En comparación con la soldadura tradicional, la soldadura láser ofrece varios beneficios, incluido un pequeño aporte de calor y una influencia térmica reducida, altas relaciones de aspecto y un proceso de soldadura automatizado.
Las aleaciones de aluminio son populares por su peso ligero, alta tenacidad, alto rendimiento y facilidad de procesamiento y conformado. Se utilizan ampliamente en la producción de productos como contenedores, máquinas, equipos de energía eléctrica, componentes de la industria química, aviación y estructuras aeroespaciales.
Reemplazar la soldadura de placas de acero por aleaciones de aluminio puede mejorar significativamente la calidad estructural. El aluminio es un metal más reactivo, con baja energía de ionización y alta conductividad térmica, pero es propenso a formar Al refractario. Película 2 Ó 3 en la superficie, que puede provocar defectos como zonas no fusionadas, poros, inclusiones y grietas térmicas en la soldadura, reduciendo así las propiedades mecánicas de la unión.
En comparación con la soldadura por arco de argón y tungsteno o la soldadura por arco de argón fundido, la soldadura por láser proporciona cordones de soldadura estrechos, pequeñas zonas afectadas por el calor, juntas traslapadas reducidas, control preciso del proceso de soldadura y automatización.
Actualmente, la soldadura láser se utiliza principalmente para soldar componentes electrónicos de paredes delgadas, piezas estructurales y componentes aeroespaciales. La tendencia futura en la investigación de la soldadura láser implica el desarrollo de láseres de fibra de 10.000 vatios para la soldadura de penetración profunda de láminas grandes y gruesas.
Principales láseres de alta potencia en aplicaciones de soldadura láser.
Rendimiento/tipo | láser de dióxido de carbono | NdYAG láser |
YbYAG LáserDac |
láser de fibra |
---|---|---|---|---|
Longitud de onda / zumbido | 10.6 | 1.06 | 1.06 | 1-2 |
Eficiencia de conversión eléctrica/% | 12-15 | 2-6 | 20 | 8-10 |
Densidad de potencia/(MW/cm-2) | 10 | 10 | 100 | 100 |
Potencia máxima/kW) | 50 | 6 | 15 | 50 |
Salida del haz | Lente óptica | Fibra óptica | Fibra óptica | Fibra óptica |
Absortividad del metal/% | 8 | 20 | 20 | 20 |
Ciclo de mantenimiento/hora | 1000 | 1000 | 1oooo | 20.000 |
Brillo del láser (103W/mm2 estereorradián)(4kW/h) | – | 7,5 (distancia focal: 200; Diámetro de la fibra: 0,6 mm) |
134,2 (distancia focal: 200; Diámetro de la fibra: 0,2 mm) |
264,4 (distancia focal: 160; Diámetro de la fibra: 0,1 mm) |
Láser de gas CO2
El medio de trabajo de los láseres de CO 2 es el gas CO 2 y, con una longitud de onda de salida de 10,6 μm, se puede clasificar en flujo cruzado y flujo axial según la estructura de excitación del láser.
Aunque los láseres de flujo cruzado de CO2 han alcanzado una potencia de salida de 150 kW, la calidad del haz no es adecuada para soldar. Por otro lado, los láseres de CO2 de flujo axial tienen una buena calidad de haz y pueden usarse para soldar aleaciones de aluminio con alta reflectividad láser.
Láser de estado sólido YAG
El medio de trabajo de los sistemas láser incluye rubí, vidrio de neodimio y granate de itrio y aluminio (YAG) dopado con neodimio, con una longitud de onda de salida de 1,06 μm.
En comparación con los láseres de CO 2 , los láseres YAG son absorbidos más fácilmente por el metal y menos afectados por el plasma. Además, los láseres YAG ofrecen los beneficios de la transmisión por fibra óptica, operaciones de soldadura flexibles y fácil acceso a la posición de soldadura.
Actualmente, los láseres YAG son los principales sistemas láser utilizados para soldar estructuras de aleaciones de aluminio.
Láser de fibra YLR
El láser de fibra YLR es una tecnología láser más nueva desarrollada después de 2002. Utiliza fibra óptica como material de matriz, dopada con diferentes iones de tierras raras, y tiene un rango de longitud de onda de salida de 1,08 μm, que también se transmite a través de fibra óptica.
El láser de fibra presenta una revolucionaria estructura de doble fibra, que aumenta la longitud de la bomba y mejora la eficiencia de la bomba, lo que resulta en una potencia de salida muy mejorada en comparación con los láseres de fibra tradicionales.
En comparación con los láseres YAG, los láseres de fibra YLR se desarrollaron más tarde, pero ofrecen ventajas como tamaño pequeño, bajos costos operativos, alta calidad del haz y alta potencia del láser.
Clasificación y soldabilidad de la aleación de aluminio.
El aluminio y las aleaciones de aluminio se pueden dividir en:
- Serie 1000 (aluminio puro industrial)
- Serie 2000 (serie Al-Cu)
- Serie 3000 (serie Al-Mn)
- Serie 4000 (Al-Si)
- Serie 5000 (Al-Mg)
- Serie 6000 (Al-Mg-Si)
- Serie 7000 (Al-Zn-Mg-Cu)
Las aleaciones de aluminio se pueden dividir en dos categorías según las características del proceso: aleaciones de aluminio deformadas y aleaciones de aluminio fundido. Las aleaciones de aluminio deformadas se pueden dividir en dos subcategorías: aleaciones de aluminio reforzadas sin tratamiento térmico y aleaciones de aluminio reforzadas con tratamiento térmico.
Cada tipo de aleación de aluminio tiene propiedades de soldadura únicas. Por ejemplo, el aluminio sin tratamiento térmico y las aleaciones de aluminio de las series 1000, 3000 y 5000 tienen buena soldabilidad. Las aleaciones de la serie 4000 tienen baja sensibilidad al agrietamiento.
Sin embargo, cuando el contenido de magnesio alcanza el 2% en las aleaciones de la serie 5000, la aleación se vuelve propensa a agrietarse. Aunque aumentar el contenido de magnesio mejora el rendimiento de la soldadura, disminuye la ductilidad y la resistencia a la corrosión de la aleación.
Por otro lado, las aleaciones de las series 2000, 6000 y 7000 son más susceptibles al agrietamiento en caliente, tienen una mala formación de cordones de soldadura y tienen una reducción significativa en la dureza al envejecimiento después de la soldadura.
Por tanto, es fundamental adoptar medidas tecnológicas adecuadas para soldar aleaciones de aluminio y seleccionar el método de soldadura y el material de aportación correctos para obtener buenas uniones soldadas. Antes de soldar, el material debe someterse a un tratamiento superficial que incluye eliminar la suciedad aceitosa con disolventes orgánicos, sumergirlo en una solución de NaOH, enjuagar la superficie con agua corriente y realizar un tratamiento fotoquímico.
Las piezas soldadas procesadas también deben someterse a experimentos del proceso de soldadura dentro de las 24 horas.
Aplicación de estructura de soldadura láser de aleación de aluminio.
Desde la década de 1990, los avances en ciencia y tecnología y el desarrollo de láseres de alta potencia y alto brillo han llevado al crecimiento de la tecnología de soldadura láser y a su creciente madurez en términos de integración, inteligencia, flexibilidad y diversidad. Ha habido una atención cada vez mayor a la aplicación de la soldadura láser a estructuras de aleaciones de aluminio en diversas industrias, tanto a nivel nacional como internacional.
Actualmente, algunos fabricantes de automóviles en China ya han adoptado la tecnología de soldadura láser en algunos de sus nuevos modelos. A medida que la tecnología de soldadura láser para placas gruesas de aleación de aluminio continúa desarrollándose, se espera que se utilice en el futuro para la estructura de vehículos blindados.
Con el fin de conseguir una fabricación ligera, la aplicación e investigación de la soldadura láser en estructuras tipo sándwich de aleación de aluminio es un foco actual de investigación en la fabricación estructural de barcos y trenes de alta velocidad.
Las aleaciones de aluminio también son un material metálico importante para las estructuras aeroespaciales, razón por la cual países desarrollados como Japón, Estados Unidos, Gran Bretaña y Alemania ponen gran énfasis en la investigación de la tecnología de soldadura láser de aleaciones de aluminio.
Con el avance de la tecnología de soldadura por láser de fibra, la soldadura por láser de fibra y la tecnología de soldadura por arco láser híbrido se han convertido en el foco de la tecnología de soldadura de aleaciones de aluminio en el campo de la fabricación de aviación en los países avanzados, particularmente para soldar placas gruesas y soldar metales diferentes.
Por ejemplo, el proyecto estadounidense NALI está llevando a cabo investigaciones sobre soldadura por láser de fibra y tecnología de soldadura por arco láser híbrido para la estructura de la cámara de combustión de aviones civiles y motores de aviones JSF.
Características de la soldadura láser de aleación de aluminio.
En comparación con la soldadura por fusión convencional, la soldadura láser de aleaciones de aluminio ofrece ventajas como calentamiento concentrado, una gran relación profundidad-ancho de la soldadura y una deformación reducida de la estructura de soldadura. Sin embargo, también existen algunas limitaciones, que incluyen:
- El pequeño diámetro del punto de enfoque láser requiere una alta precisión al soldar y ensamblar la pieza. Generalmente, el espacio libre de montaje y la desalineación deben ser inferiores a 0,1 mm o 10 % del espesor de la placa, lo que hace que la implementación de estructuras de soldadura tridimensionales complejas sea un desafío.
- La alta reflectividad de las aleaciones de aluminio a los láseres, hasta un 90% a temperatura ambiente, significa que la soldadura láser de penetración profunda de aleaciones de aluminio requiere una alta potencia.
Las investigaciones sobre soldadura láser de láminas de aleación de aluminio muestran que:
La soldadura láser de penetración profunda de aleaciones de aluminio depende tanto de la densidad de potencia del láser como de la energía lineal. Estos dos factores impactan conjuntamente el comportamiento del baño fundido durante el proceso de soldadura y se reflejan en las características de la soldadura.
Para optimizar el proceso de soldadura de penetración total, se puede utilizar la relación del ancho posterior de los parámetros característicos de formación de la soldadura para evaluar su efectividad.
- Las aleaciones de aluminio tienen un punto de fusión bajo y una buena fluidez del metal líquido, lo que puede provocar una fuerte vaporización del metal bajo la influencia de láseres de alta potencia. La nube de plasma/vapor de metal fotoinducida que se forma con el efecto ojo de cerradura puede afectar la absorción de energía láser por la aleación de aluminio durante la soldadura, provocando inestabilidad en el proceso de soldadura de penetración profunda y provocando defectos como porosidad, colapso superficial y corte inferior.
- La soldadura láser tiene altas velocidades de calentamiento y enfriamiento, lo que resulta en una mayor dureza de la soldadura en comparación con la soldadura por arco. Sin embargo, la pérdida por combustión de elementos de aleación durante la soldadura láser de aleación de aluminio puede afectar su efecto de fortalecimiento, lo que lleva a una reducción en la resistencia de la junta soldada de aleación de aluminio debido al ablandamiento.
Por tanto, el principal reto en la soldadura láser de aleaciones de aluminio es controlar los defectos de soldadura y mejorar las propiedades de las uniones soldadas.
Los principales problemas en la soldadura láser de aleaciones de aluminio.
La soldadura láser utiliza el láser como fuente de luz de alta densidad que ofrece un calentamiento rápido y una solidificación instantánea, con una relación de aspecto de hasta 12:1. Sin embargo, debido a la alta reflectividad y buena conductividad térmica de las aleaciones de aluminio, así como al efecto protector del plasma, es probable que se produzcan defectos durante el proceso de soldadura.
Los dos defectos más importantes son los poros y las grietas térmicas. El desafío en la soldadura láser de aleaciones de aluminio es mejorar efectivamente la absorción de la luz láser por el material debido a su fuerte reflexión.
El proceso de soldadura láser de aleaciones de aluminio es más complejo, siendo imprescindible mejorarlo y perfeccionarlo debido a las características de la propia aleación de aluminio.
Tasa de absorción del láser
Cuanto mayor sea la tasa de absorción del láser por el material, o cuanto menor sea el coeficiente de transferencia de calor y el coeficiente de conductividad de la temperatura, más fácilmente será absorbida la energía del láser por la superficie del material, lo que provocará un rápido aumento de la temperatura de la superficie y la fusión o evaporación del material. el material.
La Tabla 1 muestra la reflectividad de varios metales para láseres con diferentes longitudes de onda.
Tabla 1 La reflectividad de los metales para láseres de diferentes longitudes de onda a temperatura ambiente (%)
λ/μm | Ag | Alabama | Culo | cr | No | Acero |
---|---|---|---|---|---|---|
0,7 | 95 | 77 | 82 | 56 | 68 | 58 |
1.06 | 97 | 80 | 91 | 58 | 75 | 63 |
10.6 | 99 | 98 | 98 | 93 | 95 | 93 |
La reflectividad de diferentes metales disminuye a medida que la longitud de onda se acorta, y la reflectividad de Ag, Al y Cu a la luz láser alcanza el 90% o más. Esto aumenta significativamente la dificultad del procesamiento con láser.
A temperatura ambiente, la tasa de absorción de los láseres de CO2 por las aleaciones de aluminio es muy baja: el 98% de la energía del láser se refleja en la superficie de la aleación de aluminio. La reflectividad de los láseres Nd:YAG también alcanza el 80%.
Está claro que las aleaciones de aluminio tienen una alta reflectividad a la luz láser y una baja tasa de absorción, debido a su alta densidad de electrones libres. La fuerte vibración de las ondas electromagnéticas de la luz da como resultado la generación de fuertes ondas reflejadas y ondas transmitidas más débiles. Las ondas reflejadas no son fácilmente absorbidas por la superficie de la aleación de aluminio, lo que lleva a su alta reflectividad a los láseres a temperatura ambiente.
Inducción y estabilización de “pequeños agujeros”
En el proceso de soldadura láser, cuando la densidad de energía del láser excede 3,5*10 6 C/cm 2 , se generarán iones. Este método de soldadura se realiza mediante soldadura de penetración profunda y se basa en el efecto “pequeño agujero”. La presencia de "pequeños agujeros" aumenta significativamente la tasa de absorción del material por el láser y da como resultado un buen efecto de soldadura cuando se suelda con alta densidad de energía.
El principal desafío en la soldadura láser de aleaciones de aluminio es inducir y mantener la estabilidad de los agujeros pequeños, lo que se debe tanto a las propiedades del material de las aleaciones de aluminio como a las propiedades ópticas del rayo láser. Como se mencionó anteriormente, el aluminio refleja el 80% de la energía a temperatura ambiente y tiene buena conductividad térmica, lo que requiere un umbral de densidad de energía láser grande para producir "pequeños agujeros".
Una vez que la potencia de entrada supera este valor, la transmisión de energía láser al material ya no está limitada por la conducción de calor y la soldadura se realiza mediante penetración profunda. La radiación láser provoca una fuerte evaporación del metal base y forma un surco de evaporación. El rayo láser penetra el material a través de esta ranura, lo que resulta en un marcado aumento en la profundidad y eficiencia de la soldadura.
Para materiales altamente reflectantes, como aleaciones de aluminio y aleaciones de cobre, se requiere una gran densidad de potencia durante la soldadura. Esto impone ciertos requisitos en la selección de modelos de soldadura y lentes de colimación y enfoque.
Propiedades mecánicas de las soldaduras.
El fortalecimiento por refinación, el fortalecimiento por solución sólida y el fortalecimiento por precipitación por envejecimiento son tres formas diferentes de fortalecer las aleaciones de aluminio. A pesar de estos mecanismos, la gran cantidad de evaporación de elementos de aleación de bajo punto de fusión, como Mg y Zn, durante la soldadura láser hace que la soldadura se hunda y reduzca su dureza y resistencia.
Durante el rápido proceso de solidificación, la transformación de la estructura reforzada de grano fino en una estructura fundida da como resultado una disminución de la dureza y la resistencia. Además, la presencia de grietas y poros en la soldadura reduce la resistencia a la tracción.
En conclusión, el ablandamiento de las juntas es otro desafío en la soldadura láser de aleaciones de aluminio.
Estómago
Hay dos tipos principales de poros en el proceso de soldadura por láser de aleaciones de aluminio: poros de gas hidrógeno y poros de colapso en forma de ojo de cerradura.
( 1) Poros de hidrógeno: las aleaciones de aluminio forman una película de óxido en su superficie a altas temperaturas, que absorbe fácilmente la humedad del medio ambiente. Cuando se calienta con un láser, el agua se descompone en hidrógeno, y la solubilidad del hidrógeno en el aluminio líquido es aproximadamente 20 veces mayor que la del aluminio sólido. Durante la rápida solidificación de la aleación, la solubilidad del hidrógeno disminuye drásticamente a medida que pasa del aluminio líquido al estado sólido. Si el exceso de hidrógeno en el aluminio líquido no sube y se desborda suavemente, se formarán poros de hidrógeno. Estos poros son generalmente de forma regular y de mayor tamaño que las dendritas, y los patrones de solidificación de las dendritas se pueden ver en la superficie interna.
(2) Colapso del ojo de cerradura: el orificio de soldadura está en equilibrio con su propia gravedad y presión atmosférica. Una vez que se altera este equilibrio, el metal líquido en el charco fundido no puede fluir y llenarse con el tiempo, lo que resulta en agujeros desiguales. Los estudios han encontrado que el contenido de magnesio de la pared interior del orificio es aproximadamente 4 veces mayor que el de la zona de soldadura. Debido a que la velocidad de enfriamiento de la soldadura láser es muy rápida, el problema de los poros del gas hidrógeno es más grave y hay más agujeros causados por el colapso de pequeños agujeros en la soldadura láser.
Craqueo térmico
La aleación de aluminio es una aleación eutéctica común que es propensa a agrietarse en caliente durante la soldadura, incluidas grietas de cristalización de soldadura y grietas de licuefacción HAZ (zona afectada por el calor). Normalmente, las grietas de cristalización aparecen en la zona de soldadura, mientras que las grietas de licuefacción aparecen cerca de la unión. Entre las aleaciones de aluminio, las aleaciones de Al-Mg-Si de la serie 6000 son particularmente susceptibles al agrietamiento.
El metal base se somete a un rápido calentamiento y enfriamiento, lo que puede conducir a un proceso instantáneo de solidificación y cristalización. El gran grado de subenfriamiento durante este proceso hace que los granos de cristal crezcan perpendiculares al centro de la soldadura, formando compuestos eutécticos de bajo punto de fusión como Al-Si o Mg-Si, Al-Mg2Si y otros. Esto debilita la fuerza de unión del plano cristalino, haciéndolo más propenso a agrietarse bajo tensión térmica.
En el proceso de soldadura de aleaciones de aluminio, los elementos de bajo punto de ebullición como Mg, Zn, Mn y Si se evaporan y queman fácilmente. Cuanto más lenta es la velocidad de soldadura, más grave es la quemadura, lo que cambia la composición química del metal de soldadura. Debido a la segregación de componentes en la zona de soldadura, se produce segregación eutéctica y fusión de los límites de grano, lo que provoca grietas de licuefacción en los límites de grano bajo tensión, lo que reduce el rendimiento de la unión soldada.
Proceso de soldadura láser de aleación de aluminio.
Para lograr el éxito en la soldadura láser de aleaciones de aluminio y resolver los problemas mencionados anteriormente, comúnmente se adoptan varios enfoques.
Dispositivo de protección de gases
Uno de los factores más importantes que influyen en la pérdida de elementos de bajo punto de fusión en las aleaciones de aluminio durante la soldadura es la presión del gas expulsado por la boquilla. Para mitigar este problema, se puede reducir el diámetro de la boquilla y aumentar la presión y el caudal del gas. Esto reducirá la pérdida por combustión de elementos como Mg y Zn durante el proceso de soldadura y también aumentará la penetración.
Hay dos métodos de soplado disponibles: soplado directo y soplado lateral. Además, es posible soldar con chorro de arena hacia arriba y hacia abajo simultáneamente. La elección del método de soplado debe determinarse en función de las circunstancias específicas durante la soldadura.
Tratamiento de superficies
La aleación de aluminio tiene una fuerte reacción a la energía del láser. La preparación adecuada de la superficie de la aleación de aluminio, como oxidación anódica, pulido electrolítico, chorro de arena, etc., puede mejorar en gran medida la absorción de energía del haz en la superficie.
Las investigaciones han demostrado que la eliminación de la película de óxido de las aleaciones de aluminio aumenta su tendencia a formar grietas de cristalización. Para evitar dañar la condición de la superficie de la aleación de aluminio y al mismo tiempo simplificar el proceso de soldadura por láser, se puede aumentar la temperatura de la superficie de la pieza de trabajo antes de soldar, lo que aumentará la tasa de absorción del láser del material.
Parámetros del láser
La soldadura láser se divide en dos categorías: láseres pulsados y láseres continuos. Los láseres pulsados con una longitud de onda de 1064 nm tienen un haz altamente concentrado y la energía del pulso en un solo punto es mayor que la de los láseres continuos. Sin embargo, la energía de los láseres pulsados es generalmente limitada, lo que los hace más adecuados para soldar materiales de paredes delgadas.
Soldadura en modo pulso
Al realizar soldadura láser, es importante seleccionar la forma de onda de soldadura adecuada. Las formas de onda de pulso comunes incluyen onda cuadrada, onda de pico y onda de doble pico. Normalmente, las ondas del pulso duran en el rango de milisegundos. Durante un pulso láser, la reflectividad del metal cambia drásticamente. Las aleaciones de aluminio tienen una alta reflectividad de la luz, lo que significa que entre el 60 y el 98 % de la energía láser que llega a la superficie del material puede perderse debido a la reflexión. Esta reflectividad cambia con la temperatura de la superficie.
La onda pronunciada y la onda de doble pico son las mejores opciones para soldar aleaciones de aluminio, ya que la fase ascendente de la forma de onda proporciona más energía para fundir la aleación de aluminio. Una vez que se forma un “pequeño orificio” en la pieza de trabajo, la tasa de absorción del metal líquido por el láser aumenta rápidamente durante la soldadura de penetración profunda. En este punto, es importante reducir rápidamente la potencia del láser y realizar soldadura a baja potencia para evitar salpicaduras.
La parte más lenta de la forma de onda de soldadura tiene un ancho de pulso más largo, lo que reduce efectivamente la formación de poros y grietas. Esta forma de onda hace que la soldadura se derrita y solidifique repetidamente, reduciendo la tasa de solidificación del baño fundido. La forma de onda se puede ajustar según sea necesario al soldar diferentes tipos de muestras.
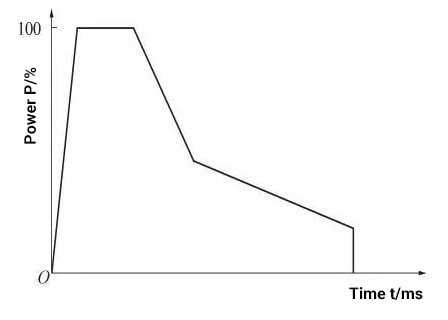
Figura 1 Forma de onda de pulso de soldadura de aleación de aluminio
Seleccionar la cantidad adecuada de difuminado también puede minimizar la formación de poros. El cambio en el desenfoque tiene un impacto significativo en la formación y penetración de la superficie de la soldadura. El desenfoque negativo puede aumentar la penetración, mientras que el desenfoque positivo en la soldadura por pulsos puede hacer que la superficie de soldadura sea más suave y visualmente más atractiva.
Debido a la alta reflectividad de las aleaciones de aluminio a la energía láser, el cabezal de soldadura generalmente está inclinado para evitar que el rayo láser se refleje verticalmente y dañe la lente de enfoque del láser. El diámetro de la junta de soldadura y la superficie de unión efectiva aumentan a medida que aumenta el ángulo de inclinación del láser. La unión de soldadura más grande y la superficie de unión efectiva se logran cuando el ángulo de inclinación del láser es de 40°. Sin embargo, la penetración del punto de soldadura y la penetración efectiva disminuyen al aumentar el ángulo de inclinación del láser, y cuando supera los 60°, la penetración de soldadura efectiva disminuye a cero. Inclinar el cabezal de soldadura en un cierto ángulo puede aumentar la profundidad de penetración y el ancho de la soldadura.
Además, es importante tener en cuenta que cuanto más rápida sea la velocidad de soldadura, mayor será el riesgo de agrietamiento. Esto se debe a que una velocidad de soldadura rápida conduce a un alto grado de subenfriamiento, lo que hace que los granos en la zona de soldadura se refinen y una gran cantidad de “haces de cristal” crezcan en la misma dirección, lo que aumenta la probabilidad de formación de grietas en el cristal. plano entre estos cristales de haz. Si la velocidad de soldadura es demasiado rápida, la profundidad de penetración de la soldadura será relativamente pequeña.
Soldadura en modo continuo
La soldadura láser tradicional puede provocar fragilidad o grietas. Por el contrario, la soldadura láser continua no tiene el mismo proceso repentino de enfriamiento y calentamiento que la soldadura láser pulsada, lo que genera menos grietas durante el proceso de soldadura. Además, la soldadura con láser de fibra de la mayoría de las aleaciones de aluminio da como resultado una mayor tenacidad después de la soldadura y reduce el riesgo de fragilidad.
La soldadura por láser pulsado es adecuada para la soldadura industrial de aluminio puro, con poco riesgo de agrietamiento después de la soldadura. Sin embargo, algunas industrias pueden requerir un pulido de la superficie posterior a la soldadura, y la soldadura por láser pulsado puede causar abolladuras y aumentar la cantidad de pulido requerido, lo que genera un aumento en el tiempo de procesamiento y los costos de producción. Los láseres continuos pueden resolver estos problemas.
Como se muestra en la Figura 2, la comparación de la costura de soldadura de la carcasa de la batería después de la soldadura por láser pulsado y la soldadura por láser continua demuestra las ventajas de la soldadura por láser continua. Las juntas de soldadura por impulso son irregulares y tienen superficies rebajadas y abolladas, con muchas salpicaduras y menor resistencia post-soldadura. Por el contrario, la soldadura láser continua da como resultado una superficie de cordón de soldadura suave y uniforme, libre de defectos y salpicaduras, sin grietas en el cordón de soldadura.
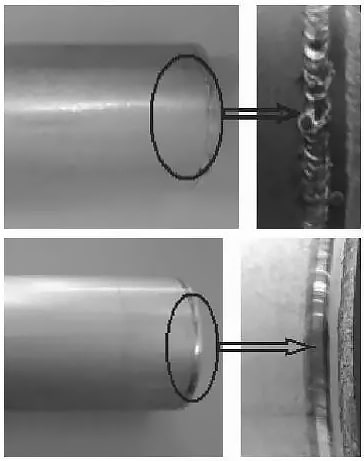
Figura 2 Soldadura pulsada y continua de aleación Al-Mn
Los cráteres de arco son algo común durante la soldadura por arco de argón, y lo mismo puede ocurrir durante la soldadura láser. Para minimizar la aparición de pequeños cráteres, se puede configurar una etapa de subida y bajada lenta en la forma de onda durante la soldadura, y la velocidad de soldadura se puede aumentar según sea necesario.
La soldadura láser continua tiene numerosas ventajas a la hora de soldar aleaciones de aluminio. En comparación con los métodos de soldadura tradicionales, la soldadura láser continua es más eficiente y elimina la necesidad de rellenar alambre. En comparación con la soldadura por láser pulsado, la soldadura por láser continua elimina defectos como grietas, poros y salpicaduras y garantiza que la aleación de aluminio tenga buenas propiedades mecánicas después de la soldadura. Además, no habrá abolladuras después de la soldadura y se reducirá la cantidad de pulido y esmerilado necesarios, ahorrando costes de producción.
Sin embargo, es importante tener en cuenta que los láseres continuos tienen un tamaño de punto relativamente pequeño, por lo que la precisión del ensamblaje de la pieza debe ser alta.
Introducción de elementos de aleación
La prevención de grietas térmicas es una tecnología fundamental para la soldadura láser de aleaciones de aluminio, especialmente para las aleaciones de la serie 6000, que son muy sensibles a las grietas. Si el contenido de ω(Mg2Si) alcanza el 1%, es probable que se produzca craqueo en caliente. Para reducir el riesgo de agrietamiento, se pueden agregar elementos de aleación adecuados para ajustar la composición química del baño fundido, como agregar polvo de Al-Si o Al-Mg-Si.
Además, la alimentación de alambre puede mejorar el efecto de soldadura y producir una costura de soldadura uniforme con mayor dureza. La introducción de material de relleno aumenta el contenido de Mg y Si en la dendrita en la zona de fusión, provocando un aumento de la resistencia de la unión debido al efecto fortalecedor de la solución sólida β”.
Normalmente, las aleaciones de aluminio 6063 y 6082 se rellenan con alambres de soldadura Al-5Si y Al-7Si, mientras que las placas 6013 y 6056 se sueldan con CO2 y Nd:YAG, respectivamente, y se rellenan con alambres de soldadura Al-12Si.
Otros métodos de proceso
Buscando estabilidad y calidad en la soldadura láser de aleaciones de aluminio.
El foco actual de la investigación en soldadura láser de aleaciones de aluminio es el uso de un proceso compuesto que combina la alta densidad de energía de los rayos láser con el amplio rango de calentamiento de los arcos, utilizando las fortalezas de ambas fuentes de calor y mejorando su alta densidad de energía y estabilidad. características. arcos.
Para materiales con alta reflectividad, como las aleaciones de aluminio, la soldadura láser híbrida puede precalentar o fundir la superficie del material utilizando energía de arco, mejorando significativamente la absorción de energía láser por parte de la aleación de aluminio.
Shida et al. utilizó con éxito un láser de CO2 de 10 kW junto con arcos TIG y MIG para soldar aleaciones de aluminio. La introducción de arcos mejoró la tasa de utilización de la energía del láser y aumentó la tasa de penetración de la soldadura entre un 5% y un 20%. El resultado fue una superficie de soldadura suave y bien formada.
La soldadura láser híbrida aumenta el tamaño del baño fundido y modifica las condiciones de flujo del material en estado fundido mediante el acoplamiento de rayos y arcos láser, lo que resulta beneficioso para eliminar los poros.
La eliminación de los agujeros de aire al soldar aleaciones de aluminio también se puede lograr mediante soldadura de doble haz. Se utilizó un láser de fibra continua de 6 kW para la soldadura a tope de doble haz de aleación de aluminio 5052, y se estudiaron los efectos de los modos de soldadura en serie y en paralelo de dos haces y las diferentes velocidades de soldadura sobre la morfología y estructura de la costura. La investigación encontró que la soldadura paralela de doble haz daba como resultado grandes agujeros en las soldaduras, mientras que la soldadura en serie de aleaciones de aluminio producía una buena formación de soldadura sin poros.
Tecnología de control de defectos de soldadura láser de aleación de aluminio
Bajo la influencia de láseres de alta potencia, los principales defectos en la soldadura láser de penetración profunda de aleaciones de aluminio son la porosidad, el colapso de la superficie y el socavado. El colapso de la superficie y los defectos socavados se pueden mejorar mediante soldadura de relleno con alambre láser o soldadura por arco láser híbrido. Sin embargo, controlar los defectos de porosidad es un desafío.
Las investigaciones han demostrado que existen dos tipos de poros característicos en la soldadura láser de penetración profunda de aleaciones de aluminio. Un tipo son los poros metalúrgicos, causados por la contaminación del material o la intrusión de aire durante el proceso de soldadura, similar a la soldadura por fusión por arco. El otro tipo es la porosidad del proceso, causada por la fluctuación inestable de pequeños orificios inherentes al proceso de soldadura por penetración profunda con láser.
Durante la soldadura láser de penetración profunda, el pequeño orificio generalmente va por detrás del movimiento del haz debido a la viscosidad del metal líquido, y su diámetro y profundidad fluctúan bajo la influencia del plasma/vapor de metal. A medida que el haz se mueve y el metal fundido fluye, la soldadura de penetración profunda incompleta se cierra debido al flujo del metal fundido, lo que provoca que aparezcan burbujas en la punta del pequeño orificio. En la soldadura de penetración profunda y de penetración total, aparecen burbujas en la cintura del pequeño orificio en el medio.
Estas burbujas migran y ruedan con el flujo de metal líquido, escapando de la superficie del charco fundido o siendo empujadas hacia el pequeño agujero. Cuando las burbujas se solidifican en el baño de soldadura y son capturadas por el frente metálico, se convierten en poros de soldadura.
Los poros metalúrgicos se pueden controlar mediante un tratamiento superficial previo a la soldadura y una protección adecuada con gas durante el proceso de soldadura. La clave para controlar los poros del proceso es garantizar la estabilidad durante el proceso de soldadura por penetración profunda con láser.
Según una investigación sobre la tecnología de soldadura láser nacional, el control de los orificios de aire en la soldadura láser de penetración profunda de aleaciones de aluminio requiere la consideración de todos los enlaces, incluso antes de la soldadura, el proceso de soldadura y el tratamiento posterior. Esto se puede lograr mediante los siguientes nuevos procesos y tecnologías.
Método de tratamiento previo a la soldadura.
El tratamiento superficial previo a la soldadura es un método eficaz para controlar los poros metalúrgicos en la soldadura láser de aleaciones de aluminio. Los métodos comunes de tratamiento de superficies incluyen la limpieza física mecánica y la limpieza química. Recientemente también ha surgido la limpieza por impacto con láser, que mejora aún más la automatización de la soldadura por láser.
Control de optimización de estabilidad de parámetros
Los parámetros del proceso de soldadura láser de aleación de aluminio suelen incluir la potencia del láser, el desenfoque, la velocidad de soldadura y la composición y el flujo del gas protector. Estos parámetros no solo afectan el efecto protector del área de soldadura, sino que también afectan la estabilidad del proceso de soldadura por penetración profunda con láser, lo que a su vez afecta la porosidad de la soldadura.
Mediante la soldadura láser de penetración profunda de láminas de aleación de aluminio, se descubrió que la estabilidad de la penetración en orificios pequeños influye en la estabilidad del baño fundido, lo que afecta la formación de la soldadura y produce defectos de porosidad. Además, la estabilidad de la soldadura por penetración profunda con láser está relacionada con la correspondencia entre la densidad de potencia del láser y la energía lineal.
Por lo tanto, determinar parámetros de proceso razonables para la formación de soldadura estable es un método eficaz para controlar la porosidad de la soldadura láser de aleaciones de aluminio. Los resultados de la investigación sobre las características de formación de soldadura estable de penetración total mostraron que la relación entre el ancho de la soldadura posterior y el ancho de la superficie de soldadura (proporción del ancho de la soldadura posterior) se puede utilizar para evaluar la formación de la soldadura y la estabilidad de las láminas de aleación de aluminio.
Al hacer coincidir adecuadamente la densidad de potencia del láser y la energía de la línea durante la soldadura láser de placas delgadas, se puede garantizar una cierta relación de ancho de soldadura, controlando efectivamente la porosidad de la soldadura.
Soldadura láser de doble punto
La soldadura láser de doble punto se refiere a un proceso de soldadura en el que dos rayos láser enfocados actúan simultáneamente sobre el mismo baño de soldadura. En la soldadura láser de penetración profunda, una de las principales causas de la porosidad de la soldadura es el cierre de gas en el pequeño orificio del baño de soldadura.
Cuando se utiliza soldadura láser de doble punto, la apertura del pequeño orificio aumenta debido a la influencia de dos fuentes de luz, lo que facilita el escape del vapor metálico interno y mejora la estabilidad del pequeño orificio, reduciendo así la porosidad de la soldadura.
Los estudios sobre soldadura láser de aleaciones de aluminio A356, AA5083, 2024 y 5A90 han demostrado que la soldadura láser de doble punto puede reducir significativamente la porosidad de la soldadura.
Soldadura por arco láser híbrida
La soldadura por arco láser híbrida es un método de soldadura en el que tanto el láser como el arco influyen en el mismo baño fundido. Normalmente, el láser es la principal fuente de calor y la interacción entre el láser y el arco aumenta la penetración y la velocidad de soldadura de la soldadura láser al tiempo que reduce la precisión del conjunto de soldadura.
El uso del alambre de aporte ayuda a controlar la microestructura y propiedades de las uniones soldadas, y el efecto auxiliar del arco mejora la estabilidad de los orificios de soldadura láser, contribuyendo a la reducción de la porosidad de la soldadura.
En el proceso de soldadura por arco láser híbrido, el arco afecta la nube de vapor/plasma de metal generada por el proceso láser, promoviendo la absorción de energía láser y la estabilidad de los agujeros pequeños.
Los estudios sobre la soldadura por arco láser híbrido de aleaciones de aluminio han confirmado su eficacia para reducir la porosidad de la soldadura.
soldadura por láser de fibra
El efecto ojo de cerradura en la soldadura láser de penetración profunda se produce debido a la fuerte vaporización del metal bajo la influencia del láser. La fuerza de la vaporización del metal está estrechamente relacionada con la densidad de potencia del láser y la calidad del haz, lo que afecta tanto la penetración de la soldadura láser como la estabilidad del ojo de cerradura.
Seiji et al. estudió el láser de fibra de alta potencia sobre acero inoxidable SUS304 y demostró que:
Durante la soldadura a alta velocidad, el baño fundido se alarga, se controlan las salpicaduras, las fluctuaciones del orificio pequeño son estables y no hay burbujas en la punta del orificio pequeño. Cuando se utiliza un láser de fibra para soldar a alta velocidad aleaciones de titanio y aleaciones de aluminio, también se puede producir una soldadura sin poros.
Investigación sobre tecnología de control de gas protector para soldadura láser de fibra de aleación de titanio realizada por Allen et al. así es como es:
Al controlar la posición del gas protector de soldadura, es posible evitar la absorción de gas, acortar el tiempo de cierre del orificio pequeño, estabilizar el orificio de soldadura pequeño y cambiar el comportamiento de solidificación del baño fundido, reduciendo así la porosidad de la soldadura.
Soldadura por láser pulsado
En comparación con la soldadura láser continua, el modo pulsado de la salida del láser puede mejorar el flujo periódico y constante del baño fundido, lo que ayuda a liberar burbujas y reducir la porosidad de la soldadura.
TY Kuo y SL Jeng investigaron el impacto del modo de salida de potencia de soldadura láser YAG en la porosidad y las características de las soldaduras hechas de acero inoxidable SUS 304L y superaleación Inconel 690.
Los resultados indican que para la soldadura por láser pulsado de onda cuadrada, a medida que la potencia base aumenta a 1700 W, la porosidad de la soldadura disminuye al aumentar la amplitud del pulso ΔP. En concreto, la porosidad del acero inoxidable disminuye del 2,1% al 0,5%, y la de la superaleación disminuye del 7,1% al 0,5%.
Tecnología de tratamiento de composites post-soldadura
En aplicaciones prácticas de ingeniería, a pesar del riguroso tratamiento superficial antes de la soldadura y de un proceso de soldadura estable, la porosidad sigue siendo un problema común en la soldadura láser de aleaciones de aluminio.
Por lo tanto, los métodos de tratamiento post-soldadura para eliminar la porosidad son cruciales.
Actualmente, el principal método utilizado es la soldadura modificada.
Uno de esos métodos para eliminar la porosidad interna y de contracción en piezas fundidas de aleaciones de aluminio es la tecnología de prensado isostático en caliente.
Al combinar esto con el tratamiento térmico bajo tensión después de la soldadura láser de aleación de aluminio, se forma un proceso compuesto de prensado isostático en caliente y tratamiento térmico de componentes de soldadura láser de aleación de aluminio. Esto no sólo elimina la porosidad de la soldadura sino que también mejora el rendimiento de la unión.
Conclusión
La aplicación de la soldadura láser de alta potencia a aleaciones de aluminio todavía presenta muchos desafíos debido a sus características únicas.
Uno de los principales desafíos es controlar los defectos de porosidad de la soldadura y mejorar la calidad de la soldadura.
Para mejorar la estabilidad del proceso de soldadura y controlar la porosidad en la soldadura láser de aleaciones de aluminio, es esencial un enfoque integral que considere todos los aspectos, desde la presoldadura hasta el proceso de soldadura y el tratamiento posterior a la soldadura.
Para afrontar este desafío, se han desarrollado varias tecnologías y procesos nuevos, incluida la limpieza láser antes de soldar, la optimización de los parámetros del proceso de soldadura mediante el control de la relación de ancho posterior, la soldadura láser de doble haz, la soldadura híbrida de arco-láser, la soldadura láser pulsada y el láser de fibra óptica. . Soldadura.