Introdução
O processamento de chapas metálicas refere-se ao processamento a frio de placas metálicas abaixo de 6 mm. Ele pode ser dividido em duas categorias: processamento de estampagem, adequado para produção em massa, e processamento de chapas CNC, adequado para produção de pequenos lotes. Esta postagem se concentra na análise e melhoria da ondulação de corte durante o corte a laser de chapas metálicas e blanking na produção de pequenos lotes.
O processamento de chapas metálicas tem uma ampla gama de aplicações em indústrias como chassis e gabinetes, eletrodomésticos, produtos de hardware, instrumentos e medidores, outdoors, lâmpadas e fabricação de máquinas. É caracterizado pela rápida velocidade de processamento, ciclo curto, pequena deformação superficial e capacidade de processar vários materiais sem ferramentas adicionais.
Nos últimos anos, nossa empresa desenvolveu a indústria de bibliotecas de disco óptico para atender à demanda do mercado por pequenos lotes e produtos diversos. A parte central do gabinete da biblioteca de disco óptico é o componente de ação interna, que desempenha um papel crucial no desempenho geral do mecanismo. A precisão da dimensão do processo dos produtos de chapa metálica central dentro do gabinete requer ± 0,1 mm.
Para garantir a precisão do processamento, nossa empresa utiliza a máquina de estampagem a laser de fibra óptica da Amada para corte a laser e blanking de produtos de chapa metálica, que tem uma precisão de processamento de ±0,07mm/1000mm.
No entanto, durante o processo de corte e apagamento a laser, podem ocorrer fenômenos de corte anormais, como ondulação de corte e rebarbas de corte, levando a defeitos do produto e aumento dos custos de processamento.
Através de análise abrangente e comparação de produtos defeituosos, descobriu-se que a ondulação do corte ocorre principalmente em produtos maiores, com uma taxa de defeito de cerca de 10%. Em contraste, produtos menores têm uma taxa de defeito menor, inferior a 1%. Para reduzir perdas de produção e custos de processamento, é essencial analisar e estudar o processo de corte a laser.
Status de corte e apagamento
A máquina composta é utilizada para corte e estampagem a laser de chapas metálicas, com o grampo da máquina segurando a chapa metálica e movendo-se ao longo das direções X e Y, conforme ilustrado na Fig. 1, que mostra o equipamento de processamento do produto e a área de processamento.
No entanto, durante o processamento contínuo, a tensão local da placa é liberada, enfraquecendo gradualmente sua resistência e fazendo com que a placa balance durante o movimento. Como resultado, ocorrem ondulações no corte a laser, levando a produtos mal processados. O tamanho da ondulação de corte também é afetado por vários fatores, como a direção de processamento do produto, a posição inicial de processamento e a ordem de remoção do produto, conforme mostrado na Figura 2 e na Figura 3.
Além disso, o corte de produtos de grandes dimensões resulta numa maior libertação de tensões da chapa, fazendo com que a chapa balance ainda mais durante o corte das restantes peças. Isso resulta no corte de ondulações, levando a custos de processamento mais elevados e desperdício de material.
Para minimizar tais ocorrências, é fundamental garantir a estabilidade e resistência da chapa durante o processo de corte, principalmente quando se trata de produtos de grande porte que exigem tempos de processamento mais longos.
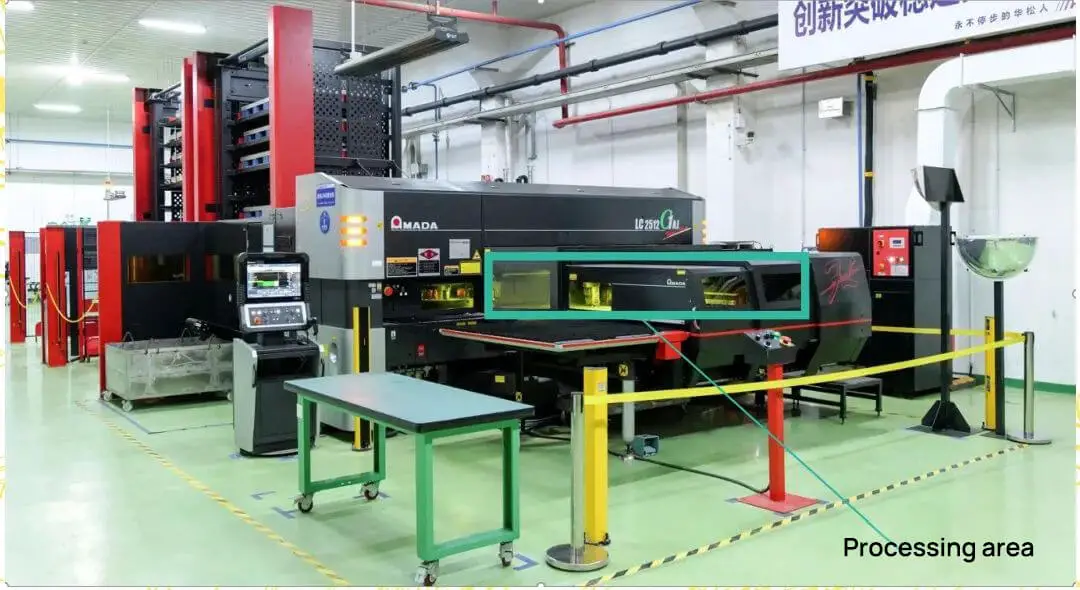
Fig. 1 equipamento de processamento e área de processamento
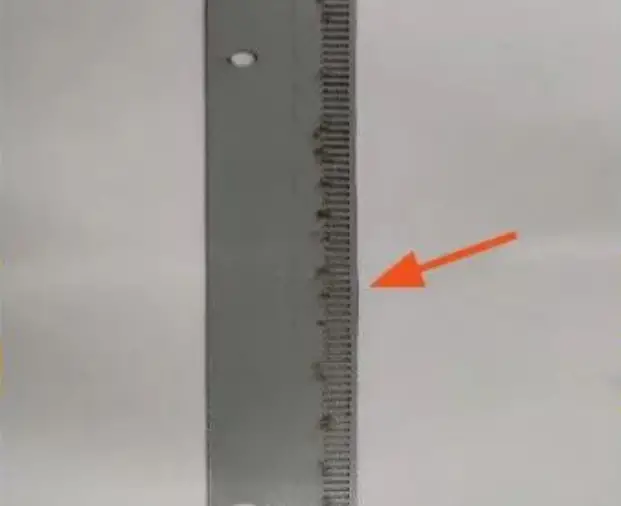
Fig. 2 estado de ondulação de corte 1
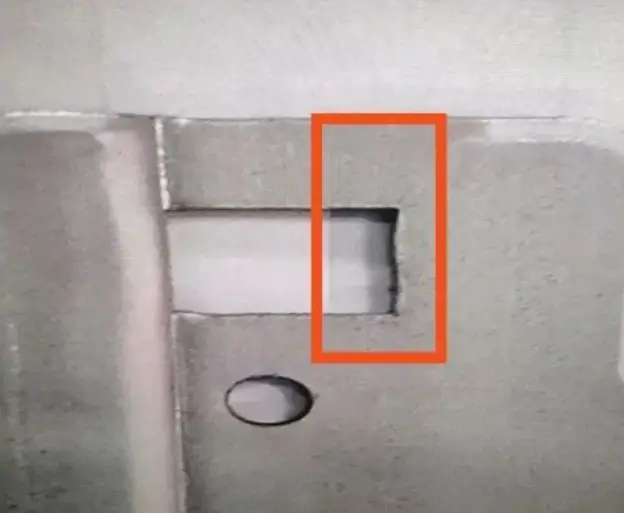
Fig. 3 estado de ondulação de corte 2
Fatores que influenciam o corte da ondulação
Posição inicial de processamento do produto
Durante o processo de corte, a posição inicial dos produtos desempenha um papel crucial na geração de ondulações de corte. Normalmente, a usinagem começa na extremidade mais distante do grampo ou na extremidade próxima ao grampo.
Se o produto for processado de uma posição distante da pinça, como mostrado na Fig. 4, a placa na extremidade da pinça pode ser finalmente cortada. Esta abordagem pode garantir que a tensão da placa não seja liberada antecipadamente, o que por sua vez garante a resistência e estabilidade da placa durante o movimento, evitando, em última análise, a ocorrência de ondulações de corte.
Por outro lado, quando o produto é processado a partir de uma posição próxima à pinça, conforme mostrado na Figura 5, a tensão da placa não é significativamente comprometida no início do processamento, portanto a ocorrência de ondulações de corte é menos provável. No entanto, o corte contínuo da placa próximo à extremidade da braçadeira irá liberar gradualmente a tensão da placa, levando a uma placa instável durante o movimento.
Quando o processamento se afasta gradualmente da braçadeira, os produtos periféricos provavelmente apresentarão ondulações de corte devido à resistência insuficiente da placa. Portanto, durante a programação, é fundamental garantir que os produtos sejam cortados a partir da extremidade mais distante da pinça e depois progressivamente em direção à extremidade da pinça. Esta abordagem garante a resistência da placa e elimina a geração de ondulações de corte.
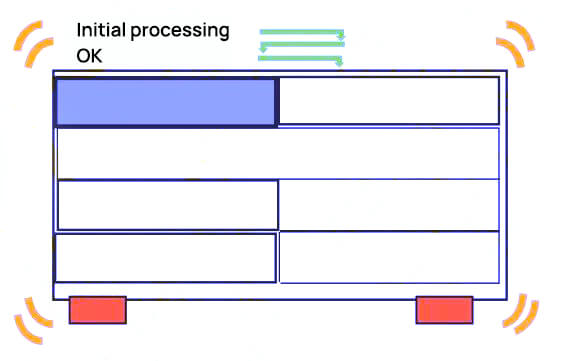
Fig. 4 boa posição inicial de processamento
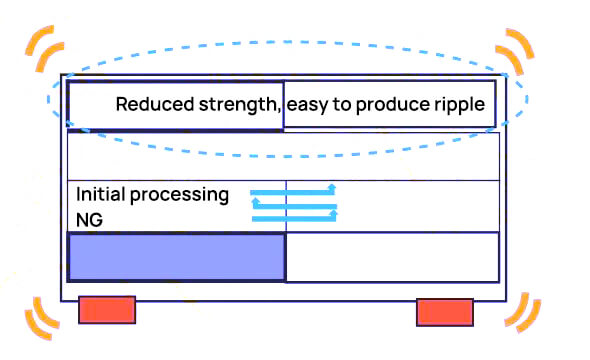
Fig. 5 A posição inicial do processamento é ruim
Posição do ponto de corte e direção de usinagem
Durante o processo de corte de chapa metálica, o ponto de entrada onde o corte é iniciado se tornará naturalmente o ponto de saída quando o corte for concluído.
A seleção de um ponto de entrada adequado pode reduzir a probabilidade de ondulações de corte.
No início do processo de corte, devido à boa resistência da chapa, o ponto de entrada e a direção do corte não têm muito impacto. No entanto, à medida que o processo de corte se aproxima do fim, o ponto de entrada e a direção do corte tornam-se cruciais para determinar se serão produzidas ondulações de corte nos produtos restantes.
Para evitar a geração de ondulações de corte, certifique-se de que os produtos próximos à extremidade do grampo tenham resistência suficiente.
Se o ponto de entrada for selecionado no meio do produto e o corte for feito no sentido horário ou anti-horário, a parte inferior do produto será cortada primeiro. Isto resulta na liberação de tensões da placa, o que reduz a resistência e estabilidade do produto. Consequentemente, podem ocorrer ondulações de corte locais, conforme mostrado na Figura 6.
Se o ponto de entrada for selecionado na extremidade inferior, o produto mais próximo da extremidade do grampo será cortado por último, o que significa que a tensão da placa não é liberada antecipadamente, tornando o processo mais estável e reduzindo a probabilidade de ocorrência de ondulações no corte, como mostrado na Figura 7.
Ao programar o processo de corte, certifique-se de que o ponto de entrada e a direção de corte sejam selecionados de forma que o produto seja finalmente cortado próximo à extremidade do grampo.
Quanto menor a distância percorrida durante o processo de corte, mais ondulações de corte podem ser evitadas até certo ponto. Obviamente, ao selecionar o ponto de entrada na parte inferior do produto, considere se a direção de corte é no sentido horário ou anti-horário.
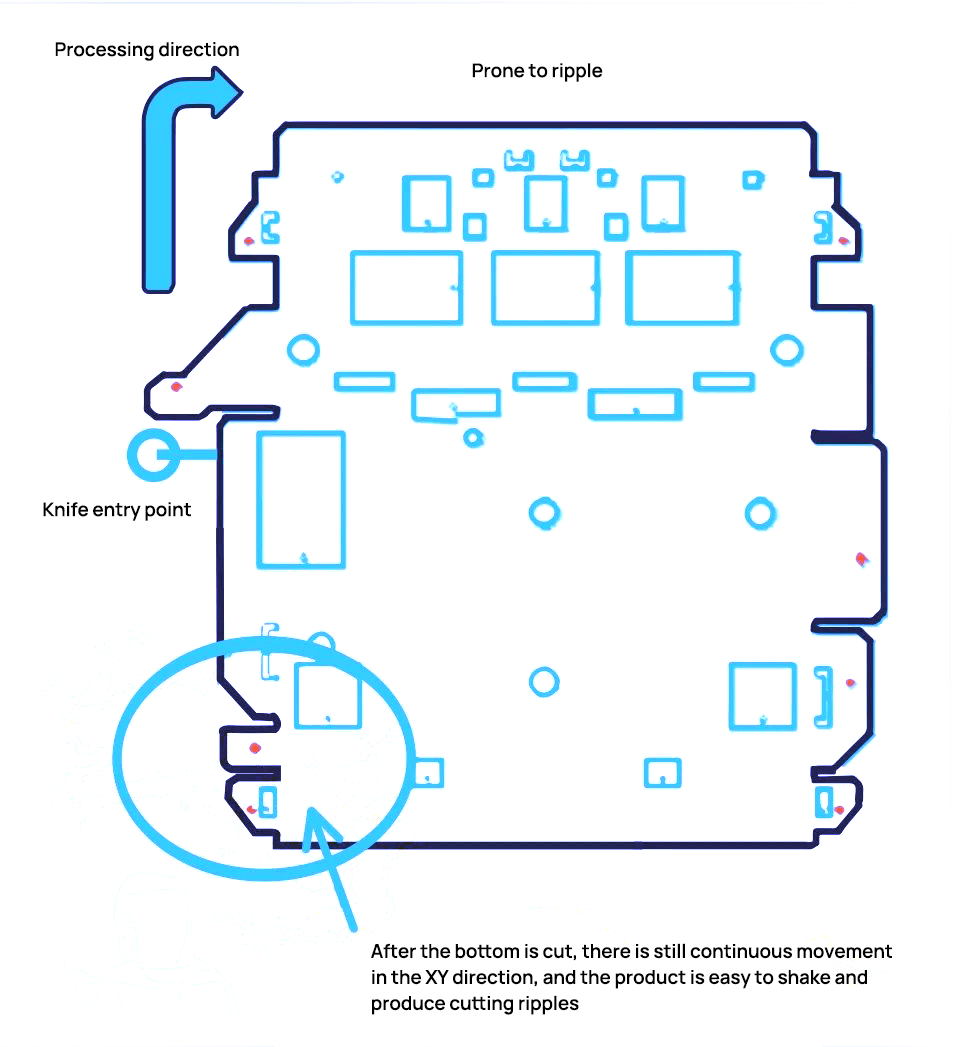
Fig. 6 A posição do ponto de corte é ruim
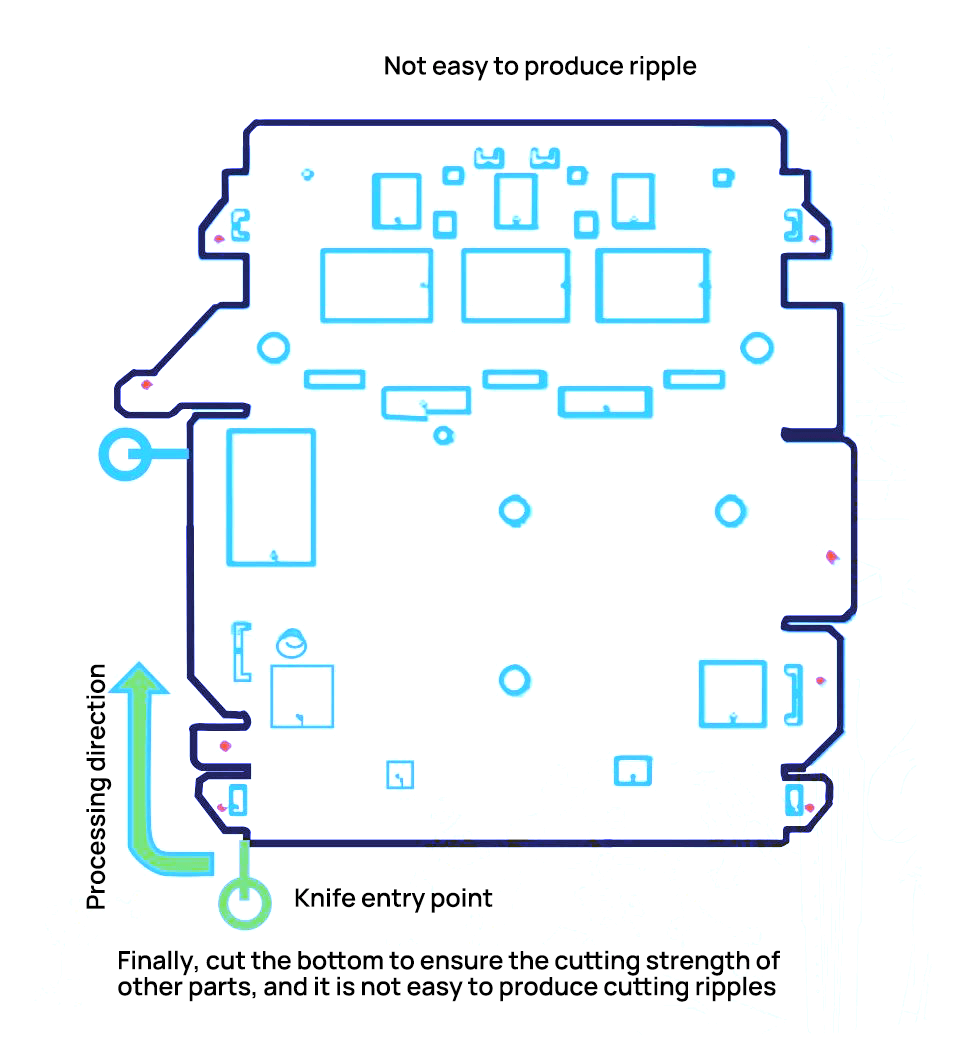
Fig. 7 a posição do ponto de corte é boa
Posição de fixação do grampo
A função dos grampos é manter a placa no lugar e permitir que ela se mova nas direções X e Y de acordo com o programa de processamento. Eles garantem a estabilidade da placa durante a operação de processamento. Portanto, é essencial distribuir uniformemente as posições dos grampos, o que evitará o tremor instável das placas causado pela deflexão dos grampos para um lado e a geração de ondulações de corte.
A Figura 8 mostra uma comparação das posições dos grampos.
Embora o posicionamento dos grampos possa impactar nas ondulações de corte, esse fator pode ser evitado durante o processo de operação.

Fig. 8 Posição de fixação do grampo
Sequência de remoção do produto
Durante o processo de produção, o manipulador TK às vezes é utilizado para auxiliar na retirada de produtos cortados, o que pode economizar recursos humanos e materiais e alcançar a produção totalmente automatizada de equipamentos. Porém, ao utilizar o manipulador TK para retirar produtos, é fundamental prestar atenção ao controle da sequência de remoção do produto para evitar enfraquecimento da resistência e agitação dos materiais que podem causar ondulações no corte.
Retirar os produtos primeiro de ambas as extremidades da placa e depois do meio pode levar à liberação de tensão em ambas as extremidades da placa, resultando em resistência insuficiente da placa. Quando o programa de processamento atinge o meio da placa, a placa pode tremer devido à resistência insuficiente, causando ondulações de corte nos produtos e resultando em altas taxas de defeitos do produto e perdas de processamento, conforme mostrado na Figura 9.
Para evitar este problema, é fundamental retirar os produtos sucessivamente pela lateral afastada da pinça. Isso garante que a concentração de tensão da placa na posição de processamento seja bem distribuída e o movimento seja estável, evitando a ocorrência de ondulações de corte, conforme mostrado na Figura 10.
Portanto, durante o processamento e a programação, é importante garantir que os produtos sejam retirados sequencialmente da extremidade afastada da pinça para manter a resistência da placa e evitar trepidações durante o movimento, evitando assim a geração de ondulações de corte.
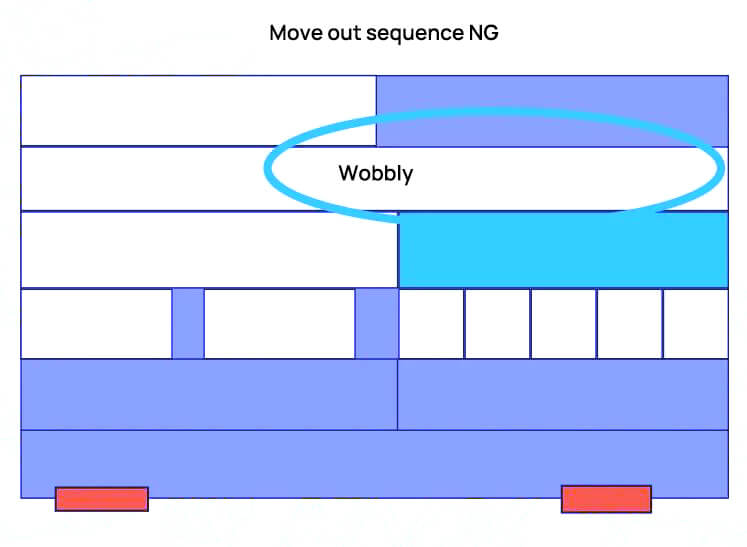
Fig. 9 má sequência de remoção do produto
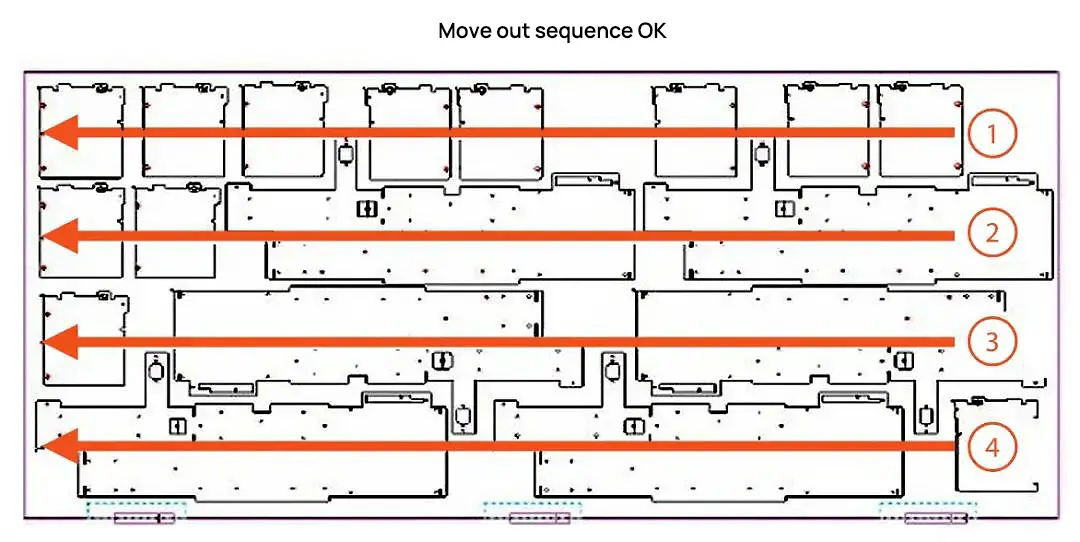
Fig. 10 boa sequência de remoção do produto
Conclusão
Os fatores que influenciam a pesquisa acima são baseados em uma análise das ondulações de corte nesta fase.
A geração de ondulações de corte não é influenciada por um único fator, mas pelos efeitos combinados de vários fatores, incluindo tamanho, peso, velocidade de processamento e outros.
Para evitar a geração de ondulações de corte, é necessária uma consideração abrangente de todos os fatores durante o processo de programação para minimizar a possibilidade de ondulações de corte.