As peças forjadas do tipo I são peças comuns na indústria de perfuração de petróleo, incluindo dispositivos de cabeça de poço, árvores de petróleo, equipamentos de estrangulamento e pressão, e há uma alta demanda no mercado por elas.
O formato deste tipo de forjamento possui as seguintes características: as duas extremidades do flange e do cilindro intermediário são coaxiais, e há uma diferença de diâmetro entre o flange e o cilindro de conexão intermediário.
Status e análise do processo de forjamento
O atual processo de produção comumente usado para peças forjadas em forma de I envolve duas etapas:
(1) O processo de produção começa forjando diretamente grandes peças forjadas cilíndricas com base nas dimensões aproximadas do diâmetro do flange do produto. Essas grandes peças forjadas cilíndricas são então processadas por meio de usinagem.
(2) Além do processo acima, um processo simbólico de tração e alongamento é usado para formar a pequena parte cilíndrica central.
No entanto, ambos os processos apresentam as seguintes deficiências:
- Baixo aproveitamento de matéria-prima, que em casos extremos pode ser inferior a 50%. Para os produtos estudados neste artigo, a taxa de utilização de matéria-prima utilizando o processo de forjamento livre direto foi de apenas 74%, no máximo.
- Grandes quantidades de peças de reposição para processamento e altos custos de processamento, resultando em altos custos de produção e fraca rentabilidade do produto.
- Longo ciclo de produção e baixo índice de satisfação do cliente.
Neste artigo, nosso foco está no tipo de forjamento. Nosso objetivo é romper as limitações do processo produtivo tradicional e evitar os problemas mencionados acima, a fim de reduzir os custos de produção, adaptar-se aos ritmos do mercado e aumentar a competitividade do mercado.
Nós nos concentramos principalmente na forma de tais peças forjadas, começando pelo projeto da matriz dividida e usando o processo de forjamento da matriz do pneu para produção para alcançar a precisão dimensional das peças forjadas.
Fluxo de processo de peças forjadas em forma de I
Como essas peças forjadas são produzidas principalmente em lotes pequenos e médios, elas são fabricadas usando o processo de forjamento sob matriz.
Devido aos investimentos excessivos em vestuário de trabalho e aos elevados custos de produção, melhorar a competitividade do mercado tornou-se um desafio. Portanto, uma análise abrangente está sendo considerada. A pesquisa sobre o processo de produção de matrizes de divisão pode oferecer benefícios duplos, como precisão em produtos forjados e a produção de vários pequenos lotes de forjamento de matrizes de pneus.
O diagrama de fluxo do processo específico é ilustrado na Figura 1.
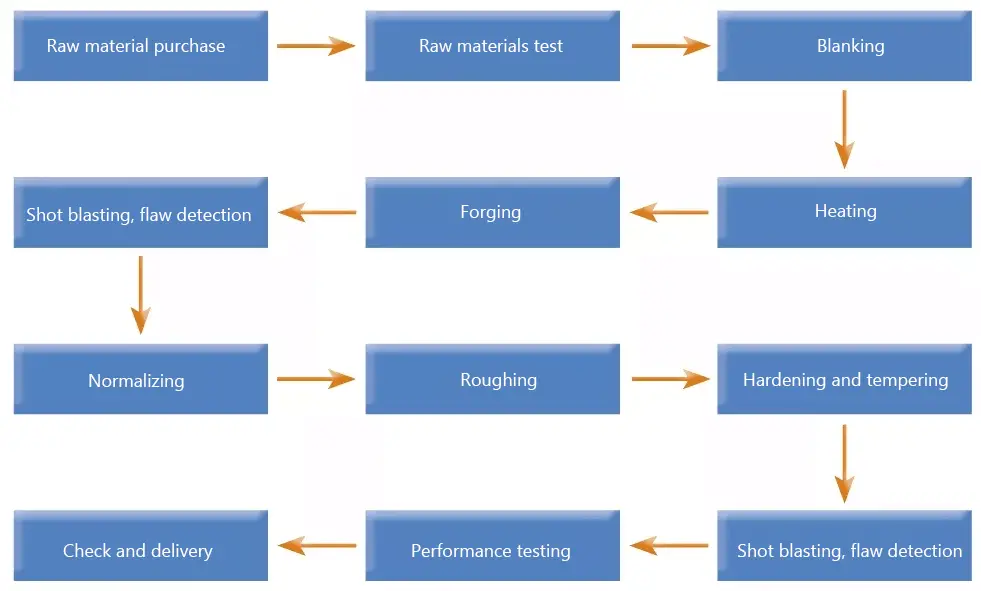
Figura 1: Diagrama de fluxo do processo
Projeto de forjamento
As peças em forma de I recém-desenvolvidas pesam 101,96 kg em massa e 154 kg em peças forjadas. O cálculo do processo de forjamento indica um fator de complexidade S de 0,53.
Como o processo de forjamento livre já pertence à complexa classe de peças forjadas, o projeto da matriz dividida exige padrões mais elevados.
Usando o diagrama de peças fornecido pelo usuário, as peças forjadas são criadas com base no novo plano de processo. Este plano aproxima o processo de forjamento do equilíbrio, resultando em alta precisão dimensional. A Figura 2 exibe os diagramas da peça e do forjamento.
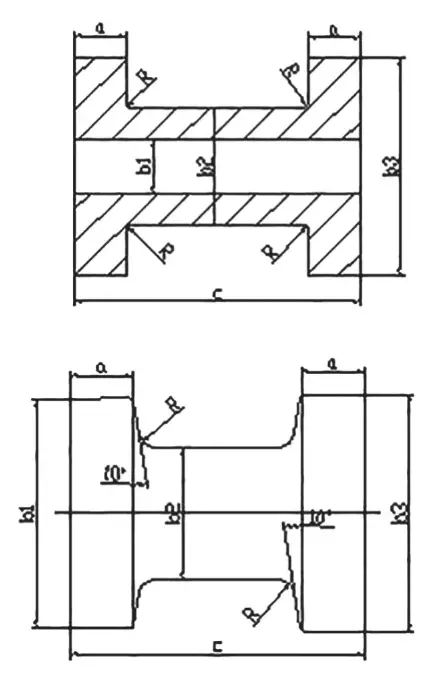
Figura 2 Diagrama de peças e forjados
Desenvolvimento de processo de forjamento
O plano de produção para o processo de forjamento é o seguinte: primeiro, o tarugo é trefilado e, em seguida, o flange é formado recortando uma extremidade da matriz do pneu, seguido pela formação do outro flange usando a combinação da inserção de partição e do tubo externo morrer.
Este processo de forjamento garante que o primeiro processo de recalque sirva como o processo de moldagem do segundo processo de recalque, permitindo assim o controle sobre as excentricidades dos forjados e a precisão dimensional das peças brutas.
Após cálculos cuidadosos, foi determinado que a qualidade das peças forjadas e a qualidade da matriz de corte combinadas pesam mais de 600 kg. Portanto, para garantir resultados ideais durante o processo de forjamento da matriz de corte final, um martelo de forjamento livre de 3t deve ser usado como equipamento de forjamento.
Projeto de molde
Base de projeto do molde do pneu, inserto dividido e molde da luva
Base do projeto do molde do pneu: diagrama de forjamento a frio → peças forjadas a quente → molde do pneu. As dimensões dos forjados a quente são calculadas conforme fórmula (1).

Na fórmula, Lt representa o tamanho do forjamento na temperatura final de forjamento (mm); L denota o tamanho da peça forjada a frio (mm); α representa o coeficiente de expansão da linha de material (1/C); t representa a temperatura final de forjamento (°C).
Para materiais de forjamento na indústria petrolífera, principalmente AISI4130 e 410SS, a temperatura inicial de forjamento é geralmente 1150°C, e a temperatura final de forjamento é igual ou superior a 860°C. Como este processo de forjamento é relativamente longo e a temperatura final de forjamento é baixa, a taxa de contração a frio é adequadamente reduzida para 1,2% – 1,4%.
O desenho da subembalagem é baseado no processo de desenho do molde do pneu, com ênfase na montagem do molde da manga durante o processo de desenho. Esta abordagem ajuda a evitar situações em que a montagem seja impossível ou difícil.
Projeto de molde de pneu e molde dividido
Com base no processo de produção de forjamento estabelecido, o molde do pneu (conforme mostrado na Figura 3), as inserções divididas (conforme mostrado na Figura 4) e o molde da luva (conforme mostrado na Figura 5) foram projetados incorporando os elementos do projeto do molde do pneu. .
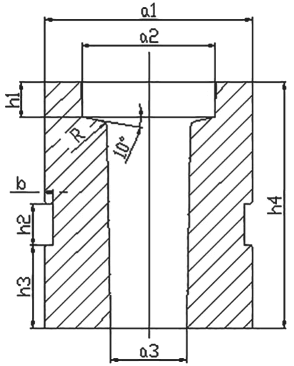
Figura 3 molde de pneu
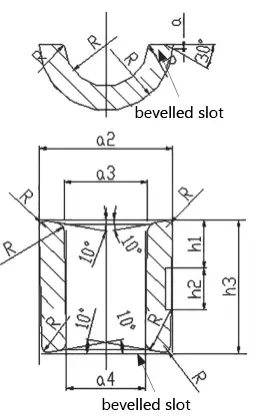
Figura 4 inserção dividida
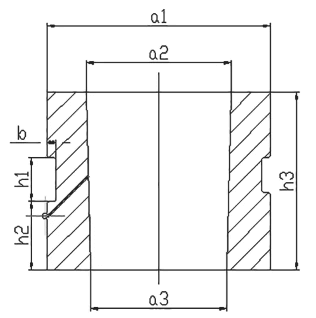
Figura 5 molde de mangas
A Figura 3 mostra a primeira matriz de recalque, que exigiu um cálculo preciso do peso da peça forjada durante a fase inicial do projeto. Não fazer isso pode resultar no preenchimento da parte posterior durante o forjamento livre após o recalque.
As pastilhas divididas estão ilustradas na Figura 4. O projeto deve levar em consideração que a pastilha dividida está localizada no cilindro intermediário da peça forjada após a conformação do forjamento. Para facilitar a remoção, é feita uma ranhura chanfrada na interface da matriz dividida. Esta ranhura permite a fácil remoção da pastilha dividida após o forjamento.
Ao mesmo tempo, foi realizado um projeto de otimização local. O desenho da face final em contato com o interior do flange foi inclinado em 10°. O chanfro interno foi de R20mm, e o chanfro de contato entre a parte externa e a segunda matriz da luva virada foi de R15mm.
A inclinação geral da parte externa do molde é a mesma que a inclinação da cavidade interna do molde de recalque mostrado na Figura 3. O diâmetro é reduzido em 1 mm em um lado para facilitar a colocação na cavidade do modelo de luva mostrado em Figura 5.
A matriz da luva, mostrada na Figura 5, é projetada para garantir o tamanho do flange após o recalque. Os tamanhos a2 e a3 são projetados para o tamanho da peça forjada a quente, com uma transição livre de inclinação da cavidade. A Figura 6 mostra uma matriz dividida composta com inserções divididas e módulo de luva.
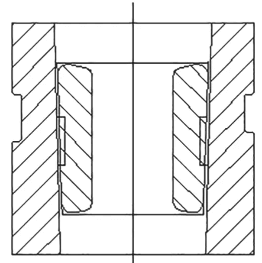
Figura 6 matriz dividida
O molde do pneu é combinado e forjado usando 3TZ, o que resulta em uma força de rolamento significativa durante o processo de forjamento. Consequentemente, na fase de projeto, a espessura do molde da luva é aumentada globalmente para compensar isso.
Conclusão
Depois de verificar a produção real de pequenos lotes, o plano do processo de forjamento em matriz dividida prova ser bem-sucedido e viável. Também tem a capacidade de garantir o processo de produção em massa.
Este artigo apresenta um novo método de processo para a produção de peças forjadas em forma de I, que economiza 23% de matéria-prima em comparação com o forjamento livre direto. O novo esquema produz efetivamente peças forjadas em forma de I que atendem ao valor alvo do processo desejado.
Os forjados feitos através deste método exibem o mesmo nível de tecnologia do forjamento em matriz. Comparado ao forjamento sob matriz ou ao forjamento livre direto, esse processo economiza de 20% a 40% de matéria-prima, reduz os custos de produção e aumenta a flexibilidade do processo.