“Mecanizado CNC” se refiere al uso de herramientas de mecanizado de control numérico.
Debido a que está controlado por programación informática, el mecanizado CNC ofrece varios beneficios, como calidad constante, alta precisión, alta exactitud de repetición, la capacidad de mecanizar superficies complejas y mayor eficiencia.
Sin embargo, cabe señalar que la calidad final del producto mecanizado puede verse muy afectada por los factores humanos y la experiencia del operador durante el proceso de mecanizado real.
Veamos ahora diez valiosos consejos de mecanizado, resumidos por un operador de máquina CNC con más de una década de experiencia en el campo.
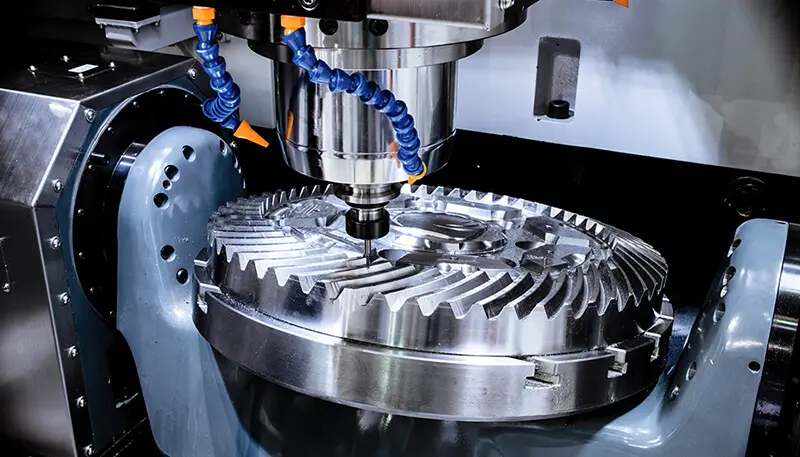
1 . ¿Cómo dividir los procesos de mecanizado CNC?
La división de los procesos de mecanizado CNC generalmente se puede realizar mediante los siguientes métodos:
Método de clasificación centrado en herramientas
El método de clasificación centrado en herramientas consiste en dividir los procesos en función de las herramientas utilizadas y utilizar la misma herramienta para mecanizar todas las piezas que se pueden completar. El segundo y tercer cuchillo se utilizan para completar otras piezas que se pueden rematar. Este enfoque reduce la cantidad de cambios de herramientas, minimiza el tiempo de inactividad y reduce los errores de posicionamiento innecesarios.
Clasificación por posición de procesamiento
Para piezas con muchos pasos de procesamiento CNC, la pieza de procesamiento se puede dividir en varias secciones según sus características estructurales, como forma interna, forma externa, superficie curva o plana, etc. seguido de agujeros; las geometrías simples se mecanizan antes que las complejas; y las piezas de baja precisión se procesan antes que aquellas con requisitos de alta precisión.
Clasificación por mecanizado CNC desbaste y fino.
Para piezas que son propensas a deformarse durante el mecanizado CNC de desbaste y fino, es necesario calibrar la forma debido a una posible deformación después del mecanizado de desbaste. Por lo tanto, los procesos generalmente se separan para mecanizado en desbaste y mecanizado fino.
En conclusión, al dividir el proceso, es importante considerar la estructura y capacidad de fabricación de las piezas, la función de la máquina herramienta, la cantidad de mecanizado NC de las piezas, los tiempos de instalación y la organización de producción unitaria. Además, el principio de concentración o dispersión del proceso debe determinarse en función de la situación real, pero debe ser razonable.
dos . ¿Qué principios se deben seguir al organizar la secuencia de mecanizado CNC?
La secuencia de mecanizado debe planificarse en función de la estructura y estado de las piezas, así como de los requisitos de posicionamiento y sujeción, con foco en evitar daños a la rigidez de la pieza. Se deben seguir los siguientes principios al organizar la secuencia:
- El procesamiento CNC del proceso anterior no debe interferir con el posicionamiento y fijación del proceso siguiente. También se debe considerar el proceso intercalado general del procesamiento de máquinas herramienta.
- Primero se debe mecanizar la forma interna y la cavidad, seguido del mecanizado del contorno.
- Los procesos de mecanizado CNC con el mismo modo de posicionamiento y sujeción o la misma herramienta deben agruparse para reducir el número de posicionamientos repetidos, cambios de herramienta y movimientos de la placa de prensa.
- Cuando se ejecutan varios procesos en la misma configuración, se debe ejecutar primero el proceso que tenga el menor impacto en la rigidez de la pieza.
3 . ¿A qué aspectos debemos prestar atención a la hora de determinar cómo arreglar la pieza?
Al determinar el punto de referencia de posicionamiento y el esquema de fijación, se deben tener en cuenta los cuatro puntos siguientes:
- Objetivo estandarizar el benchmark utilizado en los cálculos de diseño, procesamiento y programación.
- Minimizar al máximo el número de tiempos de sujeción e intentar realizar mecanizados CNC en todas las superficies a mecanizar después de un único posicionamiento.
- Evite el uso de esquemas de ajuste manual.
- El dispositivo de sujeción debe estar diseñado para poder abrirse y su mecanismo de posicionamiento y sujeción no debe interferir con el movimiento de la herramienta durante el procesamiento CNC (para evitar colisiones). En estos casos, la fijación se puede lograr mediante un tornillo de banco o agregando una placa base y extrayendo tornillos.
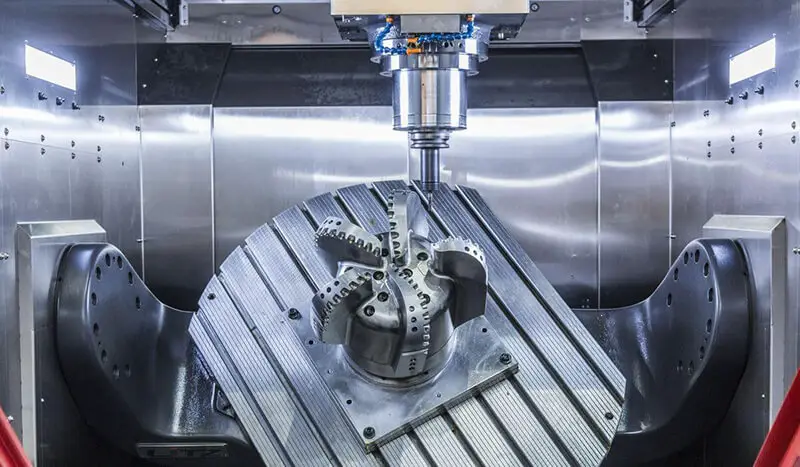
4. ¿Cómo determinar la razonabilidad del punto de ajuste de la herramienta? ¿Cuál es la relación entre el sistema de coordenadas de la pieza y el sistema de coordenadas de programación?
El punto de ajuste de la herramienta se puede establecer en la pieza mecanizada, pero es importante tener en cuenta que el punto de ajuste de la herramienta debe ser una posición de referencia o el producto final. En algunos casos, después del primer proceso de mecanizado, el punto de ajuste de la herramienta puede dañarse, dificultando la localización del punto de ajuste de la herramienta en procesos posteriores.
Para evitar esto, se debe tener cuidado de definir una posición relativa de configuración de herramienta en el primer proceso que tenga una relación consistente con un punto de referencia de referencia. De esta manera, se puede identificar el punto de ajuste original de la herramienta en función de la relación relativa entre ellos.
Esta posición relativa de ajuste de la herramienta generalmente se ubica en el banco o dispositivo de la máquina herramienta, y la selección debe tener en cuenta los siguientes principios:
- Fácil alineación
- Programación conveniente
- Error de configuración mínima de herramienta
- Facilita la inspección durante el mecanizado y permite una fácil comprobación.
El punto de partida del sistema de coordenadas de la pieza lo establece el operador. Una vez que la pieza de trabajo esté sujeta firmemente, ajustar la herramienta fijará su posición. Define la distancia entre la pieza de trabajo y el punto cero de la máquina herramienta.
Una vez establecido el sistema de coordenadas de la pieza, normalmente permanece sin cambios. Para garantizar un mecanizado preciso, es importante que el sistema de coordenadas de la pieza de trabajo y el sistema de coordenadas de programación estén sincronizados, lo que significa que sean coherentes entre sí durante el proceso de mecanizado.
5 . ¿Cómo seleccionar la ruta de corte?
La trayectoria de la herramienta se refiere a la trayectoria y dirección del movimiento de la herramienta en relación con la pieza de trabajo durante el mecanizado NC. La selección de la ruta de corte es crucial ya que afecta la precisión y la calidad de la superficie de las piezas mecanizadas.
Se tienen en cuenta los siguientes factores al determinar la ruta de corte:
- Cumplir con los requisitos de precisión de mecanizado de piezas.
- Facilitando el cálculo numérico y reduciendo el esfuerzo de programación.
- Encuentre la ruta de procesamiento NC más corta y reduzca el tiempo de inactividad de la herramienta para mejorar la eficiencia del procesamiento NC.
- Minimizando el número de segmentos.
- Asegúrese de la rugosidad superficial requerida del contorno de la pieza de trabajo después del mecanizado NC y asegúrese de que el contorno final se procese continuamente con la última herramienta.
- Considere cuidadosamente el camino hacia adelante y hacia atrás (entrada y salida) de la herramienta para minimizar las marcas de cuchillo causadas por cambios repentinos en la fuerza de corte y para evitar rayar la pieza de trabajo al cortar verticalmente en la superficie del contorno.
6 . ¿Cómo monitorear y ajustar durante el mecanizado CNC?
Una vez que la pieza esté correctamente alineada y el programa esté completamente depurado, se puede pasar a la etapa de mecanizado automático.
Durante este paso, el operador debe monitorear de cerca el proceso de corte para garantizar que la calidad de la pieza no se vea comprometida y evitar accidentes que puedan ocurrir como resultado de cortes anormales.
A la hora de realizar el seguimiento del proceso de corte se deben tener en cuenta los siguientes aspectos:
(1) Durante la fase de mecanizado en desbaste, el objetivo del seguimiento del proceso de mecanizado es principalmente la eliminación rápida del exceso de material de la superficie de la pieza de trabajo.
En la operación de máquina herramienta, el proceso de corte se lleva a cabo automáticamente de acuerdo con la ruta de corte predeterminada y los parámetros de corte establecidos por el operador.
El operador debe monitorear de cerca los cambios en la carga de corte durante todo el proceso verificando la tabla de carga de corte. En función de la fuerza de rodadura de la herramienta, los parámetros de corte deben ajustarse para maximizar la eficiencia de la máquina herramienta.
(2) Monitorear el sonido de corte durante el proceso de corte.
Durante el proceso de corte automático, cuando comienza el proceso de corte, el sonido de la herramienta cortando la pieza de trabajo es generalmente estable, continuo y ligero.
En esta etapa, el movimiento de la máquina herramienta es estable. Sin embargo, a medida que avanza el proceso de corte, problemas como puntos duros en la pieza de trabajo, desgaste de la herramienta o sujeción inadecuada de la herramienta pueden hacer que el proceso de corte sea inestable.
Los indicadores de inestabilidad incluyen cambios en el sonido de corte, colisión entre herramienta y pieza de trabajo y vibración de la máquina herramienta. En estos casos, se deben ajustar inmediatamente los parámetros y condiciones de corte.
Si el ajuste no produce el resultado deseado, se deberá detener la máquina herramienta para inspeccionar el estado de las herramientas y piezas.
(3) Monitoreo del proceso de acabado para garantizar el tamaño del mecanizado de piezas y la calidad de la superficie.
Durante el proceso de acabado, la velocidad de corte es alta y el avance es grande. Se debe prestar atención al impacto de la acumulación de viruta en la superficie mecanizada.
Para las cavidades que se están mecanizando, es importante tener cuidado con el corte excesivo y el desgaste de la herramienta en las esquinas.
Para resolver estos problemas, se pueden seguir los siguientes pasos:
- Asegúrese de que la superficie de mecanizado esté siempre fría ajustando la posición del rociador del fluido de corte.
- Mantenga la calidad de la superficie mecanizada ajustando los parámetros de corte para evitar cambios en la calidad.
Si estos ajustes no son efectivos, puede ser necesario detener la máquina y evaluar la razonabilidad del programa original.
Es importante prestar atención a la posición de la herramienta al pausar la inspección o detener la máquina. Si la herramienta de corte se detiene en medio del proceso de corte, la parada repentina del husillo puede provocar marcas de herramienta en la superficie de la pieza de trabajo.
En general, se recomienda apagar la máquina cuando la herramienta ya no esté en estado de corte.
(4) Monitoreo de herramientas: la calidad de la herramienta afecta la calidad del mecanizado de la pieza de trabajo.
La calidad de la herramienta juega un papel importante en la determinación de la calidad del mecanizado de la pieza.
Durante el proceso de mecanizado y corte automático, el desgaste normal y cualquier daño anormal de la herramienta se puede detectar mediante monitoreo de sonido, control del tiempo de corte, inspecciones durante el proceso de corte y análisis de la superficie de la pieza.
Para garantizar que la calidad del mecanizado cumpla con los estándares requeridos, las herramientas de corte deben manejarse de manera oportuna para evitar cualquier problema de calidad del procesamiento causado por un manejo inadecuado de la herramienta.
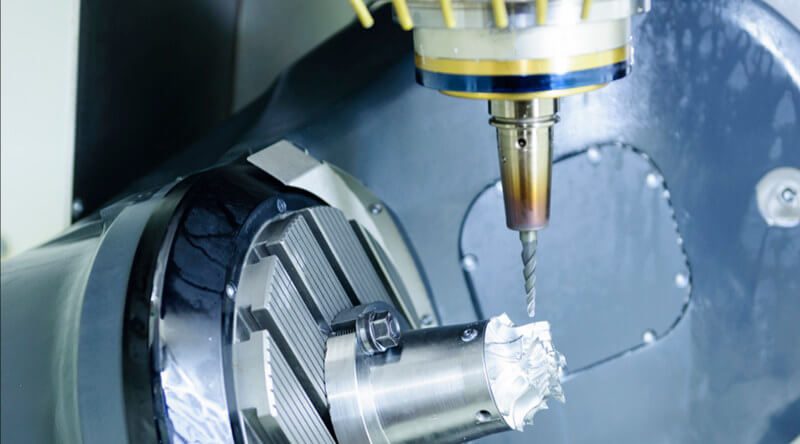
7 . ¿Cómo seleccionar razonablemente las herramientas de mecanizado? ¿Cuántos factores hay en los parámetros de corte? ¿Cuántos tipos de herramientas de corte existen? ¿Cómo determinar la velocidad de la herramienta, la velocidad de corte y el ancho de corte?
(1) Para fresado plano, se recomienda utilizar una fresa de extremo o una fresa de extremo de carburo sin rectificar. En el fresado general, es mejor utilizar el segundo avance de herramienta siempre que sea posible. Para el primer avance de herramienta, se recomienda utilizar una fresa para desbaste y avance continuo a lo largo de la superficie de la pieza. El ancho de avance recomendado de cada herramienta debe estar entre el 60% y el 75% del diámetro de la herramienta.
(2) Las fresas de extremo y las fresas de extremo con insertos de carburo se utilizan principalmente para procesar protuberancias, ranuras y superficies de boca de caja.
(3) Los cortadores de bolas y los cortadores redondos (también conocidos como cortadores de punta redonda) se usan comúnmente para procesar superficies curvas y contornos de ángulos variables. Las fresas de bolas se utilizan principalmente para semiacabado y acabado, mientras que las fresas circulares de carburo se utilizan principalmente para desbaste.
8 . ¿Cuál es la función de la hoja de cálculo del programa de procesamiento? ¿Qué se debe incluir en la hoja de procedimiento de tramitación?
(1) La lista de programas de mecanizado es un componente esencial del diseño del proceso de mecanizado NC. Sirve como un procedimiento que debe ser seguido y ejecutado por el operador. La lista de programas de mecanizado proporciona una descripción detallada del programa de mecanizado y se utiliza para aclarar el contenido del programa, el método de sujeción y posicionamiento y las herramientas seleccionadas para cada programa de mecanizado, entre otras cosas.
(2) El archivo del programa de mecanizado debe incluir la siguiente información: nombre del archivo de dibujo y programación, nombre de la pieza, croquis del método de sujeción, nombre del programa, herramientas utilizadas en cada programa, valor máximo de profundidad de corte, el naturaleza del mecanizado (como desbaste o acabado) y el tiempo teórico de mecanizado.
9 . ¿Qué preparativos se deben hacer antes de programar?
Antes de programar, es importante considerar lo siguiente después de determinar la tecnología de procesamiento:
- Método de fijación de la pieza;
- El tamaño del embrión en blanco: esto determinará el rango de procesamiento o si se requiere fijación múltiple;
- El material de la pieza – para seleccionar la herramienta adecuada para el mecanizado;
- Herramientas disponibles en stock – para evitar modificaciones en el programa debido a la falta de disponibilidad de una herramienta durante el mecanizado. Si se necesita una herramienta específica, se debe preparar con antelación.
10 . ¿Cuáles son los principios para definir la altura de seguridad en la programación?
El principio de ajuste de la altura de seguridad es garantizar que sea generalmente más alta que la superficie más alta de la pieza de trabajo o establecer el punto cero de programación en la superficie más alta. Esto ayuda a minimizar el riesgo de colisión de herramientas.