O aço para matriz de trabalho a quente H13 possui excelente resistência térmica, resistência à fadiga a frio e a quente e resistência à erosão de metal líquido. Como resultado, encontra amplas aplicações em matrizes de extrusão a quente, matrizes de fundição sob pressão de liga de alumínio e outros tipos de matrizes.
No processo de utilização, o desempenho de impacto da matriz determina a sua vida útil, uma vez que a matriz precisa suportar uma força de impacto substancial.
A tecnologia de fundição sob pressão é predominantemente utilizada na produção de peças automotivas, como suportes, embreagens e cárteres, devido ao crescimento da indústria automobilística.
As duas características significativas da fundição sob pressão são o enchimento de alta pressão e alta velocidade da cavidade do molde. Em comparação com o molde de extrusão, o molde de fundição sob pressão tem que suportar mais energia de impacto durante o processo de produção, principalmente na fabricação de peças grandes. Isso requer o uso de aço para moldes de alta qualidade.
A matriz de extrusão feita de barras de aço H13 produzidas por processos convencionais e módulos relativamente pequenos pode atingir o efeito desejado em termos de longevidade.
O fluxo do processo de produção de um lote de módulos de aço H13 em uma fábrica é o seguinte: pré-tratamento de ferro fundido → fundição em forno elétrico de 20t → refino em forno LF (forno de refino panela) → tratamento a vácuo em forno VD (forno de refino a vácuo) → fundição em lingotes de 16t → refusão de lingotes de 16t em forno de eletroescória com proteção de gás de 16t → recozimento de lingotes → aquecimento (1180 ℃, 20h) → tarugo de forjamento rápido 45MN/produto acabado (especificação da seção: 400 mm × 500 mm) → recozimento → teste não destrutivo → inspeção de amostragem.
Durante o teste de energia de impacto de uma placa de aço, descobriu-se que o desempenho de impacto não atendia ao padrão esperado.
Para identificar a causa do desempenho de baixo impacto, pesquisadores como Li Yongdeng e Yang E da Daye Special Steel Co., Ltd., Laboratório Principal Provincial de Aço Especial de Alta Qualidade de Hubei e Instituto de Supervisão e Inspeção de Qualidade do Produto Hubei Huangshi analisaram o materiais. Eles identificaram a razão para a energia de impacto insatisfatória e forneceram uma base para a melhoria subsequente da produção.
1. Inspeção física e química
1.1 Análise da composição química
A composição química do módulo de aço H13 com energia de impacto não qualificada foi detectada e os resultados estão em conformidade com os requisitos da GB/T 1299-2014 para ferramentas e matrizes de aço.
1.2 Teste de desempenho de impacto
O teste de desempenho de impacto deve ser realizado utilizando corpos de prova de impacto sem entalhes transversais.
As amostras devem ser retiradas da parte central do módulo e, em seguida, submetidas a tratamento de têmpera e revenido após a confecção do branco, seguida de usinagem até o tamanho final da amostra.
Três amostras foram testadas e o tamanho da amostra de impacto foi de 55 mm x 10 mm x 7 mm.
Uma amostra com bom desempenho de impacto deve ter uma energia de impacto superior a 300J, enquanto uma amostra com baixo desempenho de impacto deve ter uma energia de impacto inferior a 100J.
1.3 Análise SEM da fratura da amostra por impacto
Após passar pela limpeza ultrassônica, a superfície de fratura da amostra de impacto foi analisada em microscópio eletrônico de varredura.
Para amostras que não atingiram a energia de impacto esperada, a superfície de fratura parece relativamente plana em geral. Após um exame mais detalhado, vários graus de características de fratura intergranular foram observados na área de origem da fratura.
Amostras com maior energia de impacto apresentaram menores áreas de fratura intergranular, enquanto aquelas com menor energia de impacto apresentaram maiores áreas de fratura intergranular.
As amostras que atingiram a energia de impacto esperada exibiram uma morfologia de fratura de Bremsstrahlung, sem observação de fissuras intergranulares. Além disso, nenhum defeito, como grandes inclusões, foi encontrado na superfície da fratura.
As morfologias de fratura de amostras com baixa e alta energia de impacto estão representadas na Figura 1 e Figura 2, respectivamente.
Em geral, a fratura intergranular é uma forma de contorno de grão.
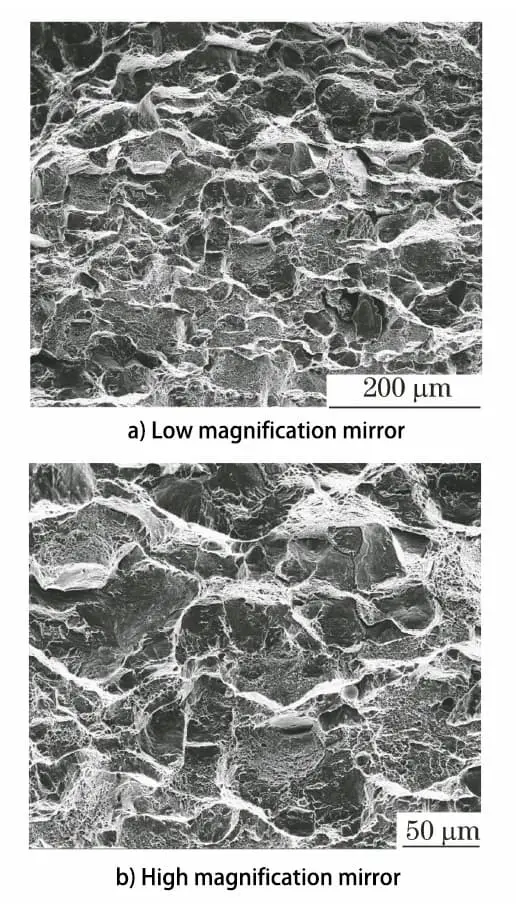
Fig. 1 Micromorfologia de Fratura de Espécime com Baixa Energia de Impacto

Fig. 2 Micromorfologia de Fratura de Espécime com Energia de Alto Impacto
1.4 Inspeção metalográfica
Após lixamento e polimento da superfície de fratura da amostra de impacto, esta foi atacada com ácido nítrico e álcool e observada ao microscópio metalográfico.
Observou-se que o contorno de grão local da amostra com baixa energia de impacto era evidente. O carboneto estava agrupado e com faixas no limite do grão, e nenhum carboneto primário significativo foi encontrado.
Foram retiradas amostras recozidas do mesmo lote com baixa energia de impacto. Após lixamento, polimento e ataque com álcool com ácido nítrico, a microestrutura apresentou perlita esférica. Carbonetos esféricos foram distribuídos em cadeias localmente e nenhuma agregação aparente de carbonetos foi encontrada. Isto indica que a segregação no processo de fundição está em um nível normal.
A Figura 3 mostra a microestrutura das amostras com baixa energia de impacto.

Fig. 3 Microestrutura de Fratura de Espécime com Energia de Baixo Impacto
Para a amostra com maior energia de impacto, a estrutura temperada e revenida mostra uma martensita revenida homogênea, e nenhum carboneto de contorno de grão óbvio foi encontrado.
Por outro lado, a estrutura recozida correspondente mostra uma perlita esferoidal uniforme, e nenhum fenômeno de rede de agregação de carboneto foi observado (consulte a Fig. 4).

Fig. 4 Microestrutura de Fratura de Espécime com Energia de Alto Impacto
2. Análise abrangente
A composição química do aço H13, fundido por refusão por eletroescória, atende aos requisitos da norma GB/T 1299-2014.
Observações da microestrutura indicam que não há acúmulo aparente de carboneto ou segregação de bandas, e não há inclusões não metálicas significativas na superfície da fratura. Isto indica que o processo de fundição está sob controle normal.
Com base na análise da micromorfologia e estrutura metalográfica da fratura por impacto, a amostra com baixa energia de impacto apresenta características intergranulares, e possui evidentes carbonetos de rede em sua estrutura.
A amostra com alta energia de impacto apresenta morfologia de covinhas e sua estrutura é uniforme.
A fratura intergranular ocorre quando o limite do grão do aço suporta a carga de impacto porque é relativamente fraco.
A principal razão para a baixa tenacidade ao impacto do aço H13 é a precipitação de carbonetos secundários ao longo do contorno do grão. A pesquisa indica que os carbonetos encontrados no aço H13 são principalmente V8C7, Cr23C6 e Cr3C2 (Cr2VC2).
O aquecimento insuficiente durante o forjamento e o resfriamento inadequado após o processo contribuem para o acúmulo desses carbonetos ao longo do contorno do grão. Esta acumulação enfraquece o limite do grão e, como resultado, reduz a tenacidade ao impacto do aço.
Para melhorar as propriedades de impacto do aço H13, é crucial evitar a precipitação de carbonetos secundários ao longo do contorno do grão. Isto pode ser conseguido controlando rigorosamente a temperatura de aquecimento antes do forjamento e a taxa de resfriamento após o processo. Ao fazer isso, a precipitação de carbonetos de rede pode ser efetivamente reduzida.
O refino e a dispersão de carbonetos no aço podem ser alcançados através da homogeneização em alta temperatura, aumentando a deformação durante o forjamento e diminuindo a temperatura final do forjamento. Este processo é benéfico na inibição da precipitação de carbonetos secundários ao longo dos limites dos grãos.
Ao submeter o aço H13 ao tratamento de homogeneização em alta temperatura, a segregação dos componentes que ocorre durante a fundição e a solidificação pode ser efetivamente melhorada, e a tendência de carbonetos e impurezas de segregar nos limites dos grãos é enfraquecida.
O resfriamento rápido após o forjamento pode evitar a precipitação de carbonetos grossos ou reticulados no aço, bem como evitar que carbonetos secundários se precipitem ao longo do limite do grão para formar cadeias de carboneto.
O resfriamento rápido seguido de recozimento após o forjamento pode produzir uma estrutura perlita esferoidal uniforme no aço.
O aumento da deformação durante o processo de forjamento pode melhorar a estrutura interna do aço. Grandes estruturas fundidas e carbonetos eutéticos instáveis podem ser quebrados pela aplicação de grandes tensões.
Se viável, o processo de recalque e forjamento por estiramento pode ser empregado para melhorar ainda mais a estrutura do aço H13 e suas propriedades.
3. Conclusão e sugestões
(1) A principal razão pela qual o desempenho do impacto transversal do aço H13 fundido por refusão por eletroescória não pode atingir a meta esperada é devido à falta de controle adequado sobre o processo de forjamento.
Após o tratamento térmico, os carbonetos secundários precipitam ao longo dos limites dos grãos, enfraquecendo-os. Para melhorar efetivamente a tenacidade ao impacto transversal do aço H13, é essencial evitar a precipitação secundária de carboneto em uma rede ao longo do limite do grão.
(2) A resistência ao impacto do aço H13 pode ser significativamente melhorada através da implementação de tratamento de homogeneização em alta temperatura, aumentando a deformação do forjamento, melhorando a taxa de resfriamento após o forjamento, minimizando a segregação e evitando a precipitação de carboneto ao longo dos limites dos grãos.