Prefacio
Para garantizar el funcionamiento adecuado de un sistema o estructura mecánica, cada componente debe ser capaz de realizar eficazmente su función prevista. El objetivo del diseño de seguridad de componentes de ingeniería es garantizar que los componentes tengan la resistencia, rigidez y estabilidad adecuadas.
La estabilidad es un concepto ampliamente comprendido y se refiere a la capacidad de mantener o recuperar su estado original de equilibrio bajo una fuerza externa. Por ejemplo, la flexión repentina de una varilla delgada bajo presión, el colapso de una columna de edificio debido a una falla en el soporte de carga o el pandeo de miembros de paredes delgadas son ejemplos de inestabilidad.
Hoy me centraré en hablar sobre mi comprensión de la rigidez y la fuerza.
Fortaleza
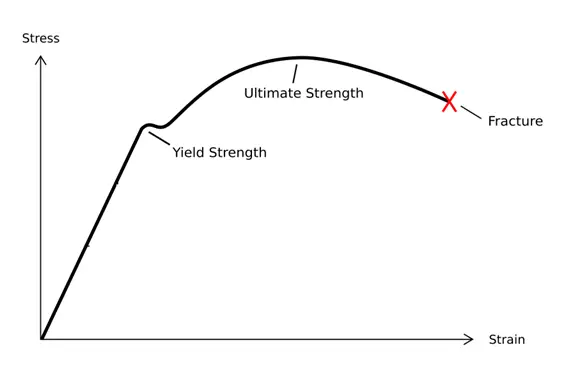
¿Qué es la fuerza?
Definición: La capacidad de componentes o piezas para resistir daños (fractura) o deformación sustancial cuando se someten a fuerzas externas.
Por ejemplo, Tom usó su iPad como balanza, pero cuando se paró sobre él, la pantalla se rompió, lo que indica falta de fuerza. Asimismo, muchas ramas grandes se rompen con los fuertes vientos del verano, lo que demuestra falta de fuerza.
La resistencia es una medida de la capacidad de un material para resistir fallas, como la fractura. Normalmente abarca la resistencia a la tracción y la resistencia a la compresión, que reflejan la cantidad de falla del material bajo tensión.
La unidad de medida de la resistencia se expresa comúnmente en MPa.
Tipo de corte de energía
Fractura frágil: fractura repentina que se produce sin deformación plástica evidente.
Por ejemplo, la fractura de una muestra de hierro fundido a lo largo de la sección transversal durante un ensayo de tracción y la fractura de una muestra de hierro fundido con una sección transversal circular a lo largo de la sección oblicua durante un ensayo de torsión.
Comportamiento plástico: el material produce importantes deformaciones plásticas y hace que el componente pierda su capacidad de trabajo.
Por ejemplo, la muestra de acero con bajo contenido de carbono tendrá una deformación plástica significativa durante la tensión o la torsión.
teoría de la fuerza
1. Teoría de la tensión máxima de tracción:
Cuando el esfuerzo de tracción máximo σ1 en un punto del miembro alcanza el esfuerzo último σb en condiciones de esfuerzo unidireccional, el material sufrirá una fractura frágil. Por lo tanto, los criterios para la falla por fractura frágil de componentes con puntos críticos bajo condiciones de tensión complejas son: σ1 = σb.
En consecuencia, las condiciones de resistencia que establece la primera teoría de la resistencia son: σ1 ≤ σb.
2. Teoría de la deformación máxima por tracción:
Cuando la deformación máxima de tracción ε1 alcanza el valor límite εu en condiciones de tensión unidireccional, el material fallará debido a una fractura frágil. Esto se puede expresar como ε1 = εu.
A partir de la Ley de Hooke generalizada, podemos calcular ε1 como: ε1 = (σ1 – u(σ2 + σ3)) / E, luego σ1 – u(σ2 + σ3) = σb.
Las condiciones de resistencia establecidas por la segunda teoría de la resistencia son: σ1 – u(σ2 + σ3) ≤ σb.
3. Teoría del esfuerzo cortante máximo:
Cuando el esfuerzo cortante máximo τMax alcanza el esfuerzo cortante último τ0 en condiciones de tensión unidireccional, el material fallará debido a la fluencia. Esto se puede expresar como τMax = τ0.
La fórmula para el esfuerzo cortante en una sección inclinada durante la tensión axial es τ0 = σs/2 (siendo σs el esfuerzo normal en la sección transversal). La fórmula para τMax es (σ1 – σ3)/2. Por tanto, la condición de daño se puede reescribir como σ1 – σ3 = σs.
La condición de resistencia establecida por la tercera teoría de la resistencia es: σ1 – σ3 ≤ σs.
4. Teoría energética específica del cambio de forma:
Cuando la velocidad de cambio de forma en un punto del miembro alcanza el valor límite en condiciones de tensión unidireccional, el material fallará debido a la fluencia.
La condición de resistencia establecida por la cuarta teoría de la resistencia es:
√(σ1^2 + σ2^2 + σ3^2 – σ1σ2 – σ2σ3 – σ3σ1) < σs.
2. Rigidez
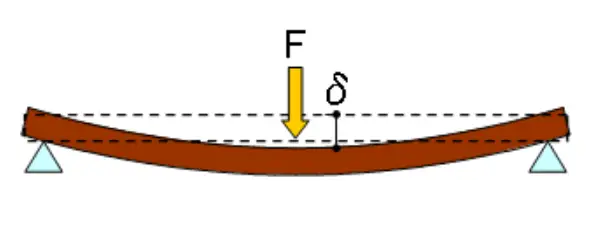
¿Qué es la rigidez?
Definición: se refiere a la capacidad de los miembros o piezas para resistir la deformación o el desplazamiento elástico bajo la acción de una fuerza externa, es decir, la deformación o el desplazamiento elástico no debe exceder el rango de diseño permitido.
La rigidez es un parámetro que refleja la relación entre la deformación estructural y la fuerza, indicando la cantidad de deformación producida por una determinada cantidad de fuerza aplicada.
En términos simples, la rigidez es similar a un resorte, donde la rigidez del resorte se define como la relación entre la fuerza de tracción y el alargamiento. La unidad de rigidez normalmente se expresa en N/m.
Tipo de rigidez:
Cuando la carga aplicada es constante, se llama rigidez estática.
Cuando la carga se alterna, esto se llama rigidez dinámica.
La rigidez estática abarca la rigidez estructural y la rigidez de contacto.
La rigidez estructural se refiere a la rigidez del miembro mismo e incluye rigidez a la flexión y rigidez a la torsión.
1. Rigidez a flexión: calculada según la siguiente fórmula:
K=P/δ
Donde P — carga estática (n);
δ——Deformación elástica en la dirección de carga (μm)。
2. La rigidez torsional se calcula según la siguiente fórmula:
K i =ML/θ
Donde M — par aplicado (n · m);
L — distancia desde la posición de acción del par hasta el extremo fijo (m);
θ—— Ángulo de torsión (°)
3. Relación entre resistencia y rigidez
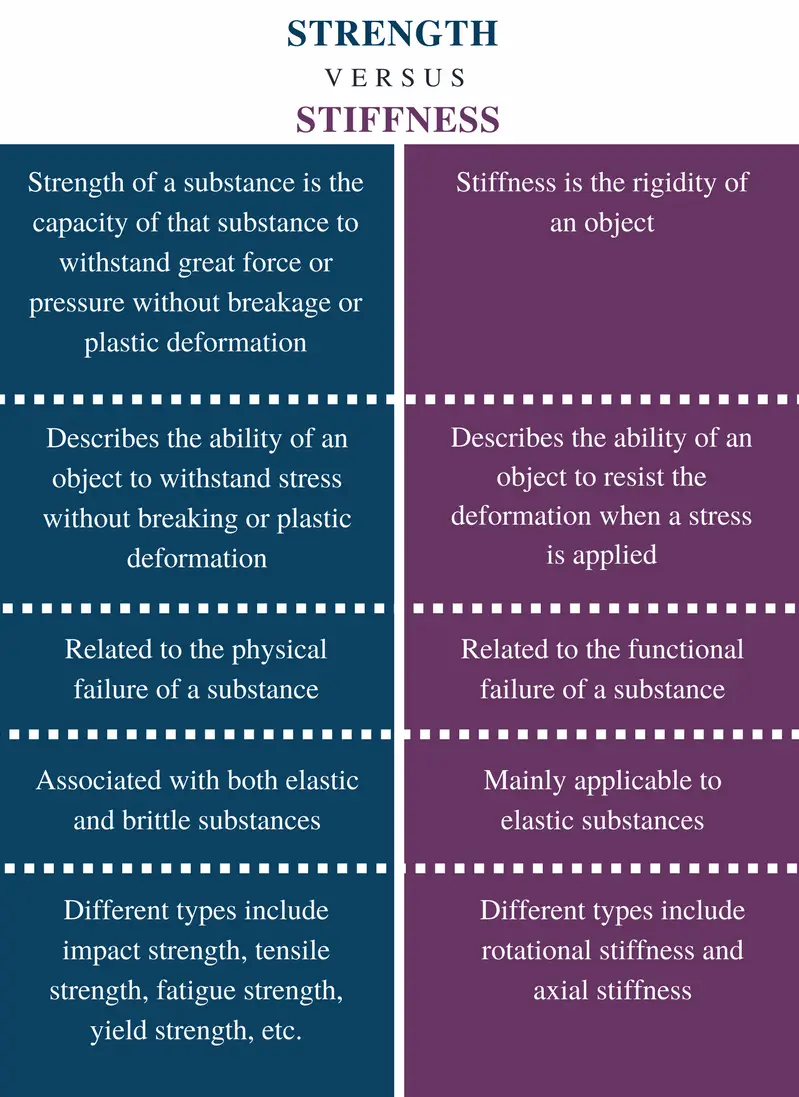
De la explicación anterior de resistencia y rigidez, se puede ver que la resistencia se centra en la falla bajo fuerza externa y se clasifica en fluencia plástica y falla por fractura frágil, que está relacionada con la curva tensión-deformación durante las pruebas de tracción. En comparación, la rigidez se refiere a la relación entre deformación y fuerza.
Como se muestra en la fig.
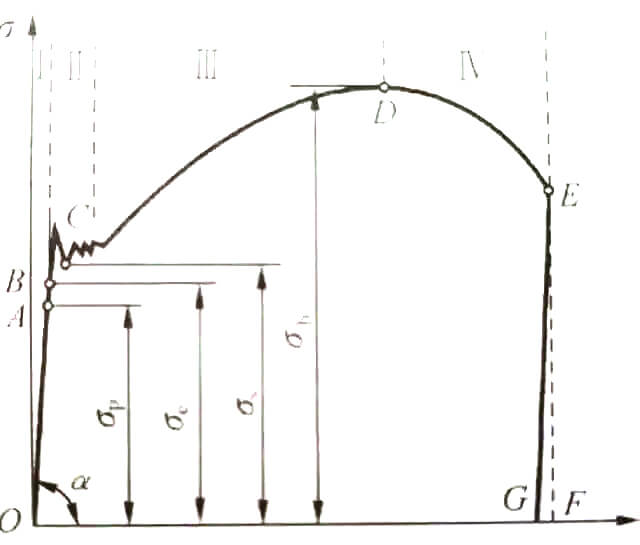
La curva de la figura se puede dividir en cuatro etapas:
1. Etapa de deformación elástica;
2. Etapa de ingreso;
3. Etapa de fortalecimiento;
4. Etapa de estrechamiento local.
La rigidez se define como la resistencia a la deformación elástica, que se produce en la fase inicial, y se rige por la ley de Hooke en condiciones elásticas.
El cálculo de la rigidez a la flexión y a la torsión bajo cargas estáticas es similar a la ley de Hooke, lo que sugiere que la rigidez sólo se mide durante la etapa de deformación elástica.
En el siguiente paso, cuando se produce deformación plástica durante el ensayo de tracción, la deformación residual no desaparece. En la curva tensión-deformación, aunque la tensión permanece casi sin cambios, la deformación aumenta significativamente. En este punto, la tensión alcanza el límite elástico y el material entra en la etapa de falla plástica. A medida que la tensión continúa aumentando, la deformación también aumenta hasta que se alcanza el límite de resistencia.
Por lo tanto, la medición de la resistencia se produce después de que el material sufre una deformación elástica y antes de alcanzar el límite de resistencia.
Envuélvelo
En conclusión, tanto la rigidez como la resistencia se evalúan durante la fase de falla de las piezas, midiendo la rigidez por tensión y la resistencia por deformación.
En términos de su orden en el proceso de deformación, la rigidez ocurre en la fase inicial, mientras que la resistencia ocurre en la fase posterior.
Por lo tanto, al evaluar las condiciones de falla de las piezas, siempre que se cumplan los requisitos de rigidez, la pieza debería poder soportar tensiones suficientes durante la etapa de deformación elástica, que a su vez debería cumplir los requisitos de resistencia.
Esta relación se refleja en varios proyectos, como el eje en equipos mecánicos. Normalmente, el tamaño del eje se determina en función de las condiciones de resistencia y luego se comprueba su rigidez en función de las condiciones de rigidez.
Por lo tanto, los requisitos de rigidez para los ejes de las máquinas de precisión son muy altos y el diseño del tamaño de su sección transversal a menudo está controlado por las condiciones de rigidez.