Resumen: Se han revisado los avances técnicos recientes en la soldadura fuerte de aluminio y aleaciones de aluminio en términos de métodos de soldadura fuerte, metales de aportación y fundentes, y se han introducido sus respectivas direcciones de desarrollo.
Se observa que la soldadura fuerte de aluminio y aleaciones de aluminio es un campo de investigación en rápido desarrollo y tiene una amplia gama de aplicaciones. La tecnología de soldadura fuerte para aluminio y aleaciones de aluminio está atrayendo cada vez más atención y parece tener un potencial significativo.

1. Estado de la investigación de la soldadura fuerte de aluminio y aleaciones de aluminio.
Las aleaciones de aluminio son una opción popular en muchas industrias debido a su baja densidad, alta resistencia y excelente resistencia a la corrosión. Se utilizan ampliamente en automóviles, vehículos ferroviarios de alta velocidad y aplicaciones aeroespaciales y militares.
Lectura relacionada: Tipos de aluminio y aleaciones de aluminio
Las propiedades físicas y químicas únicas de las aleaciones de aluminio pueden provocar varias dificultades durante el proceso de soldadura, como oxidación, grietas en caliente y poros en la soldadura. El método tradicional de soldadura de aleaciones de aluminio es la soldadura por fusión, que requiere equipos complejos y soldadores altamente calificados con estrictos requisitos técnicos.
Lectura relacionada: Método de soldadura de aleación de aluminio y selección de materiales
La soldadura fuerte de aluminio es un método crucial para conectar aleaciones de aluminio y es conocida por su mínima deformación de las piezas soldadas. En los últimos años, ha ganado un uso generalizado en China debido a su alta precisión dimensional.
La tecnología de soldadura fuerte para aluminio y aleaciones de aluminio ha sido objeto de extensas investigaciones en los últimos años, lo que ha dado lugar a rápidos avances en métodos de soldadura fuerte, metales de aportación y fundentes.
La soldadura fuerte de aluminio y aleaciones de aluminio es un campo en rápido desarrollo debido a sus excelentes propiedades, como alta resistencia, buena resistencia a la corrosión, alta conductividad y conductividad térmica. Como resultado, se utiliza cada vez más en una variedad de industrias, incluidas la aeroespacial, la aviación, la electrónica, la metalurgia, la fabricación de maquinaria y la industria ligera.
En algunos casos, el uso del aluminio ha sustituido al cobre y al acero, impulsado por el aumento sustancial del coste de los materiales de cobre y el deseo de reducir el peso, mejorar la eficiencia y mejorar la estética. Un ejemplo de esto es la sustitución del tanque de agua de cobre en los automóviles por un tanque de agua de aluminio.
En China, sólo hay unos pocos fabricantes de fundente de aluminio a gran escala, y la mayor parte del fundente de aluminio utilizado se importa del extranjero.
El aluminio y las aleaciones de aluminio tienen un punto de fusión bajo, una fuerte reactividad química y un punto de fusión alto, lo que dificulta el uso de fundentes para soldadura fuerte tradicionales. Por lo tanto, se deben utilizar fundentes de soldadura especiales para aluminio y aleaciones de aluminio para garantizar una soldadura fuerte adecuada.
Además, la resistencia a la corrosión de las uniones soldadas de aluminio y aleaciones de aluminio puede verse fácilmente comprometida por el uso de soldadura y fundente. Esto se debe a que existe una diferencia significativa en el potencial del electrodo entre la soldadura y el metal base, lo que reduce la resistencia a la corrosión de la unión, especialmente en el caso de uniones soldadas blandas.
La mayoría de los fundentes utilizados para eliminar la película de óxido de la superficie del aluminio y sus aleaciones contienen materiales altamente corrosivos. Incluso si estos materiales se limpian después de la soldadura fuerte, es un desafío eliminar por completo su impacto en la resistencia a la corrosión de la unión.
2. Método de soldadura fuerte
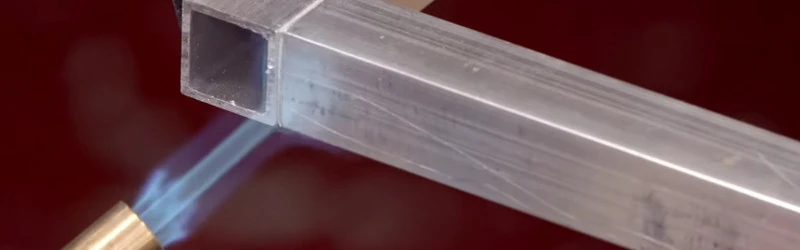
El aluminio y las aleaciones de aluminio se pueden soldar mediante soldadura fuerte por llama, soldadura fuerte en horno o soldadura fuerte en baño de sal.
La soldadura fuerte con llama es un método popular debido a su equipo simple, versatilidad en términos de fuente de gas y amplia gama de aplicaciones. Se utiliza principalmente para soldar componentes pequeños y para producir piezas individuales. Hay muchos tipos de llamas disponibles, incluido un nuevo tipo de gas llamado gas Sharp, que es el resultado de la cooperación entre China y otros países. Este gas tiene una llama suave y es una buena fuente de calor para soldar aluminio, ya que se encuentra entre las potencias del gas licuado y el oxiacetileno. Sin embargo, en comparación con otros métodos de conexión, la temperatura de calentamiento para la soldadura fuerte con llama de aluminio y aleaciones de aluminio es difícil de controlar, lo que requiere mayores niveles de experiencia del operador.
La soldadura fuerte en baño de sal ofrece un calentamiento rápido y uniforme, una deformación mínima de los componentes y una eliminación eficaz de la película, lo que da como resultado componentes soldados de alta calidad con una alta eficiencia de producción. Este método es especialmente adecuado para la producción en masa y para soldar estructuras densas. La pasta de soldadura, la lámina de soldadura o el recubrimiento de soldadura se utilizan comúnmente para la soldadura fuerte de aluminio en baño de sal. El revestimiento de soldadura suele estar compuesto de composiciones eutécticas de AlSi o hipoeutéticas de AlSi.
En la actualidad, la producción de soldadura fuerte utiliza principalmente revestimiento de metal de aportación, lo que puede mejorar la eficiencia de la producción y garantizar la calidad de los componentes soldados.

La soldadura fuerte tiene algunas limitaciones:
En primer lugar, el diseño complejo de algunos componentes puede dificultar el acceso al baño de sal, limitando las opciones de diseño y complicando el proceso de soldadura fuerte. Esto también puede dificultar la garantía de la calidad de la soldadura fuerte.
En segundo lugar, aunque la soldadura fuerte en baño de sal puede cumplir estrictos requisitos de resistencia a la corrosión, puede generar una gran cantidad de residuos de fundente en el componente, lo que requiere una limpieza exhaustiva. Además, el equipo de soldadura fuerte en baño de sal es caro y el proceso complejo, lo que lleva a un ciclo de producción largo.
La soldadura fuerte en horno de aire ofrece una inversión en equipos de bajo costo y un proceso de soldadura simple y fácil de administrar. Sin embargo, el proceso de calentamiento es lento y la superficie del componente puede oxidarse cuando se expone al aire, especialmente a altas temperaturas. Esto dificulta la eliminación de la película de fundente y el fundente también puede fallar debido a la humedad en el aire durante el calentamiento.
Para superar estos desafíos, se desarrollaron la soldadura fuerte en hornos de aire seco y la soldadura fuerte al vacío en una atmósfera protectora, que obtuvieron un uso generalizado en la soldadura fuerte de aluminio y aleaciones de aluminio. Estos métodos ofrecen procesos mejorados y han experimentado un rápido crecimiento en los últimos años.
2.1 Soldadura al vacío

Se sabe que el aluminio es activo y forma fácilmente una densa película de óxido en su superficie.
Durante el proceso de soldadura fuerte, puede resultar complicado eliminar los óxidos únicamente mediante condiciones de vacío. Por ello se deben utilizar activadores metálicos como Mg y Bi.
Es ampliamente aceptado que el mecanismo de eliminación del activador funciona de la siguiente manera:
En primer lugar, el activador reacciona con el O y el HO residuales en vacío, neutralizando sus efectos nocivos sobre la soldadura fuerte del aluminio.
En segundo lugar, el vapor de Mg penetra la capa de material debajo de la película y forma una aleación de AlSiMg de bajo punto de fusión junto con Si difundido.
Durante la soldadura fuerte, la fusión de la aleación rompe la unión entre la película de óxido y el material base, lo que permite que la soldadura fundida humedezca el material base, se extienda sobre él debajo de la película y levante la película de óxido de la superficie, eliminándola de manera efectiva.
Al soldar aleaciones de aluminio al vacío, el horno de vacío debe elegirse en función de factores como la productividad, el costo, el tamaño de la soldadura y la estructura.
Es importante limpiar minuciosamente la pieza soldada antes de soldar. El óxido de la superficie se puede eliminar con ácido o álcali y las manchas de aceite se pueden eliminar con alcohol.
Para preparar el metal de aportación, a menudo se utiliza papel de lija para eliminar la película de óxido de la superficie, seguido de una limpieza con alcohol para eliminar las manchas de aceite.
Para piezas más grandes, se recomienda precalentar antes de soldar para garantizar un calentamiento uniforme de todas las piezas antes de alcanzar la temperatura de soldadura.
La soldadura fuerte al vacío de aleaciones de aluminio depende en gran medida del activador de Mg para eliminar la película de óxido. Para garantizar que el metal base esté completamente expuesto al vapor de Mg en la soldadura con estructuras complejas, algunas unidades nacionales han adoptado medidas complementarias, como el blindaje local, lo que resulta en una mejor calidad de la soldadura fuerte.
Un método común es colocar la pieza dentro de una tapa de acero inoxidable con virutas de Mg y luego en el horno de soldadura al vacío para soldar. Esto puede mejorar significativamente la calidad de la soldadura fuerte.
El grado de vacío es el parámetro de proceso más crucial y desafiante de controlar en la soldadura fuerte al vacío. Para obtener uniones de alta calidad, el grado de vacío depende en gran medida del tamaño de la pieza de trabajo.
Según los años de experiencia de algunos expertos, se recomienda que si el equipo de soldadura fuerte no se ha utilizado durante un período prolongado, el horno de vacío debe funcionar durante varias horas antes de su uso. En el uso regular, especialmente para la producción por lotes, se recomienda mantener el intervalo de tiempo entre usos lo más corto posible para garantizar que el grado de vacío del horno de vacío cumpla con los requisitos de manera fácil y rápida.
Aunque la soldadura fuerte al vacío es un método de soldadura eficaz, también tiene algunas limitaciones, como equipos complejos y costosos y la dificultad de mantener el sistema de vacío.
2.2 Soldadura fuerte en atmósfera protectora

El uso de la soldadura fuerte al vacío de aluminio es limitado debido al costoso equipo y la compleja tecnología involucrada. Para solucionar este problema, una atmósfera neutra puede sustituir al vacío. Esto reduce los requisitos de tasa de fugas del sistema y complejidad del equipo. Además, reduce los problemas de mantenimiento de los equipos provocados por la deposición de elementos volátiles, lo que se traduce en menores costes de producción.
El calentamiento en este método se logra principalmente mediante corriente y es rápido y uniforme. Esto no sólo garantiza la calidad del producto sino que también mejora la productividad.
La soldadura fuerte de aluminio con protección de gas neutro ha ganado cada vez más atención y ha experimentado un rápido desarrollo en los últimos años. Se considera un método prometedor de soldadura fuerte de aluminio.
El mecanismo de eliminación de la película para la soldadura fuerte de aleaciones de aluminio con protección gaseosa es similar al de la soldadura fuerte de aluminio al vacío y se lleva a cabo principalmente utilizando un activador de Mg. La calidad de la soldadura fuerte se puede mejorar agregando Bi al metal de aportación.
El argón y el nitrógeno puros, con una pureza superior al 99,99%, se utilizan comúnmente como atmósfera para la soldadura fuerte de aleaciones de aluminio con protección gaseosa.
Para uniones Al/Al y Al/Cu, se ha informado que un método de unión eficaz es utilizar el principio de soldadura fuerte por difusión. Se rocía un polvo mixto compuesto de fundente para soldadura fuerte de fluoruro de potasio y aluminio sobre la superficie del aluminio en una atmósfera de nitrógeno cercana a la presión atmosférica para la soldadura fuerte. El Si puede sustituirse por otros metales eutécticos de bajo punto de fusión, como Cu, Ge o Zn, que se forman con Al.
3. Soldadura

Durante la soldadura fuerte, la conexión entre las soldaduras se realiza mediante la solidificación de la soldadura fundida. Como resultado, la calidad de la soldadura depende en gran medida del metal de aportación utilizado.
El principal metal de aportación del aluminio es la aleación Al Si, pero a veces se añaden Cu, Zn, Ge y otros elementos para mejorar el rendimiento del proceso.
Con años de experiencia y experimentación, se han desarrollado varias series de metales de aporte para soldadura fuerte de aluminio, muchos de los cuales han producido resultados satisfactorios con los procesos correctos.
A continuación, presentaremos algunos de los metales de aportación para soldadura fuerte de aleaciones de aluminio más utilizados.
3.1 Soldadura Al Si
Las soldaduras de la serie Al Si se basan en la composición eutéctica de Al Si y también incluyen aleaciones hipoeutécticas, hipereutécticas y Al Si con un máximo de 5% de elementos añadidos. Estas soldaduras son altamente soldables, fuertes, tienen un color y brillo similares al metal base, ofrecen resistencia al enchapado y a la corrosión y se consideran una buena opción para soldar.
Además, esta serie de soldaduras se puede modificar, lo que mejora significativamente su resistencia y comportamiento a flexión en uniones soldadas.
Recientemente, se desarrolló un nuevo tipo de metal de aportación para soldadura fuerte de aleación de Al Si utilizando tecnología de solidificación rápida. Este metal de aportación para soldadura fuerte tiene un punto de fase líquida más bajo, de alrededor de 3-5 °C, en comparación con los metales de aportación para soldadura fuerte cristalinos comunes de la misma composición. Su coeficiente de humectabilidad aumentó un 18% y su resistencia aumentó un 28,4%. Sus fluctuaciones también son mínimas, lo que proporciona cierto grado de flexibilidad de procesamiento.
3.2 Soldadura de cobre
La soldadura de cobre se realiza según el principio de soldadura fuerte reactiva por contacto. Actualmente, la soldadura fuerte reactiva por contacto de aluminio se considera la solución ideal a los problemas de soldadura fuerte del aluminio.
Este método ofrece varios beneficios, que incluyen:
① No requiere fundente, lo que lo hace respetuoso con el medio ambiente y evita la contaminación de los productos de soldadura. No es necesario limpiar los productos soldados y no se produce corrosión química en la costura de soldadura.
② La selección de una capa de aleación reactiva eutéctica adecuada puede reducir la temperatura de soldadura, reduciendo el consumo de energía, haciendo que el proceso de soldadura sea más fácil de controlar y con bajos requisitos de equipo.
La reacción de contacto del Cu sobre el sustrato de aluminio muestra una notable dispersión superficial preferencial, alterando la película de óxido y promoviendo la formación de una capa uniforme de relleno en fase líquida entre las interfaces de las juntas en el proceso de soldadura reactiva por contacto. Por otro lado, la frontera de grano con reacción de contacto en la dirección de la profundidad de la matriz de aluminio penetra preferentemente, garantizando la fuerza de unión de la unión soldada.
Los datos muestran que los parámetros de proceso apropiados para la soldadura fuerte por contacto reactivo de aluminio con Cu como material de capa intermedia son una temperatura de soldadura fuerte de 570-580°C y un tiempo de mantenimiento de 15-20 minutos. Sin embargo, la resistencia a la corrosión electroquímica de las uniones soldadas de Cu es pobre y la capa de reacción eutéctica es frágil.
Para mejorar las prestaciones del Cu como metal de aportación se pueden añadir otros elementos como Ag, Ni, Si, Zn, Ti, etc. El metal de aportación para soldadura reactiva con aleaciones de aluminio incluye estos elementos.
3.3 Capa compuesta de cobre y zinc como metal de aportación reactivo
Para solucionar las limitaciones de utilizar Zn y Cu como metales de aportación por separado, se puede utilizar una capa compuesta por ambos. La soldadura fuerte por reacción eutéctica de contacto se realiza utilizando la capa compuesta de Cu y Zn.
Se produce una reacción peritéctica en la interfaz Cu/Zn, mientras que se produce una reacción eutéctica en la interfaz Cu/Al, formando una fase líquida eutéctica que rompe la película de óxido sobre la superficie del aluminio.
Cuando se utiliza Cu y Zn como metal de aportación reactivo para la soldadura fuerte de aluminio, el contenido adecuado de ambos metales en la capa compuesta es crucial. Se ha sugerido que los mejores resultados de soldadura fuerte se logran cuando el espesor de la capa de Zn es de 0,2 mm y el espesor de la capa de Cu es inferior a 0,1 mm.
En este punto, la capa de reacción no sólo rompe la película de óxido, sino que también proporciona una fuerte resistencia a la corrosión electroquímica y una alta resistencia al corte.
3.4 Soldadura Al Si Cu Zn
El rango de temperatura del punto de fase líquida de soldadura está entre 500 y 577 °C. Cuando se agrega Cu a la soldadura de Al Si, su fluidez mejora enormemente.
Sin embargo, debido al alto contenido de compuesto intermetálico CuAl2, esta soldadura eutéctica ternaria es muy frágil y sólo es adecuada para moldeo en tiras, lo que dificulta su procesamiento en forma de alambre o lámina.
Agregar Zn al metal de aportación Al Si aumenta su humectabilidad y fluidez. A medida que aumenta la concentración de Zn, la solubilidad del Si disminuye rápidamente. Dado que no hay compuestos en el metal de aportación, su trabajabilidad en caliente es mejor en comparación con el sistema Al Si Cu.
Soldadura serie 3.5 Al Cu Ag Zn
El rango de temperatura de la soldadura en fase líquida es de 400 a 500 °C, que está cerca del rango de la soldadura de aleación de aluminio. La composición eutéctica ternaria Al Cu Ag le da al metal de aportación un color muy parecido al del metal base Al.
Este metal de aportación tiene buena fluidez pero es relativamente frágil. Otro sistema ternario es el metal de aportación Al Cu Zn, que también tiene un color similar al del metal base y puede producir mejores piezas mecanizadas.
Agregar 0,05% – 0,08% (en masa) de Mg, 0,05% Ni o 0,05% Cr al metal de aportación puede mejorar su resistencia a la corrosión.
Hay muchos otros metales de aportación ideales para el aluminio, pero en general, la mayoría de los metales de aportación para soldadura fuerte de aluminio existentes tienen un punto de fusión cercano al de las aleaciones de aluminio.
Como resultado, es un desafío para la mayoría de los trabajadores de soldadura encontrar un metal de aportación con un punto de fusión más bajo y mejor rendimiento tecnológico.
4. Fundente para aluminio

El aluminio es relativamente activo y su superficie forma fácilmente una capa de óxido densa y químicamente estable, lo que constituye un obstáculo importante en la soldadura fuerte de aluminio y aleaciones de aluminio. Para obtener juntas de alta calidad, se debe eliminar el óxido de la superficie.
Al soldar aluminio y sus aleaciones, el uso de un fundente para soldadura fuerte puede eliminar la película de óxido de la superficie del aluminio y reducir la tensión interfacial entre el metal de aportación y el metal base.
El fundente para soldadura fuerte para aluminio se divide en fundente para soldadura blanda y fundente para soldadura fuerte; este último se utiliza para temperaturas de soldadura por encima de 450 °C y el primero para temperaturas inferiores a 450 °C.
A continuación se presenta el fundente para soldadura fuerte de aluminio Nocolok de rápido desarrollo. El fundente para soldadura fuerte de aluminio tradicional es principalmente fundente para soldadura fuerte con sal de cloro, generalmente basado en el sistema LiCl-KCl o LiCl-KCl-NaCl. Este fundente tiene las ventajas de una alta actividad, estabilidad durante el calentamiento y no pierde fácilmente su eficacia. Se puede utilizar con una variedad de fuentes de calefacción, lo que lo hace conveniente y económico.
Sin embargo, la desventaja de este fundente es que la presencia de iones Cl provoca una fuerte corrosión electroquímica en el metal base, tiene una fuerte absorción de humedad y es difícil de conservar.
Por lo tanto, es fundamental limpiar los residuos al utilizar este tipo de fundentes para soldadura fuerte.
A finales de la década de 1970, estaba en marcha el desarrollo de un fundente de soldadura fuerte insoluble y no corrosivo. Este fundente se sintetiza utilizando el eutéctico A-KF y su solubilidad en agua es mínima.
Evita la desventaja del fundente de cloruro, que absorbe fácilmente la humedad y tiene muy poca corrosividad, de ahí su apodo de fundente Nocolok.
4.1 Propiedades de flujo
El fundente Nocolok es un polvo blanco fino, compuesto principalmente por una mezcla de fluoaluminato de potasio que puede contener agua cristalina.
El fundente fundido disuelve los óxidos de la superficie del aluminio y evita la reoxidación. Bajo la influencia del flujo, el metal de aportación penetra libremente en la superficie de la junta mediante acción capilar.
Después de enfriar, el fundente forma una película pastosa con una fuerte adherencia sobre la superficie del componente. La capa de fundente residual no es higroscópica, no corrosiva e insoluble en disolventes acuosos.
Aunque la solubilidad del fundente de fluoaluminato de potasio en agua es mínima, su estabilidad térmica no es fuerte y se producirán reacciones químicas cuando se caliente al aire.
4.2 Mejora y mayor progreso del flujo de Nocolok
En los últimos años, muchos estudios se han centrado en mejorar el método Nocolok de dos maneras principales: agregando sales adicionales a la corriente de fluoaluminato de potasio para aumentar su actividad y otras propiedades, y desarrollando nuevos métodos para usar la corriente de fluoaluminato de potasio.
El Si puede aumentar la actividad de flujo del fluoaluminato de potasio.
Lo ideal es añadirlo en forma de K 2 SiF 6 pero hay que calcular el valor del exceso de KF.
Cuando W(Si) > 2%, puede perforar automáticamente.
Añadiendo K 2 GeF 6 SnF 2 ZnF 2 etc. puede mejorar la actividad del flujo, especialmente K 2 GeF 6 .
Para mejorar Nocolok, alguien mezcló polvo de metal de aportación con este tipo de fundente.
Otros consideran KAlF 4 como un método de soldadura fuerte en fase gaseosa:
Una es mezclar directamente vapor KAlF 4 en una atmósfera libre de oxígeno a baja presión para soldar aleaciones de aluminio;
La otra es depositar al vacío una capa de KA1F 4 en el exterior de las piezas de aluminio, luego ensamblar y soldar nuevamente según sea necesario.
La soldadura compuesta formada depositando una capa de fundente KAlF 4 sobre la superficie del polvo de soldadura eutéctica Al Si se puede mezclar con pasta de soldadura con disolvente orgánico.
5. Conclusión
La soldadura fuerte de aluminio y aleaciones de aluminio ha sido ampliamente estudiada y rápidamente desarrollada en los últimos años.
Académicos extranjeros demostraron la excepcional fuerza de unión de la soldadura eutéctica Sn-Zn (8,9%) al soldar aleaciones de aluminio por debajo de 350°C, investigando la reacción de interfaz entre la aleación eutéctica Sn-Zn en fase líquida y Al.
La soldadura fuerte por difusión de aluminio también ha recibido considerable atención en los últimos años.
Un enfoque implica rociar un polvo mixto compuesto de Si y fluoruro de potasio y aluminio sobre la superficie de Al y soldar en una atmósfera de N2 cerca de la presión atmosférica.
Entre los materiales utilizados, el Si puede ser sustituido por Cu, Ge, Zn y otros metales que forman eutécticos de bajo punto de fusión con el aluminio.
Este método se puede utilizar para soldar uniones Al/Al, Al/Cu, Cu/Cu y Cu/latón.
La soldadura fuerte por difusión también se utiliza para soldar piezas fundidas de aleaciones de Al-Si, resolviendo el problema de la corrosión y la mala humectación de las piezas fundidas de aleaciones de Al en soldadura fundida.
Todavía queda mucho por hacer en la tecnología de soldadura fuerte del aluminio y las aleaciones de aluminio, y algunos avances ya se han aplicado a la producción práctica.
La aplicación de la tecnología de soldadura fuerte de aluminio y aleaciones de aluminio se centra principalmente en radiadores de aluminio, no materiales de aluminio y acero inoxidable, marcos de puertas de microondas de aleación de aluminio y otros productos.
Otro campo de investigación y aplicación es la soldadura fuerte de fondos de cacerolas compuestos de aluminio y acero inoxidable.
Aunque la soldadura fuerte de aluminio y aleaciones de aluminio es una excelente tecnología de unión, todavía quedan muchos desafíos por enfrentar.