de acero al silicio no sólo debe tener las características típicas de corte de metal, sino que también debe satisfacer los siguientes requisitos especiales.
Altura de la rebaba
La altura de las rebabas en la lámina de acero al silicio utilizada para estampar no debe exceder los 0,05 mm. Se presta cada vez más atención al impacto de las rebabas en el rendimiento de todas las partes mecánicas de la máquina.
Las características electromagnéticas de generadores, motores y transformadores que utilizan láminas de acero al silicio se ven significativamente afectadas por las rebabas.
El troquelado se utiliza para formar láminas de acero al silicio utilizadas en generadores, motores y transformadores. A menudo, la brecha en la fabricación de matrices es demasiado grande o se amplía debido al desgaste.
Durante el proceso de corte, la lámina de acero al silicio se extruye, provocando una ligera deformación plástica. Esta deformación permanece en el borde de la chapa, dando lugar a la formación de rebabas.
El rotor, el estator y el núcleo del transformador de los generadores utilizan una gran cantidad de láminas de acero al silicio con rebabas.
Las rebabas en la chapa de acero al silicio reducen el factor de apilamiento. Para instalar la misma cantidad de láminas, se debe aumentar el volumen del motor.
Además, la rebaba afecta la potencia del motor. Se ha demostrado que la potencia de salida del generador se puede aumentar entre un 0,1% y un 0,2% utilizando láminas de acero al silicio desbarbadas en comparación con generadores que no utilizan láminas de acero al silicio desbarbadas.
Impacto en la vida del generador
La presencia de rebabas en las láminas de acero al silicio crea importantes espacios entre las laminaciones, lo que puede provocar la producción de corrientes parásitas, aumento de la pérdida magnética, temperaturas más altas, ruido e incluso cortocircuitos, lo que provoca fallos en el motor.
Los motores con chapas de acero al silicio desbarbadas tienen una vida útil media superior al 5% en comparación con los motores sin desbarbado.
Las láminas de acero al silicio procesadas se pueden apilar de forma manual o automática y se debe minimizar el espacio entre las juntas. Esto requiere que el equipo mantenga una alta precisión, incluida la precisión de las piezas de repuesto, mientras alcanza la máxima capacidad de producción. Esto garantiza que los productos queden prácticamente libres de rebabas después del corte (la altura de la rebaba después del corte longitudinal de la chapa de acero al silicio no debe exceder los 0,05 mm).
De lo contrario, durante el laminado, las rebabas pueden provocar cortocircuitos entre laminaciones, aumentar la pérdida por corrientes parásitas y reducir el coeficiente de llenado de la laminación.
Las normas pertinentes de China establecen claramente que la altura de las rebabas de las láminas de acero al silicio no debe exceder los 0,05 mm. Sin embargo, muchas fábricas de automóviles no han aplicado medidas eficaces de desbarbado. Todavía instalan y utilizan láminas con rebabas de tan sólo 0,07~0,1 mm, lo que afecta gravemente a la calidad.
Además, durante el desbarbado no se debe rayar visiblemente la película de pintura aislante sobre la superficie de la chapa de acero al silicio.
Efecto del estrés
Después del corte, estampado y apilado, las láminas de acero al silicio sufren tensiones internas que deforman los granos, reducen la permeabilidad y aumentan la pérdida específica de hierro.
Para evitar o minimizar estos efectos, las láminas de acero al silicio orientado laminadas en frío generalmente se tratan con recocido relleno de nitrógeno a una temperatura de aproximadamente 800 °C después del procesamiento de cizallamiento. Este tratamiento elimina el estrés generado durante el procesamiento y asegura que se mantengan las propiedades originales.
Aunque las pruebas han demostrado que la pérdida específica de hierro de la lámina de acero al silicio orientada laminada en frío después del recocido se reduce en aproximadamente un 30%, muchos fabricantes optan por no adoptar este proceso debido al aumento de costos asociado.
Doblado de hoz de chapa de acero
Dados los requisitos de rendimiento especializados de las láminas de acero al silicio, es fundamental mantener altos estándares para su producción.
Estos estándares deben exceder incluso los criterios de flexión lateral de la Sociedad Estadounidense para Pruebas y Materiales (ASTM) para metal cortado en general, que establece un límite de no más de 6 mm/3 M de longitud. Como resultado, el diseño del proceso de corte para láminas de acero al silicio debe cumplir requisitos aún más estrictos.
borde de hoja de loto
La lámina de acero al silicio que se ha cortado debe estar libre de ondas visibles, comúnmente llamadas bordes de hoja de loto.
En el caso de las olas, la relación entre la altura y la longitud de onda no debe exceder el 2,5%.
Si no se cumple esta condición, la lámina de acero al silicio sufrirá una severa deformación plástica, lo que resultará en daños a la estructura del dominio y un aumento significativo de las pérdidas.
Aislamiento
No se permiten daños al aislamiento dentro de la tira de corte o en la superficie de la tira. Además, el borde de la lámina debe estar libre de daños por extrusión, ya que el incumplimiento de estos criterios puede afectar negativamente a la calidad del núcleo de hierro.
Aplicación de la tecnología de corte de agua.
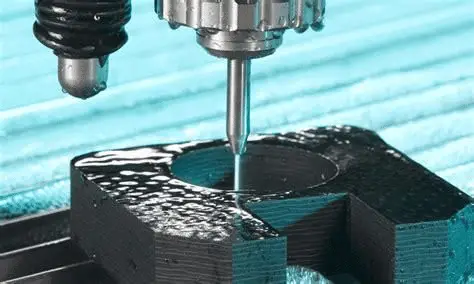
El corte con agua a ultra alta presión, también conocido como cuchilla de agua o chorro de agua, es un proceso que genera un flujo de agua de alta energía presurizando agua ordinaria en varias etapas. Luego, este flujo de agua se dirige a través de una boquilla fina para cortar materiales a una velocidad de casi un kilómetro por segundo.
Esta técnica de corte se conoce como corte con agua a ultra alta presión. Sus orígenes se remontan a Escocia, donde fue descubierto. Durante un período de 100 años, la investigación experimental condujo al desarrollo de un sistema industrial de cierre de agua a alta presión.
El corte con agua a alta presión no está patentado. Sin embargo, en 1968, un profesor de la Universidad de Columbia, en Estados Unidos, introdujo abrasivos en agua a alta presión, lo que aceleró el proceso de corte al triturar los materiales con el abrasivo y el chorro de agua a alta presión.
Hoy en día, Estados Unidos, Alemania, Rusia e Italia han logrado avances en la tecnología de corte con agua a presión ultraalta, con una presión de corte máxima de 550 MPa. Este método se usa ampliamente para cortar materiales como piedra, metal, vidrio, cerámica, productos de cemento, papel, alimentos, plásticos, telas, poliuretano, madera, cuero, caucho, municiones y más.
Hay tres usos principales del corte con agua:
En primer lugar, cortar materiales no combustibles como mármol, baldosas cerámicas, vidrio, productos de cemento y otros materiales que no pueden procesarse mediante corte térmico.
En segundo lugar, cortar materiales combustibles como láminas de acero, plástico, tela, poliuretano, madera, cuero, caucho, etc. En el pasado, el corte térmico también podía procesar estos materiales, pero a menudo provocaba zonas quemadas y rebabas. El corte con agua, por otro lado, no produce tales problemas y las propiedades físicas y mecánicas de los materiales cortados permanecen sin cambios, lo cual es una ventaja significativa del corte con agua.
En tercer lugar, el corte de materiales inflamables y explosivos, como municiones, y el corte en entornos inflamables y explosivos no pueden sustituirse por otros métodos de procesamiento.
En términos de calidad del agua, el corte con agua a presión ultraalta está disponible en dos formas: corte con agua pura y corte con abrasivo.
Prueba de corte de agua
La prueba de corte con agua para láminas de acero al silicio se lleva a cabo utilizando la cuchilla de agua Altorf como equipo principal.
El generador de alto voltaje del equipo (APW38037Z-09A) está equipado con un conjunto completo de sobrealimentadores importados originalmente de AccuStream Inc.
El sistema de control utiliza PLC en lugar de relé para lograr comunicación y control flexibles por computadora.
La plataforma de corte (APW-2030BA) tiene una estructura tipo pórtico, lo que la hace más estable y precisa en comparación con una estructura en voladizo.
El equipo está equipado con una plataforma de PC industrial con un software especial de corte por agua basado en Windows y soportado por un sistema Windows XP original.
La parte lineal del proceso de corte tiene una velocidad de 800 mm/min, mientras que la parte de arco circular tiene una velocidad de 300 mm/min. El espesor de la chapa de acero al silicio utilizada en el ensayo es de 0,5 mm.
Después de la prueba, el producto se retira del tanque de agua en la plataforma de corte, se seca y se verifica su tamaño. El producto presentó un problema fuera de tolerancia sólo en la entrada de la cuchilla durante el corte de agujeros redondos. Este problema se debió principalmente a que la cuchilla entró demasiado rápido durante la programación, lo que provocó que el orificio pareciera elíptico. Durante la nueva prueba, este fenómeno desapareció y la rebaba llegó a tener un tamaño inferior a 0,05 mm. El producto se puede apilar sin aplastarse y el resto del producto cumple con los requisitos del dibujo.
Conclusión
Los resultados de las pruebas del proceso de corte con agua para láminas de acero al silicio indican que se puede lograr una calidad óptima del producto utilizando parámetros apropiados del proceso de corte, monitoreando de cerca la calidad del agua y el tamaño de las partículas de arena, y controlando la velocidad de entrada y la dirección del arco.
El corte con agua ofrece varias ventajas, como alta velocidad, excelente calidad, ahorro de costos y fácil modificación del producto. Además, es especialmente útil durante la producción de prueba de nuevos productos, ya que no se necesitan moldes. Esto reduce significativamente el ciclo de preparación de la producción y minimiza la inversión inicial requerida para nuevos productos. Los resultados de dichas pruebas fueron muy satisfactorios.