Abstrato:
As inclusões não metálicas desempenham um papel crucial na determinação de muitas propriedades do aço e têm um impacto significativo no processamento e utilização de produtos siderúrgicos.
Este artigo fornece uma visão geral dos últimos desenvolvimentos na origem e classificação de inclusões não metálicas e resume o trabalho de pesquisa realizado nas últimas décadas.
Ele destaca as condições dinâmicas de formação de inclusões e o efeito das atuais condições de fundição na composição, quantidade e distribuição de tamanho das inclusões.
O estudo da desnaturação por inclusão concentra-se em tipos de aço, como fio de aço radial, aço para molas e aço para rolamentos, para atingir o tamanho e formato desejados das inclusões.
Além disso, devem ser tomadas medidas para evitar o entupimento do bocal de lingotamento contínuo por fluxo floculento.
Com o avanço da microscopia eletrônica, as características de distribuição das inclusões são agora mais claramente compreendidas. O excitante campo da “metalurgia de óxidos” também foi abordado no contexto da engenharia de inclusão.
Por fim, o artigo aborda a melhoria das características de inclusão e os desafios de realizar uma análise quantitativa.
Nas últimas décadas, foram feitos progressos notáveis no controle de inclusões no aço, em grande parte devido a uma compreensão mais profunda da interação entre a termodinâmica, a composição da escória do aço fundido e o processo de fabricação do aço. Isto permite a otimização de inclusões e processos para melhorar as propriedades do aço.
No entanto, ainda existem alguns desafios importantes que precisam de ser enfrentados e o processo de controlo e otimização da inclusão deve ser continuamente melhorado.
1. Introdução
Somente há cinquenta anos é que as pessoas começaram a prestar atenção ao estudo das inclusões não metálicas (NMIs) no aço. Naquela época, acreditava-se que essas inclusões eram resultado da corrosão de materiais refratários e da presença de diversos fluxos de molde e escórias de topo.
Contudo, apesar da sua importância, o estudo das inclusões não era tão amplamente reconhecido como é hoje. Isso ocorreu porque os metalúrgicos físicos geralmente se concentravam no estudo de fases metálicas, em vez de fases não metálicas, como inclusões no aço.
À medida que aumentava a demanda por aço de alto desempenho com condições de serviço severas, a correlação entre o tipo, tamanho e distribuição dos NMIs e o desempenho do aço tornou-se mais aparente. Isso levou a um interesse crescente em estudar a origem, as características e o comportamento das inclusões na fundição e processamento de produtos siderúrgicos.
Desde a década de 1980, foram feitos progressos significativos no controle e na análise quantitativa dos NMIs, e o impacto dessas inclusões nas propriedades do aço tem sido amplamente pesquisado. A engenharia de controle de inclusão tornou-se um aspecto crucial da fundição, com o objetivo de alcançar as características de inclusão desejadas através do projeto de processo adequado e da produção de aço.
Neste artigo, abordamos a origem e o controle dos NMIs, o comportamento das inclusões durante a usinagem, a análise quantitativa e as características de distribuição das inclusões e os mais recentes desenvolvimentos na engenharia de controle de inclusões. No entanto, não nos aprofundamos na influência das inclusões nas propriedades do aço, pois este é um campo extenso e em rápido crescimento.
Para aqueles interessados em explorar mais este tópico, os livros clássicos de Kiessling e as conferências e artigos da Organização Internacional do Aço Limpo, realizados a cada 3-5 anos e patrocinados pela Associação Mineira e Metalúrgica da Hungria, são fontes valiosas de conhecimento.
2. Origem e classificação das inclusões não metálicas
2.1 Classificação de inclusões não metálicas
Com os avanços contínuos na moderna tecnologia siderúrgica, observa-se que reações de oxidação e métodos de refino são empregados para eliminar elementos prejudiciais do aço.
Estas impurezas, como o enxofre do carvão e do coque, podem penetrar no ferro e no aço líquidos, mas a sua solubilidade em soluções sólidas de aço é bastante limitada.
Durante a solidificação, o aço fundido passa da frente de cristalização para o aço líquido, eventualmente formando compostos de baixo ponto de fusão, como “FeO” e “FeS” ou eutéticos que contêm ambos os compostos. Como resultado, este aço é inadequado para processos de trabalho a quente, como laminação e forjamento.
Os óxidos, sulfetos e elementos de liga (como Mn) no aço exibem uma relação complexa. Contudo, para produzir aço de alta qualidade, o teor de oxigênio e enxofre dissolvido no aço fundido deve ser reduzido.
Elementos como Mn, Al, Si podem ser utilizados como elementos de liga no aço, pois possuem alta afinidade com o oxigênio e podem ser desoxidados no aço fundido. Esses elementos desoxidados tornam-se inclusões não metálicas de óxido.
Por outro lado, o aço contém enxofre e a solubilidade de Ca e Mg no aço é mínima. Sua afinidade com terras raras e S é alta o suficiente para formar inclusões de sulfetos não metálicos com baixo ponto de fusão.
Como resultado, a maior parte do enxofre do aço é eliminada por meio do refino e entra na escória, enquanto o enxofre restante precipita inclusões de sulfetos durante a solidificação.
Essas inclusões não metálicas podem ser classificadas em duas categorias com base no seu tipo: a composição química das inclusões (como inclusões de óxido e sulfeto) e o estágio de formação da inclusão.
A solidificação marca o ponto limite na fase de formação de inclusões. As inclusões formadas antes da solidificação são conhecidas como inclusões primárias, enquanto aquelas formadas durante e após a solidificação são chamadas de inclusões secundárias.
Além dessas classificações, outras categorizações comumente utilizadas também podem ser confusas, como a origem das inclusões. As inclusões formadas durante o processo de fabricação do aço (como inclusões de óxido e sulfeto) são classificadas como inclusões “endógenas”, enquanto aquelas originadas de fontes externas (como cavacos refratários e pó de molde) são chamadas de inclusões “exógenas”.
Em geral, existem apenas algumas inclusões exógenas de partículas grandes que permanecem independentes do aço fundido por um longo período de tempo e não reagem com ele. Isto mudou em relação ao passado, quando se acreditava que tais grandes inclusões de partículas provinham do refratário e do molde de fundição. No entanto, no aço moderno, estas grandes inclusões de partículas foram significativamente reduzidas.
Alguns estudantes podem acreditar erroneamente que as inclusões exógenas são as inclusões não metálicas mais importantes, mas isso não significa que a interação entre o aço fundido e o refratário seja insignificante. A presença destas inclusões no aço indica que o aço fundido e o refratário têm impacto. Se a definição de inclusões exógenas for expandida para incluir a oxidação secundária e o envolvimento de pó de mofo, fornecerá uma definição mais apropriada de inclusões exógenas.
Porém, ainda há debate sobre a classificação dessas inclusões, pois elas podem mudar durante o processo de fundição e nem sempre é claro qual processo está envolvido.
Finalmente, um método comum de classificação de inclusões não metálicas é baseado no seu tamanho, dividindo-as em macro inclusões e micro inclusões. A classificação proposta por Kiessling é frequentemente utilizada, onde inclusões que causam danos instantâneos aos produtos siderúrgicos durante o processamento ou uso são consideradas macroinclusões.
Deve-se notar que a classificação do tamanho das inclusões é subjetiva e é difícil definir aleatoriamente as inclusões em macro e micro com base no tamanho.
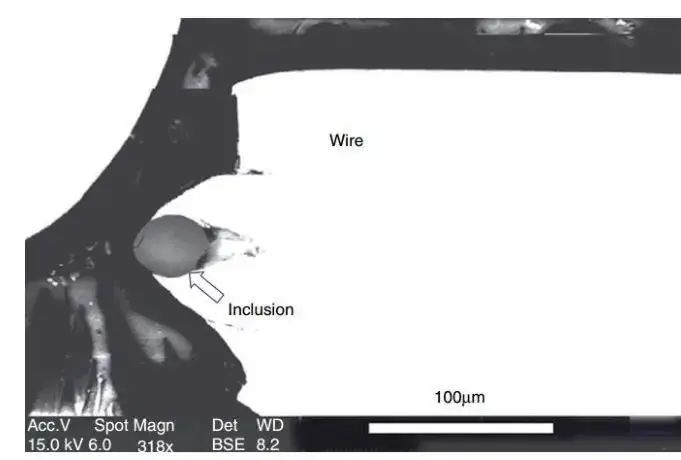
Fig. 1 Fratura do fio radial do pneu durante a trefilação devido à existência de grandes partículas na fase dura.
A inclusão é indicada por uma seta, e a foto foi tirada usando a técnica de retroespalhamento de microscópio eletrônico de varredura.
2.2 Base Termodinâmica
A alta temperatura durante a fabricação do aço aproxima a reação de formação de inclusões do estado de equilíbrio. Como resultado, a termodinâmica tornou-se uma ferramenta crucial para a compreensão das inclusões.
Durante muito tempo, a base termodinâmica da formação da inclusão tem sido foco de pesquisa. No entanto, os dados de formação termodinâmica relacionados às inclusões no óxido de alumínio permanecem inconsistentes e contraditórios, tornando-se uma área que merece um estudo mais aprofundado.
O alumínio é comumente usado como desoxidante na produção de aço, e o cálculo termodinâmico das inclusões geradas durante o processo não é problemático. No entanto, o processo de fundição de materiais de aço de nova geração com alto teor de alumínio e manganês introduz incerteza.
A situação torna-se mais complexa quando a dissolução de Mg e Ca no aço é extremamente limitada. Apesar disso, os dados termodinâmicos relacionados a estes elementos ainda são amplamente estudados no processo siderúrgico.
Nas últimas décadas, o cálculo termodinâmico tem sido aplicado para resolver problemas complexos na produção e fundição de ferro e aço. No entanto, os métodos de cálculo convencionais ainda lutam para resolver estas questões.
Muitas literaturas têm discutido a aplicação do cálculo termodinâmico em vários aspectos da produção e fundição de ferro e aço, bem como problemas de inclusão relacionados.
3. Formação, remoção e controle de inclusões
Classificar as inclusões em primárias e secundárias pode ser útil na discussão de sua formação e remoção. Em princípio, é possível eliminar inclusões primárias no aço.
Contudo, inclusões secundárias se formam durante a solidificação e não podem ser removidas. O melhor que pode ser feito é modificá-los para minimizar o seu impacto negativo no aço.
3.1 Inclusões primárias
3.1.1 Nucleação e estrutura das inclusões
Partindo da perspectiva de que as inclusões primárias formadas no aço líquido estão intimamente ligadas ao processo termodinâmico, dois aspectos fundamentais são levados em consideração: a sua nucleação e as estruturas que dela resultam.
Em geral, quando um desoxidante é adicionado ao aço fundido, ele irá nuclear rapidamente. Isto ocorre porque é observada alta supersaturação durante a adição e dissolução do desoxidante. Sigworth e Elliott conduziram uma avaliação completa das condições de nucleação de silício e descobriram que o oxigênio dissolvido supersaturado é um requisito.
No entanto, a pesquisa e as observações industriais de Miyashita não demonstraram uma supersaturação clara durante a desoxidação do silício na produção de aço. Miyashita também comparou o oxigênio dissolvido e o oxigênio total e descobriu que a taxa de redução do oxigênio total é determinada pela taxa de remoção de produtos desoxidados, conforme ilustrado na Figura 2.
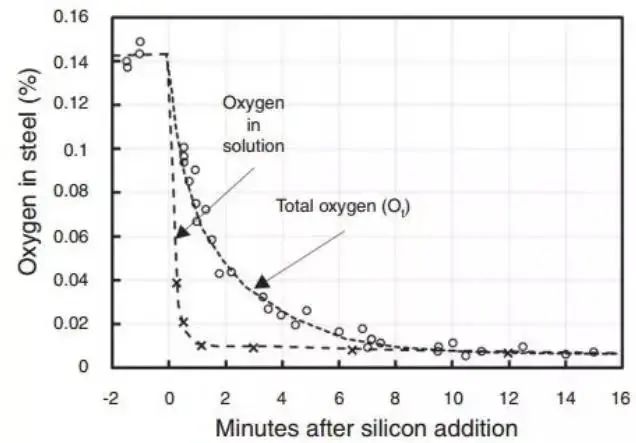
Fig. 2 O oxigênio total e o oxigênio dissolvido no aço após a desoxidação do silício no banho fundido são medidos em função do tempo.
Em muitos estudos sobre desoxidação, a diferença entre o teor de oxigênio total e o teor de oxigênio dissolvido no aço depende da quantidade de inclusões de óxido geradas. Esta conclusão chave é demonstrada na Figura 3.
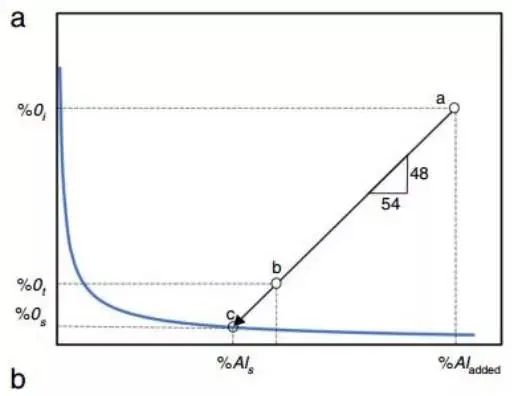
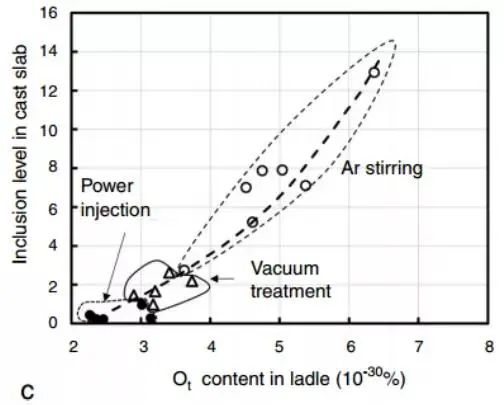
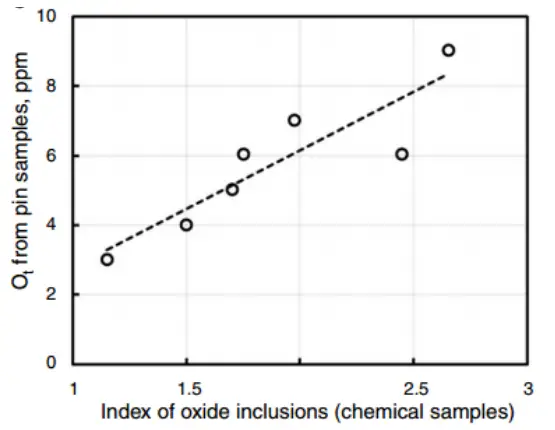
Figura 3
Esta é uma ilustração básica de como o oxigênio total e o oxigênio dissolvido no aço são afetados pela quantidade de inclusões de óxido.
No exemplo, a desoxidação começa no ponto “a” e o alumínio é adicionado ao aço, começando com uma certa porcentagem de oxigênio dissolvido, Oeu.
Sem condições de nucleação no limite de nucleação, o óxido de alumínio se forma no ponto onde o oxigênio dissolvido e o teor de alumínio atingem o ponto “c”.
O teor total de alumínio no aço corresponde ao oxigênio dissolvido (O%) no aço. O oxigênio que entra na inclusão de óxido de alumínio permanece no aço fundido e corresponde ao ponto “b”.
O processo de desoxidação do ponto “a” ao ponto “c” reage 2Al+3O=Al2Ó3 de acordo com a equação química.
Nota: Geralmente, a diferença entre alumínio completo e alumínio solúvel em ácido (% Alé) é pequeno e difícil de medir.
A relação entre o teor de inclusão e o teor de oxigênio total (%Ot) no aço é estabelecida através da literatura. A baixa inclusão e o teor total de oxigênio requerem medição cuidadosa, conforme ilustrado na Fig.
A análise de oxigênio total envolve determinar a densidade das inclusões de óxido na amostra de análise química e contá-las usando SEM (Microscopia Eletrônica de Varredura).
Suitu e colegas estudaram a formação de inclusões de alumina em uma investigação laboratorial de oxigênio supersaturado.
O uso do Si (silício) como desoxidante não apresenta problemas na siderurgia. No entanto, nas operações reais de fundição, a nucleação heterogênea é abundante e as condições observadas em laboratório não podem ser replicadas em locais de produção industrial.
A microestrutura do óxido de alumínio como núcleo de inclusão e seu crescimento no aço é importante para estudar. É por isso que o aço silenciado com alumínio é crucial para a produção industrial em grande escala.
Vários autores investigaram detalhadamente a microestrutura do óxido de alumínio, sua relação com o oxigênio supersaturado no aço e o impacto do tempo de fundição.
A Figura 4, apresentada por Steinmetz e seus colaboradores, mostra a forma de inclusão correspondente à típica atividade desoxidante e de oxigênio. A figura sugere que o oxigênio dissolvido supersaturado desempenha um papel crucial na morfologia da estrutura de inclusão.
Recentemente, Tiekink e colaboradores tentaram observar a relação funcional entre a estrutura de inclusão de óxido de alumínio, oxigênio supersaturado e composição de alumínio, como mostrado na Fig. 5. Este esforço é bastante complicado.
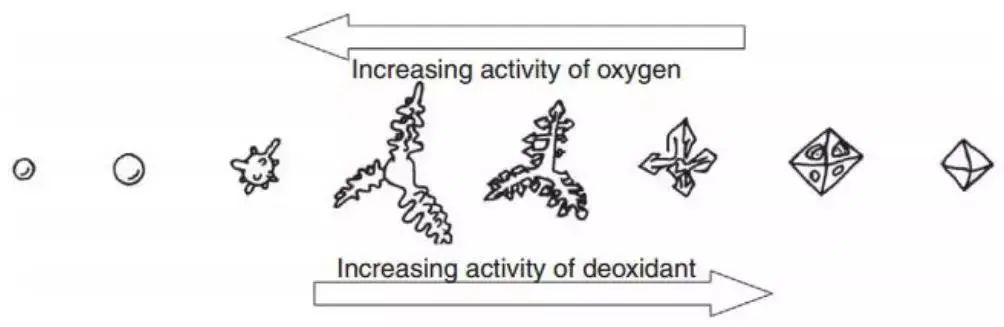
Fig. 4 Relação funcional entre atividade regional de oxigênio, atividade de alumínio e crescimento de óxido
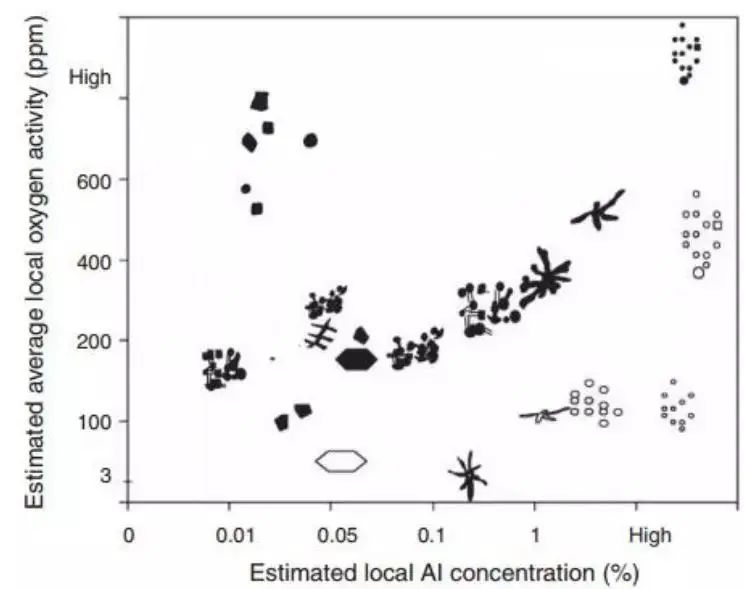
Fig. 5 Visão geral da morfologia das inclusões de alumina correspondentes a diferentes atividades de oxigênio e teor de Al no aço
A estrutura das inclusões de óxido tem um impacto importante nas propriedades do produto final. É importante notar que as inclusões formadas e cultivadas nos estágios iniciais do aço líquido possuem estruturas morfológicas distintas, conforme mostrado nas Figuras 4 e 6, devido ao efeito das inclusões umas sobre as outras (conforme ilustrado na Figura 7). Se o tempo de refinação for prolongado, a forma da inclusão mudará como resultado da energia superficial.
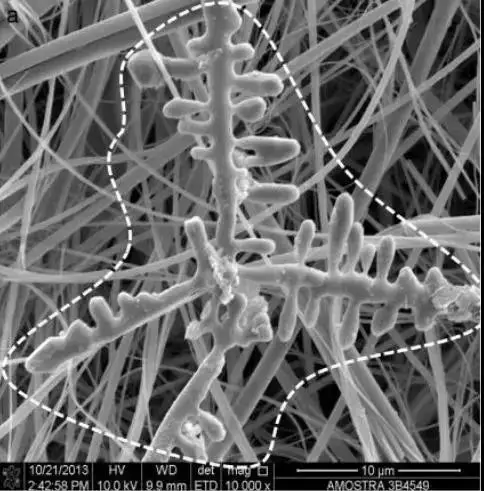
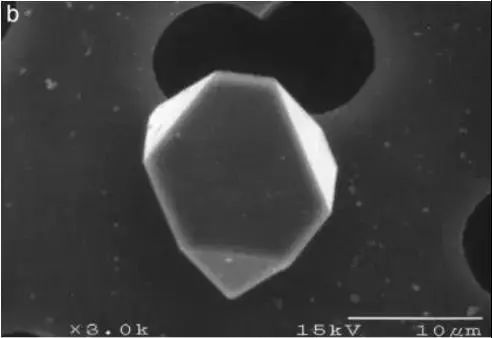
Fig. 6 Estrutura de algumas inclusões de alumina.
As inclusões extraídas da matriz do tarugo fundido são dissolvidas. A estrutura da árvore de óxido de alumínio é representada pela linha pontilhada a. Um elemento filtrante fibroso é utilizado para reter as inclusões durante o processo de dissolução e atua como pano de fundo para as inclusões.
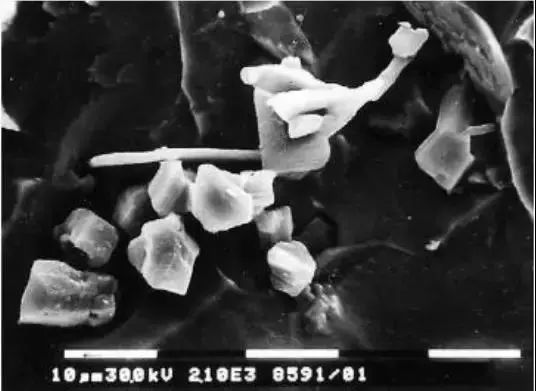
Fig. 7 Aglomerado de alumina amostrado em concha, profundamente corroído com ácido pícrico
3.1.2 Remoção de inclusões
A flotação de inclusões não metálicas em um banho estático de aço fundido pode ser calculada usando um método simples baseado nas limitações da lei de Stokes. Em profundidades normais da panela, a taxa de flutuação para pequenas inclusões de partículas é restrita e leva um tempo considerável para que elas alcancem a superfície da escória de aço. Este tempo de flutuação prolongado não é viável, especialmente para inclusões de óxido de alumínio. No entanto, a polimerização por impacto entre as inclusões ajuda-as a flutuar, tornando crítica a sua polimerização por agrupamento.
A importância desta agregação ascendente foi observada online por Emi e seus colegas. Eles observaram o comportamento das inclusões na interface entre o aço e o gás e descobriram que a aglomeração do óxido de alumínio ocorre rapidamente nessas condições. Por outro lado, as inclusões de aluminato de cálcio são difíceis de agregar e a colisão completa ocorre apenas no líquido.
Wikstrom e seus colaboradores expandiram a observação on-line da superfície da escória de aciaria e das inclusões na escória e confirmaram as descobertas de Emi na interface da escória de aciaria. Emi e seus colegas também notaram que quando o fenômeno ocorre na interface gás-aço, como na superfície das bolhas, não indica diretamente como o aço líquido se agrupa em aglomerados, o que é particularmente significativo para inclusões líquidas. Outras forças podem ser relevantes neste caso.
Independentemente de a inclusão ser sólida ou líquida, ela desempenha um papel crucial na polimerização agrupada. Durante muito tempo acreditou-se que a agitação promovia a aglomeração das inclusões, mas o fator mais importante para as inclusões é submergi-las na escória de refino e no refratário da parede da panela. Lindskog e seus colaboradores usaram traçador radioativo para testar e rastrear essa inclusão crucial na escória de refino e na parede da panela.
Devido às limitações atuais, o BaO é o único traçador adequado que pode ser usado para avaliar a escória de refino capturada final e o fluxo do molde no aço e seu impacto na limpeza do aço. O uso de traçadores de BaO é altamente eficaz na determinação do efeito da corrosão refratária da panela na limpeza do aço com número térmico.
O IRSID desenvolveu o uso do elemento lantânio como marcador de inclusões de óxidos. La2Ó3 é muito estável e quando adicionado ao aço, as inclusões de alumina já existentes podem ser identificadas pelo lantânio. Inclusões exógenas, originárias do fluxo de molde, podem ser rastreadas usando óxidos alcalinos. O fluxo de molde é normalmente usado apenas no processo de fundição contínua e contém óxidos alcalinos perceptíveis.
A maioria das inclusões removidas durante o período de refino em panela são produtos desoxidados e passam por três estágios: produção/agrupamento de inclusões separadas, movimento em direção à escória de refino ou parede refratária da panela e absorção pela escória de refino e refratário. O movimento das inclusões tem dois fatores cruciais: a agitação da poça de fusão e o movimento das bolhas ascendentes.
A maioria dos resultados de refino de panela mostram que o tamanho das bolhas de agitação de argônio na panela é muito grande para remover efetivamente as inclusões e reduzi-las no aço, a menos que uma grande quantidade de argônio seja usada. No entanto, os cálculos de Zhang e Taniguchi indicam que a agitação do argônio é eficaz quando a velocidade do fluxo do aço fundido é alta e as bolhas são pequenas.
O bico submerso SEN e o bico longo da concha de fundição contínua têm um efeito notável na prevenção da oxidação secundária, e algumas vantagens também foram observadas no fluxo de aço do riser de tratamento a vácuo RH. A agitação da concha promove a inclusão para flutuar na escória em aglomerados. A pesquisa mostrou que aumentar o poder de agitação (usando agitação eletromagnética) significa aumentar a constante de energia cinética para remover a inclusão (medida pelo teor total de oxigênio no aço).
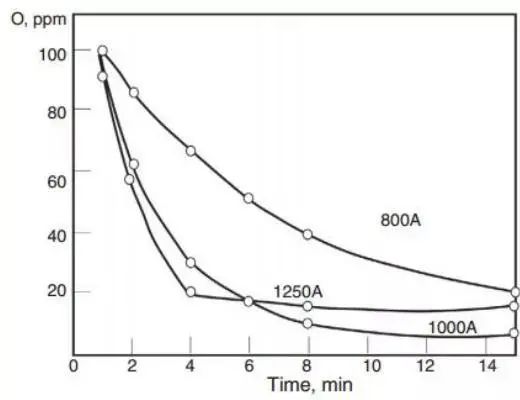
Fig. 8 O conteúdo total de oxigênio no forno panela de refino ASEA-SKF é uma função da corrente de agitação e do tempo de processamento.
O teor final de oxigênio é determinado pelo teor residual de alumínio em cada forno.
Observações industriais sugerem que a remoção de inclusão atingirá seu valor máximo em uma energia de mistura específica.
Suzuki e sua equipe foram os primeiros a relatar esta observação.
Suas descobertas são apresentadas em função do trabalho específico da mistura de energia, destacando a importância da mistura de energia. A redução na eficácia do refino para remover inclusões é provavelmente devido à adição de refratário ao aço após a corrosão, ou ao envolvimento do aço com escória, à medida que as inclusões do tipo CaO e MgO aumentam sob forte agitação. Esses resultados são ilustrados na Figura 9.
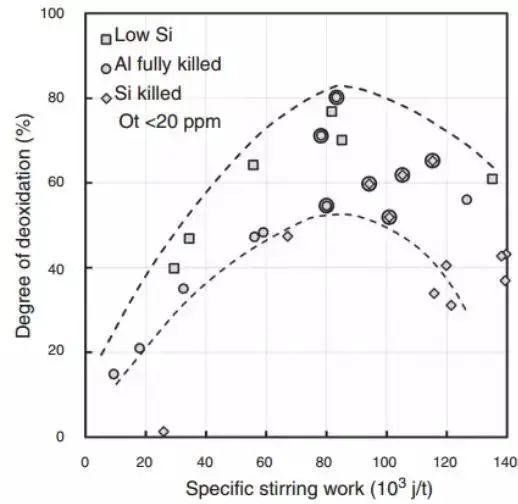
Fig. 9 A influência da potência de mistura no grau de oxidação secundária. O ponto do círculo atingiu abaixo de 20 ppm de conteúdo total de oxigênio
Mais tarde, Neifer e sua equipe, juntamente com Ek e sua equipe, usaram dinâmica de fluidos computacional e modelos físicos para investigar a remoção de inclusões de óxido. A relação entre a vazão de argônio na panela e a remoção da inclusão foi tratada como uma relação funcional.
Os resultados do modelo de Neifer indicaram que a eficiência de remoção de inclusões metálicas foi melhorada através da otimização do fluxo de gás. No entanto, observaram que o aumento da vazão do gás não teve efeito na redução do teor total de oxigênio no aço, o que atribuíram à oxidação secundária do aço fundido em contato com a atmosfera. Estas conclusões estão alinhadas com as descobertas da equipe Suzuki.
A equipe Ek descobriu que a influência da vazão de argônio na remoção de inclusões era bastante baixa e sugeriu o uso de uma vazão mais baixa para remover inclusões e limpar o aço fundido. No entanto, as medições industriais da equipe Neifer indicaram que o teor total de oxigênio no aço diminuiu com o aumento do fluxo de gás. Eles recomendaram o uso de transporte por convecção natural em experimentos industriais para obter resultados ideais. No entanto, devido aos dados de medição limitados em testes de panela em campo industrial, é um desafio tirar conclusões definitivas.
Recentemente, Zhang e Thomas coletaram muitas constantes cinéticas para uso na relação funcional entre remoção de inclusão de óxido e poder de agitação, conforme mostrado na Figura 10. Eles reuniram dados de medição e tentaram determinar o esquema de mistura ideal. Eles também realizaram simulações numéricas para reproduzir os dados de comportamento esperados da parte circundante na Figura 10.
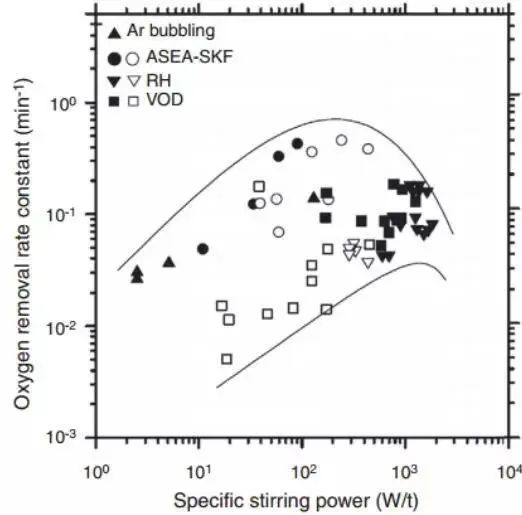
Fig. 10 A constante de remoção de oxigênio é uma função da potência de agitação em diferentes vasos de reação metalúrgica secundária na fórmula d% Ot/dt=- kt
A equipe Suzuki destacou que otimizar o processo de mistura pode resultar em oxidação secundária. A mistura excessiva pode levar à abertura de escória no topo da panela, expondo o aço fundido à atmosfera e causando revestimento de escória na borda da abertura.
A Figura 11 ilustra a alteração da composição química das inclusões não metálicas durante o processo de dessulfuração com forte agitação. A presença de Ca e Mg nas inclusões confirma que a escória foi emulsionada.
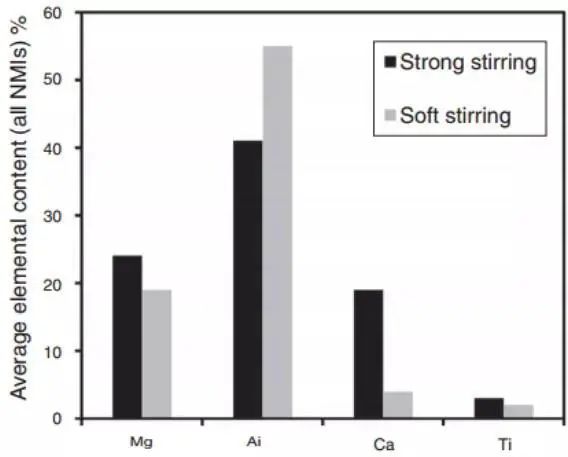
Fig. 11 A relação entre a composição média de todas as inclusões não metálicas e a intensidade de agitação foi analisada por amostragem do forno de refino, cristalizador e placa.
A equipe de Kaushik descobriu que a agitação forte aumenta a emulsificação da escória durante a dessulfurização. A prova estava no alto teor de cálcio nas inclusões. No caso de agitação excessiva de argônio e baixa escória, as inclusões de óxido de alumínio são regeneradas. Portanto, é crucial otimizar o poder de agitação para eliminar inclusões durante o refino de aço fundido limpo.
A importância da oxidação secundária para a limpeza do aço não pode ser exagerada. A equipe de Nadif relatou a importância de controlar a oxidação secundária. As siderúrgicas tomaram várias medidas nas últimas décadas para regular a oxidação secundária após o refino.
O bico submerso SEN e o bico panela são comumente usados para isolar a atmosfera no lingotamento contínuo de placas. Na produção de produtos longos, o distribuidor e o cristalizador são protegidos por gás inerte, que se tornou a norma para a produção de aços de alta qualidade.
Deve-se dar atenção especial ao projeto da válvula de gás inerte para evitar a entrada de ar causada por pressão negativa no sistema de válvula. A contribuição da tensão superficial das inclusões ligadas à escória de refino é a mais alta, seguida pela capacidade da escória de dissolver inclusões.
Independentemente da composição da escória, a maior parte da escória de refino e das inclusões são úmidas devido à diferença de energia superficial entre as inclusões e o aço fundido, e as inclusões e a escória de refino. Este fenômeno tem sido discutido há muitos anos e resumido por Olette. A fração líquida na escória de refino promove a remoção de inclusões não metálicas, o que era conhecido na literatura antiga e confirmado por experimentos.
No entanto, ainda existem algumas inconsistências na viscosidade da escória. Nakajima e Okamura propuseram um modelo para explicar o processo de inclusões que passam pela interface aciaria-escória. Posteriormente, muitos estudos discutiram mais a fundo o tema da absorção de inclusão pela escória. Nakajima e Okamura sugeriram que, sob certas condições, as inclusões entram na escória do aço, que pode incluir um filme metálico da interface como um canal, enquanto em outros casos, especialmente com inclusões sólidas, tal filme metálico não existe, como mostrado na Fig. .
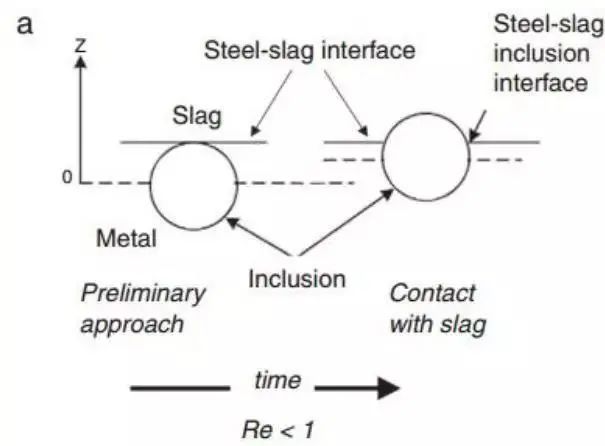
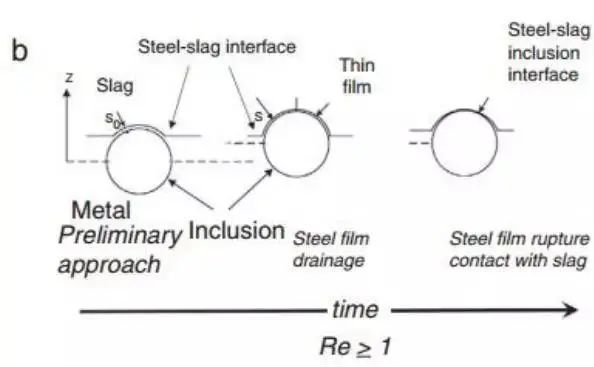
A Figura 12 mostra dois tipos de inclusões atravessando a interface da escória de aciaria, introduzidas a partir de Nakajima. O número de Reynolds de inclusões que atingem a interface determina seu comportamento
A conclusão da equipe de Sridhar é que a viscosidade da escória e a energia superficial associada são fatores cruciais para determinar a passagem das inclusões através da interface e reduzir a probabilidade de elas retornarem ao aço fundido. Isto é resumido pelo número de Reynolds quando a inclusão está próxima da interface.
Recentemente, a equipe observou o canal de fluxo desse filme online, o que é uma ocorrência comum. Na maioria dos casos, o caminho da inclusão na escória é estendido. Ao sair do aço fundido, a inclusão líquida é imediatamente dissolvida na escória.
Ao observar online, a termodinâmica da dissolução da inclusão sólida pode ser estudada experimentalmente. Em alguns casos, a dissolução é controlada pelo transporte (difusão na camada limite), enquanto em outros, como a inclusão de MgO, a formação da camada intermediária depende da composição química da escória e pode dificultar a dissolução em diversas etapas químicas do refino. Isto foi confirmado pelos resultados obtidos de métodos técnicos comuns anteriores.
Recentemente, a equipe Yan estimou a dissolução do MgO na escória e descobriu que todos os dados eram controlados pela transmissão de qualidade.
A equipe da Holappa estudou a atividade do agente de cobertura do distribuidor, que é crucial na absorção de inclusões. Eles observaram uma interação complexa entre a composição química, condições termodinâmicas, tensão superficial e viscosidade da escória quando inclusões sólidas não metálicas são dissolvidas. A equipe concluiu que são necessárias mais pesquisas sistemáticas para obter uma compreensão mais profunda deste campo e desenvolver métodos de otimização.
É bom que inclusões não metálicas sejam adsorvidas na superfície refratária da panela, mas essas inclusões também podem se tornar fonte de inclusões no próximo forno, dependendo da composição da escória da panela.
Se as inclusões forem adsorvidas no canal da tubulação de aço fundido, isso poderá causar problemas significativos, como longo tempo de tratamento e alto custo devido ao bloqueio do bico no processo de lingotamento contínuo. Este fenómeno de entupimento do bocal está bem descrito nas referências.
Nota-se que o fluxo floculento no bocal é causado pela adesão e acúmulo de inclusões de óxido de alumínio e FeO, que podem se formar na oxidação secundária. Este fenômeno está claramente descrito nas referências.
Existe uma vasta literatura sobre a absorção de inclusões primárias pelo pó do molde durante o lingotamento contínuo e o lingote. O consenso entre essas fontes é que esse fenômeno é realmente possível.
O fluxo de molde utilizado na fundição contínua e na fundição de moldes (que é semelhante ao agente de cobertura do distribuidor) deve ter múltiplas funções e possuir fluidez. No entanto, está sujeito a várias restrições dentro do molde, tais como evitar a inclusão do fluxo do molde na superfície do invólucro verde primário. Isto, até certo ponto, restringe o movimento das inclusões e as mantém dentro do fluxo do molde. Ao mesmo tempo, otimiza o fluxo do aço fundido no distribuidor e no molde, permitindo que o aço fundido alcance a interface da escória com as inclusões. No entanto, isto cria objetivos conflitantes com outras metas metalúrgicas relevantes.
A melhor forma de remover inclusões causadas pela convecção é através do refino em panela, e também é crucial evitar que a oxidação secundária crie novas inclusões, que é um aspecto crucial na produção de aço limpo.
Outra questão é a movimentação de inclusões primárias na laje de lingotamento contínuo. Tem sido amplamente reconhecido que as inclusões são distribuídas assimetricamente na seção transversal devido ao processo de fundição contínua por arco. Esta assimetria está frequentemente relacionada com o entupimento do fluxo de flocos no bocal.
Sichen demonstrou recentemente o impacto do modelo de refino secundário, particularmente o processo do forno de refino. O modelo busca explicar a reação de interface da escória de aciaria, a abertura da camada de transição de escória, a geração, nucleação, crescimento, separação e remoção de inclusões por flutuação, utilizando a maioria das tecnologias disponíveis.
No entanto, Sichen destacou que as principais variáveis no processo de refino em panela, como eficiência de transferência de massa, taxa de remoção flutuante de inclusão, abertura da camada de escória com agitação excessiva e vazão de argônio, são difíceis de simular devido às incertezas na indústria. produção, como o tampão de ventilação da panela e vazamento no gasoduto.
É um desafio controlar e detectar a velocidade do fluxo de argônio no refino industrial. A tecnologia de câmera e analisador de imagem pode ser usada para monitorar a abertura da camada de escória da panela, enquanto a medição de vibração pode ser usada para controlar o fluxo de argônio. Essas tecnologias já foram adotadas por algumas siderúrgicas.
3.2 Inclusões secundárias
Durante a solidificação, a força motriz da precipitação de inclusão secundária aumenta a segregação dos elementos do soluto, e a solubilidade dos óxidos e sulfetos no aço diminui à medida que a temperatura cai.
O fenômeno da precipitação de inclusão devido a alterações na solubilidade do aço tem sido tema de discussão há algum tempo.
Desde a década de 1960, os termos “inclusões primárias” e “inclusões secundárias” foram estabelecidos e a relação entre segregação e precipitação de inclusões foi definida.
Naquela época, foi introduzido o primeiro modelo explicando esse processo.
Turkdogan e Flemings deram uma contribuição significativa para a nossa compreensão do impacto geral das mudanças de solubilidade com a diminuição da temperatura na segregação da inclusão secundária.
Durante as décadas de 1980 e 1990, a Nippon Steel e o IRSID desenvolveram modelos avançados, que foram posteriormente aplicados à precipitação de nitreto em aço microligado HSLA durante a solidificação.
Esses modelos abriram caminho para o estudo da engenharia de inclusão.
Hoje sabemos que combinando uma base de dados termodinâmica e uma base de dados cinética podemos simular a solidificação e calcular a formação de inclusões.
Esses cálculos começam com a composição química desejada do aço, prevêem a precipitação de inclusões e orientam o projeto da composição da escória de refino durante o refino em panela para produzir aço limpo.
A interação entre aço líquido, dendritos e inclusões formadas na frente da solidificação é uma importante área de estudo.
Observações em linha indicam que as condições de solidificação desempenham um papel crucial na formação de inclusões que são empurradas para a fase líquida na interface e engolfadas pelas inclusões.
Em teoria, estes resultados podem ser calculados e ajustados para levar em conta os efeitos da tensão superficial e da densidade.
O foco da pesquisa teórica está principalmente na composição das matrizes metálicas, e as descobertas relativas às inclusões não metálicas no aço também estão mais alinhadas com as condições reais.
Os resultados indicam que a velocidade crítica de crescimento (V) pode ser representada como V = k/R, onde R é o raio de engolfamento e repulsão da interface de inclusão, e k depende do tipo de inclusão.
A estrutura das inclusões secundárias é significativamente impactada pelas reações que ocorrem durante a precipitação, sendo a precipitação de carbonetos um dos melhores exemplos.
Desde que Sims observou pela primeira vez o impacto da reoxidação na estrutura do sulfeto em 1930, ele propôs mais tarde três tipos distintos de sulfetos, que foram minuciosamente descritos por vários autores.
Recentemente, a equipe de Ishida destacou que, além do tipo de reação que acompanha a formação do sulfeto, a tensão superficial também desempenha um papel crucial na formação da estrutura do sulfeto.
4. Tratamento de desnaturação de inclusão
A equipe de Gaye apresentou a explicação mais abrangente e perspicaz da aplicação termodinâmica da engenharia de inclusão no aço.
A Figura 13 fornece uma ilustração concisa em dois diagramas de fases ternárias adiabáticas.
Uma vez identificadas as inclusões necessárias, a composição química do aço que irá produzir essas inclusões pode ser determinada.
A composição da escória de refino utilizada para o refino pode então ser calculada com base na composição química do aço através de um balanço de escória de aciaria.
O ditado “O aço só pode ser feito após a fundição da escória” é bem fundamentado e tem sido aplicado com sucesso na produção de vários tipos de aço.
Na produção de aço, é importante evitar inclusões compostas de óxido de alumínio de fase dura (como espinélio).
Por exemplo, na produção de aço para rolamentos, a inclusão atua como núcleo de nucleação durante a transformação de fase que ocorre durante o resfriamento.
O tratamento com cálcio transforma as inclusões em inclusões líquidas e, juntamente com o cálcio, modifica os sulfetos para evitar o entupimento dos bicos.
Embora o processo de modificação da inclusão possa parecer simples, é também um tópico de discussão neste capítulo.
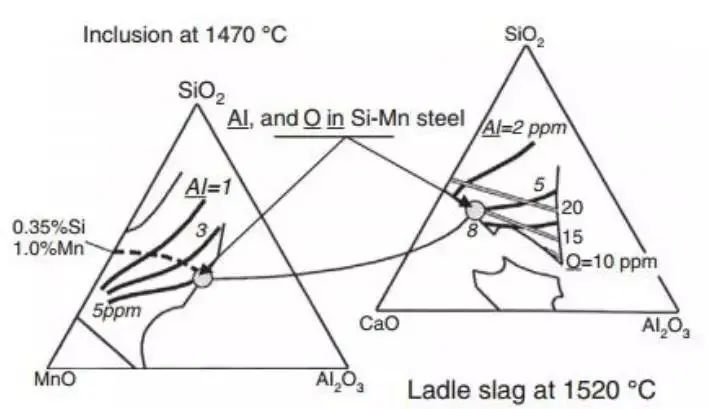
A Figura 13 mostra o processo de transformação das inclusões. Do ponto de vista termodinâmico, Al de baixo ponto de fusão2Ó3 espera-se que inclusões sejam obtidas em aço temperado com Si Mn.
As inclusões esperadas são mostradas no diagrama de fases simplificado de MnO-SiO2-Al2Ó3 sistema ternário.
O diagrama à esquerda mostra o sistema na isoterma de 1470 ℃. A região é indicada como fase 100% líquida, confinada na linha fina, conforme ilustrado na figura.
A isopleta sólida e espessa na temperatura especificada representa o teor de alumínio no aço fundido com inclusões líquidas em equilíbrio. A linha pontilhada, por outro lado, indica a composição química das inclusões no aço 0,35% Si, 1% Mn em uma determinada temperatura, variando com o teor de alumínio do tipo de aço.
Conforme diagrama, se desejar ter inclusões líquidas, o teor de alumínio do aço não deve ultrapassar o círculo cinza (8ppm).
A figura à direita mostra a escória simplificada de refino em panela de CaO-SiO2-Al2Ó3 sistema.
A isoterma de 1520 ℃ representa as condições no forno panela de refino e mostra que a região de inclusão de 100% de líquido está confinada à linha sólida fina.
Na temperatura escolhida, a linha grossa representa o teor de alumínio do aço em estado de equilíbrio dentro do sistema de escória. A linha cinza exibe o teor de oxigênio correspondente no aço sob exame.
Se forem desejadas inclusões líquidas (no lado esquerdo do diagrama), a composição da escória de refino deve ser escolhida conforme indicado no diagrama para garantir que o teor de alumínio no aço seja inferior a 8 ppm.
4.1 Arame e mola de aço do pneu radial
O fio de aço radial do pneu é feito de aço com alto teor de carbono que é desoxidado com silício-manganês.
Métodos semelhantes também são usados na fabricação de muitos aços para molas automotivos.
Inclusões frágeis não metálicas, normalmente inclusões de óxido de alumínio ou inclusões com alto teor de óxido de alumínio, têm um impacto significativo tanto no desempenho de trefilação do fio de aço quanto na qualidade do aço da mola.
Para evitar a formação de inclusões de óxido de alumínio ou ricas em óxido de alumínio, a composição do aço deve ser ajustada. Isto envolve um controle rigoroso do teor de óxido de alumínio na escória, monitoramento de matérias-primas e materiais auxiliares para evitar a entrada de alumínio no aço e o uso de um sistema de escória binária de baixa alcalinidade.
Esta solução foi inicialmente contraditória com as operações de refinação prevalecentes na época.
Existem inúmeros exemplos e artigos excelentes que abordam a termodinâmica de controle do tratamento de inclusão de pneus radiais e aços de molas.
4.2 Aço para rolamentos
O impacto de um único tipo de inclusão na vida à fadiga do aço para rolamentos permanece um tema de debate. No entanto, é amplamente aceito que o tamanho e a quantidade de inclusões no aço afetam significativamente a vida à fadiga do aço para rolamentos.
É bem conhecido que as inclusões de aluminato de cálcio e espinélio impactam negativamente o desempenho do aço para rolamentos.
Como resultado, alguns acreditam que a produção de aço para rolamentos deveria ter como objetivo atingir um teor muito baixo de oxigênio total e um teor muito baixo de enxofre e alumínio, para manter as inclusões não metálicas no mínimo.
Além disso, a introdução de magnésio da escória pode levar à formação de inclusões de espinélio, que devem ser evitadas.
Para produzir aço para rolamentos de alta qualidade, várias usinas siderúrgicas adotam diferentes métodos de processo com base em suas condições específicas.
No entanto, controlar a composição química da escória de refino é sempre um fator crítico no controle de inclusões não metálicas no aço para rolamentos.
A Figura 14 demonstra a influência dos teores de Al, O e Ag no aço para rolamento 100Cr6 (AISI52100) na composição da escória. A comparação dos teores calculados e medidos de alumínio e oxigênio no aço também é mostrada.
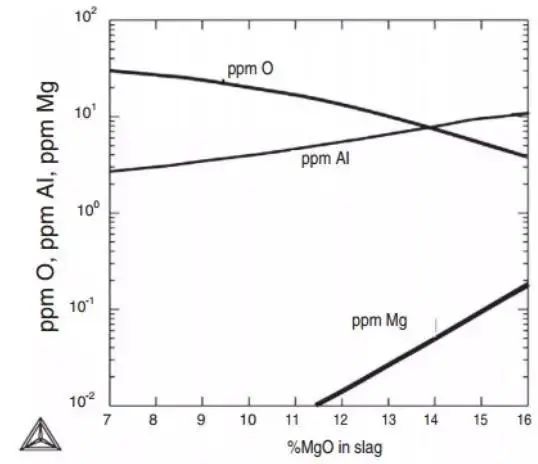
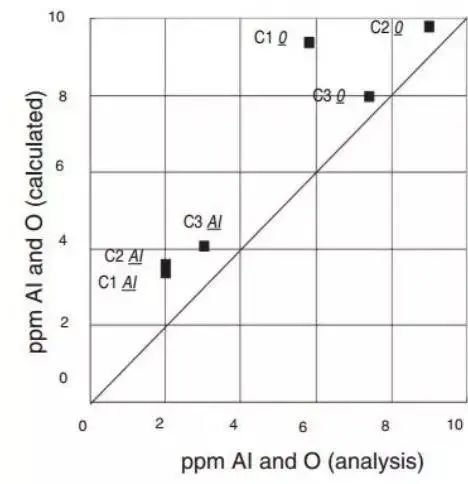
Figura 14
a. Sob o estado de equilíbrio do aço para rolamentos, a escória de refino% Al2Ó3=5%,% CaO=48% permanecem inalterados, e a influência do MgO no Al, O e Mg é calculada usando os bancos de dados Thermo calc e SLAG2 a 1540 ℃.
b. Compare o valor calculado e o valor medido do aço para rolamentos após terminar o refino do forno 3, e o banco de dados Thermo calc® e SLAG2 é usado para cálculo.
4.3 Prevenção de entupimento de bicos por tratamento com cálcio e inclusão de alumina
O tratamento com cálcio é usado para eliminar inclusões de sulfeto e regular a anisotropia de materiais laminados a quente ou forjados. Também ajuda a melhorar a trabalhabilidade das inclusões.
A prática de utilizar tratamento com cálcio para transformar inclusões de óxido de alumínio em inclusões compostas líquidas para evitar o entupimento dos flocos do bocal ganhou ampla utilização nas últimas décadas, apesar de ser um método controverso.
O processo de tratamento do cálcio é complexo, exigindo a consideração de fatores como solubilidade do cálcio, rendimento e alta pressão de vapor causada pela oxidação durante a adição de cálcio. Esses fatores foram exaustivamente pesquisados.
Estudos também foram realizados sobre o mecanismo de desnaturação da inclusão e a quantidade ideal de cálcio necessária para atingir o resultado desejado.
A formação de inclusões é um processo complexo. A camada externa, muitas vezes composta de óxidos, é coberta por um revestimento composto rico em enxofre. Este fenômeno e a distribuição dos elementos individuais são ilustrados na Figura 15.
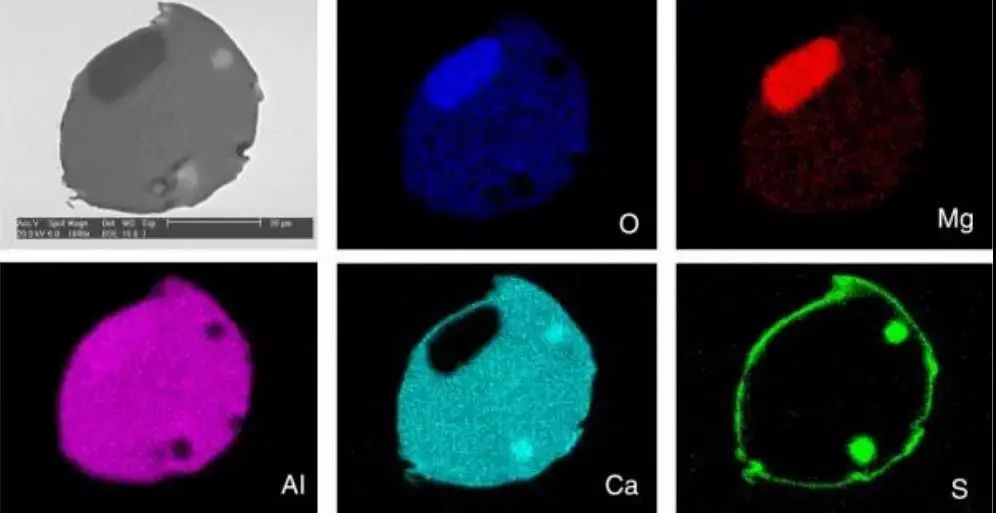
Figura 15
O tratamento com cálcio é usado para melhorar a fundibilidade do aço. Dissolve as grandes inclusões de partículas compostas de aluminato de cálcio, sulfeto e AgO encontradas na placa durante o lingotamento contínuo.
O magnésio também é reduzido da escória para o aço durante o processo de tratamento.
Como resultado do tratamento, uma porção significativa das inclusões torna-se uma fase líquida e não obstruirá o bocal durante a fundição.
No entanto, se a temperatura do aço fundido for muito baixa, a fundição se tornará um desafio.
A reação de inclusões não metálicas formadas durante a solidificação é um processo complexo, conforme ilustrado na Figura 16.
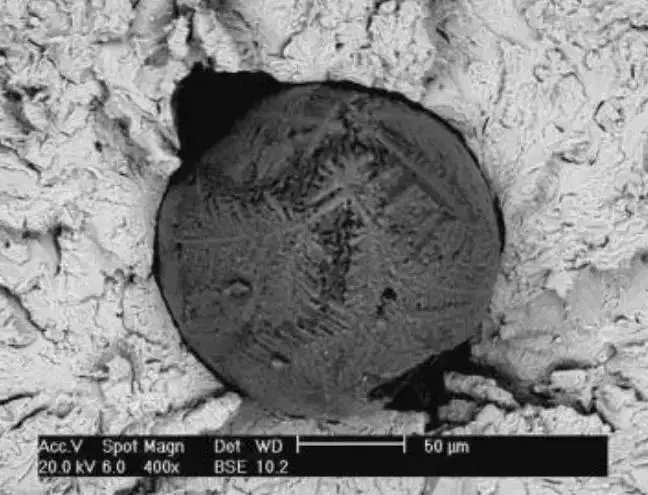
Figura 16
A amostra da placa contém grandes inclusões quebradas de aluminato de cálcio com fases complexas, e o invólucro de inclusão exibe uma estrutura de solidificação dendrítica.
A quantidade de cálcio necessária para modificar as inclusões de óxido de cálcio depende do teor total de oxigênio no aço.
Infelizmente, não existe um método atual para determinar com precisão o teor total de oxigênio no aço em tempo real, tornando difícil determinar a quantidade apropriada de cálcio a ser adicionada.
Isto representa um desafio significativo para a produção industrial.
Uma solução é usar a termodinâmica para entender o entupimento do fluxo de flocos no bocal e estabelecer a janela moldável para lingotamento contínuo.
O nível de oxigênio dissolvido pode ser medido, e esses dados também podem ser usados para monitorar a eficiência do tratamento com cálcio, conforme demonstrado na Figura 17.
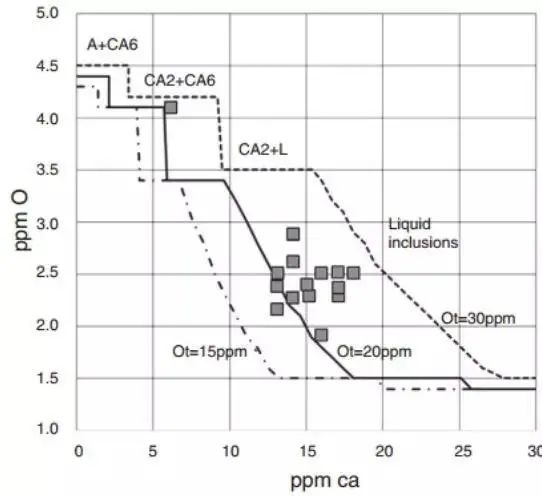
Figura 17
A figura acima mostra a correlação entre o teor de cálcio e o oxigênio dissolvido calculado em aço com uma composição de 0,025% Al, 0,01% S e teores variados de oxigênio total de 20, 25 e 30 ppm da esquerda para a direita, a uma temperatura de 1540 ℃.
A presença de fases não metálicas é indicada dentro de cada faixa de composição.
Os cálculos foram realizados utilizando as bases de dados Thermo-Calc® e SLAG3.
Cada ponto representa a medição experimental do teor de oxigênio dissolvido no aço, obtido sem qualquer bloqueio no bocal.
4.4 Metalurgia de óxido
O processo de fundição final enfrenta um desafio que exige o controle da microestrutura e não pode depender apenas da laminação a quente.
Pesquisas demonstraram que a presença de ferrita no metal de solda impacta positivamente na formação de inclusões não metálicas.
A teoria da nucleação por inclusão sugere que a formação de inclusão esgota o Mn na matriz circundante, o que parece ser eficaz.
As inclusões de óxidos não metálicos servem como núcleos de nucleação para inclusões de MnS e produziram resultados favoráveis em aplicações.
Além disso, a oxidação secundária do titânio no aço silício manganês transforma as inclusões em óxido de titânio, enquanto o óxido e o nitreto apresentam alta eficiência de nucleação na ferrita, conforme confirmado.
Koseki, Inoue, Suito e Park provaram que o nitreto de titânio pode atuar efetivamente como um agente nucleante, promovendo o aparecimento de grandes grãos equiaxiais em aço inoxidável de fundição contínua e processos de soldagem.
Park e Kang fizeram recentemente avanços neste campo.
Cálculos termodinâmicos e simulações de modelos mostram que o projeto de ligas e de processos na metalurgia de óxidos pode ser altamente benéfico.
5. Análise quantitativa de inclusões
Nas últimas décadas, a indústria siderúrgica encontrou o desafio de classificar e quantificar com precisão as inclusões não metálicas por meio de gráficos e imagens de comparação tradicionais. Para melhorar a análise quantitativa das inclusões, incluindo informações sobre tamanho, fração volumétrica e composição, surgiram novos métodos.
Em muitos casos, vários métodos devem ser empregados simultaneamente para obter uma compreensão abrangente da natureza e do processo das inclusões não metálicas. A pesquisa mostrou que certas características dependem da distribuição das inclusões, enquanto outras dependem de outros fatores. Por exemplo, o desempenho à fadiga do aço é influenciado pelo tamanho da maior inclusão.
A limpeza dos produtos siderúrgicos varia amplamente, exceto para produtos de baixo custo. O teor total de oxigênio do aço eliminado com alumínio e baixo carbono (LCAK) é de aproximadamente 40 ppm, enquanto o aço para rolamentos típico tem um teor total de oxigênio de cerca de 5 ppm. A fração volumétrica das inclusões de óxido é significativamente diferente, mas a presença de inclusões de sulfeto não é mencionada.
As estatísticas de valores extremos e sua aplicação desempenham um papel crítico na análise de fadiga. Esses métodos não são amplamente abordados na literatura geral, mas estão incluídos nesta revisão de literatura com referências fornecidas para leitura adicional. O método de notas de avaliação de inclusão por meio de estatísticas de valores extremos, proposto por Murakami no programa, tem sido amplamente utilizado na área de fadiga e tem produzido excelentes resultados.
É importante notar que este método não leva em consideração o tamanho máximo de inclusão na análise de fadiga. Na verdade, a fração volumétrica de inclusões causada por inclusões de partículas grandes pode aumentar. Este aspecto do método pode não corresponder às expectativas das siderúrgicas, pois não considera a inclusão da maior partícula.
6. Conclusão
O ditado bem estabelecido “Produzir boa escória leva a produzir bom aço” está profundamente enraizado na indústria siderúrgica.
Nas últimas décadas, o reconhecimento do impacto das inclusões não metálicas nas propriedades do aço fez com que o processo de produção de aço deixasse de meramente prevenir a contaminação por inclusão para otimizar a composição, quantidade e distribuição de inclusões no aço.
Essa transformação impacta todos os aspectos do processo de produção de aço, desde a seleção da matéria-prima (como evitar a contaminação por alumínio), até o projeto da composição da escória, a otimização das condições de refino secundário (como o tempo do processo de refino e as condições hidrodinâmicas) e o controle cuidadoso da operação do distribuidor e do molde.
Tornou-se prática padrão na produção de vários tipos de aço controlar cuidadosamente a oxidação secundária em todos os processos.
A termodinâmica desempenha um papel crítico na pesquisa da influência das inclusões no aço. A compreensão da termodinâmica, a composição química do aço e da escória de refino e as interações entre as condições do processo de produção de aço são agora amplamente estudadas.
Houve também uma melhoria significativa nas ferramentas de modelagem, permitindo uma abordagem mais baseada na ciência para controlar as inclusões no aço.
Estas tecnologias foram amplamente adotadas e continuam a evoluir no campo da modificação de inclusão não metálica. No entanto, ainda há necessidade de melhorar continuamente a escória de refino e compreender plenamente o papel das inclusões não metálicas no aço.
A modificação da inclusão e a engenharia da metalurgia de óxido são agora amplamente utilizadas em usinas siderúrgicas, resultando em um aço que é pelo menos uma ordem de magnitude mais limpo do que era há várias décadas. Isto também apresentou novos desafios para a análise qualitativa e quantitativa de inclusões não metálicas.
A análise quantitativa de todas as inclusões e seu impacto nas propriedades e comportamento do aço é agora um requisito básico, e há amplo espaço para discussão e pesquisas futuras.
Apesar dos avanços e insights resumidos nesta revisão, o desafio constante nas próximas décadas será melhorar continuamente diversas tecnologias e melhorar a qualidade do aço.