O método tradicional de produção de chapas de aço silício, utilizadas em motores e eletrodomésticos, envolve a instalação de moldes em prensas mecânicas.
A matriz de estampagem a frio de chapa de aço silício é composta principalmente de matrizes macho e fêmea, que são instaladas na prensa para perfurar a chapa de aço silício no estator e rotor do motor ou chip de ferro do transformador.
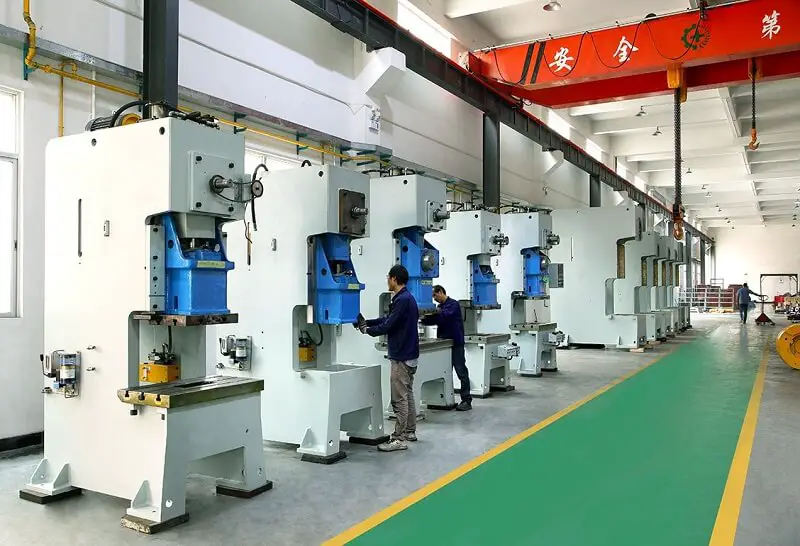
Durante a operação de uma matriz de chapa de aço silício, a borda está sujeita a forças de impacto, cisalhamento e flexão. Além disso, a borda também é comprimida e friccionada pela chapa de aço silício. Um revestimento especial na superfície da chapa de aço silício aumenta o atrito e o desgaste da borda, principal motivo da falha normal da matriz.
Como resultado, o desgaste da matriz é severo e muitas vezes precisa ser afiado antes de atingir sua vida útil ideal. O número de peças puncionadas em um conjunto de matrizes costuma ser menor que seu valor teórico.
Por exemplo, considere o processo de moldagem de uma chapa de aço silício de um determinado motor. São necessários sete tipos de matrizes para serem concluídos, com um custo total de 190.000 yuans. A dureza de uma matriz de estampagem para uma folha de rotor é de 60 a 62Hrc e é instalada em uma máquina-ferramenta de estampagem de 60t. Normalmente, a matriz pode perfurar mais de 200.000 peças.
No entanto, a borda do furo da matriz desmorona depois de ser usada menos de 9.000 vezes. Retificar a matriz (geralmente após 50.000 a 60.000 vezes) e reaplicá-la na máquina não resolve o problema. Em vez disso, o colapso persiste e aparecem rachaduras na borda externa da matriz.
Durante a estampagem contínua, as fissuras expandem-se rapidamente e a matriz falha, tornando-se inutilizável após menos de 20.000 utilizações. Cada vez que dois motores são produzidos, três tipos de moldes exigem afiação, custando entre 400 e 800 yuans cada vez, tornando o custo de fabricação do produto relativamente alto.
Especialmente durante a produção experimental de novos produtos, os custos de fabricação de moldes são consideravelmente altos e o ciclo de produção é longo, dobrando o custo de desenvolvimento de novos produtos.
Produção e requisitos de chapa de aço silício
A chapa de aço silício é um componente crucial de motores e aparelhos elétricos. Seu desempenho afeta diretamente a perda de energia elétrica e a eficiência, tamanho e peso de produtos como transformadores.
Portanto, a chapa de aço silício geralmente deve atender aos seguintes requisitos:
- Deve ter um revestimento de superfície liso, excelente formato, alta precisão dimensional e variação mínima de espessura dentro da mesma placa.
- Deve possuir propriedades eletromagnéticas favoráveis e uma estrutura de grãos orientados que atenda aos requisitos da aplicação.
O processo de corte de chapa de aço silício não deve apenas ter as características típicas de cisalhamento de metal, mas também satisfazer os seguintes requisitos especiais.
Altura da rebarba
A altura da rebarba na chapa de aço silício usada para estampagem não deve exceder 0,05 mm. O impacto das rebarbas no desempenho de todas as peças mecânicas da máquina está recebendo mais atenção.
As características eletromagnéticas de geradores, motores e transformadores que utilizam chapas de aço silício são significativamente afetadas por rebarbas.
O blanking de matriz é usado para formar as chapas de aço silício usadas em geradores, motores e transformadores. Freqüentemente, a lacuna na fabricação da matriz é muito grande ou aumenta devido ao desgaste.
Durante o processo de blanking, a chapa de aço silício é extrudada, causando leve deformação plástica. Essa deformação permanece na borda da chapa, resultando na formação de rebarbas.
O rotor, o estator e o núcleo do transformador dos geradores usam um grande número de chapas de aço silício com rebarbas.
Rebarbas na chapa de aço silício reduzem o fator de empilhamento. Para instalar o mesmo número de folhas, o volume do motor deve aumentar.
Além disso, a rebarba afeta a potência de saída do motor. Foi demonstrado que a potência de saída do gerador pode aumentar de 0,1% a 0,2% usando chapas de aço silício rebarbadas em comparação com geradores que não utilizam chapas de aço silício rebarbadas.
Impacto na vida útil do gerador
A presença de rebarbas nas chapas de aço silício cria lacunas significativas entre as laminações, o que pode levar à produção de correntes parasitas, aumento da perda magnética, temperaturas mais elevadas, ruído e até curtos-circuitos, resultando em falha do motor.
Motores com chapas de aço silício rebarbadas têm uma vida útil média superior a 5% em comparação com motores sem rebarbação.
As chapas de aço silício processadas podem ser empilhadas manualmente ou automaticamente, e a folga na junta deve ser minimizada. Isto exige que o equipamento mantenha alta precisão, incluindo precisão de peças sobressalentes, ao atingir a capacidade máxima de produção. Isso garante que os produtos fiquem praticamente livres de rebarbas após o corte (a altura das rebarbas após o corte longitudinal da chapa de aço silício não deve exceder 0,05 mm).
Caso contrário, durante a laminação, rebarbas podem causar curto-circuitos entre as laminações, aumentar a perda de correntes parasitas e reduzir o coeficiente de enchimento da laminação.
Os padrões relevantes da China afirmam claramente que a altura da rebarba das chapas de aço silício não deve exceder 0,05 mm. No entanto, muitas fábricas de automóveis não implementaram medidas eficazes de rebarbação. Eles ainda instalam e usam folhas com rebarbas de até 0,07 ~ 0,1 mm, o que afeta seriamente a qualidade.
Além disso, a película de tinta isolante na superfície da chapa de aço silício não deve ser visivelmente arranhada durante o rebarbamento.
Efeito do estresse
Após o corte, estampagem e empilhamento, as chapas de aço silício sofrem tensões internas que deformam os grãos, reduzem a permeabilidade e aumentam a perda específica de ferro.
Para evitar ou minimizar esses efeitos, as chapas de aço silício orientadas laminadas a frio são normalmente tratadas com recozimento preenchido com nitrogênio a uma temperatura de aproximadamente 800°C após o processamento de cisalhamento. Este tratamento elimina o estresse gerado durante o processamento e garante que as propriedades originais sejam mantidas.
Embora os testes tenham mostrado que a perda específica de ferro da chapa de aço silício orientada laminada a frio após o recozimento é reduzida em cerca de 30%, muitos fabricantes optam por não adotar este processo devido ao aumento de custo associado.
Dobragem de foice de chapa de aço
Dados os requisitos especializados de desempenho das chapas de aço silício, é crucial manter padrões elevados para a sua produção.
Esses padrões devem superar até mesmo os critérios de flexão lateral da Sociedade Americana de Testes e Materiais (ASTM) para metal cisalhado em geral, que estabelece um limite de não mais que 6mm/3M de comprimento. Como resultado, o layout do processo de cisalhamento para chapas de aço silício precisa atender a requisitos ainda mais rigorosos.
Borda da folha de lótus
A chapa de aço silício que foi cortada deve estar livre de quaisquer ondas visíveis, comumente chamadas de borda de folha de lótus.
No caso de ondas, a relação entre a altura da onda e o comprimento de onda não deve exceder 2,5%.
Se esta condição não for atendida, a chapa de aço silício sofrerá severa deformação plástica, o que resultará em danos à estrutura do domínio e um aumento significativo nas perdas.
Isolamento
Danos no isolamento não são permitidos dentro da faixa de cisalhamento ou na superfície da tira. Além disso, a borda da chapa deve estar livre de qualquer dano de extrusão, pois o não cumprimento desses critérios pode afetar adversamente a qualidade do núcleo de ferro.
Aplicação de tecnologia de corte de água
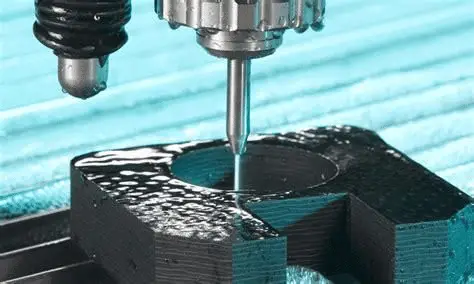
O corte com água de ultra-alta pressão, também conhecido como faca de água ou jato de água, é um processo que gera um fluxo de água de alta energia ao pressurizar a água comum em vários estágios. Esse fluxo de água é então direcionado através de um bico fino para cortar materiais a uma velocidade de quase um quilômetro por segundo.
Esta técnica de corte é conhecida como corte com água de ultra-alta pressão. Sua origem remonta à Escócia, onde foi descoberto. Durante um período de 100 anos, pesquisas experimentais levaram ao desenvolvimento de um sistema industrial de corte de água de alta pressão.
O corte com água de alta pressão não é patenteado. Porém, em 1968, um professor da Universidade de Columbia, nos Estados Unidos, introduziu abrasivos na água de alta pressão, o que acelerou o processo de corte ao moer os materiais com o abrasivo e o jato de água de alta pressão.
Hoje, os Estados Unidos, a Alemanha, a Rússia e a Itália alcançaram avanços na tecnologia de corte com água de ultra-alta pressão, com uma pressão de corte máxima de 550MPa. Este método é amplamente utilizado para cortar materiais como pedra, metal, vidro, cerâmica, produtos de cimento, papel, alimentos, plásticos, tecidos, poliuretano, madeira, couro, borracha, munições e muito mais.
Existem três usos principais do corte de água:
Em primeiro lugar, cortar materiais incombustíveis como mármore, ladrilhos cerâmicos, vidro, produtos de cimento e outros materiais que não podem ser processados por corte térmico.
Em segundo lugar, cortar materiais combustíveis como chapas de aço, plástico, tecido, poliuretano, madeira, couro, borracha, etc. No passado, o corte térmico também podia processar estes materiais, mas muitas vezes resultava em áreas de combustão e rebarbas. O corte com água, por outro lado, não produz tais problemas e as propriedades físicas e mecânicas dos materiais cortados permanecem inalteradas, o que é uma vantagem significativa do corte com água.
Em terceiro lugar, o corte de materiais inflamáveis e explosivos, como munições, e o corte em ambientes inflamáveis e explosivos não podem ser substituídos por outros métodos de processamento.
Em termos de qualidade da água, o corte com água de ultra-alta pressão está disponível em duas formas: corte com água pura e corte abrasivo.
Teste de corte de água
O teste de corte com água para chapas de aço silício é realizado utilizando a faca de água Altorf como equipamento principal.
O gerador de alta tensão (APW38037Z-09A) do equipamento está equipado com um conjunto completo de superalimentadores originalmente importados da AccuStream Inc.
O sistema de controle usa PLC em vez de relé para obter comunicação e controle flexível com o computador.
A plataforma de corte (APW-2030BA) possui estrutura tipo pórtico, o que a torna mais estável e precisa em comparação a uma estrutura cantilever.
O equipamento está equipado com uma plataforma de PC industrial com software especial de corte de água baseado em Windows e suportado por um sistema Windows XP genuíno.
A parte linear do processo de corte tem velocidade de 800mm/min, enquanto a parte do arco circular tem velocidade de 300mm/min. A espessura da chapa de aço silício utilizada no teste é de 0,5 mm.
Após o teste, o produto é retirado da caixa d'água da plataforma de corte, seco e verificado seu tamanho. O produto apresentou problema de fora de tolerância apenas na entrada da faca durante o corte de furo redondo. Esse problema foi causado principalmente pela entrada muito rápida da faca durante a programação, fazendo com que o furo parecesse elíptico. Durante o reteste, esse fenômeno desapareceu e a rebarba ficou menor que 0,05 mm. O produto pode ser empilhado sem trituração e o restante do produto atende aos requisitos do desenho.
Conclusão
Os resultados dos testes do processo de corte com água para chapas de aço silício indicam que a qualidade ideal do produto pode ser alcançada utilizando parâmetros apropriados do processo de corte, monitorando de perto a qualidade da água e o tamanho das partículas de areia e controlando a velocidade de entrada e a direção do arco.
O corte com água oferece diversas vantagens, como alta velocidade, excelente qualidade, economia de custos e fácil modificação do produto. Além disso, é especialmente útil durante a produção experimental de novos produtos, uma vez que não há necessidade de moldes. Isto reduz significativamente o ciclo de preparação da produção e minimiza o investimento inicial necessário para novos produtos. Os resultados de tais ensaios foram altamente satisfatórios.