1. ¿Qué es la fatiga ?
La fatiga se refiere a la disminución del rendimiento estructural de los materiales, particularmente los metales, cuando se los somete a tensiones o deformaciones cíclicas, lo que en última instancia conduce a la falla.
La falla por fatiga es una forma predominante de falla.
Las investigaciones muestran que las fallas por fatiga son responsables del 60 al 70% de las fallas en diversas máquinas.
La falla por fractura por fatiga se clasifica como falla por fractura frágil de baja tensión y es un desafío detectar una deformación plástica significativa durante la fatiga, ya que resulta principalmente de la deformación plástica local y ocurre en las debilidades estructurales.
Aunque la frecuencia puede desempeñar un papel en la falla por fatiga, generalmente está relacionada con el número de ciclos más que con la frecuencia.
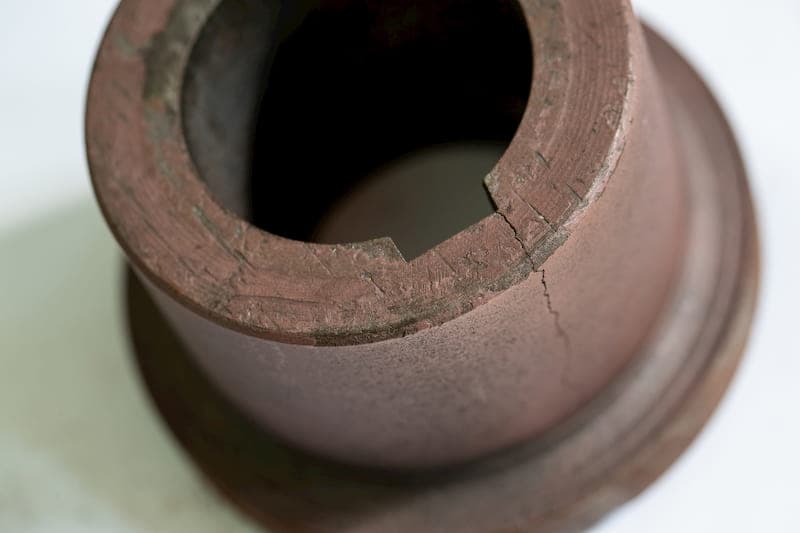
Según las características de las tensiones que provocan la falla por fatiga, se puede dividir en dos categorías:
- Fatiga mecánica causada por estrés mecánico, y
- Fatiga térmica causada por estrés térmico alterno.
En cuanto a los tiempos de ciclo, la fatiga se puede dividir en:
- ciclo alto,
- ciclo bajo y
- Fatiga de ciclo ultra alto.
En términos de propiedades de carga, la fatiga se puede clasificar en:
- Fatiga por tensión-compresión,
- fatiga torsional y
- Fatiga por flexión.
Y según el entorno de trabajo de la pieza, la fatiga se puede dividir en:
- fatiga por corrosión,
- Fatiga a bajas temperaturas y
- Fatiga por altas temperaturas.
Es importante señalar que la resistencia de los materiales y estructuras ante el daño por fatiga se denomina “límite de fatiga”.
2. Tipos de fatiga
1. Fatiga por impacto
Se refiere a la fatiga causada por cargas de impacto repetidas.
Cuando el número de impactos, N, es inferior a 500 a 1000, las piezas pueden dañarse y la forma de fractura de las piezas será similar a la de un solo impacto.
Cuando el número de impactos supera los 105, la fractura de la pieza se clasifica como fractura por fatiga, mostrando características típicas de la fractura por fatiga.
En el cálculo del diseño, si el número de impactos excede 100, la resistencia debe calcularse utilizando un método similar al análisis de fatiga.
2. Fatiga de contacto
Bajo la influencia de la tensión de contacto cíclica, las piezas sufrirán daños graduales y permanentes a nivel local.
Después de un cierto número de ciclos, el desarrollo de corrosión, incrustaciones superficiales o incrustaciones profundas en la superficie de contacto se denomina fatiga de contacto.
La fatiga por contacto es un modo de falla común en engranajes, cojinetes y árboles de levas.
3. Fatiga térmica
Los materiales o piezas que se fatigan debido al estrés térmico cíclico provocado por los cambios de temperatura se denominan fatiga térmica.
Los cambios cíclicos de temperatura dan como resultado cambios cíclicos en el volumen del material.
Cuando se restringe la capacidad del material para expandirse o contraerse libremente, se genera tensión térmica cíclica o deformación térmica cíclica.
Básicamente existen dos tipos de estrés térmico:
La expansión y contracción térmica de las piezas se ven afectadas por las limitaciones de las piezas fijas, lo que genera tensión térmica.
En ausencia de restricciones externas, las temperaturas inconsistentes entre partes de dos partes dan como resultado una expansión y contracción térmica desigual, lo que resulta en estrés térmico.
Las fluctuaciones de temperatura también provocan cambios en la estructura interna del material, reduciendo su resistencia y plasticidad.
En condiciones de fatiga térmica, la distribución de la temperatura no es uniforme, lo que provoca deformaciones plásticas graves, grandes gradientes de temperatura y concentraciones de deformación térmica.
Cuando la deformación térmica excede el límite elástico, la relación entre la tensión térmica y la deformación térmica ya no es lineal y debe tratarse como una relación elastoplástica.
Las grietas por fatiga térmica comienzan en la superficie y se extienden hacia adentro, perpendicularmente a la superficie.
La tensión térmica es proporcional al coeficiente de expansión térmica, y coeficientes mayores conducen a una mayor tensión térmica.
Por tanto, la selección de materiales debe considerar la combinación de materiales sin que las diferencias en los coeficientes de expansión térmica sean demasiado grandes.
En las mismas condiciones de deformación térmica, cuanto mayor es el módulo elástico del material, mayor es el estrés térmico.
Cuanto mayor sea la variación en el ciclo de temperatura, es decir, la diferencia entre las temperaturas límite superior e inferior, mayor será el estrés térmico.
Cuanto menor es la conductividad térmica del material, más pronunciado es el gradiente de temperatura y mayor es el estrés térmico durante una rápida aceleración o enfriamiento.
4. Fatiga por corrosión
La fatiga causada por la acción conjunta de un medio corrosivo y una tensión cíclica se denomina fatiga por corrosión.
El daño causado por la acción combinada de un medio corrosivo y tensión estática se denomina fisuración por corrosión bajo tensión.
La principal diferencia entre los dos es que la corrosión por tensión ocurre solo en ambientes de corrosión específicos, mientras que la fatiga por corrosión puede ocurrir en cualquier ambiente de corrosión bajo la influencia de tensiones cíclicas.
Para el agrietamiento por corrosión bajo tensión, existe un factor de intensidad de tensión crítico conocido como KISCC. Si el factor de intensidad de tensión KI es menor o igual que KISCC, no se producirá fisuración por corrosión bajo tensión. Sin embargo, no existe un factor de intensidad de tensión crítico para la fatiga por corrosión y se producirá fractura mientras exista tensión cíclica en un ambiente corrosivo.
La diferencia entre fatiga por corrosión y fatiga por aire es que, con la excepción del acero inoxidable y el acero nitrurado, las superficies de las piezas mecánicas sujetas a fatiga por corrosión se decoloran. Además, la fatiga por corrosión produce un gran número de grietas en lugar de una sola. La curva SN de fatiga por corrosión no tiene una porción horizontal.
Es importante señalar que el límite de fatiga por corrosión es sólo condicional y se basa en una vida útil determinada. Los factores que afectan la resistencia a la fatiga por corrosión son más complejos que los que afectan la fatiga del aire. Por ejemplo, aunque la frecuencia de la prueba de fatiga no tiene ningún efecto sobre el límite de fatiga en el aire cuando es inferior a 1000 Hz, sí tiene un impacto sobre la fatiga por corrosión en todo el rango de frecuencia.
3. Vida cansada
Cuando falla un material o componente mecánico, la vida útil total generalmente consta de tres partes:
1. Vida de iniciación del crack
Un número significativo de estudios de ingeniería han demostrado que la vida de inicio de grietas de los componentes mecánicos representa una gran parte, hasta el 90%, de la vida total de fatiga durante el servicio real.
2. Vida estable de crecimiento de grietas
En la mayoría de los casos, cuando la profundidad de una microgrieta alcanza aproximadamente 0,1 mm, crecerá continuamente a lo largo de la porción del material o componente.
3. La inestabilidad se extiende hasta la vida de la fractura.
4. Forma de fatiga de los materiales metálicos.
La fatiga de materiales metálicos incluye principalmente lo siguiente:
- Deformación Plástica General;
- Deformación Plástica por Fatiga de Bajo Ciclo;
- Deformación plástica debido a fatiga de alto ciclo;
- Microdeformación plástica del tamaño del cristal por fatiga de ciclo ultraalto.
5. Factores que afectan la resistencia a la fatiga de materiales y estructuras.
1. Estrés medio
A medida que aumenta la tensión media (tensión estadística), la tensión dinámica antifatiga de los materiales disminuye.
Para fuerzas con características iguales, cuanto mayor sea la tensión promedio σ i, menor será la amplitud de la tensión σ a para una vida determinada.
2. Concentración de estrés
Debido a las exigencias de las condiciones de trabajo o las técnicas de procesamiento, los componentes suelen tener características como escalones, pequeños orificios, chaveteros, etc. Estas características provocan cambios bruscos en la sección transversal, lo que lleva a una concentración de tensiones locales, lo que reduce significativamente el límite de fatiga del material.
Los experimentos han demostrado que la reducción del límite de fatiga no es directamente proporcional al factor de concentración de tensiones.
Para predecir con precisión el comportamiento a la fatiga de los componentes mecánicos, es necesario estimar la vida de inicio de grieta en regiones de alta tensión o defectos de fabricación.
3. Estrés residual
La revisión de la literatura destaca que es relevante considerar sólo el impacto de la tensión residual sobre la resistencia a la fatiga del metal bajo fatiga de ciclo alto. Esto se debe a que la tensión residual se relaja mucho bajo la alta amplitud de deformación de la fatiga de ciclo bajo y, por lo tanto, tiene poco efecto sobre la fatiga de ciclo bajo.
La tensión de compresión residual superficial es ventajosa para componentes sujetos a cargas axiales y cuando el agrietamiento por fatiga se origina en la superficie. Sin embargo, es importante ser consciente del problema de la relajación de la tensión residual causada por la fluencia de la tensión de tracción residual en la región del núcleo después de aplicar la carga externa.
El efecto de la tensión residual sobre la resistencia a la fatiga de los componentes es muy significativo. Esto se debe a que la tensión residual contiene concentración de tensión y tiene un mayor impacto en el crecimiento de las grietas por fatiga.
Sin embargo, la concentración de tensiones residuales no sólo está relacionada con la geometría de la entalla sino también con las propiedades del material.
4. Efecto tamaño
El valor límite de fatiga de un material, denominado σ-1, generalmente se determina utilizando una muestra pequeña, con un diámetro que normalmente oscila entre 7 y 12 mm. Sin embargo, la sección transversal de los componentes reales suele ser mayor que este tamaño.
Las pruebas han demostrado que el límite de fatiga disminuye a medida que aumenta el diámetro de la muestra.
En particular, el límite de fatiga cae más rápidamente en los aceros de alta resistencia que en los de baja resistencia.
5. Estado de la superficie de las extremidades
La superficie de un componente es propensa a producir grietas por fatiga y la tensión superficial de un componente bajo cargas de flexión o torsión alternas es mayor.
La rugosidad de la superficie de la pieza y la presencia de marcas de herramientas de mecanizado pueden afectar su resistencia a la fatiga.
Los daños en la superficie, como marcas de herramientas o raspaduras, actúan como una muesca en la superficie, provocando la concentración de tensiones y reduciendo el límite de fatiga.
Cuanto mayor sea la resistencia del material, más sensible será a las entalladuras y mayor será el efecto de la calidad de la superficie mecanizada sobre el límite de fatiga.
6. Factores ambientales
El comportamiento de fatiga de los materiales metálicos está influenciado por el entorno líquido o gaseoso circundante. La fatiga por corrosión” se refiere a la respuesta de los materiales metálicos al efecto combinado de un medio corrosivo y cargas cíclicas, típicamente en un ambiente acuoso.
Diferentes condiciones ambientales, como fatiga por corrosión, fatiga por baja temperatura, fatiga por alta temperatura y variación en la presión del aire y la humedad, pueden afectar el comportamiento de fatiga de los materiales. En ambientes atmosféricos, los ciclos de falla de un material son típicamente más cortos que en ambientes de vacío, y la vida de inicio de grietas en ambientes de vacío es más larga.
Cuando la pieza opera cerca de la presión de aire crítica (Pcr), su vida a fatiga se vuelve muy sensible. La vida a fatiga de los materiales en ambientes atmosféricos, que generalmente es más corta que en ambientes de vacío, disminuye al aumentar la temperatura, lo que acelera el crecimiento de grietas.
La humedad ambiental tiene un impacto significativo en la durabilidad del acero al cromo de alta resistencia. El vapor de agua, especialmente a temperatura ambiente, puede debilitar la tenacidad a la fractura de la mayoría de los metales y aleaciones, según el nivel de tensión, la tasa de carga y otras condiciones de carga.
Existe una fuerte interacción entre la microestructura y el medio ambiente, y el entorno gaseoso afecta la morfología de la fractura y el mecanismo de deslizamiento de la dislocación. El medio ambiente también interactúa con el cierre de grietas, particularmente en la región cercana al umbral. El impacto del medio ambiente depende de la morfología de la superficie de la grieta, especialmente en la dirección de la profundidad.
A bajas temperaturas, la resistencia del metal aumenta mientras que la plasticidad disminuye. Como resultado, la resistencia a la fatiga de ciclos altos de muestras lisas es mayor a bajas temperaturas, pero la resistencia a la fatiga de ciclos bajos es menor. Para muestras con muescas, la tenacidad y la plasticidad disminuyen aún más. Las bajas temperaturas pueden ser particularmente dañinas para las entalladuras y grietas, ya que la longitud crítica de la grieta por fatiga en el momento de la fractura disminuye drásticamente.
La “fatiga generalizada por altas temperaturas” se refiere a la fatiga que ocurre a temperaturas superiores a lo normal. Aunque algunas piezas pueden funcionar a temperaturas superiores a la temperatura ambiente, la fatiga por alta temperatura sólo se observa cuando la temperatura supera 0,5 veces el punto de fusión (Tm), o por encima de la temperatura de recristalización. A estas temperaturas elevadas, se produce fatiga mecánica y de fluencia, lo que da como resultado fatiga a alta temperatura.
7. Tipo de carga
El orden del límite de fatiga bajo diferentes cargas es: flexión rotativa
En un ambiente corrosivo, el impacto de la frecuencia de carga en la progresión de las grietas es evidente.
A temperatura ambiente y en un entorno de prueba, las frecuencias convencionales (0,1-100 Hz) tienen un impacto mínimo en el crecimiento de grietas en acero y latón.
En general, si la frecuencia de carga de prueba es inferior a 250 Hz, la influencia de la frecuencia en la vida a fatiga de los materiales metálicos es mínima.
8. Defectos materiales
Las grietas generalmente se originan en la superficie, como en la soldadura (ojal), el acero fundido (suelto) o en el subsuelo (grandes inclusiones que alteran el campo de deformación local), pero rara vez se encuentran en el interior.
La iniciación de grietas también depende del número, tamaño, tipo y distribución de las inclusiones, así como de la dirección de las fuerzas externas aplicadas.
No se debe descuidar la fuerza de unión entre las inclusiones y la matriz.
Las microfisuras son los defectos más peligrosos de los materiales, con una vida útil de un millón de ciclos. Las microestructuras controlan la vida útil de los materiales, con una vida útil de mil millones de ciclos.
Dado que la probabilidad de defectos en materiales microdimensionados es mucho mayor que en la superficie del material, la probabilidad de que se inicien grietas bajo cargas de fatiga de ciclo ultra alto en el material es naturalmente mayor que en la superficie.
Los materiales frágiles no sufren reducción de tensión ni endurecimiento por trabajo.
Si hay una muesca, puede producirse una fractura bajo una tensión nominal baja.
Se observó que cuando existe una entalla, el límite de fatiga del metal disminuye, con mayor impacto en el límite de fatiga en materiales con menor plasticidad.
9. Método de procesamiento
Se ha enfatizado en la literatura que el proceso de preparación de muestras de fatiga es un factor crítico que contribuye a la variabilidad de los resultados de las pruebas.
Por ejemplo, los procesos de torneado, fresado, enderezamiento y otros métodos de mecanizado afectan la calidad final de la preparación de la muestra.
Esto se debe a que el método de preparación y los factores del tratamiento térmico pueden afectar el comportamiento a la fatiga de los materiales, especialmente el tratamiento térmico, lo que dificulta la obtención de resultados consistentes incluso con el mismo lote, tamaño y morfología de las pruebas.
Está claro que los factores de producción y procesamiento de piezas harán que la vida útil real de las piezas se desvíe del valor de vida esperado calculado mediante análisis.
10. Propiedades de los materiales.
La dureza del material es un factor clave en la resistencia a la fatiga de ciclo alto (cuando N > 10 6 ), mientras que la tenacidad es un indicador importante para la fatiga de ciclo medio y bajo.
El acero de alta resistencia tiene baja tenacidad y, por lo tanto, pobre comportamiento a la fatiga en condiciones de alta tensión. Sin embargo, tiene buena resistencia a la fatiga en condiciones de baja tensión.
El acero de baja resistencia tiene un rendimiento de fatiga moderado.
En general, cuanto mayor es el módulo de elasticidad, más lenta es la tasa de crecimiento de las grietas.
El efecto del tamaño de grano sobre el crecimiento de grietas es significativo sólo en casos extremos (△ K → △ Kth y △ Kmax → △ KC) y tiene poco impacto sobre el crecimiento de grietas a velocidad media.
La velocidad de propagación está relacionada con la tenacidad a la fractura KIC (o KC).
Es ampliamente aceptado que aumentar la tenacidad del material disminuirá la tasa de crecimiento de grietas.
6. Discreción de los datos de las pruebas de fatiga.
La dispersión de los datos de las pruebas de fatiga se puede atribuir al equipo de prueba y a la muestra misma.
Según la literatura, un error del 3% en la carga nominal en relación con la carga real puede resultar en un error del 60% en la vida a fatiga y, en casos extremos, un error del 120% en la vida a fatiga.
Aunque un error del 3% es aceptable en las máquinas de ensayo de fatiga, se observa que no hay una dispersión significativa en los ensayos de fallo estático, incluso para materiales con una gran dispersión de resistencia, como los materiales de fundición y el vidrio.
La variabilidad en los resultados de las pruebas de fatiga está influenciada por las propiedades del material, incluidas las propiedades inherentes del material y el proceso de preparación de la prueba y el entorno externo. El proceso de preparación, especialmente el tratamiento térmico, es el factor más crítico que conduce a la dispersión de datos.
Las inclusiones y las partículas de segunda fase en los materiales también contribuyen de manera importante a la dispersión de datos; sin embargo, aún se desconoce el mecanismo detrás de esto.
7. Desarrollo de métodos de diseño de fatiga estructural.
Método de vida segura:
La tensión de diseño es inferior al límite de fatiga y se considera que no existe ningún defecto en la estructura.
Método a prueba de fallos:
La tensión de diseño está relacionada con la resistencia residual en el caso de defectos planos, y este método de diseño se adapta a niveles aceptables de tales defectos.
Método de violación de seguridad:
Ciertamente, se permite la propagación de grietas que se pueden predecir con certeza.
Método de falla local:
La tecnología de pruebas de fatiga de ciclo ultraalto, que surgió en la década de 1990, ha demostrado que incluso los microdefectos más pequeños, como la inclusión de escoria, la porosidad y los granos grandes formados durante la forja, pueden afectar significativamente la vida útil de los materiales.
Para materiales de acero, cuando no se dispone de datos de prueba de fatiga, se puede dibujar una curva SN aproximada basada en el límite de resistencia a la tracción del material.
Este método de estimación, que asocia el límite de fatiga con la resistencia a la tracción y el alargamiento de rotura de la muestra, es muy preciso.
En el análisis de fatiga de materiales y estructuras, es esencial confiar en los resultados de las pruebas, en lugar de simplemente en cálculos elástico-plásticos, para obtener datos precisos y confiables.