Las láminas de metal se doblan y forman utilizando una máquina dobladora de placas. La pieza de trabajo se coloca en la máquina y la palanca de elevación se utiliza para levantar la zapata de freno, lo que permite posicionar la pieza de trabajo. A continuación se baja la zapata de freno sobre la pieza de trabajo y se presiona la palanca dobladora para doblar la chapa.
El radio de curvatura mínimo está determinado por la ductilidad y el espesor del metal que se está formando. Para láminas de aluminio, el radio de curvatura debe ser mayor que el espesor de la lámina.
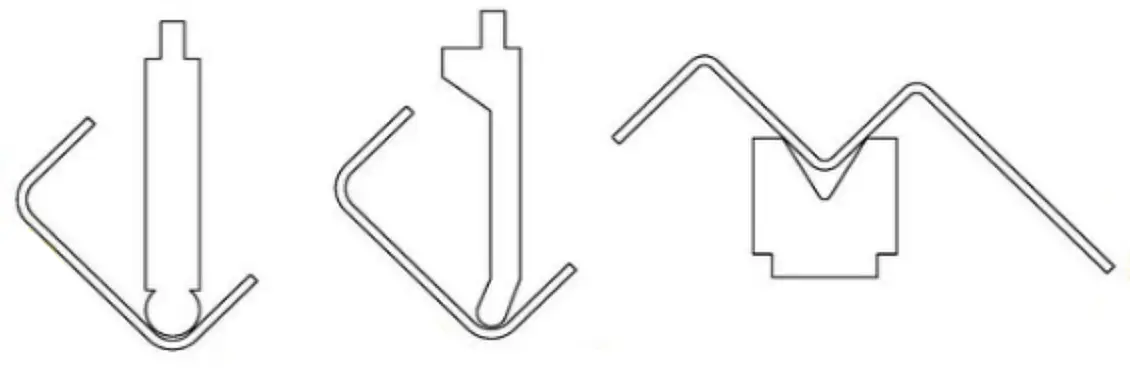
Debido a la elasticidad, el ángulo de flexión del metal es ligeramente mayor que el ángulo requerido.
El doblado de láminas de metal generalmente se realiza en un taller de procesamiento de metales. El procesamiento de chapa implica una serie de técnicas como el doblado, remachado y soldadura de materiales metálicos.
Los problemas comunes que ocurren durante este proceso y sus correspondientes soluciones se analizan a continuación.
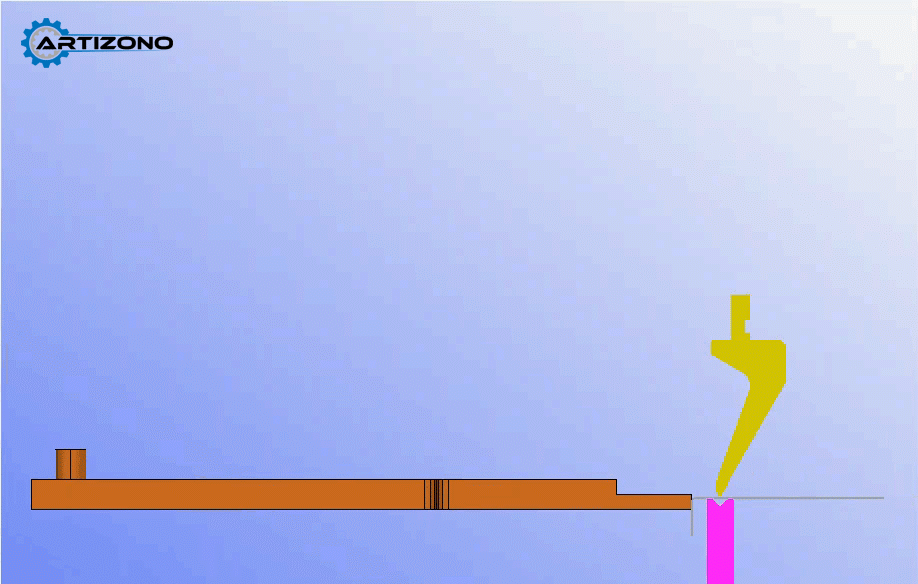
1. Desafíos al doblar ranuras y piezas múltiples
Durante el proceso de doblado de estas piezas, el ancho de la ranura es mayor que la altura de la pata, provocando interferencia entre un extremo de la pieza y el troquel superior o deslizador de la plegadora. Esto hace imposible garantizar las dimensiones de la pieza, como se muestra en la Figura 2.
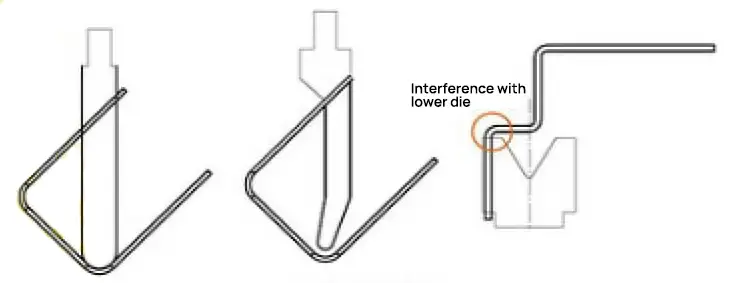
Predicción de interferencias en el plegado de chapa metálica
Cuando se trata de piezas de chapa de precisión de patas altas, determinar si se puede completar el doblado requiere varios cálculos, con las dimensiones correspondientes indicadas en la Figura 3.
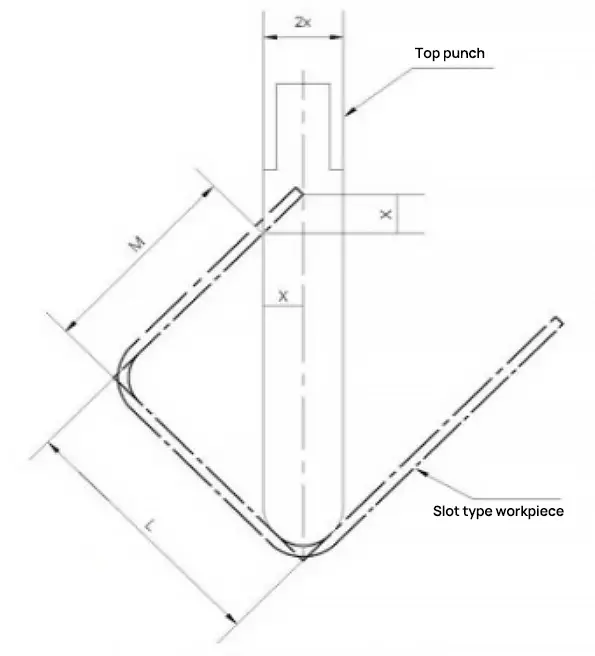
Si LM<1,5x, la pieza se puede doblar sin interferencias. Si LM>1,5x, la pieza de trabajo no se puede doblar, ya que esto provocará interferencias.
Soluciones a problemas de interferencia
(1) Si una pieza de trabajo tipo ranura sufre interferencia de flexión, se puede seleccionar un troquel superior con cuello de cisne para doblar. Esto evita la interferencia entre el borde de doblado de la pieza y la plegadora o troquel superior, asegurando las dimensiones de doblado de la pieza, como se muestra en la Figura 4.
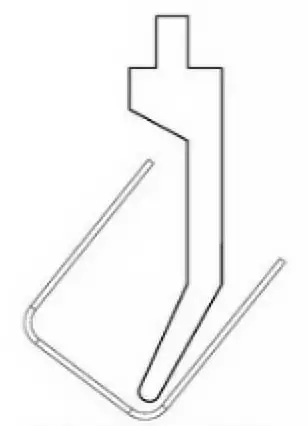
(2) Si una pieza de trabajo tipo ranura sufre interferencia de flexión y no hay matrices superiores de cuello de cisne adecuadas disponibles, se puede realizar un predoblado inverso en la mitad del plegado sin afectar los requisitos de uso, como se muestra en la Figura 5. Al aumentar artificialmente el ángulo de flexión, la pieza se puede doblar normalmente. Luego, se puede utilizar un troquel de llanta pinchada para presionar el área de predoblado para garantizar que se cumplan los requisitos de calidad del producto.
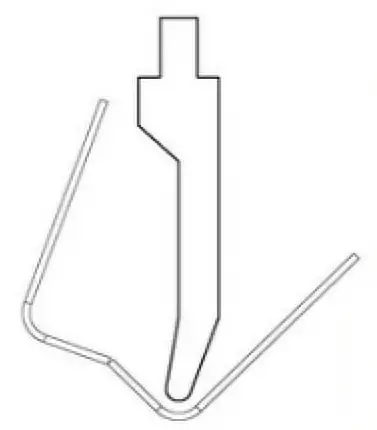
(3) Al doblar piezas de trabajo con múltiples pliegues, si H1>H o B
① Seleccione un troquel inferior de grandes dimensiones con H>H1 para garantizar la flexión normal de la pieza de trabajo;
② Seleccione una abertura de matriz inferior con B>V/2 para garantizar la flexión normal de la pieza de trabajo;
③ Si no hay un troquel inferior de grandes dimensiones, cambie la secuencia de doblado. Deforme previamente el doblez medio hasta un cierto ángulo, luego doble en el lado corto, forme el tercer doblez y finalmente sujete el doblez medio al tamaño y ángulo requeridos, asegurando el tamaño del proceso de la pieza, como se muestra en la Figura 6.
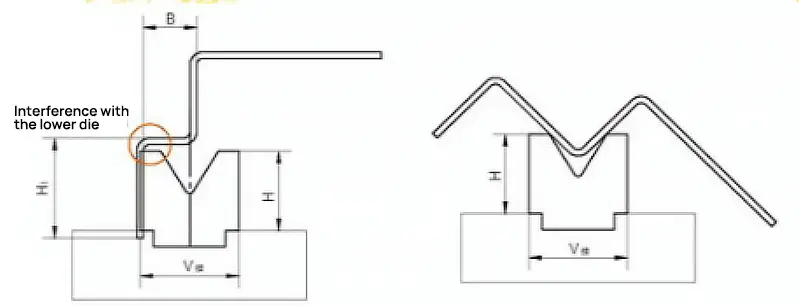
2. Agrietamiento por flexión
(1) Análisis de causa
A menudo, se producen grietas por flexión en la superficie de tracción de las piezas de chapa durante el plegado, lo que daña las propiedades mecánicas de la pieza y no cumple con los requisitos de uso, lo que provoca el desmantelamiento de la pieza y pérdidas económicas. Las principales razones son:
① La chapa tiene una estructura cristalina especial y una dirección de rodadura de la veta, y doblarse paralelamente a la dirección de la veta puede causar fácilmente fracturas;
② El radio de curvatura R elegido es demasiado pequeño;
③ El ángulo R de la ranura en forma de V del troquel inferior es pequeño;
④ El rendimiento del material es deficiente.
(2) Medidas preventivas
① Al cortar, gire la hoja para cortar en la dirección perpendicular a la curva (es decir, la dirección de curvatura del material es perpendicular a la fibra);
② Aumente el ángulo R del troquel superior;
③ Utilice un troquel inferior con un ángulo R grande para el procesamiento;
④ Elija materiales de alto rendimiento.
3. El borde doblado no es recto y el tamaño es inestable.
Análisis de causa:
- sin línea presionada ni predoblada.
- presión de material inadecuada
- filete de matriz convexo-cóncavo disimétrico y presión de flexión desigual
- baja estatura
Soluciones
- Diseño de líneas de prensado o técnicas de predoblado.
- aumentar la fuerza de elevación
- Hueco uniforme en matriz cóncava-convexa y filete pulido
- hacer que la altura sea mayor o igual al tamaño mínimo
4. La pieza de trabajo se raspa después de doblarla.
Análisis de causa:
- superficie del material irregular
- Radio de curvatura de la matriz convexa demasiado pequeño.
- espacio de flexión muy pequeño
Soluciones
- mejorar la suavidad de la matriz cóncava
- aumentar el radio de curvatura de la matriz convexa
- ajustar el espacio de flexión
5. Hay grietas en los ángulos de flexión.
Análisis de causa:
- radio de curvatura muy pequeño
- grano del material paralelo a la línea de plegado
- rebaba de la hoja de trabajo que se extiende hacia afuera
- mala remodelabilidad del metal
Soluciones
- aumentar el radio de curvatura de la matriz convexa
- cambiar el diseño de supresión
- hacer rebabas en el filete interior de la pieza de trabajo
- recocido o uso de material blando
6. La flexión provoca la deformación del agujero.
Análisis de causa:
Cuando se utiliza el doblado elástico para posicionar el orificio, la parte exterior del brazo doblador se tira por fricción sobre la superficie del molde cóncavo y la superficie exterior de la pieza de trabajo, deformando el orificio de posicionamiento.
Soluciones
- empleando flexión de formas
- aumentar la presión de cobertura
- agregue una manta de grabado a la placa de cubierta para aumentar la fricción y evitar que la pieza de trabajo se deslice al doblarse
7. La superficie de flexión es más delgada.
Análisis de causa:
- filete de molde cóncavo-convexo muy pequeño
- brecha de matriz convexa-cóncava muy pequeña
Soluciones
- aumentar el radio de filete de la matriz cóncava-convexa
- ajustar la holgura de la matriz cóncava-convexa
8. La superficie de la pieza de trabajo sobresale o es desigual.
Análisis de causa:
Bajo tensión en la dirección circunferencial, la superficie exterior del material se contrae mientras que la superficie interior se estira durante la flexión, formando protuberancias en la dirección de flexión.
Soluciones
- Proporcionar una presión adecuada al troquel cóncavo-convexo en la etapa final de estampado.
- hacer que el radio del ángulo redondo cóncavo sea igual al del círculo exterior de la pieza de trabajo
- optimizar técnicas
9. La parte cóncava es irregular en la parte inferior.
Análisis de causa:
- material desigual
- Área de contacto pequeña entre la cubierta y el material o fuerza de elevación inadecuada.
- sin dispositivo de soporte de material en la matriz cóncava
Soluciones
- materiales de nivelación
- Ajuste el dispositivo de soporte del material y aumente la fuerza de elevación.
- aumentar o corregir el dispositivo de soporte material
- aumentar los procesos de modelado
10. Los ejes de los orificios de ambos lados están desalineados después de doblarlos.
Análisis de causa:
El rebote del material cambia el ángulo de curvatura, desalineando la línea central.
Soluciones
- aumentar el proceso de corrección
- mejorar la estructura del modelo de flexión para reducir el rebote del material
11. No se puede garantizar la posición precisa del orificio después de doblarlo.
Análisis de causa:
- tamaños de despliegue incorrectos
- retorno elástico del material
- posicionamiento inestable
Soluciones
- calcular el tamaño del espacio en blanco con precisión
- aumentar el proceso de corrección o mejorar la estructura de la matriz de flexión
- cambiar los métodos de procesamiento o mejorar el posicionamiento
12. La línea de doblez no es paralela al centro de dos agujeros.
Análisis de causa:
Cuando la altura de flexión es menor que la altura mínima de flexión, la parte doblada se expande.
Soluciones
- aumentar la altura de la pieza a doblar
- mejorar las técnicas de flexiones
13. La deformación se produce en términos de ancho después de la flexión (la parte doblada ocurre una desviación del arco en ancho)
Análisis de causa:
La contracción inconsistente en profundidad y ancho de la pieza provoca torsión y deflexión.
Soluciones
- aumentar la presión de flexión
- aumentar el proceso de corrección
- asegurar un cierto ángulo entre los materiales y la dirección de flexión
14. La pieza de trabajo incisa se desvía hacia abajo
Análisis de causa:
La incisión hace que los dos bordes rectos se abran hacia los lados izquierdo y derecho, formando una desviación en la parte inferior.
Soluciones
- mejorar la estructura de la pieza
- aumente el margen de procesamiento en las incisiones para conectar las incisiones y luego corte el proceso después de doblar
15. Material deslizante durante el procesamiento.
Análisis de causa:
Al seleccionar la matriz de doblado, normalmente se elige un ancho de ranura en V de 4 a 6 veces el espesor del material (T). Sin embargo, si el tamaño del pliegue es inferior a la mitad del ancho de la ranura en V seleccionada, puede producirse deslizamiento.
Problema: La ranura en V seleccionada es demasiado grande.
Soluciones:
- Método de desviación de la línea central (mecanizado excéntrico). Cuando el tamaño del material a doblar sea inferior a la mitad de 4 a 6 veces T, increméntelo tanto como sea posible.
- Procesamiento de cumplimiento
- Doblar con una ranura en V pequeña y presionar con una ranura en V grande.
- Seleccione una ranura en V más pequeña.
16. El ancho del pliegue interior es más estrecho que el del molde estándar.
Análisis de causa:
El ancho estándar del troquel inferior de la plegadora debe ser de al menos 10 mm. Por tanto, el material a doblar debe tener un espesor inferior a 10 mm. Si la curva tiene un ángulo de 90 grados, su longitud no debe ser menor que √2(L + V/2) + T.
Para evitar el desplazamiento del molde y cualquier desperdicio resultante o accidentes de seguridad, el molde debe fijarse de forma segura a la base del molde, con excepción de cualquier grado de libertad hacia arriba.
Soluciones:
- Aumente el tamaño del pliegue negociando con el cliente y ampliando el pliegue interior.
- Procesamiento de moldes especiales.
- Utilice herramientas abrasivas, aunque esto aumenta los costes de procesamiento.
17. El agujero está demasiado cerca de la línea de doblez. La flexión hará que el agujero tire y gire el material.
Análisis de causa:
Suponga que la distancia desde el orificio hasta la línea de doblez es L. Si L es menor que (4 a 6) veces el espesor de la placa T dividido por 2, el material experimentará tensión. Esto se debe a que durante el proceso de flexión, la fuerza de tracción deforma el material, provocando tracción y distorsión.
El valor mínimo de L para diferentes espesores de lámina, basado en el ancho de ranura del molde estándar, es el siguiente:
Soluciones:
- Aumente el tamaño del pliegue y recorte el dobladillo después de formarlo.
- Amplíe el agujero hasta la línea de pliegue, pero sólo si no afecta la apariencia o la función y el cliente está de acuerdo.
- Utilice el procesamiento de secado o prensado.
- Procesar excéntricamente el molde.
- Modifique el tamaño del agujero.
18. La distancia L entre el borde dibujado y la línea de plegado es pequeña y la ubicación del borde dibujado se deforma después de doblarse.
Análisis de causa:
Cuando L es menor que (4 a 6) veces el espesor de la placa T dividido por 2, el material sufrirá deformación durante el proceso de doblado debido al contacto entre el material y el molde inferior.
Soluciones:
- Utilice el procesamiento de secado o prensado.
- Modificar el tamaño del material.
- Emplear procesamiento de moldes especiales.
- Procesar excéntricamente el molde.
19. El lado largo y plano se eleva después del aplanamiento.
Análisis de causa:
Es posible que el borde aplanador largo no se adhiera firmemente durante el proceso de aplanamiento, lo que provocará que se levante en los extremos. Esta pregunta depende en gran medida de la posición de aplanamiento, por lo que es importante prestar mucha atención a la posición de aplanamiento.
Soluciones:
- Primero doble el ángulo hacia arriba (como se muestra en el diagrama) antes de doblar el borde muerto y luego aplánelo.
- Aplanar en varios pasos.
- Presione el extremo primero para doblar el lado muerto hacia abajo.
- Aplana la parte de la raíz.
Precauciones:
La calidad del proceso de aplanamiento depende de las habilidades del operador, por lo que es importante prestar mucha atención a la situación real durante el aplanamiento.
20. El puente levadizo de gran altura es fácil de romper
Análisis de causa:
El material está muy estirado y fracturado debido a la gran altura del puente levadizo. Otras causas pueden incluir:
- Afilado insuficiente o esquinas de moldes especiales desafiladas.
- Baja tenacidad del material o puente levadizo estrecho.
Soluciones:
- Amplíe el orificio del proceso en un lado de la fractura.
- Aumentar el ancho del puente levadizo.
- Repare el ángulo R del molde especial y aumente la transición del arco.
- Agregue lubricante al puente levadizo. Tenga en cuenta que este método ensuciará la superficie de la pieza de trabajo y no se puede utilizar para piezas de trabajo AL, etc.
21. Durante el procesamiento de moldes especiales, el tamaño del procesamiento cambiará
Análisis de causa:
La pieza se desplaza hacia adelante durante el procesamiento debido a una fuerza de presión hacia adelante, lo que provoca un aumento en el pequeño ángulo L de la parte frontal.
Soluciones:
- Elimina todas las sombras de la imagen e intenta compensarlas tanto como sea posible.
- Reemplace las piezas desgastadas de autoposicionamiento del molde con marcos de retorno para un mejor posicionamiento.
22. El tamaño total de la pieza ciega (refiriéndose a la expansión) es demasiado pequeño o demasiado grande, lo que no concuerda con la superficie redonda.
Análisis de causa:
- Error de implementación del proyecto.
- Tamaño de alimentación incorrecto.
Soluciones:
- Calcula la desviación asignada a cada giro en función de la desviación total y el número de vueltas en la dirección del desvío.
- Si la tolerancia de distribución calculada está dentro del rango de tolerancia, la pieza se considera aceptable.
- Si el tamaño es demasiado grande, utilice una ranura en V pequeña.
- Si el tamaño es demasiado pequeño, utilice una ranura en V grande.
23. Descantillado o aflojamiento del agujero tras remachar y provocar deformación.
Análisis de causa:
- La fragmentación se produce debido a un pequeño ángulo R del orificio de extracción o a un exceso de rebabas en la brida.
- El remachado está flojo porque los orificios de extracción no están correctamente alineados.
- La deformación es causada por agujeros desalineados o un método de remachado incorrecto.
Soluciones:
- Utilice un punzón central con un ángulo R mayor y preste atención a las rebabas alrededor del orificio ciego al realizar el reborde.
- Aumente la presión, profundice el brochado y utilice un punzón central con un ángulo R mayor.
- Aborde la causa raíz de los agujeros desalineados y el método de remachado incorrecto.
24. El pasador de remachado está doblado o la pieza de trabajo está deformada después del remachado.
Análisis de causa:
- La pieza de trabajo no se aplana durante el procesamiento.
- Se aplica una fuerza desigual o una presión excesiva a la superficie inferior de la pieza de trabajo.
Soluciones:
- Aplana la pieza de trabajo presionando el pasador.
- Utilice una estructura de soporte.
- Reajustar la presión.
- Aumente el rango de tensión en la superficie inferior y reduzca el rango de fuerza en la superficie superior.
25. Los dos lados no son paralelos después de la flexión desplazada.
Análisis de causa:
- El molde no está calibrado correctamente.
- Las uniones del troquel superior e inferior no están ajustadas correctamente.
- Las caras superior e inferior del troquel no son idénticas.
Soluciones:
- Recalibrar el molde.
- Ajuste las articulaciones aumentándolas o disminuyéndolas.
- Utilice procesamiento excéntrico para el molde.
- Asegúrate de que el molde superior e inferior tengan la misma superficie.
26. El pliegue de la superficie del producto es demasiado profundo.
Análisis de causa:
- Pequeña ranura en V en la matriz inferior.
- Pequeño ángulo R de la ranura en V en la matriz inferior.
- El material es muy suave.
Soluciones:
- Utilice una ranura en V grande para el procesamiento.
- Utilice un molde con un ángulo R grande.
- Utilice relleno para doblar (con metal o poliuretano fundido).
27. El área cerca de la curva se deformó después de doblarse.
Análisis de causa:
La máquina funciona muy rápido durante el proceso de doblado, lo que hace que la velocidad de doblado hacia arriba durante la deformación de la pieza sea mayor que la velocidad a la que el operador sostiene la pieza con la mano.
Soluciones:
- Reducir la velocidad de funcionamiento de la máquina.
- Aumente la velocidad de retención manual del operador.
28. Las piezas AL son propensas a agrietarse cuando se doblan.
El material AL tiene tendencia a romperse a lo largo de líneas paralelas durante la flexión debido a su estructura cristalina especial.
Soluciones:
- Al darle forma, gire el material AL para que la dirección de flexión sea perpendicular a la textura y luego corte.
- Aumente el ángulo R del troquel superior.
Lectura relacionada: 12 soluciones a los problemas de doblado de chapa metálica
1 comentario
Como dobra Chapa com espessura de 8 mm se a tira estiver empenada