O que é rebarba?
Em relação às rebarbas, vamos começar definindo o que são rebarbas.
Rebarbas são minúsculas partículas de metal que se formam na superfície usinada de uma peça. Essas partículas finas são criadas como resultado de fundição de metal, retificação, corte, fresagem e outros processos semelhantes.
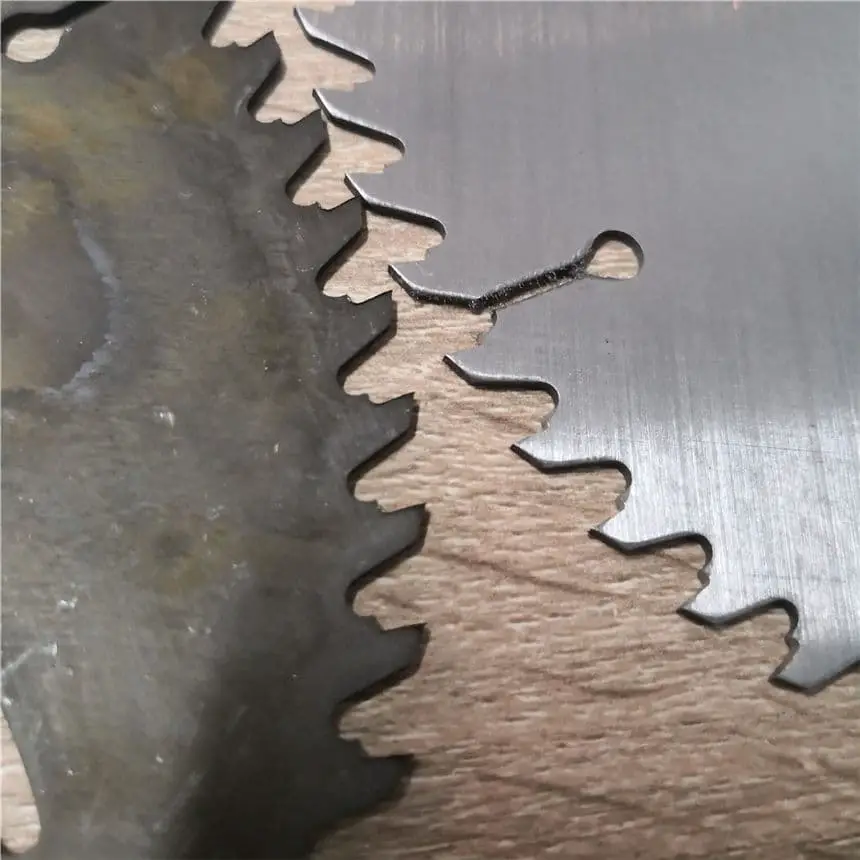
Classificação de rebarba
A formação de rebarbas varia dependendo do processo de fabricação utilizado. Com base nesses processos, as rebarbas geralmente podem ser classificadas em:
1. Rebarba de fundição:
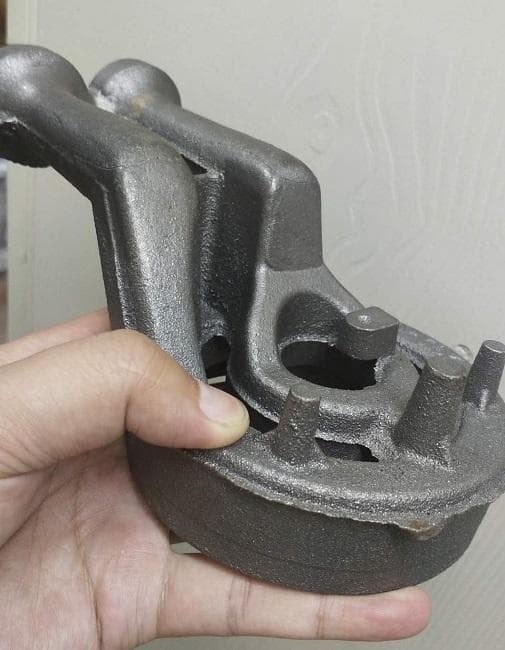
Normalmente, o tamanho da rebarba, que é o excesso de material produzido na junta do molde ou na raiz da comporta, é medido em milímetros.
2. Rebarba de forjamento:
Na junta do molde metálico, rebarbas são causadas pela deformação plástica do material forjado.
Soldagem elétrica e rebarbas de soldagem a gás:
A rebarba de soldagem elétrica refere-se ao excesso de material de enchimento que se projeta da superfície da peça.
As rebarbas de soldagem a gás são a escória que transborda do corte durante o processo de corte a gás.
3. Rebarba de estampagem:
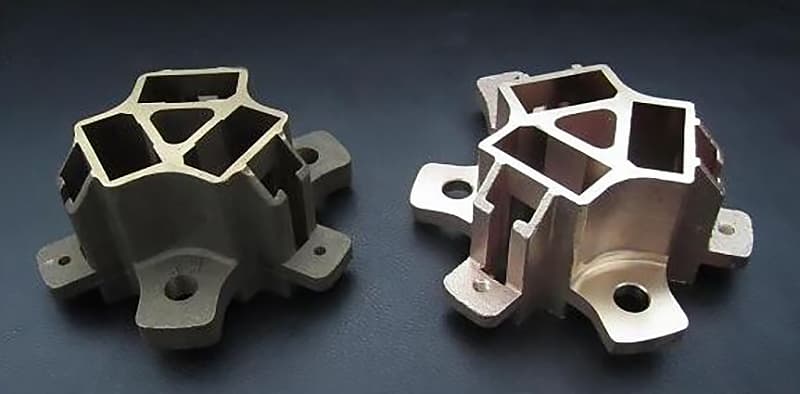
Durante a estampagem, existe uma folga entre o punção da matriz e a matriz inferior, ou entre as fresas no entalhe, o que resulta na geração de rebarbas devido ao desgaste da matriz.
O formato da rebarba de estampagem varia de acordo com fatores como o material da placa, a espessura da placa, o espaço entre as matrizes superior e inferior e o formato das peças estampadas.
4. Corte de rebarbas:
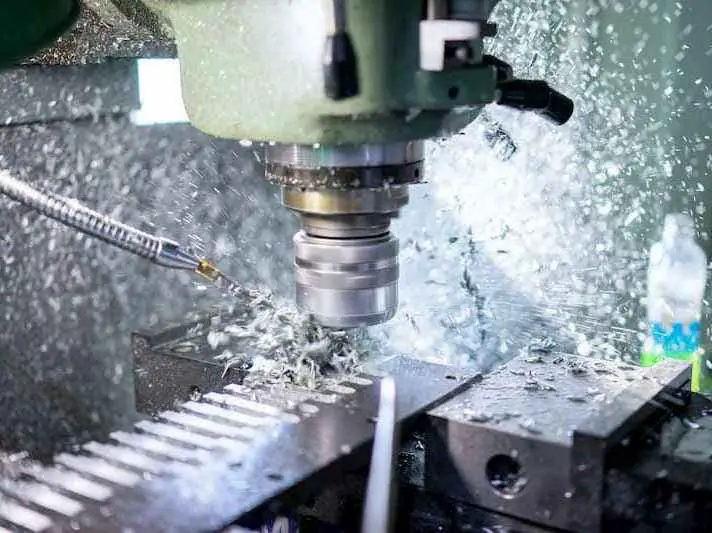
Torneamento, fresamento, aplainamento, retificação, furação, alargamento e outros métodos de processamento também podem criar rebarbas.
As rebarbas produzidas por esses diversos métodos de usinagem possuem diferentes formatos, que são influenciados pelo tipo de ferramenta utilizada e pelos parâmetros do processo.
5. Rebarba de formação de plástico:
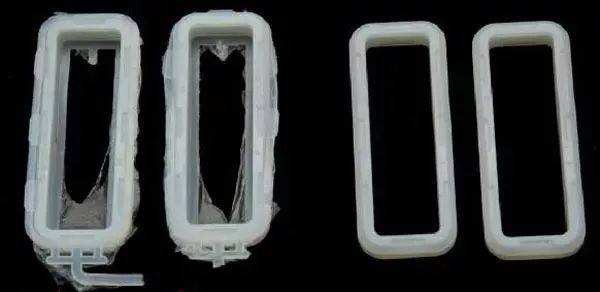
Como rebarbas de fundição, rebarbas geradas na junta do molde de plástico.
Como rebarbar?
A geração de rebarbas ocorre devido ao vão na junta entre o molde e a matriz.
Atualmente, é um desafio eliminar completamente as rebarbas devido ao alinhamento imperfeito entre o molde e a matriz.
No entanto, com os avanços nos materiais metálicos que estão se tornando mais duros, mais fortes e mais duráveis, há um número crescente de componentes integrais complexos em produtos mecânicos, tornando a rebarbação cada vez mais difícil.
À medida que a tecnologia avança e o desempenho do produto melhora, a procura por produtos de maior qualidade cresce, tornando a remoção de rebarbas das peças cada vez mais importante.
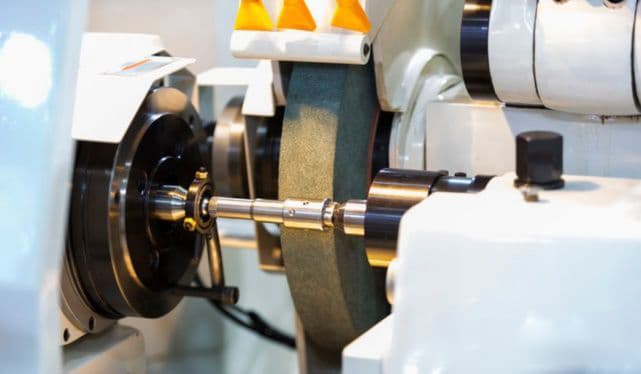
A presença de rebarbas não só prejudica a aparência dos produtos, mas também reduz significativamente o padrão de qualidade das peças metálicas e afeta sua montagem, desempenho e vida útil.
Para mitigar a ocorrência de rebarbas, é fundamental escolher ferramentas de corte de alta qualidade que minimizem sua aparência, como fresas com acabamento liso.
Mesmo com as ferramentas adequadas, a remoção de rebarbas ainda pode exigir uma operação secundária de rebarbação.
Este processo de rebarbação secundário pode representar até 30% do custo das peças acabadas e é difícil de automatizar, tornando as rebarbas um problema persistente.
As técnicas de rebarbação manual são insuficientes para atender às demandas dos requisitos modernos de rebarbação, levando ao desenvolvimento de novas tecnologias e processos de rebarbação automatizados.
A seguir, discutirei os seguintes métodos de rebarbação:
1. Rebarbação
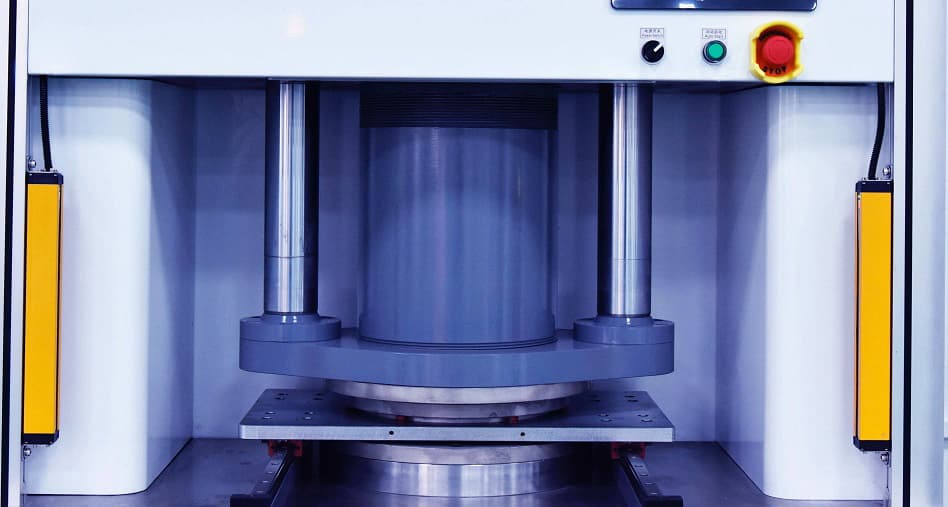
O processo de rebarbação é realizado usando uma matriz em conjunto com uma puncionadeira.
A rebarbação da matriz de corte incorre em custos de produção tanto da matriz de corte bruto quanto da matriz de corte fino e pode exigir a criação de uma matriz de modelagem. Além disso, as ferramentas podem precisar ser substituídas com frequência.
Este método é apropriado para produtos com superfície de corte simples e é mais eficiente e eficaz do que a rebarbação manual.
2. Rebarbação de moagem
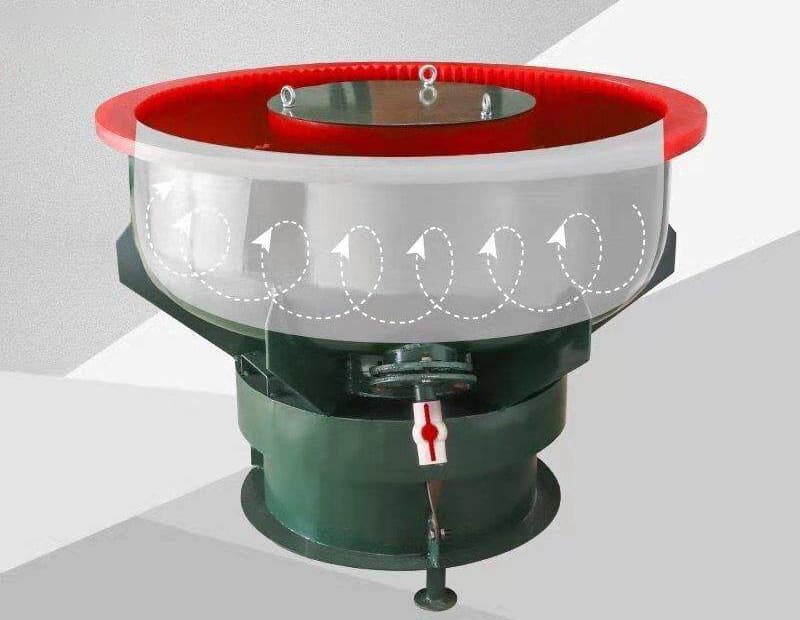
A rebarbação por esmerilhamento é um método amplamente utilizado para rebarbação, que envolve técnicas como vibração, jato de areia e rolo.
No entanto, o problema com a rebarbação por desbaste é que nem sempre resulta numa superfície completamente lisa, o que pode exigir intervenção manual adicional ou a utilização de métodos de rebarbação adicionais.
Este método é ideal para pequenos produtos produzidos em grandes quantidades.
3. Rebarbação em alta temperatura
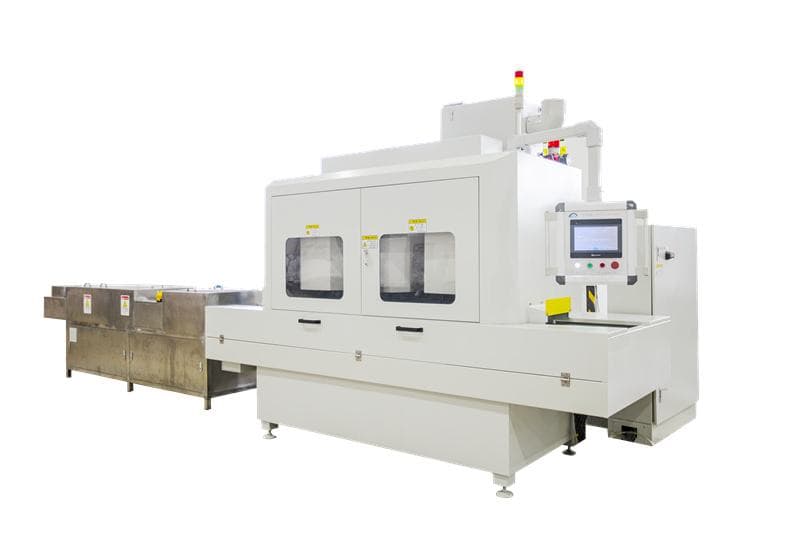
A rebarbação de alta temperatura, também conhecida como rebarbação térmica e rebarbação por explosão térmica, é um processo que envolve a introdução de gás natural em um forno de equipamento e fazendo com que ele exploda instantaneamente através de meios e condições específicos. Essa explosão gera energia que é usada para dissolver e remover rebarbas.
Este método requer equipamentos caros, normalmente custando mais de um milhão de yuans, e opera com elevados requisitos tecnológicos.
No entanto, a eficiência de rebarbação deste método é baixa e pode resultar em efeitos colaterais como ferrugem e deformação.
A rebarbação por explosão térmica é usada principalmente em peças de alta precisão em indústrias como automotiva e aeroespacial.
4. Congelar rebarbação
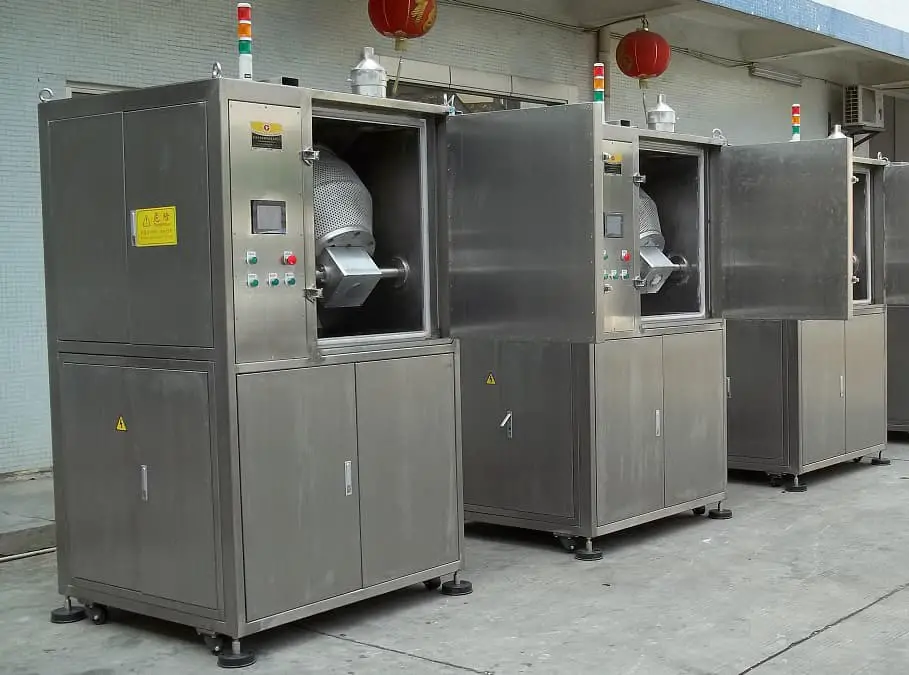
A rebarbação congelada é um processo que envolve uma rápida queda na temperatura para tornar a rebarba quebradiça rapidamente, seguida pela pulverização de projéteis para removê-la.
Este método é ideal para produtos com paredes finas de rebarbas e peças pequenas.
No entanto, o custo do conjunto completo de equipamentos não é barato, variando normalmente de duzentos a trezentos mil yuans.
5. Rebarbação química
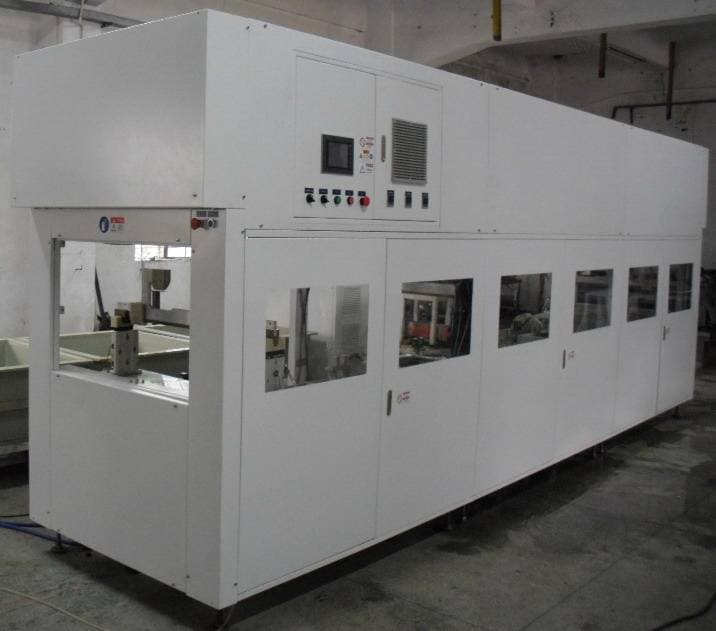
A rebarbação química é um processo automatizado que remove seletivamente rebarbas de peças metálicas usando o princípio da reação eletroquímica. É particularmente útil para remover rebarbas internas difíceis de remover, como rebarbas finas em corpos de bombas, corpos de válvulas e outros produtos similares.
6. Rebarbação de máquina de gravação
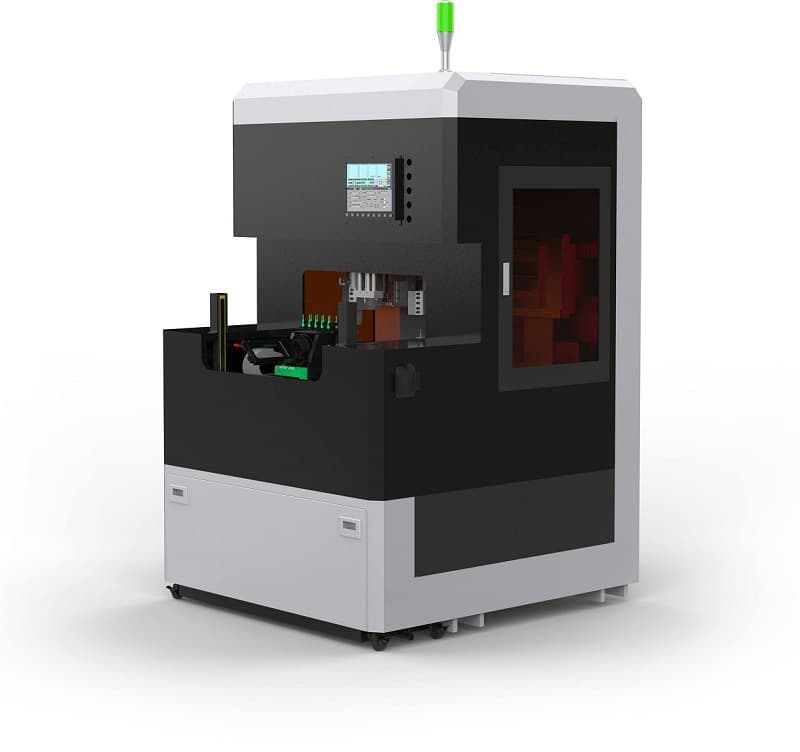
O custo deste conjunto de equipamentos para remoção de rebarbas em peças de trabalho usando uma máquina de gravação é normalmente de apenas dezenas de milhares de yuans, tornando-o uma opção acessível para remoção de rebarbas com estruturas espaciais simples e posições regulares.
7. Rebarbação eletrolítica
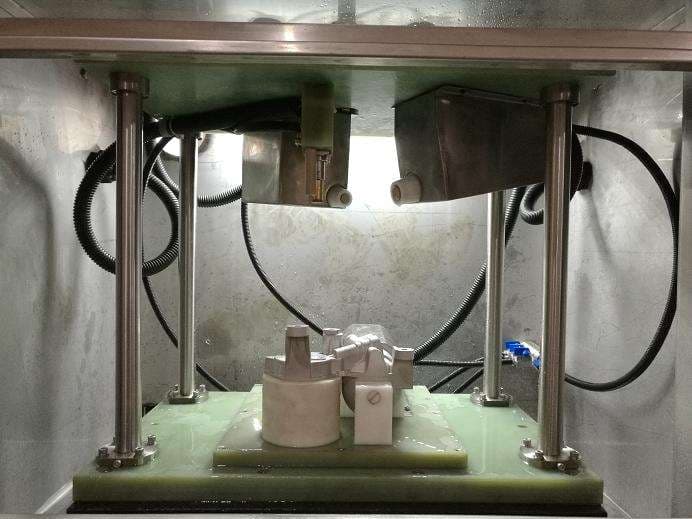
Uma técnica para eliminar rebarbas de componentes metálicos usando eletrólise:
A ferramenta catódica, normalmente feita de latão, é posicionada próxima à seção rebarbada da peça metálica com uma distância específica entre eles.
Durante a usinagem, a ferramenta catódica é conectada ao terminal negativo de uma fonte de alimentação CC, enquanto a peça de metal é conectada ao terminal positivo.
O eletrólito de baixa pressão pode então fluir entre a peça de metal e o cátodo.
Assim que a fonte de alimentação CC for ativada, a rebarba será dissolvida pelo ânodo e removida, levada pelo eletrólito.
Vantagens:
É utilizado para eliminar rebarbas de peças ocultas, furos cruzados ou componentes de formatos complexos com alta eficácia.
Normalmente, o processo leva apenas alguns segundos a algumas dezenas de segundos.
É ideal para rebarbar engrenagens, bielas, corpos de válvulas, orifícios de passagem de óleo de virabrequim, bem como arredondar cantos vivos.
Desvantagens:
A área ao redor da rebarba do componente também é impactada pela eletrólise, fazendo com que o brilho original da superfície seja perdido e potencialmente afetando sua precisão dimensional.
Além disso, o eletrólito tem efeito corrosivo, por isso é necessário limpar e prevenir a ferrugem após o rebarbamento.
8. Rebarbação ultrassônica
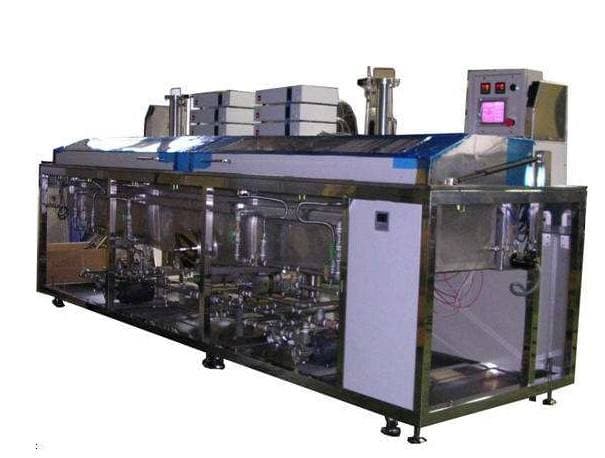
A transmissão de ondas ultrassônicas também pode produzir alta pressão momentânea, que pode ser utilizada para eliminar rebarbas nos componentes. Este método possui alta precisão e é empregado principalmente para eliminar pequenas rebarbas que só podem ser vistas ao microscópio.
9. Rebarbação com jato de água de alta pressão
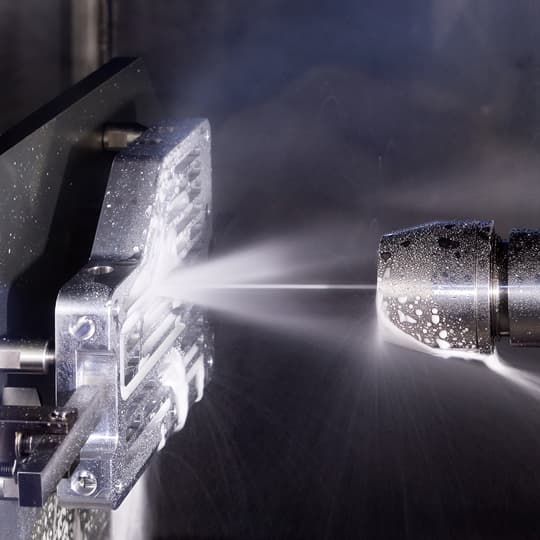
O impacto instantâneo da água é utilizado para eliminar rebarbas e rebarbas produzidas durante a usinagem, além de cumprir o objetivo de limpeza.
É categorizado em duas categorias: tipo de movimentação de peças e tipo de movimentação de bicos.
Tipo de movimentação da peça
Esta ferramenta é econômica e adequada para rebarbar e limpar corpos de válvulas simples. No entanto, tem a desvantagem de a compatibilidade entre o bocal e o corpo da válvula não ser óptima e pode não proporcionar uma rebarbação eficaz para furos transversais e oblíquos no corpo da válvula.
Bico móvel
A distância entre o bico e a parte geradora de rebarbas do corpo da válvula pode ser ajustada de forma eficaz através do controle CNC, que corresponde às rebarbas nos furos transversais, oblíquos e cegos dentro do corpo da válvula. No entanto, este equipamento tem um custo proibitivo.
Vantagens:
Bom efeito de remoção e velocidade rápida.
Desvantagens:
O equipamento básico não é suficiente e o equipamento premium não é acessível.
10. Rebarbação de dispositivo mecatrônico
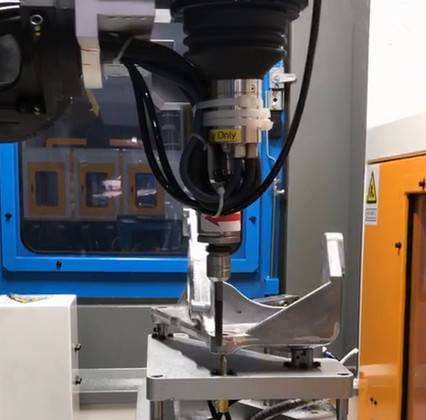
Os dispositivos mecatrônicos incorporam os mais recentes avanços de diversas disciplinas, como máquinas e máquinas de precisão, microeletrônica, computadores, sistemas de controle e acionamento automáticos, sensores, processamento de informações e inteligência artificial.
Alguns componentes comuns de dispositivos mecatrônicos incluem um cubo de alumínio, uma carcaça do conversor de frequência, uma carcaça do sincronizador, um cubo da engrenagem sincronizadora, uma tampa do rolamento, um bloco de cilindros, um corpo da válvula, uma tampa da válvula, um eixo de saída e uma engrenagem do motor.
Vantagens:
- Custo-beneficio
- Desempenho eficaz
- Alta precisão e eficiência
Desvantagens:
- Popularidade limitada, pois ainda está em fase de desenvolvimento
- Requer suporte de dados altamente preciso.
11. Rebarbação magnética
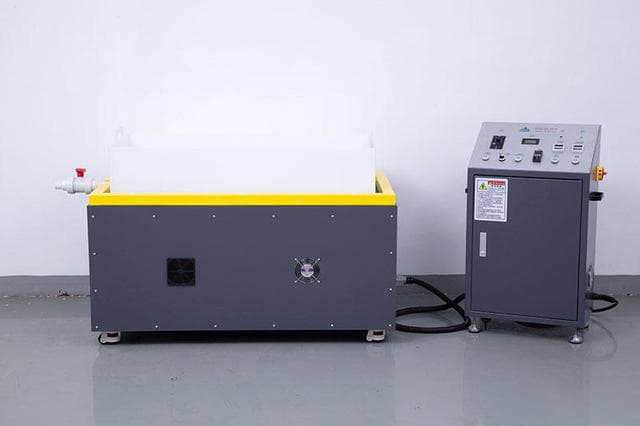
A distribuição exclusiva do campo magnético produz um efeito de indução magnética forte e estável, permitindo o desbaste completo da agulha de aço magnético e da peça de trabalho em todas as direções e em vários ângulos para uma rebarbação eficiente.
Vantagens:
Este método é eficaz para formas complexas, fendas em peças com vários furos, roscas internas e externas, etc.
Desvantagens:
Pode impactar negativamente o magnetismo de produtos com propriedades magnéticas, portanto deve-se ter cuidado ao utilizá-lo.
12. Rebarbação manual
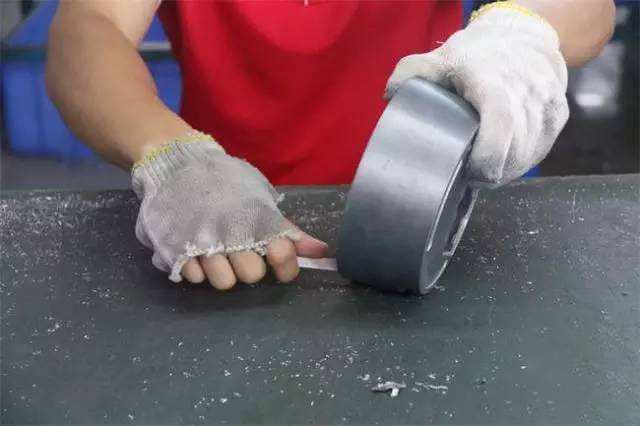
A rebarbação manual é atualmente utilizada por muitos pequenos fabricantes.
A maioria das rebarbas são pequenas e a taxa de remoção não é particularmente alta, desde que não haja rebarbas presentes.
As ferramentas usadas para rebarbação manual incluíam limas, raspadores e lixas, mas agora os aparadores de borda são usados predominantemente.
Vantagens:
- Flexibilidade na operação manual, diferentes ferramentas podem ser substituídas para rebarbar diversas partes da peça.
Desvantagens:
- O custo da mão de obra é alto, a eficiência é baixa e pode ser um desafio remover furos transversais e peças complexas.
13. Rebarbação com ferramentas manuais
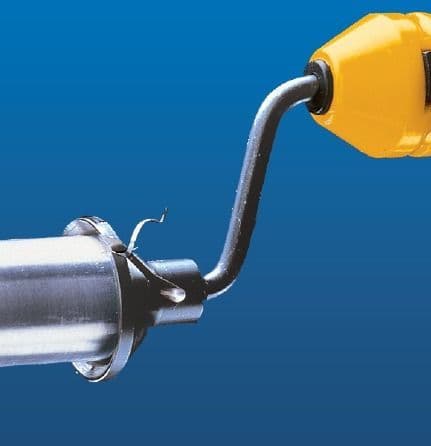
Este tipo de rebarbação não é significativamente diferente da rebarbação manual, exceto pelo uso de ferramentas diferentes.
A rebarbação manual envolve o uso de ferramentas frias. Alguns exemplos dessas ferramentas incluem uma retificadora e uma furadeira elétrica, que pode rebarbar e chanfrar usando fresas, brocas, cabeçotes de retificação e outros materiais.
Diferentes ferramentas podem ser usadas para completar a rebarbação da maioria das peças.
Vantagens: Oferece alta flexibilidade e pode se adaptar à retificação da maioria dos ambientes de peças.
Desvantagens: A velocidade é lenta e pode causar alguns danos à peça de trabalho.
14. Processo de rebarbação
Como evitar rebarbas no projeto do processo?
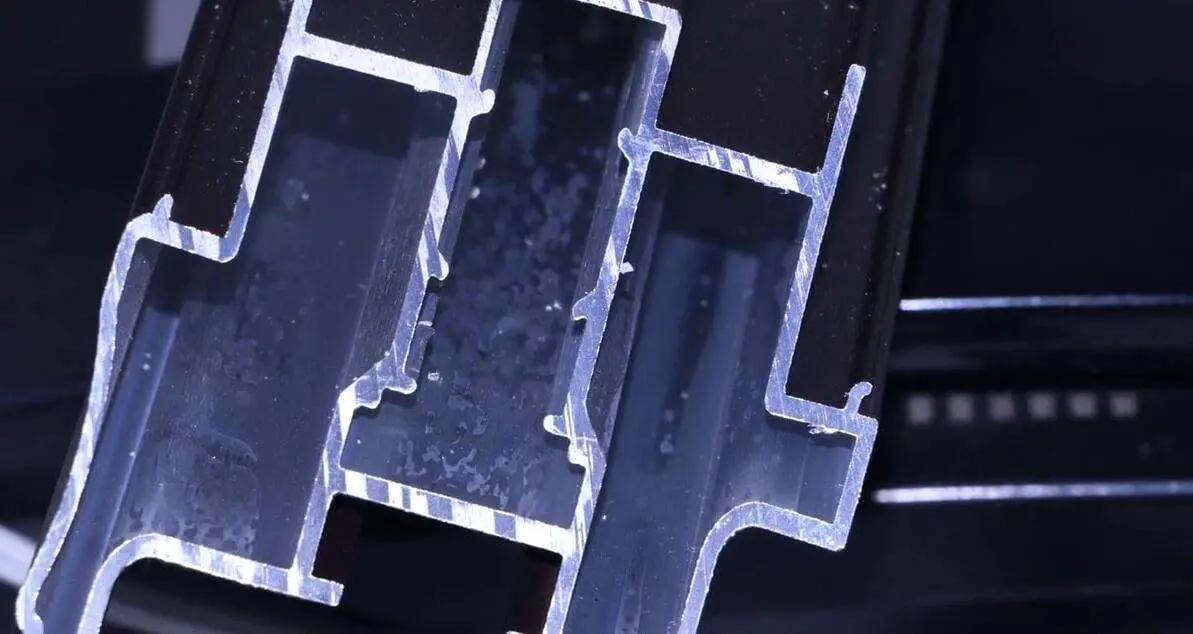
Aqui estão seis etapas para evitar rebarbas no processo de design:
(1) Adotar métodos de processamento apropriados:
No corte de metal, o tamanho e o formato das rebarbas produzidas por vários métodos de processamento variam. No processo de projeto, é melhor escolher um método que gere as menores rebarbas possíveis. Por exemplo, ao usinar superfícies planas, o fresamento ascendente é mais eficaz do que o fresamento descendente.
(2) Organize razoavelmente a sequência de processamento:
Ao organizar a sequência de processamento das peças, tente colocar primeiro o processo que gera as rebarbas maiores e o processo que gera as rebarbas menores por último, usando o próximo processo para remover as rebarbas geradas no processo anterior. Por exemplo, ao usinar peças de eixo com rasgos de chaveta, é mais razoável alterar a sequência típica de usinagem de torneamento antes do fresamento para fresamento antes do torneamento.
(3) Escolha sabiamente a direção:
Com base no efeito de canto das rebarbas, durante o corte de metal, a saída deve estar localizada na peça com grande ângulo de canto para reduzir a formação de rebarbas. Ao mesmo tempo, é importante observar que a aresta de corte deve estar localizada em um local onde seja fácil remover rebarbas, para reduzir o custo de remoção.
(4) Selecione adequadamente os parâmetros de corte:
No processo de corte de peças, usar um método que produza cavacos grandes resultará em rebarbas grandes. Isso ocorre porque a produção de cavacos grandes aumenta a resistência ao corte, o calor de corte, o desgaste da ferramenta e diminui a durabilidade, bem como aumenta a deformação plástica do material da peça, o que resulta em rebarbas maiores. Portanto, ao processar peças, geralmente é melhor reduzir a formação de rebarbas reduzindo a profundidade e a quantidade de corte, especialmente no processamento de precisão.
(5) Organize razoavelmente o processo de tratamento térmico:
O processo de tratamento térmico deve ser organizado em diferentes etapas do processo de processamento para alterar as propriedades físicas e mecânicas, como dureza e alongamento, do material da peça, o que pode reduzir as rebarbas geradas durante o processamento. Por exemplo, na produção em lote de peças, o uso de um rebolo de formação para retificar a ranhura do anel elástico das peças do eixo de uma só vez após o tratamento térmico gera mais rebarbas do que o processo de tratamento de reaquecimento após o torneamento.
(6) Use acessórios no processamento:
No processo de corte de peças, diversos acessórios podem ser utilizados na aresta de corte da peça, como suporte auxiliar, mandril ou enchimento de liga de baixo ponto de fusão. Eles são usados para melhorar a rigidez da aresta de corte da peça usinada, reduzir a deformação de corte e reduzir a formação de rebarbas na aresta de corte. Embora as rebarbas sejam inevitáveis no processo de processamento, é melhor resolver o problema das rebarbas do processo para evitar intervenção manual excessiva.