Índice Técnico Principal do Método de Condução do Cortador a Laser
AVC
O curso de um cortador a laser é a faixa de processamento que ele pode realizar, que determina o tamanho máximo da peça que pode ser processada e é um parâmetro fundamental.
A faixa de processamento mais comum atualmente é de 3m x 1,5m, o que oferece um bom equilíbrio entre capacidades mecânicas, faixa de processamento e custos de fabricação.
No entanto, à medida que o nível industrial global continua a melhorar, a proporção de modelos maiores tem aumentado ano após ano.
Precisão de posicionamento
Como máquinas-ferramenta especializadas, as máquinas de corte a laser são semelhantes às máquinas-ferramentas a frio tradicionais. O quadro geral de transmissão é essencialmente o mesmo. No entanto, o corte a laser normalmente não é usado para fins de usinagem de precisão, portanto a precisão absoluta da transmissão é ligeiramente inferior à das máquinas-ferramentas NC a frio.
A precisão de posicionamento da máquina reflete o posicionamento do fabricante, a entrada do produto e o grau de precisão das peças de transmissão selecionadas. No entanto, para o corte a laser, a precisão do posicionamento não tem um efeito significativo no resultado final do processamento, como tolerâncias de tamanho de peça e qualidade da seção cortada.
Para cortes finos, entretanto, o equipamento de corte a laser pode cortar com precisão uma dúzia de mícrons da fenda, o que está no mesmo nível da precisão operacional do cortador a laser. Neste ponto, a precisão do posicionamento torna-se muito importante.
Precisão de reposicionamento
A precisão de reposicionamento alcançada por uma máquina de corte a laser depende em grande parte da folga reversa da corrente de transmissão, que é semelhante à usinagem a frio tradicional.
A folga reversa da máquina de corte a laser também tem alguma influência na rugosidade da seção cortada. Os usuários que são muito exigentes quanto à qualidade do corte de seções devem prestar muita atenção a este indicador.
Velocidade de posicionamento
A velocidade de posicionamento, que é o parâmetro técnico mais aparente visualmente, é um índice chave ao qual todo fabricante de cortadores a laser presta atenção. É frequentemente usado como o principal critério para classificar propriedades mecânicas e classes de cortadores a laser.
Atualmente, os modelos de topo quebraram sucessivamente a velocidade de posicionamento de eixo único de 100m/min. A alta velocidade de posicionamento tem um impacto significativo na melhoria da eficiência do processamento de folhas.
No entanto, para chapas de espessura média, devido às limitações da velocidade de corte, reduzir o tempo total de processamento pode não ser tão crucial.
Força motriz
Devido à alta flexibilidade do processamento a laser, o corte em alta velocidade de peças complexas tornou-se o principal método para vários fabricantes exibirem propriedades mecânicas.
O corte em alta velocidade exige alto torque de saída para o motor. A cadeia de transmissão exige alta eficiência e resposta rápida para garantir a precisão do rastreamento e atender aos requisitos de supressão. Portanto, a aceleração é tão crítica quanto a velocidade de posicionamento.
No entanto, existe um compromisso entre alta velocidade e alta aceleração. Isto exige que os fabricantes de cortadores equilibrem cuidadosamente a relação e encontrem a solução ideal através de cálculos e experimentação.
Rigidez de transmissão
Durante o processo de alta velocidade de uma máquina de corte a laser, a tensão interna da corrente de transmissão pode flutuar violentamente. Se a rigidez da transmissão for insuficiente, pode facilmente causar distorção da trilha e resposta lenta da saída final. Isso faz com que a precisão da operação dinâmica esteja longe dos valores de medição baixos ou estáticos, o que pode afetar a precisão dimensional e a rugosidade da peça de trabalho.
No entanto, este índice não é facilmente quantificado.
4 métodos de condução da máquina de corte a laser
Acionamento por correia síncrona
A correia síncrona dentada (mostrada na FIG. 1) é composta principalmente por polias e correias.
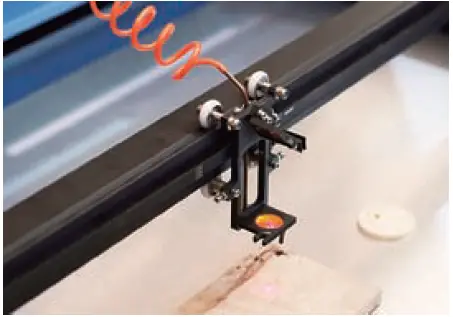
Fig.1 Transmissão por correia síncrona
Normalmente, a roda motriz e o servo motor também utilizam um redutor para amplificação de torque quando se utiliza a correia dentada síncrona (mostrada na Figura 1).
A correia síncrona dentada tem vantagens como velocidade rápida, baixo ruído, baixo custo, sem necessidade de lubrificação e fácil manutenção. No entanto, tem desvantagens como diferenças de rigidez, fácil desgaste, baixa precisão e pequena força motriz. Portanto, é adequado para aplicações de baixo custo, carga leve e alta velocidade.
É amplamente utilizado em equipamentos de corte e marcação a laser de pequena e média potência, que são de baixo custo e não requerem alta precisão.
Para equipamentos de corte a laser de alta velocidade e alta precisão, a precisão de funcionamento da correia síncrona obviamente não é suficiente, e a capacidade de carga também não é suficiente para acionar diretamente peças móveis pesadas, rígidas e de grande porte. O arranjo mais comum é colocá-lo na corrente de transmissão do fuso de esferas de alta velocidade e outras instituições para formar uma transmissão de dois estágios.
No produto básico de máquinas de corte a laser de alta potência, o acionamento do eixo Z é acionado diretamente pela correia síncrona (conforme mostrado na figura 2).
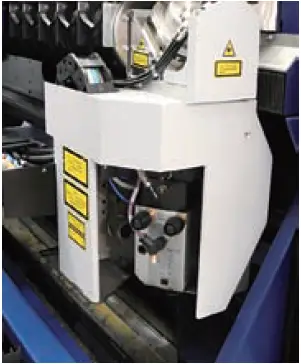
Fig.2 O movimento superior e inferior da cabeça de corte da seção do eixo z é acionado pela correia síncrona.
Para uma máquina bidimensional com sistema de três eixos, a precisão da transmissão do eixo z normalmente não afeta a precisão e a qualidade do corte.
Esse projeto aproveita de forma inteligente os benefícios da transmissão síncrona por correia, como velocidade rápida, baixo ruído e baixo custo, ao mesmo tempo em que evita a desvantagem da baixa precisão.
Acionamento por fuso de esfera
O parafuso esférico (mostrado na FIG. 3) é um mecanismo de acionamento comumente usado em vários tipos de equipamentos de processamento a frio. Esta tecnologia foi amplamente desenvolvida e seu custo é razoável.
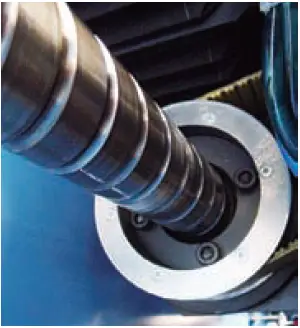
Fig.3 Parafuso de esfera rotativo porca
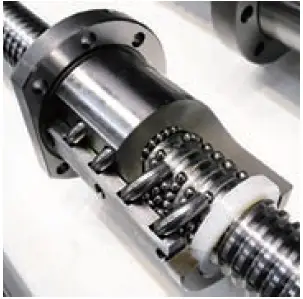
Fig.4 Estrutura interna do fuso de esfera
O fuso de esfera é um mecanismo de acionamento amplamente utilizado em vários equipamentos de processamento a frio devido à sua capacidade de atingir folga zero e manter alta eficiência e rigidez de transmissão por meio da aplicação de pré-pressão ou excursão de avanço. Ele também pode atingir até 95% de eficiência de transmissão, tornando-o um método de condução ideal para diversas aplicações.
No entanto, o uso de um fuso de esferas em uma máquina de corte a laser tem limitações. Devido ao seu peso, o parafuso esférico normalmente é apoiado em duas extremidades, resultando em uma certa inclinação no centro do parafuso. Esta deflexão pode causar instabilidade, especialmente em altas velocidades.
Para resolver esse problema, um fio-máquina mais grosso deve ser selecionado, o que pode aumentar os custos de fabricação e colocar uma carga mais pesada no motor. Portanto, o fuso de esferas é uma excelente escolha para métodos de acionamento em cortadores a laser com curso curto e pequena área de corte, pois sua precisão, velocidade e custo são adequados para tais aplicações.
No entanto, para aplicações de curso longo (≥3m) e alta velocidade (≥60m/min), a integração de uma chave de fuso de esferas não é o método ideal. Embora seja possível obter aplicações de curso longo e alta velocidade com um fuso de esferas por meio da rotação da porca ou da adição de um dispositivo de suporte auxiliar para evitar o movimento da porca, tais soluções são tecnicamente desafiadoras e enfrentam desafios significativos em termos de custo e confiabilidade.
Engrenagem e rack
A cremalheira é comumente combinada com redutores de engrenagem planetária ou redutores de rosca sem-fim de turbina para corresponder à inércia e amplificar o torque. Alguns fabricantes também utilizam motores de torque para conexão direta com a engrenagem final.
As cremalheiras de alta precisão são semelhantes aos fusos de esferas em termos de precisão de posicionamento, pois podem facilmente atingir uma precisão de posicionamento de 0,03 mm/m, que é superior à precisão necessária para corte a laser.
Em relação à velocidade, a engrenagem e a cremalheira podem alcançar várias combinações alterando o número dos dentes da engrenagem e a relação de velocidade do redutor. Não há limite para a velocidade crítica do fuso de esferas, facilitando o trabalho dos servomotores em faixas de alta velocidade e encurtando o passo equivalente para acionar grandes cargas de inércia com motores menores.
O limite teórico de engrenagem e cremalheira pode chegar a 400m/min, sendo fácil atingir velocidades de até 100m/min.
Tanto os dentes retos quanto os dentes tortos são amplamente utilizados em máquinas de corte a laser. Os dentes tortos são mais fáceis de instalar e detectar e podem atingir maior precisão operacional sob a mesma precisão de usinagem e condições de instalação.
A vantagem dos dentes tortos é que eles têm uma capacidade de carga ligeiramente maior sob a mesma carga, o que torna o projeto mais compacto. Além disso, a diferença mais significativa entre os dois tipos é que o ruído dos dentes tortos é relativamente baixo em altas velocidades, proporcionando um melhor ambiente operacional para os operadores.
Contanto que a base consiga manter precisão e rigidez suficientes, o curso da cremalheira pode ser estendido quase indefinidamente, com os custos de fabricação aumentando linearmente.
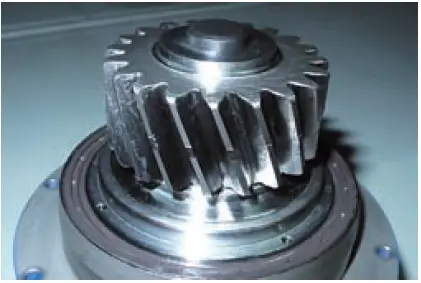
Fig.5 Acionamento da engrenagem de soldagem a laser
Contudo, a cremalheira (Figura 6) também tem suas desvantagens. Por exemplo, requer maior precisão de usinagem da base e o processo de instalação é mais complicado em comparação com o fuso de esferas. Além disso, devido à necessidade de lubrificação e expansão térmica, existe um retrocesso específico entre a cremalheira e a cremalheira, enquanto o redutor planetário na corrente de transmissão possui uma folga reversa pequena, mas perceptível. O acúmulo desses fatores torna difícil para a cremalheira atingir um efeito de operação com folga zero, como no caso de um fuso de esferas.
O uso de motores duplos, redutores duplos ou outros meios elásticos pode compensar essas desvantagens, mas isso resulta em indicadores desfavoráveis de peso, custo e dirigibilidade.
No entanto, felizmente, com um design razoável e construção precisa, uma cremalheira de dois estágios pode atender bem aos requisitos de precisão do corte a laser convencional atualmente. E ainda há amplo espaço para desenvolvimento.
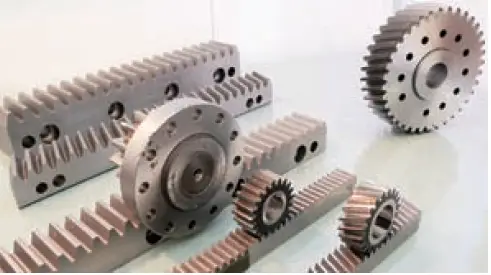
Fig.6 Cremalheira de precisão do máquina de corte a laser
Com consideração abrangente, a precisão do pinhão e da cremalheira é capaz de atender às demandas do corte a laser. Este sistema de acionamento oferece flexibilidade na seleção, maximiza o desempenho do servo motor e facilita a obtenção de alto desempenho dinâmico.
Como resultado, o acionamento por cremalheira tornou-se a principal solução para máquinas de corte a laser de alta potência.
Motor linear
Os motores lineares, como um novo modo de condução, têm sido amplamente utilizados em vários equipamentos NC, incluindo máquinas de corte a laser.
A seguir estão algumas das vantagens claras dos motores lineares:
(1) Não há contato mecânico e a transmissão é gerada no entreferro, resultando em nenhum desgaste direto do componente de acionamento.
(2) O curso é teoricamente ilimitado e o desempenho do motor linear não é afetado por mudanças no itinerário.
(3) Pode fornecer uma ampla faixa de velocidade, de vários micrômetros a vários metros por segundo, sendo a alta velocidade uma vantagem proeminente.
(4) A aceleração é significativa, até 10g.
(5) Alta precisão e repetibilidade são alcançáveis. Como o elo intermediário é eliminado, a precisão do sistema depende do elemento de detecção de posição. Com um dispositivo de feedback apropriado, a precisão operacional final pode atingir o nível submícron. Esse recurso encontrou ampla aplicação no campo de corte de precisão a laser.
Obrigado por solicitar uma revisão do conteúdo. Aqui está a versão revisada:
Devido às vantagens dos motores lineares, as máquinas de corte a laser com motores lineares estabeleceram recordes de velocidade e aceleração na indústria. Parece que o motor linear pode eventualmente substituir os parafusos de esferas e as cremalheiras como o mecanismo de acionamento principal para máquinas de corte a laser.
No entanto, com a adoção generalizada de acionamentos de motores lineares, surgiram novos problemas que não foram previstos anteriormente:
(1) O motor linear consome muita energia, especialmente em altas cargas e acelerações. A corrente instantânea da máquina pode sobrecarregar significativamente o sistema de alimentação da oficina.
(2) A alta vibração ocorre devido à baixa rigidez dinâmica do motor linear, que é incapaz de amortecer o efeito de amortecimento, levando a vibrações ressonantes em altas velocidades em outras partes da máquina.
(3) O motor elétrico linear fixado na parte inferior da bancada gera calor significativo. A posição de instalação não favorece a dissipação natural do calor, representando um desafio significativo para o controle termostático do cortador a laser.
(4) O eixo do motor acionado pelo motor linear, especialmente o eixo vertical, deve ser equipado com um mecanismo de travamento adicional como uma braçadeira guia para garantir uma operação segura. Isso aumenta o custo e a complexidade do cortador a laser.
(5) O motor linear gera um forte campo magnético e atrai limalha de ferro, o que pode ser problemático em ambientes de corte a laser com muito pó de metal minúsculo que é derretido e resfriado pelo laser. Manter a limpeza interna torna-se um desafio.
Embora fabricantes estrangeiros como MAZAK e AMADA tenham introduzido modelos motorizados lineares completos ou parciais para demonstrar a sua competência técnica e estabelecer recordes de velocidade, os preços elevados e os retornos modestos tornaram o mercado menos receptivo a este tipo de modelo.
Apesar do excelente desempenho do motor linear, permanecem questões práticas na aplicação de acionamentos de máquinas de corte a laser. Embora represente uma tendência no futuro, ainda há muito trabalho a ser feito para resolver esses problemas.
Conclusão
A busca por excelente resposta dinâmica é um objetivo comum entre diversos equipamentos de usinagem CNC de precisão, especialmente para usinagem de alta velocidade em máquinas de corte a laser.
Alcançar esse objetivo requer um projeto de sistema vasto e complexo.
Em essência, uma boa carga (leve, alta rigidez, pequena inércia), uma corrente de transmissão robusta (alta rigidez, resposta rápida, baixa folga, alta eficiência, baixo atrito) e um motor potente (correspondência de inércia, resposta rápida, forte torque ) são precisos.
No entanto, a maioria destes fatores são conflitantes entre si, tornando necessário selecioná-los cientificamente e projetar o sistema de acionamento de forma razoável.
Cada fabricante tem seu entendimento e abordagem únicos na seleção e equilíbrio desses fatores para alcançar os melhores resultados.