1. Haz una pregunta
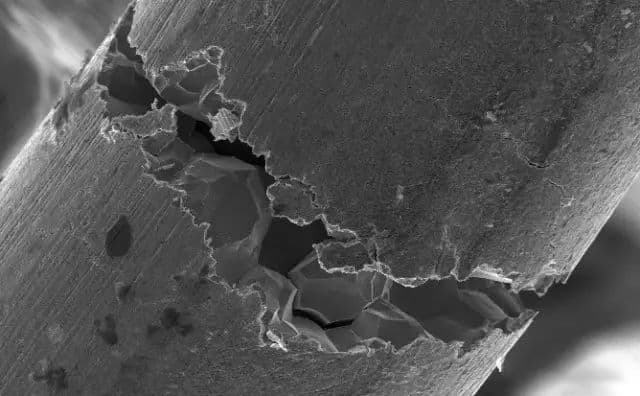
Las regulaciones técnicas unificadas generalmente requieren que los recipientes de acero inoxidable austenítico utilizados en ambientes que pueden causar corrosión intergranular se sometan a una solución sólida o un tratamiento estabilizador después de la soldadura. Este requisito es razonable.
Sin embargo, incluso si el diseñador incluye este requisito en las especificaciones técnicas del dibujo, a menudo resulta difícil para el fabricante cumplir con los estándares ideales debido a los desafíos en el control de los parámetros del proceso de tratamiento térmico y otras dificultades imprevistas. De hecho, la mayoría de los equipos de acero inoxidable que se utilizan hoy en día se utilizan sin someterse a un tratamiento térmico posterior a la soldadura.
Esto plantea la pregunta: ¿cuál es el mecanismo de corrosión intergranular, que es la forma más común de corrosión en el acero inoxidable austenítico? ¿Cuáles son las condiciones ambientales que pueden provocar corrosión intergranular? ¿Cuáles son los principales métodos para prevenir y controlar la corrosión intergranular? ¿Son necesarios tratamientos térmicos para recipientes de acero inoxidable austenítico utilizados en entornos que pueden causar corrosión intergranular después de la soldadura?
Este artículo explorará estas preguntas haciendo referencia a estándares, especificaciones y monografías relevantes y presentando opiniones personales basadas en la experiencia de producción.
2. Mecanismo de corrosión intergranular.
La corrosión intergranular es un tipo de corrosión localizada que ocurre a lo largo de los límites de los granos o muy cerca de los límites de los granos de un metal o aleación. Esta corrosión se caracteriza por una corrosión mínima dentro de los granos y una corrosión significativa a lo largo de los límites de los granos, lo que debilita la unión entre los granos.
Si la corrosión intergranular es severa, puede reducir la resistencia y ductilidad del metal, provocando que falle bajo cargas normales. Las dos teorías principales detrás de la corrosión intergranular son la teoría del bajo contenido de cromo y la teoría de la disolución selectiva de impurezas en los límites de los granos.
2.1 Teoría del cromo magro
La corrosión intergranular del acero inoxidable austenítico comúnmente utilizado en ambientes oxidantes o débilmente oxidantes generalmente es causada por un calentamiento inadecuado durante el procesamiento o uso. El calentamiento inadecuado se refiere al lento calentamiento o enfriamiento del acero en el rango de temperatura de 450-850°C, lo que lo hace vulnerable a la corrosión intergranular. Por tanto, este rango de temperatura se considera peligroso para el acero inoxidable austenítico.
El acero inoxidable austenítico se somete a un tratamiento de solución antes de salir de fábrica. El tratamiento con solución implica calentar el acero a 1050-1150 °C y luego enfriarlo rápidamente para crear una solución sólida homogénea. El acero austenítico contiene una pequeña cantidad de carbono y su solubilidad sólida disminuye al disminuir la temperatura. Por ejemplo, la solubilidad sólida del carbono en 0Cr18Ni9Ti es aproximadamente 0,2% a 1100°C y aproximadamente 0,02% a 500-700°C.
Por tanto, el carbono del acero tratado con solución está sobresaturado. Cuando el acero se calienta o enfría entre 450 y 850 °C, el carbono puede precipitar de la austenita y distribuirse a lo largo de los límites de los granos en forma de (Fe, Cr) 23C6. El contenido de cromo de (Fe, Cr) 23C6 es mucho mayor que el de la matriz austenítica, y su precipitación consume una gran cantidad de cromo cerca de los límites de los granos, que no se puede reponer oportunamente mediante difusión. La lenta difusión del cromo hace que el contenido de cromo cerca de los límites de los granos caiga por debajo del umbral de 12% Cr requerido para la pasivación, creando una región pobre en cromo y dañando el estado pasivo.
El grano en sí, sin embargo, todavía mantiene un estado pasivo con un alto potencial. El grano y el límite de grano forman una batería microgalvánica, con un cátodo grande y un ánodo pequeño, lo que provoca corrosión en la región del límite de grano.
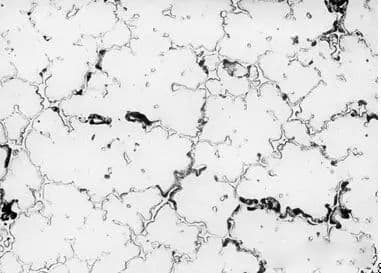
2.2 Teoría de la disolución selectiva de impurezas en los límites de grano.
En la práctica de producción, hemos observado que el acero inoxidable austenítico también puede sufrir corrosión intergranular en medios oxidantes fuertes (como el ácido nítrico concentrado), pero la naturaleza de la corrosión es diferente de la de los medios oxidantes o oxidantes débiles. La corrosión intergranular en medios oxidantes fuertes generalmente ocurre en acero tratado con solución sólida, pero no ocurre en acero sensibilizado.
Si impurezas como fósforo o silicio alcanzan 100 ppm o 1000-2000 ppm, respectivamente, en la solución sólida, se segregarán a lo largo de los límites de los granos. Estas impurezas se disolverán bajo la acción de medios oxidantes fuertes, provocando corrosión intergranular.
Cuando el acero se sensibiliza, la formación de (MP)23C6 con fósforo o la primera segregación de carbono elimina o reduce la segregación de impurezas en los límites de grano, eliminando o debilitando la sensibilidad del acero a la corrosión intergranular.
Estas dos teorías sobre el mecanismo de la corrosión intergranular se aplican al estado estructural de una aleación y un medio específicos y no son mutuamente excluyentes, sino más bien complementarias. En la práctica de producción, la mayoría de los casos de corrosión intergranular ocurren en medios oxidantes o oxidantes débiles y, por lo tanto, pueden explicarse mediante la teoría del bajo contenido de cromo.
3. Ambiente medio que causa corrosión intergranular.
Hay dos tipos principales de medios que causan corrosión intergranular en acero inoxidable austenítico. El primer tipo es un medio oxidante o débilmente oxidante, y el segundo tipo es un medio oxidante fuerte como el ácido nítrico concentrado. El primer tipo de medios es más común.
Aquí hay una lista de ambientes medios comunes que causan corrosión intergranular en acero inoxidable austenítico:
3.1 Medio común que causa la corrosión intergranular del acero inoxidable austenítico
El “Cuadro de datos de corrosión” preparado por GA. Nelson enumera los medios comunes que causan corrosión intergranular en acero inoxidable austenítico:
- Ácido acético
- Ácido acético + ácido salicílico
- Nitrato de amonio
- sulfato de amonio
- Ácido cromico
- Sulfato de cobre
- Ácido graso
- Ácido fórmico
- sulfato de hierro
- Ácido fluorhídrico + sulfato de hierro
- Ácido láctico
- Ácido nítrico
- Ácido nítrico + ácido clorhídrico
- ácido oxálico
- Ácido fosfórico
- Agua de mar
- niebla salina
- bisulfato de sodio
- Hipoclorito de sodio
- Dióxido de azufre (húmedo)
- Ácido sulfúrico
- Ácido sulfúrico + sulfato de cobre
- Ácido sulfúrico + sulfato ferroso
- Ácido sulfúrico + metanol
- Ácido sulfúrico + ácido nítrico
- sulfito
- ácido ftálico
- Hidróxido de sodio + sulfuro de sodio.
3.2 Prueba de tendencia a la corrosión intergranular
Cuando se utiliza acero inoxidable austenítico en un ambiente que puede causar corrosión intergranular, la prueba de tendencia a la corrosión intergranular se debe realizar de acuerdo con los métodos de prueba GB4334.1 a GB4334 para la corrosión intergranular de acero inoxidable. Los requisitos de selección y calificación de los métodos de ensayo para la tendencia a la corrosión intergranular del acero inoxidable austenítico deben cumplir los siguientes criterios:
(1) El acero inoxidable austenítico y el acero inoxidable especial para ácido nítrico concentrado utilizado en ácido nítrico con una temperatura de 60 °C o más y una concentración del 5 % o más se probarán de acuerdo con el método de prueba GB4334.3 para ácido nítrico al 65 %. Corrosión del acero inoxidable. La velocidad de corrosión promedio durante cinco ciclos o tres ciclos no debe exceder los 0,6 g/m 2 h (o equivalente a 0,6 mm/a). La muestra puede estar en uso o sensibilizada.
(2) Acero inoxidable austenítico de cromo-níquel (como 0Cr18Ni10Ti, 0Cr18Ni9, 00Cr19Ni10 y aceros similares): Requisitos generales: de acuerdo con el método de prueba de corrosión de sulfato de cobre con ácido sulfúrico GB4334.5 para acero inoxidable, si no hay grietas de corrosión intergranulares en el superficie de la muestra después de la prueba de flexión. Requisitos más altos: la velocidad de corrosión promedio no debe exceder 1,1 g/m 2 h según el método de prueba de corrosión por sulfato férrico de ácido sulfúrico GB4334.2 para acero inoxidable.
(3) Acero inoxidable austenítico que contiene molibdeno (como 0Cr18Ni12Mo2Ti, 00Cr17Ni14Mo2 y aceros similares): Requisitos generales: de acuerdo con el método de prueba de corrosión de sulfato de cobre con ácido sulfúrico GB4334.5 para acero inoxidable, no debe haber grietas por corrosión de partículas intergranulares en la muestra. superficie después de la prueba de flexión. Requisitos más altos: la tasa de corrosión no debe exceder 1,5 según el método de prueba de corrosión del ácido fluorhídrico con ácido nítrico GB4334.4 para acero inoxidable. La velocidad de corrosión promedio no debe exceder 1,1 g/m 2 h según el método de prueba de corrosión por sulfato férrico de ácido sulfúrico GB4334.2 para acero inoxidable.
(4) Si el medio tiene requisitos especiales, se podrán realizar ensayos de corrosión intergranular distintos de los especificados anteriormente, debiendo especificarse los requisitos de calificación correspondientes.
4. Medidas para prevenir y controlar la corrosión intergranular
Según el mecanismo de corrosión, se pueden tomar las siguientes medidas para prevenir y controlar la corrosión intergranular en acero inoxidable austenítico:
(1) El uso de acero inoxidable con contenido de carbono ultra bajo puede ayudar a reducir el contenido de carbono a menos del 0,03 %.
Por ejemplo, se puede elegir 00Cr17Ni14Mo2 para evitar la formación de (Fe, Cr) 23C6 en el acero y la aparición de una zona pobre en cromo, evitando así la corrosión intergranular.
Normalmente, para componentes que tienen baja resistencia, bajo voltaje y buena plasticidad, se puede seleccionar 0Cr18Ni9 por su rentabilidad.
(2) El acero inoxidable estabilizado se refiere al acero inoxidable que contiene titanio y niobio.
Durante la producción de acero, se agrega una cantidad específica de titanio y niobio, y estos elementos tienen una fuerte afinidad con el carbono, formando tic o NBC dentro del acero.
Además, la solubilidad sólida de tic o NBC es mucho menor que la del (Fe, Cr) 23C6 y es casi insoluble en austenita a la temperatura de la solución sólida.
Por lo tanto, incluso si (Fe, Cr) 23C6 no precipita en el límite del grano cuando se alcanza la temperatura de sensibilización, la probabilidad de corrosión intergranular en el acero inoxidable austenítico se reduce considerablemente.
Por ejemplo, aceros como 1Cr18Ni9Ti y 1Cr18Ni9Nb pueden funcionar dentro de un rango de temperatura de 500-700°C sin sufrir corrosión intergranular.
(3) Al soldar acero inoxidable austenítico con arco eléctrico, la temperatura del baño de arco puede alcanzar hasta 1300 °C y la temperatura en ambos lados de la soldadura disminuye al aumentar la distancia, creando una zona de temperatura de sensibilización.
Es ideal calentar y enfriar el acero inoxidable austenítico lo más lentamente posible dentro del rango de temperatura de sensibilización.
En el caso de tendencias a la corrosión intergranular, el acero inoxidable inestable debe calentarse a 1000-1120°C durante 1-2 minutos por milímetro y luego enfriarse.
Para acero inoxidable estabilizado, se recomienda calentar a 950-1050°C.
Después de someterse al tratamiento con solución, es importante evitar calentar el acero a la temperatura de sensibilización, ya que esto puede causar que el carburo de cromo precipite nuevamente a lo largo del límite del grano.
(4) Elegir el método de soldadura correcto es importante para reducir la sensibilidad de las uniones soldadas a la corrosión intergranular. Si la operación permanece inalterada o el material de soldadura es muy espeso, un mayor tiempo de soldadura aumenta las posibilidades de permanecer dentro de la zona de temperatura sensibilizada.
Para minimizar la sensibilidad de las uniones soldadas, es necesario minimizar la entrada de energía de la línea durante la soldadura.
En términos generales, la soldadura por arco de argón tiene una potencia de línea de entrada menor en comparación con la soldadura por arco eléctrico, lo que la convierte en una mejor opción para soldadura y reparación.
Para soldar piezas, se recomienda utilizar acero inoxidable con contenido ultra bajo de carbono o acero inoxidable con elementos estabilizadores como titanio y niobio. Además, se recomienda utilizar varillas de soldadura con muy bajo contenido de carbono o varillas de soldadura que contengan niobio.
Cuando se utiliza soldadura por arco de argón, para evitar el sobrecalentamiento de la junta de soldadura, la operación debe ser rápida y el metal base en ambos lados de la soldadura debe enfriarse rápidamente después de soldar para minimizar el tiempo transcurrido dentro del rango de temperatura de conciencia.
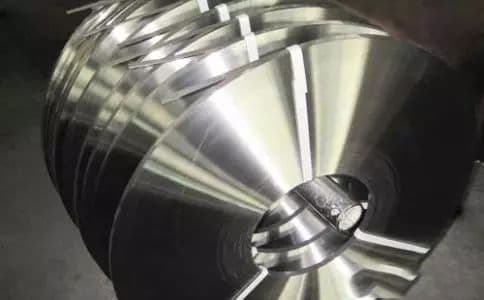
5. Tratamiento post-soldadura
El tratamiento térmico post-soldadura no siempre es una prioridad en el área de soldadura.
Normalmente, se lleva a cabo un tratamiento con solución sólida a un rango de temperatura de 1100-1150°C durante un período determinado y luego se enfría. El enfriamiento en el rango de 925-540°C debe completarse en tres minutos, seguido de un enfriamiento rápido por debajo de 425°C.
Para un tratamiento estabilizado, la pieza de trabajo debe enfriarse con aire después de haberla mantenido en un rango de temperatura de 850-880°C durante varias horas.
La eficacia del tratamiento térmico posterior a la soldadura depende en gran medida de parámetros clave del proceso, como la temperatura del horno, la tasa de aumento de temperatura, la diferencia de temperatura entre varias partes de la pieza de trabajo durante el aumento de temperatura, la atmósfera del horno, el tiempo de mantenimiento y la diferencia de temperatura entre varias partes durante el calentamiento. conservación, velocidad de enfriamiento y temperatura del horno.
Para recipientes de acero inoxidable austenítico que puedan provocar corrosión intergranular se puede realizar un tratamiento en solución o tratamiento estabilizado de piezas en general. Sin embargo, el tratamiento térmico posterior a la soldadura de todo el recipiente (normalmente un intercambiador de calor) presenta muchas dificultades.
Este tipo de tratamiento no es un tratamiento térmico local post-soldadura, sino un tratamiento térmico post-soldadura de todas las piezas o recipientes soldados.
Debido a la compleja estructura y forma de la mayoría de los recipientes químicos, como el intercambiador de calor de carcasa y tubos de uso común, es casi imposible controlar los parámetros clave del proceso para la solución sólida posterior a la soldadura o el tratamiento estabilizado de todo el intercambiador de calor de carcasa. tubo. por sí solo garantiza la calidad del tratamiento térmico post-soldadura.
En muchos casos, este tratamiento puede incluso resultar contraproducente, no sólo no mejorando la estructura de la soldadura, sino también deteriorando innecesariamente la estructura del metal base.
Por lo tanto, más del 90% de los recipientes químicos de acero inoxidable austenítico utilizados en entornos de corrosión intergranular todavía se utilizan en su estado posterior a la soldadura en lugar de someterse a un tratamiento térmico posterior a la soldadura.
6. Resumen
El acero inoxidable austenítico al cromo-níquel es el material resistente a la corrosión más utilizado, y la corrosión intergranular es la forma más común de falla en los recipientes de acero inoxidable austenítico al cromo-níquel.
La corrosión intergranular debilita significativamente la unión entre los granos y, en casos severos, puede eliminar por completo la resistencia mecánica. La superficie del acero inoxidable que ha sufrido este tipo de corrosión permanece brillante, pero puede romperse fácilmente en partículas finas con un suave golpe.
La corrosión intergranular es difícil de detectar, lo que puede causar daños repentinos al equipo y debe tomarse en serio.
Los recipientes de acero inoxidable austenítico de cromo-níquel generalmente se forman mediante soldadura, y los dos lados de la junta soldada son áreas intergranulares sensibles a la corrosión, que son más susceptibles a daños por corrosión en comparación con el metal base.
El tratamiento térmico posterior a la soldadura puede mejorar la resistencia a la corrosión intergranular en la zona de soldadura al mismo nivel que el metal base. Este es el objetivo final del tratamiento térmico post-soldadura.
Sin embargo, en la práctica, hay muchos factores a considerar, como la compleja estructura general y la forma de la soldadura, lo que dificulta garantizar los parámetros del proceso de tratamiento térmico posterior a la soldadura.
Como resultado, la mayoría de los aceros inoxidables austeníticos al cromo-níquel en servicio se utilizan después de la soldadura.
Si la zona de soldadura de un recipiente de acero inoxidable austenítico de cromo-níquel utilizado para resistencia a la corrosión intergranular se somete a un tratamiento de solución sólida o un tratamiento estabilizado, no se puede generalizar. Se debe analizar la forma estructural del contenedor para determinar si el tratamiento térmico se puede llevar a cabo de manera efectiva. De lo contrario, aunque sea necesario un tratamiento térmico post-soldadura, este podría tener efectos adversos, no sólo no logrando el resultado deseado, sino también afectando la estructura del metal base.
Para aumentar la resistencia a la corrosión intergranular de los recipientes de acero inoxidable austenítico al cromo-níquel, es necesario seleccionar acero inoxidable con contenido de carbono ultrabajo y acero inoxidable estabilizado en función del entorno y mecanismo de corrosión específicos, elegir el método de soldadura correcto durante la soldadura y combinar adecuadamente los medidas de prevención y control antes mencionadas para conseguir buenos resultados.
No basta con depender de una solución sólida o un tratamiento de estabilización después de la soldadura.