En la actualidad, la aplicación de la soldadura láser en el desarrollo de piezas estampadas de carrocerías de automóviles se refleja principalmente en la soldadura de placas por láser.
Esto permite que diferentes materiales, espesores y revestimientos de acero formen una única unidad de material, satisfaciendo mejor los requisitos de las diferentes piezas en cuanto a las propiedades del material.
Con un peso más ligero, una estructura ideal y un mejor rendimiento, la carrocería puede ser más ligera y los costos pueden reducirse mediante la promoción y la aplicación.
Al mismo tiempo, también reduce los costos de investigación y desarrollo de matrices de estampado para automóviles, diseño y análisis de procesos de fabricación.
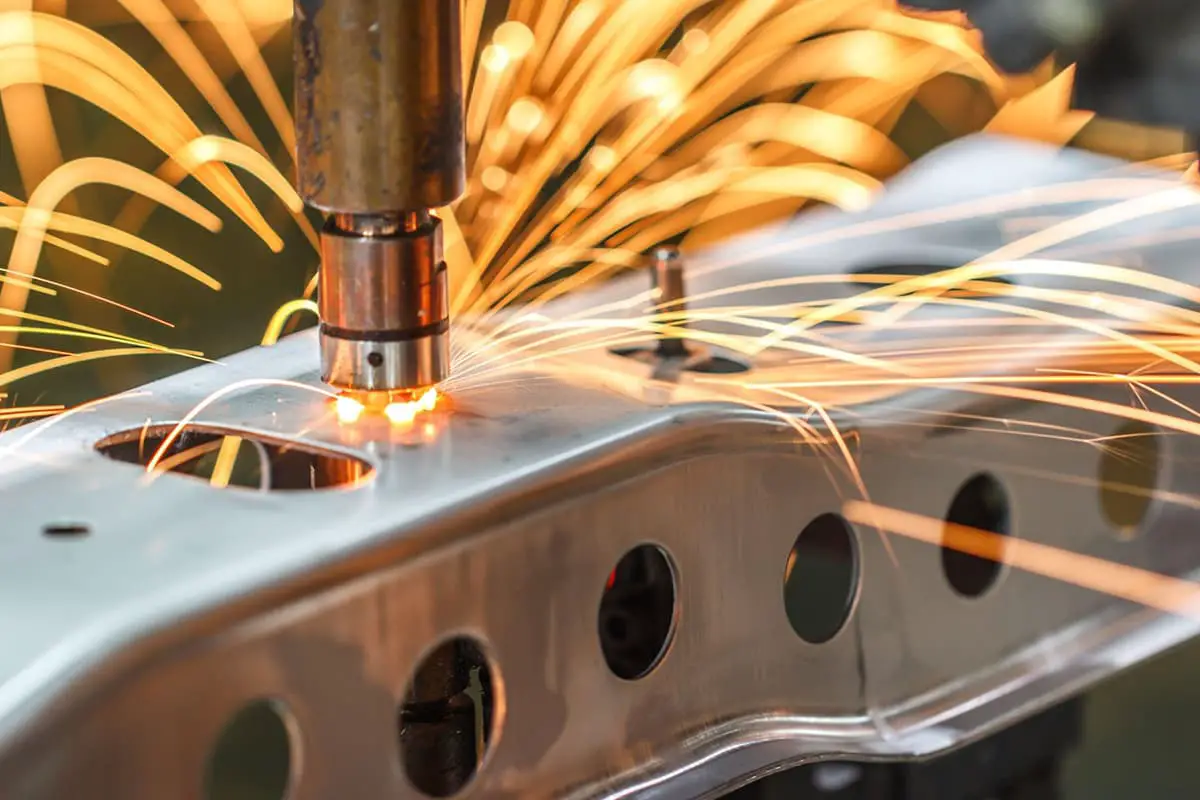
Ventajas de la soldadura láser
La soldadura por láser es un tipo de soldadura por fusión que completa la soldadura de la unión mediante un haz de energía láser. El calor generado por la soldadura se puede minimizar, la zona afectada por el calor es pequeña y la deformación térmica es mínima.
Estas ventajas determinan su importancia en la producción de piezas estampadas para automóviles. Los requisitos de planitud de la placa durante la producción de piezas estampadas para automóviles son muy altos y la deformación por soldadura de la placa de soldadura láser puede satisfacer las necesidades de producción de piezas estampadas.
Las piezas estampadas se forman directamente mediante el proceso de torneado de bordes durante la producción, por lo que los requisitos de planitud de la placa son mayores.
Al mismo tiempo, los requisitos de calidad del suministro de placas de soldadura láser serán mayores. Para reducir la deformación de la chapa y mejorar la eficiencia de la producción, las acerías generalmente adoptan un método de soldadura primero y corte después.
Esto reduce la deformación causada por la soldadura, evitando problemas de calidad como mala fusión en la junta soldada, pérdida de soldaduras y grietas en las costuras.
La aplicación de la soldadura láser a componentes estructurales de automoción.
Tomando como ejemplo algunas de las piezas internas de láminas soldadas con láser comúnmente utilizadas, como la viga transversal del techo, la lámina de refuerzo interior del paso de rueda y la placa de refuerzo frontal, se utilizan láminas delgadas y gruesas para la soldadura láser para cumplir con la resistencia a las demandas de la carrocería.
La Figura 1 muestra una parte soldada con láser de un travesaño de techo de un modelo específico, que consta de láminas del mismo grado, 210P1, pero con espesores variables, siendo la lámina más gruesa de 1,0 mm y la más delgada de 0, ,7 mm.

Figura 2: Refuerzo del panel interno soldado con láser para la calota de un modelo determinado, con espesores variables, con clases de placa idénticas HC260YD+Z-50/50-M. La placa más gruesa mide 1,0 mm, mientras que la más delgada mide 0,8 mm.
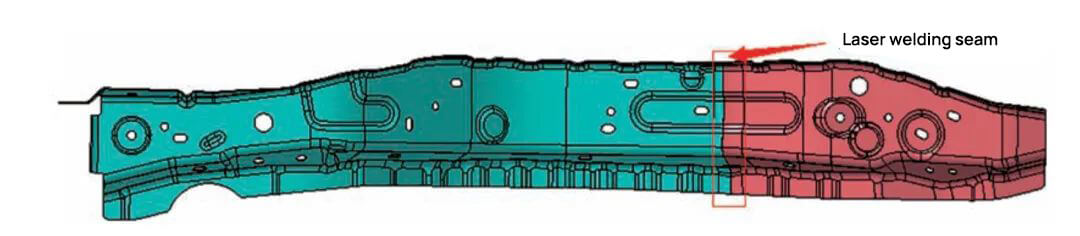
Figura 3: Panel de refuerzo soldado por láser para el bastidor delantero de un modelo de vehículo concreto, formado por láminas de distintos espesores pero del mismo tipo de material, HC420/780DP. La lámina más gruesa es de 2,0 mm, mientras que la más delgada es de 0,8 mm.
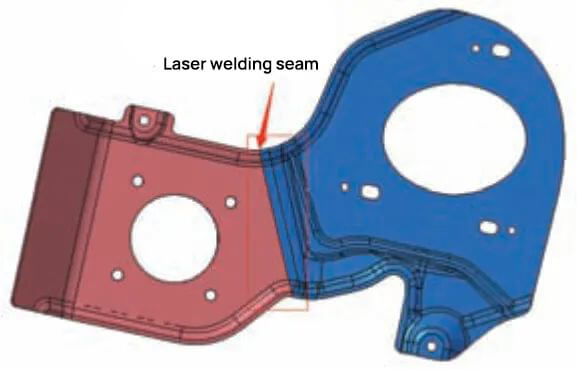
Superar desafíos en la placa de refuerzo frontal para un modelo de automóvil determinado
La aplicación de placas soldadas con láser aumentó la precisión de todo el guardabarros, la moldura delantera y la tapa superior del vehículo, lo que permitió realizar ajustes que ahorraron tiempo en todo el vehículo y redujeron los costos de mano de obra.
Sin embargo, este esquema de producción trae dificultades significativas para el desarrollo del molde, especialmente para la placa de refuerzo frontal que se muestra en la Figura 3.
La placa presenta una variación sustancial de espesor y el retorno elástico de la pieza durante el procesamiento es grande, según análisis técnicos.
Esto requiere un alto nivel de análisis de ingeniería asistida por computadora (CAE) durante el proceso de diseño, así como altas exigencias en las técnicas de compensación de recuperación elástica de los diseñadores.
Durante el desarrollo de esta pieza, frecuentemente ocurren problemas como mala formación del ángulo R, resistencia insuficiente en áreas de placas delgadas y deformación del conjunto soldado.
Solución 1: Con base en los problemas encontrados durante el proceso de producción, se llevó a cabo un análisis de compensación del proceso específico y se implementó la compensación elástica en las primeras etapas de desarrollo.
Solución 2: La Figura 4 representa el análisis de compensación de retroalimentación del resorte de estampado de espesor desigual para el conjunto soldado con láser de placa de refuerzo frontal de un determinado modelo de automóvil que se muestra en la Figura 3.
La parte gris de la pieza representa la superficie que requiere compensación de recuperación elástica.
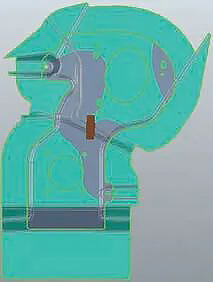
Una vez completada la compensación del rebote, la pieza de producción puede alcanzar la precisión requerida.
Sin embargo, la zona de la placa delgada se enfrenta a problemas de voladizo y resistencia insuficiente debido a la falta de nervaduras de refuerzo.
El problema de deformación de la soldadura causado por la diferencia de espesor entre las placas delgadas y gruesas que excede el espesor de la placa delgada requiere soluciones adicionales.
Pregunta clave 3: La Figura 5 representa los puntos de datos de coordenadas para la discrepancia en la superficie de una sola pieza debido a la deformación de la soldadura del conjunto soldado con láser de la placa de refuerzo del panel frontal para un modelo de vehículo determinado que se muestra en la Figura 3.
Se realizó una corrección de diferencias paralelas para el área dentro del círculo rojo en la Figura 5.
La conclusión final de la corrección es un rango de diferencia de superficie de -0,5 a 0, que puede cumplir con los requisitos del ensamblaje de soldadura y resolver el problema de deformación de la soldadura.
Este problema requiere una investigación de soldadura por arco manual en el molde para realizar la compensación de rebote para la producción de piezas.

Resumen: A través de los procesos clave de solución de problemas anteriores, esta pieza ahora cumple con los requisitos de soldadura de producción en masa y ha resuelto los problemas de deformación en la soldadura de ensamblaje.
Al mismo tiempo, nos proporciona nuevos enfoques de desarrollo y orientación de mejora técnica para el desarrollo futuro de productos, lo que ayuda a mejorar la calidad del desarrollo de piezas estampadas y reducir los costos de desarrollo de moldes.
Aporta beneficios de reducción de costes, mejora de la eficiencia y optimización de procesos a los fabricantes de moldes y proveedores de componentes, al tiempo que realiza una contribución significativa a la protección del medio ambiente.
Desarrollo futuro de la soldadura láser personalizada
La soldadura láser hecha a medida tiene un valor económico sustancial y ofrece un gran atractivo para los fabricantes de automóviles.
Sin embargo, también presenta desafíos más importantes para el desarrollo de piezas estampadas, ya que requiere mayores requisitos en cuanto a análisis CAE preliminar, diseño de procesos y capacidades del personal técnico.
En el futuro, la soldadura láser se aplicará a la soldadura de carrocerías de automóviles y evolucionará para incluir métodos de soldadura más energéticos para adaptarse a diferentes escenarios y requisitos ambientales.
Al reducir los costos de desarrollo de moldes y los costos de inversión para los desarrolladores de automóviles, se crea más valor económico para los fabricantes de automóviles.
Conclusión
(1) La tecnología de soldadura por fusión por láser contribuye a reducir el costo del desarrollo de piezas estampadas y del desarrollo de matrices.
(2) La soldadura por fusión por láser también ayuda a mejorar la competencia técnica de los ingenieros de desarrollo en el análisis CAE de la recuperación elástica de piezas.
(3) La soldadura láser también ayuda a reducir el peso de la carrocería del vehículo y los costos generales de desarrollo, mejorando las condiciones de ensamblaje del vehículo y reduciendo la deformación causada por la soldadura extensa.