1. Introdução
De acordo com o princípio do arredondamento de três pontos, a calandra de chapa utiliza o movimento rotativo e a mudança de posição relativa do rolo de trabalho para obter dobra elástica-plástica contínua. Isso resulta em chapas metálicas dobradas em formatos predeterminados, como cilindros e arcos, bem como peças de trabalho de precisão.
A máquina dobradeira de placas é amplamente utilizada em vários setores, incluindo fabricação de caldeiras, construção naval, petroquímica, estrutura metálica e máquinas formadoras de chapas metálicas.
Com base no número de rolos, a calandra de chapas pode ser classificada em tipos de dois rolos, três rolos e quatro rolos, cada um com suas características únicas.
Em comparação com o tipo tradicional de dois rolos, a calandra de chapa de quatro rolos tem diversas vantagens, incluindo centralização mais fácil, uma borda reta residual menor, maior precisão no endireitamento circular e maior eficiência de produção.
Além disso, a calandra de chapa de quatro rolos é capaz de realizar pré-plexação final de chapa e laminação de peças sem a necessidade de torneamento, tornando-a cada vez mais importante na conformação de chapas metálicas.
A máquina é composta por um rolo superior, um rolo inferior e dois rolos laterais na frente e atrás. O rolo superior gira em uma posição fixa enquanto a placa de aço é alimentada por fricção. O processo de fixação, pré-plexação e laminação da placa de aço é controlado ajustando a posição do rolo inferior e dos dois rolos laterais.
Para aumentar a precisão de laminação da chapa de aço, é crucial estudar as posições precisas do rolo inferior e dos dois rolos laterais. Atualmente, o controle de posição desses componentes é determinado pelo operador por meio de ajustes repetidos com base na experiência, e a precisão da laminação é monitorada por meio de comparação contínua e verificação de modelo, resultando em baixa precisão e eficiência.
Este artigo propõe uma fórmula de cálculo para o raio de curvatura de retorno elástico com base na teoria da recuperação elástica e estuda os requisitos de posição do rolo inferior e dos dois rolos laterais no processo de laminação de chapas de aço. É estabelecido um modelo matemático para calcular as posições desses componentes durante o alinhamento, pré-plexação e flexão.
O estudo determina com precisão o deslocamento do rolo inferior e dos rolos laterais dianteiro e traseiro durante a laminação da chapa de aço, fornecendo dados precisos de alimentação para controle digital. Os resultados deste método, verificados através da prática de produção, mostram consistência com aplicações práticas, levando a uma melhor precisão e eficiência de laminação.
1. Fluxo de processo da máquina dobradeira de placa de quatro rolos
1.1 Estrutura e princípio de funcionamento da máquina dobradeira de placa de quatro rolos
A máquina dobradeira de chapa de quatro rolos é composta de vários componentes principais, incluindo o dispositivo de rolo superior, dispositivo de rolo inferior, dispositivo de rolo lateral, dispositivo de tombamento, rack baixo, base, rack alto e estação de bomba hidráulica.
O rolo superior serve como rolo motriz e é girado por um servo motor através de um dispositivo de transmissão, com posição fixa. O rolo inferior e o rolo lateral são rolos acionados, cuja rotação é acionada pelo atrito com a chapa de aço.
O rolo inferior é fixado em seu assento de rolamento, que pode se mover verticalmente em uma ranhura guia deslizante na estrutura para acomodar diferentes espessuras de placa. Os rolos laterais são instalados em assentos de rolamentos de rolos laterais.
Para formar o raio de curvatura desejado do cilindro, o assento do rolamento do rolo lateral move-se para cima e para baixo em uma direção inclinada dentro da ranhura guia deslizante, com um determinado ângulo em relação à direção vertical.
O tombamento e o reset do rolo inferior, do rolo lateral e do rolo superior são controlados por um cilindro hidráulico. A estrutura geral do equipamento está representada na Figura 1.
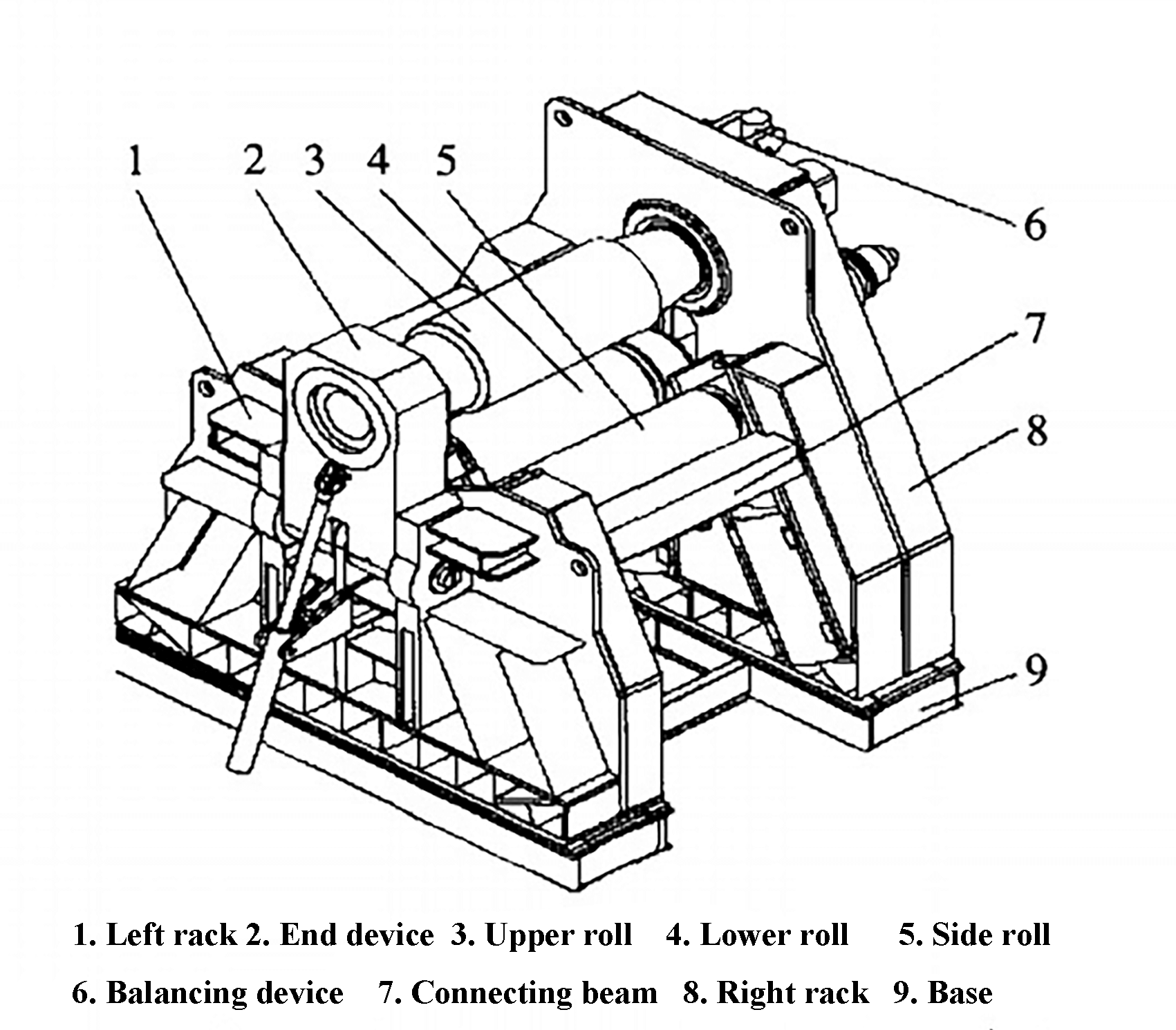
Fig. 1 Estrutura da dobradeira de chapa de quatro rolos
1.2 Fluxo de processo da dobradeira de chapa de quatro rolos
O processo de laminação de chapas de aço normalmente consiste em seis etapas, incluindo preparação, alimentação, pré-dobragem, pré-dobragem do outro lado, laminação e correção do arco. Este processo está representado na Figura 2.
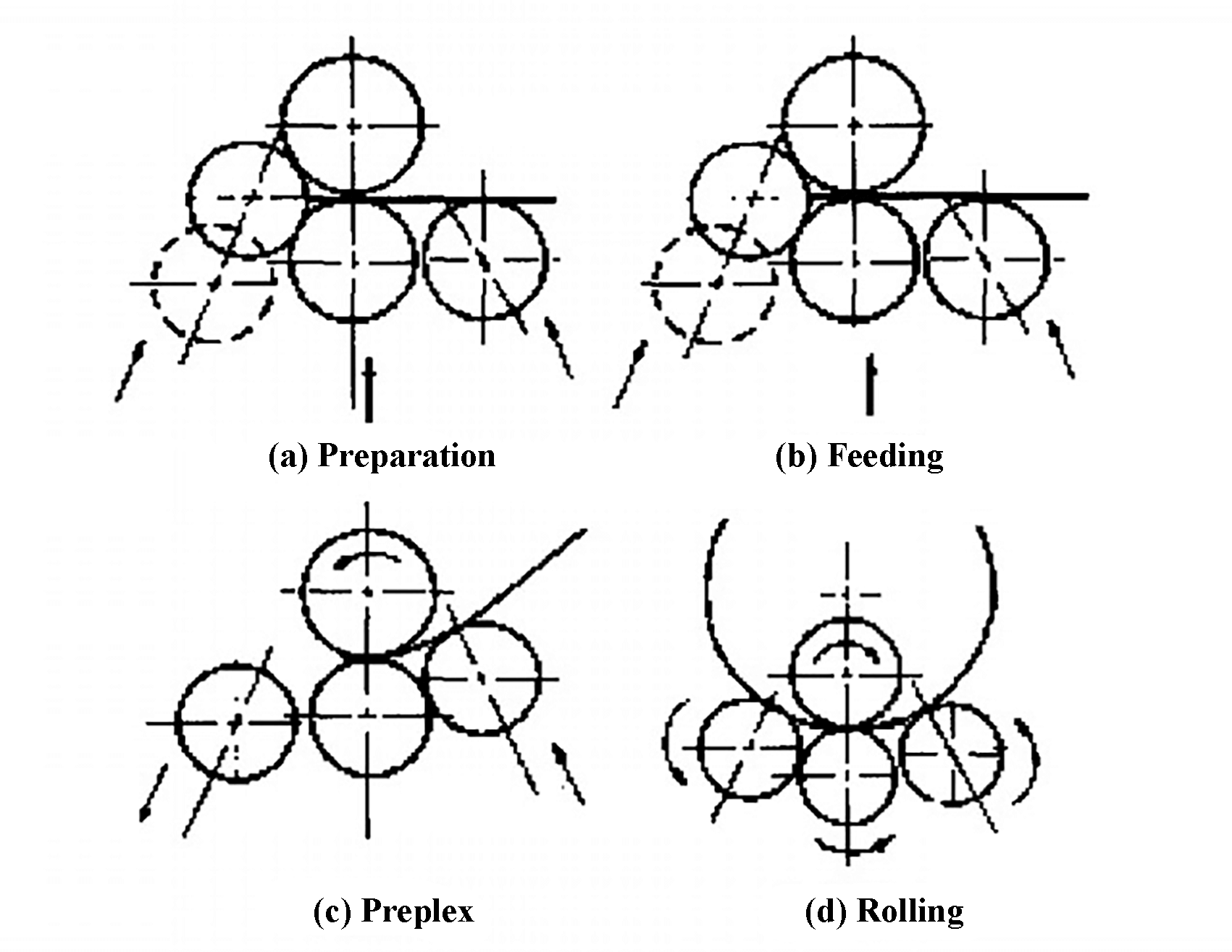
Fig. 2 Processo tecnológico da dobradeira de chapa de quatro rolos
1.2.1 Preparação e alimentação
O rolo inferior é elevado para uma posição onde a distância entre a linha geradora superior e a linha geradora inferior do rolo superior é ligeiramente maior que a espessura da peça de trabalho.
O rolo lateral traseiro é levantado para uma posição onde a geratriz superior e a geratriz superior do rolo inferior estão no mesmo plano horizontal, e então o rolo lateral frontal é levantado para uma posição onde sua linha central está localizada entre o rolo superior e inferior rolos (como mostrado na Figura 2a).
A peça de trabalho é alimentada horizontalmente entre os rolos superior e inferior, com a extremidade frontal pressionada contra o rolo frontal. O rolo inferior é então elevado para fixar a placa de aço (conforme mostrado na Figura 2b).
Concluídas essas etapas, o processo de preparo e alimentação está finalizado.
1.2.2 Pré-flexão
O rolo lateral frontal é retornado à sua posição original e o rolo lateral traseiro é elevado até a altura do processo para a curvatura de pré-dobramento da placa de aço (como mostrado na Figura 2c).
O rolo superior gira no sentido anti-horário para impulsionar a placa de aço para frente. Quando a extremidade da chapa de aço atingir metade da distância entre os dois rolos, deve-se medir para garantir que atinge a curvatura necessária.
O processo para pré-dobrar a outra extremidade é semelhante ao descrito acima.
1.2.3 Dobragem de rolo
O rolo lateral frontal é elevado até a altura do processo para a curvatura necessária, enquanto o rolo lateral traseiro é abaixado para que os rolos laterais dianteiro e traseiro fiquem no mesmo nível.
O rolo superior gira no sentido anti-horário para impulsionar o movimento da placa de aço para frente, fazendo com que ela enrole. Ao mesmo tempo, a curvatura da placa de aço saliente é medida usando um modelo, e a altura do processo é ajustada conforme necessário para atingir o radiano desejado (como mostrado na Figura 2d).
O processo de correção do arco é semelhante ao processo de dobra do rolo.
3. Cálculo do raio de retorno elástico durante flexão de chapa de aço
Atualmente, a maior parte das bobinas é produzida por laminação a frio. O fenômeno de retorno elástico é bastante pronunciado neste processo, portanto, é necessária uma quantidade adequada de sobreenrolamento para compensá-lo.
Normalmente, o raio de retorno elástico deve ser menor que o raio desejado das peças (raio de pré-flexão).
Com base na mecânica elástico-plástica, o retorno elástico no processamento de chapas metálicas é influenciado por fatores como módulo de elasticidade, módulo de elasticidade reforçado, limite de escoamento, raio de pré-enrolamento e espessura da chapa.
Através de derivação teórica, a fórmula de cálculo do raio de curvatura antes da recuperação pode ser determinada da seguinte forma:
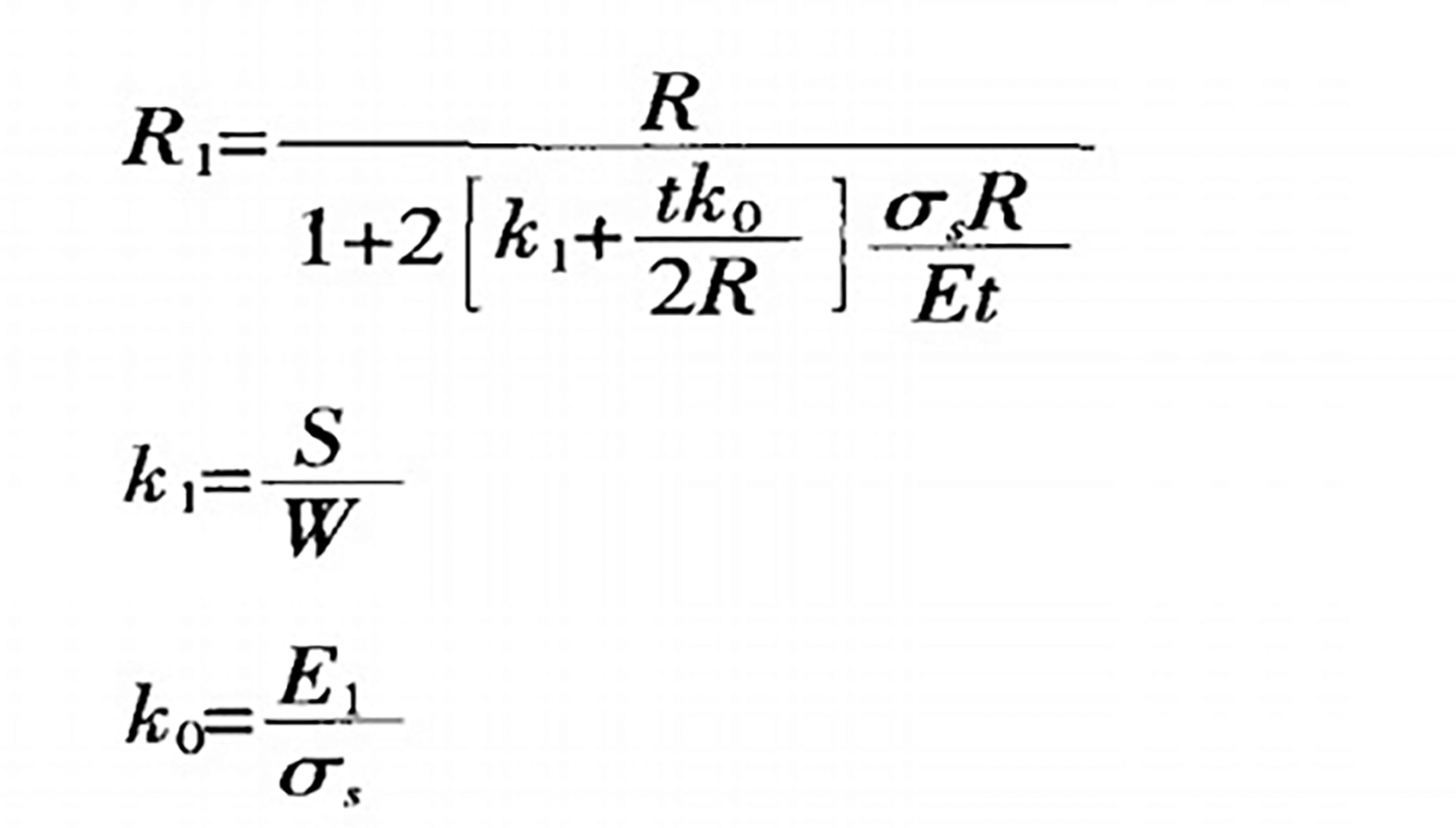
Na fórmula:
- R – Raio de pré-enrolamento, mm;
- E – Módulo elástico do material, MPa;
- t – Espessura da chapa de aço, mm;
- σé – Limite de rendimento da placa, MPa;
- S – Momento estático da seção, mm;
- W – Módulo de seção de flexão, mm;
- E1 – Módulo de elasticidade reforçado do material da chapa de aço, MPa;
- k0 – Coeficiente de reforço relativo do material;
- k1 – Coeficiente de seção, 1,5 é considerado para a seção retangular.
4. Cálculo do deslocamento de trabalho do rolo lateral
A análise do processo de laminação de chapas de aço revela que a posição do rolo superior permanece inalterada durante a laminação e que a laminação é realizada principalmente através do movimento vertical do rolo inferior e da alimentação angular dos dois rolos laterais.
Portanto, a laminação precisa da placa de aço pode ser alcançada controlando com precisão a posição de cada rolo durante o processo.
A seguir, concentra-se na modelagem matemática e no cálculo das posições do processo do rolo inferior e dos rolos laterais durante os principais processos, como movimento para frente, pré-dobragem e enrolamento.
O cálculo leva em consideração fatores como os parâmetros geométricos da laminadora, o material e a espessura da chapa de aço laminada e o raio de laminação.
Os símbolos a seguir são normalmente usados para derivar a fórmula de deslocamento para o rolo traseiro e ambos os lados da calandra de chapas:
- R é o raio de curvatura antes do retorno elástico (ou seja, o raio a ser enrolado), mm;
- A é o centro da dobradeira, que está localizado na intersecção dos ângulos de inclinação dos rolos em ambos os lados;
- α é o ângulo de inclinação dos rolos em ambos os lados, °;
- eu1 é a distância do ponto a ao centro do rolo superior, mm;
- eu2 é a distância do ponto a ao centro do rolo inferior, mm;
- eu3 é a distância do ponto a ao centro do rolo lateral, mm;
- D1 é o diâmetro do rolo superior, mm;
- D2 é o diâmetro do rolo inferior, mm;
- D3 é o diâmetro do rolo lateral, mm;
- S1 é o deslocamento inferior do rolo, mm;
- S2 é o deslocamento do rolo lateral traseiro, mm;
- S3 é o deslocamento do rolo lateral frontal, mm.
4.1. Cálculo do deslocamento do rolo lateral e do rolo inferior da dobradeira de chapas
Durante o processo de alinhamento da calandra de chapas, conforme ilustrado na Figura 2, o rolo inferior e ambos os rolos laterais sofrem deslocamento correspondente. A posição do processo de cada rolo durante o alinhamento é mostrada na Figura 3.
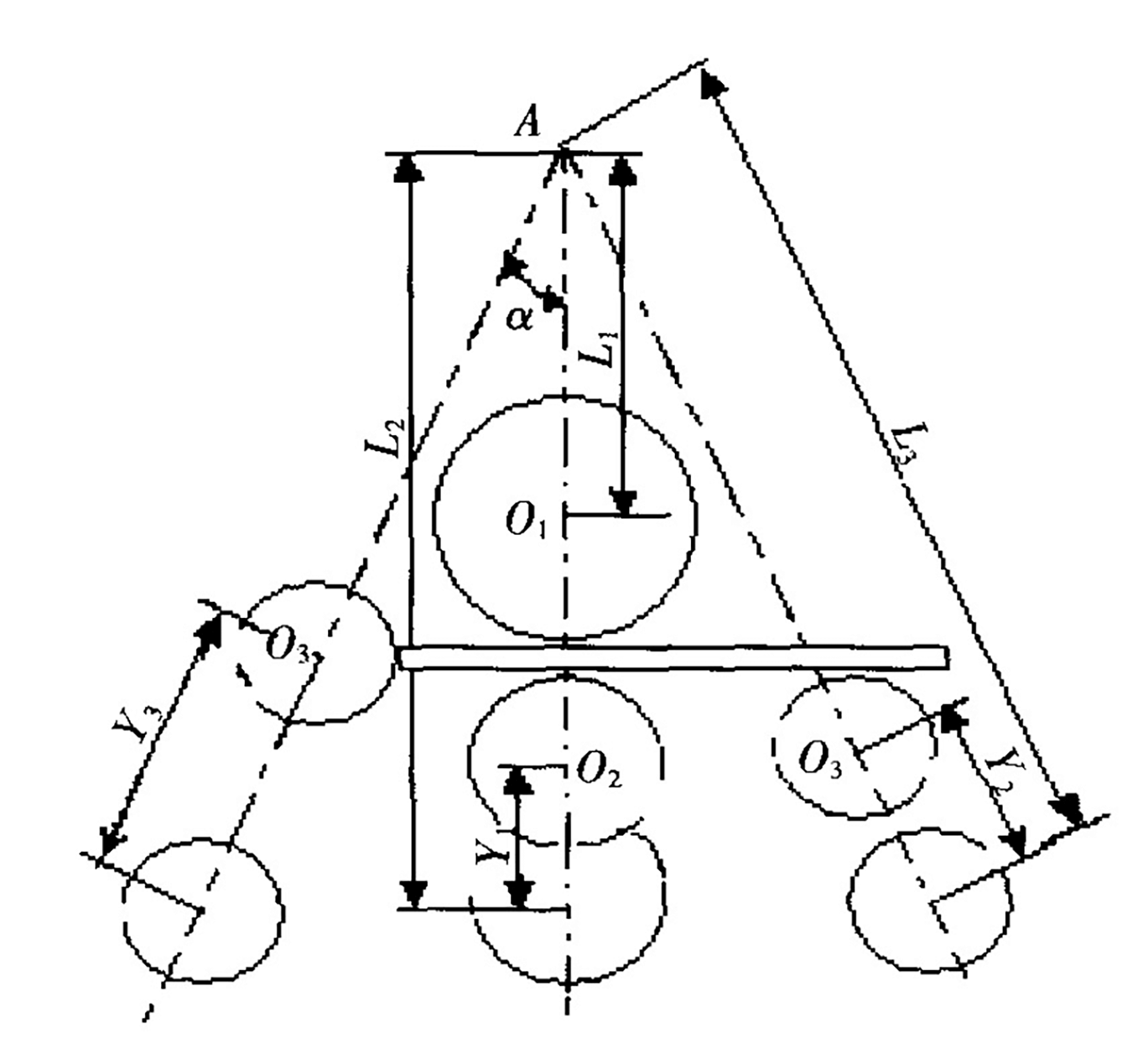
Fig. 3 Posição de processo dos rolos de alinhamento
O deslocamento dos dois rolos laterais e do rolo inferior pode ser calculado com base na relação geométrica, como segue:
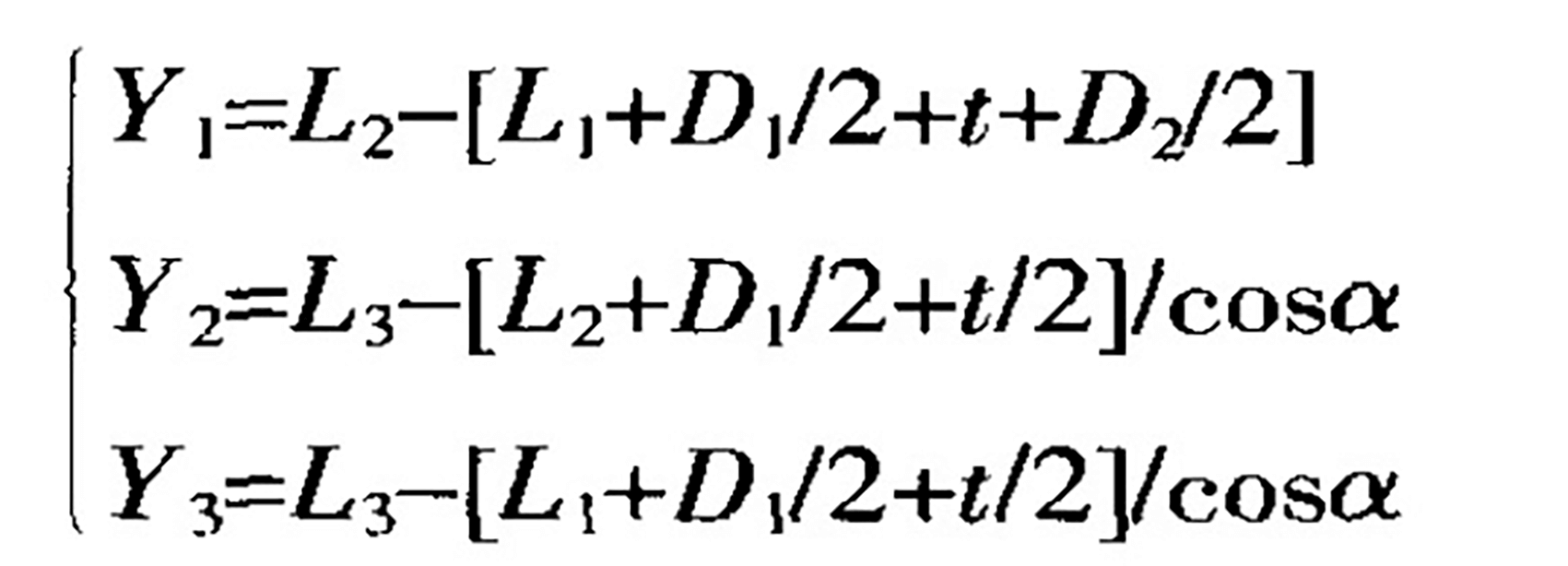
4.2 Cálculo do deslocamento do rolo lateral durante o préflexão
Durante o processo de pré-dobragem da dobradeira, conforme mostrado na Figura 2, o rolo inferior e os rolos dianteiro e traseiro sofrem deslocamento correspondente.
Para atender aos requisitos do processo de pré-dobra, a posição do processo de cada rolo durante a pré-dobra à esquerda é mostrada na Figura 4. Durante a pré-dobra à direita, as posições dos rolos dianteiro e traseiro são simplesmente trocadas, enquanto a posição do rolo inferior permanece inalterada.
O valor do parâmetro geométrico B pode ser calculado usando a fórmula de cálculo para a calandra assimétrica de chapas de três rolos. Neste artigo, B é considerado igual a 2t.
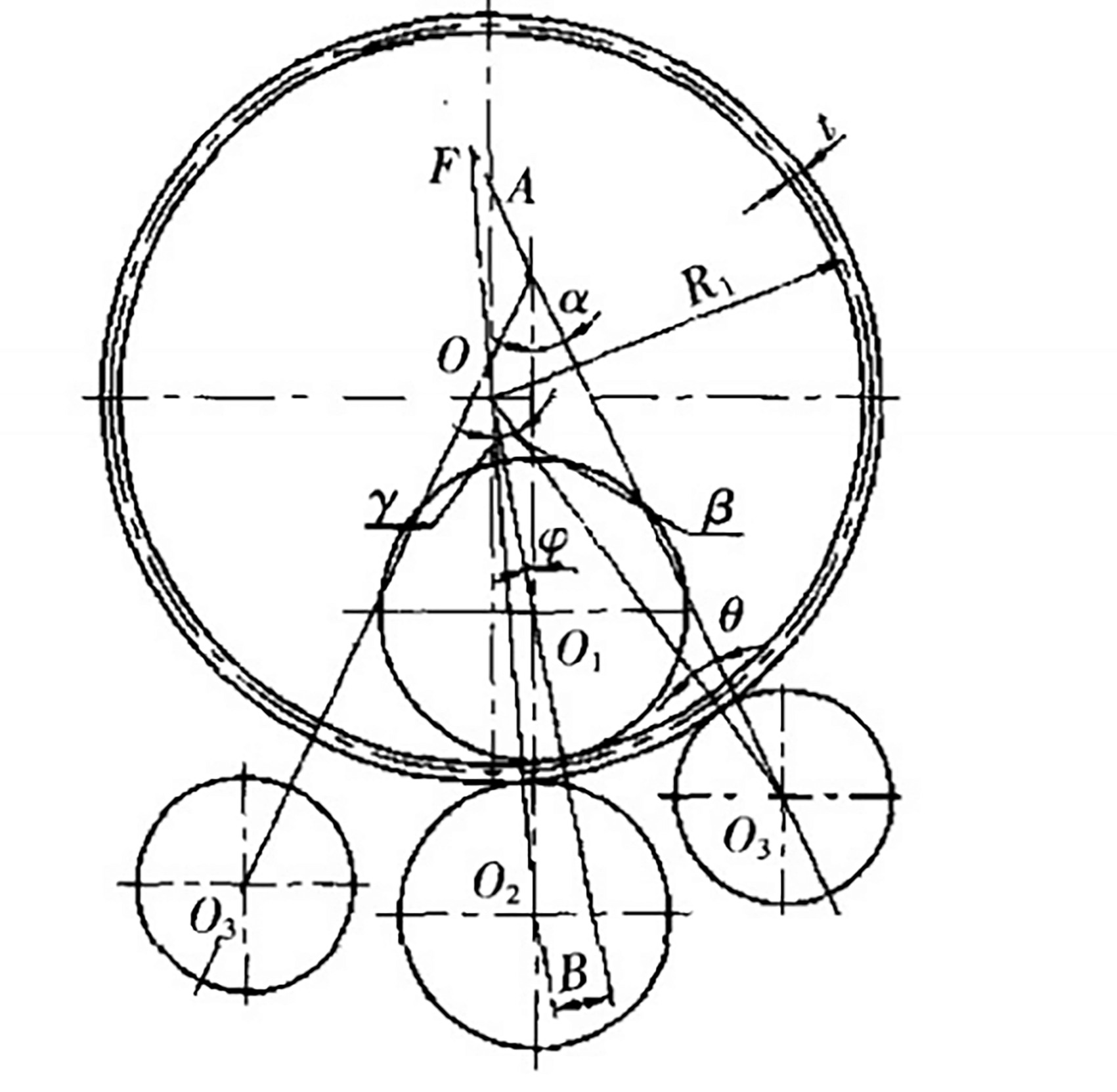
Fig. 4 Posição de processo de cada rolo durante a pré-dobragem
Suponha que “O” seja o centro de curvatura antes do retorno elástico, “y” representa o ângulo entre o centro de rotação superior e a linha central de flexão “OO1”E o ângulo entre o centro de rolo inferior e a linha central de dobra “OO2.”
O ângulo “φ” representa o ângulo entre a linha “O1Ó2” entre o centro do rolo superior e o centro do rolo inferior, e a linha entre o centro do rolo superior e o centro de dobra.
O ângulo “θ” representa o ângulo entre a linha “AO3” entre o centro da dobradeira e o centro do rolo lateral, e a linha “OO3”entre o centro do rolo lateral e o centro de dobra.
Com base nessas relações geométricas, pode-se tirar a seguinte conclusão:
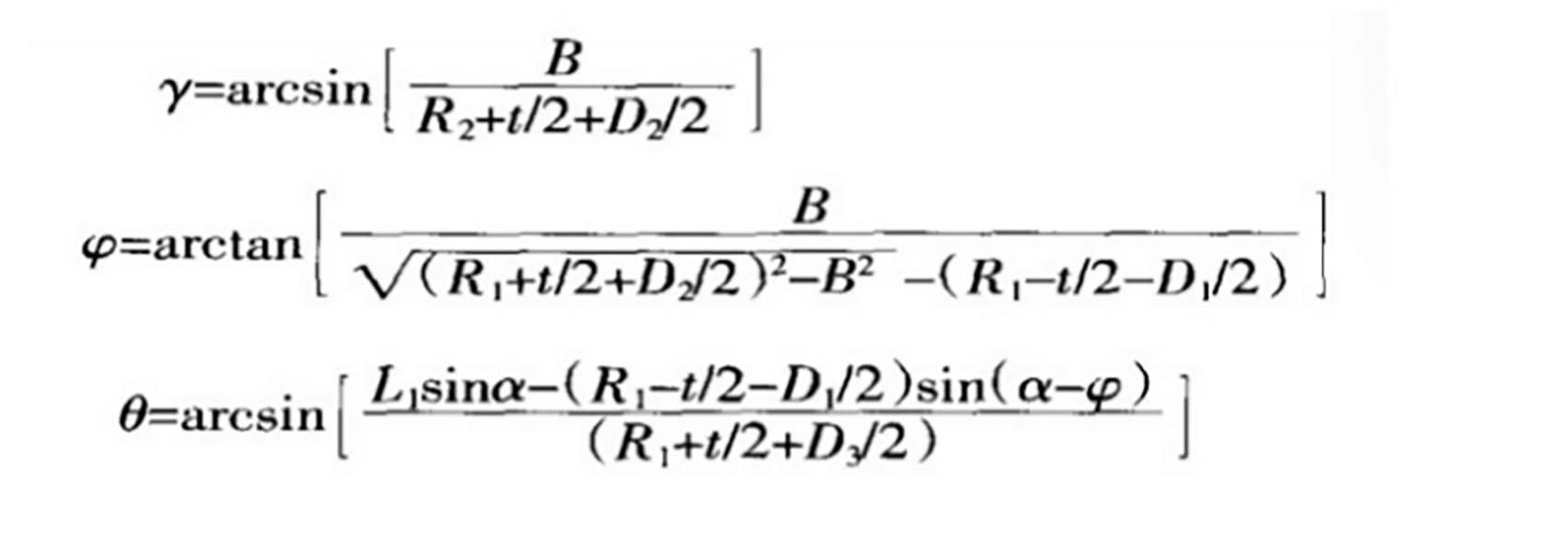
Na fórmula, o parâmetro geométrico B é o valor do centro do rolo inferior O2 para OO1que pode ser calculado de acordo com a fórmula da dobradeira assimétrica de três rolos.
Neste artigo, B = 2t e outros parâmetros são iguais aos anteriores.
Suponha que F é a interseção de OO2 e AO3e β é o ângulo entre F e a linha média dos rolos superior e inferior.

Em △ AFO2de acordo com o teorema do seno:
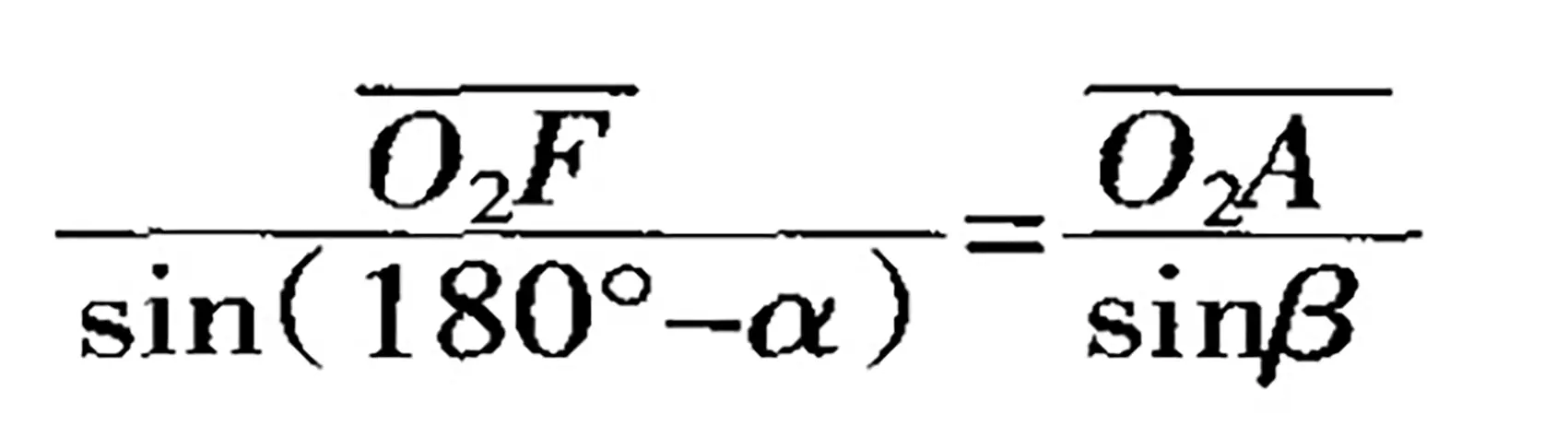
Por isso:

Da mesma forma, em △ AFO2:
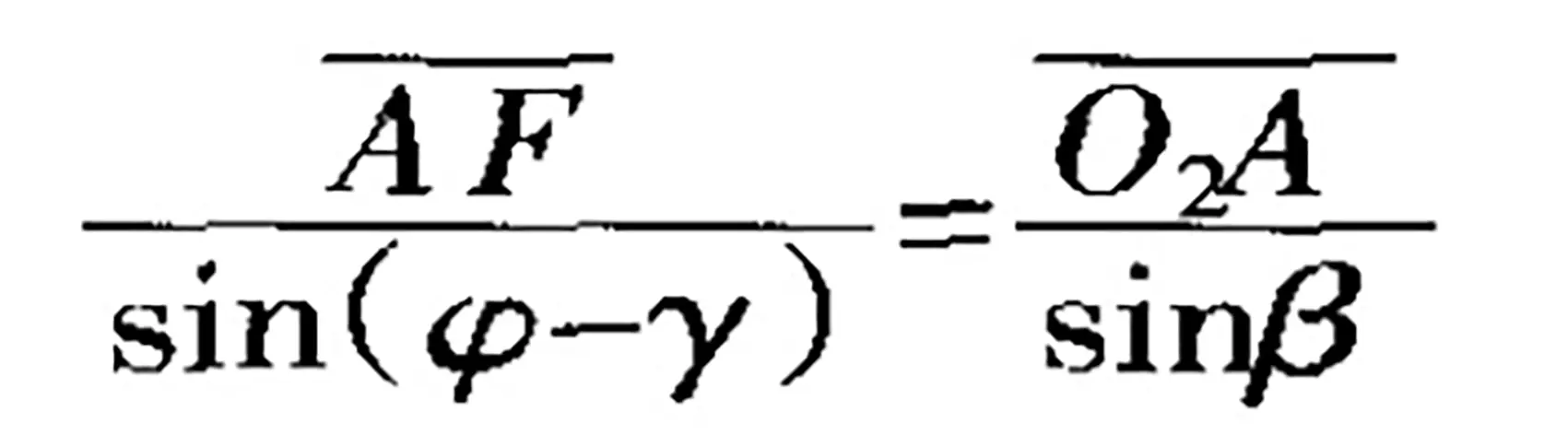
Por isso:

Em △ AFO2:

Por isso:

Aquilo é:

Portanto, o deslocamento entre os dois rolos laterais e o rolo inferior é:
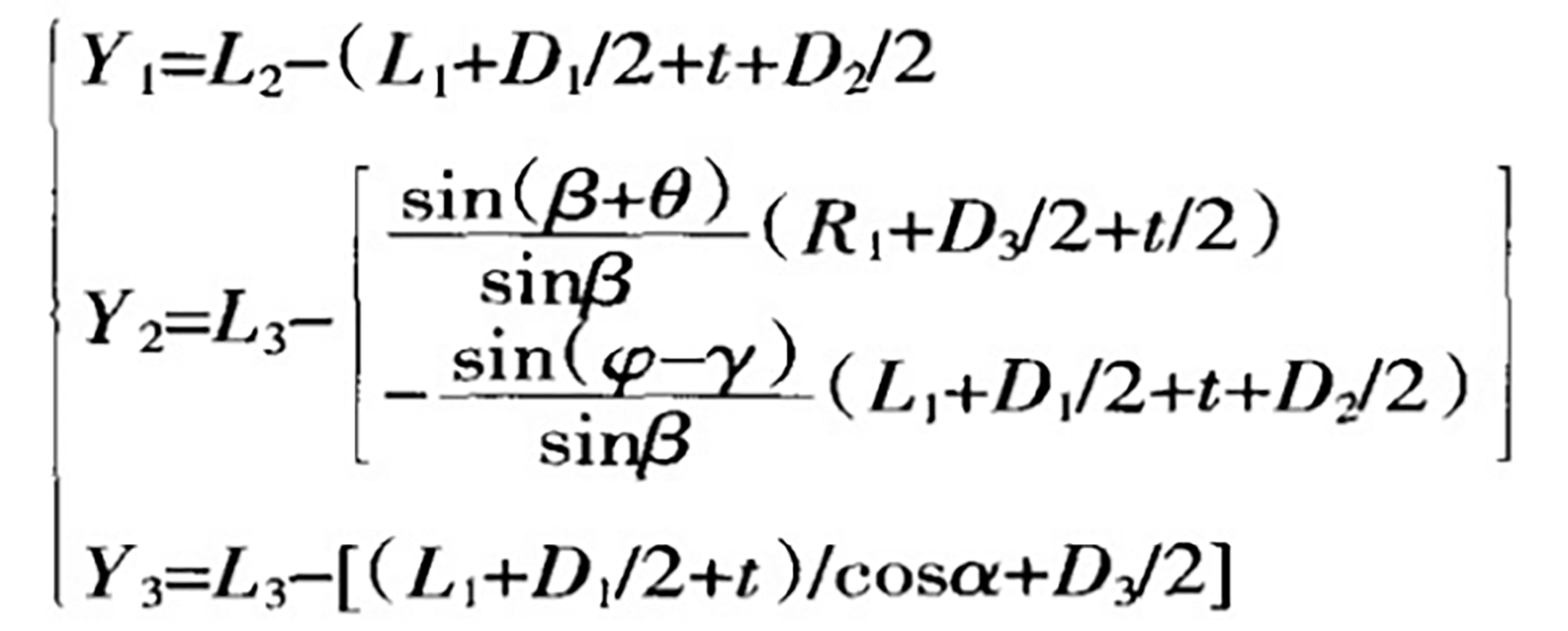
Quando o lado direito está pré-flexionado, Y1 permanece inalterado, Y2 e você3 podem ser trocados.
4.3 Cálculo do deslocamento do rolo lateral durante flexão contínua
No processo de dobra contínua da dobradeira de placas mostrada na Figura 2, os dois rolos laterais são posicionados simetricamente, e o rolo inferior e os rolos laterais dianteiro e traseiro têm deslocamentos correspondentes.
Para atender aos requisitos do processo de dobra contínua, a posição de cada rolo durante o processo é exibida na Figura 5.

Fig. 5 Posição de processo de cada rolo durante a dobra contínua
De acordo com a relação geométrica, em △OAO3do teorema do seno:
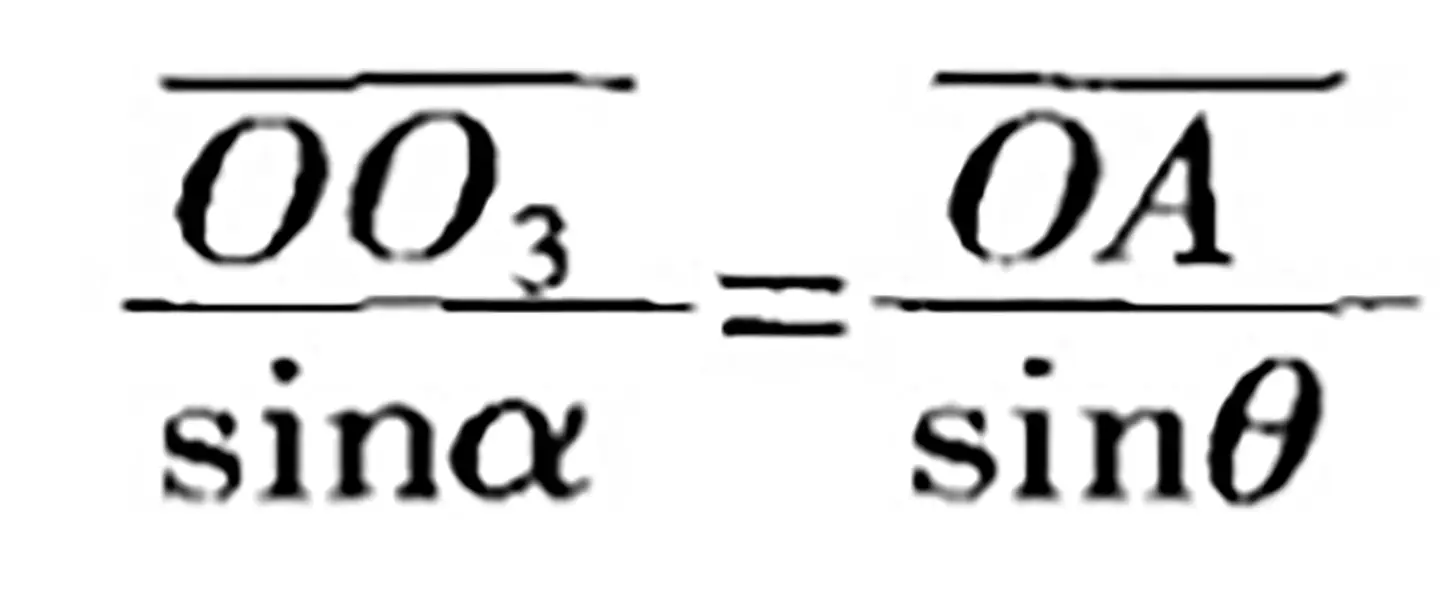
Por isso:

Suponha que O seja o centro de curvatura antes do retorno elástico, λ seja o ângulo entre OO2 e OO3então:
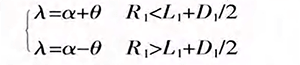
Em △OAO3:
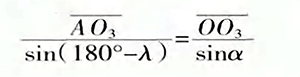
Por isso:

Se você1 permanece inalterado, Y2=S3=L3-AO3então o deslocamento dos roletes em ambos os lados e no rolete inferior é:
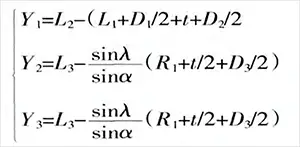
5. Resultados reais da verificação
Foi realizado um estudo experimental utilizando uma laminadora de chapas W1220 x 2500, com chapa de material Q235 de 10 mm de espessura e raio de laminação de 700 mm.
Os resultados do experimento mostraram que houve um erro absoluto de 4,8 mm entre o raio do círculo real e o raio do círculo necessário, resultando em um erro relativo de 0,68%. Com base nesses resultados, determinou-se que a correção foi suficiente para atender aos requisitos de precisão.
Ao analisar os dados de teste de múltiplas tentativas de ajustar o raio de retorno elástico, descobriu-se que a principal causa do erro foi a suposição de que a placa estava sofrendo flexão pura durante o cálculo do raio de retorno elástico, e não levando em consideração o impacto da extrusão força e atrito.
Porém, a análise técnica mostrou que o cálculo do deslocamento foi preciso e atendeu aos requisitos do processo.
6. Conclusão
Este artigo apresenta uma análise do processo de laminação de uma laminadora de chapas grossas de quatro rolos. Combinando a fórmula de cálculo do raio de retorno elástico com métodos matemáticos e mecânicos, o artigo analisa a posição de cada rolo durante o processo de trabalho da máquina.
Os resultados do cálculo foram testados em uma dobradeira de chapas de quatro rolos.
Os resultados do experimento mostraram que este método pode reduzir significativamente o número de testes e melhorar a precisão e eficiência do processo de laminação.