En los últimos años, el proceso de doblado de chapa metálica ha experimentado un rápido desarrollo en la industria del transporte ferroviario, ya que es un método de procesamiento esencial.
La precisión en los aspectos dimensionales del proceso de plegado es crucial para las empresas de procesamiento de chapa, ya que el plegado es un proceso integral de trabajo en frío.
Esta publicación utiliza el análisis teórico de piezas de chapa dobladas a 90° para deducir el método de cálculo del factor K y explica el alcance de su aplicación. Proporciona a ingenieros y técnicos de la industria de la chapa una base teórica y una referencia práctica.
Cálculo del factor K para doblar chapa metálica
En el proceso de doblado, la capa exterior de la lámina de metal está sometida a tensiones de tracción mientras que la capa interior sufre tensiones de compresión.
Entre las capas exterior e interior hay una capa de transición conocida como capa neutra, que no sufre tensiones de tracción ni de compresión.
La longitud de la capa neutra permanece constante antes y después del plegado, lo que la convierte en un factor importante a la hora de calcular el tamaño de plegado de la chapa.
La figura 1 es una ilustración esquemática de las dimensiones implicadas en el plegado de chapa metálica.
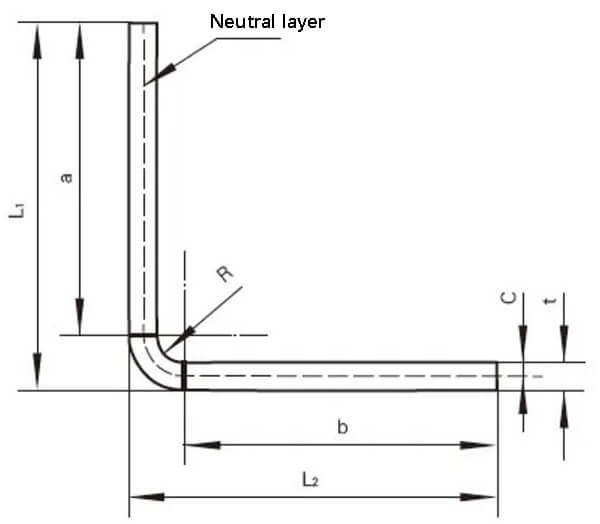
Fig. 1 Diagrama esquemático del tamaño de curvatura de la chapa.
Como se muestra en la Fig. 1, el tamaño desplegado de la lámina de metal se establece en L, por lo que hay:
l=a+b+2π(R+C)/t①
L1=a+R+t②
L2=b+R+t③
Donde factor K: 0
Derivado de las ecuaciones ① ~ ④, se puede obtener que:
K=2(L-L1-L2+2R+2t)/πt – R/t ⑤
Los resultados obtenidos en la ecuación ⑤ muestran que el valor del factor K depende de las dimensiones generales, el diámetro interno de flexión y el espesor del material de las piezas de chapa.
Cálculo manual tradicional del despliegue de chapa.
Tradicionalmente, los técnicos de chapa creaban un dibujo CAD desplegado de chapa basado en el coeficiente de flexión derivado de años de experiencia en flexión. Luego dibujarían la forma desplegada de la chapa, la exportarían en formato DXF y la insertarían en una máquina de corte por láser para obtener la forma desplegada de la pieza.
En este método tradicional de cálculo manual, el coeficiente de flexión puede variar entre diferentes instalaciones de procesamiento.
Como exemplo, considere a tampa traseira de um gabinete de energia para uma locomotiva elétrica, feita de chapa de aço laminada a frio com 1,5 mm de espessura, conforme mostrado na Figura 2. Uma planta de processamento calcularia seu tamanho de expansão da seguinte molde:
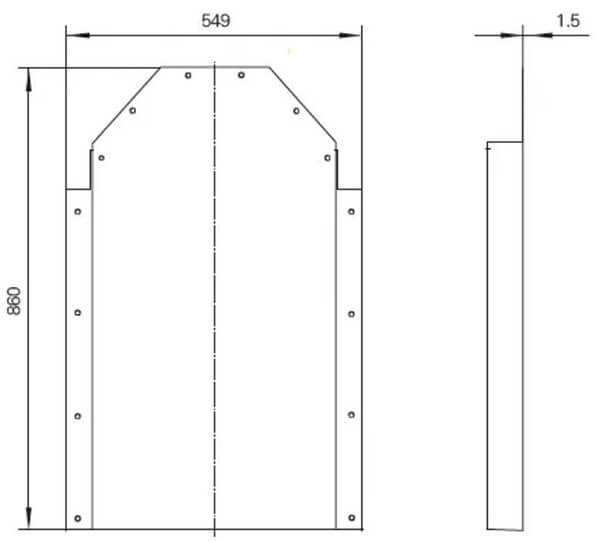
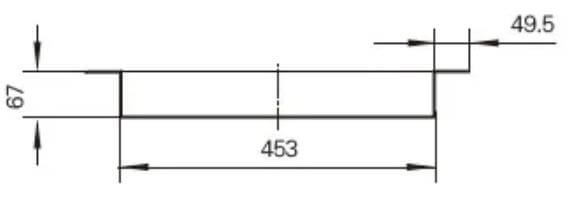
Fig. 2 Esquema dimensional de la tapa trasera de un armario de potencia
Ancho total = 453 + 67 × 2+49,5 × 2-8 × 1,5 (grosor del material) + 4 × 0,5 (factor de flexión) = 676 mm
Longitud total = 860 + 67-2 × 1,5 (grosor del material) + 0,5 (coeficiente de flexión) = 924,5 mm
Cálculo del despliegue de chapa mediante software de modelado 3D mediante el método K-Factor y su rango de aplicación.
El proceso de dibujo manual tiene baja eficiencia.
Mediante el uso de software de modelado tridimensional y el método del factor K, se mejora significativamente la eficiencia del cálculo del despliegue de chapa.
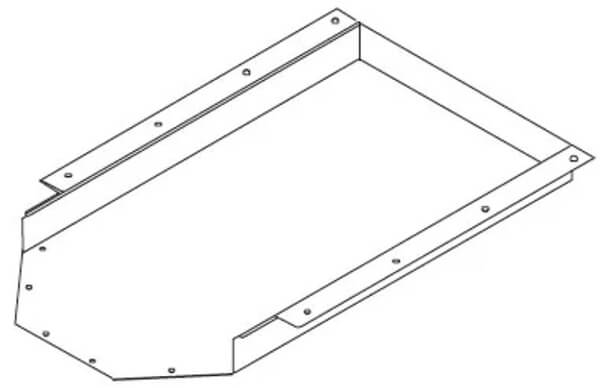
Fig. 3 Vista 3D de la tapa trasera de un armario eléctrico
Utilizando el método manual tradicional para calcular el tamaño desplegado de la chapa metálica, el tamaño desplegado y el diámetro de flexión interior se ingresan en la ecuación ⑤ para determinar el factor K correspondiente.
Durante el proceso de doblado de chapa, un diámetro de doblado interno más pequeño da como resultado una mayor compresión y tensión en las capas internas y externas del material. Si se excede el límite elástico del material, pueden ocurrir grietas y fracturas.
Por ejemplo, la cubierta trasera de un gabinete de energía para una locomotora eléctrica en la Figura 2 tiene un diámetro de curvatura interna de 1,5 mm, y el factor K correspondiente calculado usando la ecuación ⑤ es 0,486 cuando se usa software de modelado tridimensional.
De manera similar, se puede calcular el factor K para otras especificaciones de espesor.
La Tabla 1 enumera los parámetros de flexión utilizados por una empresa procesadora de chapa.
Tabla 1 Parámetros de plegado de SolidWorks
Espesor del material (mm) | factor k | Diámetro interior de flexión (mm) |
1.5 | 0,486 | 1.5 |
dos | 0,486 | dos |
3 | 0,486 | 3 |
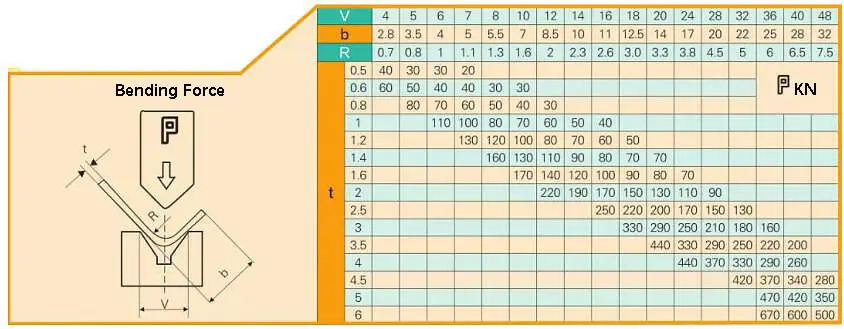
Fig. 4 Tabla de verificación rápida de la fuerza de flexión de la máquina dobladora
El resultado del cálculo del factor K se puede ingresar en el software de modelado 3D.
Sin embargo, cuando el software se utiliza para la expansión directa, pueden aparecer espacios en el dibujo ampliado, como los que se ven en los dibujos locales ampliados I y II en la Figura 5.
Estos espacios deben corregirse para cumplir con los requisitos de corte por láser, como se muestra en la Figura 6.
El software de modelado 3D también puede exportar dibujos DXF con líneas de plegado para ayudar en procesos de plegado posteriores.
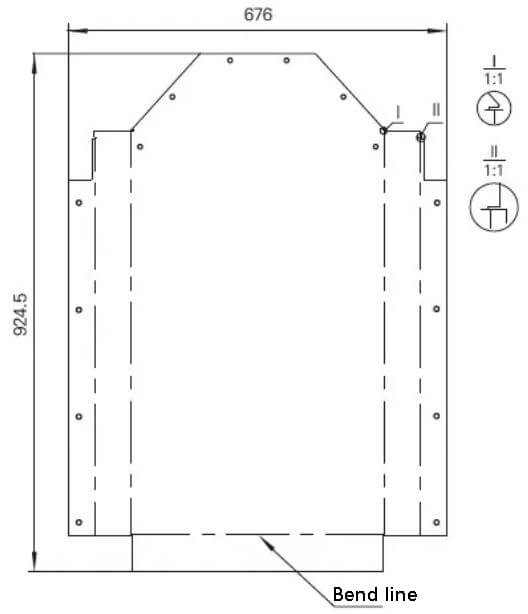
Fig. 5 Vista ampliada de la cubierta trasera del gabinete de potencia exportada directamente por el software de modelado 3D
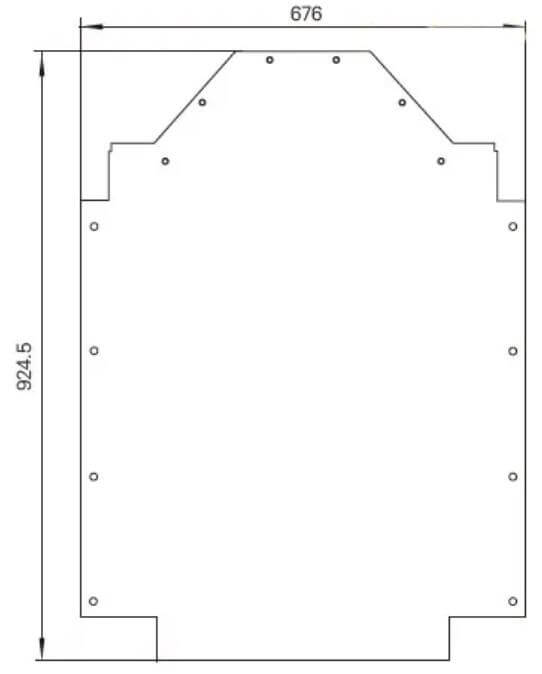
Fig. 6 Vista ampliada modificada
Análisis del proceso de plegado.
Las formas de las herramientas para doblar se muestran en la Figura 7.
Al procesar, se eligen las herramientas adecuadas en función de la forma de la pieza de trabajo.
La mayoría de empresas transformadoras disponen de una amplia gama de herramientas de plegado, especialmente aquellas con un alto nivel de especialización.
Para doblar varias piezas complejas de chapa metálica, se utilizan muchas herramientas de doblado personalizadas de diversas formas y especificaciones.
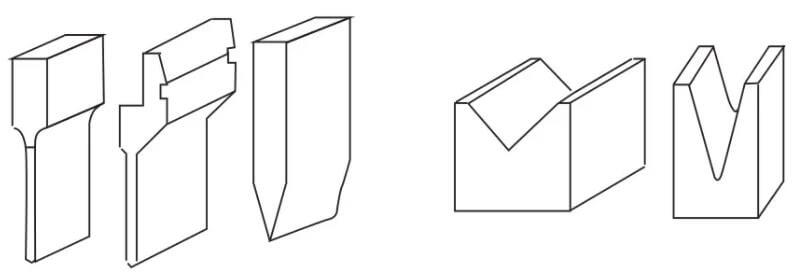
Fig.7 Herramienta para doblar
Muchos factores pueden afectar el proceso de doblado, incluido el radio del arco del troquel superior, las propiedades del material, el espesor del material, la resistencia del troquel inferior, el tamaño del troquel inferior, etc.
Para cumplir con los requisitos del producto y garantizar la seguridad de la plegadora, las empresas de procesamiento de chapa han estandarizado sus troqueles de plegado.
Es importante tener una comprensión general de las matrices de flexión disponibles durante el proceso de diseño estructural.
Como se ve en la Figura 7, el lado izquierdo representa la matriz superior y el lado derecho representa la matriz inferior.
El principio básico del doblado es utilizar la cuchilla dobladora (matriz superior) y la ranura en V (matriz inferior) de la máquina dobladora para dar forma a las piezas de chapa.
Precisión de flexión:
Un pliegue: ±0,1 mm
Dos pliegues: ±0,2 mm
Triple: ±0,3 mm
etcétera.
Conclusión
El uso del método del factor K en el software de modelado tridimensional para el cálculo del despliegue de chapa da como resultado dibujos de despliegue de alta precisión que se pueden exportar directamente. Esto elimina la necesidad de que los técnicos de despliegue de chapa rediseñen los dibujos de despliegue, mejora la eficiencia del procesamiento de las empresas de producción de chapa y acorta el ciclo de entrega.