Com o avanço da moderna tecnologia de fabricação, os equipamentos de usinagem NC e seu sistema CAM de suporte tornaram-se amplamente utilizados e desenvolvidos.
O núcleo do controle da operação de usinagem do equipamento é o caminho da ferramenta (ou seja, modo de deslocamento da ferramenta) gerado pelo sistema CAM.
Isso impacta diretamente a precisão da peça usinada, a rugosidade da superfície, o tempo total de usinagem, a vida útil das máquinas-ferramentas e, em última análise, a eficiência da produção.
Este post analisa as características distintivas do modo de alimentação da ferramenta e alguns fatores que influenciam sua seleção. Ele fornece uma base de referência para a escolha do modo de alimentação de ferramenta apropriado com base em uma comparação de métodos de processo e modos de alimentação de ferramenta no processo de fresamento.
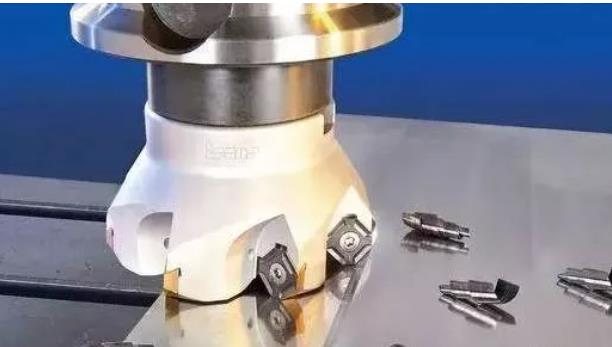
1. Modo de alimentação da ferramenta
Conceito básico do modo de alimentação de ferramenta
Na usinagem NC, o termo “modo de planejamento do caminho da ferramenta” refere-se ao modo no qual o caminho da ferramenta é planejado durante o corte da peça.
Para o processamento da mesma peça, vários métodos de corte podem atender aos requisitos de tamanho e precisão, mas suas eficiências de processamento podem ser diferentes.
Classificação dos métodos de alimentação de ferramentas
Os métodos de alimentação da ferramenta podem ser categorizados em quatro grupos: deslocamento unidirecional da faca, deslocamento alternativo da faca, deslocamento da faca de corte em anel e deslocamento da faca composta. A última categoria, caminhada com faca composta, é uma mistura dos três primeiros métodos.
Esses métodos empregam deslocamento de ferramenta unidirecional ou alternativo, que é conhecido como deslocamento de ferramenta de corte de linha em termos de estratégia de processamento.
Portanto, com base em diferentes estratégias de usinagem, os métodos de alimentação da ferramenta podem ser divididos em corte em linha, corte em anel e outros métodos especializados.
O corte em linha e o corte em anel são os métodos mais comumente usados. O processamento de corte em linha permite a utilização máxima da velocidade de avanço da máquina-ferramenta, levando a uma melhor qualidade da superfície de corte em comparação com o processamento de corte em anel.
No entanto, ao processar cavidades planas complexas com múltiplas saliências que formam múltiplos contornos internos, ações adicionais de elevação da ferramenta podem ser necessárias. Isto é necessário para evitar interferência entre a ferramenta e o ressalto ou para retornar a ferramenta à área não processada. A ferramenta precisa ser elevada a uma altura específica do plano de usinagem, transladada para o início de outro caminho da ferramenta e então continuar o processo de corte.
O caminho da ferramenta para corte linear consiste principalmente em uma série de linhas retas paralelas a uma direção fixa, tornando seu cálculo simples. Este método é ideal para acabamento simples de cavidades ou usinagem de desbaste para remover o excesso de material. Um exemplo disso é mostrado na Fig. 1 – trilho de corte alternativo.

Fig. 1 Trilho de corte alternativo
No corte circular, a ferramenta se move ao longo de um caminho que possui um contorno limite semelhante, consistindo em um grupo de curvas fechadas. Isso ajuda a manter condições de corte consistentes ao usinar peças.
No entanto, o cálculo para o corte do anel é complexo e demorado, pois envolve a construção do diagrama atual do anel e seu deslocamento contínuo para calcular o próximo anel. Apesar disso, é adequado para usinar cavidades e superfícies complexas, conforme demonstrado na Figura 2 – trilho de corte circular.
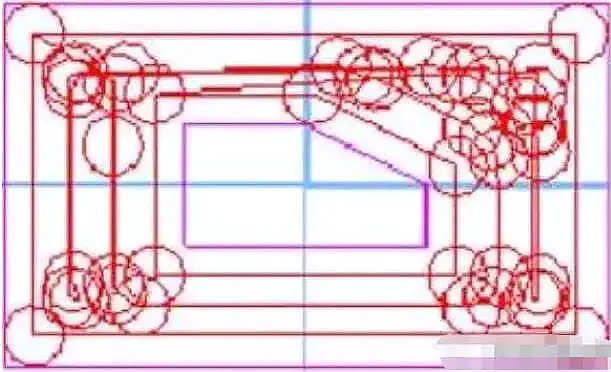
Fig. 2 Trilho de corte circular
2. Fatores que afetam o modo de alimentação da ferramenta
Forma e elementos geométricos da própria peça
A geometria e a forma da peça, incluindo a área de usinagem e o tamanho e localização de quaisquer ilhas, são características inerentes à peça que não podem ser alteradas. Estes elementos desempenham um papel crucial na determinação do modo de alimentação da ferramenta e são factores fundamentais a considerar.
Rota do processo
A rota do processo é o método direto para atingir o objetivo da usinagem e serve como principal consideração para a seleção do modo de corte.
Determina a sequência das áreas de processamento, a combinação e separação das ilhas e a divisão entre usinagem de desbaste, semiacabamento e acabamento.
Existem muitos tipos de rotas de processo que podem alcançar o resultado desejado, e a escolha do modo de deslocamento da ferramenta varia de acordo com a rota escolhida.
Material da peça
O material da peça também é um fator que influencia a escolha do modo de deslocamento da ferramenta.
O próprio material da peça é o objeto direto do processamento, mas não afeta diretamente o modo de deslocamento da ferramenta. No entanto, pode impactar a seleção do material da ferramenta, tamanho e modo de processamento, o que por sua vez pode afetar indiretamente o modo de deslocamento da ferramenta.
A forma e o tamanho da peça bruta determinarão a distribuição das tolerâncias de usinagem nas diferentes partes da peça. Além disso, para peças com blanks opcionais, o uso de diferentes tamanhos e formatos de blanks pode alterar o modo de fixação e a distribuição das áreas de usinagem, afetando assim a estratégia de usinagem e levando a diferentes modos de deslocamento da ferramenta.
Método de fixação e fixação da peça de trabalho
O método de fixação e fixação da peça de trabalho também pode afetar indiretamente o modo de deslocamento da ferramenta. Isto inclui a criação de novas “ilhas” devido à placa de prensagem, alterações no modo de deslocamento da ferramenta causadas pelo impacto das forças de fixação nos parâmetros de corte e a influência da vibração no modo de deslocamento da ferramenta.
Seleção de ferramentas de corte
A seleção de ferramentas inclui fatores como material da ferramenta, forma, comprimento e número de dentes.
Esses parâmetros influenciam a área e a frequência de contato entre a ferramenta e a peça, afetando assim o volume de material removido por unidade de tempo e a carga da máquina. Além disso, a resistência ao desgaste e a vida útil da ferramenta determinam o período de tempo em que a ferramenta pode ser usada.
O tamanho ou diâmetro da ferramenta tem impacto direto no modo de alimentação da ferramenta. A escolha de ferramentas com diâmetros diferentes alterará o tamanho da área residual, alterará o caminho de usinagem e resultará em diferentes métodos de deslocamento da ferramenta.
Seleção de domínio de usinagem
No fresamento, quando cavidades planas complexas possuem múltiplas saliências que formam múltiplos contornos internos, ações adicionais de elevação da ferramenta ocorrerão frequentemente durante o corte linear, e o caminho de usinagem se tornará mais longo no corte circular. Estas ações reduzem significativamente a eficiência de corte.
Para minimizar o número dessas ocorrências, a área de corte é dividida em diversas subáreas com base nas necessidades de usinagem. As ações de elevação da ferramenta ocorrem entre estas subáreas. As subáreas podem ser combinadas, divididas ou até mesmo ignoradas, dependendo do modo de deslocamento da ferramenta. Isto ajuda a reduzir o número de ações de elevação da ferramenta e evita que o percurso de usinagem se torne muito longo.
Além disso, ao selecionar o modo de deslocamento da ferramenta mais apropriado para cada subárea, a eficiência da usinagem pode ser melhorada.
3. Seleção razoável do modo de alimentação da ferramenta
Princípio básico de seleção
Dois fatores devem ser levados em consideração na escolha do modo de alimentação da ferramenta: tempo de processamento e uniformidade da tolerância de usinagem.
Em geral, o método de corte circular é preferido por sua margem de usinagem uniforme, que é determinada pelo formato da peça. Por outro lado, o método de corte de linha resulta em margem de usinagem não uniforme. Para obter uniformidade neste caso, o percurso circular da ferramenta de corte deve ser aumentado em torno do limite.
No entanto, ignorando o requisito de uniformidade, o método de corte em linha tem um comprimento de percurso de ferramenta relativamente curto. Por outro lado, aumentar o percurso da ferramenta de corte circular para resolver o problema de não uniformidade pode resultar num tempo total de maquinação mais longo, especialmente para limites longos, como em situações de múltiplas ilhas.
Embora o corte de linha seja mais fácil de calcular e exija menos memória, também envolve mais levantamento de ferramenta. Em contraste, o corte circular requer o deslocamento do limite do anel várias vezes e a remoção dos anéis que se cruzam automaticamente.
Seleção de acordo com características de forma
A forma da peça determina o caminho da ferramenta na usinagem.
Com base na natureza do objeto que está sendo usinado, a peça pode ser amplamente categorizada em dois tipos: cavidades planas e superfícies de forma livre.
As cavidades planas são normalmente usinadas usando corte de linha. Isso ocorre porque a maioria das peças desse tipo são criadas por meio de processos de corte e fresamento, como caixas, bases e outras peças, que possuem grandes tolerâncias de usinagem. O corte linear permite a utilização máxima da velocidade de avanço da máquina-ferramenta, resultando em maior eficiência de usinagem. Além disso, a qualidade da superfície produzida através do corte em linha é melhor do que aquela produzida através do corte em anel.
Por outro lado, superfícies de forma livre são geralmente usinadas usando corte em anel. Isso ocorre porque essas superfícies são em sua maioria fundidas ou moldadas por meio de processos regulares, resultando em distribuição residual desigual e requisitos de alta precisão. Além disso, comparado ao corte em linha, o corte em anel fornece melhores características de usinagem de superfície e pode aproximar melhor o formato real da superfície.
Selecione de acordo com a estratégia de usinagem
A usinagem de peças é normalmente dividida em três etapas: usinagem de desbaste, usinagem de semiacabamento e usinagem de acabamento. Esta divisão é importante para garantir a precisão da usinagem.
Nos métodos de processamento tradicionais, os limites entre cada etapa são claros. No entanto, no fresamento NC, esses limites podem ser menos definidos devido à capacidade da máquina-ferramenta de executar múltiplas funções. Também pode haver sobreposição entre os estágios, como usinagem fina executada durante a usinagem de desbaste ou traços de usinagem de desbaste remanescentes após a usinagem de desbaste.
Apesar disso, ainda é necessário dividir as etapas de usinagem na usinagem NC para garantir a qualidade. Porém, a determinação do conteúdo de usinagem para cada etapa pode diferir dos métodos tradicionais, pois o objetivo é reduzir o tempo de fixação e simplificar a movimentação da ferramenta.
O principal objetivo da usinagem de desbaste é maximizar a taxa de remoção de material e preparar o contorno geométrico da peça para o semiacabamento. Portanto, o corte em linha ou métodos compostos são comumente usados para corte em camadas.
O semiacabamento visa produzir um contorno plano e um acabamento superficial uniforme. Métodos de corte circular são normalmente usados para esta fase.
O objetivo da usinagem de acabamento é produzir uma peça que atenda aos requisitos dimensionais, de precisão de forma e de qualidade de superfície. Com base nas características geométricas da peça, o corte em linha é utilizado para o interior e o corte em anel para as bordas e juntas.
Selecione de acordo com a estratégia de programação
As principais considerações para determinar o modo de alimentação da ferramenta durante a programação são:
- Atendimento aos requisitos de precisão de usinagem e rugosidade superficial das peças;
- Encurtar a rota de processamento para minimizar o tempo ocioso de deslocamento da ferramenta;
- Cálculo numérico simples e redução do número de segmentos do programa para minimizar o esforço de programação.
Para cavidades planas, o corte em linha é usado para dividir o domínio de usinagem e minimizar o número de levantamentos da ferramenta. Por outro lado, as superfícies de forma livre são aproximadas na forma de anéis tangentes.
A seleção do formato do blank também afeta a escolha da programação. Ao modificar o formato da peça bruta, o processamento de formas difíceis de fixar pode ser transformado em processamento de cavidades de corte em linha que é mais fácil de fixar. Alternativamente, a usinagem de superfície de forma livre pode ser alterada para corte linear para remover folgas maiores, melhorando assim a eficiência da usinagem.