A tecnologia de corte a laser substituiu gradualmente os métodos tradicionais de processamento de metal devido ao seu baixo custo de processamento, rápida eficiência de produção, precisão de corte precisa e excelente qualidade de processamento. Essa tecnologia é amplamente utilizada no processamento de aço carbono, aço inoxidável, cobre, alumínio e outros metais não ferrosos e é considerada insubstituível nessas áreas.
No entanto, com o uso generalizado da tecnologia de corte a laser, surgiram alguns problemas. Um dos problemas mais significativos é que ao cortar chapas de aço carbono com a mesma espessura e composições diferentes usando a mesma máquina de corte a laser e parâmetros de processo de corte, há diferenças perceptíveis na qualidade superficial dos cortes.
Para compreender o impacto da composição da chapa na qualidade do corte, foram realizados testes em chapas de aço carbono com diferentes espessuras e composições, utilizando lasers de fibra com faixas de potência de 6 a 30 kW e cortando com oxigênio e ar.
Leitura relacionada: A aplicação do ar como gás auxiliar no corte a laser
1. Equipamentos e métodos experimentais
1.1 Equipamento experimental
O experimento foi conduzido usando um laser de fibra de 30KW, que é um laser multimodo de saída contínua com comprimento de onda de feixe de 1080 nm e diâmetro de núcleo de 150 μm. A cabeça do laser usada no experimento foi a cabeça do laser Genius 30 (30KW).
A distância focal de quase diâmetro da cabeça do laser era de 100 mm, e o espelho de foco tinha uma distância focal de 200 mm, o que permitia o foco automático. Para garantir a operação estável do laser de fibra de 30KW e manter seu desempenho ideal, um refrigerador de água com capacidade de resfriamento de 70,0KW foi utilizado como equipamento auxiliar.
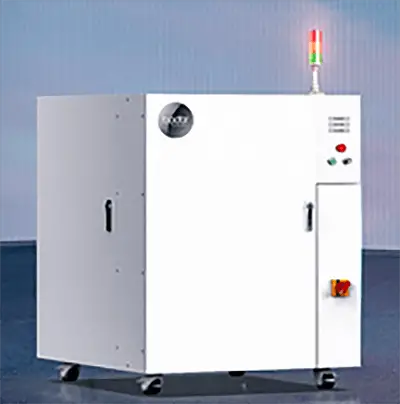
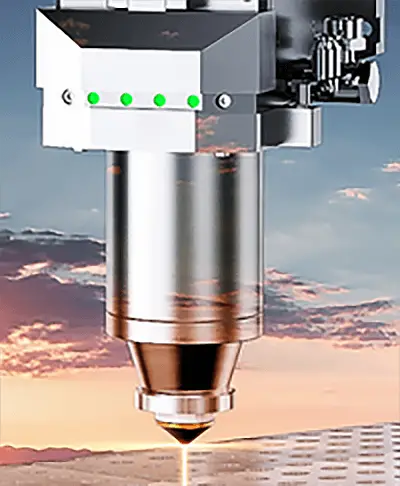
Figura 1 – Laser experimental, cabeçote de laser
1.2 Materiais auxiliares
Para garantir a precisão, eficiência e clareza dos dados experimentais, os materiais de teste utilizados neste experimento foram placas de aço carbono de diferentes espessuras, incluindo aço carbono Q235, Q345 e Q460. Para mais detalhes, consulte a folha de dados da placa experimental.
O gás auxiliar utilizado foi 99,9% de oxigênio, com pressão de alimentação de ar de 5bar. Para garantir um número suficiente de bicos, os bicos listados na ficha técnica dos bicos experimentais foram preparados para o experimento.
Tabela 1 Folha de Dados da Placa Experimental
Tipo de material | Q235 | Q345 | Q460 | Q690 | NM400 | 45# | T10 |
Tamanho/mm (C/L: 500/500) | 12 | 12 | 12 | 12 | 12 | 12 | 20 |
16 | 20 | 20 | 20 | 16 | 16 | 30 | |
20 | 30 | 30 | 30 | 20 | 20 | 40 | |
30 | / | / | / | 30 | 30 | / |
Tabela 2 Folha de Dados do Bico Experimental
Tipo de bico | Jato duplo | Jato único | ||||
Modelo de bico | B-1 | B-2 | B-3 | D-4 | D-7 | D-9 |
Quantidade | 5 | 5 | 5 | 5 | 5 | 5 |
1.3 Métodos experimentais
Sob a condição de que a qualidade do ponto do equipamento (a fibra óptica e a cabeça do laser estivessem limpas e sem danos, verificada através de um teste de papel fotográfico), pressão do ar (o oxigênio foi mantido estável em 5 bar e o ar foi mantido estável em 11 bar) , e as lentes internas da cabeça do laser (limpas, livres de sujeira e marcas de queimadura) estavam normais, os módulos internos foram controlados através do software de controle interno do laser e a potência máxima de saída foi ajustada para 12KW, 20KW e 30KW respectivamente.
Experimentos de corte foram realizados em diferentes tipos e espessuras de placas descritas na Tabela 1, sob os três estados de potência mencionados acima. O perímetro da amostra cortada foi de 205,6mm, conforme Figura 2.
As amostras cortadas foram analisadas e comparadas examinando a densidade de porosidade, rugosidade e parâmetros de processo correspondentes na superfície das amostras cortadas.
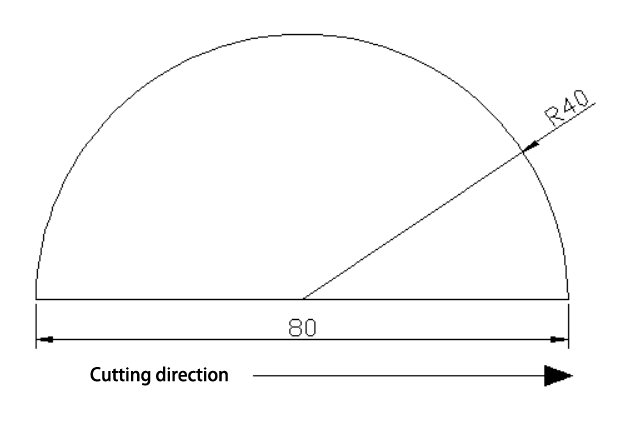
Fig. 2 – Diagrama Esquemático da Amostra de Corte
2. Resultados do teste
2.1 Análise dos parâmetros de corte
Durante o experimento, os cinco fatores que afetam a velocidade de corte (potência do laser, pressão do gás de corte, foco e abertura do bico) foram levados em consideração para garantir que as amostras após o corte se desprendessem automaticamente, sem escória, queima, gotículas e possuem um alto acabamento superficial. Os parâmetros do processo foram ajustados para obter o melhor efeito de corte para diferentes materiais e espessuras.
Leitura relacionada: Gráfico de espessura e velocidade de corte a laser
Consulte a Tabela 3 para parâmetros específicos.
Tabela 3 Tabela de Parâmetros Experimentais
Placa | Espessura/mm | Poder | Velocidade m/min | Pressão de ar/bar | Potência/KW | Foco/mm |
Q345B | 12 | 12KW | 1.7 | 0,8 | 9600 | 9,8 |
20 | 1.4 | 0,6 | 12.000 | 11.6 | ||
30 | 0,9 | 0,7 | 12.000 | 12,5 | ||
45# | 12 | 1,9 | 1.2 | 10.000 | 9,8 | |
20 | 1.6 | 1,5 | 12.000 | 9,5 | ||
30 | 1 | 0,6 | 12.000 | 12.3 | ||
NM400 | 12 | 1.6 | 1 | 9.000 | 9.6 | |
20 | 1,5 | 0,45 | 12.000 | 12 | ||
30 | 1 | 1 | 12.000 | 12 | ||
Q345B | 12 | 20KW | 1.7 | 0,8 | 9600 | 9,8 |
20 | 1.6 | 1.3 | 16.000 | 12 | ||
30 | 1.2 | 1 | 17.000 | 12,5 | ||
45# | 12 | 1,9 | 1.2 | 10.000 | 9,8 | |
20 | 1.6 | 1.3 | 14.000 | 12 | ||
30 | 1.2 | 1,5 | 16.000 | 11,5 | ||
T10 | 20 | 1 | 1.4 | 15.000 | 11 | |
30 | 0,8 | 1.6 | 18.000 | 11,5 | ||
40 | 0,7 | 1.7 | 18.000 | 11 | ||
NM400 | 12 | 1.6 | 1 | 9.000 | 9.6 | |
16 | 1,8 | 0,55 | 14.000 | 12 | ||
20 | 1,5 | 0,6 | 14.000 | 12,5 | ||
30 | 1.1 | 0,85 | 17.000 | 12,5 | ||
Q345B | 35 | 30KW | 1.3 | 1,8 | 30.000 | 12 |
40 | 0,85 | 1.2 | 24.000 | 12,5 | ||
45# | 30 | 1 | 3 | 26.000 | 13 | |
40 | 0,8 | 1.7 | 30.000 | 12,5 | ||
T10 | 35 | 0,8 | 1.6 | 18.000 | 11,5 | |
40 | 0,7 | 1.7 | 18.000 | 11 | ||
NM400 | 40 | 1.3 | 1.6 | 23.000 | 13 | |
30 | 0,8 | 1.7 | 30.000 | 12,5 |
2.1.1 Análise da velocidade de corte
Os dados da Tabela 3 mostram que, com uma potência de laser de 20KW como fundo de teste, foram comparadas as velocidades de corte de placas com espessuras de 20mm e 30mm feitas de aço Q345, 45#, NM400 e T10, conforme mostrado na Figura 3 .
Com a mesma potência do laser, espessura da placa e oxigênio do gás auxiliar, a placa T10 teve a velocidade de corte mais lenta, enquanto a NM400 teve a mais rápida. Não houve diferença significativa entre as velocidades de corte do aço Q345 e 45#.
Pode-se concluir que o teor de carbono no material de corte tem o impacto mais significativo na velocidade de corte. À medida que o teor de carbono na placa aumenta, a velocidade de corte da placa com espessura igual diminui gradualmente. Além disso, à medida que o conteúdo de elementos raros (como Cr, Ni) na placa aumenta, a velocidade de corte diminui gradualmente.

Fig. 3-Comparação de velocidade de corte de 20KW
2.1.2 Análise da pressão do ar auxiliar
O corte a laser de aço carbono com oxigênio como gás auxiliar funciona usando a energia gerada pela fonte de luz laser e a reação de oxidação durante o processo de corte.
É evidente que a pressão do oxigénio tem um efeito significativo em vários tipos de placas.
A Tabela 4 nos dados do processo de corte de 20mm e 30mm Q345, aço 45# e T10 com laser de 20KW, conforme mostrado na Tabela 3, revela que para diferentes tipos de chapas com a mesma espessura, a pressão do gás auxiliar aumenta à medida que o carbono o conteúdo nas placas aumenta, para resultados de corte ideais.
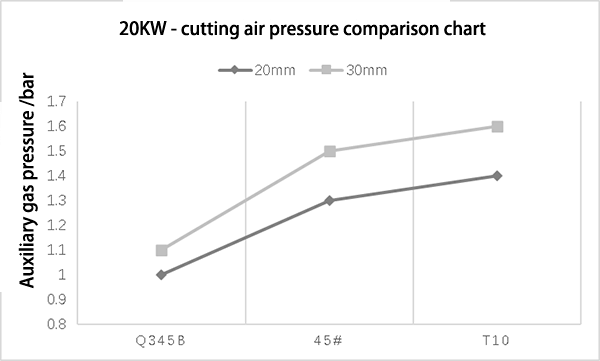
Fig. 4-Diagrama de comparação de pressão de ar auxiliar de 20KW
2.1.3 Análise de foco de corte
Os dados do teste anterior mostram que ao cortar aço Q235, Q345, aço 45# e T10 com a mesma espessura e usar oxigênio como gás auxiliar de corte, o aço 45# e o aço T10 contêm mais carbono do que Q235 e Q345.
Durante o processo de corte, um grande número de poros de dióxido de carbono se forma na superfície, causando uma superfície áspera.
O efeito de corte permanece inalterado quando o foco de corte muda dentro de ±1, portanto o foco pode ser reduzido para melhorar a velocidade de corte. Porém, o efeito de corte do Q235 e Q345 é sensível ao foco de corte, portanto eles não têm essa vantagem.
2.2 Análise do efeito de comissionamento
A tabela abaixo mostra os resultados do corte de diferentes tipos e espessuras de chapas utilizando diversos gases auxiliares e potências de corte.
Conforme mostrado na Tabela 4, fica evidente que os efeitos de corte de diferentes tipos de chapas com a mesma espessura foram comparados utilizando o mesmo poder de corte.
Os resultados indicaram uma diferença significativa na rugosidade superficial entre as amostras cortadas de diferentes materiais, com a amostra Q345B exibindo o melhor efeito de corte. A película de óxido da superfície era fina e a rugosidade da superfície era mínima.
Por outro lado, a película de óxido na superfície de corte da amostra NM400 apresentou estratificação óbvia. O lado superior da superfície de corte era liso, enquanto o lado inferior apresentava uma película de óxido mais espessa, levando a uma maior rugosidade superficial da amostra.
O corte da amostra 45# foi áspero, com uma saliência óbvia da película de óxido na parte inferior.
A amostra T10 teve o pior efeito de corte, com uma superfície áspera, numerosos poros e uma camada de óxido perceptível na parte inferior.
Em comparação, as superfícies de corte Q345B, NM400 e 45# apresentaram melhor rugosidade superficial da camada de óxido do que a placa T10.
Tabela 4 Tabela de Efeito Experimental
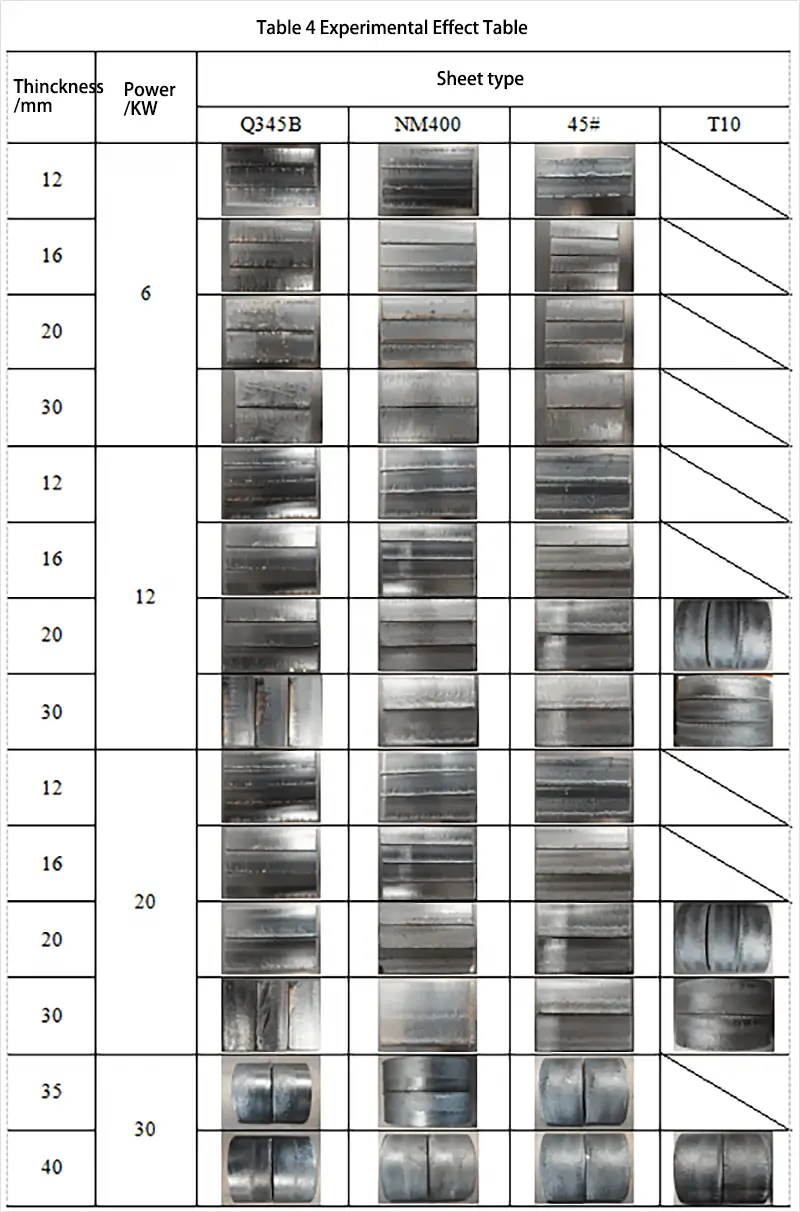
2.2.1 Análise do ponto de fusão do material
Este experimento testou quatro tipos de materiais: placas de aço carbono Q235, Q345B, NM400 e 45#. Seu teor de carbono é de 0,22%, 0,20%, 0,25% e 0,47%, respectivamente.
Ao examinar o diagrama de fases do ferro-carbono na Figura 5, pode-se observar que a temperatura do ponto de fusão destes quatro materiais é de aproximadamente 1500°C.
O corte a laser de aço carbono utiliza o laser como fonte de calor de pré-aquecimento e oxigênio como gás auxiliar. Isto cria uma reação de oxidação altamente exotérmica com os materiais, liberando uma quantidade significativa de energia de oxidação (conforme mostrado na fórmula a seguir).
Fe+O→FeO+calor(257,58kJ/mol)2Fe+1,5O2→Fé2Ó3+calor(826,72kJ/mol)
Foi estabelecido que a temperatura no local de processamento da placa excedeu 1726,85°C devido à energia liberada do laser e ao processo de oxidação durante o processamento a laser. Esta temperatura é significativamente superior aos pontos de fusão dos materiais Q235, Q345B, NM400 e 45#.
Com base nesta análise, pode-se concluir que os pontos de fusão destes materiais têm impacto limitado no efeito da incrustação de óxido na superfície após o corte.
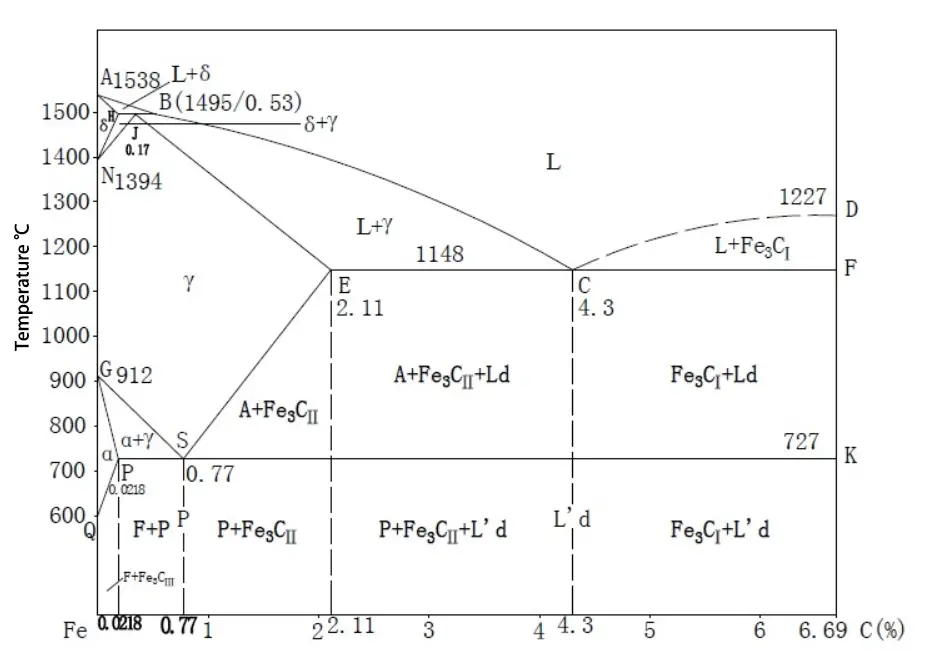
Fig. 5-Diagrama de fases Fe-C
2.2.2 Análise da composição química dos materiais
A composição química das diferentes placas de aço utilizadas neste experimento foi determinada utilizando um analisador de espectro. Os resultados são mostrados na Tabela 5.
Tabela 5 Análise de Elementos Químicos
Elemento químico/%/tipo de placa | Q345 | Q235 | Q460 | NM400 | Q690 | 45# | T10 |
C | 0,2 | 0,22 | 0,2 | 25 | 0,18 | 47 | 1 |
Mn | 1.7 | 0,65 | 1,8 | 1.6 | 2 | 0,65 | 0,4 |
Si | 0,5 | 30 | 0,6 | 0,7 | 0,6 | 27 | 0,35 |
S | 0,035 | 0,05 | 0,03 | 0,01 | 0,02 | / | 0,02 |
P | 0,035 | 0,045 | 0,03 | 0,025 | 0,025 | / | 0,03 |
Cr | 30 | 0,3 | 0,3 | 14 | 1 | 0,25 | 0,25 |
Não | 0,5 | 0,3 | 0,8 | 1 | 0,8 | 0,3 | 0,2 |
Cu | / | 0,3 | / | / | 25 | 0,3 | |
Mo | 0,1 | / | / | 0,5 | 0,3 | / | / |
N.º | 0,07 | / | 0,11 | / | 0,11 | / | / |
V | 0,15 | / | 0,2 | / | 0,12 | / | / |
Ti | 200 | / | 0,2 | / | / | / | / |
IA | 0,015 | / | / | / | / | / | / |
B | / | / | / | 0,004 | 0,004 | / | / |
1) Análise de conteúdo do elemento Mn
De acordo com a Tabela 5, que compara os elementos Q235 e Q345B, ambos os materiais são classificados como aço de baixo carbono. O teor de outros elementos nos materiais não difere significativamente, exceto o teor de manganês, que é de 0,65% para Q235 e 1,70% para Q345B. Essa diferença no teor de manganês serve como referência para explorar a relação entre a qualidade do corte a laser e o teor de manganês no material.
Os efeitos de superfície de corte dos dois materiais são mostrados na Figura 6. Os resultados mostram que a superfície é limpa e brilhante, com rugosidade superficial semelhante, e os parâmetros experimentais foram mantidos constantes.
Com base nessas descobertas, pode-se concluir que o elemento Mn tem um leve impacto no efeito de corte a laser do aço convencional de baixo carbono.
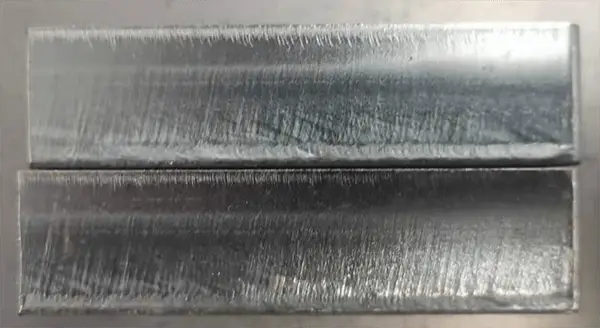
Q235-20kw-20mm
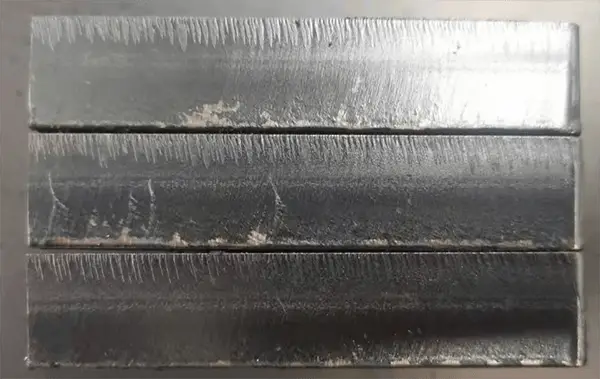
Q345B-20kw-20mm
Figura 6
2) Análise de conteúdo do elemento S
Os dados fornecidos na tabela mostram que a diferença máxima no teor do elemento enxofre (S) entre as folhas é de apenas 0,05%. Esta informação não é suficiente para determinar o impacto do conteúdo do elemento S na qualidade do corte.
Uma análise mais aprofundada dos dados revela que quando o teor de manganês (Mn) e enxofre (S) na placa está em torno de 0,5% e 0,25% respectivamente, a escória na parte inferior da superfície de corte aumenta com o aumento da espessura da placa, levando a uma diminuição gradual na qualidade do corte.
Tabela 6 Comparação dos Elementos S e Mn
Folha/Elemento% | Q345 | Q235 | Q460 | NM400 | Q690 | 45# | T10 |
Mn | 1.7 | 0,65 | 1,8 | 1.6 | 2,0 | 0,65 | 0,4 |
S | 0,035 | 0,05 | 0,03 | 0,01 | 0,02 | 0,02 |
3) Análise de conteúdo do elemento Si
Foi observado que quando o teor do elemento silício (Si) na placa metálica está abaixo de 0,25%, a velocidade de corte da placa de aço carbono com teor de Si superior a 0,25% é mais lenta em mais de 20% em comparação com a do aço carbono. placa com teor de Si inferior a 0,25%. Além disso, uma quantidade substancial de escória será produzida no fundo da placa.
4) Análise de conteúdo do elemento C
Ao comparar o conteúdo do elemento Q235, 45# e T10, verifica-se que Q235 é classificado como aço de baixo carbono, 45# é aço de médio carbono e T10 é aço de alto carbono.
Examinando a tabela de elementos, percebe-se que as únicas diferenças significativas estão entre carbono (C) e manganês (Mn).
Sob alta temperatura e com oxigênio suficiente como gás auxiliar, o carbono reage com o oxigênio da seguinte maneira:
C+O2→CO2(g)(393,5KJ/mol)
A análise teórica mostra que à medida que o teor de carbono do material aumenta, a quantidade de gás dióxido de carbono produzido pela reação de oxidação também aumentará na presença de oxigênio como gás auxiliar, levando a um aumento no número de poros no corte do material. superfície.
A Figura 4 ilustra que à medida que o teor interno de carbono do aço Q235, 45# e T10 aumenta, o número de poros na superfície de corte também aumenta correspondentemente.
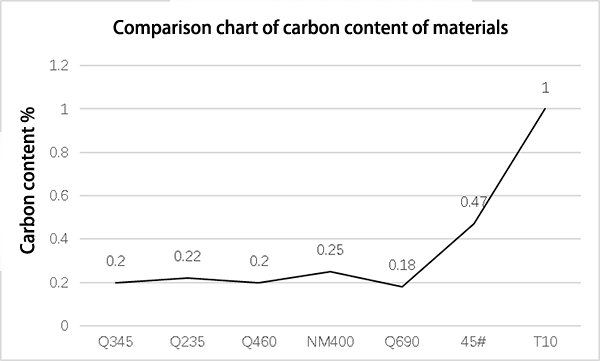
Fig. 7 – Gráfico Comparativo do Teor de Carbono dos Materiais
Ao comparar inicialmente os materiais Q235 e Q345B, descobriu-se que o conteúdo do elemento manganês (Mn) tem um impacto mínimo no efeito de corte real e pode ser desconsiderado.
A Figura 8 mostra o efeito de corte real dos três materiais com a mesma espessura. Os resultados mostram que a superfície do Q235 é brilhante com baixa rugosidade, a superfície do 45# é áspera com uma película de óxido significativamente mais espessa na parte inferior e a superfície do T10 é a mais áspera com a película de óxido mais espessa.
A partir dos resultados reais dos testes, pode-se concluir que o teor de carbono no material tem um impacto notável no efeito de corte. À medida que o teor de carbono aumenta, o número de poros na superfície de corte aumenta, a espessura da película de óxido superficial torna-se mais espessa e a rugosidade da superfície aumenta.

Fig. 8-Q235-30kw-40mm (esquerda), 45 # – 30kw-40mm (meio), T10-30kw (direita)
5) Análise de conteúdo do elemento Ni
A Tabela 7 exibe os tipos e conteúdos de elementos químicos nos materiais Q235 e Q460. A diferença no conteúdo do elemento níquel (Ni) entre os dois materiais é evidente.
Consequentemente, foram realizados testes de corte em placas de mesma espessura para ambos os materiais. Os resultados da qualidade de corte real são mostrados na Figura 10.
Não há diferença perceptível nas estrias superficiais, na espessura da película de óxido e na rugosidade da superfície.
Com base nestes resultados, pode-se concluir que no aço convencional de baixo carbono, o teor de níquel não tem impacto significativo na qualidade de corte dos lasers de alta potência.
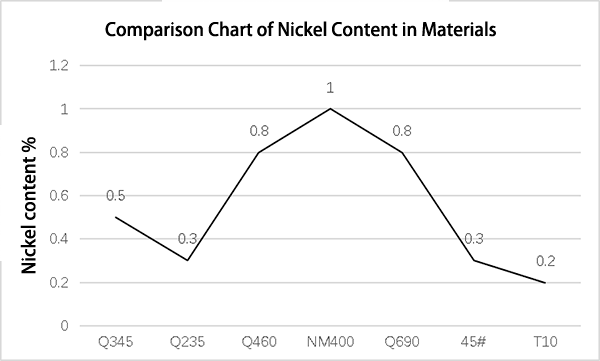
Fig. 9 – Gráfico Comparativo do Teor de Níquel em Materiais
Tabela 7 Comparação de Elementos Ni
Elemento químico/% | Tipo de placa | Q235 | Q460 |
C | 0,22 | 0,2 | |
Mn | 0,65 | 1,8 | |
Si | 0,3 | 0,6 | |
S | 0,05 | 0,03 | |
P | 0,045 | 0,03 | |
Cr | 0,3 | 0,3 | |
Não | 0,3 | 0,8 | |
Cu | 0,3 | / | |
Mo | / | / | |
N.º | / | 0,11 | |
V | / | 0,2 | |
Ti | / | 0,2 | |
IA | / | / | |
B | / | / |

Q460-20mm-20KW
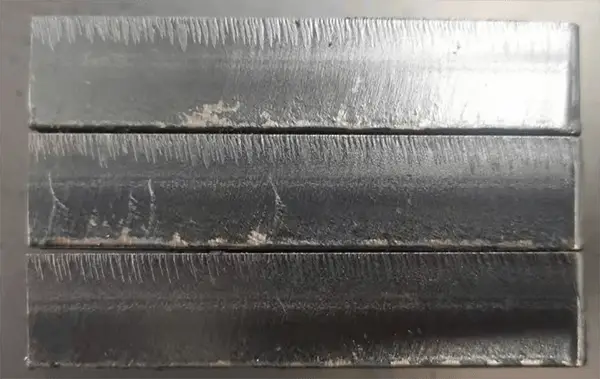
Q235-20mm-20KW
Figura 10
6) Análise de conteúdo do elemento Cr
Ao comparar o teor de elementos na placa, observa-se que o teor do elemento cromo (Cr) nos materiais NM400 e Q690 é significativamente maior que nos demais materiais, conforme ilustrado na Figura 4.2-5.
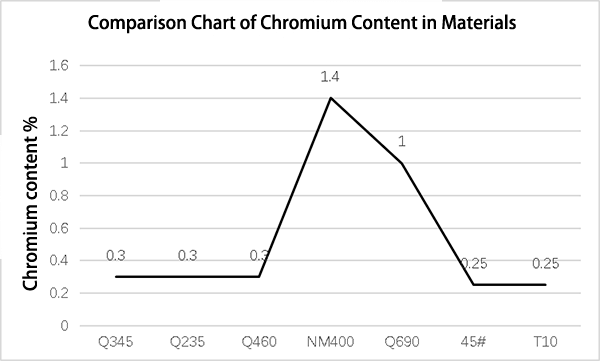
Fig. 11 Gráfico de comparação do conteúdo de cromo em materiais
Durante o processo de corte a laser, a maioria dos elementos da placa oxidará com o gás auxiliar, oxigênio, e liberará uma grande quantidade de calor quando o laser liberar calor. Isto resulta na formação de uma zona significativa afetada pelo calor na superfície da placa.
Nesta zona afetada pelo calor, o cromo (Cr) na placa irá oxidar com oxigênio e produzir Cr denso2Ó3 e outros óxidos, que aumentarão com a temperatura local. O óxido cresce gradualmente e forma uma estrutura granular semelhante a um aglomerado, conforme mostrado na Figura 12.
Com o tempo, um Cr2Ó3 película de óxido com alta tensão superficial e menos propensa a fissuras na superfície de corte do metal, o que evita a reação de oxidação entre os elementos abaixo do Cr2Ó3 oxidação e O2 (conforme mostrado na Figura 13). Isso resulta em rugosidade superficial significativamente baixa na parte inferior das superfícies de corte NM400 e Q690 (como visto na Figura 14).
Pode-se concluir que o efeito de corte piora com o aumento do teor de Cr no material e a película de óxido no fundo da amostra torna-se mais espessa.


Figura 12 – Diagrama de fases de partículas agrupadas
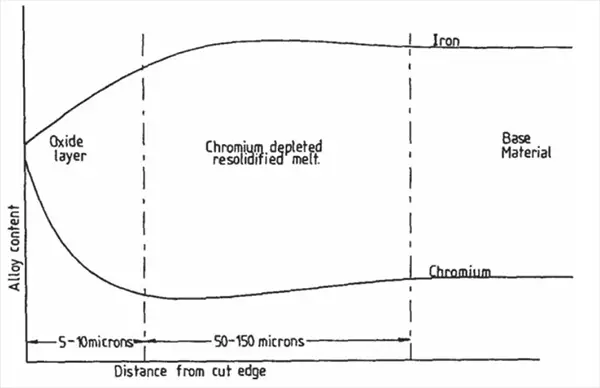
Fig. 13 – Diagrama de Análise da Camada de Óxido Superficial de Corte a Laser
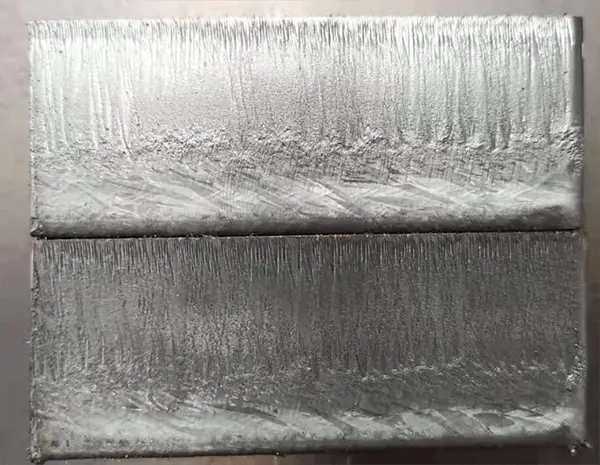
Exibição de efeito de corte 20mm NM400
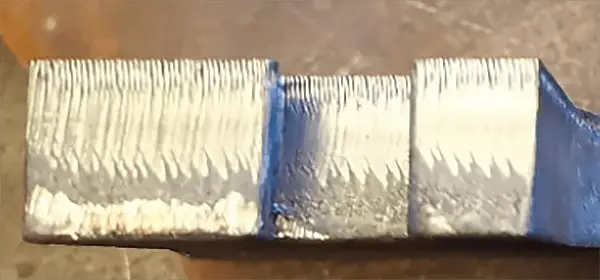
Exibição de efeito de corte 20mm Q690
Figura 14
2.3 Análise da zona afetada pelo calor
Entende-se que a qualidade do corte a laser está relacionada à zona afetada pelo calor na superfície da chapa a ser cortada. Quando a zona afetada pelo calor não é controlada, pode causar distorções, rachaduras, fragilidade, etc. na superfície da placa cortada.
De acordo com a comparação dos dados da Figura 15, sabe-se que a potência de corte a laser é o principal fator que afeta a largura da fenda de corte, e a velocidade de corte é o principal fator que afeta as estrias e a rugosidade da superfície de corte.
Portanto, no corte a laser, recomenda-se ajustar ao máximo os parâmetros do processo para minimizar a área da zona afetada pelo calor na superfície da placa, a fim de reduzir a deformação e o enriquecimento dos componentes.


Fig. 15 – Influência da potência e velocidade no corte e na superfície de corte
Durante o processo de teste real, os parâmetros do processo de corte foram otimizados para garantir superfícies de corte lisas e queda livre de amostras de diferentes tipos e espessuras.
Sob o mesmo poder de corte, não há diferença substancial na largura das fendas entre os diferentes tipos e com a mesma espessura.
Como resultado, a área da zona afetada pelo calor de materiais com a mesma espessura é semelhante sob a mesma potência, tendo apenas um impacto menor na rugosidade superficial real e pode ser desconsiderada.
3. Conclusão
Os fatores que influenciam a qualidade do corte do aço carbono por meio do corte com oxigênio incluem a composição das ligas, microestrutura do material, condutividade térmica, ponto de fusão e ponto de ebulição.
Metais com alto teor de carbono normalmente apresentam pontos de fusão elevados, tornando-os difíceis de derreter, levando a um aumento no tempo de corte e perfuração.
Isso resulta em um corte mais amplo e em uma zona afetada pelo calor na superfície expandida, causando qualidade de corte instável.
Leitura relacionada: Coisas que você deve saber sobre corte a laser
Além disso, um alto teor de composição de liga aumenta a viscosidade do metal líquido e aumenta a proporção de respingos e escória, impondo maiores demandas no ajuste da potência do laser e da pressão de sopro de ar durante o processamento.
Leitura relacionada: Como selecionar a potência da máquina de corte a laser de fibra?
Os testes acima mostram que quando o oxigênio é usado como gás auxiliar, o efeito da superfície de corte piora e a rugosidade da superfície aumenta significativamente à medida que o conteúdo dos elementos C e Cr no material aumenta. Por outro lado, quando o ar é utilizado como gás auxiliar, o efeito de corte permanece praticamente inalterado sob a mesma espessura e potência.
Para garantir a qualidade e eficiência do corte, os tipos de gás auxiliar recomendados para diferentes potências e materiais de corte estão listados na tabela a seguir:
- Impacto do teor de carbono:
Sob a mesma potência do laser, à medida que o teor de carbono aumenta, a velocidade de corte diminui gradualmente, enquanto a superfície da amostra se torna mais áspera, a película de óxido torna-se mais espessa e o efeito geral se deteriora, levando a uma redução no limite de espessura do corte a laser pratos.
- Impacto do conteúdo de cromo:
Com o aumento do teor de cromo, a película de óxido na parte inferior da superfície da amostra se acumula e engrossa visivelmente, fazendo com que a superfície de corte se torne áspera de cima para baixo.
- Impacto do conteúdo de silício:
Quando o teor de silício no material excede 0,25%, a velocidade de corte diminui significativamente com o aumento do teor de silício e a escória aparece na parte inferior da amostra de corte.
- Conteúdo de níquel:
O teor de níquel tem pouco efeito na qualidade do corte a laser de alta potência.
- Impacto do teor de manganês e enxofre:
Quando o teor de manganês e enxofre no material é de 0,5% e 0,04% respectivamente, a escória na parte inferior do corte aumenta gradativamente à medida que a espessura da placa aumenta.