Com o desenvolvimento contínuo da tecnologia de corte a plasma, a utilização de máquinas de corte a plasma CNC está se tornando cada vez mais difundida.
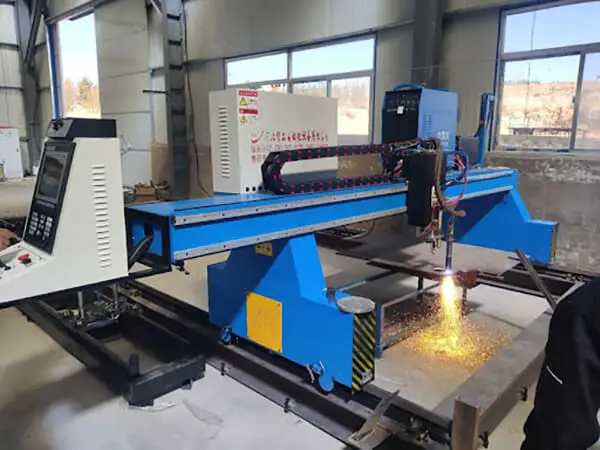
A máquina de corte a plasma CNC é um dos principais equipamentos de corte e estampagem utilizados para chapas de média e pequena espessura. Oferece inúmeros benefícios, como fácil operação, alta precisão, alta eficiência de trabalho e baixa intensidade de trabalho.
Ele é amplamente utilizado em vários setores, incluindo a indústria química, a indústria automobilística, a indústria de máquinas, a indústria de transporte ferroviário, entre outras.
Quando os métodos de corte tradicionais não conseguem cortar materiais resistentes, as máquinas de corte a plasma CNC são úteis.
Em termos de velocidade de corte, ao cortar chapas de aço carbono de média e pequena espessura, a velocidade de corte a plasma CNC é mais rápida do que a velocidade de corte por chama tradicional, e a superfície de corte permanece lisa com mínima deformação a quente.
Além disso, o método de corte a plasma CNC é uma opção mais econômica do que o corte a laser.
Princípio do Corte Plasma
Um cortador de plasma opera ionizando uma mistura de gases através de um arco de alta frequência. Este gás ionizado, ou plasma, é então expelido do bico de corte devido à pressão do gás.
A temperatura do plasma é extremamente alta, excedendo em muito o ponto de fusão do material que está sendo cortado.
Isso faz com que o material derreta rapidamente e o material fundido seja então expelido pelo gás de alta pressão do bocal. Este processo produz uma quantidade significativa de fumaça e escória fundida.
Portanto, os cortadores de plasma requerem sistemas de remoção de poeira e escória. Ao utilizar diferentes misturas de gases, o plasma pode cortar metais de diversos materiais e espessuras, destacando-se principalmente no corte de metais não ferrosos.
Escolhendo o Processo de Corte Plasma
No processo de operação CNC (Controle Numérico Computadorizado) com cortadora a plasma, a programação é o passo inicial. O processo de usinagem segue uma sequência pré-programada.
Nesta fase de programação, fatores como velocidade de corte, sequência de corte e ponto de partida desempenham um papel fundamental na determinação da qualidade do corte.
Seleção do Ponto de Partida
Idealmente, o ponto inicial do corte deve ser na borda da chapa ou dentro de uma costura previamente cortada. Se o bico estiver muito distante do material, resulta em um corte incompleto, levando ao desperdício desnecessário de material.
Por outro lado, se o bico estiver muito próximo, poderá causar um curto-circuito. Isto não só danifica o material e afeta a qualidade do corte, mas também pode danificar o bico.
Escolhendo a direção de corte
A direção do corte deve garantir que a borda final a ser cortada esteja quase toda separada do material principal.
Se ela se soltar prematuramente, a estrutura fina ao redor da peça poderá não suportar a tensão térmica do corte, fazendo com que a peça se desloque durante o processo. Essa mudança pode levar a imprecisões dimensionais, afetando a qualidade do corte.
Selecionando a sequência de corte
Durante a programação, para maximizar a utilização do material, a peça geralmente é aninhada na chapa.
Assim, a sequência de corte dita a ordem de remoção do material. Geralmente, a sequência segue o princípio de cortar peças menores antes das maiores e cortar contornos internos antes dos externos.
Caso contrário, a tensão gerada durante o corte de contornos internos ou peças menores pode levar à concentração de tensão, resultando em uma peça sucateada.
Escolhendo a velocidade de corte
A seleção da velocidade de corte é influenciada por vários fatores, como tipo e espessura do material, design do bico, corrente de corte e gás escolhido.
Entretanto, sob a mesma potência e condições, uma velocidade de corte mais rápida resulta em um chanfro maior na peça de trabalho.
Portanto, o bico deve ficar perpendicular ao material durante o corte para facilitar a rápida remoção da escória. Para garantir eficiência, a velocidade máxima de corte deve ser escolhida sem comprometer a qualidade do corte.
Otimização da Mesa de Corte
A mesa de corte da máquina de corte é sustentada por vários diafragmas. Conforme ilustrado na Figura 1, a distância entre dois diafragmas é de 110 mm.
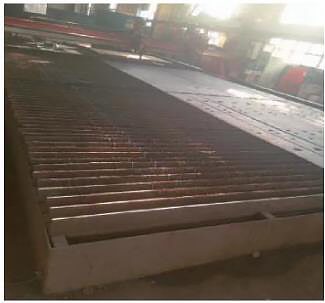
Fig. 1 Máquina de corte a plasma CNC com mesa de corte
Ao cortar peças pequenas, a peça geralmente fica entre os diafragmas, dificultando sua recuperação. O diafragma em si é uma placa de aço plana reta de 8 mm × 190 mm × 4600 mm. Devido aos cortes frequentes, o diafragma inferior acumula uma quantidade significativa de escória de óxido, o que pode impactar negativamente na qualidade do corte. Como resultado, requer limpeza ou substituição frequente para manter as operações normais de corte.
Esquema de Otimização e Implementação da Mesa de Corte
Na indústria, as estruturas e os lotes dos produtos muitas vezes não são fixos, levando ao uso de agrupamento para economizar materiais. Isso envolve combinar a composição tipográfica de materiais grandes e pequenos.
Atualmente, precisamos abordar a questão de como aumentar a taxa de utilização das máquinas de corte a plasma e prolongar a vida útil das bancadas de corte através da inovação do processo de bancada a plasma.
Para enfrentar este desafio, primeiro analisamos e categorizamos os produtos de blanking existentes. Em seguida, selecionamos a menor peça de corte, determinamos seu tamanho e projetamos um novo conjunto de bancada de acordo com as condições do local, conforme demonstrado na Figura 2.
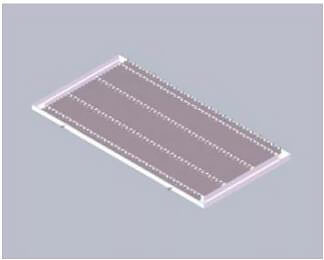
Fig. 2 Modelo de tabela após otimização da máquina de corte a plasma CNC
(1) Regime específico.
- A plataforma tem um tamanho de 1500 mm × 3000 mm e pode ser combinada com múltiplas plataformas.
- A estrutura externa da plataforma é feita de placas de 4 mm que são dobradas em partes em forma de U e soldadas em uma estrutura retangular. Este design garante a rigidez da estrutura e evita deformações durante o içamento.
- Dentro da moldura existem 2-3 peças em forma de V que são dobradas em placas de 4 mm e dobradas longitudinalmente na moldura. Além disso, um entalhe de 3,5 mm de largura é aberto na viga longitudinal para facilitar a inserção do diafragma.
- O diafragma é feito de uma placa de 1500 mm × 200 mm com um lado cortado em uma estrutura serrilhada.
(2) Processo específico de implementação.
- Projete o comprimento, largura, altura e espaçamento das partições da bancada de corte com base nos parâmetros do equipamento e no tamanho das peças de corte necessárias.
- Faça a bancada de corte de acordo com o desenho do projeto.
- Todas as peças da mesa de corte são cortadas de uma só vez usando uma máquina de corte CNC, resultando em tamanhos precisos e substituição conveniente do diafragma.
- A estrutura da mesa de corte é programada e dobrada usando uma dobradeira CNC, resultando em tamanho de posicionamento preciso e boa conformabilidade.
- Monte, solde e construa a estrutura da bancada de corte.
- Insira o diafragma na mesa de corte.
- Coloque a mesa de corte na mesa de corte original. Ao cortar, coloque o material na mesa de corte móvel para corte, conforme mostrado na Figura 3.
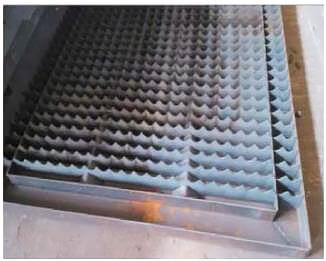
Fig. 3 Desenho físico da mesa de trabalho após otimização da máquina de corte a plasma CNC
Otimização de caminho no processo de corte
Durante o processo de corte, há um movimento relativo entre a peça usinada e o material restante devido ao efeito de expansão térmica e contração a frio da placa.
O movimento relativo pode ser categorizado em três situações com base na diferença entre o peso da peça usinada e o peso do material restante:
- Quando o peso da peça usinada é maior que o peso do material restante, a peça usinada permanece estacionária enquanto o material restante se move em relação à plataforma. Isto não afeta o tamanho da peça usinada.
- Quando o peso da peça usinada é menor que o peso do material restante, a peça usinada se move em relação à plataforma enquanto o material restante permanece estacionário. Isso resulta em um certo desvio na peça usinada.
- Quando o peso da peça usinada é igual ao peso do material restante, tanto a peça usinada quanto o material restante podem se mover em relação à plataforma, o que pode afetar o tamanho da peça usinada.
A prática tem mostrado que o erro dimensional das peças usinadas normalmente varia de 0,3 a 4 mm devido ao movimento relativo da peça usinada ou do material restante em relação à plataforma.
O caminho de corte em um lado da peça de trabalho
A seleção de um processo de corte razoável pode resultar em vários graus de deformação durante o processo de corte a plasma CNC.
Ao cortar a placa mostrada na Figura 4, se o ponto A for escolhido como ponto inicial do arco, a sequência e direção de corte deverão ser: A → D → C → B → A (ver Figura 4a).
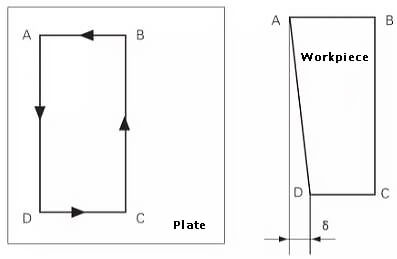
Fig. 4 Trajeto de corte e deformação de um lado da peça de trabalho
Quando a seção AD é cortada e a seção DC é processada, o material residual estreito na seção DC é alongado linearmente devido à alta temperatura durante o corte, fazendo com que a seção CB se desvie para fora.
Após o corte, o tamanho da seção DC é reduzido em δ (como mostrado na Fig. 4b). O valor de δ é proporcional ao tamanho da seção DC.
Se a sequência de corte A → B → C → D → A for selecionada, a peça de trabalho pode ser separada da placa-mãe através de DA, o que pode efetivamente reduzir a deformação de corte.
Controle de deformação de peças delgadas
Ao cortar as peças delgadas mostradas na Figura 5, seguindo a sequência A→B→C→D→A, a expansão da seção BC pode impedir a expansão da seção CD ao cortar a seção DA.
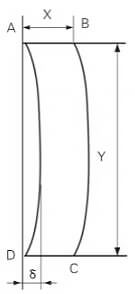
Fig. 5 Corte de peças delgadas
Após o processo de corte e resfriamento, a seção DA deve sofrer mais encolhimento do que a seção BC para dobrar a peça em direção ao lado DA.
A quantidade de flexão lateral δ depende da relação comprimento-largura Y/X da peça usinada. À medida que a relação comprimento-largura aumenta, também aumenta a quantidade de flexão lateral δ.
Ao usar dois pares para corte, conforme mostrado na Figura 6, escolha o ponto A como ponto inicial do arco e siga a direção e sequência de corte: A → B → C → D → E → A → F.
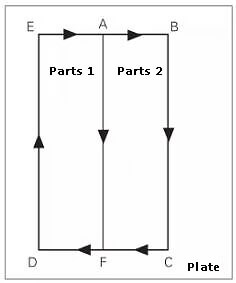
Fig.6 Corte emparelhado de duas peças delgadas
Ao trabalhar na seção DE, removê-la da placa-mãe é comparável a diminuir pela metade a relação comprimento-largura da peça de trabalho, resultando em uma redução na quantidade de flexão lateral.
Ao cortar a seção AF, a expansão e a contração em ambos os lados da peça são uniformes, levando a uma redução considerável na deformação δ das peças delgadas.
Tecnologia de corte de peças com formatos especiais
Para o corte de peças especiais (Fig. 7), os seguintes processos de corte podem ser selecionados de acordo com os métodos de processamento acima e diferentes peças com formatos especiais.
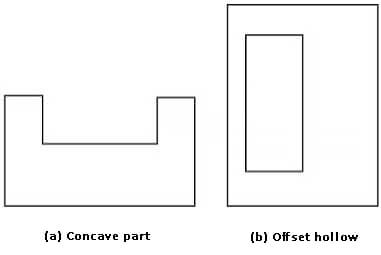
Fig.7 Corte de peças especiais
(1) Para peças côncavas, são adotados dois métodos de corte emparelhados.
Primeiro cortando a borda interna, depois cortando a borda externa e, finalmente, separando as duas partes de fora para dentro.
A sequência de corte é mostrada na Fig.
A borda interna: A1 → B1 → C1 → D1 → A1;
Exterior: A → B → C → D → A e finalmente E → F, H → G.
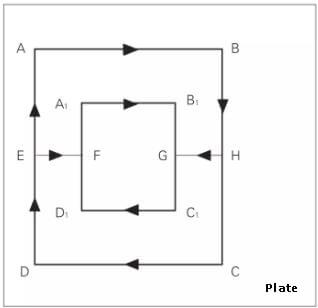
Fig.8 Corte emparelhado de duas partes côncavas
(2) Para peças ocas deslocadas, duas peças devem ser cortadas aos pares e, por fim, as duas peças devem ser separadas.
A sequência de corte é mostrada na Fig.
O lado interno: A1 → B1 → C1 → D1 → A1, A2 → B2 → C2 → D2 → A2
O lado externo: A → B → C → D → A e, finalmente, E → F.
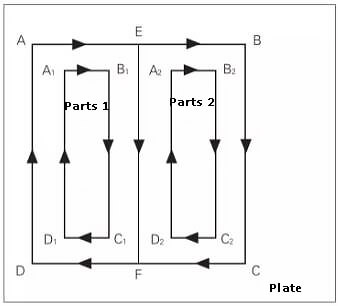
Fig. 9 Corte emparelhado de duas peças ocas deslocadas
Otimização de Equipamentos de Plasma
Durante o processo de corte com plasma de ar, a parte superior do núcleo do eletrodo sofre uma reação de oxidação em alta temperatura com o oxigênio do ar, portanto o desgaste do eletrodo é inevitável.
A vida útil de um eletrodo está relacionada ao número de inícios de arco; nas mesmas condições, quanto mais o arco se inicia, mais o eletrodo se desgasta. O início frequente do arco reduz significativamente a vida útil do eletrodo.
No entanto, o processo de corte contínuo reduz o número de pontos iniciais para peças com arestas não comuns, fazendo com que as peças com arestas compartilhadas tenham apenas um ponto inicial de corte.
Isto reduz o número de inícios de arco durante o corte, aumentando assim a vida útil do eletrodo.
Conclusão
A inovação de processos tem vários efeitos benéficos. Em primeiro lugar, melhora muito a taxa de utilização da máquina de corte a plasma. Em segundo lugar, a substituição do diafragma da mesa de trabalho é conveniente e reduz a taxa de substituição pela metade, reduzindo assim o custo de substituição. Em terceiro lugar, pode atender aos requisitos de corte de peças pequenas.
Atualmente, esta inovação de processo é amplamente utilizada no corte de estruturas metálicas para vagões ferroviários de passageiros. Como cada carro possui muitas peças pequenas que precisam ser cortadas e cegadas, esta inovação melhora a eficiência do trabalho e economiza custos.
Ao utilizar o corte a plasma, os seguintes problemas devem ser considerados: a lei de deformação e a influência do corte de peças em máquinas de corte a plasma CNC devem ser analisadas. Antes do corte, deve-se realizar o tratamento adequado de nivelamento da placa, e a placa deve ser fixada para evitar o movimento das peças usinadas durante o corte.
Ao compilar o programa de corte, um processo de corte razoável deve ser selecionado para separar a superfície de tamanho máximo da peça de trabalho da placa-mãe. Para cortar peças delgadas ou com formatos especiais, métodos de controle, como o corte emparelhado de duas peças, podem prevenir ou reduzir efetivamente a deformação das peças de corte.
Comparado ao corte por chama, o corte a plasma CNC é superior em termos de qualidade de corte e benefícios na indústria de processamento. Pode cortar todos os tipos de metais com diferentes gases de trabalho, especialmente metais não ferrosos.