O eixo de saída da caixa de câmbio auxiliar é um componente crucial que suporta um torque significativo durante a operação do veículo. Portanto, requer alta resistência.
Os requisitos técnicos do desenho incluem o uso de material 40Cr e endurecimento por indução de média frequência em ângulo R e estriado. A profundidade da camada de endurecimento no ângulo R deve ser ≥ 5 mm, e a camada de endurecimento na ranhura deve estar a 5-8 mm da parte inferior do dente. Além disso, a dureza superficial deve ser ≥ 55HRC. A matriz deve ser temperada e revenida, e a dureza deve ser 235-265HBW.
No início de 2019, o mercado informou que o eixo de saída da caixa auxiliar quebrava com frequência quando os clientes dirigiam entre 30.000-100.000 km. Através da análise das peças quebradas, foram identificados os seguintes motivos das fraturas:
- A estrutura do ângulo R do eixo de saída é côncava, dificultando o endurecimento por indução. Isto resulta em uma camada de têmpera rasa e maior sensibilidade à têmpera de trincas. Rachaduras de endurecimento por indução foram encontradas no ângulo R durante a detecção real.
- O chanfro do furo de óleo do eixo de saída da caixa auxiliar é de 0,5 mm × 45°. Devido ao efeito de ângulo agudo, as fissuras de têmpera tendem a ser grandes e as fissuras de têmpera estão presentes.
Leitura relacionada: Têmpera de rachadura vs. Forjamento de rachaduras vs. Retificação de rachaduras
Este artigo fornece uma análise das causas das fraturas do eixo de saída na caixa auxiliar e propõe uma série de medidas de melhoria para resolver o problema. A análise é baseada em princípios e as medidas são projetadas para resolver efetivamente o problema de fraturas do eixo de saída na caixa auxiliar.
1. Análise de falhas
1.1 Análise de detecção de falhas
A Figura 1 ilustra os componentes defeituosos do eixo de saída na caixa auxiliar.
Especificamente, a Fig. 1a mostra a aparência e a localização da fratura das peças defeituosas, com o círculo vermelho indicando a localização da fratura.
A fratura do eixo de saída da caixa auxiliar ocorreu na posição do ângulo R da ranhura de retirada da ferramenta, conforme evidenciado na figura.
Além disso, a Figura 1b mostra a morfologia da fratura, que é caracterizada por uma fratura reta induzida pela rotação circunferencial da haste.
Após a fratura, existem marcas de desgaste mútuo em ambas as extremidades, o que é consistente com as características da fratura por torção.
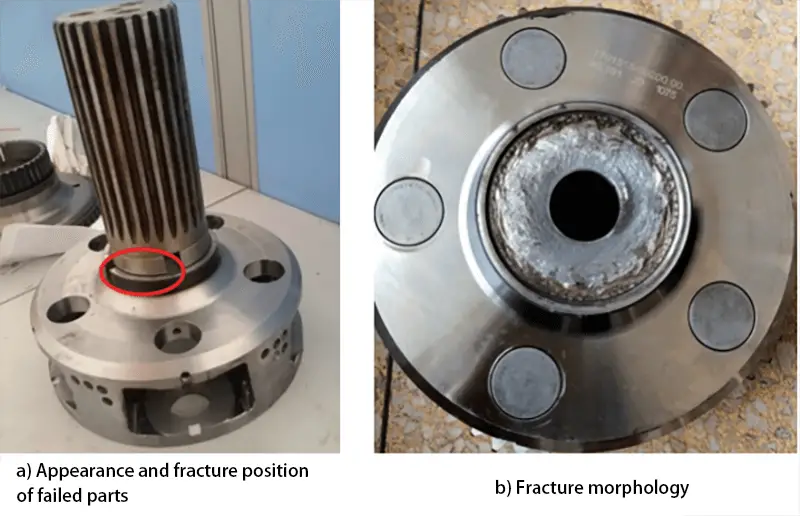
Fig. 1 Peças de falha do eixo de saída da caixa auxiliar
Ensaios não destrutivos e análises metalográficas foram realizados tanto nos produtos acabados quanto nas peças defeituosas que foram devolvidas do mercado, e os resultados dos testes são apresentados na Tabela 1.
Como pode ser visto na tabela, os resultados de têmpera por indução das peças estriadas tanto nos produtos acabados quanto nas peças com falha de mercado atendem aos requisitos técnicos. A profundidade efetiva de endurecimento das peças estriadas é ≥ 5 mm, e a estrutura metalográfica da camada endurecida é de martensita acicular de grau 4-5.
No entanto, os resultados de têmpera por indução no furo de óleo estriado e no canto R não atendem aos requisitos técnicos pelos seguintes motivos:
- O produto acabado apresenta trincas de endurecimento por indução na posição do ângulo R e furo de óleo estriado.
- A profundidade da camada de endurecimento por indução no canto R é rasa, ou mesmo inexistente, e não ultrapassa 5 mm conforme especificado nos requisitos técnicos.
Tabela 1 Resultados de testes de partículas magnéticas e análises metalográficas de peças acabadas e peças com falha
Amostras | Local de detecção: | Exame metalográfico | Teste não destrutivo |
Produtos acabados em produção | ranhura | Ds:6~8mm,4~5 grausM | Rachadura no orifício de óleo estriado (ver Fig. 2a) |
Ângulo R | Ds: 3,2 mm, 5 grau M (ver Fig. 2b) | Rachadura em ângulo R (ver Figura 2c) | |
Peças de falha de mercado | ranhura | Ds:7~9mm,4~5 grau M | Rachadura no buraco de óleo estriado |
Ângulo R | Nenhuma camada endurecida (veja 2d para a figura) |
Os resultados da inspeção acima estão alinhados com as características de fissuração da peça com falha. Isto se deve ao fato da camada de endurecimento por indução no canto R do eixo de saída da caixa auxiliar ser insuficientemente profunda, não atendendo aos requisitos técnicos necessários. Além disso, uma trinca de endurecimento por indução se desenvolveu no canto R, causando um baixo nível de resistência naquele local.
Durante a operação do veículo, o canto R é incapaz de suportar grandes tensões de torção e, por fim, fraturas. Além disso, rachaduras de endurecimento por indução estão presentes no orifício de óleo estriado, e várias peças defeituosas no mercado também tiveram eixos de saída quebrados da subcaixa neste local.
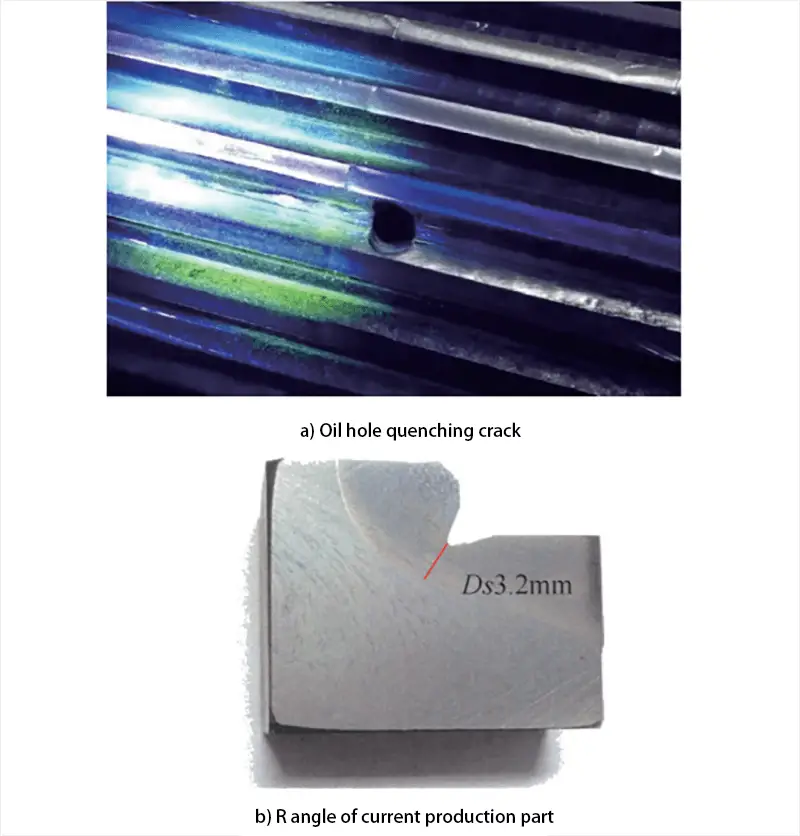
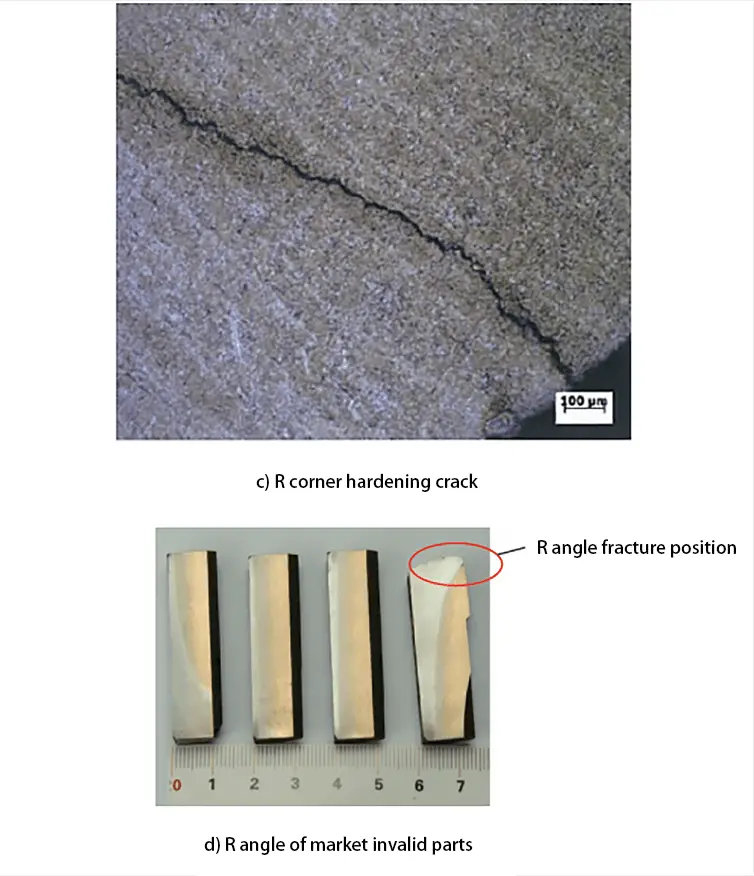
Fig. 2 Resultados de END e testes metalográficos
1.2 Análise da causa da falha
Os resultados da detecção de falha revelam dois pontos de risco de fratura do eixo de saída da caixa auxiliar: a posição do ângulo R e o orifício de óleo estriado.
A Fig. 3a ilustra a estrutura da posição do ângulo R do produto acabado durante a produção. Isso mostra que o ângulo R é uma estrutura interna de R0,5 mm, que pode ter dois efeitos no endurecimento por indução.
Em primeiro lugar, o filete de transição na parte inferior do canto R da estrutura interna do tipo R é muito pequeno, causando grande tensão de usinagem na parte inferior da depressão do canto R, o que aumenta a sensibilidade das trincas de endurecimento por indução.
Em segundo lugar, a distância entre a depressão do ângulo R da estrutura interna do tipo R e o indutor é relativamente grande.
A Figura 3b ilustra a distribuição da corrente induzida durante o aquecimento por indução no canto R.
Como resultado do efeito de proximidade do aquecimento por indução, a corrente induzida diminui à medida que a distância do sensor aumenta. Assim, a corrente induzida reduz gradativamente das áreas 1 a 4, sendo a menor corrente induzida encontrada na área 4, localizada na parte inferior do ângulo R, que é a mais distante do indutor.
No mesmo tempo de aquecimento, enquanto as áreas 1 a 3 atingem a temperatura de aquecimento de têmpera necessária como um todo, a área 4 pode não atingir a temperatura de têmpera completa. Consequentemente, ocorre o resfriamento por spray de água, causando transformação de martensita nas áreas 1 a 3, mas apenas transformação parcial de martensita ou nenhuma transformação na área 4.
Esta inconsistência na profundidade da camada endurecida das regiões 1 a 3 e região 4 leva à deformação irregular devido à transformação estrutural dentro e fora do ângulo R. Além disso, a região 4 sofre tensões de tração devido à transformação estrutural, tornando-a suscetível à concentração de tensões de usinagem, resultando em última análise na têmpera de trincas durante a têmpera.
Além disso, como a área 4 é a mais distante do indutor, é a parte mais desafiadora para o endurecimento por indução, e a profundidade da camada de endurecimento nesta área é insuficiente.
A Figura 3c ilustra a estrutura chanfrada do furo de óleo no eixo de saída do tanque auxiliar produzido atualmente. O tamanho do projeto do furo de óleo é 0,5 mm × 45°, o que não atende aos requisitos de endurecimento por indução de chanfros de furo.
Para garantir a qualidade do endurecimento por indução, é necessário um chanfro ligeiramente maior, de mais de 1 mm × 45°. Isso ocorre porque um pequeno chanfro resulta em altas temperaturas ao redor do furo de óleo devido ao efeito de ângulo agudo do aquecimento por indução, levando à formação de trincas de têmpera.
Além disso, a presença do furo de óleo força a corrente induzida a desviar em ambos os lados do furo, resultando em densidade desigual de correntes parasitas ao redor do furo. A densidade de correntes parasitas em ambos os lados do furo ao longo da direção da corrente é alta, enquanto a densidade em ambos os lados perpendiculares à direção da corrente é baixa. Isto cria uma área de alta temperatura de um lado e uma área de baixa temperatura do outro, conforme mostrado na Figura 3d.
Devido a este aquecimento desigual, a profundidade de penetração da corrente e a espessura da camada endurecida após a têmpera são diferentes. A geração de estresse organizacional e térmico durante a têmpera por indução é a causa fundamental da têmpera de trincas na borda do furo de óleo. Além disso, o resfriamento da borda do furo de óleo é mais intenso que o de outras áreas durante o resfriamento, tornando-o mais suscetível à formação de trincas de têmpera.
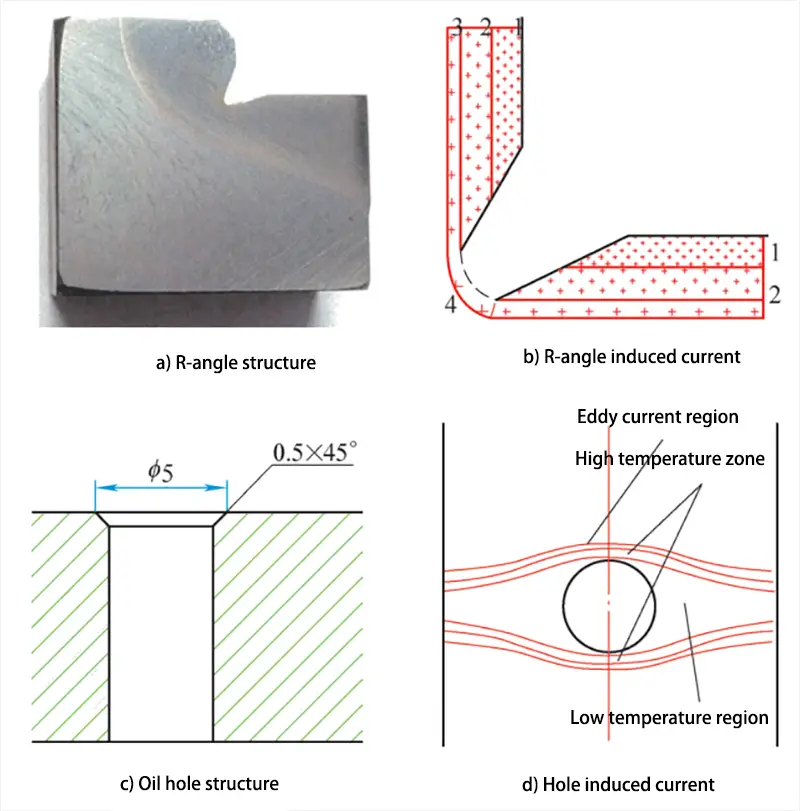
Fig. 3 Ângulo R e furo de óleo
2. Medidas de melhoria
2.1 Otimização estrutural do ângulo R e chanfro do furo de óleo
Com base na análise acima, fica evidente que a fratura do eixo de saída da caixa auxiliar se deve ao projeto defeituoso da estrutura do ângulo R e do chanfro do orifício de óleo.
Consequentemente, foram desenvolvidas as seguintes medidas corretivas:
- A estrutura do filete de transição foi modificada para R1,5mm, e a profundidade da camada de endurecimento por indução no filete otimizado deve ser ≥ 3mm.
- A estrutura do chanfro do furo de óleo foi melhorada para (1~1,5) mm × 45°.
A Figura 4a mostra a estrutura otimizada para o ângulo R.
Durante o processo de tratamento térmico por indução, se a raiz escalonada da peça necessitar de endurecimento por indução, um filete de transição deve ser incorporado. Quanto maior o filé, melhor será o resultado.
Este design oferece boa processabilidade:
① Reduz a concentração de tensões na raiz do degrau e minimiza a tendência a trincas durante o uso.
② Reduz a dificuldade de têmpera por indução, garante aquecimento uniforme da raiz do degrau, permite uma camada de endurecimento uniforme e contínua no degrau e aumenta significativamente a resistência.
A Figura 4b ilustra o projeto otimizado para o chanfro do furo de óleo, com um tamanho de chanfro aumentado de (1~1,5) mm × 45°. Sob as mesmas condições de aquecimento, quanto maior o chanfro do furo de óleo, maior será a densidade de corrente na borda do furo de óleo e menor será a probabilidade de a borda do furo de óleo rachar devido ao superaquecimento.
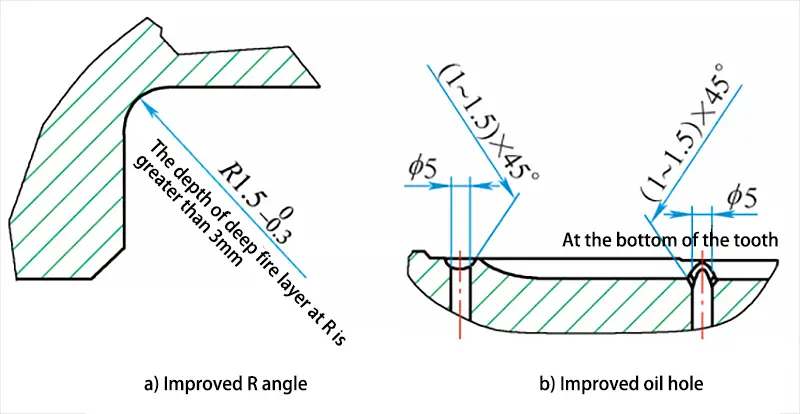
Figura 4 otimização estrutural
2.2 Otimização do processo de endurecimento por indução
O método de têmpera por varredura é usado para completar a têmpera do eixo de saída da caixa auxiliar devido à grande área de têmpera e à pequena fonte de alimentação. A vantagem significativa da têmpera por varredura é que ela pode usar equipamentos com menor capacidade para lidar com peças grandes.
Para realizar a têmpera por varredura, a peça de trabalho é colocada dentro ou perto do indutor, permitindo que o indutor e a peça de trabalho se movam um em relação ao outro. O indutor conecta corrente de alta ou média frequência para aquecer indutivamente a peça de trabalho até a temperatura de têmpera. Simultaneamente, o indutor ou jato de água pulveriza o meio de resfriamento de têmpera na peça da peça que atingiu a temperatura de têmpera.
O processo de têmpera continua até que toda a área de têmpera da peça seja tratada. Para interromper o processo, a corrente do indutor é cortada primeiro, seguida pela injeção do meio de resfriamento de têmpera.
A Figura 5 ilustra o projeto otimizado do círculo efetivo do indutor. Esta estrutura consiste em um círculo inteiro que gira em um ângulo específico (geralmente 45°) para garantir o aquecimento adequado do plano e o ângulo R na seção variável. O anel efetivo é equipado com um “Π” e a ranhura do condutor magnético é inclinada em direção à área do ângulo R.
Ao aproveitar o efeito de fenda do condutor magnético, a corrente de média frequência da bobina efetiva é expelida para a área do ângulo R, fortalecendo assim o aquecimento da região do ângulo R. Para garantir um aquecimento rápido do ângulo R, existe um espaço de 3-5 mm entre a extremidade frontal da bobina efetiva e o ângulo R. Este arranjo permite que a temperatura de têmpera seja atingida em 10 segundos, levando a uma distribuição ideal da camada de endurecimento.
Porém, ao aquecer o ângulo R, o indutor deve permanecer nesta área por um período específico para obter profundidade suficiente da camada de endurecimento no ângulo R. Durante esse tempo, as splines adjacentes acima do ângulo R também serão aquecidas. Para evitar que a profundidade da camada de endurecimento dessas estrias seja muito profunda, o que poderia resultar em “abaulamento” da camada de endurecimento na transição entre o ângulo R e a estria axial, é utilizado o efeito de proximidade do aquecimento por indução.
Especificamente, ao projetar o indutor, a superfície da estria de aquecimento e o eixo da estria formam um ângulo incluído de 7,5° para minimizar o efeito de proximidade. À medida que nos aproximamos da região do ângulo R, o espaçamento diminui, levando a uma sombra preta na Figura 5, que indica a distribuição da corrente induzida na área do ângulo R e suas regiões adjacentes.
Finalmente, ao aquecer a área do canto R, o indutor se move para cima para aquecer e extinguir a área estriada, resultando em uma camada de endurecimento uniforme e contínua que melhora a resistência geral do eixo de saída.
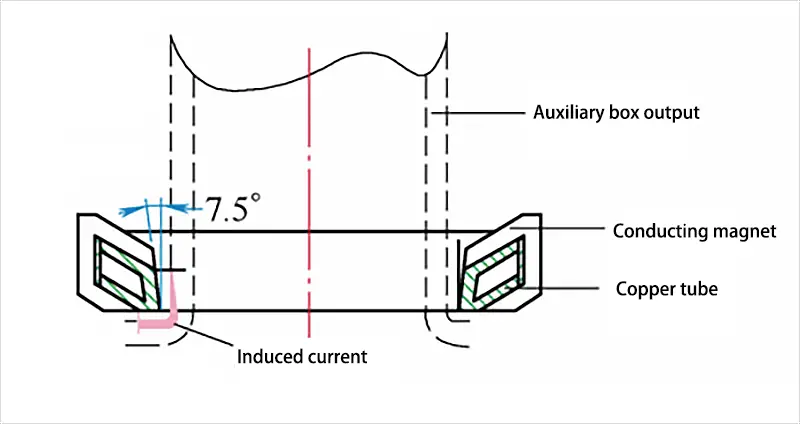
Fig. 5 Projeto do círculo efetivo
3. Conclusão
Após análise das causas da fratura do eixo de saída na caixa auxiliar, foram identificadas três medidas de melhoria:
- Otimização da estrutura do filete de transição: A estrutura do filete de transição será melhorada para r1,5mm para o filete externo, e o requisito técnico da profundidade da camada de endurecimento por indução no filete será definido para ≥ 3mm.
- Otimização do tamanho do chanfro do furo de óleo: A estrutura do chanfro do furo de óleo será melhorada para (1 ~ 1,5) mm × 45°.
- Otimização da estrutura efetiva do anel do indutor: O método de endurecimento por indução de varredura será adotado para tornar a camada de endurecimento do filete e da estria contínua e uniforme.
Após a implementação destas medidas, o eixo de saída da caixa auxiliar foi inspecionado e monitorado, sendo observadas melhorias significativas:
- A resistência do ângulo R do eixo de saída do subtanque foi significativamente melhorada e não há mais rachaduras de endurecimento por indução no chanfro do orifício de óleo e na área do ângulo R.
- O filete e a camada de endurecimento do eixo de saída agora são contínuos e uniformes. A camada de endurecimento no ângulo R tem 4 ~ 6 mm de profundidade, enquanto a camada de endurecimento na parte estriada tem 5 ~ 8 mm de profundidade. A estrutura metalográfica da camada de endurecimento é de martensita acicular de grau 4 ~ 6, e a dureza superficial é de 56 ~ 59HRC, atendendo aos requisitos técnicos.
- O eixo de saída da subcaixa não quebrou após a entrega e o carregamento, reduzindo significativamente o risco de reclamações do mercado e melhorando a qualidade do produto e a satisfação do cliente.