Visão geral
Em fevereiro de 2011, a professora Skylar Tibbits, diretora do Laboratório de Automontagem do Instituto de Tecnologia de Massachusetts (MIT), nos Estados Unidos, apresentou o conceito de modelagem por meio da automontagem de materiais durante uma palestra TED (Tecnologia, Entretenimento, Design). —uma organização sem fins lucrativos com sede nos EUA.
Em 2013, o professor Tibbits voltou ao palco do TED, apresentando pela primeira vez ao mundo o conceito de impressão 4D. Sua palestra atraiu ampla atenção em vários setores, reconhecendo-o como o inventor da impressão 4D.
Desde então, a impressão 4D captou o interesse global, avançando rapidamente em tecnologia e expandindo-se para aplicações mais amplas. O Professor Tibbits e seu Laboratório de Automontagem, em colaboração com a Stratasys, continuaram a pesquisa e desenvolveram numerosos modelos físicos de impressão 4D, conforme mostrado nas Figuras 8-1 a 8-4.
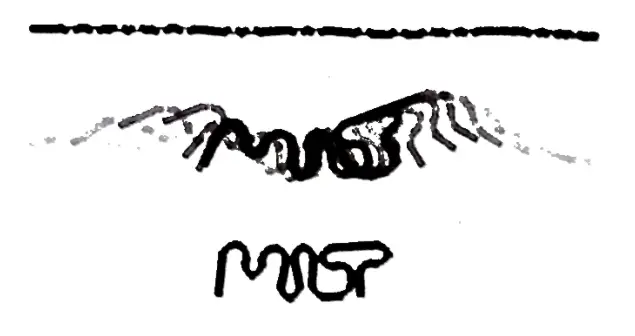
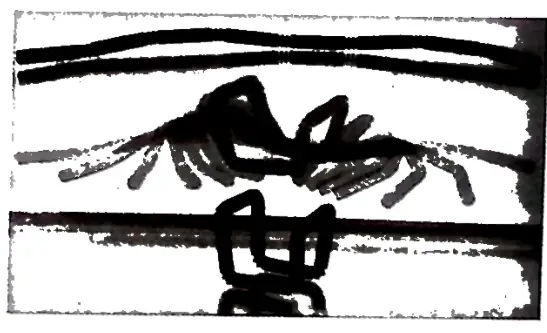

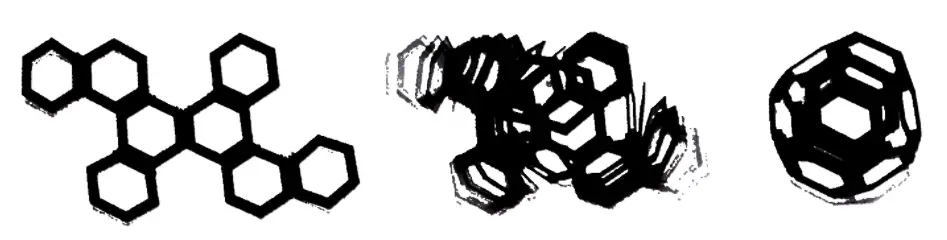
Atualmente, a tecnologia de impressão 4D ainda está em fase exploratória e ainda não alcançou aplicações de produção em larga escala.
No entanto, possui um enorme potencial para revolucionar a tecnologia de produção, atraindo a atenção de vários países ao redor do mundo, especialmente dos Estados Unidos e da China, com sucessivos resultados de investigação emergentes.
Em 2011, o MIT iniciou pesquisas em tecnologia de impressão 4D; em 2014, a empresa americana Nervous System lançou o primeiro vestido oco impresso em 4D; em 2017, a NASA usou a impressão 4D para criar tramas metálicas dobráveis, preparando-as para uso na fabricação de diversas espaçonaves; em 2016, uma equipe de especialistas do Hospital Xijing da Quarta Universidade Médica Militar da China, em conjunto com um laboratório nacional local, tornou-se a primeira a aplicar stents traqueais impressos em 4D no tratamento de bebês com doenças cardíacas congênitas complexas acompanhadas de graves bilaterais estenose traqueal.
Em resumo, a impressão 4D está preparada para mudar paradigmas, expandir o pensamento e inspirar antecipação e entusiasmo para o futuro.
O conceito e implicações da impressão 4D.
Desde que a professora Skylar Tibbits introduziu pela primeira vez o conceito de impressão 4D em 2013, a definição tem sido interpretada por um número crescente de estudiosos, levando a uma variedade de descrições e a algum debate, sem chegar a um consenso. Vale a pena notar que à medida que a tecnologia de impressão 4D continua a evoluir, o seu conteúdo conceptual também se torna mais enriquecido.
Em primeiro lugar, este livro fornece uma explicação abrangente da impressão 4D conforme descrita pelo Professor Skylar Tibbits, que é a seguinte: A impressão 4D é um novo processo que demonstra uma mudança radical na fabricação aditiva. Implica impressões multimateriais com capacidade de transformação ao longo do tempo, ou um sistema de materiais personalizado que pode mudar de um formato para outro, diretamente da mesa de impressão.
Esta técnica oferece um caminho simplificado da ideia à realidade com funcionalidade orientada para o desempenho incorporada diretamente nos materiais.
A quarta dimensão é descrita aqui como a transformação ao longo do tempo, enfatizando que as estruturas impressas não são mais simplesmente objetos estáticos e mortos; em vez disso, eles são programavelmente ativos e podem se transformar de forma independente. A impressão 4D é um primeiro vislumbre do mundo dos materiais evolutivos que podem responder às necessidades do usuário ou às mudanças ambientais.
No centro desta tecnologia estão três capacidades principais: a máquina, o material e o “programa” geométrico.
A professora Skylar Tibbits expõe a impressão 4D como um processo fundamentalmente distinto da impressão 3D (fabricação aditiva). A impressão 4D requer um sistema evolutivo de materiais múltiplos ou personalizados que, depois de ser produzido pela impressão 3D, pode continuar a evoluir ao longo do tempo ou transformar-se de uma forma para outra.
Ao incorporar recursos orientados ao desempenho diretamente no sistema de materiais, a impressão 4D oferece um atalho do conceito à realidade. A quarta dimensão da impressão 4D, que pode ser descrita como evolução ao longo do tempo, enfatiza que as estruturas criadas pela impressão 3D já não são estáticas, mas podem ser programadas para transformação autónoma.
Existem três tecnologias principais na impressão 4D: o hardware, os materiais e a “programação” geométrica.
Para compreender totalmente o conceito de impressão 4D explicado pela professora Skylar Tibbits, é necessário compreender as seguintes nuances:
A chamada quarta dimensão refere-se à evolução do sistema material evolutivo ao longo do tempo, o que, segundo o professor Tibbits, equivale à automontagem – o que significa que o sistema material pode mudar para a forma desejada dentro de um período de tempo definido com base em modelos definidos por software. .
A distinção fundamental da impressão 3D reside principalmente numa mudança transformadora na abordagem de produção. A impressão 3D requer um modelo tridimensional pré-projetado e, em seguida, usa materiais correspondentes para moldá-lo, enquanto a impressão 4D incorpora o design do modelo tridimensional diretamente no sistema de materiais, agilizando o processo do “design” ao “objeto físico”.
As três principais tecnologias referidas são as seguintes: Para o equipamento, normalmente podem ser utilizadas impressoras 3D convencionais diretamente ou com pequenas modificações; em relação aos materiais, geralmente são compósitos multifásicos ou materiais evolutivos, também conhecidos como materiais inteligentes ou materiais responsivos a estímulos.
Referem-se a materiais que podem alterar autonomamente suas propriedades físicas ou químicas (incluindo forma, densidade, cor, elasticidade, condutividade, características ópticas, propriedades eletromagnéticas, etc.) sob estímulos predeterminados (como imersão em água ou exposição ao calor, pressão , electricidade, luz, etc.).
O foco atual está principalmente em cadeias simples filamentosas e materiais finos em forma de folha, sendo o próximo objetivo da pesquisa a criação de estruturas tridimensionais mais complexas.
Atualmente, a impressão 4D é particularmente adequada para imprimir cadeias simples filamentosas. Quanto à “programação geométrica”, refere-se à relação de resposta entre os estímulos materiais e as propriedades físicas mencionadas acima, sendo o mecanismo de resposta primário a geração de deformações características localizadas (ou deformações de incompatibilidade) dentro do objeto impresso durante ou após a impressão. processo.
Para o professor Skylar Tibbits e seu Laboratório de Automontagem, os equipamentos e materiais utilizados para impressão 4D são fornecidos pela Stratasys, enquanto a “programação” geométrica é fornecida pela equipe de pesquisa e desenvolvimento da Autodesk. Eles também desenvolveram um novo software chamado Cyborg. A Figura 8-5 ilustra a explicação da professora Skylar Tibbits sobre a impressão 4D de forma mais intuitiva.
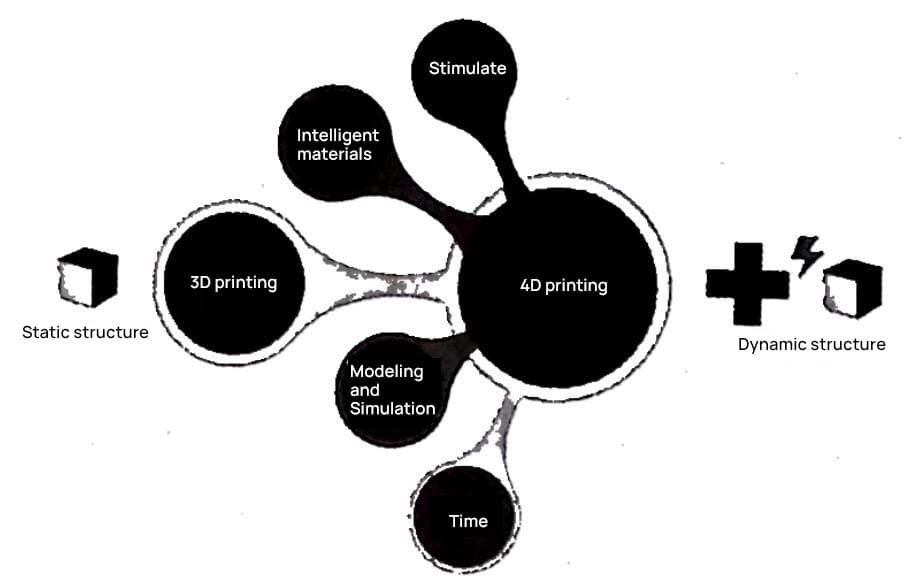
Em 2014, o professor Li Dicheng, da Universidade Xi'an Jiaotong, ofereceu um conceito conciso de impressão 4D: a impressão 4D refere-se à fabricação aditiva de materiais inteligentes, o que significa que estruturas feitas a partir da tecnologia de impressão 3D podem mudar sua forma e estrutura ao longo do tempo quando estimuladas por fatores ambientais externos. A dimensão adicional que a tecnologia de impressão 4D acrescenta à impressão 3D é o tempo.
Assim, o conceito inicial de impressão 4D pode ser entendido simplesmente como “impressão 3D + tempo”, focando na mudança de forma dos componentes ao longo do tempo com materiais inteligentes. Acredita-se que à medida que a pesquisa sobre impressão 4D continuar a se aprofundar, seu conceito e essência serão ainda mais elevados.
Materiais para impressão 4D
Um componente chave da impressão 4D são os materiais inteligentes. No final da década de 1980, inspirados por certas capacidades encontradas na natureza, cientistas americanos e japoneses introduziram pela primeira vez o conceito de inteligência no campo dos materiais e estruturas, propondo a ideia inovadora de estruturas materiais inteligentes.
Também conhecidos como estruturas inteligentes ou responsivas, esses sistemas integram elementos sensores, atuadores e processamento de sinais associados e circuitos de controle dentro da estrutura do material. Eles são projetados para responder a estímulos e controles mecânicos, térmicos, ópticos, químicos, elétricos e magnéticos.
Esses materiais não são apenas capazes de suportar cargas, mas também possuem a capacidade de reconhecer, analisar, processar e controlar, oferecendo recursos multifuncionais como autodiagnóstico, autoadaptação, autoaprendizagem e autorreparo.
Estruturas materiais inteligentes representam uma fronteira interdisciplinar, abrangendo uma ampla gama de campos como mecânica, ciência dos materiais, física, biologia, eletrônica, ciência de controle, ciência da computação e tecnologia. Um número significativo de especialistas destas disciplinas em todo o mundo está activamente empenhado no avanço destes campos.
Existem inúmeras classificações para materiais inteligentes, que podem ser amplamente categorizados com base em sua função e composição em materiais com memória de forma, polímeros eletroativos, materiais piezoelétricos, fluidos eletrorreológicos e materiais magnetostritivos, sendo os materiais com memória de forma os mais amplamente utilizados.
Os materiais com memória de forma incluem polímeros com memória de forma (SMPs), ligas com memória de forma (SMAs), hidrogéis com memória de forma (SMHs), cerâmicas com memória de forma (SMCs) e compósitos com memória de forma (SMCs).
Polímeros com memória de forma (SMPs), também conhecidos como polímeros com memória de forma, são materiais poliméricos que podem mudar e fixar sua forma inicial sob certas condições e, em seguida, recuperar sua forma original após estimulação por condições externas, como calor, eletricidade, luz ou produtos químicos. indução.
A tecnologia SMP utiliza a moderna teoria da física dos polímeros, juntamente com técnicas de síntese e modificação de polímeros, para projetar molecularmente e ajustar a estrutura molecular de materiais poliméricos comuns, como polietileno, poliisopreno, poliéster, copoliéster, poliamida, copoliamida e poliuretano.
Esses materiais são dotados de uma forma específica sob certas condições (estado inicial), que pode mudar e ser fixada (estado deformado) quando as condições externas variam. Se o ambiente externo mudar novamente de uma maneira específica, eles poderão retornar reversivelmente ao estado inicial, completando o ciclo de memorização do estado inicial, fixando o estado deformado e retornando ao estado inicial.
Os SMPs são categorizados com base no tipo de estímulo aos quais respondem, incluindo SMPs induzidos termicamente, SMPs induzidos eletricamente, SMPs induzidos por luz e SMPs induzidos quimicamente.
Polímero com Memória de Forma, SMP
Os SMPs induzidos termicamente deformam-se acima da temperatura ambiente e podem corrigir a deformação durante o armazenamento por longos períodos. Quando aquecidos a uma temperatura de resposta específica, os componentes recuperam rapidamente a sua forma inicial.
Esses polímeros são amplamente utilizados em vários campos, como saúde, esportes, construção, embalagens, automotivo e experimentos científicos, incluindo dispositivos médicos, espuma de plástico, almofadas de assento, mídia óptica de armazenamento de informações e alarmes.
A função de memória de forma dos SMPs induzidos termicamente origina-se principalmente de duas fases incompatíveis dentro do material: a fase fixa que retém a forma do produto moldado e a fase reversível que sofre amolecimento e endurecimento com as mudanças de temperatura. A fase fixa é responsável por memorizar e recuperar a forma original, enquanto a fase reversível permite que o produto mude de forma.
Com base nas características estruturais da fase fixa, os SMPs induzidos termicamente podem ser divididos em categorias termoendurecíveis e termoplásticas. Além disso, existe um polímero com memória de forma denominado “moldagem por deformação a frio”, que envolve o processamento a frio de certas resinas termoplásticas abaixo da temperatura T para obter alta deformação elástica e depois resfriar para obter um estado deformado.
Quando reaquecido acima da temperatura Tgo material também pode retornar à sua forma original.
SMPs induzidos eletricamente são compostos de materiais poliméricos com memória de forma induzidos termicamente com substâncias condutoras, como negro de fumo condutor, pó metálico e polímeros condutores. Seu mecanismo de memória é idêntico ao dos polímeros com memória de forma induzidos termicamente. O material compósito utiliza o calor gerado a partir de uma corrente elétrica para aumentar a temperatura do sistema e induzir a recuperação da forma.
Portanto, possui propriedades condutoras e excelente funcionalidade de memória de forma, usada principalmente em eletrônica, comunicações e instrumentação, como tubos de raios catódicos eletrônicos e materiais de blindagem eletromagnética.
Os SMPs foto-responsivos incorporam grupos fotocrômicos específicos (PCGs) nas cadeias principal e lateral do polímero. Após a exposição à luz UV, os PCGs sofrem uma reação de fotoisomerização, causando uma mudança significativa no estado da cadeia molecular.
Macroscopicamente, o material exibe uma transformação de forma induzida pela luz. Quando a exposição à luz cessa, os PCGs reagem reversivelmente, revertendo o estado molecular e o material à sua forma original. Esses materiais são utilizados em impressão, gravação óptica, válvulas moleculares acionadas por luz e sistemas de liberação controlada de medicamentos.
Os SMPs induzidos quimicamente são ativados por mudanças no meio circundante para permitir a deformação do material e a recuperação da forma. Estímulos químicos comuns incluem alterações de pH, equilíbrio de troca iônica, reações de quelação, transições de fase e reações redox.
Esses materiais incluem poliacrilamida parcialmente saponificada, álcool polivinílico e misturas de ácido poliacrílico em forma de filme e são usados em campos especializados, como membranas de separação para proteínas ou enzimas e motores químicos.
Liga com memória de forma, SMA
Ligas com memória de forma (SMAs) são materiais compostos por dois ou mais elementos metálicos que apresentam efeito de memória de forma (SME) por meio de transformações de fase termoelásticas martensíticas e seu reverso.
Os SMAs oferecem o melhor desempenho de memória de forma entre os materiais com memória de forma. A martensita termoelástica, uma vez formada, continua a crescer à medida que a temperatura diminui e diminui com o aquecimento, desaparecendo em um processo completamente reversível. A diferença na energia livre atua como força motriz para a transformação de fase.
Os SMAs são categorizados em três classes com base em suas características de deformação:
Efeito de memória de forma unidirecional: os SMAs se deformam em temperaturas mais baixas e recuperam sua forma original após aquecimento, exibindo um efeito de memória de forma apenas durante o processo de aquecimento.
Efeito de memória de forma bidirecional: Certas ligas recuperam sua forma de fase de alta temperatura após aquecimento e revertem para sua forma de fase de baixa temperatura após resfriamento.
Efeito de memória de forma completa: Após o aquecimento, o material recupera sua forma de fase de alta temperatura e, após o resfriamento, faz a transição para uma forma de fase de baixa temperatura com a mesma geometria, mas orientação oposta.
Até o momento, foram descobertos mais de 50 tipos de ligas com efeitos de memória de forma. Em 1969, o efeito de memória de forma da liga de níquel-titânio foi aplicado pela primeira vez industrialmente, levando à criação de um dispositivo exclusivo de acoplamento de tubos.
Ao adicionar outros elementos à liga de níquel-titânio, novas ligas com memória de forma à base de níquel-titânio, como níquel-titânio-cobre, níquel-titânio-ferro e níquel-titânio-cromo, foram desenvolvidas e pesquisadas. Além disso, existem outros tipos de ligas com memória de forma, incluindo cobre-níquel, cobre-alumínio, cobre-zinco e ligas à base de ferro (Fe-Mn-Si, Fe-Pd).
Os SMAs são amplamente utilizados em vários campos, como aeroespacial, eletrônica mecânica, engenharia biomédica, construção de pontes, indústria automotiva e na vida cotidiana.
Hidrogéis com Memória de Forma (SMH)
Os hidrogéis são um tipo de gel de rede tridimensional altamente hidrofílico que pode inchar rapidamente na água e reter um volume significativo de água sem se dissolver no estado inchado. A absorção de água está intimamente relacionada com o grau de reticulação; quanto maior for a reticulação, menor será a absorção de água. Os hidrogéis podem ser categorizados em hidrogéis tradicionais e hidrogéis ambientalmente responsivos com base na sua resposta a estímulos externos.
Os hidrogéis tradicionais não são sensíveis a mudanças ambientais como temperatura ou pH; adaptam-se alterando a ligação cruzada das macromoléculas para capturar e libertar água (fornecendo estímulo), conseguindo assim contracção e expansão para facilitar transições estruturais.
Os hidrogéis ambientalmente responsivos, por outro lado, são capazes de detectar pequenas alterações ou estímulos no ambiente externo (como temperatura, pH, luz, eletricidade, pressão, etc.) e responder com alterações significativas nas propriedades físicas e químicas, até mesmo transformações abruptas. . A característica destes hidrogéis é a notável mudança no seu comportamento de inchamento em resposta a fatores ambientais.
Com base nos diferentes mecanismos de resposta destes dois tipos de hidrogéis, hidrogéis com memória de forma foram desenvolvidos e podem ser usados como sensores, interruptores de controle, etc.
Cerâmica com Memória de Forma (SMC)
Os SMCs exibem efeitos de memória de forma que diferem dos SMPs e SMAs das seguintes maneiras: Primeiro, os SMCs têm uma capacidade de deformação menor; segundo, os SMCs experimentam vários graus de deformação irreversível com cada memória de forma e ciclo de recuperação e, à medida que o número de ciclos aumenta, a deformação cumulativa aumenta, levando, em última análise, à formação de fissuras.
SMCs podem ser classificados com base no mecanismo de geração de efeito de memória de forma em cerâmicas com memória de forma viscoelástica, cerâmicas com memória de forma de transformação de fase martensítica, cerâmicas ferroelétricas com memória de forma e cerâmicas ferromagnéticas com memória de forma.
As cerâmicas com memória de forma viscoelástica incluem óxido de cobalto, óxido de alumínio, carboneto de silício, nitreto de silício e cerâmica de vidro de mica. Quando estes materiais são aquecidos a uma determinada temperatura, eles são deformados sob carga, com a força externa mantendo a deformação. Após o resfriamento e posterior reaquecimento a uma temperatura específica, a deformação da cerâmica recupera ao seu estado original.
Estudos sugerem que as cerâmicas viscoelásticas com memória de forma contêm duas estruturas – cristalina e vítrea – e que a energia elástica que impulsiona a recuperação da forma é armazenada em uma dessas estruturas, enquanto a deformação ocorre na outra.
Cerâmica martensítica com memória de forma, como ZrO2BaTiO3KNbO3PbTiO3são empregados principalmente em elementos atuadores de armazenamento de energia e materiais funcionais especializados.
Cerâmicas ferroelétricas com memória de forma referem-se a cerâmicas que exibem características de memória de forma quando sua orientação muda sob um campo elétrico externo. As regiões de fase das cerâmicas ferroelétricas com memória de forma incluem substâncias paraelétricas, ferroelétricas e antiferroelétricas, com tipos de transição de fase como transformações paraelétricas-ferroelétricas e antiferroelétricas-ferroelétricas.
Estas transições de fase podem ser induzidas por um campo elétrico ou pela comutação ou reorientação de domínios magnéticos polares. Embora as cerâmicas ferroelétricas com memória de forma tenham deformações menores em comparação com as ligas com memória de forma, elas apresentam tempos de resposta rápidos.
Eles também podem sofrer transições reversíveis, como paramagnético-ferromagnético, paramagnético-antiferromagnético, ou de estados orbitais ordenados para desordenados, normalmente acompanhados por deformações de rede recuperáveis.
Aplicações de impressão 4D
Objetos fabricados por meio de impressão 4D são produtos inteligentes que possuem capacidades adaptativas e de autocura. Eles são amplamente aplicáveis em vários setores, incluindo tecidos e órgãos artificiais, dispositivos médicos, transporte automotivo, maquinário de precisão, aeroespacial, indústria de defesa, bem como na moda, móveis e construção. Aqui estão sete exemplos de aplicações específicas:
(1) Vestido de treliça estampado em 4D
A Nervous System, fundada nos Estados Unidos em 2007 por Jessica e Jessie, ambas formadas pelo MIT, sendo que Jessica é formada em arquitetura pela mesma instituição da professora Skylar Tibbits, começou a usar um tecido especial para criar vestidos por meio de impressão 4D em 2014. O vestido , conforme mostrado na Figura 8-6, consiste em uma estrutura de treliça composta por 2.279 triângulos e 3.316 pontos de articulação, conforme ilustrado na Figura 8-7.
A tensão entre os triângulos e as dobradiças se ajusta ao formato do corpo do usuário, garantindo que o vestido caiba bem mesmo com mudanças de peso. Este vestido não apenas aborda questões de ajuste, mas também se adapta ao formato do corpo do usuário. O vestido é criado usando a tecnologia de impressão 3D SLS, deixando o pó não sinterizado cair após a impressão, resultando em uma estrutura de fibra interligada.
A Nervous System também desenvolveu um aplicativo que permite aos usuários realizar uma digitalização 3D de seu corpo, escolher o tamanho e a forma do tecido e personalizar um vestido exclusivo impresso em 4D. Atualmente, este vestido impresso em 4D é coletado permanentemente por quatro museus ou galerias.
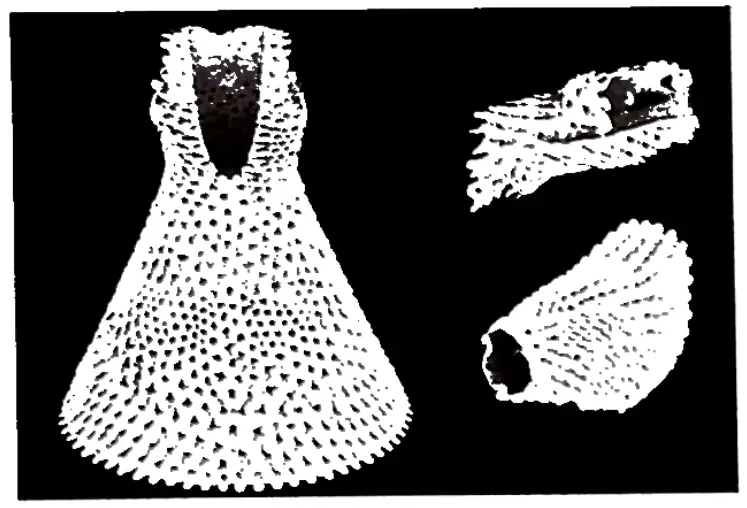
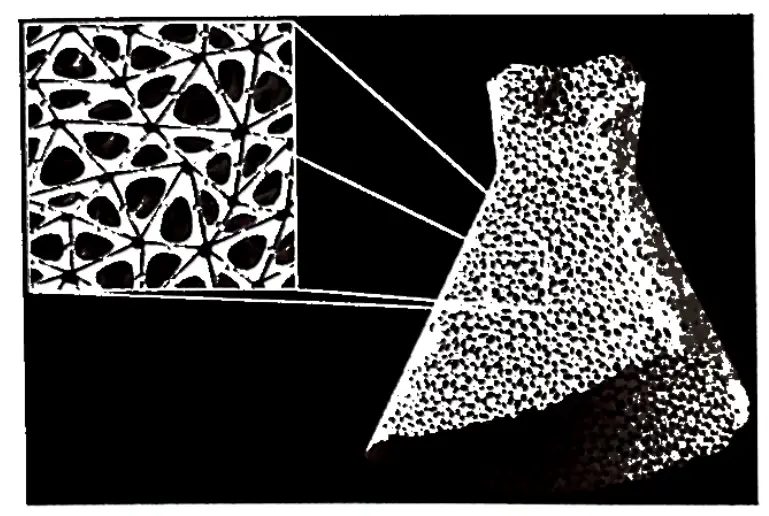
Tecido de metal espacial impresso em 4D
Em 2017, uma equipe de pesquisa liderada por Raul Polit Casillas, do Laboratório de Propulsão a Jato da NASA, relatou a criação de um tecido metálico dobrável usando tecnologia de impressão 4D, conforme mostrado na Figura 8-8. O tecido apresenta pequenos quadrados de metal prateado na frente e fios de metal preto na parte de trás, conforme mostrado na Figura 8-9.
Esta estrutura aumenta significativamente a sua capacidade de resistir a impactos externos e também é convenientemente projetada para aplicação em superfícies de naves espaciais ou trajes espaciais de astronautas. A estrutura pode refletir luz (lado quadrado metálico) e absorver calor (lado fio metálico), abrangendo cinco capacidades: resistência ao impacto físico, capacidade de dobramento semelhante a um tecido, resistência à tração semelhante à do aço, refração de luz intensa e gerenciamento térmico passivo.
O gerenciamento térmico passivo permite que a espaçonave mantenha um diferencial mínimo de temperatura com o ambiente externo, alcançando equilíbrio dinâmico quando este material é utilizado como cobertura.
A NASA prevê que este tecido metálico seja utilizado em vários domínios, incluindo grandes antenas dobráveis e que mudam de forma, isolamento térmico para naves espaciais que visitam planetas/luas frias e geladas, bem como tapetes flexíveis de isolamento para astronautas, escudos de meteoritos em miniatura para naves espaciais e trajes espaciais.
Além disso, este material inovador pode ser usado em aeronaves em luas/planetas gelados, criando “pés” dobráveis que se adaptam às superfícies planetárias ásperas, ajudando a evitar certos danos físicos e facilitando a coleta de amostras.
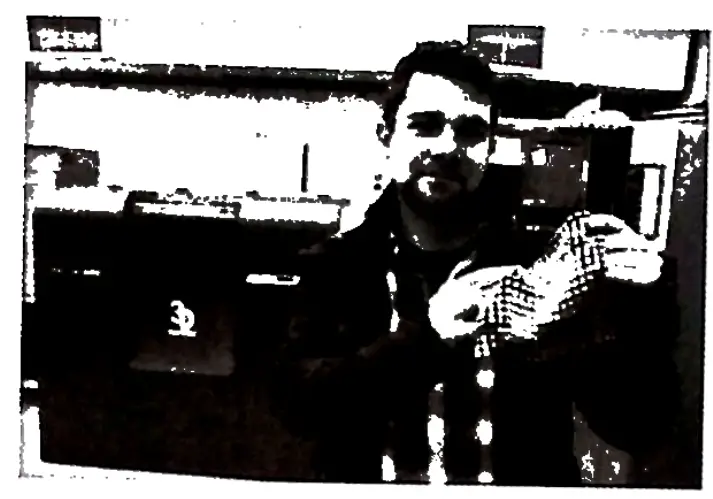
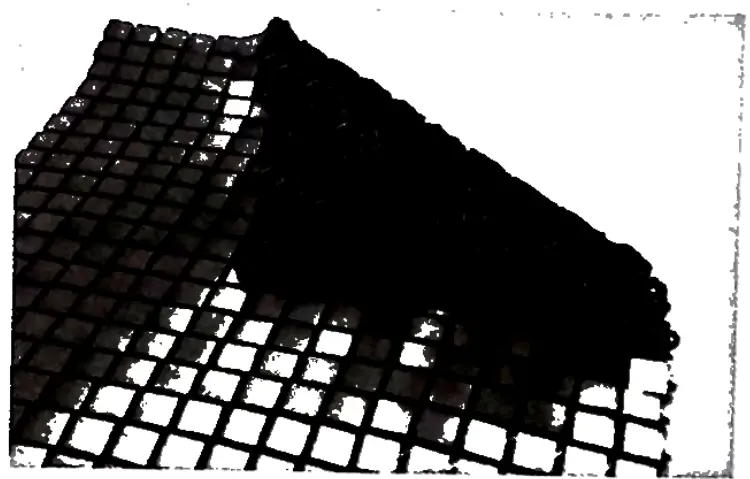
Stent traqueal biodegradável impresso em 4D
Em 28 de março de 2016, cirurgiões torácicos do Hospital Tangdu, afiliado à Quarta Universidade Médica Militar, usaram tecnologia de impressão 4D de ponta para aliviar o sofrimento de um paciente com traqueomalácia causada por tuberculose endobrônquica traqueal. O segmento traqueal afetado excedeu o comprimento máximo permitido para ressecção, impossibilitando sua remoção.
A implantação tradicional de stent pode levar a complicações como dificuldade de expectoração. Internacionalmente, a Universidade de Michigan relatou um caso semelhante no The New England Journal of Medicine, onde especialistas desenvolveram uma suspensão de stent externo para um paciente com doença brônquica esquerda abrangendo apenas 1-1,5 cm, enquanto este paciente tinha uma lesão de 6 cm no traqueia, representando um desafio maior.
Após análise cuidadosa das características da doença, o Dr. Li Xiaofei, o vice-diretor Huang Lijun e o Dr. Medical University, criou um modelo traqueal impresso em 3D.
Após uma avaliação minuciosa, decidiram prosseguir com a cirurgia de suspensão externa do stent. Eles também fizeram parceria com a equipe do professor He Jiankang da Universidade Xi'an Jiaotong para fabricar um stent traqueal biodegradável impresso em 4D para o paciente, conforme mostrado na Figura 8-10.
Utilizando o stent traqueal biodegradável impresso em 4D para envolver a traqueia enfraquecida e suturá-la no lugar, a traqueia colapsada foi apoiada e a via aérea estreitada foi aberta. Foi realizada comunicação pré-operatória completa com o paciente e sua família, conforme ilustrado na Figura 8-11.
A cirurgia foi um sucesso e o paciente se recuperou bem no pós-operatório.
O período de degradação do stent pode ser regulado controlando o tipo e peso molecular do biomaterial, permitindo que ele se degrade gradativamente e seja absorvido pelo organismo durante os próximos 2 a 3 anos, poupando ao paciente a dor de uma segunda cirurgia para remoção do stent .
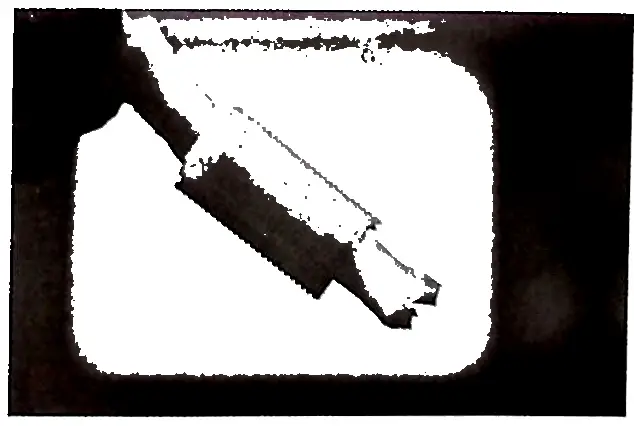
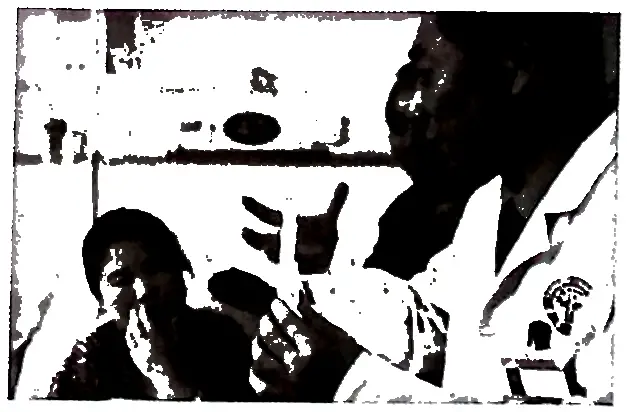
Esta cirurgia foi a primeira deste tipo a nível internacional, envolvendo a suspensão de um stent externo para um segmento mole extremamente alongado da traqueia. Além disso, em setembro daquele ano, médicos do Hospital Xijing da Quarta Universidade Médica Militar se uniram à equipe He Jiankang da Universidade Xi'an Jiaotong.
Usando um stent traqueal absorvível impresso em 4D semelhante, eles realizaram uma cirurgia de suspensão do stent em uma criança de 5 meses que sofria de doença cardíaca congênita complexa combinada com estenose brônquica bilateral grave, curando com sucesso a doença – outra novidade mundial.
Oclusores SMP impressos em 4D
Em 2019, o professor Liu Liwu do Harbin Institute of Technology colaborou com especialistas clínicos do First Affiliated Hospital da Harbin Medical University para incorporar partículas magnéticas de Fe3O4 em uma matriz de ácido polilático com memória de forma. Eles projetaram e imprimiram em 4D um oclusor SMP biodegradável e personalizável que poderia ser implantado remotamente e de forma controlada sob uma intensidade de campo magnético específica.
Eles também conduziram experimentos de viabilidade in vitro com o oclusor SMP impresso em 4D para testar a simplicidade de seu processo de implantação, conforme mostrado nas Figuras 8-12. O oclusor SMP pode ser facilmente embalado, entregue e liberado através de um cateter, com o processo de implantação sendo concluído em 16 segundos.
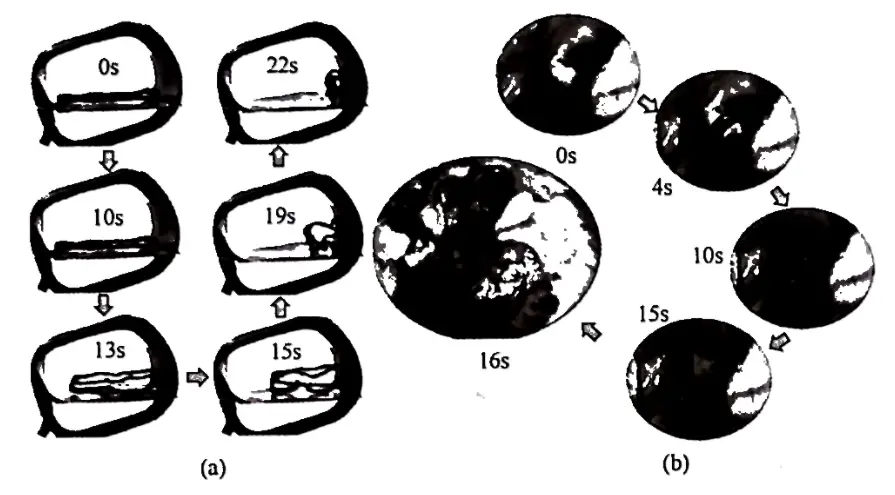
Sistemas robóticos de automontagem impressos em 4D
Na Conferência Internacional IEEE sobre Robótica e Automação em 2013, Samuel M. Felton, do Instituto de Engenharia Biologicamente Inspirada da Escola de Engenharia e Ciências Aplicadas de Harvard, apresentou um sistema robótico de automontagem feito usando tecnologia de impressão 4D.
O campo da robótica, que exige alto desempenho estrutural, automação e inteligência, muitas vezes vê efeitos surpreendentes ao combinar polímeros com memória de forma, sendo o sistema robótico de automontagem particularmente significativo. Este sistema de automontagem impresso em 4D mescla materiais planos rígidos com SMPs, obtendo ações sequenciais de dobramento, controle de ângulo e ranhura mediante estimulação externa.
As Figuras 8-13 (a) representam um robô semelhante a um verme equipado com um sistema robótico de automontagem impresso em 4D, capaz de se dobrar em uma forma funcional que se move sob corrente elétrica adequada; A Figura 8.13(b) mostra o mesmo robô semelhante a um verme demonstrando sua autopropulsão a uma velocidade de 2 µm/s. Esses robôs automontáveis podem reduzir custos de material, processamento e transporte e têm perspectivas promissoras para explorar áreas confinadas.
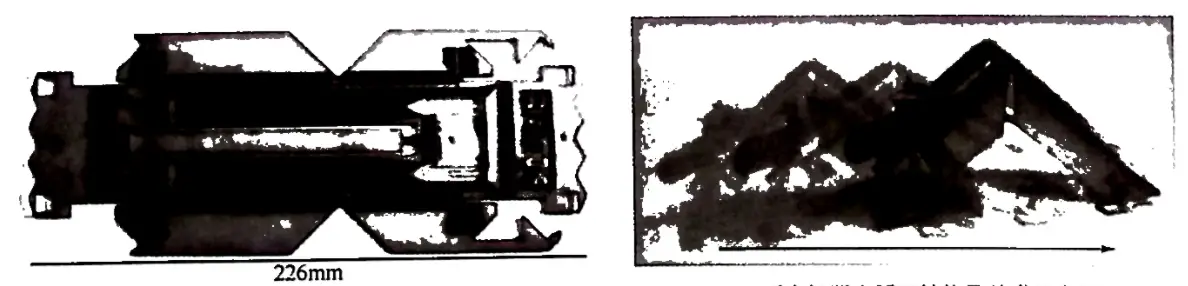
(a) Robô semelhante a um verme com sistema robótico de automontagem impresso em 4D
(b) Estrutura implantada e diagrama de progressão do robô semelhante a um verme
(6) Roupas esportivas sensíveis à umidade impressas em 4D
Em 2017, o professor Zhao Xuanhe, do Instituto de Tecnologia de Massachusetts, depositou micróbios geneticamente tratáveis em um material inerte à umidade usando um processo de impressão 3D, criando um filme biohíbrido com uma estrutura multicamadas de densidade microbiana irregular. Utilizando os comportamentos higroscópicos e bioluminescentes das células vivas, este filme biohíbrido pode responder aos gradientes de umidade ambiental em segundos.
Altera reversivelmente a forma da estrutura multicamadas e a intensidade da bioluminescência, formando abas abertas e de ventilação em ambientes de alta umidade, conforme ilustrado na Figura 8-14. Esse filme biohíbrido foi transformado em roupas esportivas sensíveis à umidade para aprimorar a experiência atlética, conforme ilustrado na Figura 8-15.
Uma vez que a deposição desta estrutura multicamadas constitui uma produção aditiva de materiais inteligentes sensíveis à humidade, este processo de impressão 3D também pode ser referido como impressão 4D.
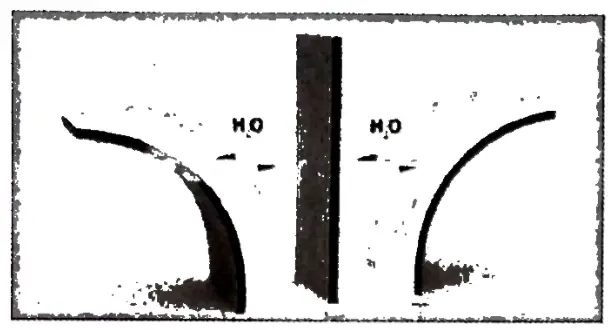
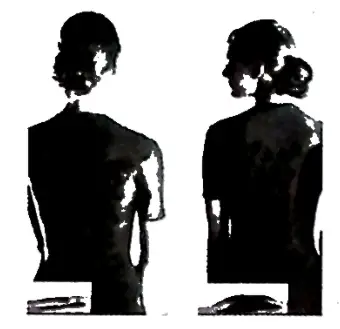
(7) Grande Deformação, Estruturas Autotransformadas de Alto Módulo
Em 2020, a equipe do professor H. Jerry Qi do Georgia Institute of Technology demonstrou um método para projetar e fabricar estruturas autotransformáveis, capazes de grandes deformações e alto módulo. Eles imprimiram as estruturas projetadas usando processos DIW multimateriais com tintas compostas que consistem em uma fração de alto volume de solvente, resinas fotopolimerizáveis, fibras curtas de vidro e sílica gasosa.
Durante a impressão, as fibras de vidro foram alinhadas através da orientação induzida por cisalhamento através do bocal, resultando em propriedades mecânicas altamente anisotrópicas. O solvente foi então evaporado, causando encolhimento anisotrópico das fibras de vidro alinhadas nas direções paralela e perpendicular. Uma etapa subsequente de pós-cura aumentou ainda mais a rigidez do material compósito de aproximadamente 300 MPa para cerca de 4,8 GPa.
O processo de impressão e deformação, ilustrado na Figura 8-16, é descrito acima. Um modelo de análise de elementos finitos foi desenvolvido para prever os efeitos do solvente, do conteúdo da fibra e da orientação da fibra nas mudanças de forma.
Os resultados confirmaram que a retração volumétrica anisotrópica poderia atuar como uma dobradiça ativa, permitindo a autotransformação de estruturas complexas com grande deformação e alto módulo. Estas estruturas mostram aplicações potenciais em estruturas leves com capacidade de suporte de carga.
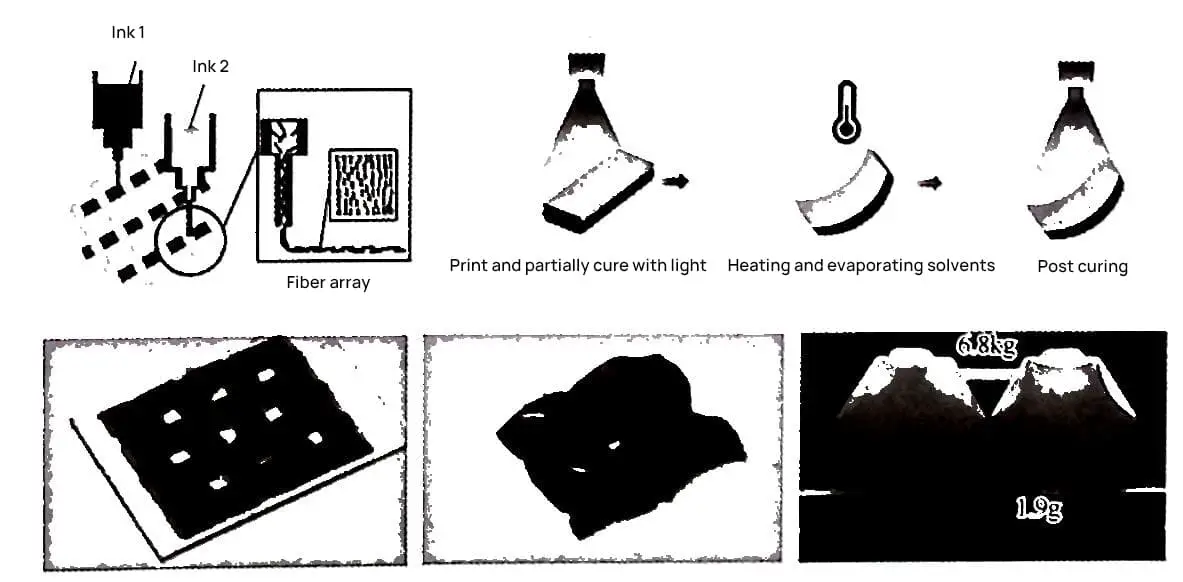