A manufatura aeroespacial é o campo mais concentrado de alta tecnologia na manufatura, pertencente à tecnologia de manufatura avançada.
Produtos notáveis incluem o motor F119 desenvolvido pela Hewlett-Packard nos Estados Unidos, o motor F120 da General Electric, o motor M88-2 da empresa francesa SNECMA e o motor EJ200 desenvolvido em conjunto pelo Reino Unido, Alemanha, Itália e Espanha. .
Estes representam os motores de aviação de alto desempenho mais avançados do mundo e têm em comum o uso generalizado de novos materiais, novos processos e novas tecnologias. Vamos dar uma olhada nesses novos materiais usados em motores de aviação de alto desempenho.
1. Ligas de alta temperatura
Ligas de alta temperatura foram desenvolvidas para atender aos rigorosos requisitos de materiais dos motores a jato e se tornaram uma classe insubstituível de materiais-chave para componentes hot-end de motores de turbinas a gás militares e civis.
Atualmente, em motores de aviação avançados, as ligas de alta temperatura representam mais de 50% do material utilizado.
O desenvolvimento de ligas de alta temperatura está intimamente relacionado ao progresso tecnológico dos motores de aviação, especialmente aos materiais dos discos e pás da turbina e aos processos de fabricação de componentes hot-end do motor, que são indicadores importantes do desenvolvimento do motor.
Devido às altas demandas impostas à resistência a altas temperaturas do material e à capacidade de suportar tensões, o Reino Unido desenvolveu inicialmente a liga Nimonic80 reforçada com Ni3 (Al, Ti) para uso como material de pá de turbina de motor a jato. Também desenvolveu sequencialmente a série de ligas Nimonic.
Os Estados Unidos desenvolveram ligas à base de níquel reforçadas com dispersão contendo alumínio e titânio, como as séries de ligas Inconel, Mar-M e Udmit desenvolvidas pela Pratt & Whitney, General Electric e Special Metals Corporation, respectivamente.
Durante o desenvolvimento de ligas de alta temperatura, os processos de fabricação desempenharam um papel significativo no impulso ao desenvolvimento da liga. Com o surgimento da tecnologia de fusão a vácuo, a remoção de impurezas e gases nocivos das ligas, especialmente o controle preciso da composição da liga, melhorou continuamente o desempenho das ligas de alta temperatura.
Depois disso, a pesquisa bem-sucedida em novos processos, como solidificação direcional, crescimento de cristal único, metalurgia do pó, liga mecânica, tipos de núcleo cerâmico, filtragem cerâmica, forjamento isotérmico, etc., impulsionou o rápido desenvolvimento de ligas de alta temperatura.
Dentre estas, destaca-se a tecnologia de solidificação direcional; as ligas produzidas por esse processo – ligas direcionais monocristalinas – podem ser usadas em temperaturas próximas a 90% de seu ponto de fusão inicial.
Como resultado, as pás das turbinas dos atuais motores de aviação avançados de vários países são fabricadas com ligas direcionais de cristal único. Globalmente, cristais equiaxiais, cristais colunares solidificados direcionalmente e sistemas de liga monocristalino foram formados a partir de ligas fundidas de alta temperatura à base de níquel.
As ligas em pó para alta temperatura também desenvolveram a partir da primeira geração discos de turbina em pó de 650°C a 750°C e 850°C e discos de pó de duplo desempenho, que são usados em motores avançados de alto desempenho.
2. Aço de ultra-alta resistência
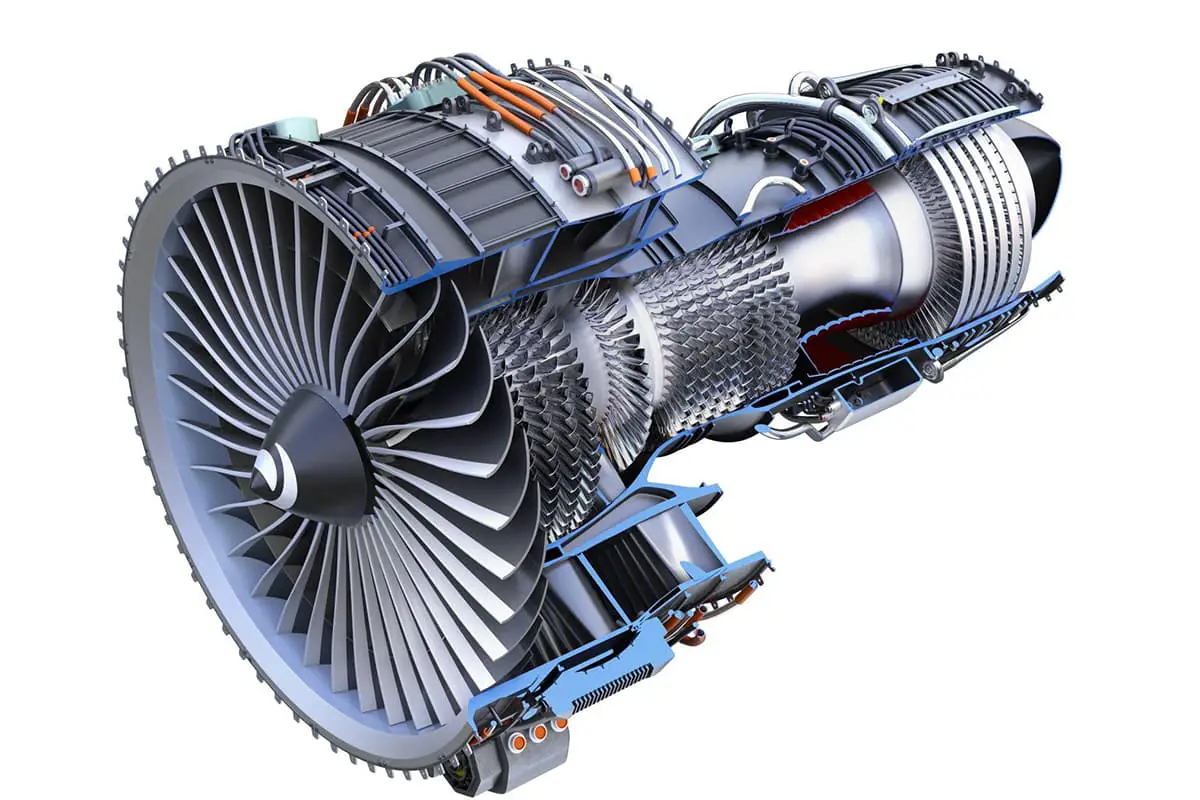
Aço de ultra-alta resistência é usado como material de trem de pouso em aeronaves. A aeronave de segunda geração utilizou aço 30CrMnSiNi2A em seu trem de pouso, com resistência à tração de 1700 MPa. No entanto, a vida útil deste trem de pouso foi relativamente curta, aproximadamente 2.000 horas de voo.
Para o projeto do caça de terceira geração, espera-se que o trem de pouso tenha uma vida útil superior a 5.000 horas de voo. Devido ao aumento do equipamento de bordo e à diminuição da relação de peso da estrutura da aeronave, maiores exigências são colocadas na seleção e tecnologia de fabricação do trem de pouso.
Os caças de terceira geração americanos e chineses adotaram a tecnologia de fabricação de trens de pouso em aço 300M (com resistência à tração de 1950 MPa).
Deve-se salientar que a melhoria na tecnologia de aplicação de materiais também está impulsionando uma maior extensão da vida útil do trem de pouso e ampliando a adaptabilidade.
Por exemplo, o trem de pouso do Airbus A380 adotou tecnologia de forjamento integral ultragrande, nova tecnologia de tratamento térmico atmosférico e tecnologia de pulverização de chama de alta velocidade, garantindo que a vida útil do trem de pouso atenda aos requisitos de projeto. Portanto, o progresso de novos materiais e tecnologias de fabricação garante a renovação e modernização das aeronaves.
O projeto de longa vida útil de aeronaves em ambientes corrosivos exige padrões mais elevados de materiais. Em comparação com o aço 300M, o aço AerMet100 fornece um nível de resistência equivalente, mas exibe resistência geral à corrosão e resistência à corrosão sob tensão superiores.
A tecnologia de fabricação de trens de pouso que acompanha tem sido empregada em aeronaves avançadas, como o F/A-18E/F, F-22 e F-35. O aço Aermet310 de maior resistência, que apresenta menor tenacidade à fratura, está atualmente sob investigação.
O aço AF1410 de ultra-alta resistência, conhecido por sua taxa de propagação de trincas extremamente lenta, é usado na junta do atuador da asa da aeronave B-1, alcançando uma redução de 10,6% no peso e uma melhoria de 60% na usinabilidade em comparação ao Ti-6Al- 4V, e uma redução de custos de 30,3%. O aço inoxidável de alta resistência usado no MiG-1.42 russo representa 30% do total.
PH13-8Mo é o único aço inoxidável martensítico de endurecimento por precipitação de alta resistência amplamente utilizado em componentes resistentes à corrosão.
Internacionalmente, o desenvolvimento de aço para engrenagens (rolamentos) de ultra-alta resistência, como CSS-42L e GearmetC69, foi testado em motores, helicópteros e aeroespacial.
3. Compostos Intermetálicos
O desenvolvimento de motores aeronáuticos de alto desempenho e alta relação peso-empuxo promoveu o desenvolvimento e a aplicação de compostos intermetálicos. Hoje, os compostos intermetálicos evoluíram para uma família diversificada, normalmente composta de compostos metálicos binários, ternários ou multielementares.
Os compostos intermetálicos possuem um potencial significativo para aplicações estruturais em altas temperaturas, oferecendo altas temperaturas de uso, alta resistência específica e condutividade térmica. Especialmente em condições de alta temperatura, possuem excelente resistência à oxidação, alta resistência à corrosão e alta resistência à fluência.
Como os compostos intermetálicos representam um novo material que preenche a lacuna entre as ligas de alta temperatura e os materiais cerâmicos, eles se tornaram um dos materiais ideais para componentes de alta temperatura em motores aeronáuticos.
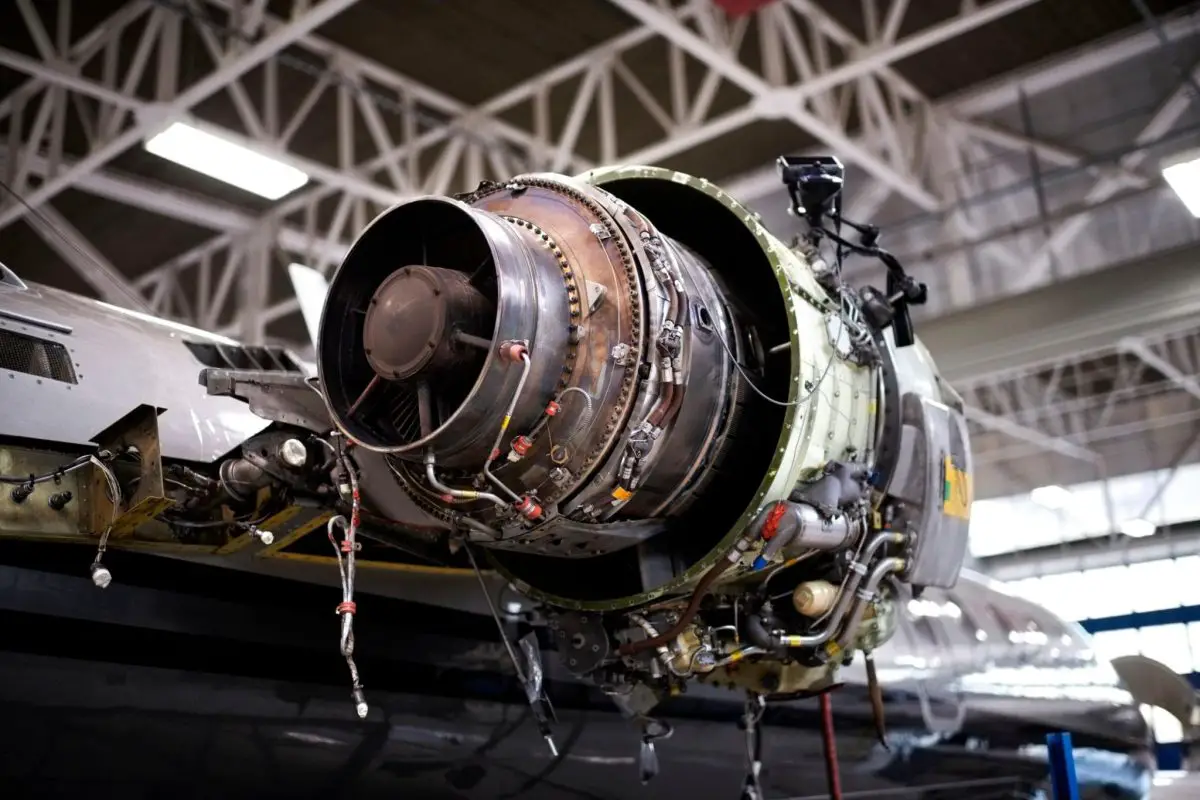
Atualmente na estrutura de motores aeronáuticos, o foco principal de pesquisa e desenvolvimento está em compostos intermetálicos, com ênfase particular em titânio alumínio e níquel alumínio. Esses compostos de titânio e alumínio compartilham uma densidade semelhante ao titânio, mas têm uma temperatura de uso significativamente mais alta.
Por exemplo, suas temperaturas de uso são 816°C e 982°C, respectivamente. As fortes ligações interatômicas e as estruturas cristalinas complexas dos compostos intermetálicos resultam em difícil deformação, exibindo características duras e quebradiças à temperatura ambiente.
Após anos de pesquisa experimental, uma nova liga com resistência a altas temperaturas e plasticidade e tenacidade à temperatura ambiente foi desenvolvida e instalada com sucesso, com ótimos resultados. O motor F119 de alto desempenho dos Estados Unidos, por exemplo, utiliza compostos intermetálicos na carcaça do motor e no disco da turbina. As pás do compressor e o disco do motor de teste F120 são feitos de um novo composto intermetálico de titânio e alumínio.
4. Compósitos de matriz cerâmica
Quando se pensa em cerâmica, naturalmente vem à mente a fragilidade. Algumas décadas atrás, usá-lo para componentes de suporte de carga em engenharia era inconcebível. Mesmo agora, quando falamos sobre compósitos cerâmicos, algumas pessoas podem não entender, assumindo que cerâmica e metais são materiais fundamentalmente não relacionados. No entanto, a engenhosa união de cerâmicas e metais mudou fundamentalmente a nossa percepção deste material, dando origem aos compósitos de matriz cerâmica.
Os compósitos de matriz cerâmica são um novo material estrutural promissor na indústria aeroespacial, particularmente na fabricação de motores aeronáuticos, onde seus atributos únicos são cada vez mais evidentes. Além de serem leves e duros, os compósitos de matriz cerâmica também possuem excepcional resistência a altas temperaturas e resistência à corrosão em temperaturas elevadas.
Atualmente, os compósitos de matriz cerâmica superaram os materiais metálicos resistentes ao calor na resistência a altas temperaturas, demonstrando excelentes propriedades mecânicas e estabilidade química, tornando-os um material ideal para zonas de alta temperatura de motores de turbina de alto desempenho.
Atualmente, países em todo o mundo estão concentrando suas pesquisas em cerâmicas reforçadas com nitreto de silício e carboneto de silício para atender aos requisitos de materiais da próxima geração de motores avançados, e têm feito progressos significativos. Alguns já começaram a incorporar esses materiais em motores aeronáuticos modernos.
Por exemplo, o motor de teste F120 dos Estados Unidos utiliza materiais cerâmicos em seus dispositivos de vedação de turbina de alta pressão e alguns componentes de alta temperatura de sua câmara de combustão. O motor M88-2 da França também utiliza compósitos de matriz cerâmica em sua câmara de combustão e bocal.
5. Materiais compostos de carbono/carbono
Os materiais compósitos carbono/carbono (C/C), emergindo como os mais notáveis materiais resistentes a altas temperaturas nos últimos anos, são atualmente os únicos materiais considerados adequados para uso em pás de rotores de turbinas, com uma relação empuxo-peso superior a 20 e temperaturas de entrada do motor atingindo 1930-2227°C.
Estes materiais são uma área de foco chave para os Estados Unidos no século XXI e um objectivo primordial perseguido pelas nações industriais avançadas em todo o mundo. Os materiais compósitos C/C, ou compósitos de matriz de carbono reforçados com fibra de carbono, combinam exclusivamente a natureza refratária do carbono com a alta resistência e rigidez das fibras de carbono, levando a falhas não frágeis.
Com seu peso leve, alta resistência, estabilidade térmica superior e excelente condutividade térmica, eles são os materiais resistentes a altas temperaturas mais ideais da atualidade. Notavelmente, sob condições de alta temperatura variando de 1000-1300°C, a sua resistência não diminui, mas sim aumenta. Mesmo em temperaturas abaixo de 1650°C, eles mantêm sua resistência e forma à temperatura ambiente. Consequentemente, os materiais compósitos C/C têm um potencial significativo para desenvolvimento na indústria de fabricação aeroespacial.
O principal problema com a aplicação de materiais compósitos C/C em motores de aviação é a sua fraca resistência à oxidação. No entanto, nos últimos anos, os Estados Unidos resolveram gradualmente este problema através de uma série de medidas de processo e aplicaram-nas progressivamente a novos motores.
Por exemplo, os tubos de escape do pós-combustor do motor F119, os bicos e dutos da câmara de combustão do motor F100 e certas partes da câmara de combustão do motor de validação F120 agora são feitos com compósitos C/C. Da mesma forma, os motores M88-2 e Mirage 2000 da França, incluindo suas barras de combustível de pós-combustão, escudos térmicos e dutos, também empregam compósitos C/C.
6. Materiais Compósitos à Base de Resina
As pesquisas sobre a aplicação de materiais compósitos à base de resina em motores turbofan de aviação começaram na década de 1950. Após mais de 60 anos de desenvolvimento, empresas como GE, PW, RR, MTU e SNECMA investiram esforços significativos na investigação e desenvolvimento destes materiais, obtendo progressos substanciais. Eles projetaram com sucesso esses compósitos para motores turbofan de aviação em serviço ativo, e há uma tendência para aumentar ainda mais seu uso.
A temperatura de serviço dos materiais compósitos à base de resina geralmente não excede 350°C. Assim, esses materiais são utilizados principalmente na extremidade fria de motores de aviação. As principais áreas de aplicação de materiais compósitos à base de resina em motores avançados de aviação estrangeira são ilustradas abaixo.
Pá do Ventilador: A pá do ventilador do motor é um componente crítico representativo do motor turbofan, intimamente relacionado ao seu desempenho. Em comparação com as pás do ventilador de liga de titânio, as pás do ventilador composto à base de resina têm uma vantagem muito clara na redução de peso. Além da nítida redução de peso, o impacto na caixa da ventoinha é menor depois que a pá da ventoinha composta à base de resina é atingida, o que é benéfico para aumentar a capacidade de contenção da caixa da ventoinha.
Atualmente, os principais representantes de pás de ventilador compostas aplicadas comercialmente no exterior incluem os motores da série GE90 para o B777, os motores GEnx para o B787 e os motores LEAP-X para o C919 da Chinese Commercial Aircraft Corporation.
Em 1995, o motor GE90-94B equipado com pás de ventilador compostas à base de resina entrou oficialmente em operação comercial, significando a aplicação formal de engenharia de compósitos à base de resina em motores de aviação modernos de alto desempenho. Considerando fatores como aerodinâmica e fadiga de ciclo alto e baixo, a GE desenvolveu novas pás de ventilador compostas para o motor GE90-115B subsequente.
Ao entrar no século 21, a forte demanda por compósitos de alta tolerância a danos em motores de aviação impulsionou o desenvolvimento da tecnologia de compósitos. No entanto, tornou-se cada vez mais desafiador atender aos requisitos de alta tolerância a danos, melhorando continuamente a resistência do pré-impregnado de fibra de carbono/resina epóxi. Neste contexto, surgiram pás de ventilador compostas de estrutura tecida 3D.
Fan Case: A fan case é a maior parte estacionária de um motor de aviação. Sua redução de peso afetará diretamente a relação empuxo-peso e a eficiência do motor. Portanto, os OEMs estrangeiros de motores de aviação avançados sempre estiveram comprometidos com a redução de peso e a otimização estrutural da caixa do ventilador. A tendência de desenvolvimento de caixas de ventiladores em motores avançados de aviação estrangeira é mostrada na figura.
Capota do ventilador: Como não é um componente primário de suporte de carga, a carenagem do ventilador foi uma das primeiras peças de um motor de aeronave a ser feita de materiais compósitos. A utilização desses materiais para carenagens de ventiladores permite menor peso, uma estrutura anticongelante simplificada, resistência superior à corrosão e melhor resistência à fadiga.
Atualmente, os materiais compósitos à base de resina são empregados na construção de carenagens de ventiladores nos motores RB211 da Rolls-Royce, bem como nos motores PW1000G e PW4000 da Pratt & Whitney.
Em comparação com o corpo principal dos motores de aeronaves, os compósitos à base de resina têm uma aplicação mais ampla em carenagens curtas de motores, conforme mostrado na figura. De acordo com os recursos, os fabricantes estrangeiros têm empregado extensivamente compósitos à base de resina em entradas de ar curtas, carenagens, reversores de empuxo e revestimentos de redução de ruído.
Os compósitos à base de resina também são aplicados em vários graus em outras partes do motor da aeronave, como palhetas guia de fluxo do ventilador, vedações de rolamentos e placas de cobertura, conforme recursos.
7. Compostos de Matriz Metálica
Os compósitos com matriz metálica, comparados aos compósitos à base de resina, possuem excelente tenacidade, não absorvem umidade e podem suportar temperaturas relativamente altas. As fibras de reforço dos compósitos com matriz metálica incluem fibras metálicas como aço inoxidável, tungstênio e compostos intermetálicos de níquel e alumínio; fibras cerâmicas como alumina, sílica, carbono, boro e carboneto de silício.
Os materiais de matriz dos compósitos com matriz metálica incluem alumínio, ligas de alumínio, magnésio, titânio e ligas de titânio e ligas resistentes ao calor. Compósitos à base de ligas de alumínio-magnésio, titânio e ligas de ferro são atualmente as principais escolhas. Por exemplo, compósitos de liga de titânio reforçados com fibra de carboneto de silício podem ser usados para fabricar lâminas de compressor.
Compostos de magnésio ou liga de magnésio reforçados com fibra de carbono ou fibra de alumina podem ser usados para produzir pás de ventilador de turbina. Compósitos de liga de níquel reforçados com fibra de níquel-cromo-alumínio-irídio podem ser usados para fabricar vedações para turbinas e compressores.
Outras peças, como carcaças de ventiladores, rotores e discos de compressor, têm casos de produção com compósitos de matriz metálica no exterior. No entanto, um dos maiores problemas com estes compósitos é que as fibras de reforço e os metais básicos tendem a reagir e formar fases frágeis, deteriorando as propriedades do material.
Isto é especialmente pronunciado durante o uso prolongado em temperaturas mais altas. As soluções atuais incluem a aplicação de um revestimento apropriado na superfície da fibra com base em diferentes fibras e matrizes, bem como a liga da matriz metálica, para retardar a reação da interface e manter a confiabilidade dos materiais compósitos.