1. Introducción al corte con gas.
El oxicorte, también conocido como oxicorte o oxicorte, es un proceso de corte muy eficaz en la fabricación de equipos.
El equipo de oxicorte es simple y fácil de operar, lo que lo hace adecuado para cortar acero al carbono y acero común de baja aleación. Puede cortar con precisión líneas rectas, círculos y diversas formas complejas, con una amplia gama de espesores de corte.
También se automatiza fácilmente, particularmente con la aplicación de tecnología CNC, tecnología de seguimiento fotoeléctrico y boquillas de corte de mayor calidad, una tendencia que es cada vez más evidente. El corte con gas produce bordes de corte limpios y tiene una velocidad de corte más rápida. Además, el oxicorte también puede cortar chaflanes directamente.
El soplete de corte a gas se utiliza para el corte térmico de materiales mezclando gas combustible con oxígeno para producir una llama. También se le conoce como corte con oxígeno o oxicorte.
Durante el corte con gas, la llama precalienta el material en el punto de corte hasta su temperatura de ignición y luego se inyecta oxígeno para provocar una combustión vigorosa al oxidar el material metálico. La escoria de óxido resultante es expulsada por el flujo de gas, creando un corte.
La pureza del oxígeno utilizado para el corte de gas debe ser superior al 99%. El gas combustible utilizado suele ser gas acetileno, pero también puede ser gas de petróleo, gas natural o gas de hulla.
El gas acetileno proporciona mayor eficiencia de corte y mejor calidad, pero es más caro. El equipo de corte con gas consta principalmente del soplete de corte y la fuente de gas.
El soplete de corte es la herramienta que genera la llama de gas, transfiere y regula la energía térmica de corte, y su estructura afecta la velocidad y calidad del corte. El uso de boquillas de corte rápido puede mejorar la velocidad de corte, lo que da como resultado cortes rectos y superficies lisas.
Para operación manual, los sopletes de corte a gas utilizan cilindros o generadores de oxígeno y gas combustible como fuente de gas. Las máquinas de corte por gas semiautomáticas y automáticas están equipadas con mecanismos de accionamiento del soplete de corte o mecanismos de accionamiento por coordenadas, mecanismos de corte de contornos, seguimiento fotoeléctrico o sistemas de control digital.
Las máquinas automáticas de corte por gas utilizadas para la producción en masa pueden equiparse con múltiples sopletes de corte y sistemas de control computarizados.
2. Mecanismo y condiciones de corte de gas.
El metal en el punto de corte de la pieza se precalienta hasta la temperatura de ignición usando una llama de oxígeno-acetileno y luego se sopla vigorosamente con una corriente de oxígeno puro a alta velocidad.
En este punto, el metal sufre una intensa oxidación y el calor generado derrite el óxido metálico hasta convertirlo en líquido.
Al mismo tiempo, el flujo de oxígeno elimina el óxido fundido, lo que da como resultado un corte limpio en la pieza de trabajo. Al mover el soplete de corte hacia adelante, la pieza de trabajo se puede cortar continuamente.
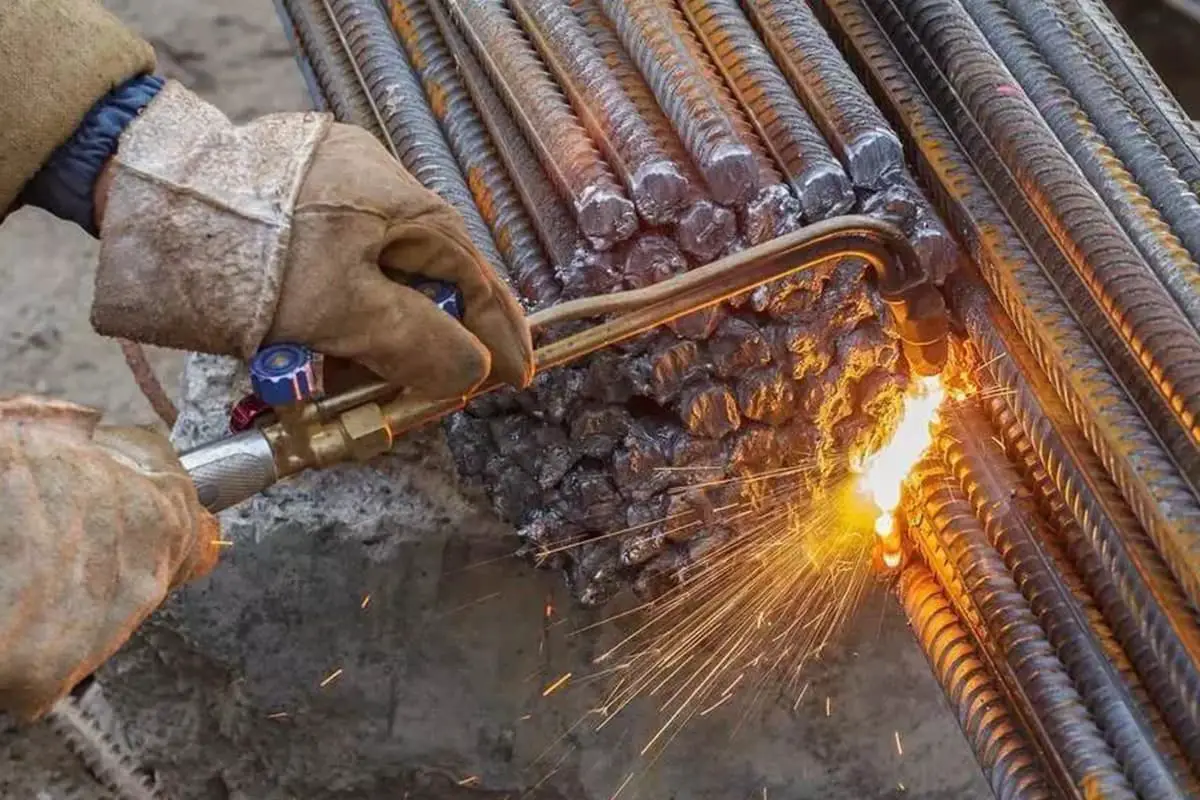
Para lograr el corte con oxígeno se deben cumplir las siguientes condiciones:
1) La temperatura de ignición del metal debe ser inferior a su punto de fusión.
2) El punto de fusión del óxido metálico debe ser inferior al punto de fusión del metal.
El hierro puro, el acero con bajo contenido de carbono, el acero con contenido medio de carbono y el acero ordinario de baja aleación cumplen las condiciones anteriores y tienen un buen rendimiento de corte con gas. El acero con alto contenido de carbono, el hierro fundido, el acero inoxidable y los metales no ferrosos como el cobre y el aluminio son difíciles de cortar con oxígeno.
3) Liberación suficiente de calor durante la combustión del metal:
A través de pruebas y análisis, se ha determinado que al cortar acero con bajo contenido de carbono, aproximadamente el 70 % del calor total requerido se libera durante la combustión, mientras que el precalentamiento de la llama solo representa del 15 % al 30 %. Por lo tanto, este requisito se puede cumplir.
4) La conductividad térmica del metal no debe ser demasiado alta:
La conductividad térmica del metal no debe ser demasiado alta, ya que la pérdida excesiva de calor por la llama de precalentamiento y la liberación de calor durante el proceso de corte en el punto de corte del metal pueden impedir que el proceso de corte comience o continúe. Por ejemplo, el cobre y las aleaciones de cobre no se pueden cortar debido a su alta conductividad térmica.
5) Buena fluidez del óxido generado:
El óxido generado debe tener buena fluidez. De lo contrario, el óxido no podrá eliminarse eficazmente durante el corte, lo que dificultará el proceso de corte.
3. Equipos de corte de gas.
Las máquinas de corte a gas son equipos mecanizados que reemplazan a los sopletes de corte a gas manuales. Presentan mayor productividad, mejor calidad de corte, menor intensidad de mano de obra y menores costos en comparación con el corte manual con gas.
1) Cortadora de gas semiautomática:
Consiste en un pequeño carro que mueve automáticamente la boquilla de corte a lo largo de una pista dedicada, pero la trayectoria de la pista debe ajustarse manualmente.
2) Máquina cortadora de perfiles a gas:
Tipo pórtico: La boquilla de corte se acciona a lo largo del perfil mediante ruedas.
Tipo de brazo oscilante: La boquilla de corte es impulsada por un mecanismo de brazo oscilante.
3) Máquina cortadora de gas con seguimiento fotoeléctrico:
Este equipo de corte por gas automatizado utiliza los principios del seguimiento fotoeléctrico para seguir patrones automáticamente y accionar el soplete de corte para cortar perfiles.
4) Máquina cortadora de gas CNC:
CNC significa Control Numérico por Computadora, que es un nuevo método de control donde las instrucciones (o programas) para controlar máquinas herramienta o equipos se proporcionan en formato digital. Cuando estas instrucciones se proporcionan al equipo de control de una máquina cortadora de gas CNC automática, la máquina puede realizar el corte automáticamente de acuerdo con el programa proporcionado.
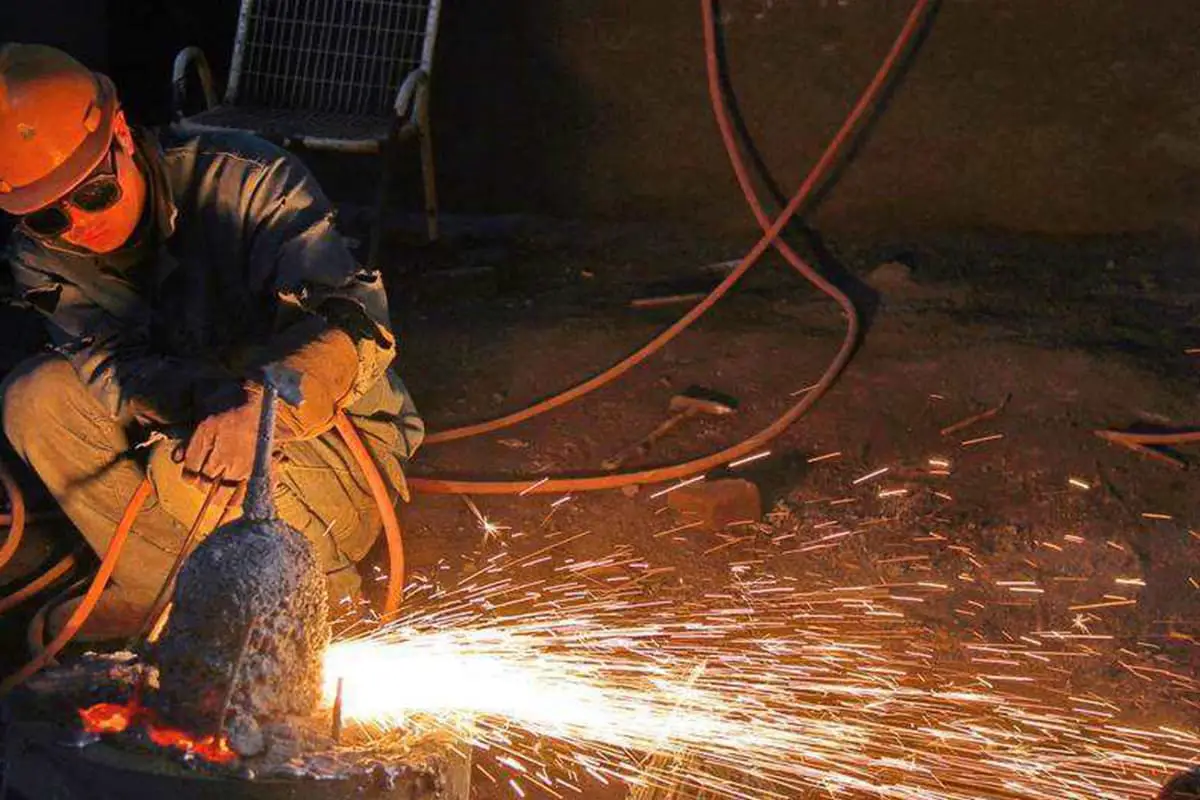
4. Proceso de corte de gas
El proceso de corte con gas incluye principalmente la presión de oxígeno de corte, la velocidad de corte, la eficiencia de la llama de precalentamiento, el ángulo de inclinación de la boquilla de corte y la pieza de trabajo, y la distancia entre la boquilla de corte y la pieza de trabajo.
1) Reducir la presión de oxígeno:
Está influenciado por el grosor de la pieza de trabajo, el tipo de boquilla de corte y la pureza del oxígeno.
Al cortar materiales finos, se debe seleccionar una boquilla de corte más pequeña y una presión de oxígeno más baja.
La pureza del oxígeno tiene un impacto significativo en la velocidad de corte, el consumo de gas y la calidad del corte.
2) Velocidad de corte:
Depende del espesor de la pieza y de la forma de la boquilla de corte. A medida que aumenta el espesor, disminuye la velocidad de corte.
La velocidad de corte no debe ser demasiado rápida ni demasiado lenta, ya que esto puede provocar una resistencia excesiva y cortes incompletos.
La precisión de la velocidad de corte se evalúa principalmente en función de la cantidad de arrastre en el corte.
3) Eficiencia de la llama de precalentamiento:
Para el precalentamiento en el corte con gas se utiliza una llama neutra o ligeramente oxidante y no se debe utilizar una llama de carburación.
La eficiencia de la llama de precalentamiento se expresa en términos del consumo de gas combustible por hora.
La eficiencia de la llama de precalentamiento está relacionada con el espesor de la pieza.
4) Ángulo de inclinación de la boquilla de corte y la pieza de trabajo:
El ángulo de inclinación de la boquilla de corte y la pieza de trabajo está determinado principalmente por el espesor de la pieza de trabajo.
El ángulo de inclinación de la boquilla de corte y la pieza de trabajo afecta directamente a la velocidad de corte y al arrastre.
Una inclinación hacia atrás puede reducir la resistencia y aumentar la velocidad de corte.
5) Distancia entre la boquilla de corte y la superficie de la pieza:
La distancia entre la boquilla de corte y la superficie de la pieza de trabajo debe determinarse en función de la longitud de la llama de precalentamiento y el espesor de la pieza de trabajo, generalmente entre 3 y 5 mm.
Cuando δ<20 mm, la llama puede ser más larga y la distancia puede aumentarse en consecuencia.
Cuando δ>=20 mm, la llama debe ser más corta y la distancia se puede reducir.
6) Requisitos de calidad para cortes con gas:
La superficie de corte con gas debe ser lisa y limpia, con líneas finas y gruesas consistentes. La escoria de óxido de hierro producida durante el corte con gas es fácil de separar. El espacio de corte con gas debe ser estrecho y consistente, y los bordes de la placa de acero no deben derretirse.
Criterios para evaluar y clasificar la calidad del corte:
a) Rugosidad de la superficie: La rugosidad de la superficie se refiere a la distancia entre los picos y valles de la superficie de corte (promedio de cinco puntos arbitrarios), indicada por G.
b) Planitud: La planitud se refiere al nivel de irregularidad a lo largo de la dirección de corte perpendicular a la superficie de corte. Se calcula como porcentaje del espesor δ de la chapa de acero cortada, indicado por B.
c) Grado de fusión del borde superior: Se refiere al grado de fusión o colapso durante el proceso de corte con gas, manifestado por la presencia de esquinas colapsadas y la formación de gotas o tiras fundidas intermitentes o continuas, indicadas por S.
d) Suspensión de escoria: La suspensión de escoria se refiere al óxido de hierro adherido al borde inferior de la superficie de corte. Se clasifica en diferentes grados según la cantidad de adherencia y la dificultad de eliminación, indicado por Z.
e) Separación máxima de defectos: La separación máxima de defectos se refiere a la aparición de ranuras en la superficie de corte a lo largo de la dirección de la línea de corte debido a vibraciones o interrupciones, provocando una disminución repentina de la rugosidad de la superficie. La profundidad de la ranura está entre 0,32 mm y 1,2 mm y el ancho de la ranura no supera los 5 mm. Estas ranuras se consideran defectos. El espacio máximo entre defectos se indica con Q.
f) Rectitud: La rectitud se refiere al espacio entre la línea recta que conecta los puntos inicial y final a lo largo de la dirección de corte y la superficie de corte en forma de corona. Lo indica P.
g) Perpendicularidad: La perpendicularidad se refiere a la desviación máxima entre la superficie de corte real y la línea perpendicular a la superficie del metal que se está cortando.
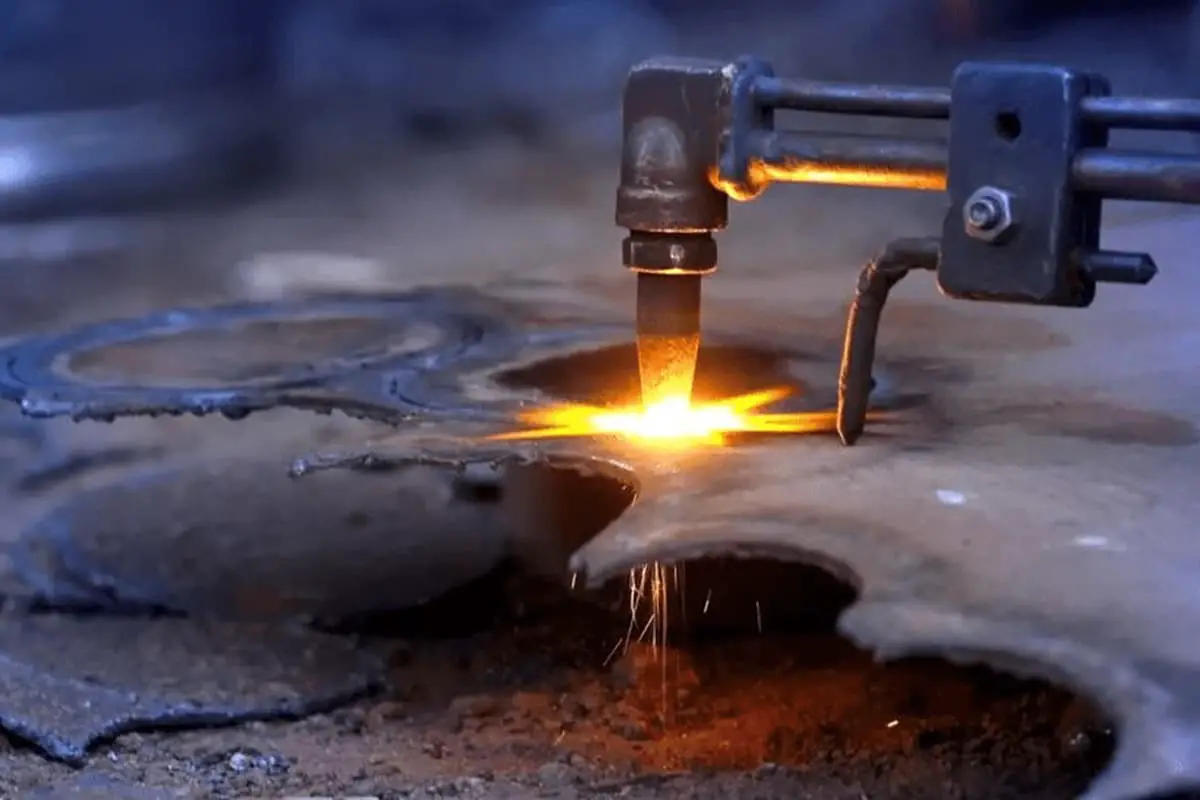
7) Causas y métodos de prevención de defectos comunes:
(1) Ancho excesivo y superficie de corte rugosa:
Esto se debe a una presión excesiva de oxígeno en el corte. Cuando la presión del oxígeno de corte es demasiado baja, la escoria no se puede expulsar, lo que hace que la escoria se pegue y sea difícil de eliminar.
Prevención: Ajuste la presión de oxígeno de corte a un nivel apropiado para el ancho de corte deseado y la rugosidad de la superficie.
(2) Fusión de bordes o superficies irregulares:
Esto se debe a una intensidad excesiva de la llama de precalentamiento o a una velocidad de corte lenta. Una intensidad insuficiente de la llama de precalentamiento puede provocar interrupciones en el proceso de corte y una superficie irregular.
Prevención: Asegurar una intensidad de llama de precalentamiento adecuada para obtener un corte regular y uniforme.
(3) Arrastre excesivo después del corte:
Esto ocurre cuando la velocidad de corte es demasiado rápida, lo que provoca una resistencia excesiva y cortes incompletos. En casos severos, la espuma puede volar hacia arriba y causar recalentamiento.
Prevención: Ajuste la velocidad de corte a un nivel adecuado para obtener un corte adecuado sin arrastre excesivo.
8) Formas de mejorar la calidad de la superficie de corte:
(1) Presión de oxígeno de corte adecuada:
Una presión excesiva de oxígeno de corte puede provocar un corte más ancho y una superficie rugosa, con lo que se desperdicia oxígeno. Una presión de oxígeno de corte insuficiente puede hacer que la escoria se pegue y sea difícil de eliminar.
Solución: Ajuste la presión de oxígeno de corte a un nivel apropiado para la calidad de corte deseada.
(2) Intensidad adecuada de la llama de precalentamiento:
Una intensidad excesiva de la llama de precalentamiento puede provocar que los bordes de la superficie de corte se derritan, mientras que una intensidad insuficiente puede provocar interrupciones en el proceso de corte y una superficie irregular.
Solución: Asegúrese de que la intensidad de la llama de precalentamiento sea adecuada para lograr un corte suave y uniforme.
(3) Velocidad de corte adecuada:
Cuando la velocidad de corte es demasiado rápida, puede provocar una resistencia excesiva, cortes incompletos y escoria que vuela hacia arriba, lo que provoca recalentamiento. Cuando la velocidad de corte es demasiado lenta, los bordes de la placa de acero pueden derretirse, los residuos de gas y las placas más delgadas pueden sufrir una deformación y adhesión excesivas, lo que dificulta la limpieza posterior al corte.
Solución: Ajuste la velocidad de corte a un nivel apropiado para la calidad de corte deseada.
5. Ventajas y desventajas del corte con gas.
Ventajas del corte con gas.
1. El corte con gas es más rápido que otros métodos de corte mecánico, lo que lo hace más eficiente.
2. Es más económico utilizar el corte con oxígeno y acetileno para cortar secciones con formas y espesores difíciles que representan un desafío para los métodos de corte mecánico.
3. La inversión en equipos de corte con gas es menor en comparación con el corte mecánico, y el equipo es liviano y portátil, lo que lo hace adecuado para operaciones de campo.
4. Al cortar arcos pequeños, la dirección de corte se puede cambiar rápidamente. Al cortar piezas grandes, no es necesario mover la pieza en sí; sólo es necesario mover la llama de oxígeno y acetileno para un corte rápido.
5. El corte con gas se puede realizar de forma manual o mecánica.
6. El equipo es portátil y puede usarse en el sitio.
7. Se pueden cortar rápidamente láminas de metal grandes en el sitio moviendo el soplete de corte en lugar de mover el bloque de metal.
Desventajas del corte de gas.
1. La tolerancia dimensional es significativamente menor que la de las herramientas de corte mecánicas.
2. Aunque el corte con gas también puede cortar metales propensos a la oxidación como el titanio, este proceso se limita principalmente al corte de acero y hierro fundido en aplicaciones industriales.
3. La llama de precalentamiento y la escoria al rojo vivo emitidas suponen un riesgo de incendio y quemaduras para los operadores.
4. Se necesitan instalaciones adecuadas de control de humos y ventilación para la combustión de combustible y la oxidación de metales.
5. El corte de aceros de alta aleación y hierro fundido puede requerir mejoras en el proceso.
6. El corte de aceros de alta dureza puede requerir precalentamiento antes del corte y calentamiento continuo después del corte para controlar la estructura metalúrgica y las propiedades mecánicas cerca del filo.
7. No se recomienda el corte con gas para cortes a larga distancia en áreas grandes.
6. Aplicaciones de corte de gas
1. Ampliamente utilizado para cortar placas de acero y preparar chaflanes para soldar.
2. Adecuado para cortar sistemas de canales de piezas fundidas, con espesores de corte de hasta 300 mm o más.
3. Se utiliza principalmente para cortar varios tipos de acero al carbono y acero de baja aleación.
4. Al cortar aceros con alto contenido de carbono y aceros de baja aleación con tendencia a templarse, para evitar endurecimiento o agrietamiento en el filo, es necesario aumentar la intensidad de la llama de precalentamiento y disminuir la velocidad de corte, o incluso pre- Caliente el material de acero antes de cortar.