1. Prefacio
Este artículo analiza el impacto de la concentración de carbono en la superficie en las propiedades del tratamiento térmico del acero 20CrMo.
Para garantizar el contenido de carbono deseado en la atmósfera del horno durante todo el proceso de cementación y la concentración de carbono requerida en la superficie de la pieza después de la cementación, la concentración de carbono en el proceso de cementación debe regularse meticulosamente. Además, optimizar el proceso de enfriamiento puede ayudar a lograr una mejor dureza de enfriamiento, lo que resulta en una buena resistencia al desgaste.
El acero 20CrMo es un acero estructural al carbono de baja aleación que se utiliza ampliamente en la producción de una variedad de piezas de trabajo, como engranajes, ejes y sujetadores de alta resistencia. Por ejemplo, en la producción de una empresa, este material se utiliza en la construcción del cilindro hidráulico de la trituradora hidráulica en máquinas de construcción.
Para que el cilindro hidráulico cumpliera con la alta dureza y resistencia al desgaste requeridas por el tratamiento térmico post-carburación, así como con buena plasticidad y tenacidad (es decir, excelentes propiedades mecánicas integrales), fue necesaria una investigación específica.
Sin embargo, durante la producción inicial del cilindro hidráulico, la dureza superficial de la pieza era baja y este problema persistió a pesar de los esfuerzos por corregirlo ajustando las condiciones del proceso. Como resultado, se llevó a cabo un estudio centrado en la pieza de trabajo.
2. Proceso de tratamiento térmico, requisitos técnicos y problemas del cilindro hidráulico.
Este tipo de cilindro hidráulico tiene un gran volumen, con un peso unitario de aproximadamente 365 kg y un espesor efectivo de 150-200 mm.
Consulte la Figura 1 para obtener una representación visual de la pieza de trabajo real.
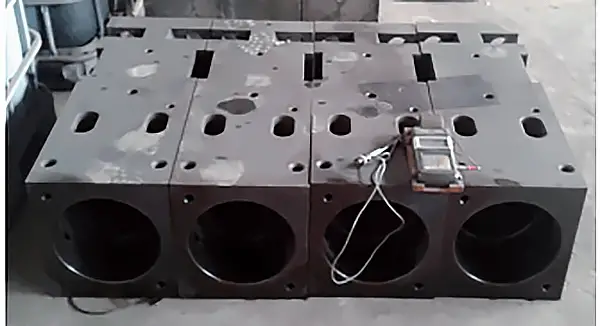
Después de someterse a tratamiento térmico, cementación y enfriamiento, la pieza de trabajo debe tener una profundidad de capa de cementación de 1,0 a 1,4 mm y una dureza total de 58 a 62 HRC.
Consulte la Tabla 1 para conocer las especificaciones de composición química del acero 20CrMo en acero estructural de aleación GB/T 3077-1999.
Tabla 1 Composición química del acero 20CrMo (fracción de masa) (%)
W. | Minnesota | Sí | cr | Mes | PAG | s |
0,17~0,24 | 0,4 ~ 0,7 | 0,17~0,37 | 0,80~1,10 | 0,15~0,25 | ≤0,035 | ≤0,035 |
Se utilizan varios métodos de proceso para el tratamiento durante la producción real. Sin embargo, los resultados indican que la dureza de la superficie es inferior a 50 HRC, lo que la hace no calificada. Ajustar la temperatura de cementación y aumentar la temperatura de enfriamiento no puede cumplir con los requisitos técnicos.
Para obtener detalles específicos sobre el proceso de tratamiento térmico, consulte la Tabla 2.
Tabla 2 proceso de tratamiento térmico
NO. | Parámetros de proceso | Dureza de la superficie de la pieza (HRC) |
1 | Fuerte permeabilidad: 920 ℃ × 330 min, potencial de carbono 1,1%; Difusión: 920℃x130min, potencial de carbono 0,85%; Enfriamiento del aislamiento: 830 ℃ × 30 min, potencial de carbono 0,85 %. |
45~47 |
dos | Fuerte permeabilidad: 920 ℃ × 350 min, potencial de carbono 1,1%; Difusión: 920 ℃ × 140 min, potencial de carbono 0,9%; Enfriamiento y conservación del calor: 840 ℃ x 30 min, potencial de carbono 0,9 %. |
46~47 |
3 | Fuerte permeabilidad: 930 ℃ × 330 min, potencial de carbono 1,2%; Difusión: 930 ℃ x 30 min, potencial de carbono 0,9%; Enfriamiento del aislamiento: 860 ℃ × 40 min, potencial de carbono 0,9%. |
49~50 |
4 | Fuerte penetración: 930℃x450min, potencial de carbono 1,2%; Difusión: 930 ℃ × 250 min, potencial de carbono 0,9%; Enfriamiento y preservación del calor: 860 ℃ x 30 min, potencial de carbono 0,9%. |
46~48 |
3. Análisis de causas de baja dureza superficial del cilindro hidráulico.
(1) Temperatura de carburación
La temperatura de cementación es un parámetro tecnológico crucial en el proceso de cementación y afecta significativamente la capacidad de la austenita para disolver el carbono.
A medida que aumenta la temperatura, también aumenta la solubilidad del carbono en austenita.
Según el diagrama de fases hierro-carbono, la solubilidad saturada del carbono en austenita es del 1,0% a 850°C y del 1,25% a 930°C.
La precisión de la temperatura de cementación afecta directamente la calidad del enfriamiento de la pieza.
Después de realizar una detección de temperatura de 9 puntos del equipo, no encontramos ninguna desviación en la temperatura, la temperatura del horno es normal y no hay ninguna diferencia de temperatura significativa.
Por tanto, podemos excluir la influencia de la temperatura sobre la dureza superficial de la pieza.
(2) Efecto de la concentración de carbono
Durante la ejecución del proceso, se utiliza un bloque de prueba de horno que mide 25 mm x 25 mm para cada número de proceso.
Los resultados de la prueba de dureza del bloque de prueba son mejores que los del cuerpo de la pieza de trabajo.
Consulte la Tabla 3 para conocer los resultados de la prueba de dureza del bloque de prueba cementado realizado según el proceso 3, tanto en la cara del extremo como en la dirección longitudinal de la pieza.
Tabla 3 Resultados de la prueba de dureza de piezas (HRC)
Superficie |
Básico |
|||||
cara final |
59 |
60 |
58,5 |
59,6 |
20 |
21 |
Retrato |
56,6 |
57,5 |
55.2 |
56 |
De acuerdo con el método de dureza especificado en GB/T 9450-2005 para determinar y verificar la profundidad efectiva de la capa endurecida de hierro y acero de cementación y enfriamiento, el gradiente de dureza de la capa de cementación se prueba en el bloque de prueba del horno después del tratamiento térmico. proceso.
Los resultados se muestran en la Tabla 4.
Tabla 4 Resultados del ensayo de gradiente de dureza de la capa de penetración de la pieza
Profundidad de la capa de cementación / mm | Dureza HV1 |
0.1 | 622,9 |
0,2 | 747,7 |
0.3 | 714.4 |
0,4 | 720 |
0,5 | 685,8 |
0,6 | 662,7 |
0,7 | 635,9 |
0,8 | 635,9 |
0,9 | 599,9 |
1 | 568,8 |
1.1 | 540 |
La capa cementada del bloque de prueba se examina utilizando el método de análisis metalográfico para verificar que la concentración de carbono cumpla con las especificaciones requeridas.
La Figura 2 ilustra la estructura metalográfica de la capa superficial y la profundidad efectiva de la capa endurecida de la pieza.
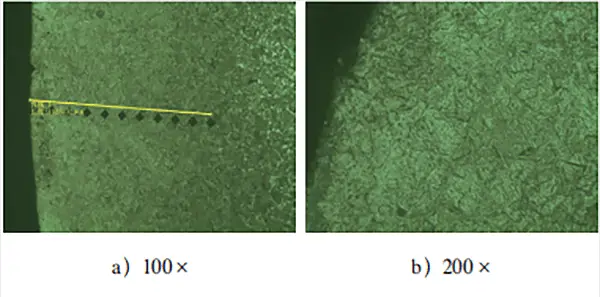
Después de observar la estructura metalográfica de la capa carburizada del bloque de prueba en la Fig. 2, se encontró que la capa superficial comprende principalmente martensita en forma de aguja y austenita residual. No se detectó ninguna composición de carburo significativa.
Además, la detección efectiva de la profundidad de la capa endurecida reveló que el bloque de prueba mostró un claro fenómeno de "cabeza arriba" después del tratamiento de cementación. Esto sugiere que hubo una atmósfera de oxidación notable en la capa carburizada, lo que resultó en una baja dureza superficial y una mayor dureza de paso.
Para examinar mejor la microestructura de la capa infiltrada del bloque de prueba de la pieza, se recoció el bloque de prueba. El proceso de recocido implicó enfriar el bloque de prueba de 860 ℃ × 30 min a 500 ℃ usando el horno, seguido de enfriamiento por aire.
Se prepararon y examinaron muestras metalográficas para observar el equilibrio de la estructura metalográfica de las piezas de acero 20CrMo carburizado, como se muestra en la Figura 3.
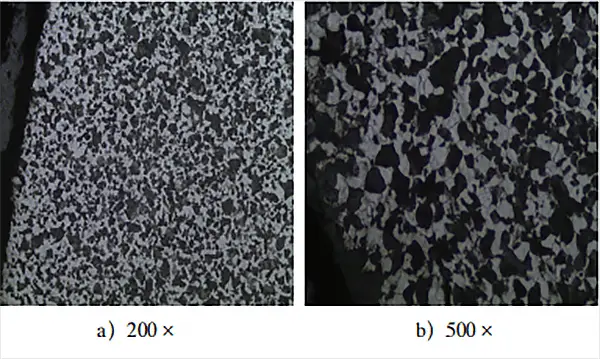
Según la observación de la estructura metalográfica de equilibrio en la Fig. 3, la morfología de la microestructura de la capa de cementación en acero con bajo contenido de carbono después de un enfriamiento lento es significativamente diferente de la del acero con bajo contenido de carbono normal. La capa hipereutectoide, la capa eutectoide y la capa de transición en la capa de cementación no se pueden distinguir de forma clara y eficaz.
La microestructura del acero con bajo contenido de carbono después de la cementación y el enfriamiento lento debe comprender una capa superficial de perlita y cementita líquida, una estructura eutectoide en el interior, una zona de transición de estructura subeutectoide y la estructura original.
En cuanto a la estructura de equilibrio en la Fig. 3, su morfología y estructura son más similares a la estructura de equilibrio obtenida después del recocido de acero ordinario de medio carbono, que tiene una estructura de perlita y ferrita distribuida uniformemente. No se encontró cementita obvia, lo que indica que el potencial de carbono de la atmósfera de cementación en el horno es insuficiente para asegurar una concentración suficiente de carbono en la superficie de la pieza.
Por lo tanto, para obtener una concentración de carbono adecuada en la superficie de la pieza y formar un gradiente de concentración de carbono efectivo, es necesario aumentar el potencial de carbono cuando la temperatura de cementación es normal.
4. Mejora de los métodos y condiciones del proceso.
La difusión de los átomos de carbono desde la superficie hacia el centro es necesaria para la cementación y para alcanzar una cierta profundidad de la capa cementada.
La fuerza impulsora detrás de la difusión es el gradiente de concentración de carbono entre la superficie y el núcleo.
Para mejorar el efecto de cementación, es crucial absorber los átomos de carbón activado a tiempo para asegurar la circulación uniforme de la atmósfera del horno. La tasa de átomos de carbono suministrados (tasa de descomposición) debe coincidir con la tasa de absorción para evitar un suministro insuficiente y la deposición de carbono.
Mediante el análisis de los enlaces del proceso original y los bloques de prueba, se encontró que la baja dureza de la pieza real se debía principalmente a la baja concentración de carbono en la superficie de la capa de carburación causada por una atmósfera insuficiente en el horno. Esto dio como resultado un tratamiento de cementación ineficaz, impidiendo la formación de una estructura de capa de cementación ideal y logrando una dureza suficiente.
Para resolver esto, se tomaron medidas de rectificación específicas para revisar el equipo, reemplazar el equipo de monitoreo del potencial de carbono, verificar la estanqueidad del cuerpo del horno y volver a realizar el tratamiento de determinación de carbono en la atmósfera del horno para garantizar la uniformidad y precisión de la atmósfera del horno. .
Después de reevaluar las condiciones del horno y redefinir los parámetros del proceso de cementación y revenido, la producción puede continuar.
Consulte la Tabla 5 para conocer el proceso de tratamiento térmico ajustado.
Tabla 5 proceso de tratamiento térmico ajustado
NO. | Parámetros de proceso | Dureza de la superficie de la pieza (HRC) |
1 | Fuerte penetración: 930℃x450min, potencial de carbono 1,3%; Difusión: 930 ℃ x 30 min, potencial de carbono 1,0 %; Enfriamiento del aislamiento: 850 ℃ × 30 min, potencial de carbono 1,0 %; Enfriamiento: 150 ℃ x 240 min |
62,6, 623, 62,1, 62,4, 62,9, 62,8 |
dos | Fuerte permeabilidad: 920 ℃ × 450 min, potencial de carbono 1,3%; Difusión: 920℃x30min, potencial de carbono 1,0%; Enfriamiento y conservación del calor: 840 ℃ x 30 min, potencial de carbono 1,0 %; Enfriamiento: 180 ℃ x 240 min |
59,4, 613, 60,1, 59,4, 60,9, 60,1 |
La estructura metalográfica de la capa infiltrada del bloque de prueba tratado mediante el proceso de tratamiento térmico ajustado se muestra en la Figura 4.
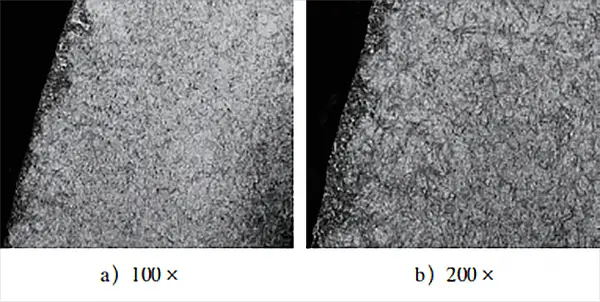
La Figura 4 ilustra que la estructura metalográfica consiste principalmente en martensita templada fina, carburo de grano fino y una pequeña cantidad de austenita residual, que se alinea con la estructura normal de cementación y enfriamiento. Esto asegura una dureza superficial efectiva y una dureza superficial general de la pieza que cumple con el rango requerido por las condiciones técnicas.
Para obtener una mejor comprensión de los cambios microestructurales antes y después de ajustes específicos en el proceso de tratamiento térmico, el bloque de prueba se somete a recocido con el mismo proceso.
El proceso de recocido implica calentar el bloque a 860 ℃ durante 30 minutos, enfriarlo a 500 ℃ en el horno y finalmente enfriarlo al aire.
Se prepararon muestras metalográficas para observar la estructura de equilibrio de piezas de acero 20CrMo carburizado.
La Figura 5 demuestra la estructura recocida después del tratamiento térmico del proceso de sintonización.
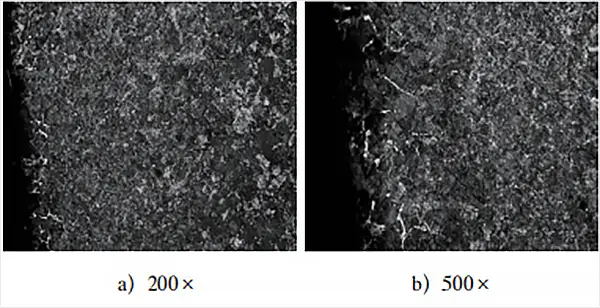
La Figura 5 muestra claramente la presencia de perlita y cementita reticulada, y una comparación de la estructura de la capa superficial en la Figura 3 resalta la diferencia entre ellas.
La estructura representada en la Fig. 3 se asemeja a la estructura de equilibrio del acero común de medio carbono después del recocido, con un contenido de carbono (fracción de masa) de alrededor del 0,5%.
Por el contrario, la estructura de equilibrio en la Fig. 5 muestra la estructura de red de perlita + cementita que resulta del recocido de cementación normal.
Este cambio de estructura sugiere que hubo un problema importante con la atmósfera del horno en las condiciones originales del proceso. Como resultado, las condiciones de cementación de las piezas no cumplieron con los requisitos definidos, lo que provocó que las piezas no cumplieran con los requisitos técnicos especificados después del tratamiento del proceso.
5. Conclusión
- La estructura de transformación en fase sólida de enfriamiento lento del acero estructural de carbono de baja aleación después de la cementación y el enfriamiento se puede utilizar para determinar el contenido de carbono en la capa cementada final. Esto, a su vez, ayuda a determinar si la atmósfera del horno cumple con los estándares requeridos.
- Aunque aumentar el potencial de carbono puede mejorar el efecto de cementación hasta cierto punto, la limitada solubilidad saturada del carbono en austenita requiere una configuración flexible del potencial de carbono basada en las condiciones reales para evitar la posibilidad de deposición de carbono.
- La precisión del equipo de tratamiento de cementación tendrá un impacto directo en los resultados finales del tratamiento térmico.